IMCA Safety Flash 04/24 PDF
Document Details
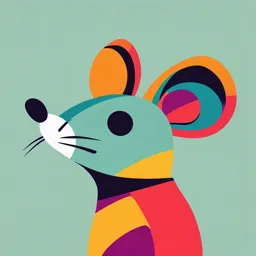
Uploaded by IntelligibleBeige
null
2024
Tags
Summary
This IMCA Safety Flash, dated February 2024, details safety incidents related to confined spaces and hot work at height on a barge. The document discusses unauthorized entry into a confined space and the importance of proper safety procedures, including risk assessments, permits to work, and appropriate signage.
Full Transcript
Safety Flash 04/24 – Fe...
Safety Flash 04/24 – February 2024 IMCA Safety Flashes summarise key safety matters and incidents, allowing lessons to be more easily learnt for the benefit of all. The effectiveness of the IMCA Safety Flash system depends on members sharing information and so avoiding repeat incidents. Please consider adding [email protected] to your internal distribution list for safety alerts or manually submitting information on incidents you consider may be relevant. All information is anonymised or sanitised, as appropriate. 1 Unauthorised entry into confined space What happened Applicable Planned repair works were taking place on a barge. The work Life Saving involved hot work (welding & grinding). During the works, the Rule(s) Bypassing Confined Work stand-by person, controlling several areas, observed sub-contract Safety Space Authorisation Controls personnel accessing a confined space in which welding was taking place. Stop Work Authority was exercised immediately, and the unauthorized personnel requested to leave the area. There was an immediate stand down to discuss the consequences of unauthorized personnel access to confined spaces and the potential consequences. No-one was harmed. Photographs from member showing where work was taking place What went right The job was stopped immediately; There was a safety stand down to allow time for crew to discuss and understand what had happened. What went wrong Working environment: A lack of physical barriers and appropriate warning notification around the confined space; The contractor did not have adequate personnel for CoW ( Control of Work) and the third-party crew did not have awareness of the specific hazards relating to confined space entry; There was insufficient or inadequate supervision of the third-party personnel onboard. Our member took the following actions Contractor management was approached to reiterate importance of compliance with vessel access and control of work procedures; Improved signage and barriers around confined space areas; IMCA store terms and conditions (https://www.imca-int.com/legal-notices/terms/) apply to all downloads from IMCA’s website, including this document. IMCA makes every effort to ensure the accuracy and reliability of the data contained in the documents it publishes, but IMCA shall not be liable for any guidance and/or recommendation and/or statement herein contained. The information contained in this document does not fulfil or replace any individual’s or Member's legal, regulatory or other duties or obligations in respect of their operations. Individuals and Members remain solely responsible for the safe, lawful and proper conduct of their operations. © 2022 Page 1 of 6 Ensured completion of Risk Assessment, Permit to Work, and robust access controls for Confined Space entry; Ensured that only trained & authorized personnel can access Confined space areas and that their access is authorized and controlled by immediate management and the stand-by person. Members may wish to refer to: SIMOPS – Smoke from hot work task enters confined space MSF: LTI – Fall from Height (control of work during SIMOPS) Confined spaces: The dangers (IMCA short video) Working in confined spaces (IMCA short video) 2 Hot work whilst working at height in a confined space – job was stopped What happened Applicable During a site visit to a vessel, it was observed that a Life Saving third-party contractor’s welder was standing on the Rule(s) Bypassing Confined Work Working at wooden platform (the actual height was over 1.80m) Safety Space Authorisation Height Controls inside a confined space (a ballast tank) doing some flame-cutting jobs. No fall protection guards were installed around the worker, not was the worker wearing fall arrest equipment. Welder’s initial position without any fall protection Temporary solution (full body harness attached to the tripod system with inertia reel) The job was stopped immediately and a temporary alternative working method was arranged where the worker wore a full body harness attached to with an inertia reel to a tripod. What went wrong The personnel authorizing these activities – working at height doing hot work within a confined space: ̶ Made no Permit to Work application for hot work nor for working at height nor for working in a confined space; ̶ Did not conduct a review