OILTAP® B Spare Parts List PDF
Document Details
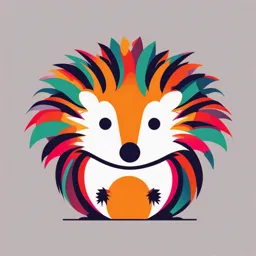
Uploaded by ValuableSugilite
Pink University
Tags
Summary
This document contains a table of contents and a detailed spare parts list for an electrical component, most likely an oil-immersed transformer. It also includes step-by-step instructions and diagrams for maintenance procedures.
Full Transcript
Table of contents Table of contents 1 Introduction......................................................................................................................... 3 2 Spare parts list................................................................................................
Table of contents Table of contents 1 Introduction......................................................................................................................... 3 2 Spare parts list.................................................................................................................... 4 2.1 Spare parts list - OILTAP® B.............................................................................................................. 5 2.1.1 Spare parts list - OILTAP® B................................................................................................................................ 6 3 Step-by-Step..................................................................................................................... 10 3.1 Note spare parts list.......................................................................................................................... 10 3.2 Tests and condition-based parts replacement at each maintenance............................................... 10 3.2.1 Tap-changer head with cover.............................................................................................................................. 10 3.2.2 Check list for maintenance.................................................................................................................................. 10 3.2.3 Wear on switching element................................................................................................................................. 13 3.3 Tests and condition-based parts replacement at each maintenance............................................... 16 3.3.1 Contact cylinder.................................................................................................................................................. 16 3.3.2 Switching cylinder............................................................................................................................................... 16 3.3.3 Trip roller and locking pawl replacement............................................................................................................. 16 3.3.4 Switching element............................................................................................................................................... 18 3.3.5 Current collector disk (delta version only)........................................................................................................... 18 3.3.6 Max. permitted contact wear............................................................................................................................... 19 3.4 Check list for maintenance............................................................................................................... 21 3.4.1 New Node........................................................................................................................................................... 23 3.5 Parts replacement after fixed number of tap-change operations intervals....................................... 24 3.6 One-time retrofit and modifications................................................................................................... 24 4 Assemblies........................................................................................................................ 25 4.1 General............................................................................................................................................. 25 4.1.1 Check list for maintenance.................................................................................................................................. 25 4.1.2 Tap-changer head with cover.............................................................................................................................. 27 4.2 Contact system, switching element.................................................................................................. 28 4.2.1 Wear on switching element................................................................................................................................. 28 4.2.2 Max. permitted contact wear............................................................................................................................... 31 4.2.3 Notes for installing the take-off contacts on the current collector disk................................................................ 33 4.2.4 Current collector disk (delta version only)........................................................................................................... 40 4.2.5 Switching element............................................................................................................................................... 40 4.2.6 Switching cylinder............................................................................................................................................... 41 4.2.7 Contact cylinder.................................................................................................................................................. 41 EN 1 Table of contents 4.3 Energy accumulator, gearbox........................................................................................................... 