Module 1 - Sensors PDF
Document Details
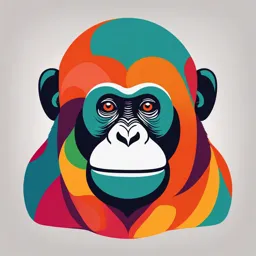
Uploaded by HandyAestheticism
Tags
Summary
This document covers the fundamentals of sensors, including active and passive sensors, and specific examples such as thermocouples and RTDs. It also outlines their applications in mechatronics systems and the use of Wheatstone bridge circuits.
Full Transcript
Module 1 – Sensors LEARNING OBJECTIVES After successful completion of this module, you should be able to: Understand the fundamentals of sensors such as: proximity sensors and switches, potentiometers, linear variable differential transformers, optical encoders, strain...
Module 1 – Sensors LEARNING OBJECTIVES After successful completion of this module, you should be able to: Understand the fundamentals of sensors such as: proximity sensors and switches, potentiometers, linear variable differential transformers, optical encoders, strain gages, load cells, thermocouples, and accelerometers; Discuss the role of sensors in mechatronics system; Apply concept of wheatstone bridge to obtain output signal from several types of sensors. SENSORS A sensor is an element in a mechatronic or measurement system that detects the magnitude of a physical parameter and changes it into a signal that can be processed by the system. Often the active element of a sensor is referred to as a transducer. Monitoring and control systems require sensors to measure physical quantities such as position, distance, force, strain, temperature, vibration, and acceleration. A transducer is a device that converts energy from one form to another. Transducers that convert physical quantities into mechanical ones are called mechanical transducers; Transducers that convert physical quantities into electrical are called electrical transducers. Examples are a thermocouple that changes temperature differences into a small voltage, or a Linear variable differential transformer (LVDT) used to measure displacement. Active vs Passive Sensors 1. Active sensors - require an external power source to operate, which is called an excitation signal. The signal is modulated by the sensor to produce an output signal. Example: Photoelectric sensors 2. Passive sensors - in contrast, generate an electric current in response to an external stimulus which serves as the output signal without the need of an additional energy source. Examples: piezoelectric sensor and thermocouple. Temperature Sensors The classical thermometer is clearly a sensor, but in its common configuration it does not provide an output signal. Its output is read directly and can’t be inputted to a controller for further use. Several temperature sensors in which the output can be used for further processing are outlined below. Thermocouple When the temperature changes at the junction formed by joining two unlike conductors, its electron configuration changes due to the resulting heat transfer. This electron reconfiguration produces a voltage (emf or electromotive force), and is known as the Seebeck effect. Two junctions (or more) of a thermocouple are made with two unlike conductors such as iron and constant an, copper and constantan, chrome and alumel, and so on. Because an electrical circuit must form a closed loop, thermoelectric junctions occur in pairs, resulting in what is called a thermocouple. We can represent a thermoelectric circuit containing two junctions as illustrated in the figure 3. An actual picture is also shown in figure 4. Figure 3. The thermoelectric circuit Figure 4. A thrermocouple The following are the percentage combination of materials used for chromel and alumel: CHROMEL – 90% nickel & 10% chromuim ALUMEL – 94% nickel, 3% manganese, 2% aliminum & 1% silicon The table below shows the different types and application of thermocouple. Resistance Temperature Detectors(RTDs) A resistance temperature device (RTD) is constructed of metallic wire wound around a ceramic or glass core and hermetically sealed. The resistance of the metallic wire increases with temperature. Figure 5. Inside a resistance temperature detector Source:electrical4u.com The resistance of metal wires changes with temperature. Then the resistance change can be converted to a proportional voltage using a Wheatstone bridge circuit. A good approximation to the resistance and temperature relationship for most RTD materials is Where 𝛼 is the temperature coefficient of resistivity. T is temperature and Rt is the resistance, Ro is the reference resistance, and To is a reference temperature. Platinum, nickel and copper wires are used in RTD devices. Typical values of 𝛼 for three materials are: The following figures shows how the two