Mechanic A Reviewer 1 PDF
Document Details
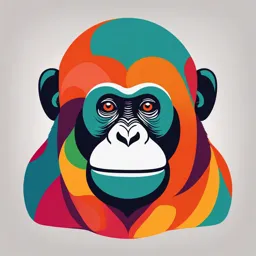
Uploaded by SolicitousPyrope
null
Tags
Related
- Aircraft Control Surface Rebalancing Procedures PDF
- FAA Aviation Maintenance Technician Handbook PDF Chapter 15 Ice & Rain Protection
- Aviation Australia CASA B-06b Aircraft Hardware PDF
- ET-PP04 Aircraft Engine Inspection, Maintenance, Operation, and Troubleshooting PDF
- Aircraft Mechanic Reviewer Philippines PDF
- A320 Technical Questions (910) - PDF
Summary
This document reviews regulations for aviation maintenance technicians in the Philippines. It covers topics such as license reinstatement, eligibility requirements, and airworthiness standards. It includes specific rules and processes related to aviation maintenance procedures and licenses.
Full Transcript
MECHANIC A REVIEWER I. REGULATORY KNOWLEDGE A. CAAP - CIVIL AVIATION REGULATION PART 2: PERSONNEL LICENSING Aviation maintenance technician license (AMT) (1) Airframe (2) Powerplant (3) Airframe and Powerplant REINSTATEMENT OF PRIVILEGES OF EXPIRED AMT/AMS LICENSES AND RATINGS (a) No person who hold...
MECHANIC A REVIEWER I. REGULATORY KNOWLEDGE A. CAAP - CIVIL AVIATION REGULATION PART 2: PERSONNEL LICENSING Aviation maintenance technician license (AMT) (1) Airframe (2) Powerplant (3) Airframe and Powerplant REINSTATEMENT OF PRIVILEGES OF EXPIRED AMT/AMS LICENSES AND RATINGS (a) No person who holds an expired AMT/AMS license or rating shall exercise the privileges of said license or rating; (b) Aviation Maintenance Technicians or Specialists who seek reinstatement of their licenses that had already expired shall comply with the following conditions: (1) Within twenty four (24) months from expiration of license, he/she shall pass the Civil Aviation Regulations test given by the Authority. (2) After twenty four (24) months from expiration of license, he/she shall pass the Civil Aviation Regulations test and must undergo the appropriate recurrent training from an Approved Maintenance Organization (AMO) or any school or facility accredited by the Authority for such purpose. (3) After sixty (60) months from expiration of license, he/she shall comply with the requirements for the application for the initial application for AMT/AMS License. (a) The following conditions qualifies for a reissue or reinstatement of the license, rating, authority or certificate: (1) expired licenses; (2) surrendered licenses; (3) suspended licenses; (4) revoked licenses; (5) exchange of licenses to lower grade or different rating; (6) and other similar conditions; Note: A license that has been suspended or revoked may be reissued or reinstated subject to the Director General’s approval. (b) Any person who holds a Philippine license, ratings authorization or certificate that has been surrendered, expired, or other similar conditions may apply for a reissue or reinstatement of such license for use provided he/she successfully complies with the requirements of the license; Note: A license that has been surrendered or has expired shall be considered as an “expired license” (c) A person who holds an expired Philippine license, ratings authorization or certificate for LESS THAN thirty six (36) months must pass the knowledge test on the Air Law to be administered by the Authority prior to the re-issue of the said license; (d) A person who holds expired Philippine license, ratings, authorization or certificate for MORE THAN thirty six (36) months must undergo the same process as the initial or original license application, including passing the Air Law, ALL the theoretical or knowledge test of the license in question and skill test and oral test requirements to be administered by the Authority prior to the re-issue of the said license; 2.6.2 AVIATION MAINTENANCE TECHNICIAN (AMT) ELIGIBILITY REQUIREMENTS: GENERAL (a) An applicant for an AMT license and any associated rating shall (1) Be at least 18 years of age; (2) Demonstrate the ability to read, write, speak, and understand the English language by reading and explaining appropriate maintenance publications and by writing defect and repair statements; (3) Comply with the knowledge, experience, and competency requirements prescribed for the license and rating sought; and (4) Pass all of the prescribed tests for the license and rating sought, within a period of 24 months. (b) A licensed AMT who applies for an additional rating must meet the requirements of (1) Subpart 2.6.2.6 and, within a period of 24 months, pass the tests prescribed by (2) Subparts 2.6.2.5 and 2.6.2.7 for the additional rating sought. KNOWLEDGE REQUIREMENTS (1) Air law and airworthiness requirements (2) Natural science and aircraft general knowledge (3) Aircraft engineering (4) Aircraft maintenance (5) Human performance SKILL REQUIREMENTS Each applicant for an AMT license or rating must pass an oral and a skill test on the license or rating he seeks. The tests cover the applicant's basic skill in performing practical projects on the subjects covered by the written test for the license or rating and shall contain at least the subjects in the IS 2.6.2.6, appropriate to the license or rating sought. EXPERIENCE REQUIREMENTS (a)Practical experience only: (1) Airframe rating - 30 months or 2 years and 6 months; (2) Powerplant rating - 30 months or 2 years and 6 months; (3) Airframe and Powerplant ratings - 60 months or 5 years (b)Approved Training. (1) Airframe rating - 24 months or 2 years; (2) Powerplant rating - 24 months or 2 years; (3) Airframe and Powerplant ratings - 30 months or 2 years and 6 months; DURATION OF THE LICENSE (a) The duration of the AMT license is (5) years. (b) The holder of a license with an expiration date may not, after that date, exercise the privileges of that license. (c) The license shall remain valid as long as the holder thereof maintains his/her competency. REQUIREMENTS FOR THE RENEWAL OF LICENSES (a) A holder of an aircraft mechanic license desiring to renew his license must accomplish and submit the following within 30 days prior to the expiry of his license: (1) Application for the renewal of license duly notarized; (2) Certification or proof that the holder has rendered services in accordance with the provisions this Part from an AMO, AOC or an ATO, or any other person found acceptable in writing by the Authority, as applicable, in any case fully in compliance with this regulations. B. CAAP - CIVIL AVIATION REGULATION PART 5: AIRWORTHINESS CAR Part 5 presents regulatory requirements for the airworthiness of aircraft expected to operate in the Republic of the Philippines using the standards and recommended practices in ICAO Annexes 6 and 8. CAR Part 5 requires all persons operating Republic of the Philippines registered aircraft to notify the Authority when certain events occur. The Authority is required to open lines of communication with the State of Design and/or the State of Manufacture so that the Authority can receive all safety bulletins and airworthiness directives for each type of aircraft operating in the Republic of the Philippines. Maintenance requirements are set forth in Part 5 for persons who are neither employees of an Approved Maintenance Organization (AMO). (1)Continuing Airworthiness. The set of processes by which an aircraft, engine, propeller or part complies with the applicable airworthiness requirements and remains in a condition for safe operation throughout its operating life. (2) Major modification. Major modification means an alteration not listed in the aircraft, aircraft engine, or propeller specifications – (1) that might appreciably affect weight, balance, structural strength, performance, power-plant, operations, flight characteristics, or other qualities affecting airworthiness; or (2) that is not done according to accepted practices or cannot be done by elementary operations. Described in IS: 5.1.1.2(a)(1). (3) Maintenance release. A certification confirming that the maintenance work to which it relates has been complied with in accordance with the applicable standards of airworthiness, using approved data. (4) Major repair. Major repair means a repair: (1) that if improperly done might appreciably affect weight, balance, structural strength, performance, power-plant, operations, flight characteristics, or other qualities affecting airworthiness; or (2) that is not done according to accepted practices or cannot be done by elementary operations. Described in IS: 5.1.1.2(a)(3). (5) Modification. The alteration of an aircraft/aeronautical product in conformity with an approved standard. (6) Preventative maintenance. Simple or minor preservation operations and the replacement of small standard parts, not involving complex assembly operations, described in IS: 5.1.1.2(a)(5). (7) Overhaul. The restoration of an aircraft/aeronautical product using methods, techniques, and practices acceptable to the Authority, including disassembly, cleaning, and inspection as permitted, repair as necessary, and reassembly; and tested in accordance with approved standards and technical data, or in accordance with current standards and technical data acceptable to the Authority, which have been developed and documented by the State of Design, holder of the type certificate, supplemental type certificate, or a material, part, process, or appliance approval under Parts Manufacturing Authorization (PMA) or Technical Standard Order (TSO). (9) Return to Service (RTS). A document signed by an authorized representative of an approved maintenance organization (AMO) in respect of an inspection, repair or modification on a complete aircraft, engine or propeller after it has received a Maintenance Release for the maintenance performed at an AMO. (10) State of Design. The Contracting State which approved the original type certificate and any subsequent supplemental type certificates for an aircraft, or which approved the design of an aeronautical product or appliance. (11) State of Manufacture. The State having jurisdiction over the organization responsible for the final assembly of the aircraft engine or propeller. (12) State of Registry. The Contracting State on whose register the aircraft is entered. CERTIFICATE OF AIRWORTHINESS ELIGIBILITY (a) Any registered owner of Republic of the Philippines registered aircraft, or agent of the owner, may apply for a Certificate of Airworthiness for that aircraft. (b) Each applicant for a Certificate of Airworthiness shall apply in a form and manner acceptable to the Authority. CLASSIFICATIONS OF CERTIFICATE OF AIRWORTHINESS (a) Standard Certificate of Airworthiness will be issued for aircraft in the specific category and model designated by the State of Design in the type certificate. (b) The Authority may issue a Special Certificate of Airworthiness in the form of a restricted certificate or special flight permit. AMENDMENT OF CERTIFICATE OF AIRWORTHINESS (a) The Authority may amend or modify a Certificate of Airworthiness: (1) Upon application from an operator. (2) On its own initiative. TRANSFER OR SURRENDER OF CERTIFICATE OF AIRWORTHINESS (a) An owner shall transfer a Certificate of Airworthiness— (1) To the lessee upon lease of an aircraft within or outside the Republic of the Philippines. (2) To the buyer upon sale of the aircraft within the Republic of the Philippines. (b) An owner shall surrender the Certificate of Airworthiness for the aircraft to the issuing Authority upon sale of that aircraft outside of the Republic of the Philippines. EFFECTIVE DATES OF A CERTIFICATE OF AIRWORTHINESS (a) Unless sooner surrendered, suspended, revoked, or a termination date is otherwise established by the Authority, Certificate of Airworthiness are effective as follows: (1) Standard Certificate of Airworthiness, special Certificate of Airworthiness, and Certificate of Airworthiness issued for restricted or limited category aircraft are effective for one year as long as the maintenance, preventive maintenance, and alterations are performed in accordance with this CAR and the aircraft is registered in the Republic of the Philippines (2) A special flight permit is effective for the period of time specified in the permit. (3) An experimental certificate for research and development, showing compliance with regulations, crew training, or market surveys is effective for 1 year after the date of issue or renewal unless the Authority prescribes a shorter period. The duration of an experimental certificate issued for operating amateur-built aircraft, exhibition, air-racing, operating primary kit-built aircraft, unless the Authority establishes a specific