Safety & Security Education Guide PDF
Document Details
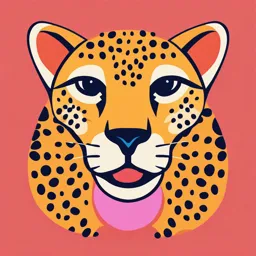
Uploaded by LovedDetroit
null
2023
null
null
Tags
Summary
This document is a guide on safety and security film for the window film industry. It provides an overview of safety film, its history, and its various applications. It also covers different types of glass and glazing systems, as well as testing and installation methods.
Full Transcript
Safety & Security Education Guide 2023 Foreword This Safety Film Education Guide is part of an ongoing education series developed by the IWFA for the window film industry. The guide is not all-inclusive as its focus is primarily on the subject of Safety and Security Film. This Guide does not pur...
Safety & Security Education Guide 2023 Foreword This Safety Film Education Guide is part of an ongoing education series developed by the IWFA for the window film industry. The guide is not all-inclusive as its focus is primarily on the subject of Safety and Security Film. This Guide does not purport to state that any particular type of product should be used in any specific application. The user has the responsibility to ensure that a competent security design professional select and/or install the products in compliance with all applicable laws, rules, regulations, standards, and other requirements. The IWFA does not design, develop, or manufacture any products, processes, or equipment referred to in this Guide and, accordingly, makes no guarantee, representation, or warranty, expressed or implied, as to their fitness, merchantability, patent infringement, or any other matter respecting their performance. The IWFA cannot guarantee and disclaims any responsibility for any specific result relating to the use of this Guide. Introduction Glass is truly an amazing and most useful product. Its presence is seen and felt every day by virtually every individual. Despite its wondrous benefits, however, glass poses a potential risk to human life and property when it breaks. Unfortunately, it is not a matter of “if” a particular piece of glass will break, but more likely “when” it will break! Equally amazing as glass is a product referred to in the industry as Safety Film. It may also be referred to as Security, Protective, Anti-Shatter, or a host of other names. It is a product whose purpose is to mitigate or lessen the harmful consequences of glass that is broken by man or nature. Like glass, Safety Film is optically clear and highly transparent. Safety Film allows visible light to pass through it but unlike glass, it is not brittle and easily subject to “breaking”. In fact, it is considered “elastomeric”, that is, having the ability to stretch. Safety Film is installed (applied) to the interior surface of existing glass using an extremely aggressive pressure sensitive adhesive. The adhesive/film combination helps hold together glass that is broken by some outside event. This Education Guide will briefly trace the history of Safety Film and its growth and evolution. The Guide will serve both to examine numerous man-made and natural events that cause glass to break and to review the basic construction of various film types, current testing methods, and standards used to measure and judge the products attributes. The Guide will explore the comparative merits of Safety Film, laminated, glass, and other glazing and related protective glazing options. The Guide will explore the problems found when some members of the industry exaggerate or distort the capabilities of Safety Film through ignorance and misrepresentative advertising and marketing. Finally, the Guide will highlight the various industry organizations involved with the window film and glazing industries. 1 Safety Film – A Brief Historical Overview The first generation of Safety Film is believed to have been developed in the early 1970’s. The product was developed for the British Government to mitigate the deadly effects of flying and falling glass during the terrorist bombings that were rampant throughout England and Northern Ireland. Due to its success in the field, the product gained broader exposure and awareness leading to greater usage in Europe and other world markets. Safety Film sales in the US were significantly impacted by several events in the late 80’s and into the 90’s which included, Hurricane Hugo and Andrew, the Loma Prieta earthquake in San Francisco, and ‘93 and ‘95 bombings in New York City and Oklahoma City. (Prior to that safety film was used mostly to slow down smash and grab type crimes). These highly publicized headline events awakened government leaders and the general population to the dangers of broken glass during these manmade and natural disasters. These events along with car-jacking dangers in many countries, drove the increasing demand for safety films. In order to fully understand safety film, it is first necessary to learn and understand the nature of glass itself, different types of glass, and the various window types. GLASS AND GLAZING SYSTEMS Float Glass Manufacturing Process Most of the glass used today starts out as float glass. It is manufactured in a continuous process by melting glass batch (soda, lime, silica sand and other materials used for heat absorbing or tinted glass when desired) and floating it on a bath of molten tin. Raw ingredients are weighed and mixed with broken glass (called cullet) into batches. The mixed batch is heated in furnaces (up to 2900o F) into a molten mass, which is then floated onto a tin bath where the ribbon of “float” glass is pulled (or drawn) through the tin float chamber. The glass ribbon then enters an annealing lehr where it is cooled in preparation for cutting. The annealing lehr cools the glass to approximately 200 degrees F in a precise, uniform manner. The lehr uses small amounts of electric heat to keep the edges of the sheet from cooling faster than the center. The ribbon of glass emerges from the lehr and continues through the cooling process to be prepared for cutting, packing, and shipping. Annealed glass is the predominant base product used to fabricate all other types of architectural and automotive glass. Types of Glass It is important to have a basic understanding of the different types of glass and their vulnerability to stress. There are essentially four types of glass categorized by the amount of heat and cooling using in the manufacturing process. Annealed Float Glass Heat-Treated Glass Tempered Glass Chemically Strengthened Glass Generally speaking, a higher temperature coupled with a more rapid cooling rate in the production process will produce glass that is stronger and more resistant to breaking. Annealed Float Glass is manufactured in the process described above. The molten glass tends to seek a level of configuration as it floats on the surface of the molten tin. The thickness is relative to the rate at 2 which the molten glass flows from the tank. If the flow rate is slowed down, the glass thickness builds up. Because the melting point of tin is much less than that of glass, the glass solidifies as it cools on top of the tin. Once the glass solidifies, it is fed into an annealing oven where it is slowly cooled so that the residual stresses are minimized. This results in a glass product which is very flat with nearly distortion- free, parallel surfaces. Since annealed glass has a minimum amount of residual surface compression, it is subject to easy breakage. However, it is the most common type of glass found and with the exception noted below in the tempered glass section, it is the most prevalent glass found in residential architecture. Its great popularity is attributed to its lower cost of production, inventory flexibility in window manufacturing, and ability to be easily cut (on-site if necessary) to fit any glazing unit. When annealed glass breaks, it does so in many small and large sharp, irregular-shaped pieces or shards. Depending on the cause of the glass breakage, these jagged pieces of glass can be propelled at high speeds and can produce serious bodily injuries and even death. Heat-Treated Glass is more resistant to breakage. In the production process the glass is only heated to about 1150 degrees F and is cooled more slowly. The results are a product that has a compressed outer surface with compensating inner tension. This type of glass has less bow and warp than tempered glass (described below) but only has a strength factor of about twice annealed glass. Although heat treated (also called heat-strengthened) glass is more resistant to heat induced stress, other types of stress do not show the same improvement over annealed glass. For those reasons, it is not considered a fire-resistant glazing, nor is it accepted as a safety glazing product as it breaks in a similar manner to regular annealed glass. Tempered Glass is a type of glass that is the result of heating and rapid cooling to induce a change in structure leading to an increase in strength. Single sheets of annealed glass are heated to temperatures around 1200 degrees F. This is the temperature at which annealed glass begins to soften. The outer surfaces of the glass are then rapidly cooled. This creates high compression in the surfaces. Once the glass is tempered it can no longer be cut to another size. This type of glass is about four times stronger than regular annealed glass. The change in structure has two main benefits. First, the glass is much stronger. Second, when the glass is broken, it breaks into small cubical pieces as opposed to the larger sharp shards created by annealed glass. This is a major benefit in areas that are high risk for accidental glass breakage. It should be noted that tempered glass is often referred to as Safety Glass. This name originates from the mid 70’s when US Federal and State governments mandated such glass be used in public spaces for safety. This legislation was initially targeted at preventing what is termed “accidental glass breakage”, i.e. people walking or falling into or through glass doors, glass next to doors, floor to ceiling windows, and heavy pedestrian walkways. While the tempered glass may not prevent the glass from breaking the break pattern of tempered glass greatly minimized the chance of serious injury due to cuts from annealed or heat-strengthened glass. Chemically Strengthened Glass is produced when glass is submerged in a molten salt bath at temperatures below normal annealing. This results in an exchange of ions at the surface of the glass. This is a complex process beyond the scope of this document. 