Print_EN OILTAP® G PDF
Document Details
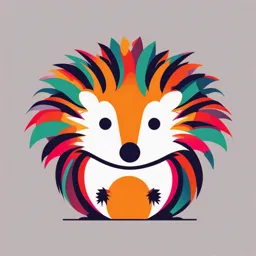
Uploaded by ValuableSugilite
Pink University
Tags
Summary
This document is a guide for maintenance and spare parts for OILTAP® G. It includes a table of contents, a spare parts list, and step-by-step instructions for various maintenance tasks.
Full Transcript
Table of contents Table of contents 1 Introduction......................................................................................................................... 4 2 Spare parts list..............................................................................................
Table of contents Table of contents 1 Introduction......................................................................................................................... 4 2 Spare parts list.................................................................................................................... 5 2.1 Spare parts list - OILTAP® G............................................................................................................. 6 2.1.1 Spare parts list - OILTAP® G - Type G III 1600.................................................................................................... 7 2.1.2 Spare parts list - OILTAP® G - Type G III 1602 - Modification set spark gaps................................................... 12 2.1.3 Spare parts list - OILTAP® G - Type G III 1602.................................................................................................. 13 3 Step-by-Step..................................................................................................................... 18 3.1 Note spare parts list.......................................................................................................................... 18 3.2 Tests and condition-based parts replacement at each maintenance............................................... 18 3.2.1 Checking de-energized tap-change supervisory control..................................................................................... 18 3.2.2 Removal of tap-change supervisory control........................................................................................................ 20 3.2.3 Connecting leads of protective spark gaps G20 000/21 000.............................................................................. 20 3.2.4 Connecting leads of protective spark gaps G22 000.......................................................................................... 21 3.2.5 Moving contact bridges - Checking transverse insulation................................................................................... 26 3.2.6 Checking travel of main contact - OILTAP® Type G 1601/1602/2002/2502/3000.............................................. 28 3.2.7 Checking bolt connection on contact bridge type G 1600................................................................................... 30 3.2.8 Contacts - Checking the solder joints.................................................................................................................. 30 3.2.9 Checking riveting - Drive shafts of contact system............................................................................................. 31 3.2.10 Energy accumulator - permissible clearances G 1600........................................................................................ 37 3.2.11 Max. permitted contact wear............................................................................................................................... 38 3.2.12 Drawing to determine the contact pressure of main contact type G 1600 / 3000 and G III 2002 / 2502............. 40 3.2.13 Cleaning the diverter switch drive tubes............................................................................................................. 43 3.2.14 Permissible wear differences between switching contact and transition contact................................................ 44 3.2.15 How to check the transverse insulation on the moving arcing contacts of the diverter switch insert.................. 45 3.2.16 Maintenance procedure for diverter switches type G with tap-change supervisory control................................ 48 3.2.17 Check of voltage-dependent resistors................................................................................................................. 49 3.2.18 Check and repair of mounting plates outer shielding rings................................................................................. 65 3.3 Checks at 120,000 operations.......................................................................................................... 67 3.3.1 Retrofitting hardened counterbolt with protection sleeve diverter switch type G1600......................................... 67 3.4 Parts replacement at 200,000 operations......................................................................................... 72 3.4.1 Replacement - Damper bolts and spring washers in the energy accumulator.................................................... 72 3.5 Parts replacement at 250,000 operations......................................................................................... 74 3.5.1 Retrofitting hardened counterbolt with protection sleeve diverter switch type G1600......................................... 74 EN 1 Table of contents 3.6 One-time retrofit and modifications................................................................................................... 79 3.6.1 Until 30 September, 2002 - Retrofitting holding segments of tap-change supervisory control........................... 79 3.6.2 Until 1 December 1987 - Replacement of damper bolts and spring washers in the energy accumulator........... 79 3.6.3 Until 1 December 1987 - Retrofitting counterbolts to switching column.............................................................. 81 3.6.4 Until 9 February 1984 - Replacement of resistor connecting leads.................................................................... 82 3.6.5 Until 1 April, 2004 - Replacement of transverse insulation................................................................................. 84 3.6.6 Replacement of connecting leads at protective spark gaps diverter switch type G 1602................................... 85 3.6.7 Until 31 December 1987 - Retrofitting hardened counterbolt with protection sleeve diverter switch type G1602.... 86 3.6.8 Retrofitting hardened counterbolt with protection sleeve diverter switch type G1600......................................... 94 3.6.9 Checking dowel pins in the energy accumulator................................................................................................. 98 4 Assemblies...................................................................................................................... 