42 4.3.1 Trip roller and locking pawl replacement............................................................................................................. 42 4.4 Supporting cylinder/supporting bars, coupling shaft, switching column............................................ 44 4.5 Transition impedance and protective circuit..................................................................................... 44 4.6 Oil compartment............................................................................................................................... 44 2 EN 1 Introduction 1 Introduction NOTICE Risk of personal damage or injury, damage to property or mal- function. If work is performed by insufficiently qualified personnel and/or safety in- structions are not observed, there is a risk of personal damage or injury, damage to property or malfunction. ► Safety, hazard and other information included in the MR operating in- structions for the relevant on-load tap-changer type must be observed! ► Please read the instructions carefully before starting work. ► The realization of the instructions below requires profound knowledge and experience that correspond to the knowledge acquired during a train- ing at MR about maintenance of the relevant on-load tap-changer type. ► It is absolutely necessary that the diverter switch insert (or selector switch insert, respectively) has been removed. EN 3 2 Spare parts list 2 Spare parts list 4 EN 2 Spare parts list 2.1 Spare parts list - OILTAP® B EN 5 Spare parts for OLTC Date: 29.08.2006 Type B 150 Doc.: B97001.xls Pictures of parts Designation Pcs Part no. Remarks Cover gasket - Cover gasket with change-over selector 2 590183:01 only for cover - Cover gasket without change-over selector 2 590366:01 from 1958 on, for cover and head - Cover gasket with change-over selector 1 590583 only for cover - Head gasket without change-over selector 1 590365 from 1958 on, for cover and head Cap nut 1 550380 Cap nut gasket 1 021736:98 included in set of small parts (12 pieces without change-over selector) 12 (13 pieces with change-over selector) 13 Vent screw M8 compl. 1 088989:00 included in set of small parts Inspection window (1) 1 570020:01 Gasket (2) 1 590250:01 Gasket (3) 1 590263 Sliding disc (4) 1 021745:02 Press ring (5) 1 021744:01 Cover for inspection window 1 001377:01 Stuffing box preassembled Square shaft 1 007451:03 from approx. 1974 on Square shaft (small flange diameter) 1 007451:01 Round shaft (small flange diameter) 1 007451:00 approx. 1960 - 1970 Gasket for stuffing box for 007451:03 1 860108:01 for 007451:01 and :00 O-Ring 1 860066 For stuffing box: Shaft sealing ring (1) 1 401676:01 Shaft sealing ring (2) 1 400048:00 For this documentation we reserve all rights according to standard DIN 34, section 2.1. Page 1 of 4 Spare parts for OLTC Date: 29.08.2006 Type B 150 Doc.: B97001.xls Pictures of parts Designation Pcs Part no. Remarks Energy accumulator compl. 70.000 - 100.000 B III 150 1 712523:00 1,2/180° 2 springs B I 150 1 712521:00 1,2/180° 1 springs in exchange B III 712522:00 in exchange B I 712520:00 Driving bell (without change-over selector) 1 012214:01 Driving bell (with change-over selector) 1 013413:02 Driving wheel 1 021552:02 Driving disc for preselector 1 001403:98 Pawl (1) with eccentric (2) 1 089012:00 BI 100.000 - 200.000 (= 1 set) BIII 300.000 - 400.000 Toothed plate preassembled (consist. of 12 parts) 1 010536:03 500.000 Guide bearing (12 parts) 1 001413:04 500.000 Current collector 2 009417:07 (2 units for each OLTC for delta connection) Lock tab 2 021985:01 2 hexagon. nuts 4 420668 Lock tab 2 021613:98 modification 1959 2 hexagon. nuts 4 451239 modification 1959 max. abrasion = 1,5 mm Contact head (12 pieces) 12 046015:03 with lock tab from 5/1971 12 066303:00 with lock tab until 5/1971 12 021622:03 Main contact - movable 3 021601:01 max. wear = 3 mm (3 pieces for each OLTC) For this documentation we reserve all rights according to standard DIN 34, section 2.1. Page 2 of 4 Spare parts for OLTC Date: 29.08.2006 Type B 150 Doc.: B97001.xls Pictures of parts Designation Pcs Part no. Remarks Aux. contact - movable 6 021607:01 max. wear = 3 mm (6 pieces for each OLTC) Lock tabs for Locking plates (1) (= 6 pieces) 6 048432:00 Aux. contact (2) (= 12 pieces) 12 022018:98 Guide plate preassembled 2 084848:00 with brass sleeve Guide plate right 2 084846:00 without brass sleeve with 2 two-hole nuts 2 420685 Switch. element compl. Y + D with brass sleeve 1 084928:00 Braided aux. contact lead 3 001421:01 Braided aux. contact lead 3 001422:01 with hex. nut 12 451237 and lock tab 6 451402 Main contact plates 3 001353:01 with 2 hex. head screws 6 453255 and 1 lock tab 3 021986:98 max. abrasion = 2 mm Sliding contact preassembled 1 014023:00 500.000 with accessories 3 pressure springs 3 550101 3 circlips 3 452203 1 lock tab 1 021985:01 2 hexagon. nuts 2 420668 Set of small parts (screws, nuts, lock tabs etc.) 088996:00 Mounting rod (8 pieces) 1 092698:00 consisting of: Mounting rod 1 016048:00 Mounting rod 6 029459:02 Mounting rod 1 029458:01 Mounting device 1 631128:00 Assembly wedge 631340:00 For this documentation we reserve all rights according to standard DIN 34, section 2.1. Page 3 of 4 Spare parts for OLTC Date: 29.08.2006 Type B 150 Doc.: B97001.xls Pictures of parts Designation Pcs Part no. Remarks Cleaning brushes 1 090783:00 1 090784:00 Accumul. C 1 631070:00 Lifting device 1 112168:00 not yet activated Lifting hooks (3 pieces) 3 112160:00 Tripping roll 2 021946:02 from 11/86 on Roller bolt 2 021947:05 Split pin 2 455090 For this documentation we reserve all rights according to standard DIN 34, section 2.1. Page 4 of 4 3 Step-by-Step 3 Step-by-Step 3.1 Note spare parts list NOTICE! The tests, parts replacements and one-time retrofittings described in the image list must be - especially in