wire and three wire RDTs are connected. RTDs are usually connected with a wheatstone bridge circuit, same with several types of sensors. Further discussion with the wheatsone bridge circuit will follow. Figure 6. Two wire RTD bridge Figure 7. Three wire RTD bridge Wheatstone Bridge Circuit The most common and simplest bridge network to find the resistance is the DC Wheatstone Bridge. This bridge is used where small changes in resistance such as sensors are to be measured. This is used to convert a resistance change to a voltage change. A wheatstone bridge circuit is shown below. Example 1. In the circuit shown compute the output voltage. Example 2. In the circuit shown compute the output voltage. Thermistors A thermistor is a semiconductor device, available in probes of different shapes and sizes, whose resistance changes exponentially with temperature. Thermistors have much narrower operating ranges than RTDs. The figure below shows example of thermistors. Figure 9. Thermistors A wheatstone bridge circuit is also used to connect thermistors and other applicable sensors to produce output in terms of voltage. p-n JUNCTION TEMPERATURE SENSORS When a p-n junction is forward biased, the current through the diode is temperature dependent. This current can be measured and used to indicate temperature. Alternatively, the voltage across the diode can be measured (almost always a preferable approach) and its dependence on temperature used as the sensor’s output. This type of sensor is called a p-n junction temperature sensor or bandgap temperature sensor. The LM35 series are precision integrated-circuit p-n junction temperature sensors, whose output voltage is linearly proportional to the Celsius (Centigrade) temperature. There are three pins consisting of Vcc(positive supply), Ground and the analog output pin. Figure 10. The LM35 temperature sensor Some features: Calibrated directly in degrees centigrade Linear + 10.0 mV/˚C scale factor Operates from 4 to 30 volts Bimetallic Strip A thermistor is a semiconductor device, available in probes of different shapes and sizes, whose resistance changes exponentially with temperature. Thermistors have much narrower operating ranges It is composed of two or more metal layers having different coefficients of thermal expansion. The strip can be straight, as shown in the figure, or coiled for a more compact design. Because these layers are permanently bonded together, the structure will deform when the temperature changes. This is due to the difference in the thermal expansions of the two metal layers. The deflection can be related to the temperature of the strip. Bimetallic strips are used in household and industrial thermostats where the mechanical motion of the strip makes or breaks an electrical contact to turn a heating or cooling system on or off. Figure 11: Effect of temperature rise in bimetallic strip Figure 12. Thermostats(with bimetallic strip inside) Optical Sensors Optical sensors are those sensors that detect electromagnetic radiation in what is generally understood as the broad optical range—from far Infrared to Ultraviolet. The sensing methods may rely on direct methods of transduction from light to electrical quantities such as in photovoltaic sensors or indirect methods such as conversion first into temperature variation and then into electrical quantities. Light Dependent Resistor (LDR) LDR is one of the widely used photo sensors. They are cheap and rugged in nature. They are basically resistors whose resistance depends on the intensity of light. Their resistance variation is continuous and inversely proportional to the intensity of light. Figure 13. The Light dependent resistor One simple use of a Light Dependent Resistor is as a light sensitive switch as shown below. When light is detected by the LDR, its resistance changes causing the transistor to trigger that activates the relay. Figure 14. Schematic diagram of a light sensitive switch Photo-diode The construction of the Photodiode light sensor is similar to that of a conventional PN- junction diode except that the diodes outer casing is either transparent or has a clear lens to focus the light onto the PN junction for increased sensitivity. The junction will respond to light particularly longer wavelengths such as red and infra-red rather than visible light. Figure 15. The Photo-diode Photo-transistor A phototransistor is a light-sensitive transistor. A common type of phototransistor, called a photobipolar transistor, is in essence a bipolar transistor encased in a transparent case so that light can reach the base–collector junction. Figure 17. The PNP and NPN phototransistor OPTICAL ENCODER A digital