VACUTAP VR 2010 Maintenance Instructions PDF
Document Details
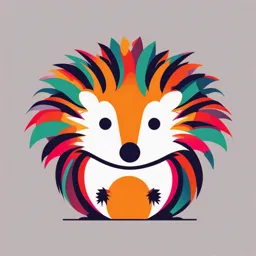
Uploaded by ValuableSugilite
Pink University
2019
Tags
Related
- OILTAP V-CDS-Komplett Maintenance Instructions PDF
- OILTAP® V Operating Instructions PDF
- VACUTAP VR 2010 Maintenance Instructions PDF
- VACUTAP VR 2010 Spare Parts & Maintenance Steps PDF
- VACUTAP VR 2010 Spare Parts & Instructions PDF
- IA 75/80 (Partial Issue) On-Load Tap-Changer Inspection Instructions PDF
Summary
This document provides step-by-step instructions for the maintenance and testing of a VACUTAP® VR 2010 on-load tap-changer. It includes safety precautions, procedures for checking latching conditions, and identifying specific parts. Detailed procedures for both testing and part replacement are described, emphasizing safety. The document also includes a spare parts list.
Full Transcript
1 Introduction 1 Introduction NOTICE Risk of personal damage or injury, damage to property or mal- function. If work is performed by insufficiently qualified personnel and/or safety in- structions are not obs...
1 Introduction 1 Introduction NOTICE Risk of personal damage or injury, damage to property or mal- function. If work is performed by insufficiently qualified personnel and/or safety in- structions are not observed, there is a risk of personal damage or injury, damage to property or malfunction. ► Safety, hazard and other information included in the MR operating in- structions for the relevant on-load tap-changer type must be observed! ► Please read the instructions carefully before starting work. ► The realization of the instructions below requires profound knowledge and experience that correspond to the knowledge acquired during a train- ing at MR about maintenance of the relevant on-load tap-changer type. ► It is absolutely necessary that the diverter switch insert (or selector switch insert, respectively) has been removed. EN 1 2 Spare parts list 2 Spare parts list 2 EN 2 Spare parts list 2.1 Spare parts list - VACUTAP® VR EN 3 Spare parts for OLTC Date: 30.07.2019 Type VR Doc.: VR1010e.xls Pictures of parts Designation Pcs Part no. Remarks Cover gasket 1 860258 Set of screws for exchange of IEM 1 77977500 Only for emergency Repacement set tap change supervisory control VR 1 1001026700 O-ring gasket 16x4 1 40030302 Parts used for replacemment drive shaft with predetermined breaking Drive shaft VR 1100NM 1 71217401 point Circlip 20 x 1.5 1 452217 Drive shaft upper side Circlip 33x1.5 1 452229 Drive shaft lower side For this documentation we reserve all rights according to standard DIN 34, section 2.1. Page 1 of 2 Spare parts for OLTC Date: 30.07.2019 Type VR Doc.: VR1010e.xls Pictures of parts Designation Pcs Part no. Remarks For this documentation we reserve all rights according to standard DIN 34, section 2.1. Page 2 of 2 3 Step-by-Step 3 Step-by-Step 3.1 Tests and condition-based parts replacement at each maintenance 3.1.1 Perform test tap-change operations NOTICE Damage on on-load tap-changer If you do not comply with the following instructions and their correct se- quence, there is a risk of damage to the on-load tap-changer while perform- ing test tap-change operations on the removed on-load tap-changer insert. 1. Ensure firm and stable standing of the DSI. 2. Grab the upper shielding ring of the coupling shaft with both hands. Be sure to wear protective gloves. 3. Perform slow and continuous turning movement until the cocking sledge releases the locking pawl and the DSI operates. Do not continue turning after release of the locking pawl until diverter switch operation is com- pleted. 4. Continue turning slowly until the eccentric has safely moved beyond the dead center position (final locking). 5. Check latched position (DSI must be in final latching position on required side) and position of moving MTF/TTF or MDC/TDC contacts. 6. Check the MTF/TTF or MDC/TDC operating levers (levers should not be broken or cracked). 7. Check the actuating cams for vacuum interrupters MSV/TTV (cams should not be broken or cracked). 8. Check the MSV/TTV actuating rollers (no pressure marks permitted on the rollers). 3.1.2 Check of latching condition In the following is described how to check the latching condition of diverter switch inserts type VACUTAP® VR® model 2010. This check must be performed during each maintenance and each VACUTAP® Condition Assessment (de-energized). Description based on the real object The following figure shows the energy accumulator of the DSI, type VR. The energy accumulator has both a locking pawl and a cocking sledge insert on the left-hand side and on the right-hand side. 6 EN 3 Step-by-Step Latched (in the following figure on the bottom left): One of the two pawls rests without gap against the cocking slide insert! Unlatched (in the following figure on the bottom right): A gap forms between locking pawl and cocking slide insert; in the figure, the gap is marked "d". Cocking slide insert Locking pawl, side A Latched! No gap! Unlatched! Gap "d"! d Figure 1: Energy accumulator latched (bottom left) and unlatched (bottom right) 3.1.2.1 Details - Check of latching condition In the following is described how to check the latching condition of diverter switch inserts type VACUTAP® VR® model 2010. This check must be performed during each maintenance and each VACUTAP® Condition Assessment (de-energized). Description based on the real object The following figure shows the energy accumulator of the DSI, type VR. The energy accumulator has both a locking pawl and a cocking sledge insert on the left-hand side and on the right-hand side. Latched (in the following figure on the bottom left): One of the two pawls rests without gap against the cocking slide insert! Unlatched (in the following figure on the bottom right): A gap forms between locking pawl and cocking slide insert; in the figure, the gap is marked "d". EN 7 3 Step-by-Step Cocking slide insert Locking pawl, side A Latched! No gap! Unlatched! Gap "d"! d Figure 2: Energy accumulator latched (bottom left) and unlatched (bottom right) Description based on 3D model For better understanding, the arrangement of the pawls, or the difference be- tween latched state and unlatched state, is shown by means of a 3D model additionally. The following figure shows the latched energy accumulator, with the locking pawl resting directly against the outer end of the cocking slide insert. Locking pawl, side A Locking pawl, side B Latched! No gap! Cocking slide insert Figure 3: 3D model of energy accumulator, view from below - latched 8 EN 3 Step-by-Step The following figure shows the unlatched energy accumulator, with a gap "d" between locking pawl and outer end of cocking slide insert. Unlatched! Gap "d"! d Figure 4: 3D model of energy accumulator, view from below - unlatched Checking the correct position of MTF lever and TTF lever At the end of the diverter switch operation, TTF lever and MTF lever must only have two defined positions, always converging in V shape. See the fol- lowing figure for the correct lever position when the on-load tap-changer is in final end position A. The right side of the figure shows final end position B. Whether the DSI is in final end position on side A or B can be seen from the position of the energy accumulator, see attachment "Position of energy ac- cumulator in final end position on side A, side B". For better understanding, the positions of the levers under the cover are il- lustrated by dashed lines. TTF lever TTF lever MTF lever MTF lever Figure 5: Position of TTF lever and MTF lever; side A (left) and side B (right) EN 9 3 Step-by-Step Summary Whether the OLTC is latched or not can be seen clearly from the resting po- sition of the pawls. The correct position of TTF lever and MTF lever is just an additional information. Inform TSC if irregularities are detected concerning the latched condition or the position of the TTF and MTF levers. 