M7A - Maintenance Practices Safety Precautions 2024 PDF
Document Details
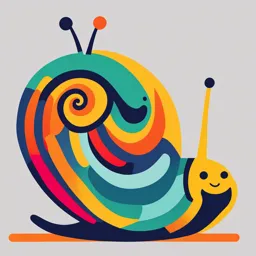
Uploaded by ElatedCrocus
BAS Aircraft Engineering Training Centre (BAETC)
2024
Tags
Summary
This document details safety precautions for aircraft and workshop environments. It covers general safety procedures, material safety data sheets, and precautions for working with various materials including fuels and compressed gases. It emphasizes the need for careful adherence to procedures.
Full Transcript
M7A- MAINTENANCE PRACTICES Knowledge Level requirement for this chapter LEVEL 3 A detailed knowledge of the theoretical and practical aspects of the subject and the capacity to combine and apply the separate elements of knowledge in a logical and comprehensive manner. Objectives: Demonstrate a det...
M7A- MAINTENANCE PRACTICES Knowledge Level requirement for this chapter LEVEL 3 A detailed knowledge of the theoretical and practical aspects of the subject and the capacity to combine and apply the separate elements of knowledge in a logical and comprehensive manner. Objectives: Demonstrate a detailed knowledge of the theoretical and practical aspects with the capacity to combine and apply elements of knowledge in a logical and comprehensive manner so that the trainee is able to: Know the theory of the subject and interrelationships with other subjects. Give a detailed description of the subject using theoretical fundamentals and specific examples. Use mathematical formulae related to the subject. Read, understand and prepare sketches, simple drawings and schematics describing the subject. Apply his knowledge in a practical manner using manufacturer's instructions. Interpret results from various sources and measurements and apply corrective action where appropriate. SAFETY PRECAUTIONS-AIRCRAFT AND WORKSHOP 1-1 Issue 10, January 2024 M7A- MAINTENANCE PRACTICES Chapter 7-1 CONTENTS 7-1. SAFETY PRECAUTIONS - AIRCRAFT AND WORKSHOP...................................................................3 GENERAL SAFETY PRECAUTIONS..........................................................................................................................3 MATERIAL SAFETY DATA SHEETS...........................................................................................................................5 Container Labelling..............................................................................................................................................6 WORKPLACE NOTICES..........................................................................................................................................8 Precautions when Working with Electricity......................................................................................................10 Precautions when Working with Compressed Gases.....................................................................................12 Precautions when working with Oils, Chemicals and Compounds..............................................................14 Precautions when working with Aircraft Fuel...................................................................................................15 Precautions when working on Aircraft Engine................................................................................................17 Engine Running...................................................................................................................................................18 FUEL TANK SAFETY...............................................................................................................................................20 Fuel Tank Precautions and Entry Procedures..................................................................................................41 BALLISTIC RECOVERY SYSTEMS...........................................................................................................................46 FIRE.......................................................................................................................................................................56 Types of Fires.......................................................................................................................................................57 Fire Extinguishers................................................................................................................................................57 Types of Fire Extinguishers and Colour Coding...............................................................................................59 AIRCRAFT HAND-HELD FIRE EXTINGUISHERS.....................................................................................................63 General...............................................................................................................................................................63 Fire Extinguisher Use...........................................................................................................................................63 Portable Facility Fire Extinguisher Inspection..................................................................................................64 Instruction on Handling a Fire...........................................................................................................................65 SAFETY PRECAUTIONS-AIRCRAFT AND WORKSHOP 1-2 Issue 10, January 2024 M7A- MAINTENANCE PRACTICES 7-1. SAFETY PRECAUTIONS - AIRCRAFT AND WORKSHOP GENERAL SAFETY PRECAUTIONS This book deals with safety in the workplace. The subject is, of course, part of the technical content of your normal trade knowledge - so to that extent should be revision, or reinforcement, when you come to study those areas. The Civil Aviation Authority, your company and your workmates will expect you to work on an aircraft/ aircraft equipment in complete safety - safety for you - safety for others - safety for the passengers - safety [or the aircraft. With the ever-rapid change in technology, aircraft, their systems and their maintenance procedures are getting more complex, more difficult to understand and more difficult to realise the possible dangers and safety implications involved when working on them. Only by careful thought, strict observance of procedures, and the reading, understanding, and implementation of the maintenance and safety procedures, as laid down by the CM, national safety organisations, your company and manufacturer's manuals will a high level of safety be achieved. It is an attitude of mind - being alert - being aware - having the knowledge - being careful - keeping abreast of modern developments. When dealing with a particular system/component/procedure you should understand the safety aspects that apply to that task. You should be aware of the safety aspects as they might affect you as well as others around you. As far as the management hierarchy structure of the organisation you work for is concerned, you should be aware of any safety implications that might affect hose people beneath you as well as those above you. Supervisors/managers should ensure that all the appropriate precautions are understood and observed by all those that are in their charge. Organisations should have procedures to ensure safe working conditions and should monitor the performance of the organisation in terms of the safety record. The sale working aircraft maintenance environment is a function of: Aircraft design. The maintenance environment. The individual - his/her training, ability, awareness. The maintenance organisation - awareness - commitment - costs - the law - CAA requirements. If all or these are working in harmony towards safe operations then the risks to maintenance personnel and others are considerably reduced, The intention of this book is to give general safety procedures, For more specific procedures you are asked to refer to: a) The manuals produced by the manufacturer (AMM, SRM etc.), b) Company regulations. c) Regulations produced by national authorities such as the CAA. d) Various laws concerning safety and health in the work place. e) The appropriate book/s in this series dealing with specific engineering tasks, SAFETY PRECAUTIONS-AIRCRAFT AND WORKSHOP 1-3 Issue 10, January 2024 M7A- MAINTENANCE PRACTICES 1. Never carry matches, lighters, or other sources of ignition when at work. 2. Never operate electronic equipment such as mobile phones near aircraft. Only electronic/ electrical equipment, which is approved for maintenance purposes, is to be used near or on an aircraft during maintenance. 3. Never carry "loose articles" - keys, trinkets etc. onto an aircraft, i.e. those that are not connected with the maintenance task in-hand or required for personal reasons. 4. Wear correct clothing, have short hair (or use a hair net), Do not wear rings on fingers, ears, or other parts of the body (ideally), and use non-sparking footwear (no metal studs in the soles). 5. Use barrier cream on hands (and any other parts of the body that might come in contact with oils, greases etc.). 6. As far as possible always avoid contact with any fluids. Also, try to avoid breathing in any of their fumes/odours. Immediately wash off any fluids that get on the skin with soap and water -- and if the liquid is a skin irritant seek medical advice, if splashed in the eyes, rinse with copious amounts of water - or preferably use an eye bath and seek medical advice. 7. Use special safety clothing where necessary - in fuel tanks for example. 8. Keep a close check on tools and other equipment. Ensure that all tools and equipment are accounted for at the end of the day's work/at the end of the shift. 9. Keep all work areas clean - inside and outside the aircraft, taxiways etc., Use a vacuum cleaner for small debris such as swarf, rivet mandrels, bits of cable etc. 10. Read and understand all safety notices - in the AMM; on notice boards, and publications such as Airworthiness Notices. Maintenance manuals are full of them. They can be boring but they should be read. 11. Never work on aircraft or aircraft equipment if unfit through drugs or drink or general condition, e.g. extreme tiredness. 12. Never carry out a task that you are unsure of, and/or unqualified to do. 13. Never carry out a task unless all the right equipment/manuals/ paperwork is available. 14. If in doubt, don’t stop work and seek assistance. Check with the manuals - the chief engineer - the manufacturer if necessary. The information is there somewhere. 