OGTS-M08 Level 1 Basic Maintenance Hand Tools PDF
Document Details
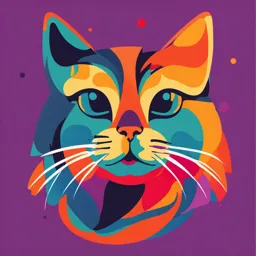
Uploaded by ReformedMagicRealism
Uganda Petroleum Institute Kigumba
2019
OGTS
Abdulhamid Hamad
Tags
Summary
OGTS-M08 Level 1 presentation, focused on Basic Maintenance Hand Tools, prepared by Abdulhamid Hamad and presented by Otim Robert. The document includes guidelines on HSE, trainer experience, and objectives of the training modules.
Full Transcript
PREPARED BY: ABDULHAMID HAMAD OGTS-M08 LEVEL 1 Basic Maintenance Hand Tools PRESENTED BY: OTIM ROBERT PROJECT 24 June 2019 / ‹#› HSE and Protocols for the Course 24 June 2019 / ‹#› ❑ Alarms and Escape Routes ▪ The...
PREPARED BY: ABDULHAMID HAMAD OGTS-M08 LEVEL 1 Basic Maintenance Hand Tools PRESENTED BY: OTIM ROBERT PROJECT 24 June 2019 / ‹#› HSE and Protocols for the Course 24 June 2019 / ‹#› ❑ Alarms and Escape Routes ▪ There are no planned alarms ▪ Any alarm must be treated as ‘live’ ▪ Leave the room in an orderly manner ▪ Proceed to the Muster Point ▪ Await further instructions ❑ Mobile Phones ▪ Please turn them off ▪ If you are ‘On Call’ turn to Vibrate ▪ Please leave room to answer ▪ Please decline social calls ❑ Comfort Breaks ▪ We will take a 15 minute break every 1.5 hour ▪ Please return promptly so we can finish on time TRAINER 24 June 2019 / ‹#› Trainer’s Work Experience ABOUT THELEARNER …. 24 June 2019 / ‹#› Who are you? What are your expectations ON this training module? OBJECTIVE 24 June 2019 / ‹#› Upon completion of this course, the participants will be able to: To Identify the use of basic maintenance hand tools Demonstrate the use of basic hand tools for maintenance tasks and the production of an artifact To demonstrate the care of basic maintenance hand tools GROUND RULES 24 June 2019 / ‹#› Punctuality Right to make Telephone switched off mistakes Help each other Participation Respect Listen Positive attitude OBJECTIVES 24 June 2019 / ‹#› Learning Activity Objectives: Upon completion of this course, participants should be able to: Identify the name and the function (application) of different Hand Tools which are commonly used in the workshop and in the plant. Describe the required safety precautions for these tools Care and Proper Use of Hand Tools Identify the name and the function (application) of drill Power Tools which are commonly used in the work shop and in the plant HAND TOOLS 24 June 2019 / ‹#› Learning Topics: ▪ Holding Tools ▪ Cutting & Shaping Tools ▪ Cutting Threads ▪ Striking Tools ▪ Fastening & Removing Tools Hand tools Safe Use 24 June 2019 / ‹#› Handtools Personal Protective Equipment (PPE) Always ware the correct minimum PPE for working safely on site or in the workshop. Head Protection. Eye Protection Hand tools Safe Use 24 June 2019 / ‹#› Handtools PPE Cont’d Hand Protection. Foot Protection CUTTING TOOLS 24 June 2019 / ‹#› CUTTING TOOLS Metal Snips Perfect for cutting soft metals Snips have a single pivot point (much like a pair of scissors), so their strength is often determined by the length of the tool. Longer handles create more leverage on a single fulcrum, so it is common to find a wider variety of tin snip lengths, typically between 6 and 14 inches. CUTTING TOOLS 24 June 2019 / ‹#› CUTTING TOOLS Metal Snips Types Snips The two main types of snips are tin snips and aviation snips. Both are used to cut sheet metal and other tough materials: 1. Tin Snip Type 2. Aviation Snip Type CUTTING TOOLS 24 June 2019 / ‹#› CUTTING TOOLS Metal Snips Straight Cut Types of Tin Snips Common types of snips are: Nibbler Straight Cut Snips Offset Offset Snips Pelican Snips Jeweler’s Snips Circular or Curved Snips Nibblers Jeweler’s Snips Pelican Duckbill Snips Bulldog Snips Duckbill Snips Circular or Curved Bulldog Snips CUTTING TOOLS 24 June 2019 / ‹#› CUTTING TOOLS Metal Snips Aviation Snips Sometimes additional strength is required with specific metals and gauges. Aviation snips, also called compound action