OILTAP® A Spare Parts List PDF
Document Details
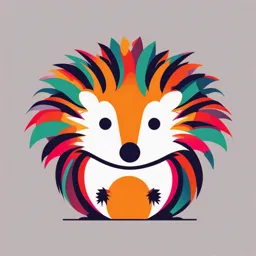
Uploaded by ValuableSugilite
Pink University
Tags
Summary
This document is a spare parts list and maintenance guide for an electrical equipment. It covers topics such as introduction, spare parts lists, step-by-step instructions, tests and condition-based parts replacement, and assembly procedures.
Full Transcript
Table of contents Table of contents 1 Introduction......................................................................................................................... 2 2 Spare parts list................................................................................................
Table of contents Table of contents 1 Introduction......................................................................................................................... 2 2 Spare parts list.................................................................................................................... 3 2.1 Spare parts list - OILTAP® A.............................................................................................................. 4 2.1.1 Spare parts list - OILTAP® A................................................................................................................................ 5 3 Step-by-Step....................................................................................................................... 7 3.1 Note spare parts list............................................................................................................................ 7 3.2 Tests and condition-based parts replacement at each maintenance................................................. 7 3.2.1 Contact cylinder.................................................................................................................................................... 7 3.2.2 Switching cylinder................................................................................................................................................. 7 3.2.3 Switching element................................................................................................................................................. 7 3.2.4 Max. permitted contact wear................................................................................................................................. 8 3.3 Parts replacement after fixed number of tap-change operations intervals....................................... 10 3.4 One-time retrofit and modifications................................................................................................... 10 3.4.1 Until 1 August, 1976 - Modifying attachment of contact cylinder........................................................................ 10 4 Assemblies........................................................................................................................ 17 4.1 General............................................................................................................................................. 17 4.1.1 Tap-changer head with cover.............................................................................................................................. 17 4.2 Contact system, switching element.................................................................................................. 18 4.2.1 Until 1 August, 1976 - Modifying attachment of contact cylinder........................................................................ 18 4.2.2 Contact cylinder.................................................................................................................................................. 24 4.2.3 Max. permitted contact wear............................................................................................................................... 25 4.2.4 Switching cylinder............................................................................................................................................... 27 4.2.5 Switching element............................................................................................................................................... 27 4.3 Energy accumulator, gearbox........................................................................................................... 28 4.4 Supporting cylinder/supporting bars, coupling shaft, switching column............................................ 28 4.5 Transition impedance and protective circuit..................................................................................... 