of the risk assessment for the task in hand; Inadequate supervision: there was no proper Control of Work by vessel crew or management at the site before the job started, and no ongoing verification of safe working as the job continued; IMCA Safety Flash 04/24 Page 2 of 6 There was a lack of hazard appreciation and risk perception by the persons involved; it took someone coming in from outside, observing the job, to actually stop it. It was easy to work unsafely: crew members misunderstood differing internal company procedural requirements for working at height; Various hazards were not recognised at all. Had the worker fallen within the tank, protruding metal elements meant that there was high potential for a very serious injury. Actions taken locally Reiteration of importance of thorough Risk Assessment, Permit to Work process, and Control of Work, including regular monitoring; Ensured more robust control of Working at Height activities and prioritized availability of engineering controls (e.g. a scaffolding platform). Members may wish to refer to: Fall from a height into a ballast tank SIMOPS – Smoke from hot work task enters confined space 3 BSEE: Confined space entry – tank cleaning The United States’ Bureau of Safety and Environmental Enforcement (BSEE) has published Applicable Safety Alert 477 relating to working in Confined Spaces. In recent months, BSEE has Life Saving observed a trend of safety incidents that occurred while personnel conducted tank Rule(s) cleaning operations in confined spaces. Confined Space Incident 1: What happened - worker required CPR A worker was vacuuming, and the nozzle became stuck inside the tank. To free the nozzle, the worker - who was wearing a respirator with organic filters specifically used for working outside the tank - fully entered the tank, where he fell ill. Coworkers found the worker inside the tank. Cardiopulmonary Resuscitation (CPR) was administered to revive the worker. What went wrong The crew could and ought to have stopped the job; The company’s existing confined space entry policies were not complied with. Human factors: it was noted that an employee felt compelled to rush, leading to hasty and ill-informed decisions. This haste ultimately led to unauthorized and unplanned entry into the tank, further exacerbating the situation. Actions included Additional refresher training for confined space rescue; Invoking safety stand downs – stop and think! Installing appropriate personnel barriers; Ensuring management meets with supervisors to go over policies and procedures before every job. Incident 2: What happened: worker almost passed out A worker began to feel ill while conducting tank cleaning operations and attempted to exit the tank. While exiting, the worker nearly passed out. The worker initially appeared alert but was slow to answer questions, was sweating profusely, and then collapsed. A coworker revived the worker using CPR. The worker was flown ashore, and medical evaluation showed the worker had nonstress-induced cardiac arrythmia that may have contributed to the episode. IMCA Safety Flash 04/24 Page 3 of 6 Actions The BSEE recommends that operators and their contractors, where appropriate, consider: Ensuring all personnel understand what constitutes a confined space and confined space entry. Ensuring personnel are aware that confined spaces may be hazardous even if part of the body remains outside of the space; Ensuring a Job Safety Analysis (JSA) is in place and is discussed before starting work; Completing, if required, a confined space entry Permit to Work, which should explain the hazards and mitigations common to confined space work; Stopping the job and discussing/analyzing any potential safety and environmental hazards; Renewing approval before proceeding when deviating from the JSA and/or permit – ensuring proper Management of Change; Ensuring proper personal protective equipment (PPE) is worn; Ensuring others know of your planned activities and the duration of the planned activities prior to entering a confined space; Ensuring personnel inside the confined space have means to communicate with personnel outside. Regular communication can be used to detect if the personnel inside have become impaired; Ensuring proper ventilation prior to entering a confined space. If proper ventilation cannot be achieved, utilizing the necessary breathing apparatus; Developing a rescue plan for extracting personnel who are unable to exit a confined space due to injury or incapacitation. Identifying the personnel who will execute the rescue plan and the equipment that will be used; Ensuring employees and/or contractors have the proper training to operate in an enclosed space. Also ensuring the training is current and up to date; Clear marking of storage tanks regarding the substance contained and