optical encoder is a device that converts motion into a sequence of digital pulses. By counting a single bit or decoding a set of bits, the pulses can be converted to relative or absolute position measurements. Encoders have both linear and rotary configurations, but the most common type is rotary. Rotary encoders are manufactured in two basic forms: the absolute encoder where a unique digital word corresponds to each rotational position of the shaft, and the incremental encoder, which produces digital pulses as the shaft rotates, allowing measurement of relative displacement of the shaft. Figure 18. Components of an optical encoder Photoelectric Sensors A photoelectric sensor emits a light beam (visible or infrared) from its light-emitting element. A reflective type photoelectric sensor is used to detect the light beam reflected from the target. A thrubeam type sensor is used to measure the change in light quantity caused by the target crossing the optical axis. In retroreflective type, the light from the emitting element hits the reflector and returns to the light receiving element. When a target is present, the light is interrupted. (a) (b) ( c) Figure 19. Types of photoelectric sensors configuration:(a) reflective, (b) thrubeam, (c) retroreflective Source: https://www.keyence.com/ss/products/sensor/sensorbasics/photoelectric/info/ Electric and Magnetic Sensors Proximity Sensor A proximity sensor is a non-contact sensor that detects the presence of an object (often referred to as the “target”) when the target enters the sensor's field. Magnetic, electrical capacitance, inductance, and eddy current methods are particularly suited to the design of a proximity sensor. Types of proximity sensors: Inductive Sensors - Detection of metallic objects Capacitive Sensors - Detection of metallic and non-metallic objects (Liquids, plastics, woods) Photoelectric Sensors - Use light sensitive elements to detect objects Magnetic Sensors - Detects the presence of permanent magnets REED SWITCH Reed Switches consist of two flat ferromagnetic reeds sealed in an inert atmosphere within a glass capsule. In the presence of a magnetic field the reeds are attracted to each other and close to complete the magnetic and electric circuit. Figure 20. How reed switch works Https://www.deeterelectronics.com/reed-switch-how-it-works/ MAGNETO RESISTOR When current-carrying material is placed in the absence of any magnetic force, the free electrons move in orderly fashion. As soon as it is subjected to magnetic force, the free electrons get excited and start moving in an indirect motion creating collision among them. Thus, the resistance of magneto resistor increases with increase in magnetic field strength. Figure 21. Working principle of magneto resistor Source: CircuitsToday.com Linear Variable Differential Transformer/Transducer The linear variable differential transformer (LVDT) is a transducer for measuring linear displacement. It consists of primary and secondary windings and a movable iron core. It functions much like a transformer, where voltages are induced in the secondary coil in response to excitation in the primary coil. The LVDT must be excited by an AC signal to induce an AC response in the secondary. The core position can be determined by measuring the secondary response. Figure 22. Output voltage of LVDT in different positions HALL EFFECT SENSOR Hall Effect Sensors are devices which are activated by an external magnetic field. The output signal from a Hall effect sensor is the function of magnetic field density around the device. When the magnetic flux density around the sensor exceeds a certain pre-set threshold, the sensor detects it and generates an output voltage called the Hall Voltage. Figure 23. Hall effect sensor principle Source: https://www.electronics-tutorials.ws Mechanical Sensors MECHANICAL SWITCH The simplest kind of displacement sensor is a mechanical switch which returns one bit of information: touching or not touching. A typical Microswitch consists of a lever which, when depressed, creates a mechanical contact within the switch, which closes an electrical connection. Figure 24. The microswitch STRAIN GAUGE The most common transducer for experimentally measuring strain in a mechanical component is the bonded metal foil strain gage illustrated in the figure. It consists of a thin foil of metal, usually constantan, deposited as a grid pattern onto a thin plastic backing material, usually polyimide. The foil pattern is terminated at both ends with Large metallic pads that allow leadwires to be easily attached with solder. The entire gage is usually very small, typically 5 to 15 mm long. Figure 25. Metal