3.1.2.2 Position of energy accumulator in locked-on position to side A and side B (VR 2010) The left-hand side of the following figure shows the diverter switch insert locked on to side A. The right-hand side shows the diverter switch insert locked on to side B. A A B B Figure 6: Diverter switch insert type VR - side A (left) and side B (right) 3.1.2.3 Change log 1 April, 2023 TSC Steindl 1. Addition replacement criterion due to introduction of VACUTAP® Condi- tion Assessment. 2. Transfer to the CDS platform. 10 EN 3 Step-by-Step 24 Sept., 2010 TSC Zieglschmid 1. First publication 3.1.3 Inspecting coupling tube This measure must be performed during each inspection / each VACUTAP® Condition Assessment. Inspecting the coupling tube requires removing the coupling tube from the di- verter switch insert. To do so, proceed as follows. 1. Remove the 6 bolts holding the lower shielding ring. Figure 7: Screws on the lower shielding ring EN 11 3 Step-by-Step 2. Lift the lower shielding ring and remove the 6 drive sleeves using pliers. Figure 8: Drive sleeves on the lower shielding ring 3. Pull out the coupling tube. 4. Clean the coupling tube with transformer oil. Note the oil quality limit val- ues. 5. Perform thorough visual inspection of the inside and outside of the cou- pling tube. Check for mechanical or electrical damage (leakage paths, dis- charge marks). The coupling tube is refitted following the instructions for removal but in re- verse order. When refitting, ensure alignment of the red adjustment mark (at top of cou- pling tube) and the adjustment mark on the diverter switch insert (energy ac- cumulator, see appendix). 12 EN 3 Step-by-Step Figure 9: Adjustment marks Figure 10: Adjustment marks In order to ensure that the adjustment marks are positioned correctly, when assembling the coupling tube, the parts must be positioned as they were be- fore being disassembled. EN 13 3 Step-by-Step 3.1.3.1 Inspecting coupling tube Inspecting the coupling tube requires removing the coupling tube from the di- verter switch insert. Proceed as follows. 1. Remove the 6 screws holding the lower shielding ring. Figure 11: Screws on the lower shielding ring 14 EN 3 Step-by-Step 2. Lift the lower shielding ring and remove the 6 drive sleeves using pliers. Figure 12: Drive sleeves on the lower shielding ring 3. Pull out the coupling tube. 4. Clean the coupling tube with transformer oil. Note the oil quality limit val- ues. 5. Perform thorough visual inspection of the inside and outside of the cou- pling tube. Check for mechanical or electrical damage (leakage paths, dis- charge marks). The coupling tube is refitted following the instructions for removal but in re- verse order. EN 15 3 Step-by-Step When refitting, ensure alignment of the red adjustment mark (at top of cou- pling tube) and the adjustment mark on the diverter switch insert (energy ac- cumulator, see appendix). Figure 13: Adjustment marks Figure 14: Adjustment marks In order to ensure that the adjustment marks are positioned correctly, when assembling the coupling tube, the parts must be positioned as they were be- fore being disassembled. 3.1.4 Checking bolt connections VR® III und II (with VR® I 2602) In the following is described how to check the bolt connections of diverter switch inserts type VACUTAP® VR® model 2010. In the following is described how to check the bolt connections of diverter switch inserts type VACUTAP® VR® model 2010. 16 EN 3 Step-by-Step This measure must be performed during each inspection /maintenance and each VACUTAP® Condition Assessment (de-energized). Perform the work steps described below on all equipped sectors. Retighten bolts on TTF/MTF to in the following figure to 4.5 Nm. Use open-end wrench size 7 mm to hold nut on. Retighten bolts on TTV, top and bottom to 5 Nm. Retighten bolts on MSV, top and bottom (see following figures "MSV, top“ and "MSV, bottom“) to 5 Nm. If you cannot reach the lower bolt with your tool, check tight seat by visual and tactile inspection. TTF 5 7 8 1 2 3 4 MSV TTV 6 9 MTF Figure 15: Overview VR® II and III (with VR® I 2602) Model 2010 3.1.4.1 Details - Checking bolt connections VR® III und II (with VR® I 2602) In the following is described how to check the bolt connections of diverter switch inserts type VACUTAP® VR® model 2010. This measure must be performed during each inspection /maintenance and each VACUTAP® Condition Assessment (de-energized). Perform the work steps described below on all equipped sectors. Retighten bolts on TTF/MTF to in the following figure to 4.5 Nm. Use open-end wrench size 7 mm to hold nut on. Retighten bolts on TTV, top and bottom to 5 Nm. Retighten bolts on MSV, top and bottom (see following figures "MSV, top“ and "MSV, bottom“) to 5 Nm. If you cannot reach the lower bolt with your tool, check tight seat by visual and tactile inspection. EN 17 3 Step-by-Step TTF 5 7 8 1 2 3 4 MSV TTV 6 9 MTF Figure 16: Overview VR® II and III (with VR® I 2602) Model 2010 18 EN 3 Step-by-Step Figure 17: MSV, top EN 19 3 Step-by-Step Figure 18: MSV, bottom Glue bolts with OT30 or OT80 coating are used in all other current-carrying bolted connections; it is not permitted to retighten them. Check tight seat of these bolt connections by visual and tactile inspection. 3.1.4.2 Change log 1 April, 2023 TSC Steindl 1. Addition replacement criterion due to introduction of VACUTAP® Condi- tion Assessment. 2. Transfer to the CDS platform 18 Jan., 2016 TSC Harder 1. First publication 3.1.5 Checking bolt connections VR® I (without VR® I 2602) In the following is described how to check the bolt connections of diverter switch inserts type VACUTAP® VR® model 2010. This measure must be performed during each inspection /maintenance and each VACUTAP® Condition Assessment (de-energized). 20 EN 3 Step-by-Step Retighten bolts in sector S1 on TDCb/MDCb - to 4.5 Nm (see following figure). Use open-end wrench size 7 mm to hold nut on. Retighten bolt on TTVb top edge to 4.5 Nm. Use open-end wrench size 8 mm to hold the nut. Retighten bolt on TTVb bottom edge to 5 Nm. 1 TDCb 7 6 2 MSVb TTVb 4 3 8 5 MDCb Figure 19: Overview sector S1 VR® I (without VR® I 2602), Model 2010 3.1.5.1 Preliminary information instructions CAUTION! The following instructions are currently being updated. The following information is preliminary. 