28 4.6 Oil compartment............................................................................................................................... 28 EN 1 1 Introduction 1 Introduction NOTICE Risk of personal damage or injury, damage to property or mal- function. If work is performed by insufficiently qualified personnel and/or safety in- structions are not observed, there is a risk of personal damage or injury, damage to property or malfunction. ► Safety, hazard and other information included in the MR operating in- structions for the relevant on-load tap-changer type must be observed! ► Please read the instructions carefully before starting work. ► The realization of the instructions below requires profound knowledge and experience that correspond to the knowledge acquired during a train- ing at MR about maintenance of the relevant on-load tap-changer type. ► It is absolutely necessary that the diverter switch insert (or selector switch insert, respectively) has been removed. 2 EN 2 Spare parts list 2 Spare parts list EN 3 2 Spare parts list 2.1 Spare parts list - OILTAP® A 4 EN Spare parts for OLTC Date: 05.10.2004 Type A Doc.: A97001.xls Pictures of parts Designation Pcs Part no. Remarks Head gasket without change-over selector AF-WN 2 590337:01 Head gasket 1 590336 Cover gasket with change-over selector AF-WN 2 081121:00 Cover gasket 1 081122:00 Cap nut M12 1 550380 8 pieces without change-over selector 8 9 pieces with change-over selector 9 Cap nut gasket 1 021736:98 (included in set of small parts) 8 pieces without change-over selector 8 9 pieces with change-over selector 9 Vent screw M8 compl. 1 088989:00 Contact roller (A III = 18 pieces) 18 022001:98 NEW d=25mm; MIN d=23mm with split pin 12 455090 and circlip lock ring 6 452202 Contact roller 6 022001:98 NEW d=25mm; MIN d=23mm (A III = 6 pieces) Energy accumulator spring A III 1 550055 70.000-100.000 A II 1 550058 AI 1 550060 Contact spring (for resistor connection) 6 021532:01 to be retrofitted up to 1967 Contact bridge 6 043338:00 to be retrofitted up to 1967 (A III 6 pieces each) For this documentation we reserve all rights according to standard DIN 34, section 2.1. Page 1 of 2 Spare parts for OLTC Date: 05.10.2004 Type A Doc.: A97001.xls Pictures of parts Designation Pcs Part no. Remarks Connecting plate 3 057743:00 to be retrofitted up to 8/76 (A III = 3 pieces) Aux. contact rod 6 021542:98 (A III = pieces) Stranded copper wire (A III = 3 pieces) 3 001342:98 Contact preassembled cpl. 3 004185:06 order via SETERSATZ (A III = 3 pieces) Slider 1 021530:05 Guide bar 021525:01 Set of small parts (screws, nuts, 088995:00 lock tab etc.) Brush 1 090783:00 Terminal 1 703892:02 (oil compartment) Current take-off terminal 1 021475:03 pressure-tight from 01.02.97 on For this documentation we reserve all rights according to standard DIN 34, section 2.1. Page 2 of 2 3 Step-by-Step 3 Step-by-Step 3.1 Note spare parts list NOTICE! The tests, parts replacements and one-time retrofittings described in the image list must be - especially in case of performance of maintenance - considered in addition to the intructions listed below. Link to spare parts list: Spare parts list [►Section 2, Page 3] 3.2 Tests and condition-based parts replacement at each maintenance 3.2.1 Contact cylinder ▪ Seal tightness ▪ Condition of hard-paper cylinder ▪ Contact wear ▪ Check current take-off ring 3.2.2 Switching cylinder ▪ Energy accumulator: Check locking pawl tension spring and catch of drive flange for cracks ▪ Locking pawl and catch flange: check impact point for wear 3.2.3 Switching element ▪ Check contact wear, and check contact rollers for easy movement, re- place out-of-round take-off contact rollers ▪ Check resistors (porcelain body) and resistor connecting plates ▪ Replace or retrofit resistor connecting plates (new shape) and connecting leads between the two angular connecting pieces if not yet installed ▪ Check current cables and pressure springs EN 7 3 Step-by-Step 3.2.4 Max. permitted contact wear 8 EN Maximum admissible contact wear (Summary) Replacement for document TCS06004en TCS06004 is replaced owing to the correction for V200 14pitches CST09001en.xls CST1 Suw 10.12.2009 Page 1/1 OLTC type Dimensions of the contacts in mm, Max. admissible or OLTC-dependent reference dimension in mm contact wear Additional wear criterions Entry in with diverter switch inserts type G 22000, R, T in mm SAP documentation as New condition minimum residual value (individual wear) movable fixed movable fixed SC TC SC TC SC TC SC