period for good cause. (b) The owner, operator, or bailee of the aircraft shall, upon request, make it available for inspection by the Authority. (c) Upon suspension, revocation, or termination by order of the Authority of a Certificate of Airworthiness, the owner, operator, or bailee of an aircraft shall, upon request, surrender the certificate to the Authority. (d) When an aircraft imported for registration in Republic of the Philippines has a Certificate of Airworthiness issued by another Contracting State, Republic of the Philippines may, as an alternative to issuance of its own Certificate of Airworthiness, establish validity by suitable Authorization to be carried with the former Certificate of Airworthiness accepting it as the equivalent of a Certificate of Airworthiness issued by Republic of the Philippines. The validity of the Authorization shall not extend beyond the period of validity of the Certificate of Airworthiness or one year, whichever is less. CONTINUED AIRWORTHINESSOF AIRCRAFT AND COMPONENTS APPLICABILITY (a) This Subpart prescribes rules governing the continued airworthiness of civil aircraft registered in the Republic of the Philippines whether operating inside or outside the borders of the Republic of the Philippines. RESPONSIBILITY (a) The owner of an aircraft or, in the case of a leased aircraft, the lessee, shall be responsible for maintaining the aircraft in an airworthy condition by ensuring that— (1) All maintenance, overhaul, modifications and repairs which affect airworthiness are performed as prescribed by the State of Registry; (2) Authorized maintenance personnel make appropriate entries in the aircraft maintenance records certifying that the aircraft is airworthy; (3) A maintenance release is completed to the certify that the maintenance work performed has been completed satisfactorily and in accordance with the prescribed methods; and (4) In the event there are open discrepancies, the maintenance release includes a list of the uncorrected maintenance items and these items are made a part of the aircraft permanent record. DAMAGE TO AIRCRAFT (a) When the aircraft has sustained damage that requires major repair or replacement of the affected component, the CAAP shall judge whether the damage is of a nature such that the aircraft is no longer airworthy as defined by the appropriate airworthiness requirements. (b) If the damage is sustained or ascertained when the aircraft is in the territory of another Contracting State, the authorities of that Contracting State shall be entitled to prevent the aircraft from resuming its flight on the condition that they shall advise the CAAP immediately, communicating to all details necessary to formulate the judgment referred to in (a). (c) When CAAP considers that the damage sustained is of a nature such that the aircraft is still airworthy, the aircraft shall be allowed to resume its flight. PERSONS AUTHORIZED TO PERFORM MAINTENANCE (a) No person may perform any task defined as maintenance on an aircraft or aeronautical products, except as provided in the following— (1) A pilot licensed by the Authority may perform elementary work as specified in IS: 5.6.1.3 (a). (2) A person working under the supervision of a aviation maintenance technician, may perform the maintenance, preventive maintenance, and modifications that the supervisory aviation maintenance technician is Authorized to perform— (i) If the supervisor personally observes the work being done to the extent necessary to ensure that it is being done properly, and (ii) If the supervisor is readily available, in person, for consultation. (3) A licensed aviation maintenance technician may perform or supervise the maintenance or modification of an aircraft or aeronautical product for which he or she is rated subject to the limitation of Part 2, Section 2.4.4 of these regulations. (4) An AMO may perform aircraft maintenance within the limits specified by the Authority. (5) No AOC holder may perform aircraft maintenance unless approved under Part 6 of these regulations. (6) A manufacturer holding an AMO may— (i) Rebuild or alter any aeronautical product manufactured by that manufacturer under a type or production certificate; (ii) Rebuild or alter any aeronautical product manufactured by that manufacturer under a TSO Authorization, a Parts Manufacturer Approval by the State of Design, or Product and Process Specification issued by the State of Design; and (iii) Perform any inspection required by Part 8 on aircraft it manufacturers, while currently operating under a production certificate or under a currently approved production inspection system for such aircraft. AUTHORIZED PERSONNEL TO APPROVE FOR RETURN TO SERVICE (a) No person or entity, other than the Authority, may approve an aircraft, airframe, aircraft engine, propeller, appliance, or component part for return to service after it has undergone maintenance, preventive maintenance, rebuilding, or modification, except as provided in the following: (1) A pilot licensed by the Authority may return his or her aircraft to service after performing Authorized preventive maintenance. (2) A licensed aviation maintenance technician may approve aircraft and aeronautical products for return to service after he or she has performed, supervised, or inspected its maintenance subject to the limitation of Part 2, paragraph 2.6.2.8 of these regulations. (3) An AMO may approve aircraft and aeronautical products for return to service as provided in the specifications approved by the Authority. PERSONS AUTHORIZED TO PERFORM INSPECTIONS (a) No person, other than the Authority, may perform the inspections required by Subpart 8.2.1.7 for aircraft and aeronautical products prior to or after it has undergone maintenance, preventive maintenance, rebuilding, or modification, except as provided in the following: (1) An aviation maintenance technician may conduct the required inspections of aircraft and aeronautical products for which he or she is rated and current, except on aircraft involved in commercial operations. (2) An AMO may perform the required inspections of aircraft and aeronautical products as provided in the specifications approved by the Authority. C. CAAP - CIVIL AVIATION REGULATION PART 6: APPROVED MAINTENANCE OGRANIZATION CAR Part 6 provides regulations for the registration and monitoring of Approved Maintenance Organizations (AMO) in Republic of the Philippines. The proper maintenance of aircraft is fundamental to aviation safety, and requires meticulous record-keeping. The AMO certificate will contain (1) The certificate number specifically assigned to the AMO; (2) The name and location (main place of business) of the AMO; (3) The date of issue and period of validity; (4) The ratings issued to the AMO; and (5) Authority signature. The AMO Specific Operating Provisions will contain (1) The certificate number specifically assigned to the AMO; (2) The class or limited ratings issued in detail, including special approvals and limitations issued; (3) The date issued or revised (4) Accountable manager and Authority signatures (5) The certificate issued to each certificated maintenance organization must be available in the premises for inspection by the public and the Authority. APPLICATION FOR AN AMO CERTIFICATE (a) The Authority will require an applicant for an AMO certificate to submit the following: (1) An application in a form and a manner prescribed by the Authority; (2) Its maintenance procedures manual in duplicate; (3) A list of the maintenance functions to be performed for it, under contract, by another AMO; (4) A list of all AMO certificates and ratings pertinent to those certificates issued by any contracting State other than Republic of the Philippines; and (5) Any additional information the Authority requires the applicant to submit. (b) An application for the amendment of an existing AMO certificate shall be made on a form and in a manner prescribed by the Authority ISSUANCE OF AN AMO CERTIFICATE (a) An applicant may be issued an AMO certificate if, after investigation, the Authority finds that the applicant (1) Meets the applicable regulations and standards for the holder of an AMO; and (2) Is properly and adequately equipped for the performance of maintenance of aircraft or aeronautical product for which it seeks approval DURATION AND RENEWAL OF CERTIFICATE (a) A Certificate or Rating issued to an Approved Maintenance Organization is valid for two (2) years from the date of issuance subject to the compliance with the Approved Maintenance Organization Procedures Manual and the provisions of PCAR Part 6, unless: (1) The Approved Maintenance Organization surrenders the Certificate or Rating; and (2) The CAAP suspends or revokes the Certificate or Rating. (b) The holder of a certificate that expires or is surrendered, suspended, or revoked by the CAAP must return the certificate and specific operating provisions to the CAAP. (c) A certificated approved maintenance organization that applies for a renewal of its CAAP approved maintenance organization certificate: must submit its request for renewal with supporting documents no later than 60 days before the approved maintenance organization's current certificate expires. Late submission of the renewal request may result in the application being treated as a new application for an AMO. Note: An AMO certificate may not be renewed if any of the conditions upon which the certificate was originally issued or amended are changed or become invalid for any reason. CONTINUED VALIDITY OF APPROVAL (a) Unless the approval has been previously surrendered, superseded, suspended, revoked or expired by virtue of exceeding any expiration date that may be specified in the approval certificate, the continued validity of approval is dependent upon (1) The AMO remaining in compliance with this Part; (2) The Authority being granted access to the organization's facilities to determine continued compliance with this regulation; and (3) The payment of any charges prescribed by the Authority. (b) The holder of an AMO certificate that expires or is surrendered, suspended, or revoked, shall return it to the Authority. CHANGES TO THE AMO AND CERTIFICATE AMENDMENTS AMO shall provide written notification to the Authority (1) The name of the organization; (2) The location of the organization; (3) The housing, facilities, equipment, tools, material, procedures, work scope and certifying staff that could affect the AMO rating or ratings; (4) The ratings held by the AMO, whether granted by the Authority or held through an AMO certification issued by another contracting State; Note: See subsection 6.2.1.1(a). (5) Additional locations of the organization; (6) The accountable manager; or (7) The list of management personnel identified as described in the maintenance procedure manual. NOTE: When the Authority issues an amendment to an AMO certificate because of new ownership of the AMO, the Authority will assign a new certificate number to the amended AMO certificate. RECORD OF CERTIFYING STAFF (a) The AMO shall maintain a roster of all certifying staff, which includes details of the scope of their authorization. (b) Certifying staff shall be notified in writing of the scope of their authorization APPROVED MAINTENANCE ORGANIZATION PROCEDURES MANUAL (a) An AMO Maintenance Procedure Manual and any subsequent amendments thereto shall be approved by the Authority prior to use. (b) The AMO Maintenance Procedures Manual shall specify the scope of work required of the AMO in order to satisfy the relevant requirements needed for an approval of an aircraft or aeronautical product for return to service. (c) The procedures manual and any other manual it identifies must: (1) Include instructions and information necessary to allow the personnel concerned to perform their duties and responsibilities with a high degree of safety; (2) Be in a form that is easy to revise and contains a system which allows personnel to determine current revision status; (3) Have the date of the last revision printed on each page containing the revision; (4) Not be contrary to any applicable Republic of the Philippines regulation or the AMO's specific operating provisions; and (5) Include a reference to appropriate civil aviation regulations. (d) The AMO shall provide an Approved Maintenance Procedures Manual for use by the organization, containing the following information (1) A statement signed by the accountable manager confirming that the maintenance organization Procedures Manual and any associated manuals define the AMO's compliance