3.1.5.1.1 Details - Checking bolt connections VR® I (without VR® I 2602) In the following is described how to check the bolt connections of diverter switch inserts type VACUTAP® VR® model 2010. This measure must be performed during each inspection /maintenance and each VACUTAP® Condition Assessment (de-energized). EN 21 3 Step-by-Step Retighten bolts in sector S1 on TDCb/MDCb - to 4.5 Nm (see following figure). Use open-end wrench size 7 mm to hold nut on. Retighten bolt on TTVb top edge to 4.5 Nm. Use open-end wrench size 8 mm to hold the nut. Retighten bolt on TTVb bottom edge to 5 Nm. 1 TDCb 7 6 2 MSVb TTVb 4 3 8 5 MDCb Figure 20: Overview sector S1 VR® I (without VR® I 2602), Model 2010 22 EN 3 Step-by-Step Retighten bolts in sector S3 on TDCa/MDCa - to 4.5 Nm (see following figure). Use open-end wrench size 7 mm to hold nut on. Retighten bolt on TTVa top edge to 4.5 Nm. Use open-end wrench size 8 mm to hold the nut. Retighten bolt on TTVa bottom edge to 5 Nm. TDCa 1 5 7 MSVa 2 TTVa 3 8 4 MDCa Figure 21: Overview sector S3 VR® I (without VR® I 2602), Model 2010 In sectors S1 and S3, retighten bolts on MSVa and MSVb, top and bottom to 5 Nm, see foloowing figures "MSV, top“ and "MSV, bottom“. If you cannot reach the lower bolt with your tool, check tight seat by visual and tactile inspection. 3.1.5.2 Change log 1 April, 2023 TSC Steindl 1. Addition replacement criterion due to introduction of VACUTAP® Condi- tion Assessment. 2. Transfer to the CDS platform 18 Jan., 2016 TSC Harder 1. First publication EN 23 3 Step-by-Step 3.1.6 Replacement bolt connection of commutation contacts The instructions below describe how to replace the commutation contacts of an on-load tap-changer type VACUTAP® VR® - model 2010. This measure must be performed during each inspection /maintenance and each VACUTAP® Condition Assessment (de-energized). The replacement applies to all commutation contacts of a diverter switch in- sert, see following figure. Commutation contact Figure 22: Bolt connection of commutation contact 3.1.6.1 Details - Replacement bolt connection of commutation contacts The instructions below describe how to replace the commutation contacts of an on-load tap-changer type VACUTAP® VR® - model 2010. This measure must be performed during each inspection /maintenance and each VACUTAP® Condition Assessment (de-energized). The replacement applies to all commutation contacts of a diverter switch in- sert, see following figure. 24 EN 3 Step-by-Step Commutation contact Figure 23: Bolt connection of commutation contact NOTICE Damage on on-load tap-changer Damage to on-load tap-changer if connections are performed incorrectly ► When using bolts and nuts with OT30 or OT80 coating, always make sure that the bolted connection elements are free of oil and grease. Re- move oil and grease from all connection surfaces as much as possible. ► Be sure to install bolted connections with OT30 or OT80 coating in a sin- gle step with the specified tightening torque, and do not release or re- tighten them later. ► If a bolted connection must be released again, use new bolts or nuts with intact OT coating. Adhesive residues escaped from the OT nut must be removed. Tighten each new bolt to 5.5 Nm. 3.1.6.2 Materials See following table for the necessary material for replacing the bolt connec- tion of the commutation contacts. The stated number is per diverter switch insert. EN 25 3 Step-by-Step 1-sector diverter switch insert Part number Description Quantity 74245400 Allen bolt OT30-8 2 Table 1: Material for replacing bolt connection commutation contacts 1-sector diverter switch in- sert 2- and 3-sector diverter switch insert Part number Description Quantity 74245400 Allen bolt OT30-8 3 Table 2: Material for replacing bolt connection commutation contacts 2- and 3-sector diverter switch insert 3.1.6.3 Change log 1 April, 2023 TSC Steindl 1. Precise description of the required material for 1- / 2- or 3-sector diverter switch inserts with the relevant quantity. Only a bolt is replaced, the com- mutation contact remains the same. 2. Addition replacement criterion due to introduction of VACUTAP® Condi- tion Assessment. 3. Transfer to the CDS platform 23 April, 2020 TSC Hartmann 1. First publication 3.1.7 Measuring the transition resistance values VR® III und II (with VR® I 2602) In the following is described how to measure the transition resistors of di- verter switch inserts type VACUTAP® VR® model 2010. This measure must be performed during each inspection /maintenance and each VACUTAP® Condition Assessment (de-energized). 26 EN 3 Step-by-Step Use multimeter to check transition resistance value of every equipped sector (permitted deviation from desired value ± 10 %). It is unimportant if the di- verter switch insert is in the final end position on side A or side B. The transi- tion resistance can only be measured if the relevant vacuum interrupter (MSV or TTV) is open. Set measuring points as shown in the following figure. Carefully open MSV vacuum interrupter using open-end wrench. Measuring point 1 Measuring point 2 Open-end wrench on MSV Figure 24: Measuring transition resistance VR® II and III (with VR® I 2602), Model 2010 3.1.8 Measuring the transition resistance values VR® I (without VR® I 2602) In the following is described how to measure the transition resistors of di- verter switch inserts type VACUTAP® VR® model 2010. This measure must be performed during each inspection /maintenance and each VACUTAP® Condition Assessment (de-energized). Use multimeter to check the transition resistance values Ra and Rb (permit- ted deviation from desired value is ± 10 %). ▪ Operate diverter switch insert to final end position on side B to measure Ra (installed in sector S3). ▪ Operate diverter switch insert to final end position on side A to measure Rb (installed in sector S1). EN 27 3 Step-by-Step Set measuring points as shown in the following figure. Measuring point 1 Measuring point 2 Figure 25: Measuring transition resistance Rb (installed in sector S1) of VR® I (without VR® 2602), Model 2010 DSI in final end position on side A 3.1.9 Until 6 July, 2022 - Replacement of retaining rings energy accumulator latch The following section describes the replacement of retaining rings at the en- ergy accumulator latch VACUTAP® VR® - model 2010. Replacement crite- ria, see following table. Delivery Design with energy Measure during: date accumulator lock- ing pawl Maintenance VACUTAP® Condition Assessment (de-ener- gized) to Attachment of lock- See instructions Until Replacement of retain- 2022-07-06 ing pawls by means 6 July, 2022 - Energy ing ringsduring each of retaining ring accumulator carrier VACUTAP® Condition replacement [►Sec- Assessment (de-ener- tion 3.3.3, Page gized) according to 75]. these instructions From Tumble-riveted at- No measures re- No measures required 2022-07-07 tachment of locking quired pawls Table 3: Replacement criteria of retaining rings energy accumulator latch The following figure shows the energy accumulator from below. The red cir- cles indicate the retaining rings to be replaced. 