15. Never run (always walk) in maintenance areas. Never "play the fool" - of course. SAFETY PRECAUTIONS-AIRCRAFT AND WORKSHOP 1-4 Issue 10, January 2024 M7A- MAINTENANCE PRACTICES MATERIAL SAFETY DATA SHEETS COSHH regulations require an employer to have copies of relevant Material Safety Data Sheets that are readily available to all shop personnel at all times. These data sheets allow for quick reference in case of a chemical spill or injury. In the case of a chemical injury, a copy of the pertinent data sheet(s) should be sent along to the emergency room to ensure immediate medical attention. A Material Safety Data Sheet consists of nine basic sections: 1. Product identification including trade name, and the address and emergency phone number of the manufacturer/supplier. 2. Principal ingredients including percentages of mixture by weight. 3. Physical data describing the substances appearance, odour, and specific technical information such as boiling point, vapour pressure, solubility, etc. 4. Fire and explosion hazard potential. 5. Reactivity data including stability and incompatibility with other substances. 6. First aid and health hazard data. 7. Ventilation and personal protection gloves, goggles, respirator. etc. 8. Storage and handling precautions. 9. Spill, leak, and disposal procedures. Figure 1-1 - Material Safety Data Sheets (MSDS) provide information on hazardous materials that are present in the workplace. Furthermore, all employers must maintain current copies of the Material Safety Data Sheets for reference at any time. SAFETY PRECAUTIONS-AIRCRAFT AND WORKSHOP 1-5 Issue 10, January 2024 M7A- MAINTENANCE PRACTICES Container Labelling Chemical hazard labels vary in size, style, and the amount of information they convey. However, all hazardous materials utilize the same colour coding and hazard indexing information. A typical hazard label consists of four colour-coded diamonds arranged into one large diamond. The colours used in the table are red, blue, yellow, and white. Within three of the coloured areas a number from zero to four appears. The label area coloured red indicates a materials flammability hazard. A zero indicates materials that are normally stable and that do not burn unless heated. A rating of four, however, applies to highly combustible gases and volatile liquids with flash points below 73°F and boiling points below 100°F. The blue area of the label rates a substances health hazard from no significant risk (0), to life threatening or permanently damaging with single or repeated exposures (4). The yellow area of the label rates a substances reactivity. A zero rating applies to materials which are normally stable, even under fire conditions, and which do not react with water. On the other hand, materials rated at four are readily capable of detonation or explosive decomposition at normal temperatures and pressures. The white diamond, appearing at the bottom of the label, conveys Special Hazard information. This information is conveyed by use of symbols that represent the special hazard. Some of the common symbols are shown here: W denotes the material is water reactive. OX denotes an oxidizing agent. COR denotes a corrosive hazard. ALK denotes an Alkali hazard. ACID denotes an Acid hazard. ( ) denotes a radiation hazard. It should also be attached with suitable label indicating the protective equipment needed when handling these materials. SAFETY PRECAUTIONS-AIRCRAFT AND WORKSHOP 1-6 Issue 10, January 2024 M7A- MAINTENANCE PRACTICES Figure 1-2 - Container Label Guide SAFETY PRECAUTIONS-AIRCRAFT AND WORKSHOP 1-7 Issue 10, January 2024 M7A- MAINTENANCE PRACTICES WORKPLACE NOTICES These are coloured notices designed to inform / warn of possible dangers that might exist in the workplace /people area. In the UK (and many other countries). It is mandatory to display them predominantly in the appropriate area / next to the equipment concerned. They: Are standardised across Europe. Use standard colours. Use symbols that allow them to be understood irrespective of language. Keep printed words (where they have to he used) down to a minimum - in the national language where they are displayed. May be printed in "day-glow" colours. Are standard sizes. They must be displayed in areas, next to machinery/equipment where there is a need to inform, worn or otherwise make known some information that would help in the present or any possible future safety or emergency situation. They should he placed in such a position as to be readily seen by the average person, and if required must be repeated as often as necessary. For example - emergency escape notices must be positioned whenever and change in escape direction is needed (at the top of staircases, at each and every exit door etc.) and repeated regularly along long corridors. Display areas include: Workshops Hangars Stores Ramp areas / aircraft movement areas Associated work areas Fuel storage areas Gas storage areas Rest rooms Offices Cargo areas Passenger areas Vehicle areas In fact any area where people are likely to be and there is a need to inform / warn. Each notice will have a predominant colour: Prohibition signs and fire notices. Shows the symbol of the item concerned Red in black behind a red “prohibition” symbol. The background colour is white. Safety, first aid and escape routes. Symbols such as a white cross (first aid) Green or a (green) man running in a white background (escape route) are used. Yellow Warning signs. Blue Hazard signs. SAFETY PRECAUTIONS-AIRCRAFT AND WORKSHOP 1-8 Issue 10, January 2024 M7A- MAINTENANCE PRACTICES Figure 1-3 - Prohibition signs – Examples (Red) Figure 1-4 - Safety and First Aid notices – Examples (Green) Figure 1-5 - Fire notices – Examples (Red) Figure 1-6 - Warning Notices – Examples (Yellow) Figure 1-7 - Hazard Signs – Examples (Blue) SAFETY PRECAUTIONS-AIRCRAFT AND WORKSHOP 1-9 Issue 10, January 2024 M7A- MAINTENANCE PRACTICES Precautions when Working with Electricity Remember it is the current that kills and any dampness or moisture that is present while working on live equipment will allow the current to flow faster. If someone is electrocuted: Switch off the current/ separate the person from the supply as soon as possible. If the current cannot be switched off quickly then, using a non-conductor (e.g. a broom handle) move the person from the live conductor. Call for help. Check the person is breathing. If he/ she is, then check for signs of injury and treat. Keep warm and comfortable. Get medical assistance. If the person is not breathing ensure that the tongue is clear of the airway, loosen collar and tie, and any tight clothing. Apply mouth-to-mouth resuscitation with the patient on his /her back. Check for pulse; if not then apply heart massage with the palm of the hand on the centre of the chest. Call for medical assistance. Do not stop treatment until told to do so by a medically qualified person. Once normal breathing commences check for any injuries and treat. When working on aircraft electrical systems always ensure: All unnecessary equipment switched off. The fuse/CB is "pulled" and "tagged" on any circuit that is to be worked on. After work on a circuit always, check thoroughly before applying power. In particular, check that switches/selectors are set to the position of the services they relate to - otherwise they may move when power is put on. Always consult the manual for any special safety precautions before commencing work. Make sure that cables are in good condition, routed, and supported as per the manual. Make sure that correct fuses/CBs are fitted. Make sure that no refuelling/de-fuelling etc. is being carried out. SAFETY PRECAUTIONS-AIRCRAFT AND WORKSHOP 1-10 Issue 10, January 2024 M7A- MAINTENANCE PRACTICES Working with electrically operated tools/equipment. Try to avoid working with electrical operated equipment on aircraft. Wherever possible use air operated equipment. When using torches etc., they should be of the safety type. Electrical cables should not be allowed to run over sharp edges, through oil, fuel, or water on the ground and not near moving machinery. All equipment should be earthed via a suitable plug or be of the double insulated type. Never work with electrically operated equipment with wet hands or feet in wet or on damp patches. Ensure that cables are secure, undamaged and the correct fuse is fitted in the plug. Never use electrical equipment in hazardous areas such as fuel tanks unless the equipment is specially designed for the job and is approved. If the equipment smells, performs poorly, Arcs more than normal return to the tool store for investigation and repair. Check that equipment has current serviceable label fitted. SAFETY PRECAUTIONS-AIRCRAFT AND WORKSHOP 1-11 Issue 10, January 2024 M7A- MAINTENANCE PRACTICES Precautions when Working with Compressed Gases Compressed gases are "explosive" in nature in that, should a gas-pressurised container fail, it will disintegrate violently. (Should a liquid filled pressurized container fail it may not disintegrate at all, but allow a small amount of high-pressure fluid to escape - probably at high speed - with possible little or no injury to anyone. Though if you are in the path of this jet of fluid serious injury can occur). All compressed gas bottles (fitted to the aircraft or used as storage bottles or transportation bottles) are lifted and should be within the test date. Return to the supplier, suitably labelled and documented, any that are not. Charging During charging, the gas pressure should be charged (or released) slowly. All connections should be tight, and bottles, charging equipment, and gauges should be labelled and within test date. If charging a system with more than one gauge and the gauges should be reading the same and are not - stop charging. Check the reasons why - rectify and continue charging. Never charge to pressures greater than the maximum specified. Always keep blanks on connections when not in use. If the gas is contaminated (with water, oil etc.) then return bottle to supplier - suitable labelled and documented. If the contamination has into the aircraft system/component then purge system/change component. Never mix gases - unless specified, e.g. charge a shock absorber with air when nitrogen is specified. Never direct a jet of high-pressure gas at the skin - it can cause serious injury. Oxygen When charging/carrying out work on oxygen equipment the following precautions should be taken: 1. Provide correct firefighting equipment. 2. Display "No Smoking" signs. 3. If artificial lighting required use explosion proof lamps and hand torches. They should meet local safety specifications - in the UK, British Standards 229 and 889, 4. All electrical equipment / electronic equipment in the vicinity should be OFF unless essential for the task in hand. 5. Ensure all equipment including the aircraft is earthed. 6. Ensure adequate ventilation to prevent the build-up of oxygen in the atmosphere. 