PSM 09 Training and Development - Engro Polymer & Chemicals PDF
Document Details
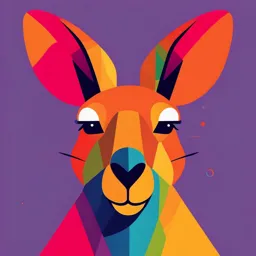
Uploaded by GreatHyperbola
Ammar Hussain
Tags
Related
- Engro Polymer & Chemicals PSM 09 Training & Development PDF
- Optimized Prep Line Reusable Assembly Checklist PDF | Philippines Version March 2020
- Fire and Emergency Services Administration - CH.6 PDF
- Risk Management and Hazard Control Process PDF
- Preventing Harassment & Violence in the Workplace for Managers (WHVP 102) PDF
- Process Safety Management Concepts PDF
Summary
This document outlines the requirements for process safety management training and development at Engro Polymer & Chemicals. It details various training procedures, including authorizing personnel and scope of the document. The document also contains change records.
Full Transcript
Document # HSE / PSM / Level-II / 09 Date Prepared: December 2008 Page 1 of 35 Revision: 02 Revision Date: October 2016...
Document # HSE / PSM / Level-II / 09 Date Prepared: December 2008 Page 1 of 35 Revision: 02 Revision Date: October 2016 PSM 09- TRAINING & DEVELOPMENT Scope: This Document describes the requirement for complying with the Process Safety Management element on Training and Development. Authorizations: Reviewed By: ________________________ Farrukh Iqbal Qureshi Prepared By: ____________________________ Corp. HSE Manager Ammar Hussain HSE Engineer Reviewed By: ________________________ Rizwan Ahmed Taqi Chairman Sub-HSE (PSRM) Reviewed By: ____________________________ Syed Muhammad Farooq Ahmed Safety Advisor Approved By: ________________________ Jahangir Waheed VP Manufacturing Change Record: All changes have been made Bold, Italic and Highlighted in Grey Sr. Date Rev. Page Section Change Description No. No. No. PSRM 09 – Personnel Training & Performance and PSM 10 - 1 Oct ‘16 02 All All Personnel Training & Performance have been merged into PSM 09 – Training & Development 2 Oct ‘16 02 38 10 SECTION-10 PSM CERTIFICATION Prepared By; Ammar Hussain Reviewed By: SMF/ FIQ/ RT Approved By: Jahangir Waheed Document # HSE / PSM / Level-II / 09 Date Prepared: December 2008 Page 2 of 35 Revision: 02 Revision Date: October 2016 SECTION-1 TABLE OF CONTENTS SECTION-1 TABLE OF CONTENTS................................................................................................................. 2 SECTION-2 BASIS............................................................................................................................................ 4 2.1 PURPOSE................................................................................................................................................................................. 4 2.2 SUMMARY.............................................................................................................................................................................. 4 SECTION-3 DEFINITIONS AND ABBREVIATIONS....................................................................................... 4 SECTION-4 TRAINING REQUIREMENTS..................................................................................................... 11 4.1 GENERAL FEATURES............................................................................................................................................................ 11 4.2 CONTRACTOR TRAINING................................................................................................................................................... 13 4.3 ESSENTIAL TRAINING AREAS / TOPICS............................................................................................................................. 13 4.4 PROCESS OVERVIEW........................................................................................................................................................... 13 4.5 SAFETY, HEALTH AND ENVIRONMENT TRAINING........................................................................................................... 13 4.6 BASIC SKILLS TRAINING..................................................................................................................................................... 14 4.7 JOB SPECIFIC TRAINING..................................................................................................................................................... 14 4.8 REFRESHER TRAINING........................................................................................................................................................ 14 4.9 WHO GETS THE TRAINING................................................................................................................................................. 16 4.10 GENERAL CATEGORIES........................................................................................................................................................ 16 4.11 EMERGENCY RESPONSE AND FIRE FIGHTING................................................................................................................... 16 4.12 STORAGE AND HANDLING OF HAZARDOUS MATERIALS............................................................................................... 16 4.13 RESPIRATORY PROTECTION............................................................................................................................................... 17 4.14 ON-THE-JOB TRAINER AND MENTOR QUALIFICATIONS............................................................................................... 17 4.15 MENTORS............................................................................................................................................................................ 17 4.16 ON-THE-JOB TRAINER....................................................................................................................................................... 18 SECTION-5 TRAINING MODEL.................................................................................................................... 19 5.1 BASIC ELEMENTS OF EFFECTIVE TRAINING....................................................................................................................... 19 5.2 NEW HIRE / TRANSFER SITE SAFETY INDOCTRINATION................................................................................................. 20 5.3 TRAINING MODEL......................................................................................................................................................... 21 SECTION-6 TRAINING PLANS..................................................................................................................... 22 6.1 TRAINING PLAN CYCLE...................................................................................................................................................... 22 6.2 TRAINING NEEDS ANALYSIS.............................................................................................................................................. 22 6.3 TNA REQUIREMENTS......................................................................................................................................................... 23 6.4 TRAINING PLAN DEVELOPMENT....................................................................................................................................... 24 6.5 TRAINING PLAN – GENERAL FEATURES............................................................................................................................ 25 6.6 TRAINING SCHEDULE.......................................................................................................................................................... 25 6.7 IMPLEMENTATION............................................................................................................................................................... 25 6.8 TRAINING PLANS – FACILITATION BY TRAINING DEPARTMENT.................................................................................... 25 6.9 TRAINING RECORDS........................................................................................................................................................... 26 6.10 BUDGET................................................................................................................................................................................ 26 SECTION-7 RESPONSIBILITIES..................................................................................................................... 27 7.1 EPCL EMPLOYEES TIER III , TIER IV, TRADE APPRENTICES, TAES OR GTES............................................................. 27 7.2 TRAINING DEPARTMENT ORGANIZATION AND RESPONSIBILITIES................................................................................ 27 7.3 TRAINING MANAGER......................................................................................................................................................... 