with this regulation and will be complied with at all times; (2) A procedure to establish and maintain a current list of the titles and names of the management personnel accepted by the Authority. The list of personnel may be separate from the Procedures Manual but must be kept current and available for review by the Authority when requested; (3) A list which describes the duties and responsibility of the management personnel and which matters on which they may deal directly with the Authority on behalf of the AMO; (4) An organization chart showing associated chains of responsibility of the management personnel. (5) A procedure to establish and maintain a current roster of certifying personnel; 6) A description of the procedures used to establish the competence of maintenance personnel; (7) A general description of manpower resources; (8) A description of the method used for the completion and retention of the maintenance records; (9) A description of the procedure for preparing the maintenance release and the circumstances under which the release is to be signed; (10) A description, when applicable, of additional procedures for complying with an AOC holder's maintenance procedures and requirements; (11) A description of the procedures for complying with the service information reporting requirement contained in 6.5.1.9; (12) A description of the procedure for receiving, amending and distributing within the maintenance organization all necessary airworthiness data from the type certificate holder or the type design organization; (13) A general description of the facilities located at each address specified in the AMO's approval certificate; (14) A general description of the AMO's scope of work relevant to the extent of approval; (15) The notification procedure for AMO to use when requesting the approval of changes to the organization of the AMO from the Authority; (16) The amendment procedure for the AMO procedures manual, including the submission to the Authority, and the method and procedures to ensure that all amendments are furnished promptly to all organizations And persons to whom the manual has been issued; (17) The AMO's procedures, acceptable to the Authority, to ensure good maintenance practices and compliance with all relevant requirements in this subsection; (18) The AMO's procedures to establish and maintain an independent quality system to monitor compliance with the adequacy of the procedures to ensure good quality maintenance practices and airworthy aircraft and aeronautical products. Compliance monitoring must include a feedback system to the person or group of persons specified in 6.4.1.1 and ultimately to the accountable manager to ensure, as necessary, corrective action. Such a system shall be acceptable to the Authority; (19) The AMO procedures for self-evaluations, including methods and frequency of such evaluations, and procedures for reporting results to the accountable manager for review and action: (20) A list of operators, if appropriate, to which the AMO provides an aircraft maintenance service: (21) A list of organizations performing maintenance on behalf of the AMO; and (22) A list of the AMO's line maintenance locations and procedures, if applicable. MAINTENANCE ORGANIZATION PROCEDURES MANUAL (a) AMO personnel shall be familiar with those parts of the manuals that are relevant to the maintenance work they perform. (b) The AMO shall specify in the Procedures Manual who should amend the manual, particularly in the case where the manual consists of several parts. (c) The Quality Manager shall be responsible for (1) Monitoring the amendment of the Procedures Manual, including associated procedures manuals (2) Submitting proposed amendments to the Authority, unless the Authority has agreed, via a procedure stated in the amendment section of the Procedures Manual. That some defined class of amendments may be incorporated without approval by the Authority. (d) The Procedures Manual shall address four main areas (1) The management Procedures Manual covering the parts previously specified: (2) The maintenance procedures covering all aspects of how aircraft components may be accepted from outside sources and how aircraft will be maintained to the required standard; (3) The quality system procedures, including the methods of qualifying mechanics, inspection, certifying staff and quality audit personnel; and (4) Contracted AOC holder procedures and paperwork. MAINTENANCE PROCEDURES AND INDEPENDENT QUALITY ASSURANCE SYSTEM (b) The AMO shall establish an independent quality assurance system, acceptable to the Authority, to monitor compliance with and adequacy of the procedures and by providing a system of inspection to ensure that all maintenance is properly performed. (c) The quality assurance system shall include a procedure to initially qualify and periodically perform audits on persons performing work on behalf of the AMO. (h) The AMO's quality system shall indicate when audits are due, when completed, and establish a system of audit reports, which can be seen by visiting Authority staff on request. The audit system shall clearly establish a means by which audit reports containing observations about non-compliance or poor standards are communicated to the accountable manager. CAPABILITY LIST (a) Each certificated approved maintenance organization must prepare and retain a current capability list approved by the Authority. The approved maintenance organization may not perform maintenance, preventive maintenance, or modifications on an article until the article has been listed on the capability list in accordance with this Part and 6.5.1.1(d)(19). (b) The capability list must identify each article by make and model, part number, or other nomenclature designated by the article's manufacturer. (c) An article may be listed on the capability list only if the article is within the scope of the ratings and classes of the approved maintenance organization's certificate, and only after the approved maintenance organization has performed a self-evaluation in accordance with 6.5.1.1 (d)(19). The approved maintenance organization must perform the self-evaluation described in this paragraph to determine that the maintenance organization has all of the facilities, equipment, material, technical data, processes, housing, and trained personnel in place to perform the work on the article as required by this part. If the approved maintenance organization makes that determination, it may list the article on the capability list. (h) The AMO shall retain the capability list(s) and self-evaluation(s) for two years from the date accepted by the Accountable Manager. PRIVILEGES OF THE APPROVED MAINTENANCE ORGANIZATION (a) The AMO shall carry out the following tasks as permitted by and in accordance with the AMO maintenance procedures manual (1) Maintain any aircraft or aeronautical product for which it is rated at the location identified in the approval certificate; LIMITATIONS ON THE AMO The AMO shall maintain an aircraft or aeronautical product for which it is approved only when all necessary housing, facilities, equipment, tools, material, approved technical data and certifying staff are available. CERTIFICATE OF RETURN TO SERVICE (a) A certificate of return to service shall be issued by appropriately authorized certifying staff when satisfied that all required maintenance of the aircraft or aeronautical product has been properly carried out by the AMO in accordance with the maintenance procedure manual. (b) A certificate of return to service shall contain (1) Basic details of the maintenance carried out; (2) The date such maintenance was completed; and (3) The identity, including the authorization reference, of the AMO and certifying staff issuing the certificate. MAINTENANCE RECORDS (a) The AMO shall record, in a form acceptable to the Authority, all details for maintenance work performed. (b) The AMO shall provide a copy of each certificate of return to service to the aircraft operator, together with a copy of any specific airworthiness data used for repairs/modifications performed. (c) The AMO shall retain a copy of all detailed maintenance records and any associated airworthiness data for two years from the date the aircraft or aeronautical product to which the work relates was released from the AMO. (d) Each person who maintains, performs preventive maintenance, rebuilds, or modifies an aircraft/aeronautical product shall make an entry in the maintenance record of that equipment: (e) No person shall describe in any required maintenance entry or form an aircraft or aeronautical component as being overhauled unless: CAA INSPECTIONS Each certificated approved maintenance organization shall allow the Authority to inspect that approved maintenance organization and any of its contract maintenance facilities at any time to determine compliance with this part. Arrangements for maintenance, preventive maintenance or modifications by a contractor shall include provisions for inspections of the contractor by the Authority. D. US-FAA 14 CFR PART 145 : REPAIR STATION OPERATORS The FAA may deny an application for a repair station certificate if the FAA finds that: A. The applicant holds a repair station certificate in the process of being revoked, or previously held a repair station certificate that was revoked; B. The applicant intends to fill or fills a management position with an individual who exercised control over or who held the same or a similar position with a certificate holder whose repair station certificate was revoked, or is in the process of being revoked, and the individual materially contributed to the circumstances causing the revocation or causing the revocation process, or; C. An individual who will have control over or substantial ownership interest in the applicant had the same or similar control or interest in a certificate holder whose repair station certificate was revoked, or is in the process of being revoked, and the individual materially contributed to the circumstances causing the revocation or causing the revocation process E. US-FAA 14 CFR PART 39: AIRWORTHINESS DIRECTIVES Airworthiness Directives (ADs) are legally enforceable rules issued by the FAA in accordance with 14 CFR part 39 to correct an unsafe condition in a product. 14 CFR part 39 defines a product as an aircraft, aircraft engine, propeller, or appliance Who has to comply with ADs? No person may operate a product to which an AD applies, except in accordance with the requirements of the AD. Furthermore, the owner or operator of an aircraft is required by 14 CFR 91.403 to maintain the aircraft in compliance with all ADs. When do I have to comply with an AD? The AD specifies a compliance time that relates to the effective date of the AD. That compliance time determines when the actions are required. When is an AD issued? The FAA issues an AD addressing a product when we find that: A. An unsafe condition exists in a product; and, B. The condition is likely to exist or develop in other products of the same type design. What types of Airworthiness Directives (ADs) are issued? We issue three types of ADs: A. Notice of Proposed Rulemaking (NPRM), followed by a B. Final Rule Final Rule; Request for Comments C. Emergency ADs When is an Emergency Airworthiness Directive (AD) issued? An Emergency AD is issued when an unsafe condition exists that requires immediate action by an owner/operator. The intent of an Emergency AD is to rapidly correct an urgent safety of flight situation. For more information, see the Emergency AD page. What is a superseded AD? An AD is considered no longer in effect when it is superseded by a new AD. The superseding AD identifies the AD that is no longer in effect. There are no compliance requirements for an AD that has been superseded. F. US-FAA FEDERAL AVIATION REGULATION PART 43: ALTERATIONS MAINTENANCE, PREVENTIVE MAINTENANCE, REBUILDING AND (a) MAJOR ALTERATIONS (1) Airframe major alterations. Alterations of the following parts and alterations of the following types, when not listed in the aircraft specifications issued by the FAA, are airframe major alterations: (i) Wings. (ii) Tail surfaces. (iii) Fuselage. (iv) Engine mounts. (v) Control system. (vi) Landing gear. (vii) Hull or floats. (viii) Elements of an airframe including spars, ribs, fittings, shock absorbers, bracing, cowling, fairings, and balance weights. (ix) Hydraulic and electrical actuating system of components. (x) Rotor blades. (xi) Changes to the empty weight or empty balance which result in an increase in