TC SC RC TC A 25 Ø 25 Ø - - 23 Ø 23 Ø - - 2Ø 2Ø none diameter B 5-6 4,5-6 - - 2 1,5 - - 3 3 none individual wear C250 5-6 4,5-6 ∗ ∗ 2 1,5 - - 3 3 none individual wear C350 18,5 18 ∗ ∗ 10,5 10 - - 8 8 none individual wear bis bis 19,5 19,5 V200 - except 22 Ø 22Ø - - 16 Ø 16 Ø - - 6Ø 6Ø none diameter with 14 pitches V200 14 pitches 22 Ø 20 Ø - - 16 Ø 16 Ø - - 6Ø 4Ø none diameter V350/500/ 22 Ø 22 Ø - - 17 Ø 17 Ø - - 5Ø 5Ø see V__09001.doc (TS Manual) diameter 700 - except with 14 pitches V350/700 14 pit. 22 Ø 20 Ø - - 17 Ø 17 Ø - - 5Ø 3Ø see V__09001.doc (TS Manual) diameter SAP document.: individual wear M 8 8 8 8 4 4 4 4 4 4 see TS284043.1 (TS Manual) addit. cont. sheet: indivi. wear D 20000 2 4 11 10 0,5 2 9,5 8 1,5 2 none individual wear oder 2,5 4 11,5 10 0,5 2 9,5 8 2 2,5 D 21000 8,5 8,5 11,5 11,5 3,5 3,5 6,5 6,5 5 5 see TS282034 (TS Manual) individual wear D 0466 6 6 6 6 1 1 1 1 5 5 see TCS05011.doc individual wear D 0444, 6 6 6 6 1 1 1 1 5 5 (TS Manual) SAP document.: individual wear E 6 6 6 6 1,5 1,5 1,5 1,5 4,5 4,5 see SI_E_2 (TS Manual) addit. contact sheet: individ. wear F 21000 8 8 8 8 1 1 1 1 7 7 individual wear F 23000 9,5 8 10 8 3 1 2,5 1 7 7 see TCS05010.doc F 24000 8 8 8 8 1 1 1 1 7 7 (TS Manual) F 26000 9,5 8 10 8 3 1 2,5 1 7 7 add. contact sheet F26000 T and R 34 34 34 34 22 22 22 22 6 6 SAP document.: total wear if end inspection see inspection instructions type R additional contact sheet sheet is not available G 21000 7 7 7 7 1 1 1 1 6 6 see TCS05012.doc SAP document.: total wear (TS Manual) additional contact sheet G 22000 entered into if total wear = 13 mm 6,5 6,5 see inspection instructions - type G SAP document.: total wear guide bridge TCS05012.doc (TS Manual) additional contact sheet K 8,5 8,5 8,5 8,5 1,5 1,5 1,5 1,5 7 7 none individual wear SC = switching contact TC = transition contact * see document TS94N094 i. A. Uwe Seltsam Copies to: CTT, CST, TS Manual, CTE, CSxO, CST1, CST3 notice board, CS4T notice board, MR subsidiaries and representatives The copying, distribution and utilization of this document as well as the communication of its contents to others without expressed authorization is prohibited. Offenders will be held liable for the payment of damages. All rights reserved in the event of the grant of a patent, utility model or ornamental design registration F00788:01 CST09001en.XLS 11.12.2009 Seite 1/1 3 Step-by-Step 3.3 Parts replacement after fixed number of tap-change operations intervals 3.4 One-time retrofit and modifications 3.4.1 Until 1 August, 1976 - Modifying attachment of contact cylinder The instructions below describe how to modify attachment of the contact cylinder of tap changers type A, if the tap changer was delivered until ap- proximately August, 1976. In any subsequent maintenance, this work is not necessary. General If tap changer type A was delivered up to approximately August, 1976 (deliv- ery date of OLTC No. 10 755: 6 August, 1976), no narrow nuts are installed under ring 049 563:01 (see attachment "Drawing of ring"). During mainte- nance, to be able to lift the selector switch insert, the ring must be removed by removing the eight M6 nuts. When the eight nuts have been removed, the contact cylinder (with reversing change-over selector) can drop approx. 3.5 mm (until the top contact cylinder flange rests on the reversing change-over selector flange). If there is no reversing change-over selector installed, the contact cylinder can drop even further, until it is held by the felt ring in the dirty oil vessel or by the transformer connecting leads. Version without / with narrow nut The version without reversing change-over selector and without narrow nut is shown in the following figure. Figure 1: Version without narrow nut The version without reversing change-over selector and with narrow nut is shown in the following figure. 10 EN 3 Step-by-Step Narrow nut Figure 2: Version with narrow nut 3.4.1.1 Details - Modifying attachment of contact cylinder The instructions below describe how to modify attachment of the contact cylinder of tap changers type A, if the tap changer was delivered until ap- proximately August, 1976. In any subsequent maintenance, this work is not necessary. General If tap changer type A was delivered up to approximately August, 1976 (deliv- ery date of OLTC No. 10 755: 6 August, 1976), no narrow nuts are installed under ring 049 563:01 (see attachment "Drawing of ring"). During mainte- nance, to be able to lift the selector switch insert, the ring must be removed by removing the eight M6 nuts. When the eight nuts have been removed, the contact cylinder (with reversing change-over selector) can drop approx. 