any associated hazards (flammability, reactivity, health hazards, etc.) - keep Material Safety Data Sheets (MSDS) for all substances found on location in an easily accessible area, including chemicals in the storage tanks. Members may wish to refer to: Hose management and chemicals: crew person felt ill Crew member fainted after working in water ballast tank Worker fainted and was injured during tanker operations in a tropical climate 4 USCG: wire rope hazard management - dropped turbine nacelle The United States Coastguard (USCG) has published Marine Safety Alert 11-23 relating to an incident in which a wire rope parted, causing a wind turbine nacelle weighing 69 tons Applicable to fall 2.2m to deck, causing significant damage and loss of the nacelle. Life Saving Rule(s) Safe What happened Mechanical Lifting A vessel crane was being used to offload the 69 ton wind turbine nacelle. While hoisting, a wire rope parted, causing the load to fall to the deck. No-one was harmed, but the load landed within a metre of working personnel – there was high potential for serious injury. There was significant damage to the vessel and total loss of the cargo. IMCA Safety Flash 04/24 Page 4 of 6 What went wrong The USCG noted that investigation revealed that corrosion, wear, and monotonic ductile overload of the wire rope caused the failure. Further, it was concluded the wire rope was still within its permitted service life but should have been replaced prior to the incident due to the corrosion and wear. The USCG notes that given the potential wear associated with harsh operating environments, it is imperative that vessel operators employ robust inspection and testing to ensure equipment suitability through its lifespan. Recommendations The US Coast Guard strongly recommends that vessels equipped with shipboard cranes: Implement increased load testing frequency to verify wire rope integrity between class society mandated 5-year load tests; Are provided with and utilize pressure lubricating devices as recommended by the manufacturer for routine maintenance; Ensure maintenance tracking systems align with manufacturer’s recommended maintenance protocol, including the period of employment and renewal of wire ropes; Consider shortened periods of employment and early renewal of crane wire ropes to prevent corrosion and fatigue induced failures; Instruct and train all personnel to never position themselves under cargo suspended by any crane, even temporarily; Ensure all shipboard crane operators are properly trained and cognizant of industry best practices; Implement increased wire rope visual inspection frequency; Degrease and remove all lubricant prior to crane wire rope visual inspections to ensure surface defects are not concealed. Members may wish to refer to: IMCA HSSE 022 LR 001 M 194 Recommended practice on wire rope integrity management for vessels in the offshore industry IMCA HSSE019 LR006 M187 D060 Guidelines for lifting operations 5 Vessel damaged in contact with platform What happened A CTV (crew transfer vessel) collided with a fixed platform when one of the engines failed. The CTV was approaching a platform to transfer crew onto it, when there was a failure of control of the port inner main engine, causing it to continue to drive the vessel forward. Whilst control of the engine and hence the vessel was regained before coming into contact with the platform, collision could not be avoided, and there was damage to the starboard side of the wheelhouse. No-one was injured. IMCA Safety Flash 04/24 Page 5 of 6 What went right The vessel crew completed their routine checks and tests prior to operations in the 500 meter zone; The Master made several immediate attempts to regain control including an emergency stop of the port inner main engine; What went wrong The vessel’s port inner main engine got stuck in forward movement as she approached the platform. What was the cause Our member’s investigation discovered that there was a failure of the pitch control propulsion actuator. The response to regain control and time taken to do so, was insufficient to avoid contact; The actuator froze because of worn-out carbon brushes in a motor. There were no OEM or company planned maintenance system recommendations for actuator electric motor maintenance. Actions Checked across fleet for similar actuator motors, then checked carbon brushes within these motors; Amended Planned Maintenance System on relevant vessels to include actuator electric motor maintenance program as specified by manufacturer; A reiteration of the importance of Loss of Power drills. Members may wish to refer to: Machinery breakdown leads to a collision Vessel collision with fixed structure on wind farm Property damage: platform supply vessel collided with legs of jack-up rig IMCA Safety Flash 04/24 Page 6 of 6