foil strain gauge construction The wheatstone bridge circuit connection is also used to obtain voltage output from the sensor. A sample diagram is shown below. Figure 26. The circuit connection using strain gauges Types of strain gage assembly: 1. uniaxial 2. biaxial 3. strain gage rosette Figure. Uniaxial stress measurement Figure. Biaxial strees measurement Figure 27. Strain gauge rosette arrangement Accelerometers Accelerometers are devices that measure acceleration, which is the rate of change of the velocity of an object. Piezoelectric Accelerometer Some materials (such as natural quartz crystal, silicon dioxide, barrium titanite, lead zirconate titanate (PZT)), called piezo crystals, produce a charge in response to a force (or deformation) applied to them. Figure 28. Piezoelectric acceleration sensor Inertial Accelerometer An inertial accelerometer is basically a small mass-spring-damper system with high natural frequency. Consider the figure shown in the figure below, which is the concept of an inertial accelerometer connected to a body whose acceleration is to be measured. As the object moves, the mass inside accelerometer vibrates. Faster speed results to higher vibration or frequency. Figure 29. Operating principle of an inertial accelerometer Magnetic Accelerometers A simple magnetic accelerometer can be built by using a permanent magnet as a mass on a spring or cantilever beam and sense the field of the permanent magnet using a Hall element or a magnetoresistive sensor as shown below. Figure 30. An accelerometer in which the position of the mass is sensed by a Hall element. Load Cell A load cell is a sensor or a transducer that converts a load or force acting on it into an electronic signal. This electronic signal can be a voltage change, current change or frequency change depending on the type of load cell and circuitry used. How load cells are attached and electrically connected are shown below. Figure 31. Load cell working principle Source: https://instrumentationtools.com Figure 32. How load cells can be connected to obtain output voltage. Potentiometer MEMS Micro-electromechanical systems(MEMS) is a process technology used to create tiny integrated devices or systems that combine mechanical and electrical components. They are fabricated using integrated circuit (IC) batch processing techniques and can range in size from a few micrometers to millimetres. MEMS have the ability to sense, control and actuate on the micro scale, and generate effects on the macro scale. In the most general form, MEMS consist of mechanical microstructures, microsensors, microactuators and microelectronics, all integrated onto the same silicon chip as show in the figure below. Figure 35. Block diagram of MEMS https://www.lboro.ac.uk MEMS technology can be incorporated into a wide variety of electronic components that can be used in mobile phones, car sensor systems and other applications. SELF ASSESSMENT 1. Which of the following statements is correct? A. Sensors and transducers are both examples of actuators. B. Actuators and transducers are both examples of sensors. C. Sensors and actuators are both examples of transducers. 2. What term describes the maximum expected error associated with a measurement or a sensor? A. Range B. Accuracy C. Precision D. Resolution 3. Which of the following forms of temperature sensor produces a large change in its resistance with temperature, but is very non-linear? A. A pn junction sensor. C. A thermistor. B. A platinum resistance thermometer. 4. One of the most widely used forms of light sensor is the photodiode. Which of the following statements is correct? A. A photodiode can be used as either a photoconductive or a photovoltaic sensor. B. A photodiode is an example of a photovoltaic sensor. C. A photodiode is an example of a photoconductive sensor. 5. The image below shows a strain. With the device oriented as shown, what is the direction of sensitivity of the device? A. Horizontal B. Vertical 6. What form of displacement sensors are shown here? A. Potentiometers. B. Inductive proximity sensors. C. Opto-switches. D. Absolute position encoders. 7. What form of displacement sensors are shown here? A. A reflective opto-switch. B. A slotted opto-switch. C. An absolute position encoder. D. An incremental position encoder. 8. All mechanical switches suffer from switch bounce. A. True B. False 9. A tactile sensor is also known as a ________ sensor. A. Temperature B. Humidity C. Pressure D. Touch 10. Select the type of temperature sensor that you are most likely to find in an Integrated Circuit. A. Thermistor B. Semiconductor based sensor C. Resistance Thermometer D. Thermocouple