3.5 mm (until the top contact cylinder flange rests on the reversing change-over selector flange). If there is no reversing change-over selector installed, the contact cylinder can drop even further, until it is held by the felt ring in the dirty oil vessel or by the transformer connecting leads. Version without / with narrow nut The version without reversing change-over selector and without narrow nut is shown in the following figure. EN 11 3 Step-by-Step Figure 3: Version without narrow nut The version without reversing change-over selector and with narrow nut is shown in the following figure. Narrow nut Figure 4: Version with narrow nut 12 EN 3 Step-by-Step How to proceed Enlarge two holes of 6.6 mm diameter as indicated in the following figure to 12 mm diameter. Next, install one serrated lock washer 451 363 and one M6 nut, 451 238, on each of the two stud bolts in the contact cylinder (see at- tachment "Materials" for correct mounting), and lift the contact cylinder at a steady pace. Figure 5: Marked boreholes EN 13 3 Step-by-Step 3.4.1.1.1 Drawing of ring 14 EN 3 Step-by-Step 3.4.1.1.2 Materials for modifying attachment of contact cylinder Quantity Description Part no. 2 Serrated lock washer 451 363 2 Hex. head screw 451 238 Table 1: Materials for modifying attachment of contact cylinder 16 EN 4 Assemblies 4 Assemblies 4.1 General 4.1.1 Tap-changer head with cover ▪ Seal tightness of tap-changer head ▪ Condition of toothing on crown wheel and pinion; flank clearance ▪ Check wind-up cam and tripping cam (crack formation) and wear of drive flange ▪ If a change-over selector is used, install locking ring with spring cam if this has not been done yet. EN 17 4 Assemblies 4.2 Contact system, switching element 4.2.1 Until 1 August, 1976 - Modifying attachment of contact cylinder The instructions below describe how to modify attachment of the contact cylinder of tap changers type A, if the tap changer was delivered until ap- proximately August, 1976. In any subsequent maintenance, this work is not necessary. General If tap changer type A was delivered up to approximately August, 1976 (deliv- ery date of OLTC No. 10 755: 6 August, 1976), no narrow nuts are installed under ring 049 563:01 (see attachment "Drawing of ring"). During mainte- nance, to be able to lift the selector switch insert, the ring must be removed by removing the eight M6 nuts. When the eight nuts have been removed, the contact cylinder (with reversing change-over selector) can drop approx. 3.5 mm (until the top contact cylinder flange rests on the reversing change-over selector flange). If there is no reversing change-over selector installed, the contact cylinder can drop even further, until it is held by the felt ring in the dirty oil vessel or by the transformer connecting leads. Version without / with narrow nut The version without reversing change-over selector and without narrow nut is shown in the following figure. Figure 6: Version without narrow nut The version without reversing change-over selector and with narrow nut is shown in the following figure. 18 EN 4 Assemblies Narrow nut Figure 7: Version with narrow nut 4.2.1.1 Details - Modifying attachment of contact cylinder The instructions below describe how to modify attachment of the contact cylinder of tap changers type A, if the tap changer was delivered until ap- proximately August, 1976. In any subsequent maintenance, this work is not necessary. General If tap changer type A was delivered up to approximately August, 1976 (deliv- ery date of OLTC No. 10 755: 6 August, 1976), no narrow nuts are installed under ring 049 563:01 (see attachment "Drawing of ring"). During mainte- nance, to be able to lift the selector switch insert, the ring must be removed by removing the eight M6 nuts. When the eight nuts have been removed, the contact cylinder (with reversing change-over selector) can drop approx. 