Engro Polymer & Chemicals PSM 03 PDF
Document Details
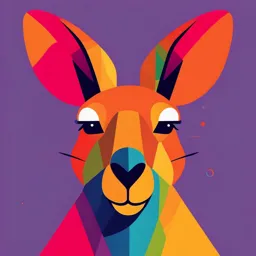
Uploaded by GreatHyperbola
2008
Ammar Hussain
Tags
Related
- PSM 09 Training and Development - Engro Polymer & Chemicals PDF
- Engro Polymer & Chemicals PSM 09 Training & Development PDF
- Module 01- Introduction to Functional Safety PDF
- Guidelines for Process Safety & Asset Integrity Management Systems (PSAIMS) PDF
- Safety Management System PDF
- Process Safety Management Concepts PDF
Summary
This document provides the requirements for complying with the Process Safety Element on Integrated Organization Structure for Engro Polymer & Chemicals, prepared in December 2008.
Full Transcript
Document # HSE / PSM / Level-II / 03 Date Prepared: December 2008 Page 1 of 53 Revision: 02 Revision Date: October 2016...
Document # HSE / PSM / Level-II / 03 Date Prepared: December 2008 Page 1 of 53 Revision: 02 Revision Date: October 2016 PSM 03- INTEGRATED ORGANIZATION STRATURE Scope: This Document describes the requirement for complying with the Process Safety Element on Integrated Organization Structure. AUTHORIZATION: Reviewed By: ________________________ Farrukh Iqbal Qureshi Prepared By: ____________________________ Corp. HSE Manager Ammar Hussain HSE Engineer Reviewed By: ________________________ Rizwan Ahmed Taqi Chairman Sub-HSE (PSRM) Reviewed By: ____________________________ Syed Muhammad Farooq Ahmed Safety Advisor Approved By: ________________________ Jahangir Waheed VP Manufacturing Change Record: All changes have been made Bold, Italic and Highlighted in Grey Sr. Date Rev. Page Section Change Description No. No. No. PSM 07 – Integrated Organization of Safety has been 1 Oct ‘16 02 All All renamed to PSM 03 – Integrated Organization Structure Prepared By; Ammar Hussain Reviewed By: SMF/ FIQ/ RT Approved By: Jahangir Waheed Document # HSE / PSM / Level-II / 03 Date Prepared: December 2008 Page 2 of 53 Revision: 02 Revision Date: October 2016 SECTION-1 TABLE OF CONTENTS SECTION-1 TABLE OF CONTENTS................................................................................................................. 2 SECTION-2 BASIS............................................................................................................................................. 3 PURPOSE 3 SUMMARY................................................................................................................................................................................................... 3 SECTION-3 CORPORATE HSE COMMITTEE.................................................................................................. 4 3.1 ROLE................................................................................................................................................................................................. 4 3.2 MEMBERSHIP................................................................................................................................................................................... 4 3.3 MEETING FREQUENCY.................................................................................................................................................................... 4 3.4 RESPONSIBILITIES............................................................................................................................................................................ 4 SECTION-4 MANUFACTURING HSE COMMITTEE ROLE & RESPONSIBILITIES....................................... 6 4.1 SCOPE............................................................................................................................................................................................... 6 4.2 FUNCTION........................................................................................................................................................................................ 7 4.3 MEMBERSHIP................................................................................................................................................................................... 8 4.4 ROLES AND RESPONSIBILITIES....................................................................................................................................................... 8 4.5 MANUFACTURING HSE MEETINGS..................................................................................................................................... 10 4.6 LEADING INDICATORS.................................................................................................................................................................. 