snips, are appropriate for these situations. They have a pivot point at the blade and one extra pivot point on each of the handles, called linkage points, that compound the force applied, increasing leverage. CUTTING TOOLS 24 June 2019 / ‹#› CUTTING TOOLS Straight Cut Metal Snips Types of Aviation Snips Offset Common types of snips are: Straight Cut Aviation Snips Offset Aviation Snips Utility Cut Utility Cut Aviation Snips Right Angle Aviation Snips Bulldog Aviation Snips Right Angle Long Cut Aviation Snips Bulldog Long Cut CUTTING TOOLS 24 June 2019 / ‹#› CUTTING TOOLS Metal Snips Aviation Snips Colour Coding A common curiosity about aviation snips revolves around the colours of the handles. It’s quite common to find aviation snips with yellow, red, or green handles. Do these colours hold meaning? CUTTING TOOLS 24 June 2019 / ‹#› CUTTING TOOLS Metal Snips Aviation Snips Colour Coding Do these colours hold meaning? Yes, they absolutely do, These snips have blades orientated either to the left or to the right These colours are an industry standard that allows users to quickly grab a pair of snips without stopping to check the orientation of the blade first. o Yellow handles are used in straight cut snips and all variations of straight snips, like long cut snips and bulldog snips. The colour specifies a straight cut or one with a wide curve. o Red handles signify straight or tightly curved cuts that move metal to the right. The bottom blade is offset to the right-hand side. o Green handles are for straight or tightly curved cuts that move the metal to the left. The bottom blade is oriented on the left-hand side of the snips. CUTTING TOOLS 24 June 2019 / ‹#› CUTTING TOOLS Metal Snips Best Use of Snips Tool Type Mild Steel / Soft Metal (ga) Stainless Steel (ga) Straight Cut 18 – 24 20 – 28 Offset 18 – 20 22 – 24 Curved 18 – 22 22 – 24 Utility Not rated for metal thickness Not rated for metal thickness Duckbill 21 – 24 23 – 28 Bulldog 16 18 Note : Gauge (or ga) sizes are numbers that indicate the thickness of a piece of sheet metal, with a higher number referring to a thinner sheet. CUTTING TOOLS 24 June 2019 / ‹#› Metal sheet gauges Thickness Weight Per Area Thickness Weight Per Area in mm lb/ft² kg/m² in mm lb/ft² kg/m² Gauge Gauge 3 0.2391 6.073 9.754 47.624 22 0.0299 0.759 1.220 5.955 4 0.2242 5.695 9.146 44.656 23 0.0269 0.683 1.097 5.358 5 0.2092 5.314 8.534 41.668 24 0.0239 0.607 0.975 4.760 6 0.1943 4.935 7.927 38.701 25 0.0209 0.531 0.853 4.163 7 0.1793 4.554 7.315 35.713 26 0.0179 0.455 0.730 3.565 8 0.1644 4.176 6.707 32.745 27 0.0164 0.417 0.669 3.267 9 0.1495 3.797 6.099 29.777 28 0.0149 0.378 0.608 2.968 10 0.1345 3.416 5.487 26.790 29 0.0135 0.343 0.551 2.689 11 0.1196 3.038 4.879 23.822 30 0.0120 0.305 0.490 2.390 12 0.1046 2.657 4.267 20.834 31 0.0105 0.267 0.428 2.091 13 0.0897 2.278 3.659 17.866 32 0.0097 0.246 0.396 1.932 14 0.0747 1.897 3.047 14.879 33 0.0090 0.229 0.367 1.793 15 0.0673 1.709 2.746 13.405 34 0.0082 0.208 0.335 1.633 16 0.0598 1.519 2.440 11.911 35 0.0075 0.191 0.306 1.494 17 0.0538 1.367 2.195 10.716 36 0.0067 0.170 0.273 1.335 18 0.0478 1.214 1.950 9.521 37 0.0064 0.163 0.261 1.275 19 0.0418 1.062 1.705 8.326 38 0.0060 0.152 0.245 1.195 20 0.0359 0.912 1.465 7.151 21 0.0329 0.836 1.342 6.553 THREADING TOOLS OPITO OUTCOMES COVERED KNOWLEDGE CRITERIA K 1.10 Tap and die sets, procedures, uses and care THREADING TOOLS 24 June 2019 / ‹#› Cutting Internal Thread Tap and Tap Holder The tap is manufactured from high speed steel. Cheaper versions are manufactured from carbon steel. In both cases they are hardened, in order to withstand the thread cutting they will endure, throughout their usable life time. HSS Taps carbon steel Taps THREADING TOOLS 24 June 2019 / ‹#› Cutting Internal Thread Taps are normally bought as a set of three taps: Second Tap or 1. Taper Tap 2. Intermediate Tap (Second Tap) 3. Plug Tap. THREADING TOOLS 24 June 2019 / ‹#› Cutting Internal Thread Taper