28 EN 3 Step-by-Step Figure 26: Energy accumulator from below 3.1.9.1 Details - Replacement of retaining rings energy accumulator latch The following section describes the replacement of retaining rings at the en- ergy accumulator latch VACUTAP® VR® - model 2010. Replacement crite- ria, see following table. Delivery Design with energy Measure during: date accumulator lock- ing pawl Maintenance VACUTAP® Condition Assessment (de-ener- gized) to Attachment of lock- See instructions Until Replacement of retain- 2022-07-06 ing pawls by means 6 July, 2022 - Energy ing ringsduring each of retaining ring accumulator carrier VACUTAP® Condition replacement [►Sec- Assessment (de-ener- tion 3.3.3, Page gized) according to 75]. these instructions From Tumble-riveted at- No measures re- No measures required 2022-07-07 tachment of locking quired pawls Table 4: Replacement criteria of retaining rings energy accumulator latch The following figure shows the energy accumulator from below. The red cir- cles indicate the retaining rings to be replaced. Figure 27: Energy accumulator from below EN 29 3 Step-by-Step Installation NOTICE! NOTICE! Make sure not to over-spread the retaining ring during installation. Open the retaining ring only until inner diameter of 15.1 mm is reached (see following figure). Only open retaining rings with retaining ring pliers A11 with overexpension guard (see attachment "Tools", item 10). Before using retain- ing ring pliers check that maximum inner diameter of 15.1 mm is not ex- ceeded. Retaining ring Figure 28: Measuring opening diameter 15.1 mm of retaining ring DSI in final end position on side A DSI is in final end position on side A. The first retaining ring is accessible. Figure 29: Retaining ring, side A The retaining ring to be removed is marked in the mirror. Mirror Figure 30: Retaining ring from below, side A 30 EN 3 Step-by-Step Remove retaining ring using angled retaining ring pliers A11 with overexpen- sion guard (see attachment "Tools", item 10). NOTICE! Fitting washers are installed under retaining ring. Pay attention that the fitting washers do not drop when removing the retaining ring. Take care to install new retaining ring (see attachment "Materials", item 10) correctly, engaging in the corresponding groove in a formlocking manner! Figure 31: How to place retaining ring pliers, side A DSI in final end position on side B DSI is in final end position on side B. The second retaining ring is accessi- ble. Remove cable tie that attaches the cable Figure 32: Retaining ring, side B The retaining ring to be removed is marked in the mirror. Mirror Figure 33: Retaining ring from below, side B EN 31 3 Step-by-Step The second retaining ring with side B in the final end position is more difficult to reach. Place retaining ring pliers A11 (see attachment "Tools", item 10) as shown in the following figure. NOTICE! Fitting washers are installed under retaining ring. Pay attention that the fitting washers do not drop when removing the retaining ring. Take care to install new retaining ring (see attachment "Materials", item 10) correctly, engaging in the corresponding groove in a formlocking manner! Figure 34: How to place retaining ring pliers, side B After replacing the retaining ring, attach the stranded copper wire again, us- ing cable tie (see attachment "Materials", item 20) that you install in the hole provided for this purpose. Figure 35: Attaching stranded copper wire 3.1.9.2 Change log 2023-06-16 TSC Steindl 1. Material - Cable ties and MD - "Toolkit VR + VM TS" added. 2023-06-01 TSC Steindl 1. Material - retaining ring added. 32 EN 3 Step-by-Step 1 April, 2023 TSC Steindl 1. Addition replacement criterion due to introduction of VACUTAP® Con- dition Assessment 2. Addition replacement criterion - date of introduction of tumble-riveted variant 3. Transfer to the CDS platform 12 Dec. 2017 TSC Przibylla 1. First publication EN 33 3 Step-by-Step 3.2 Parts replacement after fixed number of tap-change operations intervals 3.2.1 Up until 31 October, 2011 - Replacing cocking sledge of energy accumulator The section below describes how to replace the cocking sledge of the en- ergy accumulator with the current version. The activity must be performed once for diverter switch inserts with production finish date up to 31 October, 2011. As a general rule, the replacement must be performed during maintenance on the diverter switch: ▪ After 250,000 operations at the earliest ▪ After 350,000 operations at the latest The material required for the replacement must be provided via SETER- SATZ by the responsible OPS before work begins. For how to remove the cocking sledge, see chapter Removing vacuum interrupters [►Section 3.2.3.4, Page 48]. Material for replacing cocking sledge of energy accumulator Item Designation of material Part no. 10 Cocking sledge KIT 1 sect. V130780005 (until production finish date 31 October, 2011) 20 Cocking sledge KIT 3/2 V130780004 sect. (until production finish date 31 October, 2011) Table 5: Material for replacing cocking sledge of energy accumulator 3.2.2 Up until 17 August, 2020 - Replacement of connecting lead MTF to transition resistor In the following, the replacement of the connecting lead between resistor pack and MTF or resistor pack and MDC is described. The activity must be performed once for diverter switch inserts with produc- tion finish date up to 17 August, 2020. The replacement of the connecting lead between resistor pack and MTF or resistor pack and MDC must be performed during the next replacement of the IEM (Interrupter exchange module / vacuum interrupters with sup- porting structure), independent from reason for IEM replacement, see in- structions Replacement of vacuum interrupters (600,000) [►Section 4.2.4, Page 97]. 34 EN 3 Step-by-Step NOTICE Danger of incorrectly performed bolt connection during replace- ment of connecting lead without replacing the IEM at the same time. NOTICE Risk of malfunction due to inappropriately performed bolt con- nection The spacer pin, see following figure, is kept in position by an integrated ro- tation lock on its base. When loosening the bolt of the bolt connection con- necting lead - spacer pin, the rotation lock of the spacer pin can become loosened and the spacer pin starts turning. As a consequence, after replac- ing the connecting lead, the bolt connection cannot be tightened appropri- ately. ► The replacement of the connecting lead between resistor pack and MTF or resistor pack and MDC must be performed must only be performed in combination with a replacement of the IEM (Interrupter exchange module / vacuum interrupters with supporting structure), see instructions. Spacer pin Figure 36: Location of bolt connection EN 35 3 Step-by-Step NOTICE Damage on on-load tap-changer Damage to on-load tap-changer if live connections are performed incorrectly ► When using bolts and nuts with OT30 or OT80 coating, always make sure that the bolted connection elements are free of oil and grease. Re- move oil and grease from all connection surfaces as much as possible. ► Glue residue of former OT30 or OT80 coating in internal threads must be removed by recutting the internal thread. ► Be sure to install bolted connections with OT30 or OT80 coating in a sin- gle step with the specified tightening torque, and do not release or re- tighten them later. ► If a bolted connection must be released again, use new bolts or nuts with intact OT coating. Adhesive residues escaped from the OT nut must be removed. 