Powder Metallurgy PDF
Document Details
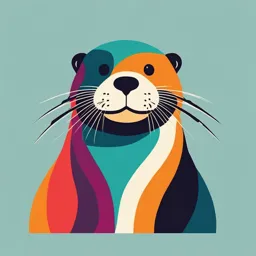
Uploaded by WellKnownSmokyQuartz
Tags
Summary
This document provides an overview of powder metallurgy, a metal processing technology used to create parts from metallic powders. It details the process, advantages, such as net shape production and reduced material waste, and disadvantages, like high tooling costs. The principles are explained by examples and diagrams.
Full Transcript
Powder Metallurgy Introduction Powder metallurgy (PM) is a metal processing technology in which parts are produced from metallic powders. The powders are compressed into the desired shape and then heated to cause bonding of the particles into a hard, rigid mass. Compression, called pre...
Powder Metallurgy Introduction Powder metallurgy (PM) is a metal processing technology in which parts are produced from metallic powders. The powders are compressed into the desired shape and then heated to cause bonding of the particles into a hard, rigid mass. Compression, called pressing, is accomplished in a press-type machine using tools designed specifically for the part to be manufactured. The tooling, which typically consists of a die and one or more punches, can be expensive, and PM is therefore most appropriate for medium and high production. The heating treatment, called sintering, is performed at a temperature below the melting point of the metal. Advantages PM parts can be mass produced to net shape or near net shape, eliminating or reducing the need for subsequent processing. The PM process itself involves very little waste of material; about 97% of the starting powders are converted to product. Owing to the nature of the starting material in PM, parts having a specified level of porosity can be made. This feature lends itself to the production of porous metal parts such as filters and oil-impregnated bearings and gears. Certain metals that are difficult to fabricate by other methods can be shaped by powder metallurgy. Tungsten is an example; tungsten filaments used in incandescent lamp bulbs are made using PM technology. Certain metal alloy combinations and cermets can be formed by PM that cannot be produced by other methods. PM compares favorably with most casting processes in terms of dimensional control of the product. Tolerances of 0.13 mm (0.005 in) are held routinely. PM production methods can be automated for economical production. Disadvantages/Limitations Tooling and equipment costs are high. Metallic powders are expensive. There are difficulties with storing and handling metal powders (such as degradation of the metal over time, and fire hazards with particular metals). There are limitations on part geometry because metal powders do not readily flow laterally in the die during pressing, and allowances must be provided for ejection of the part from the die after pressing. Variations in material density throughout the part may be a problem in PM, especially for complex part geometries. Most PM components are less than 2.2 kg (5 lb). Characterization Of Engineering Powders (A powder can be defined as a finely divided particulate solid) Geometric Features The geometry of the individual powders can be defined by the following attributes: (1) particle size and distribution (2) particle shape and internal structure (3) surface area (4) Interparticle Friction and Flow Characteristics (5) Packing, Density, and Porosity (6) Chemistry and Surface Films Virtually any metal can be made into powder form. There are three principal methods by which metallic powders are commercially produced, each of which involves energy input to increase the surface area of the metal. The methods are: (1) atomization (2) chemical (3) electrolytic In addition, mechanical methods are occasionally used to reduce powder sizes; however, these methods are much more commonly associated with ceramic powder production. Atomization This method involves the conversion of molten metal into a spray of droplets that solidify into powders. It is the most versatile and popular method for producing metal powders today, applicable to almost all metals, alloys as well as pure metals. There are multiple ways of creating the molten metal spray. Two of the methods shown are based on gas atomization, in which a high velocity gas stream (air or inert gas) is utilized to atomize the liquid metal. The gas flows through an expansion nozzle, siphoning molten metal from the melt below and spraying it into a container. The droplets solidify into powder form. In a closely related method, molten metal flows by gravity through a nozzle and is immediately atomized by air jets. The resulting metal powders, which tend to be spherical, are collected in a chamber below. This approach is similar to previous two, except that a high-velocity water stream is used instead of air. This is known as water atomization and is the most common of the atomization methods, particularly suited to metals that melt below 1600oC. Cooling is more rapid, and the resulting powder shape is irregular rather than spherical. The disadvantage of using water is oxidation on the particle surface. A recent innovation involves the use of synthetic oil rather than water to reduce oxidation. In both air and water atomization processes, particle size is controlled largely by the velocity of the fluid stream; particle size is inversely related to velocity. Several methods are based on centrifugal atomization. In one approach, the liquid metal stream pours onto a rapidly rotating disk that sprays the metal in all directions to produce powders. Chemical Reduction Chemical reduction includes a variety of chemical reactions by which metallic compounds are reduced to elemental metal powders. A common process involves liberation of metals from their