case of performance of maintenance - considered in addition to the intructions listed below. Link to spare parts list: Spare parts list [►Section 2, Page 4] 3.2 Tests and condition-based parts replacement at each maintenance 3.2.1 Tap-changer head with cover Without change-over selector ▪ Seal tightness of tap-changer head ▪ Condition of toothing on crown wheel and pinion, flank clearance ▪ Wear or abrasion of bearing flange of selector gear cover ▪ Tight seat and wear of tripping switch ▪ Check catch of energy accumulator housing (crack formation) With change-over selector ▪ Check clearance of drive roller of cogwheel and drive crank of change- over selector ▪ Wear of cogdisk bearing of selector gear cover ▪ Indication disk attachment (welded with plastic cogwheel) 3.2.2 Check list for maintenance NOTICE Safety, hazard and other information included in the MR operating instruc- tions for tap-changer type B must be observed! Please read the instructions carefully before starting work. The realization of the instructions below requires profound knowledge and experience that correspond to the knowledge acquired during a training at MR about maintenance on tap-changer type B. It is absolutely necessary that the selector switch has been removed. The instructions below specify which data have to be written down during maintenance and which activities have to be performed. 10 EN 3 Step-by-Step Data Write down the following data during maintenance: ▪ Serial numbers of tap changer and motor-drive unit ▪ Tap changer type, highest voltage for equipment and number of positions ▪ Number of tap-change operations ▪ Motor-drive unit type ▪ Transformer data ▪ Application ▪ Commissioning Check list for maintenance Tap-changer head with cover Without change-over selector ▪ Seal tightness of tap-changer head ▪ Condition of toothing on crown wheel and pinion, flank clearance ▪ Wear or abrasion of bearing flange of selector gear cover ▪ Tight seat and wear of tripping switch ▪ Check catch of energy accumulator housing (crack formation) With change-over selector ▪ Check clearance of drive roller of cogwheel and drive crank of change- over selector ▪ Wear of cogdisk bearing of selector gear cover ▪ Indication disk attachment (welded with plastic cogwheel) Contact cylinder ▪ Seal tightness ▪ Condition of hard-paper cylinder ▪ Contact wear ▪ Check current take-off ring EN 11 3 Step-by-Step Switching cylinder ▪ Locking pawl and eccentric, check for crack formation, wear of tripping rollers, condition of locking pawl tension springs ▪ Top driving disk, wear of toothing and tight seat of locking pawl bearing pin ▪ Bottom driving disk, wear of toothing ▪ Slide contact, wear of contact surface, condition of current take-off lead and pressure springs ▪ Easy movement of bearing bolt ▪ Check that all bolts are tight ▪ When changing contacts, check gaps between main contacts and attach- ment bolts on the switching element Switching element ▪ Wear of main and auxiliary contacts ▪ Condition of all leads ▪ Tight seat of lock nuts of connecting plates and / or current collector disk (if not installed yet, spring washers should be installed to set the gap due to shrinkage) ▪ Condition of contact springs and / or their attachment ▪ Check of guide plates, wear of contact carrier guide ▪ Check running of rotating tube, and check cracking ▪ Tight seat of auxiliary contact carrier attachment (if not installed yet, spring washers should be installed to set the gap due to shrinkage) ▪ Main contact carrier, check axial play ▪ Transition resistors, condition of resistor material and groove carrier, plus measurement of resistance value ▪ Check that all bolts are tight Current collector disk (delta version only) ▪ Condition of twin flexible cables and pressure springs ▪ Running and travel of guide pieces ▪ Wear of take-off contacts (max. wear approx. 3 mm) ▪ Check tight seat of take-off contacts 12 EN 3 Step-by-Step 3.2.2.1 New Node 3.2.3 Wear on switching element This chapter describes determination of wear on switching element type B and type C and subsequent actions. Determination of maximum wear and limit values Use a caliper to measure play between rotating tube and guide plates (play "1") and play between slot in guide plates and the auxiliary contact guide (play "2", see following figure). Play "2" Play "1" Play "2" Figure 1: Switching element showing marked play "1" and play "2" Max. permitted value of: ▪ play "1" is 2.5 mm (measure when new: 0.1 mm). ▪ play "2" is 3.0 mm (measure when new: 1.0 mm). EN 13 3 Step-by-Step Evaluation of the measurement of play "1" between rotating tube and guide plates and further procedure See the following table for how to proceed further. regarding play "1". Measured Further procedure value play "1" ≥ 2.0 mm Make a note of the measured value in the service report. The measured value is used to determine the measures to be taken during the next maintenance. ≥ 2.5 mm Interchange the inner guide plates with the outer guide plates The interchange is not possible for all versions of the guide plates, see the following lines. Ist ein Tausch nicht möglich, zuständigem Sach- bearbeiter kontaktieren. If an interchange is carried out, it must be noted in the service report. The measured value is used to determine the measures to be taken during the next maintenance. Table 1: Evaluation of the measurement of play "1" and further procedure Guide plates versions Depending on the year of manufacture, one of the three versions of the guide plates shown in the figure below was installed. 