3.2.2.1 Details - Replacement of connecting lead MTF to transition resistor In the following, the replacement of the connecting lead between resistor pack and MTF or resistor pack and MDC is described. The activity must be performed once for diverter switch inserts with produc- tion finish date up to 17 August, 2020. The replacement of the connecting lead between resistor pack and MTF or resistor pack and MDC must be performed during the next replacement of the IEM (Interrupter exchange module / vacuum interrupters with sup- porting structure), independent from reason for IEM replacement, see in- structions Replacement of vacuum interrupters (600,000) [►Section 4.2.4, Page 97]. NOTICE Danger of incorrectly performed bolt connection during replace- ment of connecting lead without replacing the IEM at the same time. NOTICE Risk of malfunction due to inappropriately performed bolt con- nection The spacer pin, see following figure, is kept in position by an integrated ro- tation lock on its base. When loosening the bolt of the bolt connection con- necting lead - spacer pin, the rotation lock of the spacer pin can become loosened and the spacer pin starts turning. As a consequence, after replac- ing the connecting lead, the bolt connection cannot be tightened appropri- ately. ► The replacement of the connecting lead between resistor pack and MTF or resistor pack and MDC must be performed must only be performed in combination with a replacement of the IEM (Interrupter exchange module / vacuum interrupters with supporting structure), see instructions. 36 EN 3 Step-by-Step Spacer pin Figure 37: Location of bolt connection NOTICE Damage on on-load tap-changer Damage to on-load tap-changer if live connections are performed incorrectly ► When using bolts and nuts with OT30 or OT80 coating, always make sure that the bolted connection elements are free of oil and grease. Re- move oil and grease from all connection surfaces as much as possible. ► Glue residue of former OT30 or OT80 coating in internal threads must be removed by recutting the internal thread. ► Be sure to install bolted connections with OT30 or OT80 coating in a sin- gle step with the specified tightening torque, and do not release or re- tighten them later. ► If a bolted connection must be released again, use new bolts or nuts with intact OT coating. Adhesive residues escaped from the OT nut must be removed. General The objective of the replacement of the connecting lead between resistor pack and MTF or resistor pack and MDC is kink-free and tension-free instal- lation of the connecting lead to reduce mechanical stress of the connecting lead when compared to previous method of installation. Modification The replacement must be performed in each equipped sector. EN 37 3 Step-by-Step Removal First remove diverter switch from resistor pack, and then lift the diverter switch (also see chapter Removing vacuum interrupters [►Section 3.2.3.4, Page 48]). Remove the bolt connection shown in the following figure and remove connecting lead installed between resistor pack and MTF ( ). 2 1 Figure 38: Figure of the connecting lead to be replaced Installation Bolt connection at transition resistor Regardless of resistor variant and parallel bridges that might be present, in- stall new connecting lead to terminal block strip of the transition resistor in the following way: ▪ Connecting lead must be at a 45° angle outward and upward, and ▪ Cable shoe and lead must be in line (see following figure). 38 EN 3 Step-by-Step 45° Figure 39: Alignment of new connecting lead Observe the following order when installing the new connecting lead at the transition resistor (see following figure, from right to left): 3 6 5 4 2 1 Figure 40: Installation and bolt connection of new connecting lead at the transition resistor 1 Terminal strip 2 Resistor tag 3 Cable shoe of connecting lead 4 Connecting plate (if present) (alignment as shown in figure above) 5 Washer 6 Hex. head bolt OT30 Tightening torque: 5 Nm Preparing the bolt connection at the spacer pin EN 39 3 Step-by-Step After replacement of connecting leads in all relevant sectors: reinstall resistor pack to diverter switch. Be sure to install connecting lead kink-free and tension-free. For this pur- pose, pay attention that the connecting lead aligns "in a natural way" when installing the bolt to the MTF / MDC. When tightening the bolt to the MTF / MDC, hold connecting lead on the angled cable shoe in this position to prevent twisting of connecting lead. Figure 41: Installed new connecting lead Bolt connection at the spacer pin 40 EN 3 Step-by-Step NOTICE! From 1 February, 2023 onward, the bolt connection at the spacer pin is no longer performed using an OT30 bolt, but an uncoated bolt with a smaller locking washer, see following figure and following table. Old New 2 1 3 4 Figure 42: Change of bolt connection connecting lead at spacer pin, comparison old and new 1 Bolt 2 Cable terminal 3 Locking washer 4 Spacer pin OLD (until 31 January, 2023) NEW (from 1 February, 2023) Materials Part number Materials Part number HEX HEAD BOLT M6 74275000 HEX HEAD BOLT 450064 x 35 OT30-8 M6 X 35 8.8 un- coated Locking washer SK- 40179900 Locking washer SK- 70426901 M-6, 6.1X14.2 S6, 6.1X12.2 Table 6: Change of material bolt connection spacer pin Materials See Material for replacement of connecting lead MTF to transition resistor [►Section 3.2.2.2, Page 42]. For HVDC China design, see Additional material for replacement of connect- ing lead MTF to transition resistor in HVDC - China design [►Section 3.3.2.3, Page 73]. EN 41 3 Step-by-Step Tools For tools, see Tools for replacement of connecting lead MTF to transition re- sistor [►Section 3.2.2.3, Page 42]. 3.2.2.2 Material for replacement of connecting lead MTF to transition resistor Material for replacement of connecting lead MTF to transition resistor Number of Description Part no. sectors 1 TS-KIT CONTACT LEAD MTF-RES 1017005101 UG2V7 - 1SECT. 2 TS-KIT CONTACT LEAD MTF-RES 1017005201 UG2V4 - 2SECT. 3 TS-KIT CONTACT LEAD MTF-RES 1017005301 UG2V4 - 3SECT. Table 7: Material for replacement of connecting lead MTF to transition resistor Part sets from index 01 already include the new bolt connection material. Material sets with old bolt connection material: ▪ Are preferably replaced with new material sets. ▪ Alternatively, the two material numbers, see previous table, can be re- placed by MR within the scope of maintenance. ▪ If neither of these two options is possible, the old material sets may still be used. 3.2.2.3 Tools for replacement of connecting lead MTF to transition resistor Tools for replacement of connecting lead MTF to transition resistor Quantity Description Part no. 1 Nut splitter 63245800 1 DELO mixing pistol M 902 70974900 1 Mixing tube f. DELO Au- 70429200 tomix 1895 1 Glue DELO-DUOPOX 70429101 AD895 Table 8: Tools for replacement of connecting lead MTF to transition resistor 3.2.2.4 Change log 8 Feb., 2023, TSC - Steindl 1. Transfer to the CDS platform 2. Adjusting replacement criterion - Only in combination with replacement of IEM 42 EN 3 Step-by-Step 3. Addition material for diverter switch insert in HVDC application 4. Bolt connection C9 (bolt connection at spacer pin of connecting lead MTF - transition resistor) changed: OT30 bolt M6 x 35 replaced with uncoated bolt M6 x 35, locking washer SK-M-6 replaced with smaller locking washer SK-S6, affected material sets have been adjusted and indexes increased. 23. Nov., 2021, TSC - Reichenbach 1. Addition: Procedure for live bolt connections: Glue residue of former OT30 or OT80 coating in internal threads must be removed by recutting the in- ternal thread. 