oxides by use of reducing agents such as hydrogen or carbon monoxide. The reducing agent is made to combine with the oxygen in the compound to free the metallic element. This approach is used to produce powders of iron, tungsten, and copper. Another chemical process for iron powders involves the decomposition of iron pentacarbonyl (Fe(Co)5) to produce spherical particles of high purity. Other chemical processes include precipitation of metallic elements from salts dissolved in water. Powders of copper, nickel, and cobalt can be produced by this approach. Electrolysis In electrolysis, an electrolytic cell is set up in which the source of the desired metal is the anode. The anode is slowly dissolved under an applied voltage, transported through the electrolyte, and deposited on the cathode. The deposit is removed, washed, and dried to yield a metallic powder of very high purity. The technique is used for producing powders of beryllium, copper, iron, silver, tantalum, and titanium. Conventional Pressing And Sintering After the metallic powders have been produced, the conventional PM sequence consists of three steps: (1) blending and mixing of the powders; (2) compaction, in which the powders are pressed into the desired part shape; and (3) sintering, which involves heating to a temperature below the melting point to cause solid-state bonding of the particles and strengthening of the part. Blending And Mixing Of The Powders To achieve successful results in compaction and sintering, the metallic powders must be thoroughly homogenized beforehand. The terms blending and mixing are both used in this context. Blending refers to when powders of the same chemical composition but possibly different particle sizes are intermingled. Different particle sizes are often blended to reduce porosity. Mixing refers to powders of different chemistries being combined. An advantage of PM technology is the opportunity to mix various metals into alloys that would be difficult or impossible to produce by other means. The distinction between blending and mixing is not always precise in industrial practice. Blending and mixing are accomplished by mechanical means. Four alternatives are illustrated in figure next: (a) rotation in a drum (b) rotation in a double-cone container (c) agitation in a screw mixer (d) stirring in a blade mixer Other ingredients are usually added to the metallic powders during the blending and/or mixing step. These additives include: (1) lubricants, such as stearates of zinc and aluminum, in small amounts to reduce friction between particles and at the die wall during compaction (2) binders, which are required in some cases to achieve adequate strength in the pressed but unsintered parts Compaction In compaction, high pressure is applied to the powders to form them into the required shape. The conventional compaction method is pressing, in which opposing punches squeeze the powders contained in a die. The workpart after pressing is called a green compact, the word green meaning not yet fully processed. As a result of pressing, the density of the part, called the green density, is much greater than the starting bulk density. The green strength of the part when pressed is adequate for handling but far less than that achieved after sintering. Presses used in conventional PM compaction are mechanical, hydraulic, or a combination of the two. Because of differences in part complexity and associated pressing requirements, presses can be distinguished as: (1) pressing from one direction, referred to as single-action presses; or (2) pressing from two directions, any of several types including opposed ram, double-action, and multiple action. Compaction pressures typically range from 70 MPa (10,000 lb/in2) for aluminum powders to 700 MPa (100,000 lb/in2) for iron and steel powders. The required force for pressing depends on the projected area of the PM part (area in the horizontal plane for a vertical press) multiplied by the pressure needed to compact the given metal powders. Sintering After pressing, the green compact lacks strength and hardness; it is easily crumbled under low stresses. Sintering is a heat treatment operation performed on the compact to bond its metallic particles, thereby increasing strength and hardness. The treatment is usually carried out at temperatures between 0.7 and 0.9 of the metal’s melting point. The terms solid-state sintering or solid-phase sintering are sometimes used for this conventional sintering because the metal remains unmelted at these treatment temperatures. Sintering involves mass transport to create the necks and transform them into grain boundaries. The principal mechanism by which this occurs is diffusion; other possible mechanisms include plastic flow. Shrinkage occurs during sintering as a result of pore size reduction. This depends to a large extent on the density of the green compact, which depends on the pressure during compaction. Because PM applications usually involve medium-to-high production, most sintering furnaces are designed with mechanized flow-through capability for the workparts. The heat treatment consists of three steps, accomplished in three chambers in these continuous furnaces: (1) preheat, in which lubricants and binders are burned off; (2) sinter; and (3) cool down. Densification and Sizing A number of secondary operations are performed to increase density, improve accuracy, or accomplish additional shaping of the sintered part. Repressing is a pressing operation in which the part is squeezed in a closed die to increase density and improve physical properties. Sizing is the pressing of a sintered part to improve dimensional accuracy. Coining is a pressworking operation on a sintered part to press details into its surface. Some PM parts require