the maximum certificated weight or center of gravity limits of the aircraft. (xii) Changes to the basic design of the fuel, oil, cooling, heating, cabin pressurization, electrical, hydraulic, de-icing, or exhaust systems. (xiii) Changes to the wing or to fixed or movable control surfaces which affect flutter and vibration characteristics. (2) Powerplant major alterations. The following alterations of a powerplant when not listed in the engine specifications issued by the FAA, are powerplant major alterations. (i) Conversion of an aircraft engine from one approved model to another, involving any changes in compression ratio, propeller reduction gear, impeller gear ratios or the substitution of major engine parts which requires extensive rework and testing of the engine. (ii) Changes to the engine by replacing aircraft engine structural parts with parts not supplied by the original manufacturer or parts not specifically approved by the Administrator. (iii) Installation of an accessory which is not approved for the engine. (iv) Removal of accessories that are listed as required equipment on the aircraft or engine specification. (v) Installation of structural parts other than the type of parts approved for the installation. (vi) Conversions of any sort for the purpose of using fuel of a rating or grade other than that listed in the engine specifications. (3) Propeller major alterations. The following alterations of a propeller when not authorized in the propeller specifications issued by the FAA are propeller major alterations: (i) Changes in blade design. (ii) Changes in hub design. (iii) Changes in the governor or control design. (iv) Installation of a propeller governor or feathering system. (v) Installation of propeller de-icing system. (vi) Installation of parts not approved for the propeller. (4) Appliance major alterations. Alterations of the basic design not made in accordance with recommendations of the appliance manufacturer or in accordance with an FAA Airworthiness Directive are appliance major alterations. In addition, changes in the basic design of radio communication and navigation equipment approved under type certification or a Technical Standard Order that have an effect on frequency stability, noise level, sensitivity, selectivity, distortion, spurious radiation, AVC characteristics, or ability to meet environmental test conditions and other changes that have an effect on the performance of the equipment are also major alterations. (b) MAJOR REPAIRS (1) Airframe major repairs. Repairs to the following parts of an airframe and repairs of the following types, involving the strengthening, reinforcing, splicing, and manufacturing of primary structural members or their replacement, when replacement is by fabrication such as riveting or welding, are airframe major repairs. (i) Box beams. (ii) Monocoque or semimonocoque wings or control surfaces. (iii) Wing stringers or chord members. (iv) Spars. (v) Spar flanges. (vi) Members of truss-type beams. (vii) Thin sheet webs of beams. (viii) Keel and chine members of boat hulls or floats. (ix) Corrugated sheet compression members which act as flange material of wings or tail surfaces. (x) Wing main ribs and compression members. (xi) Wing or tail surface brace struts. (xii) Engine mounts. (xiii) Fuselage longerons. (xiv) Members of the side truss, horizontal truss, or bulkheads. (xv) Main seat support braces and brackets. (xvi) Landing gear brace struts. (xvii) Axles. (xviii) Wheels. (xix) Skis, and ski pedestals. (xx) Parts of the control system such as control columns, pedals, shafts, brackets, or horns. (xxi) Repairs involving the substitution of material. (xxii) The repair of damaged areas in metal or plywood stressed covering exceeding six inches in any direction. (xxiii) The repair of portions of skin sheets by making additional seams. (xxiv) The splicing of skin sheets. (xxv) The repair of three or more adjacent wing or control surface ribs or the leading edge of wings and control surfaces, between such adjacent ribs. (xxvi) Repair of fabric covering involving an area greater than that required to repair two adjacent ribs. (xxvii) Replacement of fabric on fabric covered parts such as wings, fuselages, stabilizers, and control surfaces. (xxviii) Repairing, including rebottoming, of removable or integral fuel tanks and oil tanks. (2) Powerplant major repairs. Repairs of the following parts of an engine and repairs of the following types, are powerplant major repairs: (i) Separation or disassembly of a crankcase or crankshaft of a reciprocating engine equipped with an integral supercharger. (ii) Separation or disassembly of a crankcase or crankshaft of a reciprocating engine equipped with other than spur-type propeller reduction gearing. (iii) Special repairs to structural engine parts by welding, plating, metalizing, or other methods. (3) Propeller major repairs. Repairs of the following types to a propeller are propeller major repairs: (i) Any repairs to, or straightening of steel blades. (ii) Repairing or machining of steel hubs. (iii) Shortening of blades. (iv) Retipping of wood propellers. (v) Replacement of outer laminations on fixed pitch wood propellers. (vi) Repairing elongated bolt holes in the hub of fixed pitch wood propellers. (vii) Inlay work on wood blades. (viii) Repairs to composition blades. (ix) Replacement of tip fabric. (x) Replacement of plastic covering. (xi) Repair of propeller governors. (xii) Overhaul of controllable pitch propellers. (xiii) Repairs to deep dents, cuts, scars, nicks, etc., and straightening of aluminum blades. (xiv) The repair or replacement of internal elements of blades. (4) Appliance major repairs. Repairs of the following types to appliances are appliance major repairs: (i) Calibration and repair of instruments. (ii) Calibration of radio equipment. (iii) Rewinding the field coil of an electrical accessory. (iv) Complete disassembly of complex hydraulic power valves. (v) Overhaul of pressure type carburetors, and pressure type fuel, oil and hydraulic pumps. (c) PREVENTIVE MAINTENANCE Preventive maintenance is limited to the following work, provided it does not involve complex assembly operations: (1) Removal, installation, and repair of landing gear tires. (2) Replacing elastic shock absorber cords on landing gear. (3) Servicing landing gear shock struts by adding oil, air, or both. (4) Servicing landing gear wheel bearings, such as cleaning and greasing. (5) Replacing defective safety wiring or cotter keys. (6) Lubrication not requiring disassembly other than removal of nonstructural items such as cover plates, cowlings, and fairings. (7) Making simple fabric patches not requiring rib stitching or the removal of structural parts or control surfaces. In the case of balloons, the making of small fabric repairs to envelopes (as defined in, and in accordance with, the balloon manufacturers' instructions) not requiring load tape repair or replacement. (8) Replenishing hydraulic fluid in the hydraulic reservoir. (9) Refinishing decorative coating of fuselage, balloon baskets, wings tail group surfaces (excluding balanced control surfaces), fairings, cowlings, landing gear, cabin, or cockpit interior when removal or disassembly of any primary structure or operating system is not required. (10) Applying preservative or protective material to components where no disassembly of any primary structure or operating system is involved and where such coating is not prohibited or is not contrary to good practices. (11) Repairing upholstery and decorative furnishings of the cabin, cockpit, or balloon basket interior when the repairing does not require disassembly of any primary structure or operating system or interfere with an operating system or affect the primary structure of the aircraft. (12) Making small simple repairs to fairings, nonstructural cover plates, cowlings, and small patches and reinforcements not changing the contour so as to interfere with proper air flow. (13) Replacing side windows where that work does not interfere with the structure or any operating system such as controls, electrical equipment, etc. (14) Replacing safety belts. (15) Replacing seats or seat parts with replacement parts approved for the aircraft, not involving disassembly of any primary structure or operating system. (16) Trouble shooting and repairing broken circuits in landing light wiring circuits. (17) Replacing bulbs, reflectors, and lenses of position and landing lights. (18) Replacing wheels and skis where no weight and balance computation is involved. (19) Replacing any cowling not requiring removal of the propeller or disconnection of flight controls. (20) Replacing or cleaning spark plugs and setting of spark plug gap clearance. (21) Replacing any hose connection except hydraulic connections. (22) Replacing prefabricated fuel lines. (23) Cleaning or replacing fuel and oil strainers or filter elements. (24) Replacing and servicing batteries. (25) Cleaning of balloon burner pilot and main nozzles in accordance with the balloon manufacturer's instructions. (26) Replacement or adjustment of nonstructural standard fasteners incidental to operations. (27) The interchange of balloon baskets and burners on envelopes when the basket or burner is designated as interchangeable in the balloon type certificate data and the baskets and burners are specifically designed for quick removal and installation. (28) The installations of anti-misfueling devices to reduce the diameter of fuel tank filler openings provided the specific device has been made a part of the aircraft type certificiate data by the aircraft manufacturer, the aircraft manufacturer has provided FAA-approved instructions for installation of the specific device, and installation does not involve the disassembly of the existing tank filler opening. (29) Removing, checking, and replacing magnetic chip detectors. (30) The inspection and maintenance tasks prescribed and specifically identified as preventive maintenance in a primary category aircraft type certificate or supplemental type certificate holder's approved special inspection and preventive maintenance program when accomplished on a primary category aircraft provided: (i) They are performed by the holder of at least a private pilot certificate issued under part 61 who is the registered owner (including co-owners) of the affected aircraft and who holds a certificate of competency for the affected aircraft (1) issued by a school approved under §147.21(e) of this chapter; (2) issued by the holder of the production certificate for that primary category aircraft that has a special training program approved under §21.24 of this subchapter; or (3) issued by another entity that has a course approved by the Administrator; and (ii) The inspections and maintenance tasks are performed in accordance with instructions contained by the special inspection and preventive maintenance program approved as part of the aircraft's type design or supplemental type design. (31) Removing and replacing self-contained, front instrument panel-mounted navigation and communication devices that employ tray-mounted connectors that connect the unit when the unit is installed into the instrument panel, (excluding automatic flight control systems, transponders, and microwave frequency distance measuring equipment (DME)). The approved unit must be designed to be readily and repeatedly removed and replaced, and pertinent instructions must be provided. Prior to the unit's intended use, and operational check must be performed in accordance with the applicable sections of part 91 of this chapter. (32) Updating self-contained, front instrument panel-mounted Air Traffic Control (ATC) navigational software data bases (excluding those of automatic flight control systems, transponders, and microwave frequency distance measuring equipment (DME)) provided no disassembly of the unit is required and pertinent instructions are provided. Prior to the unit's intended use, an operational check must be performed in accordance with applicable sections of part 91 of this chapter. G. EASA PART 145: CONTINUING AIRWOTHINESS Maintenance organisation approvals shall be issued in accordance with the provisions of ANNEX I, Subpart F, or ANNEX II. Certifying staff shall be qualified in accordance with the provisions of ANNEX III (Part 66) EASA FORM 1 is a certificate of return to service for components The Agency shall develop ACCEPTABLE MEANS OF COMPLIANCE (AMC) that competent authorities, organisations, personnels may use to demonstrate compliance with the