07 Aug., 2020, TSC – Beck 1. First publication 3.2.3 Replacement of vacuum interrupters (600,000) The instructions below describe how to replace the vacuum interrupters and supporting structure. As a general rule, the replacement must be performed after every 600,000 operations: ▪ After 580,000 operations at the earliest ▪ After 620,000 operations at the latest 3.2.3.1 Material IEM List of materials replacement kit All the materials required for the modification (vacuum interrupters with sup- porting structure and all bolts, washers etc.) will be provided to your place of work by the OPS. In addition, the technician performing the job can carry the materials listed in the following table with him, which includes spare material that is needed to remove a glued bolt connection and reinstall it again later. Qty Designation of mate- Part no. Note rial 1 per TS-kit mounting mate- 779775:xx Alternative material: Glue pole rial VR-IEM 2010 bolts and nuts Table 9: Material IEM vacuum interrupters Replacement (600,000) EN 43 3 Step-by-Step 3.2.3.2 Bolt connection elements IEM The following table shows the connection elements with locking elements and tightening torques. Replace every element of the bolt connections with a new one but make sure not to replace the elements indicated with "do not re- place" in the following table. Typ Qty Element Size Part num- Posi- Torque e ber tion in drawing C1 1 Hex. head bolt M8 x 40155100 0125 20 Nm 42 1 Locking washer SKM8 8 40180000 0130 C2 1 Hex. head bolt OT30 M8 x 74692901 0545 20 Nm 20 1 Washer 8 71539500 C3 1 Thread stud OT30 70969901 0550 23 Nm 2 Roller 17.8 70969801 0160 2 Roller 17.3 72492901 0165 2 Roller 16.8 72649001 0170 C4 1 Hex. head bolt OT80 M8 x 72467200 0520 20 Nm 50 6 Spring washer 8 40037300 0155 1 M8 washer 8 451326 0145 C5 1 Flat head screw with M6 x 74188800 0515 6.5 Nm torx OT30 25 2 Spring washer 6 40037201 0135 1 Washer 6 550397 0140 C6 1 Hex. head bolt OT30 M6 x 71841600 0535 6.5 Nm 25 2 Spring washer 6 40037201 0135 1 Washer 6 550397 0140 1 Square nut M6 74050600 0260 C7 1 Flat head screw with M5 x 74157900 0530 4.5 Nm torx OT30 12 1 Locking washer SKK 5 5 77902500 0200 1 Hex. nut M5 451237 0220 C8 1 Flat head screw with M5 x 74157900 0530 4.5 Nm torx OT30 12 1 Locking washer SKM 5 73645900 0235 5 1 Washer 5 71229801 0240 1 Hex. nut M5 451237 0220 44 EN 3 Step-by-Step Typ Qty Element Size Part num- Posi- Torque e ber tion in drawing C9 1 Hex. head bolt OT30 M6 x 74275000 0525 6.5 Nm 35 1 Locking washer SKM 6 40179900 0215 6 1 Adapter piece 74122401 C10 1 Hex. head bolt M5 x 450332 0205 5 Nm 12 1 Locking washer SKK 5 5 77902500 0200 C11 1 Hex. head bolt OT30 M6 x 71841600 0535 6.5 Nm 25 2 Spring washer 6 40037201 0135 2 Washer 6 550397 0140 1 Hex. nut M6 451238 0245 C12 1 Plastic hex. head bolt M8 x 71204602 0195 2 Nm 60 1 Plastic hex. nut M8 46010201 0190 1 Glue DELO-DUOPOX 704291:xx AD895 C13 1 Hex. head bolt OT30 M6 x 70481300 0540 9.5 Nm 16 1 Spring washer 6 40037201 0135 Table 10: Bill of materials fixing elements EN 45 3 Step-by-Step C1 6x M8 20 Nm C2 1x M8 20 Nm do not replace 0130 0125 0110 0545 C3 1x M10 23 Nm C4 6x M8 20 Nm Size 19 Function Pin 2 x 0160/0165/0170 0550 0145 6 x 0155 0520 C5 12x M6 6.5 Nm C6 6x M6 6.5 Nm 0140 2 x 0135 0515 0260 0140 2 x 0135 0535 C7 2x*) M5 4.5 Nm C8 2x*) M5 4.5 Nm do not replace 0220 0200 0530 0220 0240 0235 0530 46 EN 3 Step-by-Step C9 1x*) M6 6.5 Nm C10 1x*) M5 5 Nm do not replace 0210 0215 0525 0200 0205 C11 6x M6 6.5 Nm C12 2x*) M8 2 Nm secure with glue DELO- DUOPOX AD895 0245 2 x 0140 2 x 0135 0535 0190 0195 C13 3x M6 9.5 Nm 0135 0540 Table 11: Diagram of bolt connection elements *) per equipped sector 3.2.3.3 Tools IEM Qty Description Part number Note 1 Nut splitter 6324580001 1 DELO mixing pistol 70974900 3 Lifting eye bolt e.g., H7102000 optimum size M8 x 25 1 Ratchet box-end wrench size 65225000 10 mm Table 12: Tools IEM vacuum interrupters Replacement (600,000) EN 47 3 Step-by-Step 3.2.3.4 Removing vacuum interrupters If a tap-change supervisory control is installed, first move the diverter switch insert to the final end position on side A, independent of adjustment position. If the DSI is in the final end position on side A, remove the two C4 hex head bolts (marked "1" in figure "Energy accumulator") of the energy accumulator carrier; please note that the bolts can be hidden behind the tap-change su- pervisory control. Before proceeding, first make sure to move the DSI to the final end position on side B, independent of adjustment position. NOTICE Damage on on-load tap-changer If you do not comply with the following instructions and their correct se- quence, there is a risk of damage to the on-load tap-changer while perform- ing test tap-change operations on the removed on-load tap-changer insert. 1. Ensure firm and stable standing of the DSI. 2. Grab the upper shielding ring of the coupling shaft with both hands. Be sure to wear protective gloves. 3. Perform slow and continuous turning movement until the cocking sledge releases the locking pawl and the DSI operates. Do not continue turning after release of the locking pawl until diverter switch operation is com- pleted. 4. Continue turning slowly until the eccentric has safely moved beyond the dead center position (final locking). 5. Check latched position (DSI must be in final latching position on required side) and position of moving MTF/TTF or MDC/TDC contacts. 6. Check the MTF/TTF or MDC/TDC operating levers (levers should not be broken or cracked). 7. Check the actuating cams for vacuum interrupters MSV/TTV (cams should not be broken or cracked). 8. Check the MSV/TTV actuating rollers (no pressure marks permitted on the rollers). 48 EN 3 Step-by-Step Removing coupling shaft Remove six C1 connections, and remove the six sleeves. Next, move the coupling shaft upwards and remove it (see following figure). Remove C2 connection, and remove coupling flange. Sleeve C2 Coupling flange C1 Figure 43: Coupling shaft attachment Decoupling lifting device NOTICE! Make sure that the diverter switch insert is in final latching position before removing C3. Decoupling of lifting device by removing C3 bolt connection (see left side of the following figure). During removal of C3, lift the drive hub slightly using an open-end wrench to relieve the C3 bolt connection. To do so, put open-end wrench on moving main contact carrier and lift drive hub (see right side of the following figure). Lower drive hub slowly after removing C3. C3 Main contact carrier Drive hub Open-end wrench Figure 44: Decoupling of lifting device (left) and main contact carrier - lift drive hub (right) EN 49 3 Step-by-Step Removing wind-up sledge, eccentric and lifting bolt Remove the corresponding retaining rings (3x) and fitting washers from the guide rods, so that guide rods of energy accumulator can be pulled out in di- rection of arrow (see following figure). Pull out the guide rods until they do not attach the wind-up sledge anymore. Driving blocks Wind-up sledge Guide pins 1 Figure 45: Energy accumulator Remove wind-up sledge and eccentric with spacer sleeves and fitting wash- ers (see following figure). Next, push the guide rods in again to prevent the springs from becoming de- tached and to attach the cocking sledge. Eccentric Spacer sleeves Fitting washers Figure 46: Removing eccentric Lift drive hub again as when decoupling the lifting device (see figure "Main contact carrier - lift drive hub"), move the lifting connection to the side and remove it (see following figure). Lifting connection Figure 47: Lifting connection 50 EN 3 Step-by-Step Removing energy accumulator carrier Remove the C4 connections (6 or 4 in total). Screening caps are installed on the two C4 connections that are not sub- mersed in the energy accumulator carrier. The screening caps must be in- stalled again during