100 4.1 General........................................................................................................................................... 100 4.1.1 Replacement intervals diverter switch insert, selector switch insert, diverter switch oil compartment contacts and on-load tap-changer.......................................................................................................................................... 100 4.1.2 Checking de-energized tap-change supervisory control................................................................................... 103 4.1.3 Discussion regarding max. wear values on diverter switch insert G III 1600 on 15 March, 1983..................... 105 4.1.4 Location of pipes type V and G......................................................................................................................... 107 4.2 Contact system, switching element................................................................................................ 109 4.2.1 Checking travel of main contact - OILTAP® Type G 1601/1602/2002/2502/3000............................................ 109 4.2.2 Drawing to determine the contact pressure of main contact type G 1600 / 3000 and G III 2002 / 2502........... 111 4.2.3 Checking wear values diverter switch insert type G 1600................................................................................. 114 4.2.4 Checking bolt connection on contact bridge type G 1600................................................................................. 115 4.2.5 Moving contact bridges - Checking transverse insulation................................................................................. 115 4.2.6 Contacts - Checking the solder joints................................................................................................................ 117 4.2.7 Checking riveting - Drive shafts of contact system........................................................................................... 118 4.2.8 How to check the transverse insulation on the moving arcing contacts of the diverter switch insert................ 124 4.2.9 Until 1 April, 2004 - Replacement of transverse insulation............................................................................... 127 4.2.10 Max. permitted contact wear............................................................................................................................. 129 4.2.11 Permissible wear differences between switching contact and transition contact.............................................. 131 4.2.12 Retrofitting hardened counterbolt with protection sleeve diverter switch type G1600....................................... 132 4.3 Energy accumulator, gearbox......................................................................................................... 137 4.3.1 Energy accumulator - permissible clearances G 1600...................................................................................... 137 4.3.2 Pre-tensioning of energy accumulator spring after spring replacement G21 000............................................. 137 4.3.3 Checking dowel pins in the energy accumulator............................................................................................... 139 4.3.4 Until 1 December 1987 - Replacement of damper bolts and spring washers in the energy accumulator......... 139 2 EN Table of contents 4.4 Supporting cylinder/supporting bars, coupling shaft, switching column.......................................... 142 4.4.1 Removal and installation of switching column................................................................................................... 142 4.4.2 Check and repair of mounting plates outer shielding rings............................................................................... 148 4.4.3 Removing switching column type G1601/1602/2000/3000 (attachment to TS288007).................................... 149 4.4.4 Cleaning the diverter switch drive tubes........................................................................................................... 151 4.4.5 Until 31 December 1987 - Retrofitting hardened counterbolt with protection sleeve diverter switch type G1602.... 152 4.4.6 Until 1 December 1987 - Retrofitting counterbolts to switching column............................................................ 161 4.4.7 Removal of tap-change supervisory control...................................................................................................... 162 4.4.8 Until 30 September, 2002 - Retrofitting holding segments of tap-change supervisory control......................... 162 4.4.9 Maintenance procedure for diverter switches type G with tap-change supervisory control.............................. 163 4.5 Transition impedance and protective circuit................................................................................... 165 4.5.1 Check of voltage-dependent resistors............................................................................................................... 165 4.5.2 Resistor threaded stud on G 1600 and K tap changers.................................................................................... 181 4.5.3 Connecting leads of protective spark gaps G20 000/21 000............................................................................ 182 4.5.4 Replacement of connecting leads at protective spark gaps diverter switch type G 1602................................. 182 4.6 Oil compartment............................................................................................................................. 188 EN 3 1 Introduction 1 Introduction NOTICE Risk of personal damage or injury, damage to property or mal- function. If work is performed by insufficiently qualified personnel and/or safety in- structions are not observed, there is a risk of personal damage or injury, damage to property or malfunction. ► Safety, hazard and other information included in the MR operating in- structions for the relevant on-load tap-changer type must be observed! ► Please read the instructions carefully before starting work. ► The realization of the instructions below requires profound knowledge and experience that correspond to the knowledge acquired during a train- ing at MR about maintenance of the relevant on-load tap-changer type. ► It is absolutely necessary that the diverter switch insert (or selector switch insert, respectively) has been removed. 