28 7.4 TRAINING COORDINATORS ROLE..................................................................................................................................... 28 7.5 GENERAL.............................................................................................................................................................................. 28 Prepared By; Ammar Hussain Reviewed By: SMF/ FIQ/ RT Approved By: Jahangir Waheed Document # HSE / PSM / Level-II / 09 Date Prepared: December 2008 Page 3 of 35 Revision: 02 Revision Date: October 2016 7.6 TRAINING PLANS / ACTIVITIES.......................................................................................................................................... 28 7.7 SKILL CERTIFICATION.......................................................................................................................................................... 28 7.8 FOLLOW-UP AND REPORTS............................................................................................................................................... 29 7.9 TRAINING FACILITIES / RECORD UPKEEP.......................................................................................................................... 29 SECTION-8 MEASURING EFFECTIVENESS.................................................................................................. 29 8.1 EVALUATION........................................................................................................................................................................ 30 8.2 ON-THE-JOB EFFECTIVENESS............................................................................................................................................ 30 8.3 SKILL ASSESSMENT / CERTIFICATION............................................................................................................................... 30 8.4 QUALIFICATION REQUIREMENTS FOR ASST ENGINEER, EMERGENCY SQUAD MEMBERS AND TECHNICIANS.......... 30 8.5 SKILL RE-ASSESSMENT / CERTIFICATION......................................................................................................................... 31 SECTION-9 PERFORMANCE......................................................................................................................... 31 SECTION-10 PSM CERTIFICATION................................................................................................................ 32 SECTION-11 REFERENCES AND LEVEL-3 PROCEDURES............................................................................. 35 11.1 REFERENCES........................................................................................................................................................................ 35 11.2 LEVEL-3 PROCEDURES / DOCUMENTS............................................................................................................................. 35 Prepared By; Ammar Hussain Reviewed By: SMF/ FIQ/ RT Approved By: Jahangir Waheed Document # HSE / PSM / Level-II / 09 Date Prepared: December 2008 Page 4 of 35 Revision: 02 Revision Date: October 2016 SECTION-2 BASIS 2.1 Purpose The purpose of this procedure is to ensure that Process Safety Management goal of consistently performing employees through training, refreshers, identification of gaps in employees’ training and certification, is met. 2.2 Summary This procedure is intended to address the requirements and guidelines related to: Training of EPCL employees at all positions Qualifications of instructor and mentors Personnel for whom training is to be planned and budgeted Training on emergency response and control Training needs analysis, skill surveys and training plans of all employees. Refresher and supplemental training of all the employees. SECTION-3 DEFINITIONS AND ABBREVIATIONS Prepared By; Ammar Hussain Reviewed By: SMF/ FIQ/ RT Approved By: Jahangir Waheed Document # HSE / PSM / Level-II / 09 Date Prepared: December 2008 Page 5 of 35 Revision: 02 Revision Date: October 2016 3.1 Board / Certification Panel An interviewing / evaluation team comprising of more than 02 members. The members may be Department manager, Unit Managers, Section Heads or Designates and/or training coordinators. The board meets to review Supervisors and Engineers before assigning them independent duty or hiring of GTEs / trade apprentices as employees. 3.2 Checklist The two checklists used in training are: 1. The Demonstration Checklist is based on competency (skill) that has a list of tasks which is completed by On-the-Job Trainer. The checklist is used to evaluate a trainee’s performance of technical skills or other observable knowledge, e. g., transmitter calibration, breaker rack in / rack out demonstration etc. The Supervisor, Trainer and Trainee must sign the Checklist to meet the certification requirements. These checklists are used by trainers to evaluate performance of a procedure or activity objectively use the checklists. 2. The Key Position Stand-in Checklist contains specific requirements the incumbent must review with the stand-in. The Checklist must be completed before the stand-in assumes the incumbent role. 3.3 Competency Ability to perform a skill, a task or a job to a specific standard. 3.4 Competency-Based Training (CBT) Competency-based training is learning by doing. It emphasizes how the participant performs (i.e., a combination of knowledge, attitudes and, most important, skills) rather than what information the participant has learned. In CBT, participants’ progress is continually measured against pre-established performance criteria (standards) 3.5 Core Training Core training programs for employees are implemented to ensure adequate understanding of relevant processes and procedures which include appropriate aspects of the job, i.e., potential hazards, emergency response, safety critical procedures and equipment, safe work practices, safety engineering design, process / mechanical requirements etc. Prepared By; Ammar Hussain Reviewed By: SMF/ FIQ/ RT Approved By: Jahangir Waheed Document # HSE / PSM / Level-II / 09 Date Prepared: December 2008 Page 6 of 35 Revision: 02 Revision Date: October 2016 3.6 Core Training Categories The boundaries include: Assistant Engineers, Technicians, Shift Supervisors, Shift Coordinator, Mechanical / I&E first line supervisors and relevant Contractors working at EPCL. 3.7 Course Outline Detailed plan of topics to be presented in a course and how the training will be delivered. The course outline is a planning document. 3.8 Demonstration Test An evaluation technique, in which the evaluation supervisor / person ask the trainee to explain and show the steps, and sequence if necessary, required to perform a skill or activity. A variety of methods / equipment can be used to demonstrate a procedure, including simulators, standby equipment, routine activity etc. 3.9 Employee All technical or non-technical employee of EPCL is known as employee. 3.10 Facilitator A person who makes it easier for people to learn an activity by determining the best way to make that information available. 3.11 Faculty A knowledgeable / qualified person who gives training on a specified subject area and has the ability and training to transfer them to others. Faculty imparts knowledge to others, but does not train employee technical skills. However, they may be able to demonstrate certain technical skills on models in the classroom. 3.12 Instrument and Electrical Procedures A comprehensive set of instructions for maintaining / repairing and safely returning instrumentation, control systems, electrical equipment, power generators etc. to service. 3.13 Internship A process in which a professional institute student, under-goes through formal training in any of its relevant industry training. 3.14 Key Position Approves the design, construction, and operation of the plant to prevent the occurrence of incidents Prepared By; Ammar Hussain Reviewed By: SMF/ FIQ/ RT Approved By: Jahangir Waheed Document # HSE / PSM / Level-II / 09 Date Prepared: December 2008 Page 7 of 35 Revision: 02 Revision Date: October 2016 Has direct involvement in Operating and Maintaining Process safely Acts as a first responder to an incident in order to mitigate the results from escalating Any position having a role in emergency response for the site Responsible for personnel accounting during emergencies. 3.15 Learning Life-long process of acquiring new knowledge, attitudes and skills. It may occur formally during a learning event or informally during personal reading or study. 3.16 Matrix A chart for all departments consisting of; Courses; Job Positions and Training Frequency for the following: Training requirements Personal / Technical Training Plan 3.17 Mechanical Procedures A comprehensive set of instructions for maintaining / repairing and safely returning process equipment to service. 3.18 Mentor An experienced and qualified person who is responsible to train a new employee, trade apprentice or Graduate Trainee Engineer. 