1 2 3 Figure 2: Guide plates versions 1 Old version, hard paper, 2 GRP version, white, without brass brown 3 New version GRP, white, with brass Interchange the inner guide plates with the outer guide plates 14 EN 3 Step-by-Step Replacing the inner guide plates with outer guide plates is not possible for all versions of the guide plates and is also not necessary for all versions of the guide plates. Details can be found in the table below. N Delivery Versions, proper- Interchange the inner guide plates with the o period ties outer guide plates 1 to Old version, hard Contact OPS. 1970-06-3 paper, brown Interchanging inner guide plates for outer 0 guide plates is technically not possible. 2 From GRP version, Interchanging inner guide plates for outer 1970-07-0 white, without guide plates is technically possible. 1 brass, wears out heavily 3 Not speci- New version GRP, Interchanging inner guide plates for outer fied white, with brass, guide plates is technically usually not neces- no significant wear sary. Table 2: Interchange the inner guide plates with the outer guide plates - depending on the ver- sion Evaluation of the measurement of play "2" between slot in the guide plates and auxiliary contact holder and further procedure See the following table for how to proceed further. regarding play "2". Mea- Further procedure sured value play "2" ≥ 2.0 Make a note of the measured value in the service report. mm The measured value is used to determine the measures to be taken dur- ing the next maintenance. ≥ 3.0 Contact OPS. mm Table 3: Evaluation of the measurement of play "2" and further procedure 3.2.3.1 Change log 2023-11-15 TSC Steindl 1. Guide plate versions added. Replacing the inner for outer guide plates is not necessary for every variant and is not possible for every variant. 2000-10-10 TS3 Dinauer 1. First publication EN 15 3 Step-by-Step 3.3 Tests and condition-based parts replacement at each maintenance 3.3.1 Contact cylinder ▪ Seal tightness ▪ Condition of hard-paper cylinder ▪ Contact wear ▪ Check current take-off ring 3.3.2 Switching cylinder ▪ Locking pawl and eccentric, check for crack formation, wear of tripping rollers, condition of locking pawl tension springs ▪ Top driving disk, wear of toothing and tight seat of locking pawl bearing pin ▪ Bottom driving disk, wear of toothing ▪ Slide contact, wear of contact surface, condition of current take-off lead and pressure springs ▪ Easy movement of bearing bolt ▪ Check that all bolts are tight ▪ When changing contacts, check gaps between main contacts and attach- ment bolts on the switching element 3.3.3 Trip roller and locking pawl replacement This section describes the requirements for replacing trip roller and locking pawl. Criteria for replacing the trip roller If trip roller 021 946:01 with 21 mm diameter is installed in a tap changer type OILTAP® B or OILTAP® C, it must be replaced with a trip roller with 21.5 mm diameter during maintenance. The necessary material is listed in attachment "Materials". 16 EN 3 Step-by-Step When replacing the trip roller, roller bolts and split pins must be replaced too. Split pin Trip roller Roller pin Figure 3: Overview energy accumulator Before installing the new trip roller, measure the diameter of the locking pawl holes. If diameter of one of the holes is larger than or equal to 7.5 mm Ø , locking pawl and eccentric must be replaced. Locking pawl holes Figure 4: Locking pawl holes Criteria for replacing the locking pawl of tap changer type B or C The following instructions are based on the assumption that the trip roller with 21.5 mm diameter is installed. Measure total play of trip roller to locking pawl (play II) as shown in the following figure. If total play "Play II“ is larger than 1.0 mm, roller bolt and trip roller must be replaced. After the replace- ment, if total play "Play II" is still larger than 1.0 mm, locking pawl and eccen- tric must also be replaced. Roller pushed in direction ↑ Roller pushed in direction ↓ Play II Figure 5: Measurement total play “Play II” EN 17 3 Step-by-Step Material list for replacement of trip roller Item Quantity Part no. Description 10 2 02194602 Trip roller 20 2 02194705 Roller pin 30 2 455090 Split pin 40 1 08901201 Locking pawl with eccentric (if neces- sary) Table 4: Material list for replacement of trip roller 3.3.4 Switching element ▪ Wear of main and auxiliary contacts ▪ Condition of all leads ▪ Tight seat of lock nuts of connecting plates and / or current collector disk (if not installed yet, spring washers should be installed to set the gap due to shrinkage) ▪ Condition of contact springs and / or their attachment ▪ Check of guide plates, wear of contact carrier guide ▪ Check running of rotating tube, and check cracking ▪ Tight seat of auxiliary contact carrier attachment (if not installed yet, spring washers should be installed to set the gap due to shrinkage) ▪ Main contact carrier, check axial play ▪ Transition resistors, condition of resistor material and groove carrier, plus measurement of resistance value ▪ Check that all bolts are tight 3.3.5 Current collector disk (delta version only) ▪ Condition of twin flexible cables and pressure springs ▪ Running and travel of guide pieces ▪ Wear of take-off contacts (max. wear approx. 3 mm) ▪ Check tight seat of take-off contacts 18 EN 3 Step-by-Step 3.3.6 Max. permitted contact wear EN 19 Maximum admissible contact wear (Summary) Replacement for document TCS06004en TCS06004 is replaced owing to the correction for V200 14pitches CST09001en.xls CST1 Suw 10.12.2009 Page 1/1 OLTC type Dimensions of the contacts in mm, Max. admissible or OLTC-dependent reference dimension in mm contact wear Additional wear criterions Entry in with diverter switch inserts type G 22000, R, T in mm SAP documentation as New condition minimum residual value (individual wear) movable fixed movable fixed SC TC SC TC SC TC SC TC SC RC TC A 25 Ø 25 Ø - - 23 Ø 23 Ø - - 2Ø 2Ø none diameter B 5-6 4,5-6 - - 2 1,5 - - 3 3 none individual wear C250 5-6 4,5-6 ∗ ∗ 2 1,5 - - 3 3 none individual wear C350 18,5 18 ∗ ∗ 10,5 10 - - 8 8 none individual wear bis bis 19,5 19,5 V200 - except 22 Ø 22Ø - - 16 Ø 16 Ø - - 6Ø 6Ø none diameter with 14 pitches V200 14 pitches 22 Ø 20 Ø - - 16 Ø 16 