4 EN 2 Spare parts list 2 Spare parts list EN 5 2 Spare parts list 2.1 Spare parts list - OILTAP® G 6 EN Spare parts for on-load tap-changers Date: : Type G III 1600 Doc.: G97001.xls Pictures of parts Designation Pcs Part no. Remarks Sealing ring (ring gasket) 1 860049:01 Sealing ring ((flat gasket) 2 590144:01 for the first 10 OLTCs Gasket between OLTC head and transfromer 2 590371:01 Klingersil 2mm Safety diaphragm 1 020027:04 Coupling 1 025598:02 Bearing 2 452003 Circlip 2 452257 Nut 2 452147 Taper sleeve 2 401833:00 Gasket for safety diaphragm 1 590113:01 O ring for safety diaphragm 1 860093 Worm wheel 1 002264:98 Worm (with ball end) 1 025558:04 Worm (without ball end) 1 022436:03 Energy accumulator spring 456 kp 1 550682:01 Energy accumulator spring 260 kp 1 550676 (16 2/3 Hz) Disc 2 065753:00 TS82/185.1 Pawl spring 1 004302:01 Bolt 2 099682:02 Washer 2 099683:01 Tenter pin 2 451442 For this documentation we reserve all rights according to standard DIN 34, section 2.1. Page 1 of 5 Spare parts for on-load tap-changers Date: : Type G III 1600 Doc.: G97001.xls Pictures of parts Designation Pcs Part no. Remarks Left pawl, preassembled 1 002282:06 Right pawl, preassembled 1 003767:06 Counterbolt (1) 3 003854:08 from 02/68 on Cup spring (2) 30 401634:00 Cocking pin (3) 3 451457 Protection sleeve 3 073873:01 Counter bolt, complete 3 095114:01 up to 01/68 Dished washer 24 452364:00 Cocking pin 3 452425 Protective sleeve 3 078166:00 Gaskets for diverter switch oil compartment: Flange gasket 1 590314 Gasket 3x818x758 1 590593 O ring 700-10 2 860020 O ring 11-4 2 860020 Spring guide 1 from 04/76 on (Ref. 004303:02) Guide bushing (without ball bushing) 1 025605:04 Guide Bolt 1 002280:02 Ball bushing (linear bearing) 2 452165 Washer 1 025606:98 Circlip 1 452244 Pack of current strips 48 042529:00 Lock tab 48 006643:00 Fastening plate 48 042534:00 Countersunk screw 48 453112 Armature of switch. contact 24 048763:01 Armature of auxiliary contact 24 048762:01 For this documentation we reserve all rights according to standard DIN 34, section 2.1. Page 2 of 5 Spare parts for on-load tap-changers Date: : Type G III 1600 Doc.: G97001.xls Pictures of parts Designation Pcs Part no. Remarks Spring G III 1600 left 48 550218 Spring G III 1600 right 48 550219 Contact carrier 24 002293:03 Bolt 24 025668:03 Cocking pin 24 452437 Guide bridge 12 025678:98 Shims for fixed contact 48 013210:00 from 1/72 on Plate spring 192 452356 for above shims Tension lever 24 025676:03 since 10/76 - 3 mm longer Tension lever bolt 24 050548:00 with ring 24 050549:00 and taper pin 24 451443 prior to 2/72 retaining ring Drive shafts for auxiliary contact 12 002298:02 prior to 11/87 300000 - 400000 Use always SETERSATZ with indication "drilled" for order/offer Drive shafts for Switching contact, left 6 016763:01 Use always SETERSATZ Switching contact, right 6 002297:03 with indication "drilled" for order/offer Set Roller bolt 1 1001456500 for each mov. contact Set replacement roller bolt - add. material 1 1001716600 one-time necessary For this documentation we reserve all rights according to standard DIN 34, section 2.1. Page 3 of 5 Spare parts for on-load tap-changers Date: : Type G III 1600 Doc.: G97001.xls Pictures of parts Designation Pcs Part no. Remarks Guide plate, small 2 025680:02 Sledge 3 025694:04 Tension bolt 12 025696:03 Use always SETERSATZ with indication "drilled" Cocking pin for order/offer 12 452425 4 x 18 Star-point terminal 3 002301:06 Connecting lead, left 3 002307:02 Connecting lead, right 3 002306:03 Shunt contact carrier 6 002302:02 Bolt 6 025713:01 Cotter pin 6 401530:00 Hex. head screw M 10x85 6 450136 from 1978 on For this documentation we reserve all rights according to standard DIN 34, section 2.1. Page 4 of 5 Spare parts for on-load tap-changers Date: : Type G III 1600 Doc.: G97001.xls Pictures of parts Designation Pcs Part no. Remarks Pressure spring 96 550079 Upper contact cyl. ring 1 042530:01 since 10/67 counter sink. for Lower contact cyl. ring 1 042531:01 screw & press. spring is new Connecting contact 1 002303:02 Set of Insulating piece I & II (undried) (G21000) 1 768172:00 1 Set for 1 Sector Locking plate 8 025669:98 each sector for replacement of transverse insulation parts 1 set of small parts G1600 old 1 740810:01 For this documentation we reserve all rights according to standard DIN 34, section 2.1. Page 5 of 5 Spare parts for on-load tap-changers Date: 16.03.2022 Type G III 1602 Doc.: G97020.xls Pictures of parts Designation Pcs Part no. Remarks Cover gasket 1 590588 Gasket between OLTC head and transfromer cover 1 056391:00 NB 6mm Worm without ball-shaped head 1 071439:02 Worm, double-thread, with ball-shaped head 1 069276:02 Worm, right, with ball-shaped head and drill hole 1 067062:02 Worm without ball-shaped head 1 049685:00 not deliverable Worm with ball-shaped head 1 049684:00 not deliverable Worm wheel, double-thread 1 070096:02 Worm wheel, single-thread, preassembled 1 002264:98 Energy accumulator spring: 100000 operations Pressure spring G III/G I 1602/G I 3002, p = 4708 N 1 550721:01 Energy accumulator spring G I 1612, p = 3030 N 1 550071:01 Energy accumul. spring G I 1622/G I 3022, p = 3720 N 1 550072:01 Guide tube (1) 1 012099:02 from 9/76 on Guide bushing (2) 1 049680:01 Spherical bushing (3) 2 452163 Circlip 1 452229 Circlip 1 452219 Circlip lock ring 1 452217 Pawl spring 1 004302:01 70000 - 100000 Bolt 2 099682:02 since approx. 1996 Washer 2 099683:01 Tenter pin 2 451442 Adjustment pin (auxiliary tool) 1 099685:01 Left pawl (1), preassembled 1 002282:06 Right pawl (2), preassembled 1 003767:06 Circlip 2 452216 Washer 2 451352 Pawl bolt 2 025592:03 For this documentation we reserve all rights according to standard DIN 34, section 2.1. Page 1 of 5 Spare parts for on-load tap-changers Date: 16.03.2022 Type G III 1602 Doc.: G97020.xls Pictures of parts Designation Pcs Part no. Remarks Buffer bolt (1) 2 025597:03 Cup spring 28 452363 Crown nut (3) 2 451297 Split pin (4) 2 451488:01 1 set of contacts G I 1612 with accessories 092705:02 1 set of spare contacts G III 1602 with accessories 092706:04 Switching contact support (1) 18 014886:02 Auxiliary contact support (2) 6 014885:02 Screening sleeve for main contact (1) 12 560132:00 Screening sleeve for switching contact (2) 12 560143 Contact bridge, switching contact (1) 6 051785:03 Guide bridge, main contact (2) 6 052059:03 Insulating spacer I+II (undried) 1 768171:00 material for one sector Locking plate 8 025669:98 for replacement of transveres For type G from 1971 insulation For the period 1971 to 1975 please take along material set 768173:00 in addition 1 set of small parts G1602 1 092691:03 Shim (1) 24 054201:01 Locking plate (2) 24 025669:98 Hex. head screw 2 450361 Spring insulator 48 560012 Spring insert 48 051805:00 Flat spring 96 550036 Bearing for contact holder (1) 24 025675:03 Bolt (2) 24 025668:03 Cocking pin (3) 24 452437 For this documentation we reserve all rights according to standard DIN 34, section 2.1. Page 2 of 5 Spare parts for on-load tap-changers Date: 16.03.2022 Type G III 1602 Doc.: G97020.xls Pictures of parts Designation Pcs Part no. Remarks Sledge (1) 3 051821:00 Use always SETERSATZ Tension bolt (2) 12 054536:00 with indication "drilled" Cocking pin (3) 12 452425 for order/offer Drive