Technology of Patternmaking PDF
Document Details
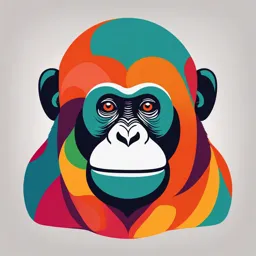
Uploaded by ImaginativePeachTree
STC/JHS
Tags
Summary
This document provides a detailed overview of patternmaking, including requirements, materials (such as wood and metals), and manufacturing techniques used in the casting process. It is suitable for students or professionals working in the field of engineering or production.
Full Transcript
## 2 Technology of Patternmaking ### 2.1 Requirement Pattern is the principal tool during the casting process. The quality of the casting produced depends largely on the material of the pattern, its design and construction. The costs of the pattern and the related equipment are reflected in the co...
## 2 Technology of Patternmaking ### 2.1 Requirement Pattern is the principal tool during the casting process. The quality of the casting produced depends largely on the material of the pattern, its design and construction. The costs of the pattern and the related equipment are reflected in the cost of the casting. The use of expensive patterns can therefore be justified where the quantity of castings required is relatively substantial. When only few castings are needed a loose pattern made from a soft variety of wood serves the purpose. Where a large number of castings are required and are to be repeatedly produced, patterns should be made in metal or epoxy resin and mounted on pattern plates for use on moulding machines. Much preparation is necessary before the patternmaker can actually start producing the pattern. The preparatory work includes decisions about (i) the type and form of material to be used, (ii) the type of pattern to suit the method of moulding to be adopted, (iii) the provision of core boxes, (iv) constructional details, including the provision of loose pieces, core prints, etc., (v) considerations as regards the value of allowances to be used, (vi) the method of gating and feeding to be followed, and (vii) the provision of various foundry aids. It is a good practice to prepare separate drawings for patterns and core boxes from the component drawing so that all details can be indicated thereon. The pattern-maker then draws a layout in full scale which becomes the basis for the production, and subsequently also for the inspection, of the pattern. The patternmaker has a very important role to play in casting production. It is he who is responsible for details of form and construction. He creates the first tangible evidence of the machine to be. He must be able to interpret the engineering drawings prepared by the designer, visualise the object in three dimensions, draw the layout of the item, and finally produce a pattern complete with gating, risers, and other auxiliary items of tooling. He has also to be conversant now with the use of computers for graphics, drawing and design. ### 2.2 Pattern Materials The selection of pattern materials depends on factors such as: * service requirements, e.g. quantity, quality and intricacy of castings, minimum thickness desired, degree of accuracy and finish required; * possibility of design changes; * type of production of castings, and type of moulding method and equipment to be used; and * possibility of repeat orders. To be suitable for use, pattern material should be: * easily worked, shaped, and joined; * light in weight for facility in handling and working; * strong, hard, and durable (i.e. of high strength-to-weight ratio); * resistant to wear and abrasion, to corrosion, and to chemical action; * dimensionally stable and unaffected by variations in temperature and humidity; * available at low cost; * such that it can be repaired or even re-used; and * having ability to take a good surface finish. The wide variety of pattern materials in use may be classified as: * wood and wood products; * metals and alloys; * plasters; * plastics and rubbers; and * waxes. ### 2.2.1 Wood and Wood Products Wood is the most commonly used material for patterns as it satisfies many of the aforementioned requirements. It can be easily shaped or worked and joined to form any complex shape, is light in weight, is easily available, and costs less than other materials. The common drawbacks, however, are its susceptibility to moisture, causing it to swell or shrink, its poor strength, and low resistance to wear. Wood, like all living matter, is composed of cells resembling long think tubes with tapered ends. The cell walls consist of cellular fibres, aligned parallel to the axis of the cells, and bonded together by a complex amorphous material called "lignin". Wood contains 50-60% cellulose and 20-35% lignin. Smaller amounts of other carbohydrates, such as pentosanes, resins, gums, and mineral matter, are also present. The cell walls are highly hygroscopic because the main constituent, cellulose, contains numerous hydroxyl groups which are strongly hydrophilic. When exposed to moisture, the cell walls absorb large