7. All equipment such as adapters, gauges, connections, benches, tools etc. should be clean and dry. If threads are to be lubricated then the correct specified lubricant / tape should be used, e.g. Teflon sealing tape to MIL SPEC T-27730. WARNING. The use of greases and oils on high-pressure oxygen connections can cause explosions. SAFETY PRECAUTIONS-AIRCRAFT AND WORKSHOP 1-12 Issue 10, January 2024 M7A- MAINTENANCE PRACTICES 8. Avoid smoking/getting near naked flames after working in an oxygen rich atmosphere (oxygen bay) as clothing will be oxygen rich and will combust readily. 9. After removing blanks, inspect connections carefully for cleanliness. 10. All valves should be opened and closed slowly. 11. Leak test using only the approved solution. Wipe dry after use. 12. If soldering is involved then only specified materials are used -particularly fluxes. Clean all soldered parts thoroughly. Toxic Gases Some gases are toxic (i.e. harmful if swallowed or inhaled, and in some cases if allowed to come in contact with the skin). These bottles will be suitably labelled. If a toxic gas is breathed-in, the person should immediately get into the fresh air and seek medical advice. SAFETY PRECAUTIONS-AIRCRAFT AND WORKSHOP 1-13 Issue 10, January 2024 M7A- MAINTENANCE PRACTICES Precautions when working with Oils, Chemicals and Compounds A wide range of non-metallic materials is used for the maintenance, repair and overhaul of aircraft, They include: compounds, greases, oils, detergents, fillers, jointing compounds, cleaning agents, pre-treatments, anti-corrosive agents, paints, paint strippers, fuels, fuel additives, hydraulic fluids , anti-ice fluids, lacquers, adhesive tapes, bonding adhesives, disinfectants, storage preservatives, alkalise, acids, powders, etc. The AMM for each aircraft type will have a comprehensive list of these "consumables". This is published in chapter 20-31-00. It is important that you consult this chapter before using any compounds from oils to paints, to greases and speed tapes. The AMM will list all the compounds that can be used on the aircraft, with their specifications. It will state the safety precautions to be observed when using them - read them - understand them - obey them. Some consumables are relatively harmless - e.g. some of the earlier hydraulic fluids. Some can cause serious problems - battery electrolyte and paint strippers for example. Even the “harmless ones" can cause dermatitis and other skin complaints so it a good idea to avoid contact with all solutions, oils, fuels, greases, compounds and powders, Always, of course, use barrier creams. For the more harmful materials, always wear protective clothing to the body and eyes. Always use barrier creams, and if the fumes are toxic then use in well-ventilated areas or in workshops that have special extractor equipment available. Always read the safety notices on the containers and follow the usage instructions carefully. If splashed, wipe-off solution immediately and remove contaminated clothing. Irrigate any part of the body affected with copious amounts of water (put under a running tap). The same applies if solution gets into the eyes (a special eyewash should be available). Obtain medical treatment as soon as possible. If overcome by fumes get into the fresh air and seek medical help. If any solution is swallowed then do not try to make the patient sick but obtain medical treatment as soon as possible. Tell the medic exactly what the patient has swallowed. WARNING: Some engine and hydraulic oils contain organo-phosphates (OPs). Exposure to these can be dangerous. Always avoid contact with the skin, eyes etc. Avoid breathing the fumes. (Organo-phosphates are used in sheep deeps and many farmers have had serious chronic health problems after working with these fluids. Currently there is at least one case of a pilot attributing his illness to organic- phosphate exposure due to engine oil fumes in the flight-deck.) SAFETY PRECAUTIONS-AIRCRAFT AND WORKSHOP 1-14 Issue 10, January 2024 M7A- MAINTENANCE PRACTICES Precautions when working with Aircraft Fuel 1. Carried out in a fuelling zone (minimum 20ft [6m] radius cleared specified area). 2. No smoking, naked lights or unauthorised electrical equipment operation allowed. 3. NO SMOKING signs displayed 50ft (15m) from outermost tank vent or refuelling point. 4. If APUs (Auxiliary Power Units) have to run, they should be started before fuelling commences. 5. GPUs (Ground Power Units) should be located as far away as possible and not started or stopped during fuelling. Each unit should be cleared to run in fuelling zones. (Sometimes called Ground Carts.) 6. Correct fire extinguishers should be available. 7. Check under the aircraft for adequate clearance between it and equipment as the aircraft will settle during fuelling. 8. Aircraft engines should not be running - though with some (helicopter) operations this is permissible. 9. All vehicles should have cleat entrance and exit paths. 10. Only "safety" portable electrical equipment to be used - torches etc. 11. All combustion heaters are OFF (aircraft and external heaters). 12. Only authorised personnel allowed in the fuelling zone. 13. No fuelling within 100ft (30m) of operating ground radar equipment. 14. No fuelling during electrical storms. 15. If any part or the aircraft is over-hot (brakes, engines etc.) do not carry out fuelling operations. 16. No flash photography within 20ft (6m) of filling or venting points. Do not use mobile phones or other personal electronic/electrical equipment. 17. Refer to AMM for specific safety precautions. 18. Carry out electrical bonding e.g., hose to aircraft, aircraft to ground (check nose wheel tyre), tanker or pumping unit to ground, tanker or pumping unit to aircraft. 19. Check pressure relief valves (pressure refuelling) for correct operation. 20. Avoid over filling and spillage. Dealing with Fuel Spillage Clear-up all fuel on the aircraft and on the ground. If a major spillage occurs, evacuate all personnel, try to stop the fuel flow, and call the fire services. Do not start aircraft engines or vehicles until all fuel bas been cleared. If the aircraft is moveable, move it away from the area. Remove fuel from tyres and all other parts of the aircraft immediately. (It will quickly deteriorate rubber). Do not allow fuel into drains, waterways etc. If this does occur, inform the local water authority SAFETY PRECAUTIONS-AIRCRAFT AND WORKSHOP 1-15 Issue 10, January 2024 M7A- MAINTENANCE PRACTICES and follow their advice. Fuel can be mopped up using fuel absorbent agents or emulsion compounds. These should be disposed of in accordance with the local authority regulations. All tools and equipment used to be flameproof and/or spark proof. Work In Fuel Tanks Before work is carried out on fuel tanks they should be drained using the same precautions as when refuelling. They may be defuelled using the same equipment as for refuelling. If fuel flow calibration checks have to be carried out in the hangar, this may require the aircraft on jacks (rigging position). It is advisable to have the fire service standing by, as the aircraft cannot be moved out of the hangar in the event of fire. Tanks will have to be purged if work is to be carried out inside, or if heat or electrical equipment is to be used. If working inside a tank a "kerosene suit" or "wet-suit" should be worn, with remote breathing equipment and communications maintained with a lookout man/woman. Check that the person that is to work inside the tank does not suffer from claustrophobia. If he/ she does then he/ she should not go inside. SAFETY PRECAUTIONS-AIRCRAFT AND WORKSHOP 1-16 Issue 10, January 2024 M7A- MAINTENANCE PRACTICES Precautions when working on Aircraft Engine 1. Always use approved safety electrical equipment. 2. As far as possible try and use non-flammable cleaning fluids, agents, compounds etc. 3. Keep all work areas, aircrafts and hangars clean and free of equipment not in use. 4. All inflammable liquids should be stored in correct containers correctly labelled, in fireproof buildings outside hangars. 5. Special care should be taken to prevent static build-up (when brush doping the aircraft for example). Fit earth bonding leads to aircraft when in hangar. 6. Never allow aircraft lagging/insulation, carpets, upholstery etc. to become contaminated with oil or other fluids. 7. Rectify all leaks immediately - hot air (anti-icing, heater systems, engine tapings for cabin pressurisation etc.) - engine oil - fuel - hydraulic. Make sure that oil, fuel and hydraulic pipes are routed away from heat sources in accordance with the AMM. 8. Keep all aircraft drains and vents clear and all aircraft structure, systems and equipment clean. 9. Ensure the serviceability of the aircraft electrical bonding. 10. Check that there are no gaps through aircraft fireproof bulkheads (between the engine and the rest of the airframe). 11. Ensure that no oil or grease is used on O2 connections. If a lubricant/tape has to be used, use an approved type. 12. Take special precautions with pyrotechnics (squib/cartridge units etc.). Never handle them unnecessarily. Observe all instructions supplied by the manufacturer. Return to the supplier when unserviceable or life expired. 13. Ensure aircraft furnishings are of the approved type. Ashtrays are serviceable (closing lid) and correct hand held fire extinguishers are fitted. 14. Avoid overloading of electrical circuits. Ensure correct fuses/CBs are fitted. Check cable insulation and equipment for contamination and signs of over-heating. Check for adequate ventilation. 15. Check arcing from generators, motors, switches, relays and batteries (when connecting/ disconnecting). 16. Magnesium and titanium swarf should be containerised and removed from the area of the aircraft and/ or hangar. Chemical dry powder extinguishers should be available. 17. Failed engine bearings are a source of heat. Check oil systems for level and contamination - indicating possible bearing failure. SAFETY PRECAUTIONS-AIRCRAFT AND WORKSHOP 1-17 Issue 10, January 2024 M7A- MAINTENANCE PRACTICES Engine Running 1. Always refer to the AMM and safety regulations promulgated by your company and the airfield operator. 2. Have the correct (qualified) starting crew. Ensure they are briefed as to the correct procedure. Use ear protection. Make sure that all starting crew can communicate with each other. 3. Have fire-fighting equipment standing by (CO2). 4. Have look-out men / women to ensure personnel or vehicles do not approach danger zones. 5. Ensure areas in front of, and behind, jet engines are clear of any debris. 6. Stay out of danger zones (laid down in the AMM) - in front of jet engine intakes - behind jet engine exhausts - near propellers. 