shafts, main contact (1) 12 014251:03 before 11/87 300000 - 400000 Drive shafts, switching contact (2) 12 014250:03 before 11/87 300000 - 400000 Use always SETERSATZ with indication "drilled" for order/offer Tension lever, switching contact (1) 12 051752:00 Tension lever, main contact (2) 12 052056:00 Bolt for tension lever (3) 24 051780:02 Riveting washer (4) 24 025690:98 Set Roller bolt 1 1001456500 for each mov. contact Set replacement roller bolt - add. material 1 1001716700 one-time necessary Guide plate, small 2 015557:00 Counterbolt (1) 3 003854:08 from 12/87 on Cup spring (2) 30 401634:00 Cocking pin (3) 3 451457 Protection sleeve 3 073873:01 Main contact support 6 014247:02 Main contact, preassembled 3 014264:06 Main contact support 6 262750:02 For this documentation we reserve all rights according to standard DIN 34, section 2.1. Page 3 of 5 Spare parts for on-load tap-changers Date: 16.03.2022 Type G III 1602 Doc.: G97020.xls Pictures of parts Designation Pcs Part no. Remarks Copper rod, right 3 014243:03 Copper rod, left 3 016896:01 Switching contact (1) 12 017420:00 Switching contact (auxiliary) (2) 12 017420:00 Coupling tube lock nut 48 068340:00 Plate spring 96 452357 Lock tab 48 051767:00 Switching contact 12 017420:00 Since 30.06.89 guide plate Switching contact (auxiliary) 12 017420:00 with self-locking nut Pressure spring for switching and main contact (1) 96 550079 Pressure spring main contact (oil damping) (2) 24 550089 Pack of current strips (1) 36 051769:00 Lock tab (2) 48 051767:00 Hex. nut (for reasons of precaution) 2 451239 Screening, center (1) 6 052169:04 Separating wall (2) 36 703325:00 Separating wall (3) 12 705335:00 Pack of current strips, left 6 052066:00 Pack of current strips, right 6 052067:00 Protective spark gap dev. 1 015857:01 installed since 11/74 Resistor pack 1 015852:00 For this documentation we reserve all rights according to standard DIN 34, section 2.1. Page 4 of 5 Spare parts for on-load tap-changers Date: 16.03.2022 Type G III 1602 Doc.: G97020.xls Pictures of parts Designation Pcs Part no. Remarks Connection leads per sector Flex. resistor leads !! Part-list V1137400 to be heeded !! Small parts 092701:00 Fixing material for div. switch drive tube consisting of: 3 065926:00 installed since 11/86 Connecting tube 6 055925:03 Screening sleeve 3 065924:00 Screw M8x133 3 068340:00 Coupling tube lock nut 1 set of spare contacts with accessories 1 phase 1 092705:02 3 phases 1 092706:04 Taper pins for supporting cylinder 4 451463 Repair fixation outer lower screening ring Washer 3 451325 Lock nut 3 453977:01 Um >= 170kV bzw Slotted socket screw 3 450710 Reihenspannung >= 150 kV Angualr fixing strip 3 731370:00 Cylindrical head screw 3 450876 Washer 3 451326 For this documentation we reserve all rights according to standard DIN 34, section 2.1. Page 5 of 5 3 Step-by-Step 3 Step-by-Step 3.1 Note spare parts list NOTICE! The tests, parts replacements and one-time retrofittings described in the image list must be - especially in case of performance of maintenance - considered in addition to the intructions listed below. Link to spare parts list: Spare parts list [►Section 2, Page 5] 3.2 Tests and condition-based parts replacement at each maintenance 3.2.1 Checking de-energized tap-change supervisory control Before starting work, ensure de-energized tap-change supervisory control. Bushing of tap-change supervisory control Figure 1: Bushing of tap-change supervisory control G tap changer NOTICE Danger of electric shock This section must be read and followed before removing the on-load tap- changer cover. The following section describes how you can tell without removing the on- load tap-changer cover whether it is a version with tap-change supervisory control and how you can ensure that the tap-change supervisory control is de-energized. NOTICE! If it is a version with tap-change supervisory control, ensure that the tap-change supervisory control is in de-energized condition before re- moving the on-load tap-changer cover! The variant with magnetic switch has been in use since the beginning of 1990. 18 EN 3 Step-by-Step Recognizing the tap-change supervisory control without connection diagram The version with tap-change supervisory control is always clearly recogniz- able by its bushing at the on-load tap-changer head. De-energization of the tap-change supervisory control by the operator NOTICE! The tap-change supervisory control of the on-load tap-changer is connected to terminals in the motor-drive unit. The connection of the supply voltage depends on the connection diagram of the respective motor-drive unit. Ensuring the de-energization of the tap-change supervisory control before removing the on-load tap-changer cover Open the cover of the bushing by loosening of the four bolt connections. Cover of bushing Figure 2: Cover of bushing of tap-change supervisory control Ensure de-energized condition by measuring at all connection terminals against ground potential (housing) in AC and DC mode of the digital multi- meter. Figure 3: View of the opened bushing EN 19 3 Step-by-Step Figure 4: Connection diagram for connection configuration of terminal strips NOTICE! Adjustment position different depending on tap-changer design! 3.2.2 Removal of tap-change supervisory control When trial tap-change operations of diverter switch insert are performed at open air, it is necessary to remove the tap-change supervisory control at the beginning of maintenance and reinstall it when work is finished, in order to prevent damage to tap-change supervisory control. The holder segments of DSIs manufactured after September 2002, were at- tached clamping sleeves pins to prevent that tap-change supervisory control settings get lost during removal. If the clamping sleeve is not yet installed to a DSI, retrofit it before removing the tap-change supervisory control. When you have removed the tap-change supervisory control, continue main- tenance as usual. 3.2.3 Connecting leads of protective spark gaps G20 000/21 000 Time for checking 3 sectors is estimated to be 0.5 hours. Expect 1 hour more when the connecting leads need to be replaced. 20 EN 3 Step-by-Step Checking Check whether the following criteria are fulfilled: ▪ Connecting leads are made of flexible wire, ▪ Connecting leads are movable. ▪ Connecting leads are not damaged. If one of the 3 criteria is not fulfilled, the connecting leads must be replaced. Replacement On diverter switch inserts G 20 000 and G 21 000, the connecting leads of the protective spark gaps are attached to the outside of the resistor cylinder and can be replaced without having to remove the cylinder. 