amounts of moisture and swell. This characteristic of wood reduces its rigidity and causes dimensional instability. The moisture in green wood consists of water absorbed by the cell walls and water contained within the cell cavities (Fig. 2.1). As the wood dries, the water is first removed from the cell cavities until they are empty. At a point called "fibre saturation point", the cell walls are fully saturated with water although the cell cavities are empty. This point occurs at about 25-35% moisture in wood. On further air drying, moisture decreases until an equilibrium moisture content (EMC) is reached. The value of EMC depends on relative humidity and temperature. For example, for 60% relative humidity and 20°C temperature, EMC is about 11%. Variation in the moisture content of wood with atmospheric conditions results in swelling and shrinkage when the moisture content is below the fibre saturation point. The dimensional changes occur in a direction transverse to the long axis of wood, because the cell walls swell or shrink in the direction perpendicular to the fibre length. The tree trunk develops from a young sapling by a process of laying down successive concentric layers of cells outside the established wood and under the bark. The seasonal variations in temperate climate result in two stages of growth of the wood substance, one very rapid stage occurring in spring and the other a slow rate stage occurring in summer. The cells formed in spring have very thin walls and the wood has an open texture. Those formed in summer have much thicker walls, making the wood texture close and relatively strong. This growth pattern results in marked differences in the wood structure, which appear in the form of characteristic annular rings representing the boundaries between spring and summer wood. The tree trunk becomes separated in two zones; the inner one, which is stronger, harder, and more durable, is heart wood, and the outer one is sap wood (Fig. 2.2). The outermost layer on the inside of the bark is cambium, followed by sap wood rings. The wood in this sap wood region is fresh and therefore weak and prone to decay. The ray cells radially dispersed in the section are called medullary rays. These rays are noted as fine white lines and serve as reinforcement against lateral spreading of vertical fibres under the axial load and also help in storing and distributing food material. ### Seasoning of Timber To prevent excessive shrinkage or swelling, wood can be seasoned before it is finally put into service. Seasoning minimises the effect of subsequent moisture variations by adjusting the water content of wood as nearly as possible to what would be obtained at the equilibrium level under exposure to average atmospheric conditions. More precisely, wood is seasoned in order to make it: * stable in dimensions; * stronger and lighter; * resistant to decay; and * take preservative, paint, or polish. Seasoning can be done by natural or artificial methods. In natural seasoning, the wood is stacked suitably in open spaces and subjected to air drying for a period of time extending up to one full cycle of weather conditions. Another method of natural seasoning prescribes keeping the timber immersed in flowing water, so that a large part of the moisture is washed away and removed, and then air drying it for a shorter duration. In artificial seasoning, the timber is stacked in drying kilns and subjected to fast air drying by allowing hot air to pass through the kiln chamber. The air is heated, usually by steam passing through pipes. The temperature and humidity have to be precisely controlled in the kiln to prevent the timber from developing defects, such as cracks and buckling. In the beginning, hot but moist air is introduced, so that heating may take place uniformly through the whole section of wooden pieces without appreciable drying to avoid any differential contraction. Then the moisture content in the air is gradually reduced to the desired value. The kiln is equipped with suitable arrangements for air circulation, heating, humidity control and ventilation. Ordinarily, one week is sufficient to carry out seasoning. Another method of artificial seasoning, is electrical seasoning: fairly large sections of timber are exposed to a high frequency electric field such that the moisture content is brought down to the desired level within few minutes. Chemical seasoning has also been used where wood is kept immersed in suitable salt solutions and then exposed to air for drying. The following Indian standards can be referred to, for detailed guidelines on wood seasoning and methods of preservation. * IS: 401-1967 gives the code of practice for the preservation of timber and deals with various methods of preservation. * IS: 1141-1973 gives code of practice for seasoning of timber and lays down the procedure for kiln seasoning. * IS: 7315-1974 gives guidelines for design, installation and testing