7. Run engines in the designated area - aircraft into wind. 8. If engine becomes over-primed (piston engines) or fuel is spilt then starting procedure should be cancelled and excess fuel dealt with. 9. If fire occurs during running then follow the procedure laid down in the AMM/aerodrome standard procedures. If CO2, BCF or Mechanical Foam is drawn in to a jet engine then it can be cleared by carrying out an engine run. If Methyl Bromide or Chemical Foam is drawn into the engine it must be stripped down for cleaning and inspection. Methyl Bromide, particularly in its Iiquid form (at temperatures below 4°C), is corrosive. Foams leave a deposit and the chemical foam deposit will need cleaning after strip-down. 10. After a wet start on a jet engine carry out a dry run before trying to start the engine again. SAFETY PRECAUTIONS-AIRCRAFT AND WORKSHOP 1-18 Issue 10, January 2024 M7A- MAINTENANCE PRACTICES Figure 1-8 - Engine intake and exhaust hazard areas SAFETY PRECAUTIONS-AIRCRAFT AND WORKSHOP 1-19 Issue 10, January 2024 M7A- MAINTENANCE PRACTICES FUEL TANK SAFETY Following several aircraft accidents, the influences on fuel tank safety had widely been discussed to establish means by which fuel tank explosions can be prevented in the future. As a result aircraft maintenance personnel had to undergo a Fuel Tank Safety Training as required by FAA/EASA. Mainly influenced is PART 145.A.30 requesting Initial and Continuation Training. Issue Prompting this Action On July 17, 1996, a 25-year old Boeing Model 747–100 series airplane was involved in an in-flight breakup after takeoff from Kennedy International Airport in New York, resulting in 230 fatalities. The accident investigation conducted by the National Transportation Safety Board (NTSB) indicated that the center wing fuel tank exploded due to an unknown ignition source. The NTSB determined that the probable cause of the explosion was ignition of the flammable fuel/air mixture in the center wing fuel tank. Although the ignition source could not be determined with certainty, the NTSB determined that the most likely source was a short circuit outside of the center wing tank that allowed excessive voltage to enter the tank through electrical wiring associated with the fuel quantity indication system (FQIS). The NTSB issued recommendations intended to: Reduce heating of the fuel in the center wing fuel tanks on the existing fleet of transport airplanes, Reduce or eliminate operation with flammable vapors in the fuel tanks of new type certificated airplanes, and Reevaluate the fuel system design and maintenance practices on the fleet of transport airplanes. This accident prompted the FAA to examine the underlying safety issues surrounding fuel tank explosions, the adequacy of the existing regulations, the service history of airplanes certificated to these regulations, and existing maintenance practices relative to the fuel tank system. Service History / Review of Past Accidents Following the 1996 accident, the service history of all types of the transport airplane fleet (including turbofan and turboprop airplanes) over the last 40 years was examined. This study identified and analyzed 17 known instances of accidents related to fuel system (other than those following impact with the ground) of transport aircraft operations worldwide and are summarized in Tables 1 and 2. Table 1-1 is based on Operational Events while Table 1-2 on Refueling & Ground Maintenance Events. These tables are grouped by cause (Lightning, Engine Separation, Refueling, Maintenance, etc.), and categorized by operational phase, ignition source, type of fuel tank involved. The mitigating actions taken subsequent to each event is also summarized. The data sources used were accident and incident reports provided by investigating organizations, regulatory authorities, and original equipment manufacturers’ safety-related databases. From the data, there appears to be a difference in the respective safety levels of wing tanks and center tanks. All the wing tank events had been due to known, external ignition sources (lightning strikes, over-wing fire, refuelling, and maintenance error) - there are no known internal ignition sources in more than 520 million hours of commercial transport fleet operation that resulted in a tank explosion. Corrective actions to prevent recurrence of these wing tank events had been in place for many years, and had demonstrated to be effective. By contrast however, in the three most recent center tank events (the Manila B-737, New York B-747 and Bangkok B- 737) the exact ignition sources had not been identified and are the ones for which the corrective actions had not been proven in subsequent airline service. SAFETY PRECAUTIONS-AIRCRAFT AND WORKSHOP 1-20 Issue 10, January 2024 M7A- MAINTENANCE PRACTICES Over the years, center tanks have accumulated considerably fewer operating hours than wing tanks (for example, a B-737 has two wing tanks and one center tank, and therefore accumulates wing tank hours at twice the rate of center tank hours). Since the equipment in wing and center tanks is very similar, i.e. there are similar types and numbers of potential ignition sources, one would expect there to be significantly fewer center tank events than wing tank events. Actually the numbers of events are equal. This indicates that center tanks are significantly more susceptible to explosion than wing tanks. It might be argued that the reason for this disparity is that components in the wing tanks are more often submerged than those in the center tanks, which often operate almost empty. However, this may be an over-simplification. There are several pieces of equipment inside wing tanks which routinely operate in the vapor space, such as fuel quantity probes and wiring, and partially submerged boost pumps. There is still considerable potential for the existence of ignition sources within the ullage of wing tanks. This being the case, if center tanks are experiencing considerably more explosions than might be expected relative to wing tanks, it must be that center tanks are significantly more flammable than wing tanks. Reducing the flammability in center tanks down to wing tank levels would be a worthwhile goal. In the last 20 years (when Jet A has been the predominant fuel), there have been five tank explosion events involving center/fuselage tanks, and two wing tank events (which were both exceptional ones). The continuing incidence of center tank explosions (all of which involved Jet A fuel) indicates that these tanks have not yet reached the safety level attained by wing tanks, and that action to further reduce the flammability levels in center tanks should be considered. Table 1-3 summarizes the numbers of fatalities and degree of aircraft damage resulting from all these events. The following conclusions can be drawn from the foregoing discussion: There is a close relationship between the incidence of explosions in wing tanks and the use of wide-cut fuel. Wing tanks operating with Jet A type fuel have demonstrated an acceptable safety record. In comparison, center tanks and fuselage-mounted tanks are more vulnerable to explosion in the presence of ignition sources. Apart from the three most recent events, the causes of all the other events have been addressed by actions designed to prevent or minimize their recurrence. The safety level performance of wing tanks has been identified as a target for the technologies applied to center wing tanks and their safety level performance. Fuel Tank Safety Development Since the July 17, 1996, accident, the FAA, NTSB, and aviation industry have been reviewing the design features and service history of the Boeing model 747 and other transport airplane models. Based upon its review, the NTSB had issued recommendations to the FAA (to enhance the already good safety record of aircraft fuel systems worldwide). These recommendations were intended to reduce exposure to operation with flammable vapors in fuel tanks, prevention of ignition sources and addressed possible degradation of the original type certificated fuel tank system designs on transport airplanes. The following recommendations were related to ‘‘Reduced Flammability Exposure’’: A–96–174: Require that significant consideration should be given to the development of airplane design modification, such as nitrogen inerting systems and the addition of insulation between heat-generating equipment and fuel tanks. Appropriate modifications should apply to newly certificated airplanes and, where feasible, to existing airplanes. SAFETY PRECAUTIONS-AIRCRAFT AND WORKSHOP 1-21 Issue 10, January 2024 M7A- MAINTENANCE PRACTICES A–96–175: Require that pending implementation of design modifications, the operational procedures be modified to reduce the potential for explosive fuel-air mixtures in the fuel tanks of transport-category aircraft. In the B–747, consideration should be given to refueling the center wing fuel tank (CWT) before flight whenever possible from cooler ground fuel tanks, proper monitoring and management of the CWT fuel temperature, and maintaining an appropriate minimum fuel quantity in the CWT. ‘‘A–96–176: Require that B–747 Flight Handbooks of TWA and other operators of B–747s and other aircraft in which fuel tank temperature cannot be determined by flight crew be immediately revised to reflect the increases in CWT fuel temperatures found by flight tests, including operational procedures to reduce the potential for exceeding CWT temperature limitations. A–96–177: Require modification of the CWT of B–747 airplanes and the fuel tanks of other airplanes that are located near heat sources to incorporate temperature probes and cockpit fuel tank temperature displays to permit determination of the fuel tank temperatures. The following recommendations were related to ‘‘Ignition Source Reduction’’: A–98–36: Conduct a survey of fuel quantity indication system probes/wires in Boeing Model 747’s equipped with systems other than Honeywell Series 1–3 probes/compensators and in other model airplanes to determine whether potential fuel tank ignition sources exist that is similar to those found in the Boeing Model 747. The survey should include removing wires from fuel probes and examining the wires for damage. Repair or replacement procedures for any damaged wires that are found should be developed. A–98–38: Require in Boeing Model 747 airplanes and other airplanes with fuel quantity indication system (FQIS) wire installations that are co-routed with wires that may be powered, the physical separation and electrical shielding of FQIS wires to the maximum extent possible. A–98–39: Require, in all applicable transport airplane fuel tanks, surge protection systems to prevent electrical power surges from entering fuel tanks through fuel quantity indication system wires. Based on these recommendations in October 26, 1999, the FAA issued Notice of Proposed Rulemaking (NPRM) 99–18, which was published in the Federal Register on October 