provisions of the Annexes of this regulation. II. CAAP - MAINTENANCE PROCEDURE MANUAL Line Maintenance A. Any maintenance that must be carried out before flight to ensure that the aircraft is fit for the intended flight. This may include: (1) Trouble shooting. (2) Defect Rectification. (3) Component replacement with use of external test equipment if required (this may include components such as engines or propellers). (4) Scheduled maintenance including ADs and SBs and/or checks including visual inspections that will detect obvious unsatisfactory conditions/discrepancies but do not require extensive indepth inspection. It may also include internal structure, systems and powerplant items, which are visible through quick opening access panels/doors. (5) Minor repairs and modifications which do not require extensive disassembly and can be accomplished by simple means. B. Line maintenance shall be performed only on aircraft listed in this MPM. It may include scheduled checks up to and including Weekly/A-Checks in accordance with customer or operator requirements. C. Maintenance activities at the LTP Line Maintenance Southern Philippines-Cebu and Davao facilities are limited to Line Maintenance on aircraft listed in this MPM. D. Maintenance activities at the LTP-Clark facility are limited to Line Maintenance for narrow and wide body aircraft and including A-Checks for narrow body aircraft listed in this MPM. E. Maintenance of any aircraft listed in this MPM at a location other than the approved locations shall be subject to the need for such maintenance arising from the necessity to unground unserviceable aircraft or to support occasional line maintenance; and to the availability of all necessary Responsibilities of Authorized Signatories A. The person approving for return to service of an aircraft, airframe, aircraft engine, appliance or component after performing any inspection shall make an entry in the maintenance record of that equipment containing the following information: (1) The type of inspection and a brief description and statement of the extent of the inspection. (2) The date of the inspection and total time in service of aircraft or component. (3) The signature, the certificate number and kind of certificate held by the person approving for return to service the aircraft, airframe, aircraft engine, propeller, appliance, component or portions thereof. Certifying Staff Qualification A. All Inspection and Return to Service (RTS) authorized personnel must: (1) Be thoroughly familiar with all inspection methods, techniques and equipment of their specialty to determine the quality or airworthiness of an article undergoing maintenance or alteration. (2) Be proficient in the use of inspection aids intended for that purpose. (3) Avail themselves and be familiar with current specifications involving inspection tolerances, limits and procedures as set forth by the manufacturer of the article undergoing inspections and other forms of inspection information such as CAA airworthiness directives, manufacturer’s bulletins and applicable CAA regulations and advisory circulars. (4) Be able to read, write and understand the English language. (5) Have the required continuation training. (6) Have been involved in at least six (6) months of actual relevant aircraft or component maintenance experience in any consecutive two (2) years period. (7) Have appropriate CAAP license. B. Certifying staff are able to determine when the aircraft or aircraft component is ready to release to service and when it should not be released to service. Position Description: Aircraft Mechanic Reports to: Maintenance Crew Chief/ForemanBay Production/Aircraft Maintenance Authority and Responsibilities: General A. Accomplishes routine and non-routine checks in accordance with the customer maintenance program. B. Oversees and monitors Line and Base Maintenance activities to make sure that the Customer’s aircraft are released on time and in accordance with the terms of contract. C. Reports technical delays and other pertinent aspects concerning the station for the information and guidance of the Customer. D. Administers and coordinates the international spare pooling activities at the station with the Customer pooling partners to maximize and fully exercise the benefits from this agreement. E. Provides store service for Customer spare parts, worksheets and forms including the requesting of replacements for issued and expired items to ensure availability when required. F. Keeps an up-to-date record of Customer tools and equipment to see to it that they are always in operating condition. G. Generates work order for non-routine services. H. Ensures that Customer property such as aircraft materials and components, manuals, forms, documents, etc., are placed in such a way to prevent commingling with that of another Customer. Proper identification and labeling is necessary. I. Accomplishes regular servicing and maintenance of airframe, engines and components as required in the Line Maintenance checks in accordance with the procedures set forth in the Customer manuals or manufacturer specifications. J. Determines defects and unsatisfactory condition present in aircraft and diagnoses their causes to pinpoint areas or system where corrective actions are needed. K. Performs corrective repairs, adjustments or unit replacements consistent with the quality standards set by the Customer to keep the aircraft in flying condition. L. Signs off work accomplishment in required Customer record and accomplishes forms or paper works which may be needed in the performance of duties. M. Maintains a clean and neat working area at all times and follows all safety rules and regulations. Inspection System Acceptable Forms of Signatures/Sign-off A. Various forms of signatures/sign-off are used to attest completion of maintenance tasks. Acceptable forms of signatures/sign-off for LTP maintenance records are: (1) Signature and employee ID Number (2) Initials and employee ID Number (3) Authorized stamp Procedures A. When using signature or initial as a means of sign-off, personnel shall always indicate their ID number. B. Signature over printed name or initial is acceptable but not required unless otherwise specified. C. Signature or initial shall be written using indelible blue or black ink unless otherwise specified. D. Stamp imprints should be identifiable and legible. Worn-out stamps shall be surrendered to QMA - Internal Authorizations (QM-A1) for replacement. E. At no time shall personnel sign-off more than one task with a single signature, initial or stamp. F. An impression of stamp placed on the appropriate column indicates that the particular task was satisfactorily accomplished as per specified procedure. G. Each issued stamp shall be identified with a unique number or marking. No two (2) individuals will be issued identical stamps. H. Only controlled stamps shall be used in lieu of signature or initial to sign-off aircraft documents or component maintenance records. Production Planning stamps are controlled by the Department/Division concerned. I. All signatures and/or stamp impression on maintenance documents shall be provided with dates. Inspection and Maintenance Authorization Stamp A. Inspection and certification of maintenance may be signified by a stamp in lieu of signature or initial to indicate acceptance or rejection of a particular task documented during and in connection with maintenance, preventive maintenance, overhaul, repair and alteration. B. Stamps can be used to accept as serviceable or reject applicable aircraft parts during inspection at Central Receiving Section (MM21). For unsatisfactorily accomplished task items, or articles found not in conformance with the requirements, impression of stamps opposite appropriate remarks/ entry on document shall signify work and/or component rejection. Responsibilities for the Control of Stamps A. Stamp holder shall: (1) Be responsible for the control and total upkeep of their stamp. The stamps shall never be loaned to other persons and/or left lying around workbenches or the work areas. (2) Keep their stamp and inkpad clean at all times to ensure clear and neat stamp impression. (3) Be responsible to safeguard the issued stamp. He shall immediately report to his Division Head in writing if his stamp was lost. He shall submit supporting documents for the missing stamp containing the following information: (a) Name (b) Stamp description (c) Date of lost (4) Accomplish Request for Authorization Stamp Form (F11-050L) in case the previously issued stamp was damaged, lost or needs replacement due to position change; and after endorsement by the Division Head, submit to QM-A - Internal Authorizations (QM-A1) for further action and approval. (5) Surrender to QM-A1 his/her stamp upon termination of employment, position change or suspension/revocation of authorization. Notes: (1) The letter adjacent to each employee Identification Number (ID) is the counting letter starting from A to Z incrementing every issue of replacement. (2) The LTP employee ID number of the resigned personnel shall not be re-issued to the same person in case of re-employment nor to any other person. Suspected Unapproved Parts A. An aircraft, article or a part of an aircraft article that was not manufactured or maintained in accordance with approved procedures specified in aviation regulations (e.g. 14 CFR Part 21, CAR Part 5) or that does not conform to an approved type design or certain standards, or has missing, altered or incomplete certification or delivery documentation, may be considered as a Suspected Unapproved Parts (SUP). @ Note: It is possible that the part or documentation may have been deliberately manufactured or altered (counterfeit) in order to appear to be genuine. Passing on of Information A. Information available about unapproved parts received from authorities, production organizations, customers, etc., should be passed on to the Quality Management Department which will, if necessary, conduct an investigation to establish if LTP or vendor has used the affected part(s). Detection of SUP A. Unapproved parts may be brought into circulation with invalid or forged certificates of return to service histories or accompanying papers and incorrect labels and packaging. B. Unapproved parts may also be discovered installed on aircraft during maintenance and inspection. C. Such parts are not easy to identify because they are very similar to approved parts. Genuine and counterfeit parts frequently differ only in the material or production method used. D. SUP may be found or detected at any phase of inspection from goods receiving through installation or removal on aircraft. E. The following indicators suggest that a part may be an unapproved part: (1) Modified or unusual surface finish. (2) Part is of a different color. (3) Missing data plate or unusual presentation, particularly tampered/altered part number and/ or serial number. (4) Part or serial numbers engraved in an unusual place. (5) Generally distinctive and unusual appearance of the part. F. Distinctive Documents and Packaging. (1) Missing, incorrect or incomplete documents. (2) Modified, smudged, overwritten or over-stamped entries, particularly the date, PN or SN. (3) The packaging material looks different, e.g. not the original box. (4) Use of simpler packaging, such as missing protective sleeves. (5) Slight modification to the Company logo. G. Distinctive Features of Suppliers. (1) The price of a part is significantly lower than the price asked by other suppliers. (2) The delivery time for a part that is not currently in the warehouse is significantly shorter than with other suppliers. (3) The supplier gives the impression that he can obtain any part in any quantity. (4) The supplier is unable to immediately supply all the requested accompanying documents, particularly the certificate of return to service. (5) Unusual or distinctive financial procedures. Suspected Unapproved Parts Handling Procedure A. Upon discovery of a Suspected Unapproved Part (SUP) (1) User: (a) Shall immediately report to Quality Management Department. (b) Shall provide unit with SUP identification label/tape. (c) Shall route unit to Aircraft Material Management (MM) for quarantining and shall request for a written confirmation of the receiving party that he/she had received the unit. (2) Quality Management Department: (a) Shall initiate investigation as necessary. (b) Shall notify/report the SUP occurrence to CAAP, as appropriate and to the customer/ owner of the part. (c) Shall retain SUP record for at least five (5) years. 