of timber-seasoning kilns. ### Types of Timber for Pattern Work The woods commonly used for pattern work are pine, mahogany, teak, walnut, and deodar. Pine wood, though weak, is often favoured for its extreme lightness, stability, ease of working, and ability to take good finish. It is suitable where a small number of castings, say up to 25 in number and under 500 mm in size, on any one side are required. Mahogany is a hard, strong, and very durable type of wood with negligible shrinkage or swelling after seasoning. It takes a very fine natural polish, stains well, and glues excellently. Amongst natural woods, therefore, mahogany is the best choice for pattern work. It is ideal where the number of castings required is large and involves permanent production work on moulding machines. Teak is also a hard and strong variety of wood, unaffected by fungus, and easily available in the country. Deodar is a soft variety, slightly harder than pine but easily machinable, and takes good polish. The wood products gaining more popularity for pattern work in recent times include compressed wood laminates and laminated wood impregnates. * **Compressed Wood Laminates** These laminates are available as plywoods and as laminated boards, plain or veneered. Thin wooden laminates are glued and pressed together such that the grains of alternate laminates occur in the opposite direction. These laminated forms of wood are stronger, denser, and dimensionally more stable than plain woods. These are available as sheets in different sizes in thickness varying from 12 mm to 50 mm. Metal-faced plywood is also available which has facing of mild steel, stainless steel or brass. It is made by the hot pressing technique and has superior mechanical properties, resistance to wear and abrasion, and dimensional stability. * **Laminated Wood Impregnates (Plastic Wood)** These varieties are the result of attempts to overcome the drawbacks found in woods and to improve properties such as strength, density, hardness, resistance to wear, and dimensional stability, at the same time preserving the natural advantages of woods. The wood laminate may be simply impregnated with resins so as to fill up the cell cavities, or be impregnated and compressed to increase density and hardness. WPC, i.e. wood plastic combination, is one such compressed impregnate which possesses exceptional properties and has been used as a substitute for more expensive aluminium patterns for automotive casting work. Complete polymerisation of plastic resin is necessary and is achieved sometimes by using nuclear radiations in the form of intense gamma rays. Commercially resin applied include phenol formaldehyde, methyl methacrylate, styrene, acrylonitrile, isocyanates and polyester. These varieties are also available as sheets of varying thicknesses. ### Wooden Patterns with Metallic Coatings For short production runs where metallic patterns cannot be economically employed and wooden patterns are not found satisfactory due to low strength and lack of high finish, metal-coated patterns are sometimes used. The wooden patterns are sprayed with a thin metallic coating of about 0.25 mm thickness, the metals generally used being bismuth, zinc or aluminium. The metal in the form of wire is fed into a spray gun, and is heated therein by an oxyacetylene flame. Then under pneumatic pressure it is blown in an atomised form through a nozzle over the wooden surface. For details of this process, refer to 8.1.2 (XV) on metal spraying. ### 2.2.2 Metals and Alloys Metallic patterns are used where repetitive production of castings is required in large quantities. The metals commonly used are aluminium alloys, cast iron, steel and copper base alloys such as brass or bronze. A comparative evaluation of these metals is given in Table 2.1. | Factors | Grey cast iron | Steel | Aluminium | Brass | |:-------------------------|:---------------|:-------|:------------|:----------| | Availability | Good | Good | Good | Good | | Castability | Good | Difficult| Less difficult| Good | | Machinability | Good | Good | Very Good | Very Good | | Surface finish | Good | Good | Very Good | Very Good | | Lending to modification | Good | Good | Very Good | Very Good | | Tendency to oxidation | Yes | Yes | No | No | | Weight | Very heavy | Very heavy| Very light | Heavy | | Brittleness | High | Low | Low | Low | | Cost | Low | Low | Medium | High | | Requiring machining | Yes | Less | BHN value | Not much | Grade 20 cast iron as per IS: 210-1962, which has BHN value 197-241, is the most suitable of all cast irons. High duty iron and SG iron are also now being increasingly used. Owing to its heavy weight, cast iron can be used only for small-sized patterns. The overwhelming advantages of aluminium make it the most popular choice for patterns. The alloys recommended are grade 4223, 4600 and 4420 as per IS: 617-1975. A near equivalent of grade 4420 in British standards is LM 25 WP, widely