29, 1999 (64 FR 58644). The notice proposed three separate requirements: Firstly, a requirement was proposed for the design approval holders of certain transport category airplanes to conduct a safety review (detailed failure analysis) of the airplane fuel tank system to preclude the presence of ignition sources in the fuel tanks, develop specific fuel tank system maintenance and inspection instructions for any items determined to require repetitive inspections or maintenance and to include mandatory fuel system maintenance in the limitations section of the Instructions for Continued Airworthiness Secondly, a requirement was proposed to prohibit the operation of those airplanes beyond a specified time, unless the operators of those airplanes incorporated instructions for maintenance and inspection of the fuel tank system into their inspection programs. Thirdly, for new designs the proposal also included a requirement for minimizing the flammability of fuel tanks employing new technologies. SAFETY PRECAUTIONS-AIRCRAFT AND WORKSHOP 1-22 Issue 10, January 2024 M7A- MAINTENANCE PRACTICES Table 1-1 - Summary of Operational Events SAFETY PRECAUTIONS-AIRCRAFT AND WORKSHOP 1-23 Issue 10, January 2024 M7A- MAINTENANCE PRACTICES Table 1-2 - Summary of Refuelling and Ground Maintenance Events SAFETY PRECAUTIONS-AIRCRAFT AND WORKSHOP 1-24 Issue 10, January 2024 M7A- MAINTENANCE PRACTICES Operational Events No. of Events No. of Fatalities Hull Loss with Fatalities 6 540 Hull Loss 2 Substantial Damage 2 Non-Operational Events Hull Loss with Fatalities 1 1 Hull Loss 2 Substantial Damage 4 1 Total 17 542 Table 1-3 - Aircraft Damage & Fatalities Maintenance and Inspection Instruction and its Development These tasks must be included in an operator’s approved maintenance program/ schedule. The task interval may be quoted in any usage parameter (FH, FC or Calendar time) depending on the cause of potential degradation that, if not detected and addressed, could lead to an unacceptable risk. Unless otherwise stated, the tasks and intervals specified in the Fuel Airworthiness Limitation document are mandatory and cannot be changed, escalated or deleted without the concurrence of the Primary Certification Authority. Under the existing process, the development of these tasks should be coordinated with the cognizant EASA/FAA office to ensure that the maintenance action proposed is an acceptable means of correcting the unsafe condition. During the process of developing information, the design approval holder should evaluate the various types of maintenance actions (inspecting, testing, repairing, replacing, or overhauling) to ensure that the most effective and practical means has been selected. The practicality of the maintenance action should also be validated through processes, such as the lead airline process, to ensure that it effectively addresses the safety concern. Examples of information to consider in developing Airworthiness Limitation Item instructions that are Maintenance and Inspection Instructions are the following: The location of the fuel tank system components to be maintained or inspected and any access requirements. Any unique procedures required, such as special detailed inspections or a dual sign-off maintenance record of requirements. Specific task information, such as inspections defined by pictures or schematics. Intervals for any repetitive task. Methods, techniques and practices required to perform a task and the pass/fail criteria for any inspection. Special equipment or test apparatus required. The following documentation should also be reviewed to avoid confusion or inconsistencies with existing flight crew procedures, maintenance tasks, and the Master Minimum Equipment List. Current Instructions for Continued Airworthiness (if they exist) that parallel maintenance and inspection requirement instructions proposed. Identification of the controlling document, in other words, the Airworthiness Limitation section for the fuel tank system. Operator comments on requirements. Changes to the Master Minimum Equipment List and associated maintenance or operational procedures. Changes to flight crew procedures in the Aircraft Flight Manual. SAFETY PRECAUTIONS-AIRCRAFT AND WORKSHOP 1-25 Issue 10, January 2024 M7A- MAINTENANCE PRACTICES Maintenance and Inspection instruction of A318/A319/A320/A321 is shown as an example in Figure 1-9. Figure 1-9- Example of Maintenance and Inspection Tasks SAFETY PRECAUTIONS-AIRCRAFT AND WORKSHOP 1-26 Issue 10, January 2024 M7A- MAINTENANCE PRACTICES Design Features of Airbus Aircraft to enhance FTS Wing Trim and Center Tank Structure Material and the large number of fasteners make sure that the fuel tank structures are electrically bonded. Composite ribs are bonded by means of metallic strips attached to the non-metallic structure. Aluminum structural items have finishing for protection against electrical harnesses short-circuit with the structure. Combination of the construction and thickness of the tank boundary skins give protection against a lightning strike causing ignition (heat). Fuel Quantity Indicating (FQI) Equipment Probes and sensors have low power supply. Electrical connection is done through a terminal block. The protective gap between the probes and the tank structure is maintained and are electrically isolated Bleed air pipes are insulated and separated from the tank boundary Lightning Protection & Wiring All equipment installed in fuel tank are bonded to the structure Only when absolutely necessary, wiring is routed inside fuel tanks External electrical wiring support clamps make sure that a cut cable cannot come into contact with the fuel tank boundary or structure in a fuel vapor area There is a complete segregation between in-tank wiring equipment and fuel calculators from other aircraft system wirings Fuel Pumps Safety features to prevent pumps from working in an empty fuel tank Rotating surfaces remain lubricated after prolong usage Contained within an explosion-proof canister and moving parts inside the pump are normally submerged in fuel Electrical connections to all pumps are made outside Figure 1-10- Explosion-proof cannister SAFETY PRECAUTIONS-AIRCRAFT AND WORKSHOP 1-27 Issue 10, January 2024 M7A- MAINTENANCE PRACTICES Valves and Pressure Switches Motor operated valves within the fuel tanks have the actuator located outside the tank wall The valve mechanisms inside the tank are dual bonded and do not have an ignition hazard Pump pressure switches are mounted on the tank boundaries and are separated from the fuel by a diaphragm Electrical connections are fully sealed and explosion proof Figure 1-11- Valve position 1 Figure 1-12- Valve Position 2 Figure 1-13- Pressure Switches SAFETY PRECAUTIONS-AIRCRAFT AND WORKSHOP 1-28 Issue 10, January 2024 M7A- MAINTENANCE PRACTICES Fuel Leaks Fuel leaks from the wing and trim tanks go either to the leading or trailing edge cavities or to the outside Any fuel overflowing from the NACA intake is directed downward and away from the engines In the leading and trailing edges the equipment is explosion proofed and insulated from the leakage The APU fuel feed and Trim Tank transfer pipes at the rear fuselage are shrouded so any fuel leakage is drained overboard via the drain mast. Figure 1-14 NACA intake Figure 1-15- Refuelling and Venting System SAFETY PRECAUTIONS-AIRCRAFT AND WORKSHOP 1-29 Issue 10, January 2024 M7A- MAINTENANCE PRACTICES Critical Design Configuration Control Limitations (CDCCL) and its Development As applied to Fuel Tank safety policy, this term refers to a feature of the fuel system design the integrity of which must be maintained to ensure that unsafe conditions do not develop. Features in an aircraft installation or component that must be retained during modification, change, repair, or scheduled maintenance characterize CDCCL. These features may exist in the fuel system and its related installation or in systems that could, if a failure condition were to develop, interact with the fuel system in such a way that an unsafe condition would develop in the fuel system. The definition of CDCCL does not include, “all the features inherent,” in a design; it includes only information necessary to ensure safety of fuel tank systems. The consideration underlying this definition is that holders of type certificates and supplemental type certificates should develop this information and make it available to operators of affected airplanes. This is consistent with the information required for airworthiness limitations required by CS25.571, “Damage-tolerance and fatigue evaluations of structure.” The Critical Design Configuration Control Limitations will be identified in the Airworthiness Limitation section of the Instructions for Continuing Airworthiness as an Airworthiness Limitation Item. However, the Critical Design Configuration Control Limitations are not inspections or life- limited items, as are most existing Airworthiness Limitation Items. They are features usually controlled by having operators (or, where necessary, holders of type certificates or supplemental type certificates) develop appropriate procedures. Some examples of Critical Design Configuration Control Limitations (CDCCL) are the following: Example 1. In some cases, the CDCCL will apply when an operator replaces a fuel tank system component that has a critical design feature. Assume that the lack of a bonding strap would disable an ignition prevention feature and, thus, contribute to an unsafe condition. A typical CDCCL item would be the means to ensure reattachment of the fuel pump bond strap when an operator changes the pump. Only the reattachment of the bonding strap is essential to prevent the unsafe condition. Therefore, the CDCCL is reattaching the bonding strap—not the entire installation procedure. Example 2. A specific configuration of the fuel tank system may be identified as necessary to prevent development of an unsafe condition. Assume that separation of external fuel gauging system wires has been determined as a way to keep unsafe energies out of the fuel tank. Separating fuel gauging system wiring from other wiring would become a CDCCL. This step ensures that—in combination with another failure—unsafe ignition energies cannot be produced in the fuel system. Example 3. In the event of certain failures, specific features of components, such as fuel pumps, ensure the mitigation of a hazardous condition. The safety concern is that, in the event of a pump repair or overhaul, certain safety features may not be installed or overhauled in accordance with the Component Maintenance Manual or other maintenance procedures acceptable to certificating authority for that component. The fuel pump will become the CDCCL and should be identified as such. Identification and Awareness of Critical