3 Chemically strengthened glass has similar compressive strength to heat treated glass. The product is generally not used for window glass but is more commonly seen in industries where very thin, strong glass is needed. When broken, this glass has similar breakage patterns to annealed glass and is therefore not generally recommended for safety glazing. Glass Breakage No discussion of glass is complete without discussing how and why it breaks. Glass can break for any number of reasons associated with either pressures on the glass or direct impact to the surface from objects. They include: Human Impact – An adult or child running into or falling into a piece of glass. Forced entry – Breakage resulting from attempted illegal entry through glass. Windstorm – Breakage from flying objects or pressures associated with windstorms. Earthquake – Breakage from the racking motion created during an earthquake. Blast – Breakage resulting from the pressure wave of an explosion. Nickel-sulfide inclusions – Tempered glass breakage from a glass contaminant. Thermal breakage- Cracking associated with edge stresses caused by heat. Tensile stress – Stress from the weight of the glass in relationship to the building spec and design. Tensile stress from the weight of the glass is a building design issue and not generally considered a possible reason for the application of safety film. Each of the other glass breakage events will be discussed in later sections. WINDOW CONSTRUCTIONS The three major types of glass previously described are found in six broad categories of window constructions: Monolithic Glass windows (Single pane) Insulated Glass windows (dual or triple pane) Laminated Glass windows Ballistic Glass windows Blast resistant Glass windows Other types Monolithic Glass is the simplest window construction type. It consists of a single flat piece of glass. The glass can vary in thickness and can be annealed, heat-treated, or laminated. Most glass in use today is annealed. The glass is usually 1/8” (3mm) for residential and ¼” (6mm) for commercial. Insulated Glass consists of two panes of glass and a spacer fabricated into a sealed insulated glass unit (IGU). The spacer creates an airgap of constant thickness. The purpose of the airgap is to reduce heat transfer by conduction and convection through the glass unit. (Refer to the architectural training guides for more information about heat transfer). The glass panes are generally clear, annealed glass but often have coatings to improve solar properties. 4 Laminated Glass features two layers of annealed or tempered glass bonded together by an interlayer of polyvinyl butyral (PVB). The bonding process uses heat and pressure that is produced by drawing a vacuum in an autoclave. The surface of the PVB is slightly roughened and the autoclave provides a pressure that eliminates any air between the glass and the PVB at the same time creating pressure for the bonding process. Laminated glass is used in automotive and residential glazing systems for increased safety and security. Compared to tempered glass, laminated glass is used less frequently because of increased cost. Its most significant benefit is its ability to maintain structural integrity even after it is broken. Thus, it usually remains in the opening to protect against exposure to the elements and unauthorized entry. An additional benefit of laminated glass is its ability as a noise reduction glazing. Bullet and Blast Resistant Glass is normally comprised of multiple laminates of glass and polycarbonate. Often the glass is thicker than a normal windowpane as well. This glass tends to require special framing due to thickness and weight and is expensive due to the framing and lamination process complexity. Other Glass Types can sometimes be encountered in the marketplace such as wired, textured, and patterned glass. Each of these were developed for special uses and require special handling. Please contact the manufacturer for more information on these glass types. SAFETY FILM CONSTRUCTION Safety Film is probably best described by two names given to it by the U.S. Government, glass fragment retention film and anti-shatter film. The U.S. Army Corps of Engineers and the General Services Administration (GSA) developed these names to describe the ability of Safety Film to hold glass together in the event it is broken. Safety Film is comprised of optically clear, tinted, or reflective layers of polyester film. Most of the discussion in this guide will deal with clear safety film. Higher solar performance versions of safety film are available and from a safety standpoint work in the same way as the clear versions. However, the majority of safety film sold today is clear. For more information on how high-performance window films work and their impact on solar performance and glass interactions please check out the Flat Glass Education Guide and the Advanced Flat Glass Education Guide. Safety film is usually described in terms of its thickness. Depending on the country of use this thickness is described in “mils”, each being equal to one-thousandth of an inch, or in microns, each being equal to one-ten thousandth of a meter. One mil equals 25.4 microns. Safety film ranges in thickness from 4 mils (100 microns) to 15 mils and occasionally thicker. The varying thickness is achieved by using different thickness of polyester film or laminating multiple layers of film together in a factory setting with a pressure sensitive adhesive. The material is packaged in rolls of varying lengths and widths with the upper width usually topping out at 72” although occasionally wider films may be available. Standard available sizes are 36”, 48”, 60”, and 72” widths with lengths normally available at 100’. Some very thick films come in shorter lengths due to shipping and handling weight restrictions. Safety film is usually “retrofitted” to existing glass with the window frames already structurally in place. Occasionally, the film is applied on new glass before the glass has been installed. Typical film installations cover the visible portion of the interior surface of the glass all the way to the edge of the frame, but do not extend to the glass edge within the frame. This installation is referred to as a 5 “daylight installation”. The protective performance level of Safety Film can be enhanced through installation techniques that attach the film to the framing system. This will be discussed later in the guide. When properly installed, Safety Film forms an almost invisible protective coating on the interior side of the glass surface. The film is attached to the glass with an extremely aggressive pressure sensitive adhesive. This adhesive is applied to the film at the time of manufacture and is protected by a release liner until installed. When stress causes the glass to break, the film can stretch and absorb some or all the energy generated by the stress. The result is that the broken glass may remain intact within the framing system preventing shards of glass from becoming lethal projectiles. If the stress on the glass is too great, as in the case of an extreme explosion, the film will be stretched to its maximum at which point it may tear and burst. However, potential personal injury is significantly reduced because the film will reduce the amount of glass shards produced and the velocity and distance that they are propelled. The film also will allow a portion of the destructive blast shock wave to dissipate (prior to the glass and film failing), substantially reducing damage and life-threatening injuries. Basic Construction of CLEAR Safety Film Clear Safety film is manufactured with single or multiple layers of clear polyester film laminated together in a variety of constructions. For example, a 4-mil film is laminated to a 4-mil film to produce an 8-mil film, or three separate 4-mil films can be laminated to form a 12-mil film. Generally speaking, the more layers or plies that a particular safety film constructions contains, the greater its ability to uniformly absorb impact energy when the glass is broken until the film reaches its actual burst strength. Such a film has a higher manufacturing cost, as each layer requires a separate production pass through the coating and laminating equipment. The strength of polyester film is often described by its tear strength and tensile strength. A simple definition of these two characteristics is the force necessary to tear the film either with or without an initial cut and the force necessary to pull a strip of film into two separate pieces. The force at which the film comes apart is called the break strength. It is also possible to perform these tests on a manufactured sample of safety film which includes the adhesive and multiple layers of polyester if applicable. None of these tests simulate the effectiveness of a safety film in an actual event. It is strongly recommended that performance tests be used instead of physical characteristic tests when specifying safety film for a particular application. Most clear safety films contain ultraviolet (UV) absorbers in the adhesive layers. These UV absorbers are used to prevent the sun’s rays from degrading the polyester film and the adhesive itself. Some clear safety films also use polyester films with UV absorbers impregnated in the film itself. The UV absorbers have the added benefit of helping to provide some protection against fading of interior furnishings and fabrics as UV is considered the most significant contributor to fading. It is important to always be clear with consumers that: NO WINDOW FILM OR GLAZING PRODUCT WILL TOTALLY PREVENT OR STOP FADING. (For an in-depth discussion on the benefits of UV protection for people and surfaces please refer to the Flat Glass and Advanced Flat Glass Education guides.) 