12 SECTION-5 SUB HSE COMMITTEE (PROCESS)...........................................................................................14 SECTION-6 SUB HSE COMMITTEE (MECHANICAL)..................................................................................16 SECTION-7 SUB HSE COMMITTEE (I & E)..................................................................................................20 SECTION-8 SUB HSE COMMITTEE (OHIH)..................................................................................................25 SECTION-9 SUB HSE COMMITTEE (IRRC)...................................................................................................27 SECTION-10 SUB HSE COMMITTEE (B & A)..................................................................................................30 SECTION-11 SUB HSE COMMITTEE (T & DS)................................................................................................32 SECTION-12 SUB HSE COMMITTEE (PSM)...................................................................................................34 SECTION-13 SUB HSE COMMITTEE (T & D).................................................................................................36 SECTION-14 SUB HSE COMMITTEE (CONTRACTOR SAFETY)...................................................................39 SECTION-15 DEPARTMENT LEVEL (“B”) SAFETY COMMITTEE ROLE STATEMENT................................43 SECTION-16 ‘D’ LEVEL SAFETY COMMITTEE...............................................................................................46 SECTION-17 OFF-THE-JOB HSE AWARRENESS...........................................................................................52 SECTION-18 ORGANOGRAM.........................................................................................................................53 SECTION-19 ATTACHMENTS.........................................................................................................................53 Prepared By; Ammar Hussain Reviewed By: SMF/ FIQ/ RT Approved By: Jahangir Waheed Document # HSE / PSM / Level-II / 03 Date Prepared: December 2008 Page 3 of 53 Revision: 02 Revision Date: October 2016 SECTION-2 BASIS 2.1 Purpose The purpose of this document is to provide details of overall safety organization at EPCL. 2.2 Summary The purpose of the overall safety organization is to mobilize all available talent in the interest of safety, health, and environmental protection. It does not in any way relieve individual members of the line organization of their safety responsibilities; rather it provides additional resources upon which they can draw to execute these responsibilities more effectively. Safety committees and safety meetings have proven to be effective means of formulating and carrying out company safety policies, gathering and dissem- inating safety information, enlisting employee participation in the safety effort, and generating and sustaining interest in safety. Committees are staffed principally by members of the line organization supplemented by safety staff members and other specialists. The document at the next page describes the safety organization in place at EPCL. Prepared By; Ammar Hussain Reviewed By: SMF/ FIQ/ RT Approved By: Jahangir Waheed Document # HSE / PSM / Level-II / 03 Date Prepared: December 2008 Page 4 of 53 Revision: 02 Revision Date: October 2016 SECTION-3 CORPORATE HSE COMMITTEE Background EPCL Safety Management System requires visible involvement of top level Executives in Safety Management Programs. We believe that Safety must be led from the top: Performance will only be as good as leadership demands & visibly supports. 3.1 Role The HSE top level Committee’s primary role is to provide strategic guidance to the overall safety improvement initiatives for EPCL. The Committee would provide visible personal leadership, commitment, support, accountability and follow-through for all safety programs. 3.2 Membership Chairman - EPCL President/ CEO Secretary - Corporate HSE Manager or above as appointed by the President/ CEO Members - All Executive Managers reporting directly to the President/ CEO 3.3 Meeting Frequency Once a Quarter 3.4 Responsibilities The committee would define a vision of the level of excellence EPCL should attain. The purpose of the committee is to own & maintain the HSE policy & ensure that all EPCL operations adhere to the policy. Coordinate HSE work across EPCL from strategic leadership perspective. 