used in the UK and elsewhere due to its easy castability, low shrinkage, good strength, and high wear resistance. The best properties are achieved after solution heat treatment and precipitation heat treatment. In case of simple shapes the pattern can be prepared direct from standard rolled forms by machining. Duralumin is best suited after a stress relieving treatment. Brass and bronze are excellent materials for pattern work because of their high physical strength besides their strong resistance to deformation and corrosion, ease of production and joining, and ability to take good finish. Their main limitation is the high price. Low melting point alloys, such as white metal and cerro-alloys that contain tin and bismuth, are also used for dies, which are required for investment casting, and for moulds, which are used for making epoxy resin patterns or plaster patterns. These alloys have a low melting temperature, thus enabling easy and quick melting and immunity from the effect of chilling. Cerro-alloys containing tin and bismuth in the proportion of 60: 40 or 43: 57 have an extremely low coefficient of expansion (0.5 mm per metre); besides they are quite hard and malleable and the melting point is only about 138°C. Metal electro-deposition or electro-forming has lately found application for pattern and die work. Like electroplating, this method uses an electrically conductive shaped mandrel (master pattern or mould) along with an electrolyte, which is made up of a solution of the metal to be deposited, such as nickel, chromium, and copper. On passing current at suitable voltage, the metal from the solution moves towards the mandrel and deposits a uniform layer on it. With proper equipment, high deposition rates are possible. The shape so formed is subsequently separated from the mandrel and used as either a mould or a pattern. The method can be used for producing intricate shapes with an extreme degree of accuracy. Fine details can be reproduced with utmost fidelity and the method is adaptable to large scale production. Frozen mercury also has been used as pattern material in the "Mercast" process for producing highly intricate and accurate castings. Its use however is greatly limited due to prohibitively high cost. Metallic patterns being employed for mass production are generally required in a large number. They are therefore prepared by casting from a master pattern, which may be made in wood, plastic, plaster, or metal. Double allowances have to be made for contraction and machining on the master pattern. Metallic patterns are cast from the master pattern by sand casting. After machining and finishing wherever necessary, these patterns are mounted on pattern plates. Where patterns are of the split type, each half may be mounted on separate pattern plates or on either side of the same plate. Proper marking must be used when mounting patterns which must be carefully executed. Templates and other tooling may be used to ensure that the cope and drag parts of the moulds prepared separately from the halves will match and produce a casting without any defect. Pattern plates used for mounting patterns can be of wood or metal, though more often they are metallic. IS: 4604-1968 gives the specification for pattern plates for machine moulding boxes. Metallic pattern plates are usually made in grey cast iron (grade 20) or cast aluminium alloy (grade 4420). ### 2.2.3 Plasters Gypsum plaster (plaster of paris) when mixed with a correct quantity of water sets in a given time and forms a hard mass having high compressive strength, e.g. up to 300 kg/cm². Plasters ordinarily available expand on solidification. By choosing plaster of proper expansion rate, it is possible to completely offset the shrinkage of the casting; then no contraction need be separately provided for on the pattern. Further, by careful design and the use of hardening and reinforcing materials, such as talc and portland cement, the strength and hardness of plaster can be further enhanced. Plaster can also be conveniently used for preparing follow-boards for moulding work. Proprietary varieties of gypsum plasters, are also available. These have different setting times, expansion rates, and compressive strengths and are suited for varying requirements of pattern shops and foundries. The supplier's recommendations should be followed while selecting the plaster for a particular type of application. Gypsum plaster patterns can be prepared either by directly pouring the slurry of plaster and water into desired shape by the sweep-and-strickle method. ### 2.2.4 Plastics and Rubbers Both thermosetting and thermoplastic materials are used for pattern work. The former are used for making long-lasting and durable patterns, and the latter for short runs or piece work. In the thermosetting variety, epoxy and polyester resins have found increasing use. In the thermoplastic type, polystyrene has become very popular. Silicone