Design Configuration Control Limitations The holder of a type certificate or supplemental type certificate will normally identify each CDCCL as an item in the Airworthiness Limitation section of the existing Instructions for Continuing Airworthiness. This is the mechanism for identifying critical configuration features and requiring their control. To ensure that the mechanic maintaining the airplane or the operator introducing a modification is aware of the need to consider the critical configuration feature, it will be necessary to insert cross-references to CDCCLs in certain documents. CDCCL items are identified by a WARNING in the procedures where they occur. When a procedure identifies a CDCCL item, it is mandatory condition that you do the instruction correctly and accurately as the procedure tells you. SAFETY PRECAUTIONS-AIRCRAFT AND WORKSHOP 1-30 Issue 10, January 2024 M7A- MAINTENANCE PRACTICES For CDCCLs like that in Example 1, the holder of a type certificate or supplemental type certificate should identify the task with WARNING or CAUTION notes for the critical item in the AMM procedure affected. The entity that operates or maintains the airplane should ensure that there are procedures for adequate maintenance of the CDCCLs. For CDCCLs like that in Example 2, the holder of a type certificate or supplemental type certificate should include information in standard practices manuals, such as the standard wiring practices manual for the type design. For CDCCLs like that in Example 3, the holder of a type certificate or supplemental type certificate should identify the appropriate Component Maintenance Manual. In addition, the certificate holder should insert a statement into both the Component Maintenance Manual and the Airplane Maintenance Manual that the component is classified as a CDCCL and, therefore, that it may be repaired or overhauled only in accordance with the Component Maintenance Manual or other maintenance procedures acceptable to the certificating authority for that component. CDCCL of A318/A319/A320/A321 is shown as an example in Figure 1-16. SAFETY PRECAUTIONS-AIRCRAFT AND WORKSHOP 1-31 Issue 10, January 2024 M7A- MAINTENANCE PRACTICES Figure 1-16- Example of CDCCL SAFETY PRECAUTIONS-AIRCRAFT AND WORKSHOP 1-32 Issue 10, January 2024 M7A- MAINTENANCE PRACTICES AD NO. Reason for Issue Action Required Compliance Date 2000-24-08 To prevent electrical Operational:- Circuit breaker Within 90 days January arcing of the fuel boost 1QA, 2QA, 7QA, and 8QA for 8, 2001 pump wire any wing tank fuel boost pump is tripped, do not reset Maintenance:- Detailed visual inspection of the wiring and the adjacent structure along the length of the fairings 2000-14-15 Prevention against Modify the fuel pipe couplings Within 36 months after explosion risks- and install Bonding leads in August 28, 2000 Electrical cables the specified locations of the fuel tank 2005-20-36 Prevention against Install a bounding lead Within 56 Months from explosion risks- In tank between the low pressure November 16, 2005 bonding valve and the adjacent pipe assembly, in both left and right wing. 2005-22-05 Fuel pumps- Prevention Modify the cables and the Within 56 Months from against explosion risks structure around the fuel November 30, 2005 (Chafing of cables) pumps 2006-10-03 Fuel system - Modify the wires to the pump Within 20 months from Prevention against control of the center tank, in June05, 2006 explosion risks (Dry accordance with the running fuel pump) instructions of SB A320-28- 1059 Revision 6. 2007-07-09 Prevention against Modify the electrical bonding Within 58 months after Explosion Risks- In of all structure and systems October 26, 2005 (the Tank Bonding installed inside the fuel center effective date of AD tank. 2005-19-14) 2007-15-06 Subsequent to fuel Revise Airworthiness 3 months from August system reviews Limitations Section (ALS) to 28, 2007 12 months conducted by the Incorporate Fuel Maintenance from August 28, 2007 manufacturer. and Inspection Tasks Revise ALS to Incorporate CDCCLs Table 1-4- Airworthiness Directives issued by Airbus for A320 APPROACHES OF FUEL TANK SAFETY Three conditions must be present in a fuel tank to support combustion. These include the presence of a suitable amount of fuel vapor, the presence of sufficient oxygen, and the presence of an ignition source. This has been named the “fire triangle” as shown in Figure 1-45. Each point of the triangle represents one of these conditions. Because of technological limitations in the past, the FAA philosophy regarding the prevention of fuel tank explosions to ensure airplane safety was to only preclude ignition sources within fuel tanks. This philosophy included application of fail-safe design requirements to fuel tank components (lightning design requirements, fuel tank wiring, fuel tank temperature limits, etc.) that are intended to preclude ignition sources from being present in fuel tanks even when component failures occur. SAFETY PRECAUTIONS-AIRCRAFT AND WORKSHOP 1-33 Issue 10, January 2024 M7A- MAINTENANCE PRACTICES In spite of the past efforts, the three accidents which occurred in the last 13 years as the result of unknown ignition sources within the fuel tank highlighted the difficulty in continuously preventing ignition from occurring within fuel tanks. Between 1996 and 2000 NTSB issued recommendations to improve fuel tank safety that included prevention of ignition sources and addressing fuel tank flammability (i.e., the other two points of the fire triangle). Therefore two different approaches were suggested: 1) Flammability Reduction ( Inerting Approach) 2) Ignition Source Prevention Figure 1-17- Flammability Reduction significantly reduces hole size in flammability layer, virtually eliminating future accidents. IGNITION SOURCE PREVENTION There are four primary phenomena that can result in ignition of fuel vapors in fuel tanks. They are: Electrical arcs. Friction sparks. Hot surface ignition or auto ignition and Filament heating. The conditions required to ignite fuel vapors from these ignition sources vary with pressures and temperatures within the fuel tank and can be affected by sloshing or spraying of fuel in the tank. Due to the difficulty in predicting fuel tank flammability and eliminating flammable vapors from the fuel tank, design practices have assumed that a flammable fuel air mixture exists in aircraft fuel tanks and require that no ignition sources be present. Any components located in or adjacent to a fuel tank must be qualified to meet standards that assure that during both normal and failure conditions, ignition of flammable fluid vapors will not occur. This is typically done by a combination of design standards, component testing and analysis. Testing of components to meet explosion proof requirements is carried out for various single and combinations of failures to show that arcing, sparking, auto ignition or flame propagation from the component will not occur. SAFETY PRECAUTIONS-AIRCRAFT AND WORKSHOP 1-34 Issue 10, January 2024 M7A- MAINTENANCE PRACTICES Testing for components has been accomplished using standards and component qualification tests. The standards include for example Eurocae 1 / RTCA2 DO160 and BS 3G 100 that defines explosion proof requirements for electrical equipment and analysis of potential electrical arc and friction sparks. IGNITION SOURCES 1) Electrical Arcs and Sparks: Ignition sources from electrical arcs can occur as a result of electrical component and wiring failures, direct and indirect effects of lightning, HIRF / EMI, and static discharges. The level of electrical energy necessary to ignite fuel vapors is defined in various standards. The generally accepted value is 0.2 milli-joules. An adequate margin needs to be considered, when evaluating the maximum allowable energy level for the fuel tank design. 2) Friction Sparks: Rubbing of metallic surfaces can create friction spark ignition sources. Typically this may result from debris contacting a fuel pump impeller or an impeller contacting the pump casing. 3) Hot Surface Ignition: Guidance provided in AC 25-8 has defined hot surfaces, which come within 300﮿C (50﮿F) of the auto-ignition temperature of the fuel air mixture for the fluid, as ignition sources. It has been accepted that this margin of 30 degrees Centigrade supported compliance to JAR 25.981(a). Surface temperatures not exceeding 200oC have been accepted without further substantiation against current fuel types. 4) Filament Heating: Analyses and testing indicate a small piece of wire from steel wool can ignite jet fuel when a current of 30 to 40 ma Root-Mean-Square (RMS) is applied to the wire. Therefore, electrical power with the potential to create a filament heating ignition source in the fuel tank should be limited to less than 30 ma RMS. 1 The European Organisation for Civil Aviation Equipment 2 Radio Technical Commission for Aeronautics SAFETY PRECAUTIONS-AIRCRAFT AND WORKSHOP 1-35 Issue 10, January 2024 M7A- MAINTENANCE PRACTICES LESSONS LEARNED The following sections intend to present a list of faults, which have occurred to fuel system components and precautions to be observed during maintenance. By its nature it cannot be an exhaustive list, but is only attempting to provide a list of undesirable features of fuel system components that should be avoided when designing/working on fuel tanks. Pumps a) Pump inducer failures have occurred resulting in ingestion of the inducer into the pump impeller and generation of debris into the fuel tank. b) Pump inlet check valves have failed resulting in rubbing on pump impeller. c) Stator windings have failed during operation of the fuel pump. Subsequent failure of a second phase of the pump caused arcing through the fuel pump housing. d) Thermal protective features incorporated into the windings of pumps have been deactivated by inappropriate wrapping of the windings. e) Cooling port tubes have been omitted during pump overhaul. f) Extended dry running of fuel pumps in empty fuel tanks, violation of manufacturers recommended procedures, are suspected causing in two incidents. g) Use of steel impellers which might produce sparks if debris enters the pump. h) Debris has been found lodged inside pumps. i) Pump power supply connectors have corroded allowing fuel leakage and electrical arcing. j) Electrical connections within the pump housing have been exposed and designed with inadequate clearance to pump cover resulting in arcing. k) Resettable thermal switches resetting at higher trip temperature. l) Flame arrestors falling out of their respective mounting. m) Internal wires coming in contact with the pump rotating group, energising the rotor and arcing at the impeller / adapter interface. n) Poor bonding across component interfaces. o) Insufficient ground fault current