6 Safety film is almost always applied to the interior side of the glass surface by means of an aggressive adhesive coating. A thin protective “release” liner that is removed before the film is installed on the window protects the adhesive coating. Safety Films use a Pressure Sensitive (PS) acrylic adhesive system to bond the film to the glass. A scratch resistant protective coating is usually applied to the film’s exposed room side surface. 7 Safety Film Adhesives Safety films often use a different adhesive to laminate the layers together than the adhesive used to hold the film to the glass. This is not a hard and fast rule and safety films exist that use the installation adhesive to laminate the layers together. The installation adhesives used for safety films do however differ significantly from the installation adhesives often used in standard architectural films. Safety film adhesives are designed to hold glass in place and keep the glass adhered to the film. Standard film adhesives are designed to just hold the film to the glass and as such are not designed to take the impact normally associated with safety films. The strength of the adhesive is measured by its peel and shear strength which is tested according to ASTM standards and listed by most manufacturers on the specification sheets associated with safety films. Adhesive strength tests are conducted after the adhesive has had time to dry and cure after installation. The cure time should be listed in the test report. See diagram below for the differences between different angle of peel strength tests. Note the angle that the film is pulled away from the glass changes based on the test method and the thickness of the film. This change in angle can significantly impact the “peel strength” leading to the assumption that the peel strength of a thick film is different than a thin film when the adhesive strength is the same. Additionally, it is very difficult to test a piece of safety film once it is installed on an actual window and the adhesive has cured. Various “in situ” test methods have been tried, most of which involve hanging a weight from the end of a film strip cut in the installed film, bending the film back 180 degrees, letting a weight hang and then measuring the time it takes for the film to travel (peel) a certain distance. There are several variables that are not controlled in this type of test, including the temperature of the specimen and the speed of the pull. While some have used this as a pass/fail type test, IWFA strongly recommends the use of a standard test method in controlled conditions to determine the peel strength of an adhesive. See diagram below showing a shear strength test. Note the film is being pulled down the surface of the glass instead of being pulled away from the glass surface. 8 Ideally, the performance of a safety film should be determined by a test that simulates the actual event trying to be mitigated instead of typical physical properties like peel, film thickness, or tensile strength. For a listing of the IWFA guideline physical test methods and guidance on the proper reporting of these tests please see appendix A. Exterior Safety Film While some exterior safety films exist, the dynamics of how film performs when installed on the exterior surface of a glazing system is outside the scope of this training guide. For more information on this subject please see the manufacturer offering this type of product and be aware that the longevity issues of an exterior safety film when compared to an exterior solar films are quite different. The solar film is only required to stay on the glass, while a safety film is often required to main its physical film integrity. Solar Safety Film It is possible to achieve both the protective benefits of a safety film and the solar performance benefits of a solar control film in the same product. These films come in a variety of light transmissions and performance levels based on construction. The film construction is similar to Clear Safety film but with the added performance layers found in solar control films. Below is an example of a solar safety film construction featuring a metallized layer. 9 From a sales and marketing perspective Solar Safety Film represent an opportunity for increased profits as they typically demand higher prices, and the same installation achieves added benefits. Clear safety films offer the benefits of Safety Protection and some amount of UV protection, but depending on the building size orientation, solar safety films can also provide extra benefits. Heat Control Enhance fade deterrence Reduced energy costs Glare reduction Increased privacy Increased comfort and working conditions Improved building appearance Glass Breakage from Thermal Stress Glass breakage from thermal stress is a result of uneven temperature distribution across the surface of the glass lite. An example of uneven temperature distribution can be found when a cold, east facing window is suddenly heated on a sunny winter morning. The center of the glass heats more quickly than the shaded edges of the glass under the frame. This heat difference causes stresses at the edge of the glass causing it to crack. This type of heat differential can also occur if the window has uneven shading from overhangs or other exterior shading. These types of thermal breaks will generally show as a short 10 crack perpendicular to the edge of the glass that then extends in a diagonal jagged line into the rest of the glass pane. The application of Clear safety film should have little if any impact in creating thermal stress fractures. However, caution should be observed in applying solar safety films. Most window film manufacturers issue “Film To Glass Application Guidelines” to assist dealers in evaluating their particular circumstances. It is strongly recommended that the student study the Flat Glass Education Guide and the Advanced Flat Glass Education Guide if they are planning on using Solar Safety films. The depth of knowledge necessary to sell and safely install solar films is outside the scope of this guide. GENERAL IWFA TESTING GUIDELINES The industry standard testing methods described in this document are incorporated by reference into the IWFA False Advertising Policy. Any product or advertising claims supported by legitimate and replicable tests using these methods will be deemed to comply with the IWFA’s Policy against misleading advertising. Any product or advertising claims purportedly supported by other testing methods will be deemed to violate the Policy against misleading advertising, unless the party making the claim can substantiate by showing the particular testing method to be reputable and performed in a reliable manner. For product or advertising claims to be considered fairly and credibly supported by testing conducted in accordance with the Endorsed Standards and therefore considered compliant with the IWFA’s False Advertising Policy, the party making the particular product or advertising claims must adhere to the following guidelines: With regard to any testing with respect to which film is applied to glass, the glass thickness and glass type must be disclosed in the product or advertising claim. Testing results incorporated into the product or advertising claim must be reported in the units specified in the test method or an equivalent unit conversion. The testing that supports that particular product or advertising claim must have been conducted on the product that actually is being sold and which is the focus of the particular claim. For example, the tensile strength of a product must be the actual window film, not just the polyester used to produce the window film. If pass/fail criteria are written into the relevant standard, the product must achieve a pass to be used as substantiation of a claim. If the standard lists several levels of acceptance, the level achieved must be reported as well. Statements like “tested to XXXX test method” under circumstances in which the product does not pass the stated test are not acceptable. If making a comparison claim about an installed window film compared to a window without the product, testing must be conducted on both the window without film and the installed film and both test reports should be made available to the public from a readily accessible source. Any safety claims must be backed up with a recognized standard test method from a recognized standard setting organization and that test method and results must be made available to the public from a readily accessible source. Substantiation of claims made using glass types or thicknesses rarely found in typical buildings or homes will be considered misleading. Care should also be taken with extremely large windows, especially if the window is larger than the specimen size used in the test. 11 Violating IWFA’s False Advertising Policy could result in suspension or termination of a member’s IWFA membership and denial of membership applications for those that engage in practices inconsistent with the Policy prior to applying for membership. A listing of endorsed industry testing standards can be found in Appendix A of this training guide and on-line at iwfa.com/guidelines. BASIC SAFETY TEST STANDARDS Safety film requirements and performance should be described by the films ability to pass a standard test created to simulate the force or impact protection benefit desired. While other physical properties such as thickness, tensile strength, or peel strength may be found in specifier documents or specification sheets, safety film should not be specified or sold based solely on those properties. Tests specifically designed to test for the films ability to withstand the specified situation and force are always the preferred documentation of performance. Because safety and security films often deal with life safety issues it is particularly important that claims be substantiated using testing methods from recognized standard setting organizations. Safety standards often have several levels of acceptance. To comply with IWFA’s False Advertising