3.19 On Job Training Training that occurs on the job and often is accomplished through personal instruction, guidance from a supervisor or even observing coworkers. 3.20 On-the-Job Trainer A person, who instructs, demonstrates and directs trainees. It is usually a certified Operator / Technician responsible for training the new operator, technician or trade apprentice as follows: Review Trainee Training Plan Familiarize with PSM and leads through PSM training modules. Complete Trainee Demonstration Provide coaching until Technician or Operator gets certified. Prepared By; Ammar Hussain Reviewed By: SMF/ FIQ/ RT Approved By: Jahangir Waheed Document # HSE / PSM / Level-II / 09 Date Prepared: December 2008 Page 8 of 35 Revision: 02 Revision Date: October 2016 3.21 Operating Procedures A comprehensive set of instructions for the operation of a process. They should provide a clear understanding of the detailed operating parameters and limits for safe operation in all process modes (e.g., start-ups, normal operation, shutdowns), including an explanation of the consequence of operation outside the process limits and a description of steps to be taken to correct and / or avoid deviations. 3.22 Orientation Plan A plan developed for new employees, GTEs, TAEs, trade apprentices, etc. which covers safety, environmental hazards, administrative and other functions of the area. The orientation plans may vary for different individuals based on job / task requirements. 3.23 Participant Individual receiving training; also known as student, trainee or learner. The term participant is used most frequently in class room training. 3.24 Proficiency The ability to perform a skill or skills efficiently, precisely and with expertise. 3.25 Qualification The final step in the process of developing new knowledge, attitudes and skills in a specific skill area. After the trainee demonstrates mastery of the knowledge and skills presented in a course and successfully completes a demonstration, that individual is assessed as competent and therefore ready to perform that skill(s) or provide that service independently. Qualification does not imply certification, which is done by a board or panel for GTEs, Section Incharges/Supervisors and through Skill Certification Process for Tier IV Employees. 3.26 Refresher Training Re-training imparted to an individual to maintain certification and competency, refresher training is completed. 3.27 Safety & Environment Procedures A comprehensive set of instructions for site safety and environment procedures, that is, Safety manual, Emergency response procedures, Environment management system, Asbestos handling manual etc. 3.28 Safety Critical Equipment Refer to PSM 13 - Process Safety Information (PSI) package. Prepared By; Ammar Hussain Reviewed By: SMF/ FIQ/ RT Approved By: Jahangir Waheed Document # HSE / PSM / Level-II / 09 Date Prepared: December 2008 Page 9 of 35 Revision: 02 Revision Date: October 2016 3.29 Skill Questionnaire Set of validated and reliable questions used to assess the trainee’s knowledge and skill. 3.30 Self-Paced Learning Learning directed by the individual in order to meet personal learning objectives (also known as Individualized Learning). 3.31 Simulator Process simulator training on; basic towers; compressors; boilers; furnaces, pumps and control systems used to develop Operator / Technician skills in preparation for working as Boardman on board or Technician. 3.32 Skill Certification Process The process of training of newly hired employees or cross-trained employees, which ends in skill certification after formal tests and reviews by line-management, is called Skill Certification. This is mandatory for all operators before assigning independent duty as "Post Operator" on any of the operating posts including emergency planning / response and for technicians before assigning independent jobs / tasks. This system ensures that all employees have achieved the appropriate level of competence for operating and maintaining the plant. This system also ensures that all employees who could affect site health, safety or environment have achieved the appropriate level of competence. 3.33 Technical Employees Employees working for plant operation, engineers and technicians working in Production Department, I&E, Field Maintenance, Technical, Safety, Environment and Training Department and Laboratory are known as Technical employees. 3.34 Trades and Posts at EPCL Process Posts The Process Units are divided into Operating Posts both for administrative and technical aspects, e.g. UTY/CCPP Area-I, EDC/VCM Area-300, PVC-I BE etc. Trade Position Various trades and crafts are defined in various sections of departments based on skills and job type e.g., Shop Machinist, Pipe Fitter, Electrician etc. Prepared By; Ammar Hussain Reviewed By: SMF/ FIQ/ RT Approved By: Jahangir Waheed Document # HSE / PSM / Level-II / 09 Date Prepared: December 2008 Page 10 of 35 Revision: 02 Revision Date: October 2016 3.35 Trainee Anyone who is acquiring new knowledge, attitudes and skills. Also known as participant or student. The term learner may be used in both On-the-Job training and Class Room Education / Training. 3.36 Training It is the process used by trainer to impart new knowledge, attitudes and skills to trainees. 3.37 Trainer Person who has knowledge and skills in a specified subject area and the ability and training to transfer them to others. Trainers are proficient (expert) in the skills and activities in which they provide training. In addition, they have received specialized training and practice in training skills on Train the Trainer concept. 3.38 Training Plan A document that provides the Mentor or On-the-Job Trainer with guidelines on how training should be conducted for consistency and effectiveness. 3.39 Up-graded Employee An up-graded employee is a person (e.g., Boardman or technician) who has completed the Up-graded certification requirements. The role of the Up-graded is stand-in for a Shift Supervisor on a Process Unit or Mechanical Craft. 3.40 Abbreviations API American Petroleum Institute PFDs Process Flow Diagrams DDC Document and Data Controller PHA Process Hazards Analysis EPCLEngro Polymer & Chemical Ltd PHR Process Hazard Review EPA Environmental Protection PLC Programmable Logic Controllers HRD Human Resources Department, PPE Personal Protective Equipment Head office Karachi HSE Health, Safety and Environment PSI Process Safety Information JSA Job Safety Analysis QSP Quality System Procedure KI Knowledge Index SIC Shift In-charge, coordinator MOC Management of Change SMP Safety Management Practices T/A Trade Apprentice P&IDs Process and Instrumentation TNA Training Needs Analysis DTC Departmental Training Committee TAE Trainee Asst. Engineer Prepared By; Ammar Hussain Reviewed By: SMF/ FIQ/ RT Approved By: Jahangir Waheed Document # HSE / PSM / Level-II / 09 Date Prepared: December 2008 Page 11 of 35 Revision: 02 Revision Date: October 2016 SECTION-4 TRAINING REQUIREMENTS This section provides procedure describing training requirements; EPCL training model, essential training areas, refresher training guidelines and details of training programs. Properly trained and performing personnel are a requirement for keeping process equipment and machinery operating safely. Many serious incidents have been caused by lack of adequate training. In particular, personnel must be trained on how to maintain the operating conditions within the specified range and when to shutdown if conditions go outside the specified range. Prior to operating a process, each employee should be trained in an overview of the process, and in the safety and health hazards, emergency operations, including shutdown, and safe work practices. Similarly, personnel in Mechanical, Projects, Process, Instrument, Electrical, Inspection and Machinery shall be trained. Maintaining of these trained personnel is of utmost important for safety and smooth operation of the site. Refresher training is also required to maintain high levels of proficiency. The training include following features: 4.1 General Features 1. An inventory of the basic skills necessary to perform a given job is developed and basic skills training provided where necessary to ensure that all personnel have at least a minimum level of proficiency. 2. Systems are in place to provide initial and ongoing training to meet job requirements. 3. The management shall ascertain that each employee involved in operating and maintaining the process has received and understood prescribed training. 4. Additional training must be provided as the process and facilities are changed, a system shall be in place to ensure employees receive appropriate training prior to commencing the new or expanded facilities. 5. New and reassigned personnel receive training in an overview of the process and in specific safety and health hazards. See Section 4.2 below for details. 