3. The committee would initiate, validate, sponsor & support corporate HSE objectives. The committee would set HSE goals & track their accomplishments for the organization. The committee would ensure HSE organization at Division level to administer HSE activities effectively - one that cascades from top to the lowest level. The HSE Committee will review major incidents e.g. injuries, fires, environment incidents & Occupational illness etc. to ensure effective measures to prevent recurrence & to act on management system failure at the highest level of the organization. The Committee would steward “OSHA compliance road map” on a quarterly basis. Prepared By; Ammar Hussain Reviewed By: SMF/ FIQ/ RT Approved By: Jahangir Waheed Document # HSE / PSM / Level-II / 03 Date Prepared: December 2008 Page 5 of 53 Revision: 02 Revision Date: October 2016 The Committee would ensure compliance to relevant National standards & regulations such as the National Environmental Quality Standards. The committee would oversee the activities of HSE Sub Committees & activities of Plant level Manufacturing HSE. The Committee members would formally conduct “Management Safety Audits” at the Division as per defined frequency. The HSE Committee would appoint adhoc safety committees when there is a strategic or technical need to do so. Prepared By; Ammar Hussain Reviewed By: SMF/ FIQ/ RT Approved By: Jahangir Waheed Document # HSE / PSM / Level-II / 03 Date Prepared: December 2008 Page 6 of 53 Revision: 02 Revision Date: October 2016 SECTION-4 MANUFACTURING HSE COMMITTEE ROLE & RESPONSIBILITIES Manufacturing HSE is the top safety committee at manufacturing site of Engro Polymer & Chemicals Ltd. The MHSE reports to the Vice President – Manufacturing. MHSE is the final review authority for Health, Safety & Environment matters related to manufacturing site and may only be over-ruled by Vice President – Manufacturing or Corporate HSE Committee. 4.1 Scope Following items are supposed to be reviewed by Manufacturing HSE for recommendations approval, implementation of changes, organization decisions and approval of deviations from standards that may have safety implications. The MHSE or the MHSE Chairman will review and approve any deviations from those standards. 4.1.1 Studies and Audits Schedule 1. Annual Health, Safety and Environment Surveys and Audit Matrix 2. Internal / External Health, Safety and Environment Audits 4.1.2 Layout Plant layout changes such as: 1. Changes which affect the spacing standards 2. Layout of the plant 3. Changes in roads, crane path ways 4.1.3 Waivers Following deviations from standards and schedules shall be reviewed in and approved by MHSE chairman / Co- chairman; the approval could be on waiver forms or a joint review by MHSE forum: Deviations of design or spacing standards Non-compliance to Safety Critical equipment preventive maintenance or inspection schedules Non-compliance to site safety training schedules For details refer to HSE Waiver Procedure - HSE / Safety / SSM/ Level II/ 05 Prepared By; Ammar Hussain Reviewed By: SMF/ FIQ/ RT Approved By: Jahangir Waheed Document # HSE / PSM / Level-II / 03 Date Prepared: December 2008 Page 7 of 53 Revision: 02 Revision Date: October 2016 4.1.4 Dropping of Safety Recommendations Safety recommendations (pending incident report, PHA, PSSR etc.) which are not practical and are required to be dropped shall be reviewed and approved by MANF. HSE chairman / co-chairman. 4.1.5 Contractors Work Permit Signing Authority Any contractor who is required to handle work permit and jobs independently – names of contractors and jobs that are supposed to be handled shall be listed. 4.2 Function The MHSE’s primary function is to promote, set standards, and monitor personnel safety, health and risk management in the areas of design, operations, and maintenance of EPCL facility in line with the Company’s Health, Safety and Environment Policy. In addition to above, the committee is required to provide direction, guidance, and assistance and monitor activities related to operational safety and health recognizing that the safety in all its aspects rests with the line organization and individuals. 4.2.1 Injury and Incident Prevention MHSE will: 1. Review all accidents, injuries, fires, operational upsets and significant near misses. 2. Periodically monitor the progress on the recommended actions emanating from investigations of these incidents. 3. Steward Total Recordable Injury Rate (TRIR), Total Recordable Incident Frequency (TRIF) for first aid cases, Process Safety Total Incident Rate (PSTIR) and Fleet Accident Frequency Rate (FAFR) on monthly basis and will take appropriate actions to control them. 4.2.2 Safety Reviews and Audits MHSE will: 4. Ensure that the safety reviews of all plant equipment modification, addition and new or modified operating procedure, are conducted before these are put into service. 5. Sponsor periodic external audits and overview implementation of internal audits to assess the adequacy of existing facilities, procedures and personnel skill level. MHSE will review the audit results and monitor progress on actions to eliminate deficiencies (e.g. PHA reviews, PSM audits and other risk management studies). Prepared By; Ammar Hussain Reviewed By: SMF/ FIQ/ RT Approved By: Jahangir Waheed Document # HSE / PSM / Level-II / 03 Date Prepared: December 2008 Page 8 of 53 Revision: 02 Revision Date: October 2016 6. Periodically review plant emergency preparedness to cope with hazardous material (e.g. EDC, VCM, HCL, Chlorine, and Ethylene) leakages or fire / explosions or other emergencies) 7. Approve the safety critical devices list and periodically review the test results of the safety critical control securities. 