Policy, safety claims must be substantiated by listing the level of standard achieved, not the level tested. The following sections describe various known test standards from recognized national or international organizations. Other test standards from individual countries may apply in specific countries or regions. As stated previously, there are many situations in which safety film (depending on the installation method) can provide some level of protection from flying glass shards, falling glass, or intrusion through the glass itself. Each of these types of situations and the tests designed to simulate them are described in the sections below. Human Impact – ANSI Z97.1 Injuries from glass breakage have always been a major concern for people since the first glass panes were produced. This concern was heightened in the early days of the automotive industry leading to the development and gradual introduction of tempered and laminated glass for side windows and the windscreen respectively. Attention was slower to come to the residential and commercial markets. Concern for public safety in high pedestrian traffic areas, prompted the US Government to initiate legislative action in the early 1970’s to establish commercial building codes requiring the installation of tempered glass in glazing systems exposed to high injury risks. These include doors of all types, windows close to the floor or floor to ceiling, glass partition, etc. Later, such codes extended installation of safety glass to include residential buildings as well where the codes cited: Storm doors or combination doors Entry doors and sidelights (glass immediately adjacent to doors) Bathtub and Shower doors and enclosures Sliding glass doors 12 The safety requirements are designed to reduce or eliminate unreasonable risks of death or serious injury to consumers when the glass is broken by human impact. These Human Impact tests were developed by the federal government and then adopted by the American National Standards Institute in 1984 and are know by their number, ANSI Z97.1 The test standard attempts to simulate the effects of a certain size and weight individual walking through a piece of glass roughly the size of a standard sliding glass door (34” x 76”). The test involves releasing a swinging leather bag filled with 100 pounds of lead shot from a height of 12” perpendicular to the center of a pane of glass mounted in a stationary frame. This creates the equivalent of 100 foot- pounds of impact per square foot. This is a Pass/Fail type test. If the glass breaks, the leather bag cannot create an opening bigger than a three-inch steel ball can pass through, for the panel to be given a Pass. Four individual successive panels must meet this requirement for an official Class C Pass to be recorded for the glazing system. If the specimen does not fail, then four more panels are tested at a height of 18”. This level would be considered a 150-foot-pound Pass or Class B. If these specimens do not fail, then four more panels can be tested at a 48” drop height. This level represents a 400-foot- pound impact or Class A. Human Impact -CPSC CFR 1201 Category I and II The Consumer Product Safety Commission developed a test standard similar to ANSI. This test standard was referred to as CPSC CFR 1201. In 2015, this test standard was changed to incorporate the ANSI test method. The same testing apparatus is used but while the ANSI test has three levels of performance the CPSC only has two. Category I is equivalent to Class B and Category II is equivalent to Class A. A simplified drawing of the testing apparatus is shown below. 13 Windstorm Events The destructive power of Hurricane Andrew in 1992 caused in excess of $45 billion in storm damage costs and led to serious investigations and studies. These studies highlighted significant shortcomings in the Southern Florida residential building inventory. Weak building codes, lax enforcement of the existing codes, poor construction design, and shoddy workmanship all played a part in creating a situation where the forces of wind and water easily compromised the structural integrity of thousands of homes and small businesses. Broken windows and doors played a key role in allowing differential atmospheric pressure between the exterior and interior of buildings to, in effect raise roofs and collapse walls. The phenomenon was most noted in two story homes versus one-story homes and homes with gable roofs versus homes with a hip roof design. This was probably due to a combination of how the wind traveled across the surface of this roof type and how the roof was attached to the rest of the house. This phenomenon illustrates the importance of understanding all the factors in play during a windstorm event and explains why windstorm testing requires an integrated approach. The challenge of how to protect buildings from damage during a hurricane or other severe windstorm is very complex, causing disagreement even among experts. There are several dynamics involved. For example, a glazing system must withstand the pressure of high winds against the glazing surface. This is referred to as wind-load. Generally speaking, glass fitted with safety film is capable of withstanding high wind loads. In a hurricane however, wind pressures are not constant. The pressure on the glazing system will alternately ‘push” and “pull” the unit inward and outward. This type of loading is referred to as cyclic loading. Again, safety film generally performs well in this type of loading situation. However, the constant back and forth movement exerts tremendous pressure on the framing system often leading to failure. In advertising and promoting safety film dealers may create potential legal liabilities for themselves as well as the industry by over-selling the benefits of safety film or using phrases such as 14 “hurricane protection” or “hurricane proof”. Even using the word hurricane or showing pictures of hurricanes can be problematic in some regions. The most difficult challenge in windstorms is protecting against window breakage from wind-borne debris. Significant time, effort, and dollars have been spent in studying this variable and attempting to determine an appropriate test or series of tests to simulate what is likely to happen in a windstorm and then to determine what is a reasonable level of protection to help mitigate the risk during a windstorm event. Some areas which have been historically hit hard such as coastal Florida and Texas adopted very conservative and prescriptive codes designed to mitigate building damage during the most extreme and less likely windstorm. These codes apply to new construction and anytime buildings are changed enough to require the building to be brought up to existing codes. These are integrated codes which require not just a glazing to pass a simulated debris impact test but also require the glazing, frame and the system that attaches the frame to the building envelope to be tested as a total system through a very grueling series of tests. One of the most well-known of these type of total system tests is called the Dade County Protocol. Dade County Protocol Dade County Florida, one of the most populous and largest counties in Southern Florida was significantly impacted by the Category 4 Hurricane Andrew. After the event, the Metro Dade County Building Code Task Force was formed to survey and investigate the damage caused by the hurricane. Besides water damage which is always a large contributor to hurricane damage on the coast, homes further inland were also significantly damaged due to wind. Studies were conducted to determine why so many buildings failed, and to provide more rigorous testing and evaluation procedures to enhance the performance of hurricane-resistant building materials, particularly glazing systems. Investigations identified the loss of windows, doors, and roofing materials as a major contributing factor in the destruction of commercial and residential dwellings during the hurricane. The reason was simple to understand. When windows and doors failed, the integrity of the building envelope was breached, producing intense internal pressurization of the structure. This pressurization often led to a complete collapse of the walls and roof of the building. The main culprit causing the breach in the building “envelope” was found to be wind-borne debris. The debris would strike and shatter the glazing system allowing wind (and water) to enter, thus causing the destructive internal pressurization to occur. This formed a cause-and-effect circular event. The more the buildings in a neighborhood collapsed, the more debris was created, causing more glazing systems to fail and more roofs to collapse. In recognition of this wind-borne debris problem, Dade County adopted tough new building standards. In essence, the new code required that every exterior opening in a newly constructed house or business be protected against flying debris propelled by hurricane force winds. Other counties in Southern Florida soon followed suit and other states or state sponsored insurance programs adopted similar codes and test standards. The Dade County Protocol consists of an impact test and a pressure test. The impact test uses two different debris types which are called “missiles”. The large missile is a 9 lbs, 2” x 4” piece of building lumber launched from an air cannon to achieve 34 mph (50 ft/second) speed at the point of impact. A 15 pass of the impact portion of the test requires three glazing system samples to survive two impacts each – one in the center and one in a corner- without penetration. This debris size is designated for any window opening 30 feet or less from ground level. A second impact missile was chosen for any window opening above 30 feet from ground level because it was assumed that even at hurricane windspeed, large objects were unlikely to be traveling at high speed over 30’ in the air. These test missiles were intended to represent roof debris weighing two grams moving at 130 ft/second (over 80 mph). Steel ball bearings are used to maintain sample size and weight. As with the large missile the test requires