6. Appropriate basic skills training and job specific training programs are in place. See Section 4.2 below for details. 7. Refresher training to operations employee is imparted at least every three years to ensure that the he /she understands and adheres to the current operating procedures of the process. See Section 4.2.5 below for details. For maintenance / technical employees line management shall determine the appropriate frequency of refresher training. 8. Provide specific training and drilling in emergency response on a periodic basis. Training should cover safe and prompt shutdown of facilities; accounting for personnel; notification of affected parties, site and local emergency response groups, regulatory agencies, fire fighting efforts, etc. For details see PSM 22 - Emergency Planning and Response. 9. Training requirement for manufacturing personnel should be well established and followed. Core training employee categories are mentioned in section 4.3 Who Gets the Training. Prepared By; Ammar Hussain Reviewed By: SMF/ FIQ/ RT Approved By: Jahangir Waheed Document # HSE / PSM / Level-II / 09 Date Prepared: December 2008 Page 12 of 35 Revision: 02 Revision Date: October 2016 10. A documented procedure shall be in place for qualified instructor criteria. See Section 4.4 on the job trainer and mentor qualification for details 11. Information and manuals related to employees’ day-to-day work should be made accessible to him. The document types are: PSM Level-1 / 2 procedures, Production, I&E, Training and Mechanical Procedures. For details see PSM 15 – Procedure & Performance Standards. 12. The basic elements of effective training to be included are: Classroom training – explaining how and why procedures are written the way they are. Field Training – to complete the classroom training and to show “how” and “where” Hands-on demonstration by the trainee. Qualification testing – including, but not limited to, written testing. The management must verify that the employee understood the training. Use of skill labs, demo simulators, practical simulations to be considered as appropriate. 13. Safety orientation and indoctrination shall be done for new / transferred employees. 14. TNA survey of employees to be done at an interval not to exceed 2 years. See Training Needs Analysis 6.2 below for details. 15. Training programs are assessed and updated as needed to assure effectiveness. 16. In addition to the ongoing measures indicated for each requirement there shall be an assessment of the training system through PSM internal / external audits at defined interval. 17. Training records shall be maintained that shall contain following: Identity of the employee, Description of the material covered Date of the training, and Means used to verify that the employee understood the training. 18. A system shall be in place which allows all personnel to get information of their scheduled / completed training. 19. A system shall be in place through which employees get information of their testing and recording of post / craft training results. 20. Provide training to employees unless desired results are achieved. 21. Training Manager and training coordinators are the overall administrator of the training system. See Section - 7 Responsibilities for details. 22. Management shall maintain adequate training resources to keep the training program effective. See Measuring Effectiveness for details. 23. Periodic auditing and assessment of employee’s performance to ensure compliance with the established procedures. This may be done through interviews and observations, or more systematically in combination with formal job knowledge review procedures such as a job cycle check. Job Cycle Check procedure is given in PSM 15 – Procedure & Performance Standards. 24. Key positions are defined and identified. There is a process in place to ensure stand-in checklists are filled when an employees is upgraded. 25. Holders of key positions and their stand-ins are trained in necessary health, safety and environmental aspects of their jobs before assuming their responsibilities. 26. Before implementing the emergency response plan, the management shall designate and train a sufficient number of persons to assist in the safety and orderly emergency evacuation of employees. Prepared By; Ammar Hussain Reviewed By: SMF/ FIQ/ RT Approved By: Jahangir Waheed Document # HSE / PSM / Level-II / 09 Date Prepared: December 2008 Page 13 of 35 Revision: 02 Revision Date: October 2016 4.2 Contractor Training Management shall consider contractor training as and when required, for complete guidelines see PSM 12 Contractor Safety Management. 4.3 Essential Training Areas / Topics Each employee assigned to process shall receive training in the following, as appropriate: 4.4 Process Overview An overview of the process, emphasizing on: Process flow diagram Major process reactions and chemicals 4.5 Safety, Health and Environment Training 1. Management shall provide training to each employee who is required by this section to use PPE. Each such employee shall be trained to know at least the following: When PPE is necessary What PPE is necessary How to properly don, doff, adjust Adjust and wear PPE The limitations of the PPE The proper care, maintenance, useful life, and disposal of the PPE. 2. Each affected employee shall demonstrate an understanding of the training specified in paragraph above and the ability to use PPE properly before being allowed to perform work requiring the use of PPE. 3. When management / supervision find any gap in the above requirements (as per TNA), such employee shall be retrained. Circumstances where retraining is required include, but are not limited to: Changes in the workplace render previous training obsolete, or Changes in the types of PPE to be used render previous training obsolete; or Inadequacies in an affected employee's knowledge or use of assigned PPE indicate that the employee has not retained the requisite understanding or skill. 4. Specific safety and health hazards of chemicals 5. Precautions necessary to prevent exposure 6. Control measures to be taken if exposure occurs. 7. Emergency response and control procedures. For details, see Minimum Training Requirements for Emergency Squad in PSM 22 - Emergency Planning and Response. 8. Emergency operations (including shutdown) 9. Special or Unique hazards, e.g., Furnace related hazards at EDC VCM Area 300 post. Orientation on appropriate environmental procedures and work practices at the start of their work assignments. Prepared By; Ammar Hussain Reviewed By: SMF/ FIQ/ RT Approved By: Jahangir Waheed Document # HSE / PSM / Level-II / 09 Date Prepared: December 2008 Page 14 of 35 Revision: 02 Revision Date: October 2016 4.6 Basic Skills Training Basic training as required for the assignment: 1. Fundamentals of equipment operation, such as pumps, valves, filters, distillation columns 2. Fundamentals of instrument and interlocks, input / output devices 3. Electrical equipment, generators, motors, transformers etc. operation 4. Construction of Valves, Vibration measuring equipment, Lubrication, Sleeve bearings, Coupling alignment, Mechanical seals, Labyrinths O-rings and closures, Packing, Rolling contact bearings, Couplings, installation & removal, Surface grinder, Lapping Machine, Electric arc welding. 4.7 Job Specific Training Job-specific training includes: 1. Operating procedures training for normal, start-up, shutdown, and emergency handling / shutdown conditions. 2. Actions required to keep the process within the desired operating range, and an understanding of the consequences of going outside the desired operating range. 3. Must understand when shutdown is necessary. 4. Safety and health hazards associated with the job. 5. Safe work practices applicable to the employee’s job tasks. 4.8 Refresher Training Some of the refresher training guidelines are given below. 1. Refresher training shall be provided to operations employee at least every three years to ensure that the employee understands and adheres to the current operating procedures of the process. For maintenance, Instrument, Electrical or other Technical employees’ line management shall determine the appropriate frequency of refresher training. 2. The refresher training shall include assessments of employee knowledge and skills relative to job requirements as per TNA. 3. Refresher training requirements for all personnel to be in compliance with TNA. 4. Employee’s feedback on type of methods used and interval of training shall be incorporated in the training program and TNA. 5. Some refresher training frequencies are given in table below. For detailed frequency information, see PSM resource material. Prepared By; Ammar Hussain Reviewed By: SMF/ FIQ/ RT Approved By: Jahangir Waheed Document # HSE / PSM / Level-II / 09 Date Prepared: December 2008 Page 15 of 35 Revision: 02 Revision Date: October 2016 Source of Frequency of Who is Included Contents Regulation Training Train & inform employees in proper evaluation procedures; duties of those who remain for critical operations; who to Initial assignment, when Employee Emergency account plan changes, when Plans & Fire for all after evacuation, rescue & medical All Employees employee's Prevention 29 CFR duties; preferred means of reporting fires responsibilities in plan 1910.38 & emergencies’ apprise of fire hazards of change materials & processes employee is exposed to. Storage and Handling All employees Initially upon The proper loading, unloading, handling of VCM & Chlorine 29 required to handle assignment & procedures; & proper action to take in the CFR 1910. 