8. Promote and sponsor activities related to safety technology improvements and use. 9. Periodically review programs to ensure that National Environmental Quality Standards for plant effluent are being followed. 10. Overview programs of Sub HSE Committees for Process, Mechanical, Instrument & Electrical, PSM, OHIH, B &A, IRRC, Training & Development, Contractor Safety and Transport and driving safety and will periodically review the progress of programs. 11. Review the Site Process/ Personnel Leading Indicators of Safety and Environment Performance monthly and provide assistance and guidance to areas needing help. Note: In the absence of MHSE & Sub HSE Committee Chairmen / Co-Chairmen, the stand-in are not authorized to chair the meetings unless waiver is obtained from MHSE Chairman. For details refer to HSE Waiver Procedure - HSE / Safety / SSM/ Level II/ 05 4.3 Membership Chairman : V. P. Manufacturing or Department Manager, appointed by the Vice President - Manufacturing. Co-Chairman: Plant Manager and/ or GM Operation, appointed by the Vice President Manufacturing. Secretary : HSE Advisor. Members : GM Operations and All Department Managers, other personnel with special skills may be appointed to the MHSE from time to time by the VP Manufacturing/ MHSE Chairman. 4.4 Roles and Responsibilities 4.4.1 HSE Advisor – Secretary HSE advisor responsibilities are to: 1. Develop agenda of MHSE in close coordination with MHSE chairman / Co-chairman. 2. Plan and conduct MHSE meetings monthly 3. Issue minutes of MHSE meeting. Prepared By; Ammar Hussain Reviewed By: SMF/ FIQ/ RT Approved By: Jahangir Waheed Document # HSE / PSM / Level-II / 03 Date Prepared: December 2008 Page 9 of 53 Revision: 02 Revision Date: October 2016 4. Steward and track all action-able items / recommendations till completion. Share the status in MHSEs as and when required. 5. Develop and update Site Process/ Personnel leading safety performance indicators based on guidelines given in section 4.6 Process/ Personnel Leading Indicators. 6. Identify weak areas based on past safety incidents, MSA observations, site safety audits etc. and present to MHSE for setting direction. 7. Make plans for site Health, Safety, Environment activities, circulate to all MHSE members / department heads and steward them till their completion. 8. Get site internal and external safety audits conducted on their defined frequencies. 4.4.2 Corp. HSE Manager Corp HSE Manager Responsibilities are to: 1. Analyze site safety situation and give direction to the forum for future action plan. 2. Helps in making plans for site Health, Safety, Environment activities 3. Implements all MHSE safety recommendations and action-able items related to his department with 100% compliance. 4. Get site internal and external safety audits conducted on their defined frequencies. 4.4.3 Technical Manager Technical Manager Responsibilities are to: 1. Highlights any safety issues / programs with site wide safety implications.. 2. Implement all MHSE safety recommendations and action-able items related to his department with 100% compliance. 4.4.4 Maintenance Manager Maintenance Manager Responsibilities are to: 1. Highlights any safety issues / programs with site wide safety implications.. 2. Implement all MHSE safety recommendations and action-able items related to his department with 100% compliance. 4.4.5 I&E Manager I&E Manager Responsibilities are to: 1. Highlights any safety issues / programs with site wide safety implications.. 2. Implement all MHSE safety recommendations and action-able items related to his department with 100% compliance. Prepared By; Ammar Hussain Reviewed By: SMF/ FIQ/ RT Approved By: Jahangir Waheed Document # HSE / PSM / Level-II / 03 Date Prepared: December 2008 Page 10 of 53 Revision: 02 Revision Date: October 2016 4.4.6 Production Managers Production Manager Responsibilities are to: 1. Highlights any safety issues / programs with site wide safety implications.. 2. Implement all MANF. HSE safety recommendations and action-able items related to his department with 100% compliance. 4.4.7 Technology & Training Manager Technology & Training Manager Responsibilities are to: 1. Highlights any safety issues / programs with site wide safety implications.. 2. Implement all MHSE safety recommendations and action-able items related to his department with 100% compliance. 4.5 MANUFACTURING HSE Meetings 4.5.1 Frequency MHSE meetings shall be held on monthly basis. 