3) Material Services Section: (a) Perform proper handling per Material Management process in IQ MOVE for SUP Handling. Acceptable Aviation Authority Airworthiness Forms (Certificate of Release to Service for Components) A. Airworthiness Approval Tag or CAAP Form 1 (1) Used to certify airworthiness of a product after performance of maintenance, rebuilding or alteration by an approved CAR Part 6 Maintenance Organization. B. Authorized Release Certificate or EASA/JAA Form 1 (1) Used to certify the airworthiness of the product after performance of maintenance, rebuilding or alteration by an approved EASA 145 Maintenance Organization. C. Airworthiness Approval Tag or FAA Form 8130-3 (1) Used to certify airworthiness of a product after performance of maintenance, rebuilding oralteration by an approved 14 CFR Part 145 Repair Station. Certification of Return to Service A. A Certificate of Return to Service shall be issued for the following: (1) Before flight at the completion of any package of maintenance scheduled by the operator’s approved aircraft maintenance program on the aircraft, whenever such maintenance took place as base or line maintenance. (2) Before flight at the completion of any defect rectification, while the aircraft operates between scheduled maintenance. (3) At the completion of any maintenance on an aircraft component when off the aircraft, in accordance with the CAAP approved maintenance capability. B. Only personnel with Return to Service authorization shall return an aircraft and/or article to service after proper completion of the required maintenance and inspections of the aircraft or aeronautical product. C. These persons must meet the qualification requirements set forth under Certifying Staff Qualification, Chapter 5-2 of this manual. D. A decision of such personnel not to return an aircraft or aeronautical product to service can only be overruled by a hierarchically higher staff of the Production Quality Inspection Division if this individual is also properly qualified, licensed and authorized as above. Such person shall sign to clearly accept responsibility for the course of action decided upon. To further ensure that no exposure to unairworthiness resulted from action taken, each overruled item shall be submitted to the Manager Production Quality Inspection Division for further review and concurrence before Return to Service. E. All airworthiness requirements under CAR Part 5, must be satisfied prior to the Return to Service of aircraft, airframe, powerplant, or appliance after maintenance, preventive maintenance, or alteration. F. All personnel with Return to Service authorization shall be responsible for assuring that all maintenance and/or inspection requirements are complied prior to returning an aircraft and/or article to service. Return to Service Authorized Personnel A. The Approved Maintenance Organization personnel executing aircraft return to service shall be conversant with the following: (1) Customer’s General Maintenance Manual/Engineering Procedures manual (2) Customer’s Approved Minimum Equipment List (MEL) (3) Appropriate Aircraft Maintenance Manual (4) Customer’s Maintenance Documentation Procedures (5) Applicable Airworthiness Regulations (6) LTP Maintenance Procedures Manual (7) LTP-Customer Joint Procedures Manual B. Shall have been actively engaged or working on that particular type of aircraft for at least six (6) months within the preceding twenty-four (24) months. C. Shall be in compliance with the current training requirements applicable to Return to Service personnel under the CAAP approved LTP Training Program. Procedure A. The purpose of the aircraft return to service is to certify that all maintenance and/or inspection performed or required to be performed is completed satisfactorily and that no condition known to the signatory exists which would render the aircraft unairworthy. B. The aircraft return to service signified by the authorized personnel signature constitutes a certification of the following: (1) The work was performed to the required standard in accordance with LTP approved procedures and customer work order. (2) All items required to be inspected were inspected and determined to be satisfactorily completed. (3) No known condition exists that would render the aircraft unairworthy. (4) The documentation has been completed and correctly certified. (5) As far as the work performed is concerned, the aircraft is in condition for safe operation. Acceptable Certificates of Return to Service A. For RP-registered aircraft: (1) Certification of Return to Service shall be done in accordance with CAAP approved Maintenance Procedures Manual using Approved Maintenance Organization Certificate No. 40-00. (2) The Return to Service certification shall be in accordance with operator requirements stipulated in the operator General Maintenance Manual (GMM) or equivalent. B. Certification of Return to Service shall be executed by LTP and/or customer authorized personnel by entries in the Aircraft Maintenance Logbook, with the following information: (1) Make, model, registration number and serial number or as required by customer documentation procedures. (2) Description of the work performed or work order, as required by customer documentation procedures. (3) The following written Approved for Return to Service statement, if not prescribed otherwise by the customer’s manual: “The aircraft identified was repaired and inspected in accordance with the current maintenance rules of the CAAP Civil Aviation Regulations, was determined to be airworthy, and is approved for return to service. Pertinent details of the work carried out are on file at this Approved Maintenance Organization under Work Order No. xxx” (4) Approved Maintenance Organization Certificate No. 40-00. (5) The date (6) Full signature, ID number of the authorized person. C. At the completion of a base maintenance package, a Certificate of Return to Service {Form No. F39-008L (CAAP)} shall be issued by a duly authorized Inspector. This is in addition to the certification of return to service executed in the operator’s Aircraft Maintenance Logbook. D. Items requiring maintenance action on enroute station shall require an aircraft maintenance logbook entry of corrective action made and sign-off by personnel, who performed the corrective action indicating time, date and station where the work was accomplished. E. Personnel appropriately authorized to issue Return to Service and rated for such type of aircraft can defer the correction of discrepancy in accordance with the operator’s Minimum Equipment List (MEL) and the customer’s deferred maintenance procedure. F. All work should be carried out in accordance with the customer’s maintenance program. Maintenance, Preventive Maintenance or Alteration RII - Required Inspection Item, a designation of the items of maintenance and alteration that must be inspected (required inspections), including at least those that could result in a failure, malfunction, or defect endangering the safe operation of the aircraft, if not performed properly or if improper parts or materials are used. The term RII may be interchanged with Duplicate Inspection and Independent Inspection. Required Inspection Item Sign-Off A. RII’s are indicated in the customer maintenance forms (maintenance task card, inspection writeup forms and check sheets) by providing inspection sign-off block or column. An authorized personnel stamp or signature and ID number signifies accomplishment of required inspection. Line Maintenance A. LTP as an Approved Maintenance Organization is approved to perform line maintenance for air carriers conducting operations under CAAP regulations and other customers approved programs on any aircraft for which LTP is authorized as described in the Scope of Work (Chapter 2-3) and the corresponding Approved Maintenance Organization Certificate and Operations Specifications issued to LTP. B. The Vice President - Aircraft Maintenance shall ensure that: (1) The necessary equipment, trained personnel, and technical data to perform line maintenance are available. (2) The Scope of Work is in accordance with LTP’s Approved Maintenance Organization Operations Specifications and limitations. (3) Work is performed in accordance with the customer inspection and documentation requirements as detailed in the customer manual. (4) Work shall be performed in accordance with the customer’s approved maintenance program. (5) All line maintenance shall be performed by authorized and certified personnel in compliance with LTP procedures and/or with the customer’s instructions/procedures or customer manual. (6) There is access to hangars during inclement weather such that particular maintenance or inspection tasks can be carried out with undue distraction. Rest and Duty Limitations for Persons Performing Maintenance Functions A. No person may assign, nor shall any person perform maintenance functions for aircraft, unless that person has had a minimum rest period of eight (8) hours prior to beginning of duty. B. No person may schedule a person performing maintenance functions for aircraft for more than twelve (12) consecutive hours of duty. C. In situations involving unscheduled aircraft unserviceability, persons performing maintenance functions for aircraft may be continued on duty for (1) Up to sixteen (16) consecutive hours; or (2) Twenty (20) hours in twenty-four (24) consecutive hours. D. Following unscheduled duty periods, the person performing maintenance functions for aircraft shall have a mandatory rest period of ten (10) hours. E. LTP shall relieve the person performing maintenance functions from all duties for twenty-four (24) consecutive hours during any seven (7) consecutive day period. Airworthiness Directives Procedure Introduction A. Airworthiness Directive (AD) are legally enforceable rules issued by the Aviation Authorities which identifies aeronautical products (aircraft, aircraft engines, propellers and appliances) in which an unsafe condition exists or where condition is likely to exist or develop in other products of the same design. It prescribes corrective actions to be taken or the conditions or limitations under which the products may continue to be operated. B. This subject applies to those customer air carriers that contracted LTP for support or complete Engineering services for their fleet or specific aircraft. Human Factor Safety Learning Experience Training (SLEX) SFAR 88 Electrical Wiring Interconnecting System (EWIS) US-FAA Part 145 EASA Part 145 CAR Part 1 to 9 Proficiency of Authorized Personnel Introduction A. This section describes the procedures for establishing and maintaining the qualification, certification and authorization of inspection and maintenance personnel. Inspection and maintenance personnel must be thoroughly familiar with applicable regulations and inspection methods, techniques, practices, aids, equipment and tools used to determine the airworthiness of the article returned to service. B. Certifying staff shall be in compliance with the following conditions: (1) The person should hold a license issued by the CAAP pursuant to CAR Part 2 and in accordance with ICAO Annex 1; and a certifying staff authorization issued by LTP. (2) The scope of work of the person should not exceed the scope of the rating defined by the national license/certifying staff authorization. (3) Certifying staff should have received training on CAAP Civil Aviation Regulations and are required to be familiar with CAR Parts 4, 5, 6, 7, 8, 9. (4) The person should have received training on human factors. (5) The person should demonstrate five (5) years maintenance experience for line maintenance certifying staff and eight (8) years for base maintenance certifying staff. However, those persons whose authorized tasks permits the holder to issue certificates of return to service following minor scheduled line maintenance and simple defect rectification within the limits of tasks specifically endorsed on the authorization, need to demonstrate three (3) years maintenance experience only. (6) Line maintenance certifying staff and base maintenance support staff should receive type training at a level corresponding to ATA Specification 104 Level 3 for every aircraft on which they are authorized to make certification. However, those personnel whose authorized tasks permits the holder to issue certificates of return to service following minor scheduled line maintenance and simple defect rectification within the limits of tasks specifically endorsed on the authorization, may receive task training in lieu of complete type training. Qualification and Authorization Procedure Application for Authorization A. Certifying and support staffs should be at least twenty-one (21) years old. B. Applications are submitted by maintenance personnel to division heads using Authorization Application Form (F29-008L). This form shall be completed by the applicant and endorsed by the concerned Division Head to QM-A - Internal Authorizations (QM-A1). The following supporting documents shall be made available as applicable: (1) Photocopy of the current CAAP license duly endorsed by the Division Head. (2) Proof of Training (as applicable) (3) Record of Practical Experience (a) Experience must be demonstrated on the specific aircraft/component for which the authorization is being sought, for at least six (6) months preceding the application for authorization. 