rubbers have been used for making dies in special cases. #### Epoxy Resins Epoxy resin patterns have become very popular because of their * easily castable nature which renders machining superfluous, * high strength-to-weight ratio (5.4 compared to 4.0 of aluminium alloys and 1.2 of cast iron), * low cost of working, * good resistance to wear and abrasion, and * complete immunity from the action of moisture and the effect of mild heating when in contact with sand. Epoxy resin patterns (Fig. 2.3) have thus tended to replace the more expensive metallic patterns for mass production. In spite of the high price of resin which is used as raw material, the cost of these patterns works out lower than that of aluminium patterns because there is no expense on casting and machining as is incurred in metal patterns. Epoxy resin is used as a two-component material, namely a liquid binder resin and liquid hardener. When mixed together, the two liquids set and form a hard mass in a given length of time. Three types of resin combinations are commonly employed: * **Gel Coat or Surface Coat Resin** This resin, mixed with the appropriate quantity of hardener (as prescribed by the resin manufacturers), is used to obtain the surface layer on the pattern, which is required to be harder and stronger than the inner layers. For forming the pattern, the mould (prepared earlier from a master pattern in metal, plaster, or epoxy resin itself) is first given a thin coat of release agent and then two or three layers of the gel coat mix. * **Laminating Resin** This resin, mixed with its respective hardener, is used to apply a few layers of glass wool laminations on the back of the gel coat. Glass wool or glass fibre is soaked in the resin mixture and then applied all over the gel coat layer. This treatment imparts additional strength, toughness, and flexibility to the pattern. * **Casting Resin** This resin, mixed with its respective hardener, is used to provide the necessary backing and to form the complete solid shape by filling up the void. To increase the strength, rigidity, and hardness of the pattern and at the same time reduce its cost, suitable fillers, such as talc, chalk powder, slate powder and fine sand, may be added to the casting resin. For large patterns, suitable reinforcements and solid inserts roughly shaped to internal cavity may also be provided. Depending on the service requirements of the pattern, all the three types of resin combinations may be used or lamination may be dispensed with and casting resin poured directly over the gel coat. For quick jobs, which do not require a very hard surface layer, casting resin may also be directly poured over the master pattern. Complete setting of the resins takes place in about 24 hours after which the master pattern may be stripped off and the pattern so obtained used as either a loose pattern or a match-plate pattern (mounted on the pattern plate). Hot setting resins which set within a much shorter time are also available, but they have greater shrinkage and are therefore unsuitable for pattern work. The manufacturers' instructions should be followed as regards resin selection, hardener proportions, etc. To economise on the resin requirement, coring, ribbing, etc. can be used on the patterns. Methods used for making epoxy patterns are shown in Fig. 2.4. #### Polyester Resins As a cheaper substitute for epoxy resins, fibre reinforced polyester resins (FRP) are also being increasingly used. The cost of polyester resins is less than half that of epoxy resins, and yet, the patterns produced are rigid, strong and durable. The setting time in case of FRP patterns is only about four hours and production rates can be much faster. Several brands and varieties of polyester resins are available. The one chosen for pattern work should possess: * ability to be cured at room temperature * low shrinkage characteristics * ability to produce hard, wear-resistant surfaces with high finish Though polyester resins shrink more than epoxy resins, shrinkage can be taken care of by proper pattern design. The FRP patterns can easily be made hollow, i.e. the necessity for using a casting resin is not felt. One or two gel coat layers, followed by glass fibre laminations in two or three layers can build sufficient rigidity, and no further backing is required. The stripping of the pattern is also easy. The polyester resin is used in three parts, a resin binder, an accelerator and a catalyst. For correct selection of resin variety and proportion of the three parts, the manufacturers' instructions should be followed. #### Polystyrene Of the thermoplastic variety of plastics which tend to become soft and subsequently gasify on heating, the most common is polystyrene foam often called EPS. This material is available in different densities in foamed (expanded) form. It can be easily shaped, machined, and fabricated by gluing to form the pattern. The pattern can be used in the