Tap: These are generally used for initiating a thread and are usually tapered from the bottom point up to the sixth thread from the top. The point diameter equals the core diameter of the thread. A taper tap produces full thread in a through hole. Second Tap: These are used for deepening the cut threads by taper taps in “blind holes” (deep drillings without virtual ends). The tapering angle on these taps is quite similar to that of taper taps, but only for the first six threads. Plug Tap: Unlike the above types, plug taps are not tapered and are solely used for the purpose of producing neat finishes to the ends of blind holes or very deep through holes. THREADING TOOLS 24 June 2019 / ‹#› Cutting Internal Thread Taps Holders : The tap is secured at the centre of the wrench, which has jaws that tighten on the square section shank. Three Tap holders can be recognized: 1. American Tap wrench 2. Bar Tap wrench 3. Chuck Tap wrench The tap wrench should not slip, when being rotated during use. THREADING TOOLS 24 June 2019 / ‹#› Cutting Internal Thread Tap size selection The purpose of the ‘tap’, is to cut a thread into a ‘hole’, that has been accurately drilled to a specific size. For example: 5mm hole can be ‘tapped’ for a M6 (metric) thread. 6.8mm diameter hole can be ‘tapped’ for a M8 screw thread. Note: This varies and depends on whether a coarse of fine thread is required. Most common metric tapping drill sizes THREADING TOOLS 24 June 2019 / ‹#› Cutting Internal Thread Basics of Tapping Procedure: Types of Holes: Holes can be drilled in a specimen taking one of the following forms: 1. Through Hole 2. Blind Hole Blind Hole In both cases above , the hole that is Through Hole prepared for threading shall have the size called ( Tapping Size hole) based on the screw core diameter THREADING TOOLS 24 June 2019 / ‹#› Cutting Internal Thread Basics of Tapping Procedure: Bolt Core diameter: Thread assigned to has a three diameters: 1. Major Diameter 2. Minor Diameter 3. Pitch Cylinder Diameter To create an internal thread, a hole is first drilled the size of the Minor diameter of the screw. This is called a tapping size hole. THREADING TOOLS 24 June 2019 / ‹#› Cutting Internal Thread Basics of Tapping Procedure: Thread Bitch and Thread per Inch: Thread pitch : Terminology of METRIC system Thread per Inch : Terminology of IMPERIAL system THREADING TOOLS 24 June 2019 / ‹#› Cutting Internal Thread Tap Drill hole size: Metric Sizes THREADING TOOLS 24 June 2019 / ‹#› Cutting Internal Thread Tap Drill hole size: Metric Sizes THREADING TOOLS 24 June 2019 / ‹#› Cutting Internal Thread Tap Drill hole size: Imperial Sizes THREADING TOOLS 24 June 2019 / ‹#› Cutting Internal Thread Tap Drill hole size: Imperial Sizes THREADING TOOLS 24 June 2019 / ‹#› Cutting Internal Thread Tap Drill hole size: Imperial Sizes THREADING TOOLS 24 June 2019 / ‹#› Cutting Internal Thread Tapping Procedure: When cutting Internal thread: Through Hole 1. The taper tap is placed in the wrench. 2. The ‘taper’ end of the tap is placed in the hole. 3. The wrench is turned clockwise for a ONE full rotation 4. Then HALF a turn in an anticlockwise rotation, this clears debris from the hole being threaded. THREADING TOOLS 24 June 2019 / ‹#› Cutting Internal Thread Tapping Procedure: When cutting Internal thread: Blind Hole 1. The taper tap is placed in the wrench. 2. A ‘blind hole’, will need to be cut using the taper tap first, followed by the intermediate tap and finally the plug tap. 3. Follow the same procedure of through holes 4. It is important to use cutting compound, during this procedure. Using all three taps on a blind hole, ensures the thread is cut almost to the bottom of the hole. THREADING TOOLS 24 June 2019 / ‹#› Cutting Internal Thread Tapping Procedure: When cutting Internal thread: Cutting Compound 1. Non-Blind Hole Tapping : It is recommended that ‘cutting compound’, such as Trefolex, is applied to the taper of the tap. This