Ø - - 6Ø 4Ø none diameter V350/500/ 22 Ø 22 Ø - - 17 Ø 17 Ø - - 5Ø 5Ø see V__09001.doc (TS Manual) diameter 700 - except with 14 pitches V350/700 14 pit. 22 Ø 20 Ø - - 17 Ø 17 Ø - - 5Ø 3Ø see V__09001.doc (TS Manual) diameter SAP document.: individual wear M 8 8 8 8 4 4 4 4 4 4 see TS284043.1 (TS Manual) addit. cont. sheet: indivi. wear D 20000 2 4 11 10 0,5 2 9,5 8 1,5 2 none individual wear oder 2,5 4 11,5 10 0,5 2 9,5 8 2 2,5 D 21000 8,5 8,5 11,5 11,5 3,5 3,5 6,5 6,5 5 5 see TS282034 (TS Manual) individual wear D 0466 6 6 6 6 1 1 1 1 5 5 see TCS05011.doc individual wear D 0444, 6 6 6 6 1 1 1 1 5 5 (TS Manual) SAP document.: individual wear E 6 6 6 6 1,5 1,5 1,5 1,5 4,5 4,5 see SI_E_2 (TS Manual) addit. contact sheet: individ. wear F 21000 8 8 8 8 1 1 1 1 7 7 individual wear F 23000 9,5 8 10 8 3 1 2,5 1 7 7 see TCS05010.doc F 24000 8 8 8 8 1 1 1 1 7 7 (TS Manual) F 26000 9,5 8 10 8 3 1 2,5 1 7 7 add. contact sheet F26000 T and R 34 34 34 34 22 22 22 22 6 6 SAP document.: total wear if end inspection see inspection instructions type R additional contact sheet sheet is not available G 21000 7 7 7 7 1 1 1 1 6 6 see TCS05012.doc SAP document.: total wear (TS Manual) additional contact sheet G 22000 entered into if total wear = 13 mm 6,5 6,5 see inspection instructions - type G SAP document.: total wear guide bridge TCS05012.doc (TS Manual) additional contact sheet K 8,5 8,5 8,5 8,5 1,5 1,5 1,5 1,5 7 7 none individual wear SC = switching contact TC = transition contact * see document TS94N094 i. A. Uwe Seltsam Copies to: CTT, CST, TS Manual, CTE, CSxO, CST1, CST3 notice board, CS4T notice board, MR subsidiaries and representatives The copying, distribution and utilization of this document as well as the communication of its contents to others without expressed authorization is prohibited. Offenders will be held liable for the payment of damages. All rights reserved in the event of the grant of a patent, utility model or ornamental design registration F00788:01 CST09001en.XLS 11.12.2009 Seite 1/1 3 Step-by-Step 3.4 Check list for maintenance NOTICE Safety, hazard and other information included in the MR operating instruc- tions for tap-changer type B must be observed! Please read the instructions carefully before starting work. The realization of the instructions below requires profound knowledge and experience that correspond to the knowledge acquired during a training at MR about maintenance on tap-changer type B. It is absolutely necessary that the selector switch has been removed. The instructions below specify which data have to be written down during maintenance and which activities have to be performed. Data Write down the following data during maintenance: ▪ Serial numbers of tap changer and motor-drive unit ▪ Tap changer type, highest voltage for equipment and number of positions ▪ Number of tap-change operations ▪ Motor-drive unit type ▪ Transformer data ▪ Application ▪ Commissioning Check list for maintenance Tap-changer head with cover Without change-over selector ▪ Seal tightness of tap-changer head ▪ Condition of toothing on crown wheel and pinion, flank clearance ▪ Wear or abrasion of bearing flange of selector gear cover ▪ Tight seat and wear of tripping switch ▪ Check catch of energy accumulator housing (crack formation) With change-over selector ▪ Check clearance of drive roller of cogwheel and drive crank of change- over selector ▪ Wear of cogdisk bearing of selector gear cover ▪ Indication disk attachment (welded with plastic cogwheel) EN 21 3 Step-by-Step Contact cylinder ▪ Seal tightness ▪ Condition of hard-paper cylinder ▪ Contact wear ▪ Check current take-off ring Switching cylinder ▪ Locking pawl and eccentric, check for crack formation, wear of tripping rollers, condition of locking pawl tension springs ▪ Top driving disk, wear of toothing and tight seat of locking pawl bearing pin ▪ Bottom driving disk, wear of toothing ▪ Slide contact, wear of contact surface, condition of current take-off lead and pressure springs ▪ Easy movement of bearing bolt ▪ Check that all bolts are tight ▪ When changing contacts, check gaps between main contacts and attach- ment bolts on the switching element Switching element ▪ Wear of main and auxiliary contacts ▪ Condition of all leads ▪ Tight seat of lock nuts of connecting plates and / or current collector disk (if not installed yet, spring washers should be installed to set the gap due to shrinkage) ▪ Condition of contact springs and / or their attachment ▪ Check of guide plates, wear of contact carrier guide ▪ Check running of rotating tube, and check cracking ▪ Tight seat of auxiliary contact carrier attachment (if not installed yet, spring washers should be installed to set the gap due to shrinkage) ▪ Main contact carrier, check axial play ▪ Transition resistors, condition of resistor material and groove carrier, plus measurement of resistance value ▪ Check that all bolts are tight 22 EN 3 Step-by-Step Current collector disk (delta version only) ▪ Condition of twin flexible cables and pressure springs ▪ Running and travel of guide pieces ▪ Wear of take-off contacts (max. wear approx. 