conventional form of sand casting where it has to be removed from the mould by withdrawing it, if possible, or else by burning it with a gas torch or breaking it. Another way of using this pattern is as a full mould casting where the pattern is embedded in sand and, without removing it from the mould, the molten metal is poured. The heat of the molten metal causes gasification of the pattern. The ash content of the pattern material is extremely low and the gas developed during burning is easily able to permeate through the sand. Polystyrene patterns are also used in investment casting. The details of the moulding process known as full mould casting are given in Section 3.6.3(2). IS: 10094-1981 gives the specification of expanded polystyrene for pattern making. Polyurethane foam too has been used like polystyrene but to a much smaller extent. Urethane elastomers (referred to as flexanes) are applied on a limited scale for forming dies for investment casting in the same way as epoxy resins. This material has low thermal conductivity, high strength, and no shrinkage. Certain types of rubbers, such as silicon rubber, are favoured for forming intricate types of dies for investment casting. This material, like epoxy resin, is available in two parts, binder and hardener. When the two parts, originally in liquid form, are mixed together, poured over a master pattern or into a die, and cured, a solid shape is produced. ### 2.2.5 Waxes Wax patterns are excellent for the investment casting process. The materials generally used are blends of several types of waxes and other additives, which act as polymerising agents and stabilisers. The waxes commonly chosen are paraffin wax, carnauba wax, shellac wax, bees wax, cerasin wax, and microcrystalline wax. The properties desired in a good wax pattern include low ash content (up to 0.05%), resistance to the primary coat material used for investment, high tensile strength and hardness, good wettability, resistance to oxidation, low shrinkage, and substantial weld strength. The blending or compounding of waxes and other additives is so done that most of the desired properties can be achieved. The actual ingredients and composition to be used have generally to be determined by trial and experimentation. The normal practice of forming wax patterns is to inject liquid or semiliquid wax into a split die. Solid injection also is used to avoid shrinkage and for better strength, however, much higher injection pressures are required for solid injection. If wax is poured into the die in a liquid state under gravity, it will shrink much more and the size of the pattern will be affected. After injection, the die is cooled, opened and the wax pattern extracted. As the patterns are generally small in size, a number of patterns are welded (two ends to be joined by a hot spatula are heated and pressed lightly together) to a common runner or sprue through in-gates. The whole assembly of patterns complete with runner, sprue, etc., which is often termed a "tree", is then invested to prepare the investment mould. Details of investment casting process are given in Section 3.6.3(1). Casting waxes used for investment casting can be classified into following categories: * **Pattern wax:** (a) Straight or unfilled wax * **Runner wax:** (b) Emulsified pattern wax (c) Filled pattern wax * **Reclaimed or reconstituted wax** * **Water soluble wax** * **Special waxes**, such as dipping, patching and adhesive waxes. Straight wax is a complex compound made up of several waxes and resin components. Its surface finish is bright. It can be reclaimed after use from the investment mould for use on runner systems as also on patterns. Emulsified waxes are those varieties which are emulsified with water in the proportion of 7 to 12%. The water acts partially as a filler and hence very little cavitation takes place keeping the surface finish smooth. It is a versatile variety giving good strength and flowability and can be reclaimed and reused. Filled pattern waxes are similar to straight waxes but they are blended with powdered and inert material which is insoluble in base wax in order to give the material greater stability, less cavitation, better hardness and strength and high pourability and flowability. Runner wax is produced specifically for preparing runner systems by blending with various waxes and filler materials which can impart high strength which the runner systems demand. Reclaimed waxes are those which are obtained on heating the investment moulds. These are used again for preparing patterns and runner systems. Water soluble waxes are used for producing internal shapes which are difficult or impossible to obtain by other means. These are soluble in water or in mild acidic solutions. Special waxes are unfilled wax compounds used for dipping, patching and adhesive applications. ### Desirable Properties of Investment Wax * Low contraction rate and low cavitation or blow