three glazing system samples to survive with no penetration, but the impact is 10 missiles in a group, impacting the samples at three spots – the center, at the edge and near a corner for a total of 30 missiles. If the glazing system specimen survives the impact phase of the test, then the specimens are subjected to the pressure testing portion of the standard. Hurricane winds don’t blow at a constant rate, so this test simulates hurricane force loading at 9000 wind cycles, where each cycle is a function of the maximum wind speed (converted to pressure) for which the product will be “rated”. To pass, the specimens must remain in their frame and have no tear or crack longer than five inches and wider than 1/16 of an inch through which air can pass. In addition, weathering tests are conducted on all the glazing materials used in the system to assess how the materials can be expected to perform in a storm many years after installation in a building. Water leakage is also performed on the specimens. Safety film on standard glazing is not an approved hurricane mitigation solution according to this protocol for residential use as no known film can survive the large missile impact testing. Additionally, no glazing product on its own can be considered to be a hurricane mitigation solution as the complete glazing system of frame and attachment must be tested. There was considerable confusion around this test standard and the actual code when it was introduced. The reader may still find reference to this testing standard associated with window film, but it is imperative that no one claims that a safety film passes the Dade County Protocol since film by itself cannot be tested and given a pass or fail. References might list a film on a particular glass type “passes” the small missile test, but this is not mean the film “meets” Dade County Protocol. Further hurricanes such as Katrina ($100B) and Wilma ($20B) in 2005 and Sandy ($65B) in 2012 allowed research to continue on windstorms and ASTM test methods were developed based on this additional information. Today the most common test methods in windstorm applications are: ASTM E1886: Standard Test Method for Performance of Exterior Windows, Curtain Walls, Doors, and Impact Protective Systems Impacted by Missile(s) and Exposed to Cyclic Pressure and, ASTM E1996: Standard Specifications for Performance of Exterior Windows, Curtain Walls, Doors, and Impact Protective Systems Impacted by Windborne Debris in Hurricanes. ASTM E1886 introduced a smaller large missile option which was half the weight of the Dade County missile at 4.5 lbs. This was added after research indicated that there was less than a 5% chance of a missile the size used in the Dade County test impacting a window in the non-coastal 110mph or less wind zones. 16 The most recent Florida Building Code (FBC) states that any product, must be tested and approved per FBC Section 1609.1.4. This section states that windows (glazed openings) and doors with windows shall be impact resistant (such as certain types and thicknesses of laminated glass or glass/plastic laminate combinations) or shall be protected with an impact resistant covering (such as impact shutters or other approved products) meeting the impact and cyclic wind load testing of any one of the following approved test methods: SSTD 12-99 ASTM E1886 and ASTM E1996 Miami-Dade TAS 201,202, and 203 Each of these has a standard for a large missile (9lbs) and small missile (2 grams) test and each missile test is followed by a series of over 4000 positive and negative pressure cycles. (It is important to note that some of the test methods also have a reduced Large Missile Test consisting of a 4(4.5?) 2” X 4” which may apply based on wind speed zones and wind-borne debris zones and building category. Hopefully it is now becoming clear why IWFA cannot offer any recommendations on the use of safety window film in regions where codes have been adopted referencing the large missile impact portion of these tests. Codes are set for various regions based on design wind speed charts, designated wind-borne debris regions, distance from the mean high-water line, and building category. It is outside the scope of this document to educate the reader on the details of each of these requirements as they differ significantly by state and county adoption of codes and the revision year of the code currently enacted in that state. Examples of each type of requirement are shown below but remember, these charts and definitions often change every code cycle and keeping current with what each state or locations current requirements is best left to building inspectors and the engineers that design and sign-off on meeting the current code. Building Category Building codes designate buildings into categories designed to assign risk to human life and critical infrastructure. For the most part residences fall into Category II but a code official would make the official designation. A copy of Table 1604.5 from the International Building Code can be found in Appendix C. Wind Speed Diagram X is a map of the Eastern and Southern coastal areas highlighting the differences between the 2016 version of the wind speed charts and the 2022 version. This chart can be found at fema.gov along with extensive information about hurricanes. Wind speed maps mostly follow the contour of the coast but are often updated both up and down in windspeed depending on the latest data. The 2022 map for example showed a decrease in wind speed for the coastal and interior part of the far northeast region. 17 Wind-borne debris regions In addition to the wind speed charts codes will also specify regions as those required to meet impact requirements. Below is a diagram depicting the wind-borne debris region of Florida. Remember, these codes are updated periodically and subject to change. Florida building code wind-borne debris maps are 18 available on the Florida building code site. 19 20 In addition, Florida has a designated High Velocity Hurricane Zones (HVHZ) which has even stricter code standards both for performance and for engineering oversight of glazing design and installation. As of the writing of this manual, IWFA is not aware of any safety window film that has successfully passed the Large Missile (9 lbs) Impact Test followed by the cyclic loading when applied to glass and frame types in existing windows which do not already meet the FBC. Most window film, including safety window film is installed as a retrofit product and as such is very often not covered under new construction codes. However, many states also now require that homes in high wind speed and wind-borne debris regions must have storm protection to obtain state backed homeowners’ insurance. Several safety film products have passed the small missile and cyclic loading test, which applies in all glazing found 30’ or more above grade. Again, in most cases it is required that the total glazing system by tested in order claim a “pass” of the testing standard used. Additionally, some films installed in specific installation configurations, which include attachments to the framing or other considerations, have met the smaller “large missile”. Many existing homes in lower wind speed areas may benefit from the use of safety film. It may be particularly useful to those part-time residents who are not available or capable of installing removable type shutter or prefer a solution with better aesthetics, lower installation costs, and does not eliminate desirable outside lighting when implemented. Any claim by a seller that their products have met any impact test, including human impact in hazardous locations, should alert the consumer to ask for a copy of the actual written approval for the specific product in question if the consumer is seeking the code-approved protection level. A complete consumer public statement related to windstorm protection from safety film can be found at iwfa.com. Earthquake Events (should we call this Seismic?) While considerable attention in building codes and standards has been focused on the design of architectural glazing to withstand windstorm damage, considerably less has been focused on seismic or earthquake activities. Perhaps this is due to the more limited area and frequency over the past 10 years of earthquake events. Most of the focus is on the design and engineering of new commercial buildings with much of the work focused on curtainwall and large commercial storefronts. Not surprisingly the amount of attention and money invested in this type of research is directly related to the location and timing of the events. The original seismic testing standards were developed in Japan and are still in use today (JIS A5759). After the California earthquakes work was completed which eventually led to the following test methods: AAMA 501.4B AAMA 501.6 21 ASCE 7-10, 13.5.4 and 13.5.9 The major cause of glass breakage in a seismic event is movement of the glass in relationship to the frame and building. Most glazing tests today utilize dynamic racking to simulate the movement of the glazing in a seismic event. Dynamic racking tests are performed at various frequencies and include in- plane, out-of-plane and torsional motions. The tests called “crescendo tests” because of their progressively increasing racking amplitudes at a constant frequency, produce distinct and repeatable results in identifying in-plane drift magnitudes associated with predefined seismic limit states for architectural glass. Crescendo tests were initially preformed on architectural glass commonly employed in storefront wall systems. A subsequent series of tests were conducted on a variety of glass commonly employed in curtain wall systems used on mid-rise buildings. It should be noted that the overall performance level of the total glazing system is affected by three elements; 1) the type of glass, 2) the wall framing system, and 3) the silicone structural glazing used. The original tests were designed to investigate and measure the breakage and fallout behavior of various types of glass. Only a 4 mil, un-anchored film was included in the original test program. The