1. Practical experience may be less than six (6) months provided that the authorization being sought is for a second or additional aircraft type of the same manufacturer and such duration of practical experience is also acceptable to the customer. 2. Practical experience may be demonstrated through a significant number of actual experiences on major aircraft systems. 3. Practical experience may be supplemented by actual experience on aircraft/ component of similar design or manufacturer philosophy. (Example: A320 experience may be supplemented by actual experience on A330 and/or A340). (4) Eye test certificate (as applicable) (5) Weld test certificate (as applicable) Renewal of Authorization A. Personnel applying for renewal of their authorization shall submit to QM-A - Internal Authorizations (QM-A1) the following documents: (1) Duly accomplished Authorization Application Form (F29-008L). (2) Photocopy of the renewed license duly endorsed by the Division Head. (3) Proof of recurrent training (as applicable). (4) Authorized Personnel Log (F11-054L) or other system generated report/document with similar content/information (e.g. TRAX Reported Manhour, Defect Report Print, etc.) detailing the recent work experience; to the effect that such person has been actively engaged or working on relevant aircraft or component maintenance environment for a period of at least six (6) months within the preceding twenty-four (24) months period. @Note: Those who do not meet the recent work experience requirement shall take the applicable refresher/recurrent training to be able to regain their authorization. (5) Eye test certificate (as applicable). (6) Weld test certificate (as applicable). Application for Additional Authorization A. Application shall be made in accordance with Authorization Application Form (F29-008L) along with the following documents: (1) Photocopy of the training certificate relevant to the authorization being applied for if not available in QM-A - Internal Authorizations (QM-A1) file. (2) Record of Practical Experience (a) Experience must be demonstrated on the specific aircraft/component for which the authorization is being sought, for at least six (6) months preceding the application for authorization. 1. Practical experience may be less than six (6) months provided that the authorization being sought is for a second or additional aircraft type of the same manufacturer and such duration of practical experience is also acceptable to the customer. 2. Practical experience may be demonstrated through a significant number of actual experiences on major aircraft systems. 3. Practical experience may be supplemented by actual experience on aircraft/ component of similar design or manufacturer philosophy. (Example: A320 experience may be supplemented by actual experience on A330 and/or A340). Suspended/Removed Authorization A. Once an authorization is suspended due to expired license or required training, QM shall issue a memorandum detailing the reason for suspension of the authorization/s. A revised Authorization Form (F00-062L) if applicable, shall be issued minus the suspended authorization affected by the required training. Upon receipt of the revised Authorization Form (F00-062L), personnel shall surrender the superseded Authorization Form (F00-062L) to the Division Head who shall destroy the old Authorization Form to ensure that it will not be used. B. Re-application for the reinstatement of a suspended or revoked authorization shall be made as follows: (1) Application in accordance with Authorization Application Form (F29-008L). (2) QM-A - Internal Authorizations (QM-A1) verifies compliance with conditions for the reinstatement of the suspended or revoked authorizations. (3) Upon approval, QM-A1 shall update the database and issue the approved/signed authorization. A photocopy of the approved Authorization Form (F00-062L) signed by the holder shall be retained by QM-A1 on the individuals file while the original copy shall be given to the holder. Authorization Validity A. Authorization validity shall be subject to the holder continuing to meet the pre-requisites of the authorization (i.e. recent practical experience, license, training, eye test, NDT or welders test certificate, as applicable, etc.). B. Authorization holder shall: (1) Be responsible for ensuring that recent practical experience requirement is being met and all relevant licenses and pre-requisites for authorizations are current. @Note: (1) Failure to demonstrate practical experience on the specific aircraft/component or process for which the personnel is authorized, for at least six (6) months within the preceding twenty-four (24) months period shall invalidate granted authorizations. (2) Authorization is valid for two (2) years from the date of issuance; with reference to CAAP license validity and/or recurrent training requirement. (3) Revocation or expiration of the relevant licenses shall automatically invalidate all granted authorizations. (2) Submit record of practical experience before renewal of authorization. (3) Immediately report suspension/revocation of their license to QM-A - Internal Authorizations (QM-A1) and Division Head. (4) Be responsible for renewing the relevant license in accordance with the requirements of CAAP CAR Part 2.6.2.13 and Part 2.6.3.12. (5) Submit photocopy of renewed license duly endorsed by the Division Head to QM-A1 immediately after license renewal and apply for renewal of authorizations held. C. Upon confirmation of promotion or transfer of an authorized personnel to another position or office not requiring authorization; (1) Authorization holder shall: (a) Surrender the original copy of authorization and stamp to QM-A1. (b) Cease from further certifying any task, and/or releasing article to service. (2) Immediate superior or Division Head shall inform QM-A1 in writing about the change in position, promotion or transfer of personnel. (3) QM-A1 shall: (a) Destroy the authorization. (b) Update the database to remove the authorization and delete the stamp information. (c) Issue a memorandum letter to concerned division confirming the removal of the authorization and update of database. (d) Safekeep the surrendered stamp. D. In case of long term absences (e.g. personnel on long sick leave/leave of absence) or personnel reassignment where the person no longer exercises the privileges of the authorization on a specific aircraft/component or process: (1) Division Head shall: (a) Monitor personnel whose period of absences (applied leaves, including the covered rest days/holidays) has reached a total of thrity (30) calendar days or more. (b) Inform QM-A1 in writing about the status/details of the person on long sick leave or any long leave of absence. (c) Inform QM-A1 in writing about the status/details of the reassignment of the person concerned. (3) QM-A1 shall: (a) Evaluate the status of the person concerned with reference to recent practical experience requirement. The authorization/s of personnel who are not in compliance with recent practical experience requirement due to long sick leave or reassignment shall be removed. (b) Update the database to remove the affected authorization/s and delete the stamp information, as applicable. (c) Issue a memorandum to HR and the Division concerned confirming the removal of authorization/s. (d) Safe keep the surrendered stamp, as applicable. Display/Inspection of License and Authorization A. Authorized personnel shall keep his/her license and authorization within the immediate area where he/she normally exercise the privileges of the license/authorization and shall present it for inspection upon the request of a person of authority. License Validity Forecast A. QM-A - Internal Authorizations (QM-A1) transmits to applicable Department/Division Heads a monthly license validity forecast, which contains the list of authorized personnel whose licenses are about to expire or have already expired. B. Based on this license forecast, QM-A1 shall remove/suspend the respective authorizations affected by the expired license. Authorization and Skill Types A. Lufthansa Technik Philippines shall distinguish between the following types of authorizations: (1) Return to Service (RTS) - certifies airworthiness of an aircraft after maintenance, alteration, repair, rectification of flight and ground remarks and other maintenance activities. This authorization shall be issued to A&P Mechanics and Aircraft Inspectors only. (3) RTS Support Staff - certifies that all relevant tasks and inspections have been carried out to the required standard before the Return To Service certifying staff issues the Certificate of Return To Service. The sign-off in the “Control Check” box of the maintenance job card constitutes a supporting statement to the final release person. (4) Certification of Maintenance (COM) - certifies that the work specified in the maintenance document was carried out in accordance with the applicable, approved and/or acceptable data/ reference and with respect to the work performed, the aircraft or article is ready for Return to Service. 1) WHAT IS LTP’S CAAP APPROVED MAINTENANCE ORGANIZATION CERTIFICATE NUMBER? ANS: CAAP AMO 40-00 2) WHAT AVIATION AUTHORITY AND APPROVAL NO. IS INDICATED IN THE RELEASE TO SERVICE DOCUMENT OF EUROPEAN REGISTERED CUSTOMER AIRCRAFT (EX. LUFTHANSA, VIRGIN ATLANTIC)? ANS: EASA.145.0098 3) WHERE CAN YOU FIND LTP’S POLICIES/PROCEDURES AS AN APPROVED EASA PART-145 MAINTENANCE ORGANIZATION? (WRITE IN FULL AND IN ABBREVIATION) ANS: MANAGEMENT MANUAL PLUS IQ MOVE 4) WHAT MANUAL DEFINES THE AREA OF RESPONSIBILITY AND THE PROCEDURES TO BE FOLLOWED DURING THE CONTRACTED MAINTENANCE TO BE PERFORMED BY LTP ON CUSTOMER AIRCRAFT? (WRITE IN FULL AND IN ABBREVIATION) ANS: JOINT PROCEDURES MANUAL (JPM) 5) WHAT MANUAL REPRESENTS THE CAAP, US-FAA AND EASA MANDATE FORMS AND LTP REQUIRED CONTROLLED FORMS? ANS: Forms Manual 6) AS A US-FAA AIR AGENCY CERTIFICATE HOLDER, LTP CONDUCTS ITS OPERATION AS A REPAIR STATION IN ACCORDANCE WITH WHAT CODE OF FEDERAL REGULATIONS (CFR)? ANS: 14 CFR PART 145 7) WHERE CAN YOU FIND PRECISE INFORMATION TO PERFORM ADJUSTMENT/TEST OF A SYSTEM COMPONENT OF AN AIRCRAFT SYSTEM? (WRITE IN FULL AND IN ABBREVIATION) ANS: AIRCRAFT MAINTENANCE MANUAL – AMM 8) THE ATA-100 NUMBERING SYSTEM CONSISTS OF A THREE ELEMENT NUMBER SEPERATED BY DASHES; WHAT DOES THE FIRST ELEMENT REPRESENT? ANS: AIRCRAFT SYSTEM 9) IN THE ATA-100 NUMBERING SYSTEM, WHAT IS THE NUMBER DESIGNATED FOR TIME AND LIMITS ANS: ATA 05 10) IN THE ATA-100 NUMBERING SYSTEM, WHAT IS THE PAGE BLOCK DESIGNATED FOR ADJUSTMENT/TEST? ANS: PAGE BLOCK 501-599 11) IN THE AIRCRAFT MAINTENANCE MANUAL, WHERE CAN YOU FIND PRECISEINFORMATION REGARDING ANGLE OF ATTACK VANE HEATING? (WRITE ATA CHAPTER AND TITLE) ANS: ATA 30 – ICE AND RAIN PROTECTION 12) (1)AIRWORTHINESS DIRECTIVES ARE FEDERAL AVIATION REGULATIONS AND MUST BE COMPLIED WITH UNLESS SPECIFIC EXEMPTION IS GRANTED. (2)AIRWORTHINESS DIRECTIVES OF AN EMERGENCY NATURE MAY REQUIRE IMMEDIATE COMPLIANCE UPON RECEIPT. REGARDING THE ABOVE STAEMENTS: A. ONLY NO. 1 IS TRUE B. ONLY NO. 2 IS TRUE C. BOTH NO. 1 AND 2 ARE TRUE 13) WHEN MUST AN AIRWORTHINESS DIRECTIVES (AD) BE COMPLIED WITH AFTER IT BECOMES EFFECTIVE? A. AS SPECIFIED IN THE AD B. DURING THE NEXT SCHEDULED INSPECTION C. AT THE DATE OF EFFECTIVITY 14) LTP CAN RELEASE AN AIRCRAFT ENGINE OR APPLIANCE IN CONTRAVENTION TO THE LIMITING PROVISIONS AND DIRECTIVES OF AN APPLICABLE AD? YES/NO? NO 15) THE REPLACEMENT OF APPLIANCES SUCH AS ELECTRICAL OR RADIO UNITS WITH PARTS SUPPLIED BY THE ORIGINAL MANUFUCTURER IS CONSIDERED AN: A. AIRFRAME MINOR ALTERATION