111 VCM & Chlorine periodically thereafter. event of an emergency. Those employees who Upon initial issue of The limitations of the equipment as well Eye & Face Protection must wear protection equipment & as as any precautions by the manufacturer 29 CFR 1910. 133 for the eyes & face. conditions change. must be transmitted to the user. The proper selection use & care of the respirator. Also instruction should be provided for routine use as well as possible emergency uses. This includes the safe use of Respiratory Protection All employees who Initially, and at least respirator in dangerous atmospheres that 29 CFR 1910. 134 use respirators. annually thereafter. may be encountered. This training shall provide the employees the opportunity to handle, wear, be fitted and wear in test atmosphere. This includes how to wear, how to adjust the respirator. Those employees where fire extinguishers are for To recognize the type of 29 CFR1910.156 Portable Fire their use. And those Upon initial assignment fire, properly operate the appropriate fire Extinguishers designated to use & at least annually extinguisher how to fight the fire & when 29 CFR 1910.157 firefighting thereafter. to leave if the fire becomes equipment as part uncontrollable. of the emergency action plan. Initially upon assignment & annually To be able to adequately inspect, Fire Extinguishing Those employees who review their training to maintain, operate repair system. System, General inspect, maintain, & keep them up-to-date (Manufacturer commonly outlines 29 CFR 1910.164 operate the system. on the functions they necessary skill levels.) must perform. Initially upon Those employees who assignment & annually To be able to adequately inspect, Fire Detection service, maintain, or review their training to maintain, operate repair system. System test keep them up-to-date (Manufacturer commonly outlines 29 CFR 1910. 164 the system. on the functions they necessary skill levels.) must perform. Prepared By; Ammar Hussain Reviewed By: SMF/ FIQ/ RT Approved By: Jahangir Waheed Document # HSE / PSM / Level-II / 09 Date Prepared: December 2008 Page 16 of 35 Revision: 02 Revision Date: October 2016 Any operations in their area where hazards are present; the standard, location Hazard All employees who Upon initial assignment & availability of written program; methods Communication work in areas & whenever a new to detect chemicals; measures employees 29 CFR 1910. containing hazardous hazard is introduced can use to protect themselves; emergency 1200- chemicals. into the work area. procedures; details of HC programs (i.e. labeling system, MSDSs etc.) Upon initial assignment Employees who are Electrical & periodically to Such that the employee is familiar with the required to perform 29 CFR 1910. Sub maintain competency & construction & operation of the electrical work activities on Part S proficient work equipment & the hazards involved. electrical systems. practices. 4.9 Who Gets the Training Training is provided to following crafts, posts or positions: 4.10 General categories 1. Trade Apprentices (Technical) 2. Graduate Trainee Engineers 3. Employees TIER III & TIER IV 4. TAEs Production Area Engineer of PVC I, PVC II, UTY/CCPP, CA, EDC VCM units Maintenance, I&E and Lab technicians Production, Maintenance and I&E First line supervisors Process, project, inspection, machinery, and safety engineers (also includes any expansion / special project engineers) 5. Refreshers and professional skill development training for all employees (TIER III & TIER IV) as per need and job functions. 6. Employees whose assignment has been changed as per plan / need. 4.11 Emergency Response and Fire Fighting 1. Train and inform employees in proper evaluation procedure 2. Duties of those who remain for critical operations (Operations Personnel and Emergency Squad) 3. How to account for all after evacuation 4. Preferred means of reporting fires and emergencies 5. Apprise of fire hazards of materials and processes employee is exposed to. 6. Refer PSM 22 - Emergency Planning and Response for more details. 4.12 Storage and Handling of Hazardous Materials All employees required to handle hazardous material shall get following training: Prepared By; Ammar Hussain Reviewed By: SMF/ FIQ/ RT Approved By: Jahangir Waheed Document # HSE / PSM / Level-II / 09 Date Prepared: December 2008 Page 17 of 35 Revision: 02 Revision Date: October 2016 1. Handling procedures 2. Proper actions to be taken in the event of an emergency. 4.13 Respiratory Protection All employees who use respirators shall get respiratory protection training initially and at least annually thereafter. 4.14 On-the-Job Trainer and Mentor Qualifications On-the-job trainer and mentor qualification requirements should be established and documented for all key position trainings, including managers, first line supervisors, technicians and operators as On-the-Job trainers. These requirements shall include On-the-job trainer and Mentor qualification, experience, ability and communication of techniques to the trainee etc. Note: As a minimum, 1/5th of the population may be trained to be mentors. Mentors %age can be increased based on requirement. The training of some of the skills (mentioned below) is imparted by training section (train the trainer concept). Communication skills; Written / Verbal How learning works 4.15 Mentors Following shall be considered for instructors: 1. Must be presently working at the same post for which they are going to be On-the-job trainers / mentor. 2. Shall have relevant and up-to-date information of work practices, procedures, techniques etc. 3. Shall have adequate experience for the job being mentored. 4. Knows and follows good delivery techniques. See Section 5.1 Basic Elements of Effective Training for details. 5. Knows adult learning theory and instructional principles to develop mentor training program 6. Communicates effectively through speech, writing, listening 7. Maintains current knowledge of plant modifications 8. Recognizes and respond to disruptive trainee behavior 9. Counsels trainees in career planning and concerns relating to training problems 10. Provides remedial training techniques / materials to trainees 11. Understands how training relates to other company/plant functions 12. Analyzes training needs for the position 13. Develops training plan Prepared By; Ammar Hussain Reviewed By: SMF/ FIQ/ RT Approved By: Jahangir Waheed Document # HSE / PSM / Level-II / 09 Date Prepared: December 2008 Page 18 of 35 Revision: 02 Revision Date: October 2016 14. Constructs learning objectives 15. Chooses training method 16. Develops performance test items (oral, written, demonstration etc) 17. Analyzes trainee performance based on discussion, reviews 18. Analyzes personnel performance problems on the job. 19. Establishes and maintains positive working relationships with trainee 20. Conducts discussions 21. Responds to trainee questions 22. Reviews demonstrations / hands-on exercises 23. Discusses training performance with trainee 4.16 On-the-Job Trainer Following shall be considered for On-the-Job Trainer: 1. Must be presently working at the same post for which they are going to be On-the-job trainers / mentor. 2. Shall have relevant and up-to-date information of work practices, procedures, techniques etc. 3. Shall have adequate experience for the job being mentored. 4. Maintains current knowledge of plant modifications 5. Knows and follows good delivery techniques. See Section 5.1 Basic Elements of Effective Training for details. 6. Establishes and maintains positive working relationships with trainee 7. Communicates effectively through speech, writing, listening 8. Recognizes and respond to disruptive trainee behavior 9. Conducts training as per training plan. 10. Performs demonstrations / hands-on exercises 11. Conducts discussions 12. Responds to trainee questions 13. Discusses trainee performance with trainee 14. Provides remedial training materials to trainees Prepared By; Ammar Hussain Reviewed By: SMF/ FIQ/ RT Approved By: Jahangir Waheed Document # HSE / PSM / Level-II / 09 Date Prepared: December 2008 Page 19 of 35 Revision: 02 Revision Date: October 2016 SECTION-5 TRAINING MODEL An effective training system results in, increased safety awareness, increased productivity, fewer errors, reduced waste, improved customer relations, lesser time spent in direct supervision and higher morale. 