3 mm) ▪ Check tight seat of take-off contacts 3.4.1 New Node EN 23 3 Step-by-Step 3.5 Parts replacement after fixed number of tap-change operations intervals 3.6 One-time retrofit and modifications 24 EN 4 Assemblies 4 Assemblies 4.1 General 4.1.1 Check list for maintenance NOTICE Safety, hazard and other information included in the MR operating instruc- tions for tap-changer type B must be observed! Please read the instructions carefully before starting work. The realization of the instructions below requires profound knowledge and experience that correspond to the knowledge acquired during a training at MR about maintenance on tap-changer type B. It is absolutely necessary that the selector switch has been removed. The instructions below specify which data have to be written down during maintenance and which activities have to be performed. Data Write down the following data during maintenance: ▪ Serial numbers of tap changer and motor-drive unit ▪ Tap changer type, highest voltage for equipment and number of positions ▪ Number of tap-change operations ▪ Motor-drive unit type ▪ Transformer data ▪ Application ▪ Commissioning Check list for maintenance Tap-changer head with cover Without change-over selector ▪ Seal tightness of tap-changer head ▪ Condition of toothing on crown wheel and pinion, flank clearance ▪ Wear or abrasion of bearing flange of selector gear cover ▪ Tight seat and wear of tripping switch ▪ Check catch of energy accumulator housing (crack formation) EN 25 4 Assemblies With change-over selector ▪ Check clearance of drive roller of cogwheel and drive crank of change- over selector ▪ Wear of cogdisk bearing of selector gear cover ▪ Indication disk attachment (welded with plastic cogwheel) Contact cylinder ▪ Seal tightness ▪ Condition of hard-paper cylinder ▪ Contact wear ▪ Check current take-off ring Switching cylinder ▪ Locking pawl and eccentric, check for crack formation, wear of tripping rollers, condition of locking pawl tension springs ▪ Top driving disk, wear of toothing and tight seat of locking pawl bearing pin ▪ Bottom driving disk, wear of toothing ▪ Slide contact, wear of contact surface, condition of current take-off lead and pressure springs ▪ Easy movement of bearing bolt ▪ Check that all bolts are tight ▪ When changing contacts, check gaps between main contacts and attach- ment bolts on the switching element Switching element ▪ Wear of main and auxiliary contacts ▪ Condition of all leads ▪ Tight seat of lock nuts of connecting plates and / or current collector disk (if not installed yet, spring washers should be installed to set the gap due to shrinkage) ▪ Condition of contact springs and / or their attachment ▪ Check of guide plates, wear of contact carrier guide ▪ Check running of rotating tube, and check cracking ▪ Tight seat of auxiliary contact carrier attachment (if not installed yet, spring washers should be installed to set the gap due to shrinkage) ▪ Main contact carrier, check axial play 26 EN 4 Assemblies ▪ Transition resistors, condition of resistor material and groove carrier, plus measurement of resistance value ▪ Check that all bolts are tight Current collector disk (delta version only) ▪ Condition of twin flexible cables and pressure springs ▪ Running and travel of guide pieces ▪ Wear of take-off contacts (max. wear approx. 3 mm) ▪ Check tight seat of take-off contacts 4.1.1.1 New Node 4.1.2 Tap-changer head with cover Without change-over selector ▪ Seal tightness of tap-changer head ▪ Condition of toothing on crown wheel and pinion, flank clearance ▪ Wear or abrasion of bearing flange of selector gear cover ▪ Tight seat and wear of tripping switch ▪ Check catch of energy accumulator housing (crack formation) With change-over selector ▪ Check clearance of drive roller of cogwheel and drive crank of change- over selector ▪ Wear of cogdisk bearing of selector gear cover ▪ Indication disk attachment (welded with plastic cogwheel) EN 27 4 Assemblies 4.2 Contact system, switching element 4.2.1 Wear on switching element This chapter describes determination of wear on switching element type B and type C and subsequent actions. Determination of maximum wear and limit values Use a caliper to measure play between rotating tube and guide plates (play "1") and play between slot in guide plates and the auxiliary contact guide (play "2", see following figure). Play "2" Play "1" Play "2" Figure 6: Switching element showing marked play "1" and play "2" Max. permitted value of: ▪ play "1" is 2.5 mm (measure when new: 0.1 mm). ▪ play "2" is 3.0 mm (measure when new: 1.0 mm). 28 EN 4 Assemblies Evaluation of the measurement of play "1" between rotating tube and guide plates and further procedure See the following table for how to proceed further. regarding play "1". Measured Further procedure value play "1" ≥ 2.0 mm Make a note of the measured value in the service report. The measured value is used to determine the measures to be taken during the next maintenance. ≥ 2.5 mm Interchange the inner guide plates with the outer guide plates The interchange is not possible for all versions of the guide plates, see the following lines. Ist ein Tausch nicht möglich, zuständigem Sach- bearbeiter kontaktieren. If an interchange is carried out, it must be noted in the service report. The measured value is used to determine the measures to be taken during the next maintenance. Table 5: Evaluation of the measurement of play "1" and further procedure Guide plates versions Depending on the year of manufacture, one of the three versions of the guide plates shown in the figure below was installed. 1 2 3 Figure 7: Guide plates versions 1 Old version, hard paper, 2 GRP version, white, without brass brown 3 New version GRP, white, with brass Interchange the inner guide plates with the outer guide plates EN 29 4 Assemblies Replacing the inner guide plates with outer guide plates is not possible for all versions of the guide plates and is also not necessary for all versions of the guide plates. Details can be found in the table below. N Delivery Versions, proper- Interchange the inner guide plates with the o period ties outer guide plates 1 to Old version, hard Contact OPS. 1970-06-3 paper, brown Interchanging inner guide plates for outer 0 guide plates is technically not possible. 2 From GRP version, Interchanging inner guide plates for outer 1970-07-0 white, without guide plates is technically possible. 