B. AIRFRAME MINOR REPAIR C. APPLIANCE MINOR REPAIR 16) INSTALLATION OR MODIFICATION OF ANY SYSTEM AFFECTING THE STRUCTURAL AIRWORTHINESS, FLIGHT BEHAVIOR OR CONTROL OF THE AIRCRAFT IS CONSIDERED AN: a. AIRFRAME MAJOR REPAIR B.AIRFRAME MAJOR ALTERATION C.AIRFRAME MINOR ALTERATION 17) COMPLEX REPAIR OPERATION ON AN APPLIANCE REQUIRING THE USE OF SKILLED TECHNIQUES AND OR SPECIAL TOOLS AND TEST EQUIPMENT NOT AVAILABLE TO A MECHANIC WORKING OUTSIDE AN APPLIANCE SHOP IS CONSIDERED AN? a. APPLIANCE MAJOR REPAIR b. APPLIANCE MINOR REPAIR c. APPLIANCE MAJOR ALTERATION 18) REPLACEMENT OF BULBS, REFLECTORS AND LENSES OF POSITION AND LANDING LIGHTS IS CONSIDERED AN? APPLIANCE MINOR REPAIR AIRFRAME MINOR REPAIR PREVENTIVE MAINTENANCE 19) CHANGE TO THE BASIC DESIGN OF AN APPLIANCE, MADE IN ACCORDANCE WITH THE CAAP APPROVED RECOMMENDATION OF THE APPLIANCEMANUFUCTURER IS CONSIDERED AS: APPLIANCE MINOR REPAIR APPLIANCE MINOR ALTERATION PREVENTIVE MAINTENANCE 20) TROUBLE SHOOTING AND REPAIR OF BROKEN CIRCUITS IN LANDING LIGHT WIRING CIRCUITS IS CONSIDERED AS: APPLIANCE MINOR REPAIR AIRFRAME MINOR REPAIR PREVENTIVE MAINTENANCE 21) WHERE ARE THE BODY STATIONS USUALLY REFERENCE TO IN A BOEING AIRCRAFT? A. FUSELAGE FRAMES B. SKIN LAP JOINTS C. FUSELAGE PRODUCTION JOINTS 22) WHERE IS FUSELAGE STATION NO. 7662 LOCATED? a. 7662 INCHES FWD OF THE RADOME OR FIXED REFERENCE LINE b. 7662 INCHES AFT OF THE ZERO OR FIXED REFERENCE LINE c. 7662 INCHES AFT OF THE RADOME 23) WING STATIONS ARE USUALLY REFERENCE TO: d. FLAP-SLAT TRACK LOCATIONS e. WING RIBS 24) WHICH OF THE FOLLOWING IS AN INDICATION/APPEARANCE OF CORROSION? a. SURFACE FILMING, ETCHING COMBINED WITH GRAY OR WHITE POWDERY DEPOSITS ON ALUMINUM ALLOY b. GREENISH FILM ON COOPER ALLOY c. BOTH A AND B 25) WHICH OF THE FOLLOWING ARE CAUSES OF CORROSIONS? FINISH DETERIORATION, ENVIRONMENT CONTAMINATION INSULATION BLANKETS, MAINTENANCE PRACTICES ALL OF THE ABOVE 26) IT IS THE RESULT ON A PART OR MATERIAL THAT WAS SUBJECTED TO EXCESSIVE TEMPERATURE EVIDENCED BY CHANGE IN COLOR OR APPEARANCE? A. BURNED B. CARBONED C. OVERHEATED 27) IT IS THE DESTRUCTIVE OXIDATION CAUSED BY HIGHER TEMPERATURE THAN THE PARENT MATERIAL CAN WITHSTAND? a. BURNED B. CARBONED C. OVERHEATED 28) IT IS THE FRICTIONAL WEAR DAMAGE USUALLY CAUSED BY TWO PARTS RUBBING TOGETHER WITH LIMITED MOTION. C. FRAYED A. SCRATCHED B. CHAFFED 29) WHAT INFORMATION IS GIVEN TO A PILOT TO INDICATE THAT ALL OF THE LANDING GEARS ARE DOWN AND LOCKED? ANS: THREE GREEN TRIANGLES 30) SCOOPE TYPE OF DAMAGED CAUSE BY PRESSURE OR IMPACT OF FOD? ANS. GOUGH CAAP CAR PART 2 - PERSONNEL LICENSING CAAP CAR PART 5 – AIRWORTHINESS CAAP CAR PART 6 – APPROVED MAINTENANCE ORGANIZATION ATA CHAPTER 76 - ENGINE CONTROLS LG UP AND LOCKED – NO LIGHTS TXA T’= --------------------A+B T’ – COMPUTED TORQUE T – TORQUE REQUIRED A – LENGTH OF WRENCH B – LENGTH OF EXTENTION 160 LB IN X 1.5 FT 240 LB IN / FT T’= ------------------------ T’= -------------------T’= 120 LB IN 1.5 FT + 0.5 FT 2 FT AD HANDLING (MPM 4-8-1; TS HANDBOOK 3-1-2/3) Airworthiness Directives (AD) are legally enforceable rules issued by the aviation authorities which identifies aeronautical products such as aircraft, aircraft parts and equipments in which an unsafe condition exist or a condition where likely to exist or develop on other products of the same design it prescribes corrective actions to be taken or conditions or limitations, under which the products may continue to be operated. AD may warrant urgent maintenance, inspection or modification in order to ensure that an aircraft type may not encounter potential system or component failures that may lead to tragic incidents. Thus, AD is an approved document by the authority governing the registry of an aircraft. Authorities may identify manufacturer’s service bulletin and other source data, or develop and prescribe inspection, procedure and limitations in the form of an AD for mandatory compliance pertaining to the aircraft that they oversee. Airworthiness Directives are being handled by TS1 to provide service to customers or air carriers who have Technical Service Agreement or any technical contract with LTP. The customer is responsible for the AD control, to conduct an initial review to determine if the AD is potentially applicable to their aircraft or its component. LTP shall assist as per customer request in detailed review of an AD to determine its applicability. If so, TS1 shall determine the action required and issue the appropriate engineering paper work. Compliance with an AD is mandatory. The records of accomplishment covering the AD shall be retained by LTP while the aircraft is under LTP’s responsibility. QUALIFICATION REQUIREMENTS AND SIGNATORY RESPONSIBILITIES OF LTP PERSONNEL EXECUTING AIRCRAFT MAINTENANCE RELEASE 1.) LTP personnel executing aircraft maintenance release shall be conversant and well knowledgeable with the following: a.) Customer’s General Maintenance Manual (GMM) & Engineering Procedures Manual (EPM) b.) Customer’s Approved Minimum Equipment List (MEL) c.) Customer’s Maintenance Document Procedures d.) Appropriate Aircraft Maintenance Manual (AMM) e.) Applicable Airworthiness Regulations f.) LTP-Customer Joint Procedures Manual (JPM) g.) LTP CAAP Maintenance Procedures Manual, US-FAA and EASA Management Manual plus IQ MOVE 2.) Shall have been actively engaged or working on that particular type of aircraft for at least six (6) months within the preceding twenty-four (24) months. 3.) Shall be in compliance with the current training requirements applicable to Return to Service personnel under the US-FAA Repair Station Training Program Manual, or CAAP approved LTP training program, or EASA approved LTP training program depending on the aircraft registry being maintained. Personnel executing aircraft maintenance release should have the major responsibility and ensure that the work was performed to the required standard in accordance with LTP approved procedures and customer work order; that all items required to be inspected were inspected and determined to be satisfactorily completed; that no known condition exists that would render the aircraft un-airworthy; the documentation has been completed and correctly certified; most importantly, that the aircraft is in condition for safe operation. DOCUMENTATION AND PROCEDURE OF RTS FOR CUSTOMER AIRCRAFT Lufthansa Technik Philippines as a qualified repair station or approved maintenance organization with its authorized personnel certifies Return to Service in accordance with: CAAP, Maintenance Procedure Manual (MPM) using Approved Maintenance Organization certificate number 40-00 for RP registered aircraft US-FAA, Management Manual plus IQ MOVE using Air Agency certificate number LOTY566Y for US registered aircraft EASA, Management Manual plus IQ MOVE using Maintenance Organizaton certificate number DE.145.0001 (EASA.145.0098) for European or EU member state registered aircraft Certification of Return to Service shall be done in accordance with the operator requirements General Maintenance Manual (GMM), Engineering Procedure Manual, or equivalent. Certification of Return to Service shall be executed by LTP and/or Customer Authorized Personnel by entries in Aircraft Maintenance Logbook with the following information: 1. Aircraft Make, Model, Registration Number, and Serial Number or as Required by the Customer Documentation Procedures 2. Descriptions of Work Performed or Work Order or as required by Customer Documentation Procedures 3. The following written approved for Return to Service statement, if not prescribed by customer manual 4. The Approved Certificate Number, for CAAP 40-00, for US-FAA LOTY566Y, for EASA DE.145.0001 (EASA.145.0098) 5. The Date and Time 6. Full Signature and ID Number of Authorized Personnel Any items requiring maintenance action on enroute station shall require an Aircraft Maintenance Logbook entry of corrective action made and Sign-off by person who performed the corrective action indicate the Date, Time, and Station where the work was accomplished. Personnel appropriately authorized to issue Return to Service and rated for such type of aircraft can defer the correction of discripancy in accordance with the Operator’s Minimum Equipment List (MEL) and Customer’s Deferred Maintenance Procedure. REQUIREMENTS AND RESPONSIBILITIES FOR CONTINUATION VALIDITY OF LTP ISSUED AUTHORIZATION For an LTP authorized personnel maintaining authorization validity shall be subjected to meet the prerequisites of the authorization such as being responsible for ensuring that all relevant licenses and prerequisites for authorizations are current. And that no revoked or expired license be present that shall automatically invalidate all granted authorizations. He/she must immediately report suspended/revoked license to QM1 and corresponding Division Head, and also must be responsible for renewing his/her relevant license in accordance with the requirements of CAAP CAR Part 2.6.2.13 and Part 2.6.3.12. After renewing he/she must submit a photocopy of the renewed license duly endorsed by Division Head to QM1. Another important responsibility of an authorized personnel is keeping his/her license and authorization within immediate area where he/she usually exercise the privileges of the license and authorization and shall present it for inspection within a reasonable time upon request from an authority personnel. In the event of promotion or transfer of an authorized personnel to another position or office not requiring his/her authorization, the holder shall surrender both the authorization and the stamp to his/her immediate superior for further handling and must stop from further certifying any task and/or releasing an aircraft or component to service. The immediate superior shall destroy the authorization and submit the stamp to QM1 with the information in writing regarding the change in position or transfer of the personnel and recommend an update of the database for the removal of the authorization. SUP? DETECTION AND REPORTING SUP Suspected Unapproved Parts (SUP) may be defined as aircraft article or a part of an aircraft article that was not manufactured or maintained in accordance with approved procedures specified in aviation regulations such as 14 CFR Part 21, CAR Part 5, EASA Part 21, EASA Part 145 or that does not conform to an approved type design of certain standards, or has a missing, or altered or incomplete certification or delivery documentation. Detection: SUP may be brought into circulation with invalid or forged certificates of return to service histories or accompanying papers and incorrect labels and packaging. They may be discovered installed on aircraft during maintenance and inspection. Genuine and counterfeit parts frequently differ only in the material or production method used. They can be found or detected at any phase of inspection from goods receiving through installation or removal on aircraft. The following indicators suggest that a part may be unapproved part: Modified or unusual finish; Part is of different color; Missing data plate or unusual presentation, particularly tampered/altered part number/serial number; Part/serial number engraved in an unusual place; Generally distinctive and unusual appearance of the part. They have distinctive packaging and documentation such as incorrect, incomplete or missing documentation; modified, smudged, overwritten or over-stamped entries, particularly the date, PN or SN; the packaging looks different, example: not the original box; the use of simpler packaging like missing protective sleeves; and there is slight modification of the company logo. And also there are distinctive features from the suppliers such as the price of a part is significantly lower than the price asked by other suppliers; delivery time for a part that is not currently in the warehouse is significantly shorter than with other suppliers; supplier gives the impression that he can obtain any part in any quantity; the supplier is unable to immediately supply all the requested accompanying documents particularly the certificate of return to service, and unusual or distinctive financial procedures. Reporting/Handling: Any available information about SUP from the authorities, manufacturing organizations, customers should be passed to the Quality Management Department which will, if necessary, conduct an investigation to establish if LTP or vendor has used the affected parts. Upon discovery of a SUP, the user should provide the unit with SUP identification label/tape and immediately report to QM Department, and r