lubricates the tap, making cutting much easier and smoother.The ‘taper’ end of the tap is placed in the hole. 1. Blind Hole Tapping : It is important to use cutting compound THREADING TOOLS 24 June 2019 / ‹#› Cutting Internal Thread CARE OF TAPS Do not attempt to sharpen taps. Keep cutting edges lightly oiled. Wipe excess oil and metal shavings from tap and tap wrench. Store them in a case or wrap individually in cloths to protect cutting surfaces. THREADING TOOLS 24 June 2019 / ‹#› Cutting Internal Thread Easy Out Extractors: Sometimes a screw or a bolt will shear off and cannot be removed with a wrench. then, an easy out can be employed. They are very hard and tapered. The method is to : 1. Drill a smaller hole into the broken bolt. 2. Then gently tap in the extractor and since it has a left hand thread, if it is turned, then it and the broken bolt will screw out. THREADING TOOLS 24 June 2019 / ‹#› Cutting External Thread Cutting an external thread is achieved through the use of a die, held in a stock. Dies are manufactured from carbon steel or high speed steel HSS , hardened and tempered. Material : HSS Shape : Circular Material : carbon steel Shape: Hexagonal THREADING TOOLS 24 June 2019 / ‹#› Cutting External Thread Die Types There are following types of dies are used: Solid Die Split Die Adjustable Die Die Nut Pipe Die Chaser Die Acron Die THREADING TOOLS 24 June 2019 / ‹#› Cutting External Thread Die Types Solid Die A solid die is made in a single piece and its size remains fixed. It is mainly used in making old and worn-out threads. It is also called a die nut. Split Die A split die is used to accommodate large size differences. It is also called a circular die or button die. Two-Piece Adjustable Die It gives more adjustment than split dye. These dies are always found in pairs and used together. THREADING TOOLS 24 June 2019 / ‹#› Cutting External Thread Die Types Die Nut is exactly the same in appearance to an ordinary square or hexagonal nut Die holes of different sizes are made in it. The function of a die nut is not for cutting threads, but for sharpening an existing thread. Pipe Die It is used for making a thread on a pipe. Chaser Die These types of the die are mostly used in automatic machines. Acron Die It is mainly used for cutting threads in depth. THREADING TOOLS 24 June 2019 / ‹#› Cutting External Thread Die Construction The most common form of die, is the circular split die. The flutes of the die, produce the ‘cut’ in the material being threaded, forming a thread. The ‘circular’ gaps allow chippings of waste material to escape from the die, preventing clogging of the cutting tool. THREADING TOOLS 24 June 2019 / ‹#› Cutting External Thread Diestock Types Diestock is a device used to hold the die during external threading. Generally die stock is made of cast steel, mild steel, or cast iron. Types of Die Stock : Solid Die Stock Adjustable Die Stock Quick Die Stock THREADING TOOLS 24 June 2019 / ‹#› Cutting External Thread Diestock Types Solid Die Stock It is made from a solid piece of metal with a circular body and two handles fitted on either side of the body. The body has two side screws and a centre screw to hold and adjust the die. It is also called button pattern die stock. This die stock is used to hold the circular solid and split dyes. Adjustable Die Stock It has a rectangular body and two handles fitted on either side of the body. There is a clamping screw on the body for the adjustment of the die. It is used to hold a two-piece die. THREADING TOOLS 24 June 2019 / ‹#› Cutting External Thread Diestock Types Quick Die Stock It consists of a circular body and handle fitted on the body. It is used to hold the adjustable screw plate die. THREADING TOOLS 24 June 2019 / ‹#› Cutting External Thread Diestock shapes Diestock can accommodate two different types of cutting tools , usually known as: Round Head Die Hex Head Die THREADING TOOLS 24 June 2019 / ‹#› Cutting External Thread