capability. p) Poor bonding of components to structure. q) Premature failure of fuel pump thrust bearings allowing steel rotating parts to contact the steel pump side plate. Figure 1-18 Failure Conditions Identified SAFETY PRECAUTIONS-AIRCRAFT AND WORKSHOP 1-36 Issue 10, January 2024 M7A- MAINTENANCE PRACTICES Wiring to pumps located in metallic conduits or adjacent to fuel tank walls Wear of Teflon sleeving and wiring insulation allowing arcing to conduit causing an ignition source in tank, or arcing to the tank wall. Fuel pump connectors Electrical arcing at connections within electrical connectors has occurred due to bent pins or corrosion. FQIS Wiring Degradation of wire insulation (cracking) and corrosion (copper sulphate deposits) at electrical connectors, unshielded FQIS wires have been routed in wire bundles with high voltage wires. FQIS Probes Corrosion and copper sulphide deposits have caused reduced breakdown voltage in FQIS wiring, FQIS wiring clamping features at electrical connections on fuel probes has caused damage to wiring and reduced breakdown voltage. Contamination in the fuel tanks including: steel wool, lock wire, nuts, rivets, bolts; and mechanical impact damage, caused reduced arc path between FQIS probe walls. Bonding straps Corrosion, inappropriately attached connections (loose or improperly grounded attachment points). Static bonds on fuel system plumbing connections inside the fuel tank have been found worn due to mechanical wear of the plumbing from wing movement, and corrosion. Failed or aged seals Seal deterioration may result in leak internal or external to fuel system, as well as fuel spraying. FLAMMABILITY REDUCTION Regulations used as the standard for certification of transport category airplanes prior to amendment 25-102, effective June 6, 2001, were intended to prevent fuel tank explosions by eliminating possible ignition sources from inside the fuel tanks. Service experience of airplanes certificated to the earlier standards shows that ignition source prevention alone has not been totally effective at preventing accidents. Commercial transport airplane fuel tank safety requirements have remained relatively unchanged throughout the evolution of piston-powered airplanes and later into the jet age. The fundamental premise for precluding fuel tank explosions has involved establishing that the design does not result in a condition that would cause an ignition source within the fuel tank ullage (the space in the tank occupied by fuel vapor and air). A basic assumption in this approach has been that the fuel tank could contain flammable vapors under a wide range of airplane operating conditions, even though there were periods of time in which the vapor space would not support combustion. Previous attempts were made to develop commercially viable systems or features that would reduce or eliminate other aspects of the fire triangle (fuel or oxygen) such as fuel tank inerting or ullage space vapor “scrubbing'' (ventilating the tank ullage with air to remove fuel vapor to prevent the accumulation of flammable concentrations of fuel vapor). Those initial attempts proved to be impractical for commercial transport airplanes due to the weight, complexity, and poor reliability of the systems, or undesirable secondary effects such as unacceptable atmospheric pollution. On January 23, 1998, the FAA published a notice in the Federal Register that established an Aviation Rulemaking Advisory Committee (ARAC) working group, the Fuel Tank Harmonization Working Group (FTHWG). The FTHWG evaluated numerous possible means of reducing or eliminating hazards associated with explosive vapors in fuel tanks. On July 23, 1998, the ARAC submitted its report to the FAA. The report provided a recommendation for the FAA to initiate rulemaking action to amend Sec. 25.981, applicable to new type design airplanes, to include a requirement to limit the time transport airplane fuel tanks could operate with flammable vapors SAFETY PRECAUTIONS-AIRCRAFT AND WORKSHOP 1-37 Issue 10, January 2024 M7A- MAINTENANCE PRACTICES in the vapor space of the tank or providing means to mitigate the effects of an ignition of fuel vapors within the fuel tanks such that any damage caused by an ignition will not prevent continued safe flight and landing.'' The report included a discussion of various options for showing compliance with this proposal, including managing heat input to the fuel tanks, installation of inerting systems or polyurethane fire suppressing foam, and suppressing an explosion if one occurred. The level of flammability defined in the proposal was established based on a comparison of the safety record of center wing fuel tanks that, in certain airplanes, are heated by equipment located under the tank, and unheated fuel tanks located in the wing. The ARAC concluded that the safety record of fuel tanks located in the wings with a flammability exposure of 2 to 4 percent was adequate and that if the same level could be achieved in center wing fuel tanks, the overall safety objective would be achieved. The thermal analyses documented in the report revealed that center wing fuel tanks that are heated by air conditioning equipment located beneath them contain flammable vapors, on a fleet average basis, in the range of 15 to 30 percent of the fleet operating time. Design features such as locating the air conditioning equipment away from the fuel tanks, providing ventilation of the air conditioning bay to limit heating and to cool fuel tanks, and/or insulating the tanks from heat sources, would be practical means of complying with the regulation proposed by the ARAC. In addition to its recommendation to revise Sec. 25.981, the ARAC also recommended that the FAA continue to evaluate means for minimizing the development of flammable vapors within the fuel tanks to determine whether other alternatives, such as ground-based inerting of fuel tanks, could be shown to be cost effective. To address the ARAC recommendations, the FAA continued with research and development activity to determine the feasibility of requiring inerting for both new and existing designs. Air is made up of about 78 percent nitrogen and 21 percent oxygen, and the hollow fiber membrane material uses the absorption difference between the nitrogen and oxygen molecules to separate the NEA from the oxygen. In airplane applications NEA is produced when pressurized air from an airplane source such as the engines is forced through the hollow fibers. The NEA is then directed, at appropriate nitrogen concentrations, into the ullage space of fuel tanks and displaces the normal fuel vapor/air mixture in the tank. Use of the hollow fiber technology allowed nitrogen to be separated from air, which eliminated the need to carry and store the nitrogen in the airplane. Researchers were aware of the earlier system's shortcomings in the areas of weight, reliability, cost, and performance. Recent advances in the technology have resolved those concerns and eliminated the need for storing nitrogen on board the airplane. The Flammibility Reduction Means (FRM) is intended to add an additional layer of safety by reducing the exposure to flammable vapors in the heated center wing tank, not necessarily eliminating them under all operating conditions. Consequently, ignition prevention measures will still be the principal layer of defense in fuel system safety, now augmented by substantially reducing the time that flammable vapors are present in higher flammability tanks. SFAR 88 3 addressed ignition prevention only. Inerting was not seen as practical at the time SFAR 88 was issued. The FRM uses a nitrogen generation system (NGS) that comprises a bleed-air shutoff valve, ozone converter, heat exchanger, air conditioning pack air cooling flow shutoff valve, filter, air separation module, temperature regulating valve controller and sensor, high-flow descent control valve, float valve, and system ducting. The system is located in the air conditioning pack bay below the center wing fuel tank. Engine bleed air from the existing engine pneumatic bleed source flows through a control valve into an ozone converter and then through a heat exchanger, where it is cooled using outside 3 Special Federal Aviation Regulations SAFETY PRECAUTIONS-AIRCRAFT AND WORKSHOP 1-38 Issue 10, January 2024 M7A- MAINTENANCE PRACTICES cooling air. The cooled air flows through a filter into an air separation module (ASM) that generates NEA (Nitrogen-Enriched Air), which is supplied to the center fuel tank, and also discharges Oxygen-Enriched Air (OEA). The OEA from the ASM is mixed with cooling air from the heat exchanger to dilute the oxygen concentration and then exhausted overboard. The FRM also includes modifications to the fuel vent system to minimize dilution of the nitrogen-enriched ullage in the center tank due to cross-venting characteristics of the existing center wing fuel tank vent design. Figure 1-19- NGS System Figure 1-20- Air Separation Module SAFETY PRECAUTIONS-AIRCRAFT AND WORKSHOP 1-39 Issue 10, January 2024 M7A- MAINTENANCE PRACTICES Figure 1-21- Inerting System on B747 SP Figure 1-22- Inerting Installation on A320 SAFETY PRECAUTIONS-AIRCRAFT AND WORKSHOP 1-40 Issue 10, January 2024 M7A- MAINTENANCE PRACTICES Fuel Tank Precautions and Entry Procedures The following is a list of precautions to be observed while working on Fuel System: 1) For any maintenance activity inside a fuel tank, two persons are necessary for this procedure. One person in the tank and a second person out of the tank to monitor the safety conditions. 2) When you do work on the fuel system wiring, you must use test equipment that is approved (refer to international or national specifications for intrinsically safe test equipment: EN50020, UL913 or equivalent). Test equipment that is not approved can cause fire or an explosion. 3) Do not use metallic wire wool in fuel tanks. Metal wool strands can cause electrical arcing, which can start a fire. 4) Do not wear a headset or touch cables/lines connected to the aircraft when there is a risk of lightning. Lightning is dangerous 5) Always connect the ground cable to the parking ground point before you connect it to the aircraft. Do not attach the cable to the aircraft first (there is a risk of electric shock). 6) You must discard o-rings on disconnected pipes and install new o-rings during installation of the pipes. This prevents possible leaks. 7) Make sure that the aircraft is grounded correctly. 8) Make sure that the lighting in the work area is sufficient to work safely. Use only the approved spark-proof lamps and torches in the work area. Sealed vapor-lamps are not to be used. 9) Make sure that the flow of clean air in the work area is sufficient to work safely. 