re-assembly. C4 Figure 48: Energy accumulator carrier Remove 12 times C5 bolt connections, loosen 6 times C6 (see figure "Con- nection supporting bar - energy accumulator carrier"). Do not remove the C6 connections! Lift the energy accumulator carrier upwards. Take lifting bolt out and remove it (see figure "Upper base plate with lifting bolt"). C5 C6 Figure 49: Bolt connection supporting bar - energy accumulator carrier Lifting bolt Figure 50: Upper base plate with lifting bolt Removing transition resistors and selector drive shaft From every equipped sector, remove the specified bolt connections in the following sequence: ▪ 2 times connection C8, ▪ 2 time connection C7, EN 51 3 Step-by-Step ▪ Remove leads L1 and L2 (will not be used anymore), ▪ 1 time connection C10, ▪ 1 time connection C9, ▪ Remove the 2 C12 connections using nut splitter. ▪ Then remove 6 C11 connections and put down resistor pack slowly. C9 L1 C7 L2 C11 C8 C10 Nut splitter Figure 51: Diverter switch insert with installed resistor 52 EN 3 Step-by-Step Screw three lifting eye bolts in the connection points of the energy accumu- lator holder in the upper base plate (bolt connection C4). Lift IEM from resistor pack and selector drive shaft (see following figure). Lifting eye bolts Figure 52: Lifting the IEM 3.2.3.5 Installing new vacuum interrupters Overview screwing positions: Drawing of screwing positions [►Section 3.2.3.6, Page 63] EN 53 3 Step-by-Step Unpack new IEM and remove transport protection. All parts which were installed for transport protection are red (see following figure). All red parts must be removed. If you return the old IEM, install the transport protection to the removed IEM accordingly. Figure 53: IEM with transport protection NOTICE Damage on on-load tap-changer Damage to on-load tap-changer if connections are performed incorrectly ► When using bolts and nuts with OT30 or OT80 coating, always make sure that the bolted connection elements are free of oil and grease. Re- move oil and grease from all connection surfaces as much as possible. ► Be sure to install bolted connections with OT30 or OT80 coating in a sin- gle step with the specified tightening torque, and do not release or re- tighten them later. ► If a bolted connection must be released again, use new bolts or nuts with intact OT coating. Adhesive residues escaped from the OT nut must be removed. Installing transition resistors and selector drive shaft ▪ Before installing the C11 connections, make sure that the upper holder of the resistor pack rests against the lower base plate (connection point C12, figure "IEM with transport protection"). ▪ C12 connections must be secured with DELO-DUOPOX AD895. After glu- ing the C12 bolt connection, make sure to wait 3 hours before filling the di- verter switch oil compartment with oil. Alignment and trial tap-change op- erations can be performed after a waiting period of 1 hour. ▪ Install the elements in reverse order of removal, in accordance with chap- ter Removing vacuum interrupters [►Section 3.2.3.4, Page 48], section "Removing transition resistors and selector drive shaft". Replace leads L1 and L2 with new ones. 54 EN 3 Step-by-Step Installing energy accumulator carrier ▪ Screw lifting bolt down to limit stop, and then unscrew it again three quar- ters of a full turn (note if lifting bolt cannot be screwed down: hub with tapped hole can be turned relative to the upper base plate). ▪ Unscrew the C6 connections by one turn. NOTICE! Never remove the C6 connections. While the C6 connections are loosened, the supporting bars should not be exposed to transverse forces (e.g., twisting of IEM on the table). ▪ Install the energy accumulator carrier analog to removal procedure in ac- cordance with section Removing vacuum interrupters [►Section 3.2.3.4, Page 48], section "Removing energy accumulator carrier". ▪ Install the C4 connections. Install the screening caps to the two C4 con- nections that are not submersed. ▪ Install the C5 connections. ▪ The unscrewed C6 connections must be replaced one at a time. Do not remove several C6 connections at the same time. ▪ Replace the energy accumulator springs with the supplied energy accu- mulator springs, see following figure. Figure 54: Replacing energy accumulator springs NOTICE! If the old DSI (the one that is being serviced) was delivered before October 2011 and has reached 300,000 operations, the cocking sledge must be replaced with a new one. Replace it now if this has not yet been done. If necessary, the new cocking sledge will have been delivered with the rele- vant spare material. Installing eccentric and lifting connection ▪ Slide lifting connection on lifting bolt (lift drive hub for this purpose, see fig- ure "Installing lifting connection"). ▪ Support selector drive shaft from below so that it is in the topmost position (that is, selector drive shaft pushed up until limit stop). ▪ Install spacer sleeves and eccentric in accordance with figure "Marking eccentric - selector drive shaft"). Ensure correct position of marking holes (see figure "Marking eccentric - selector drive shaft")! EN 55 3 Step-by-Step ▪ Install wind-up sledge in reverse order compared to removal (see chapter Removing vacuum interrupters [►Section 3.2.3.4, Page 48], section "Re- moving wind-up sledge, eccentric and lifting bolt"); do not yet install the re- taining rings on the guide rods. ▪ The lower edge of the eccentric must be on the same level as the lower edge of the driving block (of the wind-up sledge, see figure "Lower edge of eccentric and lower edge of driving block on the same level"). Add fitting washers on adjustment position 1 (see figure "Eccentric on selector drive shaft") to adjust eccentric level. ▪ Install retaining rings and fitting washers to the guide rods. Figure 55: Installing lifting connection Figure 56: Marking eccentric - selector drive shaft 56 EN 3 Step-by-Step Eccentric Adjustment position 2 Driving block Adjustment position 1 Spacing sleeves Figure 57: Eccentric on selector drive shaft Driving block Eccentric Driving block Figure 58: Lower edge of eccentric and lower edge of driving block on the same level Installing coupling shaft Install coupling flange on selector drive shaft. Ensure correct position of marking boreholes (see following figure)! Coupling flange Figure 59: Marking borehole on coupling flange and selector drive shaft EN 57 3 Step-by-Step Top edge of selector drive shaft must be 0.1-0.4 mm higher than top edge of coupling flange (see following figure). Remove fitting washers from adjustment position 2 if selector drive shaft is too low. If the selector drive shaft is too high, add fitting washers at adjust- ment position 2 (see figure "Eccentric on selector drive shaft"). Add connec- tion C2. Upper edge selector drive shaft Upper edge coupling flange Figure 60: Connection flange - selector drive shaft Install coupling shaft on coupling flange. Ensure matching position of marking boreholes (see following figure)! The red marks (see figure "DSI in adjustment position") do not need to match in this work step. Install bushings in accordance with chapter Removing vacuum interrupters [►Section 3.2.3.4, Page 48], section "Removing coupling shaft", and per- form C1 screw connections. Figure 61: Marking holes 58 EN 3 Step-by-Step Only at the stage when the diverter switch insert is in adjustment position, the red marks