Diestock controls In order to accomplish the task of creating uniform threads on different devices, a diestock provides the framework that make it possible to position the cutting tools, usually called Dies. Diestocks provided with different numbers of screws used for : Locking the Die Adjusting the size of the die 1. Single Locking screw Diestock 2. Three screws Diestock 3. Four screws Diestock 4. Five screws Diestock THREADING TOOLS 24 June 2019 / ‹#› Cutting External Thread Typical die stock The diestock has three screws that locate in recesses and the slot in the split circular die. By adjusting the three screws, the die can be enlarged or made slightly smaller, thus cutting a slightly oversize or slightly undersized screw thread. THREADING TOOLS 24 June 2019 / ‹#› Cutting External Thread Typical die stock with a central adjusting screw Hexagon Rethreading Dies made from Carbone Steel Hexagonal die can be used with a wrench or socket in limited space Best suited for maintenance and repair work Good for removing rust from rust bolts Re-threading Damaged Threads THREADING TOOLS 24 June 2019 / ‹#› Cutting External Thread The die stock is turned over so that the bottom is facing upward. The die is located on the shaft and is then screwed onto it Fix the Dia flutes on the face of the Rod Turning 1½ turns clockwise, then ½ a turn back. This process is repeated until a sufficiently long thread is cut. A little cutting oil or grease is wiped onto the die to help it cut and to give the screw thread a smooth finish. THREADING TOOLS 24 June 2019 / ‹#› Cutting External Thread Caution during Operation of Die Important points to remember while cutting the thread from die: 1. The right size die should be selected according to the size of the rod on which the thread is to be cut. 2. The edge of the rod on which the thread is to be cut should be chamfered slightly so that the die can easily start the cut on it. 3. The die should be run straight. 4. The die should be driven half a circle forward and half a circle back. 5. The dye should be cleaned after applying oil or grease. THREADING TOOLS 24 June 2019 / ‹#› Cutting External Thread It is vitally important to keep the die and die stock square to the bar or a drunken thread will be cut. CARE OF DIES1.Do not attempt to sharpen dies.2.Keep cutting surfaces clean and lightly lubricated.3.Store in a case or wrap individually in cloths wherethey will not come in contact wi THREADING TOOLS 24 June 2019 / ‹#› Cutting External Thread CARE OF DIES Do not attempt to sharpen dies. Keep cutting surfaces clean and lightly lubricated. Store in a case or wrap individually in cloths where they will not come in contact with other tools. SCRAPERS OPITO OUTCOMES COVERED KNOWLEDGE CRITERIA K 1.11 Types, uses and care of scrapers Scrapers 24 June 2019 / ‹#› What is Scraping? Scraping is a method in which high spots are removed from the surface in order to fit the parts together with precision. What is Scraper? A scraper is a tool used for removing or scraping away material or residue from a surface. In metalworking, scraping plays a vital role in achieving the required flatness and straightness of metal parts, which is crucial for their proper assembly and operation. Scrapers 24 June 2019 / ‹#› Types of Scrapers There are following types of scrapers tools are used and their uses are described below in detail. Flat Scraper Half Round Scraper Three Square Scraper Bullnose Scraper Two Handle Scraper Hook Scraper Scrapers 24 June 2019 / ‹#› Types of Scrapers Scrapers 24 June 2019 / ‹#› Types of Scrapers Flat Scraper A flat scraper is used for scraping on flat surfaces. Its cutting edge is round like in a convex shape. Flat scrapers are found in length from 100 mm to 300 mm and Its edge is made by grinding on one side at an angle of 81 °. The sharpened scraping tip is often slightly convex to help prevent the corners of the scraping surface causing burrs. Non-Sparking Non-Magnetic