10) Before you start the maintenance task make sure that these are available: the correct fire-fighting equipment and an approved persons to use the fire- fighting equipment. 11) Do not get aircraft fuel in your eyes, mouth, nose, ears or on your skin. 12) If you get aircraft fuel in your eyes, mouth, nose or ears: Flush with clean water. Get medical aid. 13) If you get aircraft fuel on your skin Remove any clothing soaked with fuel. Clean the skin with soap and water. Flush the skin with clean water. If the skin is dry, apply an approved cream to it. 14) Do not get your clothes soaked with fuel and use approved protective clothing made from material which will not cause sparks. 15) Protect your skin with barrier cream. 16) You must use a respirator if the fuel-gas concentration in the work area is more than 5% of the Lower Explosive Limit (LEL). SAFETY PRECAUTIONS-AIRCRAFT AND WORKSHOP 1-41 Issue 10, January 2024 M7A- MAINTENANCE PRACTICES 17) Put "NO SMOKING" warning notices around the work area. 18) In the work area you must not: Smoke use flames which do not have protection operate electrical equipment which is not necessary for the task operate electrical equipment which is not approved for the task pull or move metal objects along the ground use footwear which has metal studs or steel toe-caps use hearing-aids or battery-operated equipment which will cause sparks have any material which will cause sparks or flames 19) You must immediately flush away or remove any fuel leakage. 20) You must put any material which is used to remove any fuel leakage in special fireproof containers 21) You must do all maintenance tasks in very clean conditions. Do not let oil, dirt, grit, or loose paint cause contamination of the tank. 22) Use only approved cleaning materials. 23) Make sure that all signs of solvents and cleaning agents are removed from the equipment/components before they are installed. 24) Make sure that all electrical circuits in maintenance are isolated before you apply electrical power to the aircraft. 25) If possible, all components before you place them inside the fuel tank. All wire locking must be completed outside the fuel tank. 26) Put blanking caps on all disconnected pipes and openings in components and tanks 27) Make sure that all the fuel system components have correct electrical bonding. 28) Do not connect electrical equipment to a power source less than 30 meters away, unless the power source has spark-proof connectors. 29) During removal and installation of panels and equipment record the position of each bolt. This prevents damage to structure. 30) Make sure that the access platform or the step ladder are grounded. 31) You must complete the Pre-Entry Checklist before you do work in a fuel tank. 32) Make sure that the work area is clean and open to the air. 33) The person in the fuel tank and the safety person out of the fuel tank must obey these precautions. There must be a continuous flow of clean filtered air through the fuel tank when the person is in the tank. If possible, the safety person must position himself to be able to see the person in the fuel tank and monitor his safety. You must put on an air-supplied respirator to go into a fuel tank, unless the Local Regulations permit you to work without a respirator. 34) Do not go in a tank until you know the location and dimensions of the work areas. SAFETY PRECAUTIONS-AIRCRAFT AND WORKSHOP 1-42 Issue 10, January 2024 M7A- MAINTENANCE PRACTICES 35) Do not touch or push against the magnetic level indicators when you are in the fuel tank. This will prevent damage to them. 36) Do not touch or push against the FQI probes when you are in the fuel tank. This will prevent damage to them and their installation. 37) Do not cause damage to the internal structure, sealant, electrical cables, or conduits during maintenance 38) Do not use Fuel pipes and the equipment as handholds when you do work in a fuel tank. This will prevent damage to them. 39) Use only an approved Textile-Lint free Cotton – (Material No. 14SWBA1) to dry the fuel tank internally. 40) Use protective mats on the floor of the fuel tank to prevent damage to the fuel tank structure injury to person 41) Bonding straps should be positioned correctly and not corroded, damaged or broken. If necessary, new bonding straps may be installed before reinstalling the fuel tank access panels. Figure 1-23- Safety Barriers and Warning Notices SAFETY PRECAUTIONS-AIRCRAFT AND WORKSHOP 1-43 Issue 10, January 2024 M7A- MAINTENANCE PRACTICES Figure 1-24- Ventillation and Combustible Gas Indicator Figure 1-25- Fuel Tank Entry Checklist SAFETY PRECAUTIONS-AIRCRAFT AND WORKSHOP 1-44 Issue 10, January 2024 M7A- MAINTENANCE PRACTICES Figure 1-26- Fuel Tank Entry Personnel Figure 1-27- Example of an Airbus A330/A340 Wing Fuel Tank (Collector Cell) SAFETY PRECAUTIONS-AIRCRAFT AND WORKSHOP 1-45 Issue 10, January 2024 M7A- MAINTENANCE PRACTICES BALLISTIC RECOVERY SYSTEMS Ballistic recovery systems (BRS), also known as “Ballistic Parachute Systems (BPS)” in aviation refer to parachute systems designed to safely recover an aircraft and its occupants in the event of an emergency, such as an unrecoverable spin or structural failure. These systems are a crucial safety feature, offering an additional layer of protection for pilots and passengers. The concept of using parachutes for aircraft recovery dates back to the early 20th century, but it wasn't until the latter half of the century that practical applications began to emerge. In the 1920s, the idea of using parachutes for aircraft recovery gained attention, and several experimental systems were developed. However, it wasn't until the 1970s that the first practical ballistic recovery systems for general aviation aircraft were successfully developed and tested. One of the pioneers in this field was Boris Popov, who, after surviving a mid-air collision, dedicated himself to creating a reliable aircraft parachute system. In 1975, he founded Ballistic Recovery Systems, Inc. (BRS) and introduced the first viable aircraft parachute system for small aircraft. The technical operation of a ballistic recovery system involves a rocket-deployed parachute that is housed in a canister mounted on the aircraft. In the event of an emergency, the rocket is fired, extracting the parachute from its container and allowing it to deploy and slow the aircraft's descent. These systems are designed to work at various altitudes and airspeeds, providing a crucial safety net in situations where traditional recovery methods are ineffective. Modern ballistic recovery systems are meticulously engineered to meet stringent safety standards and are tailored to specific aircraft models. They undergo rigorous testing to ensure reliability and effectiveness. Today, these systems are commonly found on a wide range of general aviation aircraft, including light sport aircraft, kit-built planes, and some certified aircraft models. They are particularly popular among recreational pilots and flight training organizations, as they provide an added sense of security during flight. The deployment of a ballistic recovery system is typically initiated manually by the pilot, although some systems are equipped with automatic activation features that can sense critical flight conditions and deploy the parachute if necessary. These systems are designed to provide a controlled descent, minimizing the risk of injury to occupants and reducing the likelihood of catastrophic damage to the aircraft. While they are not a substitute for proper pilot training and maintenance, ballistic recovery systems offer an invaluable last-resort option in emergency situations. The effectiveness of ballistic recovery systems in saving lives and reducing the severity of accidents has been demonstrated in numerous real-world incidents. By providing a means of controlled descent and impact, these systems have significantly improved the odds of survival in otherwise dire situations. As aviation technology continues to advance, ballistic recovery systems are likely to undergo further refinements and become even more prevalent across different segments of the aviation industry, contributing to overall safety for pilots and passengers alike. Figure 1-28- Aircraft equipped with BRS SAFETY PRECAUTIONS-AIRCRAFT AND WORKSHOP 1-46 Issue 10, January 2024 M7A- MAINTENANCE PRACTICES Operation of BRS BRS comprises a parachute (packed), a rocket with trigger and firing systems and the connecting lines and carrier harness involved. The parachute, carrier harness and some of the suspension lines are packed in or on the aircraft. The parachute is connected permanently to the suspension points on the aircraft structure via the carrier harness and suspension lines. Suspension lines may be made of plastic or steel. They are often laminated or glued onto the surface of the fuselage, and are released from the fuselage structure as far as the actual suspension points themselves when the parachute opens. The pilot releases the rescue parachute via a handle and the release cable. Pulling the handle fires a small solid-fuel rocket, which fires off from the aircraft with the parachute package on a short line. If the BRS is inside the fuselage, the rocket passes through the fuselage itself first, pulling the parachute package with it. Where the rocket is fired from, and/or where the firing aperture is, varies from one aircraft type to another. The direction the rocket takes when fired may be up to 15° from the angle at which it was originally fitted. Figure 1-29- Parachute opening – CAPS (Cirrus Airframe Parachute System) SAFETY PRECAUTIONS-AIRCRAFT AND WORKSHOP 1-47 Issue 10, January 2024 M7A- MAINTENANCE PRACTICES Figure 1-30- BPS parachute opening in a VLA (Very light aircraft) Rocket The rocket consists of the guide tube, the primer mixture, primary booster material and the solid-fuel rocket. The solid-fuel rocket is often referred to as the rocket motor, and is the component which leaves the aircraft once ignited, taking the parachute pack tow line with it. Figure 1-31- Cross-sectional drawing of rocket SAFETY PRECAUTIONS-AIRCRAFT AND WORKSHOP 1-48 Issue 10, January 2024 M7A- MAINTENANCE PRACTICES Both rocket motor and igniter unit contain explosives. The rockets used vary in size, depending on the size, model and take-off weight of the aircraft concerned. The rocket is mounted permanently in or on the aircraft: that is to say, it is bolted to the aircraft structure. The flight manual states that the pilot must activate the BPS, i.e. the rocket, when preparing to take off, so they merely need to pull the handle to fire the rocket in an emergency. The igniter unit and guide tube remain bolted to the structure once the rocket is fired. Figure 1-32- Typical BPS installed Figure 1-33- BPS release handle SAFETY PRECAUTIONS-AIRCRAFT AND WORKSHOP 1-49 Issue 10, January 2024