holes * Low ash content, preferably, less than 0.02% * Low viscosity and high flowability * Fast setting rate * Low congealing point or melting point * High strength and hardness in cold state * Good hardness * Good surface finish * Resistant to oxidation and high stability * Easy reclaimability ### 2.2.6 Old Castings Old castings are sometimes used as patterns during an emergency when time is short. In order to increase the thickness and other dimensions to provide for contraction, machining, and other allowances, surfaces are lagged with thin strips of wood or leather. Metal coating by metal spraying may also be provided to build up the required size. The castings to be used as patterns have to be well cleaned and smoothened so that there are no undercuts and they can be easily withdrawn from the mould. Core prints, if necessary, may have to be provided on the casting. ## 2.3 MACHINES AND TOOLS FOR PATTERNMAKING ### 2.3.1 Machines for Wood Patternmaking Most of the machines used for the patternmaking are the same as those for other jobs in woodworking. However, some of the operations otherwise done by a group of machines for instance, boring, milling, slotting, shaping, grooving, and cutting special profiles such as gear teeth are more efficiently performed on a special purpose machine called the "pattern miller". The size and the capacity of the machines used depend on the size of the general run of work to be performed. The machines chosen for the pattern shop should not only be sturdily built and of sizeable proportions so that they can cope with a variety of jobs, but should also have dependable accuracy. The ones favoured for patternmaking are: * woodworking lathe; * circular saw; * band saw; * jig saw or scroll saw; * jointer; * planer; * shaper; * pattern milling machine; * disc and bobbin sander, and * machines for tool grinding. #### (1) Woodworking Lathe The woodworking lathe is one of the most important machines to the patternmaker since patterns and core boxes often involve some sort of cylindrical work. It is designed chiefly for turning jobs, both external and internal. However, by suitably manipulating the tool, tapers, and radii, other irregular shapes can also be easily turned. The woodworking lathe (Fig. 2.5) consists of four major parts: the head stock, which has a spur or live centre fitted in a hollow spindle; the tail stock, carrying a dead centre; a tool rest, which is stationary and adjustable; and a bed to which are fastened the other three parts. Pattern shops are equipped with a special type of woodworking lathe, known as the patternmaker's lathe. This lathe is a modified version of the woodworking lathe and in many respects resembles the centre lathe used for metal working operations. The design of its various parts makes it more robust and sturdy and therefore more dependable than the woodworking lathe. First, the patternmaker's lathe has a backgearing arrangement by means of which the available number of spindle speeds is doubled. Secondly, it is equipped with a feed shaft and a sliding carriage in place of the fixed type tool rest. On the carriage is fitted a cross slide, a compound slide, and a tool post. Thus, in this lathe, the tool traverse, both parallel to the work axis as well as across it, can be precisely regulated for better size control. The size of woodworking lathes is usually specified in terms of the "swing" or height-of-centre of the lathe and the maximum distance between the centres. The height-of-centre is taken as the distance from the lathe centre to the upper surface of the bed, and swing is double that of the height-of-centre. Generally, the woodworking lathe is supplied together with a number of accessories, which considerably increase its usefulness and adaptability. Some of the typical accessories include different types of centres, such as drive centre, cup centre, and screw centre, a face plate, a 4-jaw independent chuck, a 3-jaw self-centring chuck, a tool holder, and a set of wood turning tools. The types of tools commonly used on these lathes are illustrated in Fig. 2.6. The material of these tools is high carbon steel containing about 0.8-1.0% carbon. #### (2) Circular Saw The circular saw is also an essential machine in the pattern shop. It can be used for all cutting operations, such as ripping, cross-cutting, beveling, rabbeting, grooving, and mitering. The principal parts of the circular saw are: a cast iron table upon which the work is supported and from where it is fed into the saw: a circular saw blade supported in bearing on the under side of the table and rotating at high speed; a driving arrangement for the saw blade, consisting of an electric motor and a set of pulleys mounted on shafts; a cut-off guide, which is used during cross-cutting to steer the piece towards the saw blade; and a ripping fence, which acts as a guide while sawing along the grains of wood. The circular saw usually has provision