3.5 mm (until the top contact cylinder flange rests on the reversing change-over selector flange). If there is no reversing change-over selector installed, the contact cylinder can drop even further, until it is held by the felt ring in the dirty oil vessel or by the transformer connecting leads. Version without / with narrow nut The version without reversing change-over selector and without narrow nut is shown in the following figure. EN 19 4 Assemblies Figure 8: Version without narrow nut The version without reversing change-over selector and with narrow nut is shown in the following figure. Narrow nut Figure 9: Version with narrow nut 20 EN 4 Assemblies How to proceed Enlarge two holes of 6.6 mm diameter as indicated in the following figure to 12 mm diameter. Next, install one serrated lock washer 451 363 and one M6 nut, 451 238, on each of the two stud bolts in the contact cylinder (see at- tachment "Materials" for correct mounting), and lift the contact cylinder at a steady pace. Figure 10: Marked boreholes EN 21 4 Assemblies 4.2.1.1.1 Drawing of ring 22 EN 4 Assemblies 4.2.1.1.2 Materials for modifying attachment of contact cylinder Quantity Description Part no. 2 Serrated lock washer 451 363 2 Hex. head screw 451 238 Table 2: Materials for modifying attachment of contact cylinder 4.2.2 Contact cylinder ▪ Seal tightness ▪ Condition of hard-paper cylinder ▪ Contact wear ▪ Check current take-off ring 24 EN 4 Assemblies 4.2.3 Max. permitted contact wear EN 25 Maximum admissible contact wear (Summary) Replacement for document TCS06004en TCS06004 is replaced owing to the correction for V200 14pitches CST09001en.xls CST1 Suw 10.12.2009 Page 1/1 OLTC type Dimensions of the contacts in mm, Max. admissible or OLTC-dependent reference dimension in mm contact wear Additional wear criterions Entry in with diverter switch inserts type G 22000, R, T in mm SAP documentation as New condition minimum residual value (individual wear) movable fixed movable fixed SC TC SC TC SC TC SC TC SC RC TC A 25 Ø 25 Ø - - 23 Ø 23 Ø - - 2Ø 2Ø none diameter B 5-6 4,5-6 - - 2 1,5 - - 3 3 none individual wear C250 5-6 4,5-6 ∗ ∗ 2 1,5 - - 3 3 none individual wear C350 18,5 18 ∗ ∗ 10,5 10 - - 8 8 none individual wear bis bis 19,5 19,5 V200 - except 22 Ø 22Ø - - 16 Ø 16 Ø - - 6Ø 6Ø none diameter with 14 pitches V200 14 pitches 22 Ø 20 Ø - - 16 Ø 16 Ø - - 6Ø 4Ø none diameter V350/500/ 22 Ø 22 Ø - - 17 Ø 17 Ø - - 5Ø 5Ø see V__09001.doc (TS Manual) diameter 700 - except with 14 pitches V350/700 14 pit. 22 Ø 20 Ø - - 17 Ø 17 Ø - - 5Ø 3Ø see V__09001.doc (TS Manual) diameter SAP document.: individual wear M 8 8 8 8 4 4 4 4 4 4 see TS284043.1 (TS Manual) addit. cont. sheet: indivi. wear D 20000 2 4 11 10 0,5 2 9,5 8 1,5 2 none individual wear oder 2,5 4 11,5 10 0,5 2 9,5 8 2 2,5 D 21000 8,5 8,5 11,5 11,5 3,5 3,5 6,5 6,5 5 5 see TS282034 (TS Manual) individual wear D 0466 6 6 6 6 1 1 1 1 5 5 see TCS05011.doc individual wear D 0444, 6 6 6 6 1 1 1 1 5 5 (TS Manual) SAP document.: individual wear E 6 6 6 6 1,5 1,5 1,5 1,5 4,5 4,5 see SI_E_2 (TS Manual) addit. contact sheet: individ. wear F 21000 8 8 8 8 1 1 1 1 7 7 individual wear F 23000 9,5 8 10 8 3 1 2,5 1 7 7 see TCS05010.doc F 24000 8 8 8 8 1 1 1 1 7 7 (TS Manual) F 26000 9,5 8 10 8 3 1 2,5 1 7 7 add. contact sheet F26000 T and R 34 34 34 34 22 22 22 22 6 6 SAP document.: total wear if end inspection see inspection instructions type R additional contact sheet sheet is not available G 21000 7 7 7 7 1 1 1 1 6 6 see TCS05012.doc SAP document.: total wear (TS Manual) additional contact sheet G 22000 entered into if total wear = 13 mm 6,5 6,5 see inspection instructions - type G SAP document.: total wear guide bridge TCS05012.doc (TS Manual) additional contact sheet K 8,5 8,5 8,5 8,5 1,5 1,5 1,5 1,5 7 7 none individual wear SC = switching contact TC = transition contact * see document TS94N094 i. A. Uwe Seltsam Copies to: CTT, CST, TS Manual, CTE, CSxO, CST1, CST3 notice board, CS4T notice board, MR subsidiaries and representatives The copying, distribution and utilization of this document as well as the communication of its contents to others without expressed authorization is prohibited. Offenders will be held liable for the payment of damages. All rights reserved in the event of the grant of a patent, utility model or ornamental design registration F00788:01 CST09001en.XLS 11.12.2009 Seite 1/1 4 Assemblies 4.2.4 Switching cylinder ▪ Energy accumulator: Check locking pawl tension spring and catch of drive flange for cracks ▪ Locking pawl and catch flange: check impact point for wear 4.2.5 Switching element ▪ Check contact wear, and check contact rollers for easy movement, re- place out-of-round take-off contact rollers ▪ Check resistors (porcelain body) and resistor connecting plates ▪ Replace or retrofit resistor connecting plates (new shape) and connecting leads between the two angular connecting pieces if not yet installed ▪ Check current cables and pressure springs EN 27 4 Assemblies 4.3 Energy accumulator, gearbox 4.4 Supporting cylinder/supporting bars, coupling shaft, switching column 4.5 Transition impedance and protective circuit 4.6 Oil compartment 28 EN