5.1 Basic Elements of Effective Training Following are guidelines for effective training: 1. Classroom training to explain “how” and “why” 2. Field training to show “where” 3. Skill demonstration by trainee, for this following techniques may be applied: Training simulators Hands on training – field demonstration 4. To assess whether person is competent to independently do the task, qualification testing shall be done. Following techniques can be used: Written test papers / Verbal Field demonstration utilizing standby / surplus equipment Prepared By; Ammar Hussain Reviewed By: SMF/ FIQ/ RT Approved By: Jahangir Waheed Document # HSE / PSM / Level-II / 09 Date Prepared: December 2008 Page 20 of 35 Revision: 02 Revision Date: October 2016 5.2 New Hire / Transfer site Safety Indoctrination Prepared By; Ammar Hussain Reviewed By: SMF/ FIQ/ RT Approved By: Jahangir Waheed Document # HSE / PSM / Level-II / 09 Date Prepared: December 2008 Page 21 of 35 Revision: 02 Revision Date: October 2016 5.3 TRAINING MODEL Prepared By; Ammar Hussain Reviewed By: SMF/ FIQ/ RT Approved By: Jahangir Waheed Document # HSE / PSM / Level-II / 09 Date Prepared: December 2008 Page 22 of 35 Revision: 02 Revision Date: October 2016 SECTION-6 TRAINING PLANS Training plan shall follow a model that consists of: 1. Determining if Training is Needed 2. Identifying Training Needs 3. Identifying Goals and Objectives 4. Developing Learning Activities 5. Conducting the Training 6. Supervision ensuring Training is Utilized On-the-Job 7. Evaluating Program Effectiveness 8. Improving the Program 6.1 Training Plan Cycle The Training Plan Cycle is: 1. Conduct TNA Survey 2. Develop Training Plan 3. Deliver Training 4. Analyze success/relevance against business plan Identify performance gaps between point 3 and 4 above. Identify ways / options to fill performance gaps: e.g. 1. Change working environment e.g. terms and conditions/practices 2. Change the resource input 3. Change the job/tasks 4. Change the team 5. Change the person Change the person: identify knowledge, skills, attitude training needs and ways to meet them: e.g. coaching/mentoring/training course/in service team building Re-analyze training needs in relation to business needs at the end of this process the next stage would be to develop a Training Plan. 6.2 Training Needs Analysis A training needs analysis (TNA) should be part of a continuous process to monitor the training requirements of employees. For effective training, the approach to training must be analytical and systematic. This analysis starts with the study of training needs. Prepared By; Ammar Hussain Reviewed By: SMF/ FIQ/ RT Approved By: Jahangir Waheed Document # HSE / PSM / Level-II / 09 Date Prepared: December 2008 Page 23 of 35 Revision: 02 Revision Date: October 2016 TNA is: 1. A tool which supports the development and efficiency of an organization and its members 2. A way of helping employees work to a defined standard 3. Part of a process which integrates training with the business or development plan of an organization. TNA involves the detailed, objective assessment of employees (learners’) needs and the specification of cost-effective training solutions. Effective TNA will ensure that: 1. All performance and associated learning needs are identified 2. Redundant training is avoided 3. Appropriate, cost-effective solutions are defined 4. Training budgets are objectively justified and effectively used 6.3 TNA Requirements Following are the requirements of TNA: 1. Training Needs Analysis (TNA) shall be conducted for all employees (TIER III & TIER IV) up to Unit Manager position. 2. Training Needs Analysis (TNA) shall be conducted by line managers / supervisors on a frequency not to exceed 02 years or on need basis to identify the training needs. 3. Each department / section designs and conducts TNA on the basis of its own job functions either individual or team basis. 4. Employee’s current job or future plans requirements shall be considered in TNA. 5. On transfer of employee to new section, the TNA shall be revived as per applicable basic / technical knowledge requirements. 6. Line managers to develop skill survey forms as per the requirement of the particular section / craft or related key skill areas. 7. The skill survey forms may be designed in a manner so as to capture knowledge / skills of an employee: Overview of process. Basic knowledge of relevant job. Critical equipment or process. 8. The skill survey form used for TNA has activities / skill dimension in columns and employees names in rows. 9. The skill / knowledge shall be marked on a scale of 1 to 4, where 4 is the lowest level of skill / knowledge. This skill / knowledge assessed in numerical form is referred as Knowledge Index (KI). Prepared By; Ammar Hussain Reviewed By: SMF/ FIQ/ RT Approved By: Jahangir Waheed Document # HSE / PSM / Level-II / 09 Date Prepared: December 2008 Page 24 of 35 Revision: 02 Revision Date: October 2016 10. Averaging any individual’s KIs of various dimensions, will generate an average KI. Average KI can be denominated by any abbreviation by departments / sections. Scale Explanation 1 Fully capable, can handle job independently. The employee has complete knowledge of equipment and is fully capable of handling any job independently. 2 Knowledgeable, needs guidance occasionally. The employee is knowledge-able on this equipment. To handle jobs he occasionally needs guidance or help. 3 The employee has some knowledge but needs training, guidance and exposure. Can handle routine or non- critical activity on job / task under close supervision at all times. He needs training and more exposure on this post. 4 The employee has knowledge. Ignorant, no exposure – cannot handle job, needs training and evaluation. 6.4 Training Plan Development Following are guidelines for training plans development: 1. Training plans to be developed by respective Unit Managers / Section Heads or Section Incharges of various sections. 2. TNA survey shall be considered for training plans development. 3. Plan may be developed on a single worksheet, having timeline (months, quarters etc) in columns and courses in rows. 4. While developing the plan, the course contents shall be explained to faculty (person who has to deliver the course) and his consent and understanding on course contents and time shall be taken. 5. The final plan shall be circulated to all the relevant interfaces, including faculty, training coordinators, participants (trainees) and department managers. 6. The training plan stewardship and coordination lies with training coordinators or any other assigned person by department manager. 7. Managerial competencies training plans are developed by respective department managers and are stewarded and coordinated by Human Resource Department. 8. For GTEs & TIER III, dimensions for training plans are: Basic skills training Prepared By; Ammar Hussain Reviewed By: SMF/ FIQ/ RT Approved By: Jahangir Waheed Document # HSE / PSM / Level-II / 09 Date Prepared: December 2008 Page 25 of 35 Revision: 02 Revision Date: October 2016 Job specific skills training Managerial / supervision competencies training 9. For TA, TAE & Asst Engineers, dimensions for training plans are: Basic skills training Job specific skills training 10. Training plans are used by the on-the-job trainer / mentor, as a guide in preparing the Operator / Technician or trainee being able to meet the requirement for skill assessment / certification. 6.5 Training Plan – General Features 1. Employee orientation to be done soon after joining. 2. Area / unit to be allocated to employee by the respective Department Manager / Section Head. 3. Training Plan and Schedule is given by the respective Unit Manager / Section Head. 4. The training plan shall include following: Dates / Milestones for: Training plan issuance, Training plan start, Interim reviews and tests, Training completion date. Names of training mentor and supervisor On-the-job and other training activities planned and their duration Assessment by on-the-job trainer / mentor and Unit Manager / Section Head at regular intervals. 5. At the end of training, employee evaluation shall be conducted through skill certification process by a board comprising of two or more unit managers / designates. Recommendation for hiring is developed based on interim and final evaluations. 6.6 Training Schedule The training section is responsible for scheduling the required courses and class room training for employees. 