for tilting the table, thus enabling cutting at an angle as required during mitering, beveling, etc. The tilting can be done up to an angle of 45°. The size of the circular saw is specified by the diameter of the saw blade. A 300 mm saw is commonly used for small and medium-sized work. The cutting speeds for sawing vary from 1000 metres to 3000 metres per minute according to the hardness of the wood. #### (3) Band Saw The band saw makes use of an endless metal saw band, which travels over the rim of two rotating pulleys. Although the number of operations that can be performed on a band saw is less than those on a circular saw, it is favoured for curved or irregular cuts in wood. The main parts of a band saw are: * A set of cast iron pulleys or wheels carrying the saw band on their periphery: Of the two wheels, one is adjustable and the other is fixed so that the centre-to-centre distance can be slightly varied to maintain proper tension of the band. * A cast iron table on which the workpiece is placed and from where it is fed into the saw band for cutting; the table, which can be tilted as in the case of the circular saw, carries a slot in the centre through which the band passes. * A roller guide, fixed to an adjustable arm, which helps in keeping the saw band in position while cutting. * A heavy cast iron frame or body to which all the other parts are fitted. * A driving arrangement, consisting of an electric motor and a set of pulleys, to transmit power to the driving wheel. * A ripping fence as in the circular saw. The band saw is available in two models, horizontal and vertical. In the former, the two wheels are arranged alongside each other and the table is underneath. In the latter model, the more popular of the two, the wheels are arranged one above the other and the band thus has to pass through the table, which is mounted in a central position between the two wheels. The size of the band saw is specified as the distance from the saw band to the inner side of the frame. This distance is roughly equal to the diameter of the wheels. The width of the saw band varies from 6 mm to 50 mm and is dependent on the size of the machine. Narrow bands are usually employed on small machines where cutting is to be done along a small radius. #### (4) Jig Saw or Scroll Saw The jig saw, which is also known as a scroll saw, is ideal for cutting small-size work to an intricate profile. It is actually a diminutive type of band saw and specially adapted to irregular work. The table of the jig saw too can be tilted for angular work. The special characteristic of this saw is its ability to cut inside curves as well. This is done by first threading the blade through a previously bored hole and then working along the desired layout. This internal sawing facility is not available in any other traditional woodworking machine and is invaluable in patternmaking, such as for preparing strickle boards and core boxes. The width of the jig saw blades varies from 1.5 mm to 9 mm. #### (5) Jointer The wood jointer is designed for planing the straight edges and surfaces of boards. Its use, therefore, eliminates the labour involved in hand planing. The jointer (Fig. 2.7) consists of a revolving cutter head to which three or more cutter knives are fitted; a table on which the board to be planed is kept pressed and fed by hand against the revolving cutter head; and an adjustable fence for guiding the board at a predetermined angle to the surface of the table. By means of the adjustment provided, the fence may be kept either at 90° to the table or inclined at any other angle for angular and bevel cuts. For regulating the depth of the cut, the cutter head can be raised or lowered by moving a handwheel. #### (6) Planer The purpose of a wood planer is similar to that of a jointer, but it is designed primarily for planing large and heavy stock at a comparatively faster rate and involving a lesser amount of manual labour (Fig. 2.8). The boards to be planed are fed into the machine by means of feed rolls along a table against a revolving cutter head, thus eliminating the labour of hand feeding. The cutter head is mounted on an overhead shaft which is adjustable for regulating the depth of the cut (Fig. 2.9). The table of the planer is generally much wider and longer than that of a jointer and more accommodating for large plants. The planer is also usually equipped to automatically surface the wood to desired thicknesses. #### (7) Shaper The machine consists of a cutter head, carrying a cutter and rotating about a vertical axis, and a horizontal table similar to that of a jointer. The wood is fed by hand along the table against the cutter and guided by an adjustable fence, Fig. 2.10(A). The shape of the cut on the surface of the wood is the same as that of the profile of the teeth on the cutter. By suitably designing the cutter, a variety of shapes can be produced. The types of cut that can be taken by a shaper