4.5.2 MANUFACTURING HSE Yearly Goals / Calendar Functioning of the MHSE will mainly be controlled through a yearly calendar prepared at the start of the year and distributed to all interfaces upfront. MHSE shall review and steward following in a yearly cycle to ensure safety programs compliance, actions on their findings and measure the progress. Generally, the MHSE items shall be based on following aspects: 1. Items falling in MHSE scope as given in section 4.1 Scope. 2. Analysis of increasing failures, safety management systems or safety / cardinal rules violations which can jeopardize site safety 3. Any items which requires decision or direction for future site safety programs or re- organizations Note: Items which fall in Sub HSE committee’s domain or other forums e.g., Plant Review Meeting (PRM) etc. can be brought to MHSE if MHSE secretary recommends and MHSE chairman or Co-chairman approves. Following are items which shall be reviewed in MANUFACTURING HSE during a year. Prepared By; Ammar Hussain Reviewed By: SMF/ FIQ/ RT Approved By: Jahangir Waheed Document # HSE / PSM / Level-II / 03 Date Prepared: December 2008 Page 11 of 53 Revision: 02 Revision Date: October 2016 4.5.2.i Routine Items Review Following items shall be reviewed in every MHSE or on need basis: 4. Stewardship of all safety related recommendations e.g., Pending Incident Reports Recommendations, PHA, PSSR, Emergency Response recommendations etc. 5. Review of the Site Process/ Personnel Leading indicator of Safety & Environment 6. Serious incidents / injuries investigation finding 7. Incident/ Injury Analysis 8. Inspection program compliance and issues faced for past year and plans for next year 9. D-Level Safety Committees Performance 10. Review of the results of incident reports analysis by IRRC 11. MSA Analysis 12. PSM Audit Summary 13. Temporary Repairs Status 14. Fire Extinguisher Survey / PPEs / Safety showers surveys recommendations – if needed 15. Review of the Safety Critical Defeat analysis 16. Off-the-Job Safety Committee Performance and Plan 17. Site HSE Matrix Compliance 18. Status of Audit Recommendations 19. Review of Site Safety Procedures (Site HSE Manual / Emergency Response Manual) for Updates 20. Safety Trainings Status – Man-hours, outcome etc. 21. HSE Plans/ Proposal 22. Update on various surveys, e.g Illumination, Noise etc. 4.5.3 Minutes of Meeting / MHSE Recommendations and Action Plan MHSE secretary will issue minutes of meeting of every MHSE soon after the meeting. All the items which need some action or are recommendations of MHSE shall be converted to actionable items and shall be stewarded until they are completed or evaluated to be closed. The completion of all such items shall be documented which justification / reasoning of what actions have been taken and who did the work. Prepared By; Ammar Hussain Reviewed By: SMF/ FIQ/ RT Approved By: Jahangir Waheed Document # HSE / PSM / Level-II / 03 Date Prepared: December 2008 Page 12 of 53 Revision: 02 Revision Date: October 2016 4.6 Leading Indicators Site shall develop criteria and steward it in MHSE for proactive site safety management. Site Leading Indicators are categorized into two segments Process LIs and Personnel LIs. Process LIs encompasses the following items; 1. Actions PHA Recommendations Compliance – Weightage 25% a. PSSR Recommendations Compliance b. Incident Report Recommendations Compliance c. HSE Recommendations Compliance d. Quarterly Drill Recommendations Compliance e. Risk Management Audit Recommendations Compliance f. PSM (Internal/External) Audit Recommendations Compliance g. Inspection Recommendations Compliance h. Timely submission of B-reports /Items Follow up 2. Mechanical Integrity - Weightage 35% a. Safety Critical preventive maintenance compliance b. Inspection plan compliance c. % of timely removal of Temporary Repairs d. Plant Operation with SCDs e. Risk Management Audit Compliance f. Plant Operation without LTD 3. Management of Change - Weightage 10% a. Percent of Start Ups (after modifications) without any Safety Issue b. Percentage of sampled MOCs that satisfied all aspect of the MOC procedure c. As Built and Ever Green P&ID up to date d. TR Audit (TR Forms Available/ TR as per Field verification by Ops) 4. Safety Culture - Weightage 05% a. Manager & UM participation in B-level b. D-level Effectiveness c. B-level Effectiveness d. %age Compliance of due waivers e. Housekeeping Points (Zero to departments having -ve points greater than average housekeeping points on SITE) f. Safety Culture Audit g. Inherent Safety Audit Compliance h. Inherent Safety Audit Recommendations Compliance Prepared By; Ammar Hussain Reviewed By: SMF/ FIQ/ RT Approved By: Jahangir Waheed Document # HSE / PSM / Level-II / 03 Date Prepared: December 2008 Page 13 of 53 Revision: 02 Revision Date: October 2016 5. Operating & Maintenance Procedure - Weightage 15% a. Work Permit Procedure Compliance b. LOTOTO Procedure Compliance c. Percentage of procedure related MSA observations in area should be