Non-sparking flat scraper for use in petrochemical, grain production (explosive-dust), utilities, and hazmat applications. Scrapers 24 June 2019 / ‹#› Types of Scrapers Flat Scraper Sizes Scrapers 24 June 2019 / ‹#› Types of Scrapers Half Round Scraper Also called ‘bearing scrapers’ or ‘half-round scrapers’, as they’re used for scraping the inside of bearings and other curved surfaces to achieve a better mating surface. Curved blade scrapers have two sharp edges. It is a true multitasker, combining the attributes of both flat and curved scrapers. The half-round profile allows for seamless transitions between different surface geometries It is especially useful when needing to switch between different types of scraping without losing time to change tools. Scrapers 24 June 2019 / ‹#› Types of Scrapers Three Square Scraper Its shape is triangular and has three cutting edges so it is also called a triangular scraper. Each edge can be sharpened to a different profile, offering versatility without the need to switch tools frequently. This shape is particularly useful for getting into corners and tight angles that other scrapers cannot reach. It is used for sharpening the edges of bush bearings and for scraping the inner spherical surface. Scrapers 24 June 2019 / ‹#› Types of Scrapers Bullnose Scraper The shape of these types of scrapers is similar to the shape of the nostrils of a bull, so it is called a bullnose scraper. It is used for scraping flat and half round surfaces. Its edge is found in a circular disc, and It is in 2/3 of the circle. It is helpful in scraping large size bearings. For this, the large bearing surface is scraped by longitudinal stroke or with circumferential movement. Scrapers 24 June 2019 / ‹#› Types of Scrapers Two Handle Scraper It is used to scrape large flat surfaces and also used to scrape large curved surfaces. Hook Scraper Its shape is like a flat scraper, but its point is bent at an angle of 90 °. Therefore, where a flat scraper cannot be used, it is used. It is often used for finishing work. Scrapers 24 June 2019 / ‹#› Scraping Techniques Before embarking on any scraping operation, it is imperative to : prepare the workpiece's surface adequately. cleaning and the application of a pigment or marking media. Scraping Pigments The pigments, serve as essential aids in detecting irregularities and achieving precise scraping results. The following pigments are often used: (a) Prussian Blue (b) Lamp Black (c) Red Lead mixed with oil Proper technique and the right scraper for the job are crucial to achieving the desired surface finish and component accuracy Scrapers 24 June 2019 / ‹#› What is the major limitation of scrapers? The major limitation of scrapers is that they can potentially damage or scratch the scraped surface. FASTENERS OPITO OUTCOMES COVERED KNOWLEDGE CRITERIA K 1.12 Screws, washers, nuts and bolts: types and uses Fasteners 24 June 2019 / ‹#› FASTENERS Bolts, nuts and washers are some of the most common industrial fasteners in use. The same task is carried out by all fasteners: connecting and fastening two or more components mechanically. The performance and service life of the fastener, however, are considerably impacted by variations in type, quality, shape, and material. Fasteners 24 June 2019 / ‹#› Bolts What is a Bolt ? A bolt is an externally helical threaded fastener that fastens objects with unthreaded holes together. This is done by applying a twisting force (torque) to a matching nut. The bolt has an external thread requiring a matching nut with an internal thread. Unlike a screw, which holds objects together by the restricting motion parallel to the axis of the screw via the normal and frictional forces between the screw's external threads and the internal threads in the objects to be fastened, Fasteners 24 June 2019 / ‹#› Bolts Bolt components Fasteners 24 June 2019 / ‹#› Bolts Bolt Type of threads Basic Nomenclature: A screw or bolt size is typically