1 brass, wears out heavily 3 Not speci- New version GRP, Interchanging inner guide plates for outer fied white, with brass, guide plates is technically usually not neces- no significant wear sary. Table 6: Interchange the inner guide plates with the outer guide plates - depending on the ver- sion Evaluation of the measurement of play "2" between slot in the guide plates and auxiliary contact holder and further procedure See the following table for how to proceed further. regarding play "2". Mea- Further procedure sured value play "2" ≥ 2.0 Make a note of the measured value in the service report. mm The measured value is used to determine the measures to be taken dur- ing the next maintenance. ≥ 3.0 Contact OPS. mm Table 7: Evaluation of the measurement of play "2" and further procedure 4.2.1.1 Change log 2023-11-15 TSC Steindl 1. Guide plate versions added. Replacing the inner for outer guide plates is not necessary for every variant and is not possible for every variant. 2000-10-10 TS3 Dinauer 1. First publication 30 EN 4 Assemblies 4.2.2 Max. permitted contact wear EN 31 Maximum admissible contact wear (Summary) Replacement for document TCS06004en TCS06004 is replaced owing to the correction for V200 14pitches CST09001en.xls CST1 Suw 10.12.2009 Page 1/1 OLTC type Dimensions of the contacts in mm, Max. admissible or OLTC-dependent reference dimension in mm contact wear Additional wear criterions Entry in with diverter switch inserts type G 22000, R, T in mm SAP documentation as New condition minimum residual value (individual wear) movable fixed movable fixed SC TC SC TC SC TC SC TC SC RC TC A 25 Ø 25 Ø - - 23 Ø 23 Ø - - 2Ø 2Ø none diameter B 5-6 4,5-6 - - 2 1,5 - - 3 3 none individual wear C250 5-6 4,5-6 ∗ ∗ 2 1,5 - - 3 3 none individual wear C350 18,5 18 ∗ ∗ 10,5 10 - - 8 8 none individual wear bis bis 19,5 19,5 V200 - except 22 Ø 22Ø - - 16 Ø 16 Ø - - 6Ø 6Ø none diameter with 14 pitches V200 14 pitches 22 Ø 20 Ø - - 16 Ø 16 Ø - - 6Ø 4Ø none diameter V350/500/ 22 Ø 22 Ø - - 17 Ø 17 Ø - - 5Ø 5Ø see V__09001.doc (TS Manual) diameter 700 - except with 14 pitches V350/700 14 pit. 22 Ø 20 Ø - - 17 Ø 17 Ø - - 5Ø 3Ø see V__09001.doc (TS Manual) diameter SAP document.: individual wear M 8 8 8 8 4 4 4 4 4 4 see TS284043.1 (TS Manual) addit. cont. sheet: indivi. wear D 20000 2 4 11 10 0,5 2 9,5 8 1,5 2 none individual wear oder 2,5 4 11,5 10 0,5 2 9,5 8 2 2,5 D 21000 8,5 8,5 11,5 11,5 3,5 3,5 6,5 6,5 5 5 see TS282034 (TS Manual) individual wear D 0466 6 6 6 6 1 1 1 1 5 5 see TCS05011.doc individual wear D 0444, 6 6 6 6 1 1 1 1 5 5 (TS Manual) SAP document.: individual wear E 6 6 6 6 1,5 1,5 1,5 1,5 4,5 4,5 see SI_E_2 (TS Manual) addit. contact sheet: individ. wear F 21000 8 8 8 8 1 1 1 1 7 7 individual wear F 23000 9,5 8 10 8 3 1 2,5 1 7 7 see TCS05010.doc F 24000 8 8 8 8 1 1 1 1 7 7 (TS Manual) F 26000 9,5 8 10 8 3 1 2,5 1 7 7 add. contact sheet F26000 T and R 34 34 34 34 22 22 22 22 6 6 SAP document.: total wear if end inspection see inspection instructions type R additional contact sheet sheet is not available G 21000 7 7 7 7 1 1 1 1 6 6 see TCS05012.doc SAP document.: total wear (TS Manual) additional contact sheet G 22000 entered into if total wear = 13 mm 6,5 6,5 see inspection instructions - type G SAP document.: total wear guide bridge TCS05012.doc (TS Manual) additional contact sheet K 8,5 8,5 8,5 8,5 1,5 1,5 1,5 1,5 7 7 none individual wear SC = switching contact TC = transition contact * see document TS94N094 i. A. Uwe Seltsam Copies to: CTT, CST, TS Manual, CTE, CSxO, CST1, CST3 notice board, CS4T notice board, MR subsidiaries and representatives The copying, distribution and utilization of this document as well as the communication of its contents to others without expressed authorization is prohibited. Offenders will be held liable for the payment of damages. All rights reserved in the event of the grant of a patent, utility model or ornamental design registration F00788:01 CST09001en.XLS 11.12.2009 Seite 1/1 4 Assemblies 4.2.3 Notes for installing the take-off contacts on the current collector disk NOTICE Risk of personal damage or injury, damage to property or mal- function. If work is performed by insufficiently qualified personnel and/or safety in- structions are not observed, there is a risk of personal damage or injury, damage to property or malfunction. ► Safety, hazard and other information included in the MR operating in- structions for the relevant on-load tap-changer type must be observed! ► Please read the instructions carefully before starting work. ► The realization of the instructions below requires profound knowledge and experience that correspond to the knowledge acquired during a train- ing at MR about maintenance of the relevant on-load tap-changer type. ► It is absolutely necessary that the diverter switch insert (or selector switch insert, respectively) has been removed. The instructions below describe how to install the take-off contacts on the switching element's current collector disk. General Scope of application These instructions apply to variants of the on-load tap-changer types OILTAP® B and C shown in the following table. Tap changer type Version OILTAP® B B III 150D OILTAP® C C III 250D, C III 350D, C I 400, C I 600, C I 602, C I 900 Table 8: Overview of on-load tap-changer types Replacement criteria for the take-off contacts If, during maintenance, you find that old take-off contact variants are still in- stalled, you must install the current variant (regardless of wear). If the current take-off contact variant is installed and wear is ≥ 3 mm, replace the take-off contacts. The wear is the difference of the measured value between the front of the take-off contact head and the wrench surface and the new value of 17 mm (see A.1). EN 33 4 Assemblies An overview of previous take-off contact variants is shown in the following figure. old variants current variant Figure 8: Take-off contact head variants A detailed drawing of the permitted take-off contact head variant is shown in the attachment. Variant 1 Variant 2 Lock tab Guide piece Table 9: Lock tabs and correlating guide pieces of current collector disk 34 