3.2.4 Connecting leads of protective spark gaps G22 000 One hour is needed to check 3 sectors. Additional 3 hours are needed to re- place connecting leads. Checking A mirror must be used for the check. Check whether the following criteria are fulfilled: ▪ Connecting leads are made of flexible wire, ▪ Connecting leads are movable. ▪ Connecting leads are not damaged. If one of the 3 criteria is not fulfilled, the connecting leads must be replaced. Replacement To replace the connecting leads, the diverter switch must be removed from the resistor cylinder. EN 21 3 Step-by-Step Remove supporting cylinder, drive shaft and guide gib as described in the in- spection instructions. Figure 5: Diverter switch insert G22 000 Remove connecting leads from fixed transition and switching contacts. Figure 6: Connecting leads 22 EN 3 Step-by-Step Remove clamping screws of connecting leads at lower end of round copper rods. Figure 7: Clamping bolts NOTICE! Before removing the resistor from the diverter switch, attach di- verter switch to lifting gear and secure it. Remove the bolts that attach resistor cylinder to switching columns (6 x M8). Figure 8: Attachment bolts on switching column Lift complete diverter switch from resistor cylinder. EN 23 3 Step-by-Step NOTICE! Pay attention to zero mark and tap-changer serial number on re- sistor cylinder. Figure 9: Lifting complete diverter switch Replacement of connecting leads at protective spark gaps NOTICE! The connecting leads to be installed depend on the diverter switch version, G I or G III. NOTICE! Number depending on installed version NOTICE! G III : 3 cables on left, 3 cables on right Figure 10: Connecting leads at protective spark gaps 24 EN 3 Step-by-Step Current version with flexible connecting leads. Figure 11: Current version Old version with rigid leads must be replaced. Figure 12: Old version with rigid leads and large cable terminals Old version with rigid leads and small cable terminals must be replaced. Figure 13: Old version with rigid leads and small cable terminals Installation Reinstallation of diverter switch insert is done in reverse order of installation. Make sure that any unscrewed or removed connection is reinstalled and se- cured correctly. EN 25 3 Step-by-Step Tightening torques of bolt connections that need to be secured: Bolt connection Tightening torque Resistor connecting leads (Figure "Con- 6 Nm necting leads") Clamping joint round copper rods (Figure 20 Nm "Clamping bolts") Attachment bolts resistor cylinder (Figure 20 Nm "Attachment bolts on switching column") Attachment bolts of protective spark 6 Nm gaps (Figure "Current version") Table 1: Tightening torques of bolt connections that need to be secured 3.2.5 Moving contact bridges - Checking transverse insulation The use of a megohmmeter is absolutely necessary; a measuring device for varistors may NOT be used for this measurement. The moving main switch- ing contacts and the auxiliary contacts should be insulated from the lever system to ensure electrical functionality of the diverter switch insert. For this purpose, insulation between contact sledge and contact carrier should be measured using a megohmmeter with a measured voltage of 2500 V in ac- cordance with figure "Arcing contacts type G" of chapter Performing the measurement OILTAP® G [►Section 3.2.5.1, Page 26] and the two figures "Contact system type K" in chapter Performing the measurement OILTAP® G [►Page 27]. During the 10-second period of the measurement, the insu- lation value may not fall below the value of 1000 MΩ. Contact the responsi- ble OPS if the value falls below the limit value of 1000 MΩ. When performing the test, make sure that the tested arcing contact is in the open position. 3.2.5.1 Performing the measurement OILTAP® G Measurement in both positions of the contact carrier (2 positions per contact carrier). 1: Guide bridge 2/3: Contact carrier 26 EN 3 Step-by-Step Measurement between the positions 1 - 2, 1 - 3, and 2 - 3 respectively for all main switching contacts and transition contacts in all sectors. 3 2 P1: Megohm- 1 meter Figure 14: Arcing contacts type G Measurement on moving contact system Measurement in both positions of the rocker contact (2 positions per moving contact) 1: Connection to contact system 2/3: Contact bridge Measurement between the measuring points 1 - 2, 1 - 3, and 2 - 3 respec- tively for all main switching contacts and transition contacts in all sectors. 3 2 P1: Megohm- 1 meter Figure 15: Contact system type K Measurement on lower fixed contacts Measurement between measuring points 1: Connection to contact system and 2: Lower fixed contact When measuring the fixed lower transition contacts, the respective main switching contact should be open as well, since otherwise measurement on the transverse insulation will be inaccurate, too. EN 27 3 Step-by-Step P1: Megohm- 2 meter 1 Figure 16: Contact system type K 3.2.6 Checking travel of main contact - OILTAP® Type G 1601/1602/2002/2502/3000 Main contact The clearances to be checked and permissible limit values are listed in the chapter below. Check clearances during every maintenance. Contact the relevant OPS if a limit is not reached. Play between copper contact fingers Measure play between copper contact fingers when in closed position. Min. permissible clearance: S1 ≥ 0.5 mm s1 F1 F1 f1 45 Figure 17: Play S1 between contact fingers Play between contact finger in closed position and contact carrier Measure play between copper contact finger in closed position and contact carrier. 28 EN 3 Step-by-Step Min. permissible clearance: S1 ≥ 1.0 mm s1 F1 F1 f1 45 Figure 18: Play f1 between copper contact finger and contact carrier Play between switching contacts Measure play S2 between switching contacts in closed position. Min. permissible clearance: S2 ≥ 0.5 mm s2 F2 f2 F2 Figure 19: Play S2 between switching contacts Play between switching contact and contact carrier Measure play f2 between switching contact in closed position and contact carrier. Min. permissible clearance: S2 ≥ 0.5 mm s2 F2 f2 F2 Figure 20: Play f2 between switching contact and contact carrier Play between copper contact finger and round copper rod Measure play f3 between copper contact finger and round copper rod before the moving switching contact is detached from the fixed contact. EN 29 3 Step-by-Step Min. permissible clearance: S3 ≥ 0.8 mm f3 Figure 21: Play between copper contact finger and round copper rod 3.2.7 Checking bolt connection on contact bridge type G 1600 During maintenance work of diverter switches G1600, the two middle bolts of all contact bridges (2 per contact bridge) must be removed and measured. Make sure that middle attachment bolt is an M6 x 18 bolt. If such a bolt is not available, an M6 x 20 bolt can be shortened. Note down in the assembly re- port: "Contact bridges are bolted with M6 x 18 bolts". Figure 22: Bolt connection at the contact bridges 3.2.8 Contacts - Checking the solder joints During maintenance work of diverter switches type G, visually check the sol- der joints of the contact pieces at the moving contact bridges for cracks. If any cracks are