machining after sintering. Machining is rarely done to size the part, but rather to create geometric features that cannot be achieved by pressing, such as internal and external threads, side holes, and other details. Impregnation and Infiltration Porosity is a unique and inherent characteristic of powder metallurgy technology. It can be exploited to create special products by filling the available pore space with oils, polymers, or metals that have lower melting temperatures than the base powder metal. Impregnation Impregnation is the term used when oil or other fluid is permeated into the pores of a sintered PM part. The most common products of this process are oil-impregnated bearings, gears, and similar machinery components. Self-lubricating bearings, usually made of bronze or iron with10% to 30% oil by volume, are widely used in automotive industry. The treatment is accomplished by immersing the sintered parts in a bath of hot oil. An alternative application of impregnation involves PM parts that must be made pressure tight or impervious to fluids. In this case, the parts are impregnated with various types of polymer resins that seep into the pore spaces in liquid form and then solidify. In some cases, resin impregnation is used to facilitate subsequent processing, for example, to permit the use of processing solutions (such as plating chemicals) that would otherwise soak into the pores and degrade the product, or to improve machinability of the PM workpart. Infiltration Infiltration is an operation in which the pores of the PM part are filled with a molten metal. The melting point of the filler metal must be below that of the PM part. The process involves heating the filler metal in contact with the sintered component so that capillary action draws the filler into the pores. The resulting structure is relatively nonporous, and the infiltrated part has a more uniform density, as well as improved toughness and strength. An application of the process is copper infiltration of iron PM parts. Alternative Pressing And Sintering Techniques Isotactic Pressing A feature of conventional pressing is that pressure is applied uniaxially. This imposes limitations on part geometry, because metallic powders do not readily flow in directions perpendicular to the applied pressure. Uniaxial pressing also leads to density variations in the compact after pressing. In isostatic pressing, pressure is applied from all directions against the powders that are contained in a flexible mold; hydraulic pressure is used to achieve compaction. Isostatic pressing takes two alternative forms: (1) cold isostatic pressing and (2) hot isostatic pressing. Cold Isostatic Pressing Cold isostatic pressing (CIP) involves compaction performed at room temperature. The mold, made of rubber or other elastomer material, is oversized to compensate for shrinkage. Water or oil is used to provide the hydrostatic pressure against the mold inside the chamber. Advantages of CIP include more uniform density, less expensive tooling, and greater applicability to shorter production runs. Good dimensional accuracy is difficult to achieve in isostatic pressing because of the flexible mold. Consequently, subsequent finish shaping operations are often required to obtain the required dimensions, either before or after sintering. Hot Isostatic Pressing Hot isostatic pressing(HIP) is carried out at high temperatures and pressures, using a gas such as argon or helium as the compression medium. The mold in which the powders are contained is made of sheet metal to withstand the high temperatures. HIP accomplishes pressing and sintering in one step. Despite this apparent advantage, it is a relatively expensive process and its applications seem to be concentrated in the aerospace industry. PM parts made by HIP are characterized by high density (porosity near zero), thorough interparticle bonding, and good mechanical strength. Materials And Products For Powder Metallurgy Materials The raw materials for PM processing are more expensive than for other metalworking because of the additional energy required to reduce the metal to powder form. From a chemistry standpoint, metal powders can be classified as either elemental or pre-alloyed. Elemental powders consist of a pure metal and are used in applications in which high purity is important. For example, pure iron might be used where its magnetic properties are important. The most common elemental powders are those of iron, aluminum, and copper. Elemental powders are also mixed with other metal powders to produce special alloys that are difficult to formulate using conventional processing methods. Tool steels are an example. Because the powders are pure metals, they are not as strong as pre-alloyed metals. Therefore, they deform more readily during pressing, so that density and green strength are higher than with pre-alloyed compacts. In pre-alloyed powders, each particle is an alloy composed of the desired chemical composition. Pre-alloyed powders are used for alloys that cannot be formulated by mixing elemental powders; stainless steel is an important example. The most common pre-alloyed powders are certain copper alloys, stainless steel, and high-speed steel. The commonly used elemental and pre-alloyed powdered metals, in approximate order of tonnage usage, are: (1) iron, by far the most widely used PM metal, frequently mixed with graphite to make steel parts, (2) aluminum, (3) copper and its alloys, (4) nickel, (5) stainless steel, (6) high-speed steel, and (7) other PM materials such as tungsten, molybdenum, titanium, tin, and precious metals. Products Some of the components commonly manufactured by powder metallurgy are gears, bearings, sprockets, fasteners, electrical contacts, cutting tools, and various machinery parts.