tests established the following two broad performance definitions: 1) serviceability drift limit (SDL) and 2) “ultimate drift limit (UDL). SDL is defined as the drift that causes glass to become crushed and cracked ( a condition that would necessitate glass replacement but no other risk). UDL is defined as drift that causes the glass to fall out (a condition that would pose serious life hazard to building occupants and pedestrians). Test results indicate that thicker heat-strengthened glass panels and laminated glass panels were found to be resistant to a higher SDL. Laminated glass exhibited the highest fallout resistance of any glass tested. The 4 mil safety film provided similar SDL improvement as thicker heat-strengthened glass and improved the UDL but not to the level of laminated glass when installed in an unanchored manner. Studies of actual glass failures in real buildings during an earthquake have shown the following observations. Buildings with complex or irregular configurations show almost twice the structural and serious glass breakage as those with regular configurations. Smaller window glass areas receive less serious damage than larger glass areas. Vertical glass shapes receive almost twice the damage as horizontal or square shapes. More flexible glazing systems receive twice as much serious glass damage as more rigid systems. Buildings that are adjoined by other buildings 25 to 75 percent as high receive twice as much serious glass damage as buildings with much lower or higher adjoining buildings, due to pounding between buildings. Subsequently, the IWFA completed their own research testing which confirmed the findings of the original testing. In addition, the testing included anchored system which were shown to provide a significant improvement is glass retention (low fallout) when anchored from the top of the window. 22 Most new construction seismic codes are focused on the sealant used, the edges of the glass (rounded corners) and other structural factors to improve both the SDL and the UDL in new construction. Safety window film may provide improvements in both SDL and UDL when used in existing buildings where replacing all the windows is neither possible nor cost effective. Consult a manufacturer for testing available on seismic racking. Blast Events Blast events fall into two categories: 1) industrial accidents, and 2) acts of terrorism. While accidental industrial blasts are not common, they do occur and safety window film my be used to protect employees from flying glass, especially in older factories and offices around factory buildings. These explosions are most usually the results of an out-of-control chemical reaction due to a processing fault or storage problem. These types have become increasingly infrequent in most developed countries with government enforced safety standards. Blast associated with acts of terrorism can be the result of a single individual or an organized on-going effort to disrupt the lives and government of a country. The significant use of safety film for protection against flying glass started in the UK during the IRA terrorist bombings in the early 1990s when the attacks became more deadly and increasing in number. British directives on the use of safety film to help secure government and other important buildings helped increase the use of safety film. Many privately held companies that were in adjacent areas to government buildings also enacted strategies to try and protect both personnel and interior furnishings and computers. In the US, the bombing of the A.P. Murrah building in Oklahoma City, which resulted in 168 deaths, including young children in the associated daycare center, was the first bombing to cause the US to develop directives around terrorist blast protection. After the 1995 bombing, an Executive Order was issued to assess the vulnerability of federal office buildings to acts of terrorism. Prior to this study there were no government-wide standards for security at federal facilities and no central database of the security currently in place at any of these buildings. The Executive Order created a special committee which was given 60 days to: 1) Survey the state of existing security 2) Establish recommended minimum security standards based on levels of risk. The findings and recommendations of that report were exhaustive and since that time the security of buildings has continued to be enhanced. Injuries and deaths from bomb blasts have long been attributed to the hazardous breaking of glass, not only at or near the immediate point of the blast but also significantly removed from the site. Even prior to 1995, the State Department had used safety film at certain embassies and other overseas buildings for protection. The General Services Agency (GSA), the US governmental arm generally responsible for establishing performance criteria for products purchased and used by the government has created criteria for use of safety film in existing buildings based on risk criteria and has also studied laminated glass and other forms of protection for existing and new construction. The US Army Corps of Engineers and other military organizations also have criteria for the use of safety window film. The dealer may still find many of these criteria and standards still referenced although they have been replaced for the most part. Let’s examine the various types of blast testing. 23 Open Frame Testing This method consisted of placing two panes of glass side by side mounted in rigid frames with no enclosure behind them. One of the panes was coated with safety film and the other did not have any coating. The windowpanes were usually standard annealed or occasionally tempered glass. An explosive charge was detonated near the two specimens. The size of the charge was designed to shatter the glass. In most instances the glass with the safety film remained intact it the frame, holding the glass together or blew totally out of the frame as one large glass “blanket” with the film attached. The unprotected glass would shatter and be blown into a large arc of jagged pieces of glass over a large area. Often these Open Frame Tests were not conducted in conjunction with official independent laboratories, but rather in metropolitan markets with local police or fire and often the media invited. While the video made good copy, there was no standard and the size of the glass, size of the charge, distance of the specimen from the charge and other variables were not controlled. From an engineer’s perspective this form of testing was only anecdotal in nature and was not considered valid. Shock Tube Testing In this test procedure a special shock tube directs a simulated bomb blast positive pressure-impulse wave of specified magnitude against a glazing system. The positive pressure-impulse against an untreated glazing system (either annealed or tempered glass) will cause the glass to explode into an enclosed room built behind the glazing system. The enclosure is a specified size and shape. The back wall of the enclosure is fitted with a “witness panel”. Glass from the untreated glazing system will imbed itself into the panel during the pressure wave event which is an indication that significant injury from the broken glass could occur. The test is repeated with a bast mitigation glazing system (various thicknesses of safety film applied to the interior side of the glass for example). The results compare the amount and location of glass shards imbedded in the witness panel and in designated floor regions. Shock Tube Testing is a serious and useful test method for studying some facets of blast mitigation dynamics. It is significantly less expensive than the Open-Air Arena testing described below but suffers from two significant deficiencies. 1) The positive-impulse phase is usually over energetic and does not exhibit a force that decreases gradually over a sustained time frame. 2) This test method does not produce a negative phase. In actuality, a bomb blast produces both a positive forward moving force, and a negative backward force that will function in a manner so as to “pull” the window outwardly from its frame. Both Shock Tube testing limitations are accounted for in Open-Air Arena Testing, a procedure that generally receives greater credibility from the engineering community for more closely simulating an actual blast event. Open-Air Arena Testing The preferred and more recognized method for testing the performance level of glass fragment retention is Open-Air Arena testing with large explosive charges and glazing systems mounted in an enclosed structure. Such tests are very expensive. However, this type of testing more closely replicates 24 the actual results of a bomb blast situation, as it would affect untreated glass, laminated glass, safety film treated glass, and other glass breakage mitigation devices and techniques. The GSA, US Department of State (DoS), and the Department of Defense (DoD) have developed performance criteria for evaluating the mitigating glass fragment effects of glazing systems. In general, the criteria are based on whether the glass doesn’t break, cracks but fragments are mostly held at the frame, fragments enter the space but are not likely to reach an individual seated at their desk, fragments enter the space and while dangerous may not impact an individual in a lethal manner, or the glazing fails catastrophically, likely leading to serious injury. While it is easy to imagine how broken shards of annealed glass could be lethal, in a blast event flying rounded pieces of tempered glass can also cause serious injury. Blast Test Methods and Standards ASTM F1642; Standard Test Method for Glazing and Glazing Systems Subject to Airblast Loadings and ASTM F2912; Standard Specification for Glazing and Glazing Systems Subject to Airblast Loadings. ASTM F1642 is a glass or fenestration test and requires shock tube or open arena testing. It evaluates hazards of glazing against airblast loads. Glazing tests can be performed with or without a frame system. The actual rating and hazard levels are contained in ASTM F2912. GSA TS01; US General Services