discovered, contact the relevant OPS to discuss further measures. Figure 23: Example for a crack 30 EN 3 Step-by-Step Figure 24: Example for a crack 3.2.9 Checking riveting - Drive shafts of contact system The chapter below describes how to check the riveting of the drive shaft sys- tem of on-load tap-changer type OILTAP® G. Proceed as follows if rivet washers are loose. Check riveting during every maintenance. Drive shaft design Symmetrical design of riveted roller bolt with drive shafts ( see following fig- ure, as well as "Figure 014250:xx - Drive shafts preassembled"). Rivet head Rivet washer Function Slide washer Drive shafts Figure 25: Design roller bolt with drive shafts EN 31 3 Step-by-Step Decision factor Riveting is ok if the rivet washer cannot be moved in relation to the rivet head. If a rivet washer is loose, check if it can be tilted. If the rivet washer can be turned, riveting of the rivet head can be reworked as shown in section "Rework loose riveting". Rivet head Rivet washer Figure 26: Turnable rivet washer If the rivet washer can be tilted up and down, riveting must be replaced using new material, as shown in section "Replace riveting", Rivet head Rivet washer Figure 27: Tiltable rivet washer If the rivets are accessible, checking can be done in installed condition. Reworking loose riveting Please note that the drive shafts have been removed to describe the steps for reworking loose riveting. The drive shafts must be reinstalled at their orig- inal position (be sure to mark position before removal). 32 EN 3 Step-by-Step Put riveted end of drive shafts vertically on a stable surface (do not clamp in bench vise). A second person secures the drive shafts in this position. Re- work the rivet head using a hammer and a punch until the rivet washer can- not be moved anymore. Punch drift Second person securing Figure 28: Reworking rivet connection If the rivets are accessible, you can rework the riveting in installed condition. Replacing the riveting This work step can only be executed if the drive shaft assembly has been re- moved. The drive shafts must be reinstalled at their original position (be sure to mark position before removal). First, file or drill down one side of the rivet head and remove the rivet washer. Then remove roller bolt from the drive shafts. Figure 29: Sanding the rivet head Roller bolts preassembled on one side (following figure, item 10 in parts list ) are available for replacement. EN 33 3 Step-by-Step The assembly is performed in accordance with section "Assembly drive shafts". Make sure that the Teflon coatings of the slide washers show out- ward, in the direction of the rollers. Perform riveting on the side of the roller bolts that was not preassembled, as described in section "Reworking loose riveting". Figure 30: Preassembled rivet bolt Materials Item Materials Part no. 10 Roller pin set 10014565:xx 20 Set change roller bolt 10017166:xx G21000 (set of small parts) 30 Set change roller bolt 10017167:xx G22000 (set of small parts) Table 2: Material Drive shafts of contact system - Checking riveting 34 EN 3 Step-by-Step 3.2.9.1 Preassembled drive shafts EN 35 3 Step-by-Step 3.2.10 Energy accumulator - permissible clearances G 1600 Worm wheel / worm gear: min. permissible cog width = 1.5 mm Worm wheel Worm gear Figure 31: Worm wheel / worm gear Locking pawl pin, roller, roller pin: max. permissible clearance: 0.5 mm Locking pawl pin Roller pin Function Figure 32: Locking pawl / roller of energy accumulator EN 37 3 Step-by-Step 3.2.11 Max. permitted contact wear 38 EN Maximum admissible contact wear (Summary) Replacement for document TCS06004en TCS06004 is replaced owing to the correction for V200 14pitches CST09001en.xls CST1 Suw 10.12.2009 Page 1/1 OLTC type Dimensions of the contacts in mm, Max. admissible or OLTC-dependent reference dimension in mm contact wear Additional wear criterions Entry in with diverter switch inserts type G 22000, R, T in mm SAP documentation as New condition minimum residual value (individual wear) movable fixed movable fixed SC TC SC TC SC TC SC TC SC RC TC A 25 Ø 25 Ø - - 23 Ø 23 Ø - - 2Ø 2Ø none diameter B 5-6 4,5-6 - - 2 1,5 - - 3 3 none individual wear C250 5-6 4,5-6 ∗ ∗ 2 1,5 - - 3 3 none individual wear C350 18,5 18 ∗ ∗ 10,5 10 - - 8 8 none individual wear bis bis 19,5 19,5 V200 - except 22 Ø 22Ø - - 16 Ø 16 Ø - - 6Ø 6Ø none diameter with 14 pitches V200 14 pitches 22 Ø 20 Ø - - 16 Ø 16 Ø - - 6Ø 4Ø none diameter V350/500/ 22 Ø 22 Ø - - 17 Ø 17 Ø - - 5Ø 5Ø see V__09001.doc (TS Manual) diameter 700 - except with 14 pitches V350/700 14 pit. 22 Ø 20 Ø - - 17 Ø 17 Ø - - 5Ø 3Ø see V__09001.doc (TS Manual) diameter SAP document.: individual wear M 8 8 8 8 4 4 4 4 4 4 see TS284043.1 (TS Manual) addit. cont. sheet: indivi. wear D 20000 2 4 11 10 0,5 2 9,5 8 1,5 2 none individual wear oder 2,5 4 11,5 10 0,5 2 9,5 8 2 2,5 D 21000 8,5 8,5 11,5 11,5 3,5 3,5 6,5 6,5 5 5 see TS282034 (TS Manual) individual wear D 0466 6 6 6 6 1 1 1 1 5 5 see TCS05011.doc individual wear D 0444, 6 6 6 6 1 1 1 1 5 5 (TS Manual) SAP document.: individual wear E 6 6 6 6 1,5 1,5 1,5 1,5 4,5 4,5 see SI_E_2 (TS Manual) addit. contact sheet: individ. wear F 21000 8 8 8 8 1 1 1 1 7 7 individual wear F 23000 9,5 8 10 8 3 1 2,5 1 7 7 see TCS05010.doc F 24000 8 8 8 8 1 1 1 1 7 7 (TS Manual) F 26000 9,5 8 10 8 3 1 2,5 1 7 7 add. contact sheet F26000 T and R 34 34 34 34 22 22 22 22 6 6 SAP document.: total wear if end inspection see inspection instructions type R additional contact sheet sheet is not available G 21000 7 7 7 7 1 1 1 1 6 6 see TCS05012.doc SAP document.: total wear (TS Manual) additional contact sheet G 22000 entered into if total wear = 13 mm 6,5 6,5 see inspection instructions - type G SAP document.: total wear guide bridge TCS05012.doc (TS Manual) additional contact sheet K 8,5 8,5 8,5 8,5 1,5 1,5 1,5 1,5 7 7 none individual wear SC = switching contact TC = transition contact * see document TS94N094 i. A. Uwe Seltsam Copies to: CTT, CST, TS Manual, CTE, CSxO, CST1, CST3 notice board, CS4T notice board, MR subsidiaries and representatives The copying, distribution and utilization of this document as well as the communication of its contents to others without expressed authorization is prohibited. Offenders will be held liable for the payment of damages. All rights reserved in the event of the grant of a patent, utility model or ornamental design registration F00788:01 CST09001en.XLS 11.12.2009 Seite 1/1 3 Step-by-Step 3.2.12 Drawing to determine the contact pressure of main contact type G 1600 / 3000 and G III 2002 / 2502 40 EN 3 Step-by-Step 3.2.13 Cleaning the diverter switch drive tubes For cleaning the inside of the diverter switch drive shafts on type G, the up- per coupling hub (energy accumulator) and on diverter switch type K, the lower coupling hub (diverter switch) must be removed. The connection between drive tube and