6.7 Implementation Training plans implementation shall be done by line management and stewarded, facilitated by training coordinators or HRD. 6.8 Training Plans – Facilitation by Training Department Following are training section facilitation for planned trainings: 1. Stewards, prompts and facilitates different departments of the Manufacturing Division to ensure that training is being conducted as per training plan. Prepared By; Ammar Hussain Reviewed By: SMF/ FIQ/ RT Approved By: Jahangir Waheed Document # HSE / PSM / Level-II / 09 Date Prepared: December 2008 Page 26 of 35 Revision: 02 Revision Date: October 2016 2. Ensures that planned training is imparted, and related training process is followed through follow up. 3. Development of status report of departments training plans in technical areas of training and its updating. 4. Training coordinator assists the respective department managers for development of annual training plans in coordination with the interfaces and areas. 5. Arranges Professional skill development courses by internal or external faculty. 6.9 Training Records Record keeping requirements for initial training and refreshers training include: 1. Training records shall be maintained that shall contain following: Identity of the employee, Description of the material covered Date of the training, and Means used to verify that the employee understood the training. Identity of instructor 2. A system shall be in place which allows all personnel to get information of their scheduled / completed training. 3. A system shall be in place through which employees get information of their testing and recording of post / craft training results. 6.10 Budget Training budget is prepared and approved every year along with other Business Line Plans for every department by respective units / sections. Prepared By; Ammar Hussain Reviewed By: SMF/ FIQ/ RT Approved By: Jahangir Waheed Document # HSE / PSM / Level-II / 09 Date Prepared: December 2008 Page 27 of 35 Revision: 02 Revision Date: October 2016 SECTION-7 RESPONSIBILITIES Line management is responsible for training of individuals. The responsibilities includes, TNA survey, training plans development, imparting effective training and measuring the effectiveness of training. 7.1 EPCL Employees TIER III , TIER IV, Trade Apprentices, TAEs or GTEs All EPCL personnel are required to complete the training requirements which have been identified for their Job Position. It is imperative that an employee makes maximum efforts to improve his knowledge and ability to prepare himself for the demands of his work situation. The management will, therefore, only supplement the efforts of an employee for self-development by providing training opportunities for the acquisition of greater knowledge, skills and ability by employees. The employee is required to: 1. Complete the knowledge and skill requirements of the position identified for the job. 2. Agree on the given training plan, and achieve the desired results. 3. TIER III clear the board reviews where applicable. 4. Clear process post, mechanical, I&E or other crafts skill assessment. 5. Actively participate in planned training and refresher training 6. All classroom training require employee to sign a class room training attendance and complete an evaluation form at the end of the course. 7.2 Training Department Organization and Responsibilities The training section is responsible to ensure every employee receives the training information, to meet the requirements in a timely manner, and provide the individual with the validation process to critique the training module(s) / course(s). 1. Training section is managed by training coordinators reporting to Training manager. 2. The training coordinators report to Training Manager administratively and carry out functional assignment of the respective Department Managers. 3. Training section is responsible for training and administration of internees of different Universities. 4. Training Section will steward, prompt and facilitate different departments of the Manufacturing Division to ensure that training needs analysis is being done, training planned and imparted, and related training process is being followed. 5. Training section is responsible for management of Training Library which includes Training Video's, training books, plant operation manuals, post manuals, Slide show modules. 6. Provide the audio / visual aids, stationary and office assistance services for the training courses and programs being held in the training center by respective departments depending upon the availability of equipment Prepared By; Ammar Hussain Reviewed By: SMF/ FIQ/ RT Approved By: Jahangir Waheed Document # HSE / PSM / Level-II / 09 Date Prepared: December 2008 Page 28 of 35 Revision: 02 Revision Date: October 2016 7.3 Training Manager Training Manager (a manager to whom training section is reporting) is the administrator of the training system. Responsibilities are to ensure all the training requirements are implemented at EPCL. 7.4 Training Coordinators Role Training coordinators are assigned specific or general training related activities like preparation or review of TNA survey, assessments, and plans for a department. Training coordinators are responsible for following and shall also ensure that: 7.5 General 1. Schedule and facilitate classroom training for employee core training and other training required. 2. Arrange the logistics for training sessions and courses. 3. Initiate newly hired trade apprentices or internees site safety indoctrination program. 4. Trade apprentices recruitment, administration and maintenance of their training records. 5. Selection and training guidelines for trade apprentice are being followed. 7.6 Training Plans / Activities 1. Training plan is developed based on the results of skill survey. 2. Training activities are progressing as planned. Review monthly non-compliance training reports. 3. Training matrices are available for all departments and provide the following information: Training modules and classroom courses required. Frequency module or course must be taken Knowledge training required Skills training required 4. Upkeep and availability of classrooms for training courses and programs by different departments in the EPCL training center as per predefined and issued schedules. 7.7 Skill Certification 1. Skill of trade apprentices, TAEs, Asst Engineers, SICs and technicians is being tested through the Skill certification Checklist. 2. All the relevant Skill certification Checklist are maintained up to date and are available with them. 3. Conduct Skill certification test as and when required. 4. Keep records of Skill certification and their results against each employee. 5. Follow up with the departments for development and updates of Skill certification test papers as per procedure. 6. Participate in skill assessment / certification and board reviews. Prepared By; Ammar Hussain Reviewed By: SMF/ FIQ/ RT Approved By: Jahangir Waheed Document # HSE / PSM / Level-II / 09 Date Prepared: December 2008 Page 29 of 35 Revision: 02 Revision Date: October 2016 7.8 Follow-up and Reports 1. Issue status report of each department in technical areas of training and keep records updated. 2. The skill survey is conducted bi-annually (after every two years) and the results are analyzed to identify the training needs of the technical personnel. 3. Distribute compliance / non-compliance training reports to departments in a timely manner. 7.9 Training Facilities / Record Upkeep 1. All the training modules are preserved in the training section. 2. Employee training record is being maintained as per training plan requirement. See section 6.3.1 Training Plan – General Features. 3. Maintain training section library. 4. All the procedures which are marked to training section, are available in adequate quantity to be distributed to trainees / employees for training purpose. 5. The training coordinators are responsible for the new / updated procedures communication to the affected employees. 6. Mechanical and I&E coordinators to maintain the Mechanical and I&E Skill labs to facilitate the training process in future. 7. Appropriate equipment and facilities suitable for EPCL operations will be provided and maintained by the respective departments. SECTION-8 MEASURING EFFECTIVENESS Prepared By; Ammar Hussain Reviewed By: SMF/ FIQ/ RT Approved By: Jahangir Waheed Document # HSE / PSM / Level-II / 09 Date Prepared: December 2008 Page 30 of 35 Revision: 02 Revision Date: October 2016 Measuring effectiveness of imparted training is a vital tool for maintaining the necessary skills of employees critical to site safety and business. The procedure also describes assessment of effectiveness of imparted training. Effectiveness of the training is ascertained by clearing of necessary examinations by the individual, through skill assessment / certification, professional examinations and performance in assignments – fewer repairs / fewer repetitions / root cause analysis, and in performance evaluation. 8.1 Evaluation Training program evaluation process shall include: 1. On-the-Job Effectiveness 2. Skill certification / board review 3. Tests at the end of training sessions 8.2 On-the-Job Effectiveness On-the-Job trainer or mentor shall review the progress of the trainee and measure the effectiveness of On-the-Job training. 