Administration Standard Test Method for Glazing and Window Systems Subject to Dynamic Overpressure Loadings. This test standard is intended to ensure an adequate measure of standardization and quality assurance in the testing of window systems including but not limited to glazing, sealants, seats and seals, frames, anchorages and all attachments and/or secondary or restraint mechanisms designed to mitigate the hazards from flying glass and debris. This standard is the sole test protocol by which blast resistant windows and related hazard mitigation technology and products shall be evaluated for facilities under the control and responsibility of the US General Services Administration (GSA). Within this standard there is also provision for a special evaluation specified by the Department of State for locations within their purview. ISO 16934; Glass in building – Explosion resistant security glazing – Test and classification by shock-tube loading. ISO 16934 specifies a shock tube test method and classification requirements for explosion-pressure- resistant glazing, including glazing fabricated from glass, plastic, glass-clad plastics, laminated glass, glass/plastic glazing materials, and film-backed glass. ISO 16934 also provides a structured procedure to determine the blast resistance and the hazard rating of glazing and glazing systems. The standard sets out procedures to classify such security glazing sheet materials by means of tests on specimens of a standard size in a standard frame for the purpose of comparing their relative explosion resistance and hazard rating. Specifically, ISO 16934 applies a method of test and classifications against blast waves generated in a shock tube facility to simulate high-explosive detonations of approximately 30 kg to 2 500 kg TNT at distances from about 35 m to 50 m. The classifications approximately represent the reflected pressures and impulses that are experienced by these equivalent threat levels on the face of a large building facade positioned perpendicular to the path of the blast waves. 25 Classification is defined in terms of both blast shock-wave characteristics, expressed in terms of peak reflected pressure, impulse, positive phase duration and wave-form parameter (decay coefficient), and rating criteria, expressed in terms of degrees of glazing damage and fragment impact hazard. Classifications and ratings are assigned based upon the performance of the glazing and are specific to the blast characteristics under which the test has taken place. Glazing that has received an air-blast classification and rating is suitable for use in blast-resistant applications only for blasts of comparable characteristics and only if installed in a properly designed frame. Design based on knowledge of the air blast resistance reduces the risk of personal injury. ISO 16933; Glass in building – Explosion resistant security glazing – Test and classification for arena air- blast loading. ISO 16933 provides a structured procedure to determine the air-blast resistance of glazing and sets forth the required apparatus, procedures, specimens, other requirements and guidelines for conducting arena air-blast tests of security glazing. Seven standard blasts simulating vehicle bombs and seven standard blasts simulating smaller satchel bombs that can be used to classify glazing performance are incorporated in this International Standard and cover a broad range of blast parameters. Security glazing, including that fabricated from glass, plastic glazing sheet material, glass-clad plastics, laminated glass, insulated glass, glass/plastic glazing materials and film-backed glass, can be tested and classified in a standard frame or tested but not classified in frames provided with the glazing. Classification and ratings are assigned based on the performance of glazing loaded by air-blast pressures and impulses and are specific to the blast characteristics under which the test takes place. Glazing that has received an air-blast classification and rating is suitable for use in blast-resistant applications only for blasts of comparable characteristics and only if installed in a properly designed frame. Design based on knowledge of the air-blast resistance reduces the risk of personal injury. Often these test methods are shown together on manufacturers’ lists of available test results since they have many similarities and differ only in how they classify or name the hazard risk. The tests allow a variety of different pressures to be tested depending on the type of and magnitude of the blast being simulated by the test. The actual details of the test including, glass type, thickness, mitigation device, pressure wave, duration, etc must be shown in the test report for the reader to have full information on what was tested and what combination is receiving the hazard classification. Shown below are the performance conditions and description of the hazard levels associated with the various classifications for GSA TS01. Other standards may have a different classification system. 26 Observations: The following general observations can be made from these tests: Laminated glass and glass clad polycarbonate, and polycarbonate sheets can be engineered to withstand significant blast loads provided adequate framing rebates and anchoring methodologies are provided. 27 The failure mode for laminated glass exhibited a tendency to be pulled out of the window bite or farming system if not designed correctly. Safety Film properly installed on windows provided significant hazard mitigation. Safety Film performed better on heat-treated and/or tempered systems versus annealed glass, especially when attachment systems are utilized. Increasing film thickness generally improved the blast mitigation performance. Methods of film attachment, mechanical or otherwise, provide better protection than “daylight” installed film applications. Forced Entry – Burglary Resisting Glazing Material For many years the standard test method mentioned to determine the suitability of glazing for burglary resistance was Underwriters Laboratory Inc., Test UL 972. UL is a not-for-profit organization established in 1874. The organization’s purpose is to establish, maintain, and operate laboratories for the examination and testing of devices, systems, and materials, to determine their inherent or mitigation effectiveness to hazards to life and property, and to ascertain, define and publish standards, classifications, and specifications for materials, devices, products, equipment, constructions, methods, and systems affecting such hazards. There are several parts to UL972, whose scope and procedures are also approved by ANSI. The objective of the test is to develop standards for materials intended to resist burglary attacks of the “smash and grab” type. Smash and grab burglary are crimes that depend on stealth and speed so measures that slow the criminal in their efforts to get through the glass can be effective. A minimum of 37, 24” x 24” glazing specimens are needed to complete all phases of the standard. In the basic test phase, a 5 lbs. steel ball is dropped from a height of 10 feet onto the two-foot square specimen. In the case of safety film, the film is on the back side from the impact as would be the case in a building where the film would be on the inside of the glass and the attack would take place from the exterior. The procedure requires that multiple drops of the steel ball be made on the same specimen five times in succession within a specified area in the center of the specimen. The test requires that the steel ball not penetrate the specimen on any one of the five impacts on nine out of 10 samples tested during each of the test phases. Penetration is considered to occur if the ball passes completely through the glazing system. The complete testing standard calls for this test to be repeated at various temperatures in an outdoor and indoor setting. There is also a High-Energy Impact test wherein the steel ball is dropped from a vertical height of 40’. The difficulty in safety film passing or using this test standard is two-fold. The ball cracks the glass and especially with annealed glass, on each successive drop small sharp shards of glass begin to cut the film until the weight of the ball causes it to drop through the specimen 28 UL has determined that they will not issue a passing test report for just a glass/safety film combination. The product tested must be the complete glazing system…including the framing which means that unless the building in question has significant glazing to justify completing a test for the exact configuration of the glass/film/framing combination, it is cost prohibitive to complete this testing for each building. For the reasons stated above the most frequently cited test standard for security glazing is EN-356 European Standard for Glass in building. Security Glazing – Testing and classification of resistance against manual attack. P1A and P2A. EN356 shares some similarities with the UL test in that it uses a steel ball in a drop test but there are significant differences. The steel ball is 4.11 kg (9.1 lbs.) and each of 3 glazing specimens is impacted three times in a triangular pattern (total of 9 impacts over the 3 glazing specimens). No impact can allow the steel ball to penetrate. The glass specimens are 1100mm (roughly 43”) x 900mm (about 35”). The P1A impact height is 1500mm (59”) and the P2A impact height is 3000mm (118”). EN 356 is still an extremely difficult test to pass, especially on glass types and thicknesses normally found in existing buildings. As with all safety film, the dealer is encouraged to make sure the consumer need is well understood, the testing matches the existing glazing, and the performance of the installation offered is not overstated. Active Shooter Events Another possible forced entry event is that of an active shooter trying to gain access to a building with the intent of shooting an occupant or in many cases multiple occupants. IWFA does not make any statements or claims with regards to any safety film/existing glazing combination being bullet resistant or in any manner “bullet-proof”. Some manufacturers have tested their products with certain film/glass combinations in order to assess the amount of time that a perpetrator may be delayed from entering a building. Always ensure that the consumer is aware of the glass type and thickness compared to their existing glazing and indicate the type of weapon, load, and stand-off distance used in the test/demonstration. Glass Defacement The use of sharp instruments or chemical etching agents to deface glass is a particular use for thick safety films. These films are often called graffiti films and the action of defacing the glass is often referred to as “tagging”. Specialized films are produced by some manufacturers that allow for easy removal and replacement of the film after it is defaced and other films are available for use on exterior glazing such as store fronts. Installation Types and Attachments The special requirements of a thick safety film installation are outside the scope of this document (see Appendix C for visual inspection standards and cure times for thick films). However, a review of the differences in installation types is useful. 