coupling hub is provided by connec- tion pipes and bolts. Until approx. June 1971, rivet bolts with Ø 10 mm were installed in diverter switch type K. In this version, the holes must be enlarged from Ø 10 mm to Ø 12 mm before removal. When enlarging the hole, pay attention that the coupling does not get twisted and that the connection pipes fit tightly. Next, remove the chips from the drive tube. EN 43 3 Step-by-Step 3.2.14 Permissible wear differences between switching contact and transition contact Permissible wear differences between switching contact and transition con- tact Note: For more contact wear criteria, see inspection instructions type G, IA57/83 44 EN 3 Step-by-Step 3.2.15 How to check the transverse insulation on the moving arcing contacts of the diverter switch insert NOTICE Risk of personal damage or injury, damage to property or mal- function. If work is performed by insufficiently qualified personnel and/or safety in- structions are not observed, there is a risk of personal damage or injury, damage to property or malfunction. ► Safety, hazard and other information included in the MR operating in- structions for the relevant on-load tap-changer type must be observed! ► Please read the instructions carefully before starting work. ► The realization of the instructions below requires profound knowledge and experience that correspond to the knowledge acquired during a train- ing at MR about maintenance of the relevant on-load tap-changer type. ► It is absolutely necessary that the diverter switch insert (or selector switch insert, respectively) has been removed. The section describes how to check the transverse insulation on the moving arcing contacts of diverter switch inserts type G and K. Make sure to carry out this procedure during every maintenance. General notes on performance of measurement The use of a megohmmeter is absolutely necessary; a measuring device for varistors may NOT be used for this measurement. The moving main switching contacts and the auxiliary contacts should be in- sulated from the lever system to ensure electrical functionality of the diverter switch insert. For this purpose, insulation between contact sledge and contact carrier should be measured using a megohmmeter with a measured voltage of 2500 V in accordance with the following figures. During the 10-second period of the measurement, the insulation value may not fall below the value of 1000 MΩ. Contact the responsible OPS if the value falls below the limit value of 1000 MΩ. When performing the test, make sure that the tested arcing contact is in the open position. EN 45 3 Step-by-Step Performing the measurement Diverter switch insert OILTAP® G Measurement in both positions of the contact carrier (2 positions per contact carrier). 1: Guide bridge 2/3: Contact carrier Measurement between positions 1 - 2, 1 – 3 and 2 - 3 for all main switching contacts and transition contacts in all sectors. 4 3 1 2 Figure 33: Arcing contacts type G 1 Guide bridge 2 Contact carrier 3 Contact carrier 4 P1: Megohmmeter Diverter switch insert OILTAP® K Measurement on moving contact system Measurement in both positions of the rocker contact (2 positions per moving contact) 1: Connection to contact system 2/3: Contact bridge Measurement between measuring points 1 - 2, 1 – 3 and 2 - 3 46 EN 3 Step-by-Step for all main switching contacts and transition contacts in all sectors. 3 4 2 1 Figure 34: Contact system type K 1 Guide bridge 2 Contact carrier 3 Contact carrier 4 P1: Megohmmeter Measurement on lower fixed contacts Measurement between measuring points 1: Connection to contact system and 2: Lower fixed contact When measuring the fixed lower transition contacts, the respective main switching contact should be open as well, since otherwise measurement on the transverse insulation will be inaccurate, too. 1 2 3 Figure 35: Lower contacts type K 1 Connection to contact system 2 Lower fixed contact 3 P1: Megohmmeter EN 47 3 Step-by-Step 3.2.16 Maintenance procedure for diverter switches type G with tap- change supervisory control When trial tap-change operations of diverter switch insert are performed at open air, it is necessary to remove the tap-change supervisory control at the beginning of maintenance and reinstall it when work is finished, in order to prevent damage to tap-change supervisory control. The holder segments of diverter switches manufactured after September 2002, were attached using dowel pins to prevent that tap-change supervi- sory control settings get lost during removal. On diverter switch inserts that do not yet have this clamping sleeve, the at- tachment must be performed as shown in the following before removing the tap-change supervisory control: Remove supporting cylinder from diverter switch. Drill hole of Ø (diameter) 6 mm and depth 15 mm at distance of 37.7 mm from the respective outer edge of the tap-change supervisory control seg- ment (see figures 1 to 3). Drive clamping sleeves 452405 in the respective holes. m 15 m mm 15 Figure 36: Diverter switch head, fixing hole positions 37.7 mm Figure 37: Left segment, hole position 37.7 mm Figure 38: Right segment, hole position When you have removed the tap-change supervisory control, continue main- tenance as usual. 48 EN 3 Step-by-Step 3.2.17 Check of voltage-dependent resistors This section describes how to deal with voltage dependent resistors (varis- tors) in Zinc oxide (ZnO) version for on-load tap-changers type OILTAP® R, T, M and VACUTAP® VM®, VR® and in silicon carbide (SiC) version for on- load tap-changer type OILTAP® G. EN 49 3 Step-by-Step Overview of versions and distinguishing features 50 EN 3 Step-by-Step Version Varistor types OLTC types Delivery date / serial number 33 mm Toshiba QN 33 OILTAP® From 1 January, QN 33 Ø: 33 +1 mm M, R, T, G 2004 ZnO H: 33 +2 mm VACUTAP® See Overview ZnO VM®, VR® varistors, diameter 33 mm QN33 (1 January 2004) for details. strip isolation to 33 Several manufacturers OILTAP® From 1 January, mm and types M, R, T, 1979 (several) Ø: 32-35 mm to 31 December, ZnO H: 30.5-34 mm 2003 For details see OILTAP® G Overview ZnO varistors, diameter From 1 Novem- 33mm, until 31 De- ber, 1984 cember 2003 to 31 December, 2003 EN 51 3 Step-by-Step Version Varistor types OLTC types Delivery date / serial number strip isolation to 56 Several manufacturers OILTAP® G, MR060352, mm and types Type 2002 / MR060375; ZnO Ø: 56 mm 2500 MR060384, MR060421; H: 26 mm MR060426, For details see MR060441 Drawing ZnO varis- tor stack, diameter 56mm [►Section 3.2.17.2, Page 58] See drawing ZnO varistor stack, diameter 56mm for details SiC stack Ø: 60 mm OILTAP® G to 31 October, See Drawing SiC H: 253 mm 1984 varistor stack [►Section 3.2.17.3, Page 59] for de- tails. Table 3: Overview of versions and distinguishing features 3.2.17.1 Details - check of voltage-dependent resistors This section describes how to deal with voltage