EN 4 Assemblies Installation Variant 1 Align lock tab parallel to guide piece. Figure 9: Aligning lock tab Secure the lock tab against turning. Torque the take-off contact to M = 8 Nm and make sure it is aligned parallel to the lock tab. Figure 10: Tightening the take-off contact head Bend lock tab upward. Figure 11: Bending upward EN 35 4 Assemblies Secure the lock tab. Figure 12: Securing The lock tab must fit closely parallel and completely to the take-off contact head. Figure 13: Alignment of lock tab Variant 2 Bend one corner of the lock tab in the direction of the thread. Figure 14: Bending the lock tab Insert take-off contact head together with the bent lock tab into the guide piece. Secure the lock tab against turning. Torque the take-off contact head to M = 8 Nm and make sure it is aligned parallel to the edge of the current collector disk. 36 EN 1 2 3 4 5 6 7 8 9 10 4x Text bo Text b 11 12 13 14 15 16 17 18 19 20 Text box Text box 8 M8 x 20 30 Nm 4 Assemblies 6 cm Arial Unicode 9, normal Punch the lock tab's bent side and even guide piece side together. Figure 15: Punching lock tab and guide piece together As a result, the lock tab must be tightly seated on guide piece. Figure 16: Tightly seated lock tab Secure take-off contact head with opposite side of the lock tab. Figure 17: Securing take-off contact head with lock tab Make sure that lock tab is tight. Figure 18: Tightly seated lock tab (11) EN 37 1 2 3 4 5 6 7 8 9 10 A B AB 4 Assemblies 4x Textfeld 1 2 3 4 5 6 7 8 9 10 Textfeld 11 12 13 14 15 16 17 18 19 20 Textfeld Textfeld 8 M8 x 20 30 Nm Check It is absolutely necessary to check the reset force of the take-off contact heads after they have been installed and secured. 6 cm To do so, use appropriate tools to push in and release each take-off contact Arial Unicode 9, normal head multiple times. Figure 19: Pushing the take-off contact in and releasing it The take-off contact must move to its original position automatically. Repeat the procedure several (5 – 10) times per take-off contact head. If the take-off contact head does not move back to its original position, find the cause and eliminate it 38 EN 4 Assemblies Attachment Take-off contact – current design Wrench surface 17 EN 39 4 Assemblies Current collector disk Current collector disk Take-off contact 4.2.4 Current collector disk (delta version only) ▪ Condition of twin flexible cables and pressure springs ▪ Running and travel of guide pieces ▪ Wear of take-off contacts (max. wear approx. 3 mm) ▪ Check tight seat of take-off contacts 4.2.5 Switching element ▪ Wear of main and auxiliary contacts ▪ Condition of all leads ▪ Tight seat of lock nuts of connecting plates and / or current collector disk (if not installed yet, spring washers should be installed to set the gap due to shrinkage) ▪ Condition of contact springs and / or their attachment ▪ Check of guide plates, wear of contact carrier guide ▪ Check running of rotating tube, and check cracking ▪ Tight seat of auxiliary contact carrier attachment (if not installed yet, spring washers should be installed to set the gap due to shrinkage) ▪ Main contact carrier, check axial play ▪ Transition resistors, condition of resistor material and groove carrier, plus measurement of resistance value ▪ Check that all bolts are tight 40 EN 4 Assemblies 4.2.6 Switching cylinder ▪ Locking pawl and eccentric, check for crack formation, wear of tripping rollers, condition of locking pawl tension springs ▪ Top driving disk, wear of toothing and tight seat of locking pawl bearing pin ▪ Bottom driving disk, wear of toothing ▪ Slide contact, wear of contact surface, condition of current take-off lead and pressure springs ▪ Easy movement of bearing bolt ▪ Check that all bolts are tight ▪ When changing contacts, check gaps between main contacts and attach- ment bolts on the switching element 4.2.7 Contact cylinder ▪ Seal tightness ▪ Condition of hard-paper cylinder ▪ Contact wear ▪ Check current take-off ring EN 41 4 Assemblies 4.3 Energy accumulator, gearbox 4.3.1 Trip roller and locking pawl replacement This section describes the requirements for replacing trip roller and locking pawl. Criteria for replacing the trip roller If trip roller 021 946:01 with 21 mm diameter is installed in a tap changer type OILTAP® B or OILTAP® C, it must be replaced with a trip roller with 21.5 mm diameter during maintenance. The necessary material is listed in attachment "Materials". When replacing the trip roller, roller bolts and split pins must be replaced too. Split pin Trip roller Roller pin Figure 20: Overview energy accumulator Before installing the new trip roller, measure the diameter of the locking pawl holes. If diameter of one of the holes is larger than or equal to 7.5 mm Ø , locking pawl and eccentric must be replaced. Locking pawl holes Figure 21: Locking pawl holes 42 EN 4 Assemblies Criteria for replacing the locking pawl of tap changer type B or C The following instructions are based on the assumption that the trip roller with 21.5 mm diameter is installed. Measure total play of trip roller to locking pawl (play II) as shown in the following figure. If total play "Play II“ is larger than 1.0 mm, roller bolt and trip roller must be replaced. After the replace- ment, if total play "Play II" is still larger than 1.0 mm, locking pawl and eccen- tric must also be replaced. Roller pushed in direction ↑ Roller pushed in direction ↓ Play II Figure 22: Measurement total play “Play II” Material list for replacement of trip roller Item Quantity Part no. Description 10 2 02194602 Trip roller 20 2 02194705 Roller pin 30 2 455090 Split pin 40 1 08901201 Locking pawl with eccentric (if neces- sary) Table 10: Material list for replacement of trip roller EN 43 4 Assemblies 4.4 Supporting cylinder/supporting bars, coupling shaft, switching column 4.5 Transition impedance and protective circuit 4.6 Oil compartment 44 EN