8.3 Skill Assessment / Certification Employees– Asst Engineers, Welders, Field Machinists, Metal craft, Auto technician, Shop Machinist, Instrument and Electrical technicians – in Production, Mechanical, I&E department are evaluated through skill assessment / certification process for minimum competence required for the specific job / task. See skill certification forms in section 8.2 Qualification Requirements for Asst Engineers, Emergency Squad Members and Technicians below 8.4 Qualification Requirements for Asst Engineer, Emergency Squad Members and Technicians Purpose When training of Asst Engineers, Emergency Squad Members and Technicians has been completed, and qualification audits made for the tasks associated with a particular job, the Asst Engineers /DCS Boardman Skill Certification Form in Section 8.2.5 below should be completed, signed, and a copy forward to the training section. After initial qualification, employees will need to re-qualify every three years or on change of assignment. For technicians, skill assessment is carried using Skill Assessment Forms. Skill Assessment / Certification Following are guidelines on skill assessment / certification requirements: Prepared By; Ammar Hussain Reviewed By: SMF/ FIQ/ RT Approved By: Jahangir Waheed Document # HSE / PSM / Level-II / 09 Date Prepared: December 2008 Page 31 of 35 Revision: 02 Revision Date: October 2016 1. Skill certification shall be done for: All Asst Engineers at operating plants, namely UTY/CCPP, CA, PVC I, PVC II & EDC VCM units. Members of Emergency Squad on Emergency Planning / Response 2. Skill Assessment shall be carried out for: All trades in mechanical, instrument and electrical departments Technicians working in Laboratory, Inspections, Machinery, etc. 3. Each Asst Engineers, Emergency Squad Member and Technician should by their signature indicate their confirmation of safety training, process training, emergency response training and job task training. 4. The Asst Engineers, Emergency Squad Member and Technician should provide the name, payroll number, area, jobs qualified for, signature, and data. 5. A separate form should be used for each individual Asst Engineers / Emergency Squad Members and Technicians. 6. The member of line supervision that is responsible for the operator / technicians, while in consultation with each Asst Engineers / Emergency Squad Members and Technicians must complete the Management Statement. 7. A copy of the completed form must be sent to the training section / coordinators and employees personal file. 8. An original completed form will be placed in the units training file and entered into the electronic records system. 9. All shift supervisors, shift incharges, relevant mechanical, I&E, Technical supervisors / engineers shall be informed through e-mail by unit manager about employee skill assessment / certification. 8.5 Skill Re-Assessment / Certification A skill certification may expire or may be cancelled under following circumstances: 1. If a skill certified Asst Engineers has not worked on that specific post for more than six months. 2. If maintenance or I&E or any other technician has not performed that particular task or job (welding, PSV calibration etc.) for more than 1 year. 3. Re-certification after 3 year will be done by the respective departments 4. If an individual is found to be inadequate for that particular job, not performing as per requirement or other disciplinary problems. In such cases, a skill re-certification is necessary before deploying that person on that particular job. The process of certification will remains the same with few exemptions as mentioned in the skill certification form on next page. SECTION-9 PERFORMANCE Prepared By; Ammar Hussain Reviewed By: SMF/ FIQ/ RT Approved By: Jahangir Waheed Document # HSE / PSM / Level-II / 09 Date Prepared: December 2008 Page 32 of 35 Revision: 02 Revision Date: October 2016 Establish programs designed to ensure that personnel handling hazardous materials are fit for duty and are not compromised by external influences, including alcohol and drug abuse 9.1 General Features The program shall include the following: 1. Identification of jobs where diminished capacity might contribute to the release of a hazardous material or impair emergency response. 2. Establishment of practices to detect diminished capacity when hiring. 3. Development of appropriate facility security measures for search and seizure of contraband in accordance with legal requirements. 4. Development of a policy to deal with suspected cases of diminished capacity. 5. Establishment of appropriate rehabilitation / assistance programs for employees. 6. Communication of policies to employees. 7. All first line supervisors and section heads are trained to: Recognize symptoms of diminished physical or mental capability and To deal with them when suspected. 8. In case of physical impairment, Doctor and Employee Supervisor shall evaluate the extent of impairment and assign the employee appropriate job. 9. For long term physical impairments, consider assigning the employee on lighter jobs e.g., filing, procedures, office work etc. 10. Training should provide guidance on protecting the facility and personnel while respecting personal privacy rights. 11. Training shall also be provided to supervisors on how to deal with such impairments by medical personnel. For details refer to PSM 7 – Motivation & Awareness. SECTION-10 PSM CERTIFICATION Prepared By; Ammar Hussain Reviewed By: SMF/ FIQ/ RT Approved By: Jahangir Waheed Document # HSE / PSM / Level-II / 09 Date Prepared: December 2008 Page 33 of 35 Revision: 02 Revision Date: October 2016 It is mandatory for all permanent employees to get PSM certification within 06 months of joining the company. PSM Certification/ Test shall be done for following elements only; PSM 09 - Training & Development PSM 10 - Audits & Observations PSM 11 - Incident Investigation PSM 12 - Contractor Safety Management PSM 13 - Process Safety Information PSM 14 - Risk Assessment & Process Hazard Analysis PSM 15 - Procedure & Performance Standards PSM 16 - Management of Change – Facilities & Technology (Single Test) PSM 18 - Quality Assurance PSM 19 - Pre-Startup Safety Review PSM 20 - Mechanical Integrity PSM 21 - Management of Change - Personnel PSM 22 - Emergency Preparedness and Contingency Planning For GTEs and TAEs the deadline for getting PSM certification is 03 months since joining date and for TAs the deadline is 06 months. For details refer to Training Department Level III procedures/ guidelines. All employees including GTEs, TAEs and TAs must follow the process of certification through Online Tests and Interview with Safety Engineer and Safety Advisor. Note: Site Coordinator is authorized to conduct PSM interview of TA and TAEs only. However, final signoff on certificate shall be done by Safety Advisor. For permanent employee hiring specifically in production department, PSM certification can be taken within 04 months after their area skill certification. However, following PSM Elements need to be cleared by an individual before skill certification; PSM No 15 Procedures & Performance Standards; PSM 13 Process Safety Information; PSM No 14 Risk Assessment and Process Hazards Analysis; PSM No 19 Pre- start-up Safety Reviews & PSM 22 Emergency Preparedness and Contingency Planning. For details refer to Unit Management Manual. For permanent employee hiring (Cl-25 and above) the online test regime shall not be compulsory however they must appear for an interview to get certification. Prepared By; Ammar Hussain Reviewed By: SMF/ FIQ/ RT Approved By: Jahangir Waheed Document # HSE / PSM / Level-II / 09 Date Prepared: December 2008 Page 34 of 35 Revision: 02 Revision Date: October 2016 If an individual rejoins the company within one year he/ she shall be exempted from PSM online testing. However, he/ she shall appear for PSM final interview. Beyond this defined period recertification is mandatory. Prepared By; Ammar Hussain Reviewed By: SMF/ FIQ/ RT Approved By: Jahangir Waheed Document # HSE / PSM / Level-II / 09 Date Prepared: December 2008 Page 35 of 35 Revision: 02 Revision Date: October 2016 SECTION-11 REFERENCES AND LEVEL-3 PROCEDURES Following are EPCL document references related to this procedure: 11.1 References 1. I&E Manual 2. Maintenance Department Training Process 3. Safety, Environment Hygiene & Training 4. HRD's Inter personnel Skills Core program for TIER-III. 5. Training Section Function Organization 6. TA Hiring Process and Procedure 7. PSM Level-2 Procedures 11.2 Level-3 Procedures / Documents 1. Production Department Skill Certification Procedure. 2. Production Department Training Needs Analysis. 3. Process Engineering TNA. 4. Contract Inspectors Qualification Procedure. 5. Training Manual Prepared By; Ammar Hussain Reviewed By: SMF/ FIQ/ RT Approved By: Jahangir Waheed