dependent resistors (varis- tors) in Zinc oxide (ZnO) version for on-load tap-changers type OILTAP® R, T, M and VACUTAP® VM®, VR® and in silicon carbide (SiC) version for on- load tap-changer type OILTAP® G. 52 EN 3 Step-by-Step Overview of versions and distinguishing features EN 53 3 Step-by-Step Version Varistor types OLTC types Delivery date / serial number 33 mm Toshiba QN 33 OILTAP® From 1 January, QN 33 Ø: 33 +1 mm M, R, T, G 2004 ZnO H: 33 +2 mm VACUTAP® See Overview ZnO VM®, VR® varistors, diameter 33 mm QN33 (1 January 2004) for details. strip isolation to 33 Several manufacturers OILTAP® From 1 January, mm and types M, R, T, 1979 (several) Ø: 32-35 mm to 31 December, ZnO H: 30.5-34 mm 2003 For details see OILTAP® G Overview ZnO varistors, diameter From 1 Novem- 33mm, until 31 De- ber, 1984 cember 2003 to 31 December, 2003 54 EN 3 Step-by-Step Version Varistor types OLTC types Delivery date / serial number strip isolation to 56 Several manufacturers OILTAP® G, MR060352, mm and types Type 2002 / MR060375; ZnO Ø: 56 mm 2500 MR060384, MR060421; H: 26 mm MR060426, For details see MR060441 Drawing ZnO varis- tor stack, diameter 56mm [►Section 3.2.17.2, Page 58] See drawing ZnO varistor stack, diameter 56mm for details SiC stack Ø: 60 mm OILTAP® G to 31 October, See Drawing SiC H: 253 mm 1984 varistor stack [►Section 3.2.17.3, Page 59] for de- tails. Table 4: Overview of versions and distinguishing features The different types of varistor elements 33 mm (several) and 33 mm QN33 were provided by different manufacturers; please note that the types cannot be clearly distinguished visually and dimensionally. The only unique, differ- entiating feature is 1 mA voltage. The difference is as follows: ▪ Measurement using test equipment with voltage 10 kV @1 mA (see at- tached section 10 kV test equipment 1 mA (33 mm QN33, 33 mm (sev- eral), 56 mm): – Measured value of varistor elements type 33 mm (several): Between 5kV and 6.8 kV. – Measured value of varistor elements type 33 mm QN33: Between 8 kV and 9 kV. ▪ Measurement using test equipment with voltage 7 kV @1 mA (see at- tached instruction 7 kV test equipment 1 mA (33 mm (several) and 56 mm): – Measured value of varistor elements type 33 mm (several): Between 5 kV and 6.8 kV. – Measured value of varistor elements type 33 mm QN33: Test equip- ment does not change to current limitation (yellow LED) EN 55 3 Step-by-Step Checks and criteria for ZnO varistors after 31 December, 1981 For delivery dates after 31 December, 1981, rated current value is indicated on the individual varistor elements. Proceed as follows during maintenance: Version Time period Measure 33 mm QN33 From 1 January, 2004 No measures normally 33 mm (several) From 31 December, 1981 Check and measurement at ev- to 31 December, 2003 ery maintenance strip isolation to 56 From 31 December, 1981 Check and measurement at ev- mm onwards ery maintenance Table 5: Activities for varistor maintenance Limit values Varistor stack Individual varistor element Maximum deviation from new value: 10% Maximum deviation from new value: 20% Table 6: Limit values for varistor maintenance after 31 December, 1981 If the relevant criterion is not fulfilled when measuring varistor elements type 33 mm (several), all varistor stacks must be replaced with 33 mm QN33 at next maintenance. Within one varistor stack, varistor elements type 33 mm QN33 must not be used together with varistor elements type 33 mm (several). If limit values are exceeded when measuring varistor elements type 33 mm QN33, it is allowed to interchange individual varistor elements within one varistor stack. Always make sure that total voltage of varistor stacks in the individual sectors does not deviate by more than 1.5 kV. Varistor elements 56 mm are only installed in the following tap changers type OILTAP® type G: 060352, 060375; 060384, 060421; 060426; 060441 Some varistor elements are available from stock. Checks and criteria for ZnO varistors delivered before 31 December, 1981 Please note for delivery dates before 31 December, 1981, that rated current value Uv was not written on the individual varistor elements. The varistor el- ements must be measured at every maintenance. Proceed as follows: Measure value "UV20" for each varistor element and write value on varistor element, if this has not been done yet. Use waterproof, non-conductive pen (e.g., Edding 8300 industry permanent marker). The relevant spots must be free of oil and grease. 56 EN 3 Step-by-Step Limit values Version Criterion 10 varistor elements Total UV20 > 40 kV 7 varistor elements Total UV20 > 33 kV Table 7: Limit values for maintenance of varistors before 31 December, 1981 During measurement, if measured value is below relevant criterion, all varis- tor stacks must be replaced with 33 mm QN33 at next maintenance. Ensure that the limit values specified in above section are observed. Example: 7 varistor elements, temperature at time of measurement 20°C Test voltage of varistor elements in kV 1 2 3 4 5 6 7 Total 5.77 4.53 4.23 4.45 4.75 4.89 4.75 33.67 Table 8: Example for measuring varistor elements Value "Total UV20" is > 33 kV. The criterion is met. Check and measurement of SiC varistors Before inspection or maintenance of diverter switch insert type OILTAP® G, the relevant OPS must specify in the service order whether SiC varistors (see drawing of SiC varistor stack) are installed. The relevant table or characteristic line sheet (see example of test protocol SiC varistors) must be added to the order. Check plastic parts (spring counterpart and lock nut) for thermal damage. Spring holder Lock nut Figure 39: Overview SiC varistor stack EN 57 3 Step-by-Step The complete varistor stack must be replaced with a new varistor stack with varistors type 33 mm QN33 if the characteristic line of the varistors is in an inadmissible range or if the plastic parts are melted together in a way that plastic moved alongside the varistor stacks or into the gaps. Replacement of the varistor stacks must be performed within 2 months. 3.2.17.2 Drawing ZnO varistor stack, diameter 56mm Varistors with diameter 56 mm (583080XX) are installed in the following on- load tap-changers type G only (serial numbers): MR060352, MR060375; MR060384, MR060421; MR060426; MR060441 strip isolation to 56 isolation strip mm to 26 mm Figure 40: Drawing ZnO varistor stack, diameter 56mm 58 EN 3 Step-by-Step 3.2.17.3 Drawing SiC varistor stack EN 59 3 Step-by-Step 3.2.17.4 Instructions for using 8kV test equipment 12 mA (SiC varistors) Before switching on the equipment, the switch on the rear of the equipment must be set to the respective grid voltage. The equipment may only be con- nected to a grounded socket. Then connect HV test cable to HV terminal "HV" (1) and tighten retaining ring (2). Connect black test cable (0) to test terminal "0V" (3). Before the measurement, set switch "Current se