on energy accumulator holder and coupling shaft must match (see following figure). Figure 62: DSI in adjustment position Coupling lifting device Lift drive hub as shown in section Removing vacuum interrupters [►Section 3.2.3.4, Page 48], section "Decoupling lifting device", using open-end wrench, and make C3 connection using old bolt and rollers with diameter of 17.3 mm (see chapter Connection elements [►Section 3.2.3.2, Page 44], ta- ble "Depiction of connection elements"). Check sizes shown in figure "Check sizes 1, 2 and 3 in cross-sections (DSI in final end position on side B)" in accordance with table "Check sizes lifting device". Lifting device 1 1 2 3 2 Figure 63: Check sizes 1, 2 and 3 in cross-sections (DSI in final end position on side B) EN 59 3 Step-by-Step Check size DSI in final end position DSI in final end position on side A on side B 1 ≥ 1 mm 2 ≥ 1 mm 3 ≥ 1 mm Table 13: Check sizes lifting device Measure check size on side B using feeler gauge, then move DSI to final end position on side A and measure check sizes and using feeler gauge. If the sizes are not within the required values, other rollers can be inserted at C3 to achieve the predefined values. ▪ Value below dimension or : Install rollers with diameter of 17.8 mm. ▪ Value below dimension : Install rollers with diameter of 16.8 mm. The two rollers can be combined randomly. 1 1 3 Figure 64: Measuring check sizes 1 and 3, DSI in final end position on side A 60 EN 3 Step-by-Step 2 2 Figure 65: Measuring check size 2, DSI in final end position on side B NOTICE Damage on on-load tap-changer If you do not comply with the following instructions and their correct se- quence, there is a risk of damage to the on-load tap-changer while perform- ing test tap-change operations on the removed on-load tap-changer insert. 1. Ensure firm and stable standing of the DSI. 2. Grab the upper shielding ring of the coupling shaft with both hands. Be sure to wear protective gloves. 3. Perform slow and continuous turning movement until the cocking sledge releases the locking pawl and the DSI operates. Do not continue turning after release of the locking pawl until diverter switch operation is com- pleted. 4. Continue turning slowly until the eccentric has safely moved beyond the dead center position (final locking). 5. Check latched position (DSI must be in final latching position on required side) and position of moving MTF/TTF or MDC/TDC contacts. 6. Check the MTF/TTF or MDC/TDC operating levers (levers should not be broken or cracked). 7. Check the actuating cams for vacuum interrupters MSV/TTV (cams should not be broken or cracked). 8. Check the MSV/TTV actuating rollers (no pressure marks permitted on the rollers). Proceed as follows if it is not possible to keep the required dimensions by varying the number of rollers at C3 (see following figure): ▪ Remove 3 C13 connections ▪ Remove sliding block of lifting device EN 61 3 Step-by-Step ▪ Push lifting connection from lifting bolt ▪ Turn lifting bolt one complete turn out ▪ Reinstall sliding block again, using the old C13 elements ▪ Couple lifting device ▪ Check the relevant sizes in accordance with table "Check sizes lifting de- vice"), and readjust using additional rollers on C3 connection if necessary. C13 Sliding block Figure 66: Sliding block of lifting device NOTICE! Finally, as soon as all check sizes are in the required range, re- place the screwing elements of C3 and C13 with new ones. 62 EN 3 Step-by-Step C6 3.2.3.6 Drawing of screwing positions C5 C8 C7 C13 C9 C3 C4 C1 C10 C11 C2 C4 C12 Figure 67: Drawing of screwing positions of vacuum interrupters with supporting structure EN 63 3 Step-by-Step 3.3 One-time retrofit and modifications 3.3.1 Up until 31 October, 2011 - Replacing cocking sledge of energy accumulator The section below describes how to replace the cocking sledge of the en- ergy accumulator with the current version. The activity must be performed once for diverter switch inserts with production finish date up to 31 October, 2011. As a general rule, the replacement must be performed during maintenance on the diverter switch: ▪ After 250,000 operations at the earliest ▪ After 350,000 operations at the latest The material required for the replacement must be provided via SETER- SATZ by the responsible OPS before work begins. For how to remove the cocking sledge, see chapter Removing vacuum interrupters [►Section 3.2.3.4, Page 48]. Material for replacing cocking sledge of energy accumulator Item Designation of material Part no. 10 Cocking sledge KIT 1 sect. V130780005 (until production finish date 31 October, 2011) 20 Cocking sledge KIT 3/2 V130780004 sect. (until production finish date 31 October, 2011) Table 14: Material for replacing cocking sledge of energy accumulator 3.3.1.1 Tools and material - Replacement of cocking sledge of energy accumulator Tools replacement xxx Item Description Part no. 10 MH-"Toolkit VM + VR TS“ 65246400:xx Table 15: Tools replacement xxx 64 EN 3 Step-by-Step Material for replacing cocking sledge of energy accumulator Item Designation of material Part no. 10 Cocking sledge KIT 1 sect. V130780005 (until production finish date 31 October, 2011) 20 Cocking sledge KIT 3/2 V130780004 sect. (until production finish date 31 October, 2011) Table 16: Material for replacing cocking sledge of energy accumulator 3.3.2 Up until 17 August, 2020 - Replacement of connecting lead MTF to transition resistor In the following, the replacement of the connecting lead between resistor pack and MTF or resistor pack and MDC is described. The activity must be performed once for diverter switch inserts with produc- tion finish date up to 17 August, 2020. The replacement of the connecting lead between resistor pack and MTF or resistor pack and MDC must be performed during the next replacement of the IEM (Interrupter exchange module / vacuum interrupters with sup- porting structure), independent from reason for IEM replacement, see in- structions Replacement of vacuum interrupters (600,000) [►Section 4.2.4, Page 97]. NOTICE Danger of incorrectly performed bolt connection during replace- ment of connecting lead without replacing the IEM at the same time. NOTICE Risk of malfunction due to inappropriately performed bolt con- nection The spacer pin, see following figure, is kept in position by an integrated ro- tation lock on its base. When loosening the bolt of the bolt connection con- necting lead - spacer pin, the rotation lock of the spacer pin can become loosened and the spacer pin starts turning. As a consequence, after replac- ing the connecting lead, the bolt connection cannot be tightened appropri- ately. ► The replacement of the connecting lead between resistor pack and MTF or resistor pack and MDC must be performed must only be performed in combination with a replacement of the IEM (Interrupter exchange module / vacuum interrupters with supporting structure), see instructions. EN 65 3 Step-by-Step Spacer pin Figure 68: Location of bolt connection NOTICE Damage on on-load tap-changer Damage to on-load tap-changer if live connections are performed incorrectly ► When using bolts and nuts with OT30 or OT80 coating, always make sure that the bolted connection elements are free of oil and grease. Re- move oil and grease from all connection surfaces as much as possible. ► Glue residue of former OT30 or OT80 coating in internal threads must be