29 There are three general installation techniques: 1) Daylight 2) Edge to Edge 3) Anchored (Mechanical and Wet Glazed) These three installation techniques and their variants differ significantly in their ability to keep shattered glass in the frame during an event. Daylight Installation This installation technique is the most widely used and accepted method of applying Safety Film in the industry. The technique involves cutting and applying the film onto the surface of the glass leaving a slight space between the edge of the film and the edge of the framing system. This form of application is generally more than sufficient to hold broken annealed glass intact within the framing system under instances of human impact, small missile impact, and small explosive charges. It also provides sufficient resistance to attempted forced entry in most cases unless the attack is more than “smash and grab” in nature. In the case of tempered glass, however, a more robust method is necessary to keep the glass from falling out of the frame when the tempered glass breaks into small pieces. In the case of tempered glass and in instances where the forces are greater than previously stated, the other installation techniques may be required to meet the stated needs of the project. Edge to Edge Installation In this method, the film is applied to cover 100% of the glass surface. The technique is generally more associated with application to new glass that is awaiting installation in a frame (versus a retrofit situation) whereby the glass would be removed from the framing system and the film applied “edge to edge”. Anchored Installation There are two broad forms of anchored installation methods, generally referred to as “mechanical” and “wet glazed) installations. Within the mechanical category there are two types with the second being used more widely. In the first type of mechanical installation the safety film not only covers the entire surface of the glass, but it also extends to overlap the framing system and is held in place by a mechanical bar and batten type of attachment system. The system can be attached to the tope of the frame, on two opposite sides, or on all four sides. In the second type of mechanical installation, the film is installed in the daylight method and then a special seal with adhesive on two parallel faces of a folding gasket-like material is applied to the film and the frame to create a “hinge” which connects the film/glass to the frame. This attachment system tends to be more flexible, quicker to install, and thus more economical to use. In the “wet” system the film is applied in the daylight method, however there is not visible gap between the film and the edge of the framing system. The installer undercuts the existing gasket and then creates a new seal with a special sealant material which overlaps both the frame and the film/glass combination. The adhesive (caulking) must extend onto the glass and the framing system 3/16” or more. 30 Both mechanical and wet anchor type systems significantly enhance the performance level of the entire glazing system to maintain its integrity in the event that the glass is broken. An installation using an anchoring system is more labor intensive, and thus more costly than a daylight installation, but still considered less than the cost of laminated glass in most cases. The type of anchoring system and how it is installed will determine the overall aesthetics of the system. Government Agencies (US) There are numerous federal agencies that have direct and indirect involvement in numerous issues related to Safety Film. This involvement runs the gamut from developing and establishing test procedures and test standards, natural disaster mitigation, and final purchasing authority. The following list is by no means all-inclusive, and each country and region will have their own set of agencies. General Services Agency (GSA) There are 26 Federal agencies that are authorized to purchase, own, or lease space, buildings, or other parcels of land. The General Services Agency is the largest of these agencies and has the only real authority that allows an agency to sublet the space to other agencies and to purchase buildings for that purpose. The GSA is the government entity charged with providing office space for most of the federal civilian work force. As part of its mission, it is the GSA’s responsibility to protect Federal property and employees, under its charge and control, by providing a safe and secure environment for the conduct of government operations. Department of Defense (DOD) The Department of Defense is a cabinet-level organization. Reporting to it are the three military departments (Army, Navy, and Air Force) and 14 defense agencies. The mission of the DoD is to provide the military forces needed to deter war and to protect the security of the US. The agency actively carious out its own research into mitigation protection and is responsible for funding in many cases. Department of State (DOS) The Department of State advises the President of the US and leads the nation in foreign policy issues. The State Department negotiates treaties and agreements with foreign entities and represents the United States at the United Nations. Ambassadors to other countries report through the State Department and as such the State Department often has their own guidelines around security measurements in US government buildings around the globe. Department of Homeland Security (DHS) Under the direction of the Secretary of Homeland Security, DHS is responsible for counterterrorism, cybersecurity, aviation security, border security, port security, maritime security, administration and enforcement of immigration laws, protection of national leaders, protection of critical infrastructure, detection of and protection against chemical, biological, and nuclear threats, and response to disasters. Some well-known agencies under DHS include TSA, the Secret Service and FEMA. 31 The Federal Emergency Management Agency (FEMA) is the agency tasked with helping people before, during and after disasters. Floods, hurricanes, earthquakes, and forest fires, whatever the disaster, FEMA leads the federal government’s response. 32 Appendix A Safety and Security General Guidelines Because safety and security films often deal with life and personal safety issues it is particularly important that claims be substantiated using test methods from recognized and reputable standard- setting organizations. Safety standards often have several levels of acceptance. To comply with IWFA’s False Advertising Policy, safety claims must be substantiated by identifying the level of standard achieved, not the level tested. The IWFA Board of Directors, upon recommendation from the IWFA Technical Committee, endorses the following test standards, from recognized and reputable national or international standard-setting organizations, as Endorsed Standards in the particular areas and categories referenced below. As such, safety claims that relate to the particular subject matter referenced below and which are based on testing performed in accordance with the specified standard will be presumed to comply with the IWFA False Advertising Policy, provided such testing is performed in a reasonable and replicable manner and consistent with the guidelines set out in this Exhibit A of the IWFA Policies and Procedures. Safety and Security Standards and Guidelines Other test standards from individual countries may apply in specific countries or regions. The IWFA endorses the use of the following test methods conducted in accordance with the guidelines set out below: Physical Properties1 o EN15752, Section 6 o Total thickness of product without liner. o Polyester Structural Thickness o Report total thickness of polyester layers used in the product. o ASTM D882 o Tensile Strength – Report both MD and TD separately and report must list the direction for each. o Break Strength – Report both MD and TD separately and report must list the direction for each. o Elongation at Break – Report both MD and TD separately and report must ist the direction for each. o ASTM D1001 – Tear Strength o Peak load – Report MD and TD separately o Elongation o ASTM D1044- D, 100 cycles, 500 gms, vacuum on, wheel type – CS10F o Abrasion resistance expressed as a change in haze. o ASTM E84 Flammability o Flame Spread Index o Smoke development Index o ASTM D1929 o Flame Ignition o ASTM D3330 33 o Peel strength at 180 degrees, report in Lbs/in. Dry or wet lamination to glass, cure time and conditions as specified by the manufacturer. Test 1” strip cut from larger sample. o Peel strength accuracy is diminished as film thickness increases. Acceptable to report peel strength on 2 mil or 4 mil product only as long as thickness is disclosed. 1 Physical properties may not be indicative of films performance under various natural or human caused events. Performance test may be necessary or desirable to prevent false or misleading performance claims. Appendix C 34 35