written. Diameter – Thread Pitch X Length. Define your units. Are you working in Standard (UTS) or Metric (ISO)? UTS : Unified Thread Standard , For screw threads commonly used in the (USA) /Canada ISO: Fasteners 24 June 2019 / ‹#› Bolts Bolt Type of threads Examples 1/4-20 (Diameter-Thread Pitch) describing a screw or bolt with 1/4" diameter and 20 full threads per 1" of threaded region. A M8-1.0 would indicate a screw or bolt with an 8mm diameter and a 1 mm distance between one peak of thread to the next (fine thread). Fasteners 24 June 2019 / ‹#› Bolt Type of threads What Diameter? METRIC: a Capital M is used to signify METRIC, and the diameter. This diameter is in millimeters (mm) even though it is written starting with a capital M. Table is continued in the next page … Fasteners 24 June 2019 / ‹#› Bolt Type of threads What Diameter? UTS : When working in inches, UTS, if the diameter is under ¼”, instead of using fractions, a # (Number) system is used. #0 - #12 (these are broken down in increments of 0.0130”) Table is continued Fasteners 24 June 2019 / ‹#› What Diameter? UTS Designation Basic designation syntax: Nominal Diameter in Inch Fraction Pitch in TPI Series: UNC / UNF / UNEF / UN Class: 1A, 2A, 3A, 1B, 2B or 3B Series: UNC – Unified Inch Coarse Thread Series UNF – Unified Inch Fine Thread Series UNEF – Unified Inch Extra Fine Thread Series Class: The class is defined by a two-character code. The first character is a digit between 1 and 3. 3=Tight fit, 2=Medium fit, and 1=Loose fit The second character is a letter. A=External thread and B=Internal thread. Fasteners 24 June 2019 / ‹#› Bolt Type of threads Thread Types: There are 2 major thread styles: 1. Machine Screw Thread - 60° thread angles designed to go into a TAPPED hole or mate with a threaded nut 2. Spaced Screw Thread - have a gap or flat between threads and designed to go into holes WITHOUT threads. Fasteners 24 June 2019 / ‹#› Bolt Type of threads Thread Types: Machine Thread Assign the grade of the following: 1. Machine Thread 2. Type 1 3. Trilobular 4. Type 23 5. Type F 6. Type C Fasteners 24 June 2019 / ‹#› Bolt Type of threads Thread Types: Machine Screw Thread: Also referred to as 60° Screw Threads are designed to thread into a hole or nut that is pre-tapped to form a mating thread for that screw. Machine screw thread is the most common type of thread one interacts with daily as it used in applications where something is unscrewed and then tightened again or something which needs to be tightly torqued. Whenever you see a nut and bolt, these are locked together with machine screw thread. Fasteners 24 June 2019 / ‹#› Bolt Type of threads Thread Types: Self-Tapping Screws: Type A Spaced Screw Thread Type A - Denotes Coarse Thread version of a self-tapping screw and was designed for self- starting in thin (.015" to.050" thick) metal or resin-filled plywood. Type AB Spaced Screw Thread - Type AB - Denotes Fine Thread version of self-tapping screw and was designed for use in the thinner sheet metal commonly used today, particularly in appliances. Fasteners 24 June 2019 / ‹#› Bolt Type of threads Thread Types: Self-Tapping Screws: High-Low Screw Thread - This thread design has a “Double Lead”. There are 2 different SPACED thread splines spiralling around the shank of the screw. One thread or “Lead” is higher than the other (Hence the name "High-Low"). This thread allows for an easier and faster installation due to the larger distance between threads allowing 1 turn (revolution) of the screw to move further into the workpiece. Concrete screws often share this similar thread design. Trilobular Screw Threads - (Used for Plastic) Thread Rolling Screws form their own thread in a plastic. Also referred to as Thread Forming Screws or by their brand name Plastite®, this design is ideal for plastics. Commonly used in housings for household appliances, assembly housings such as vacuums, power tools and kitchen products. Fasteners 24 June 2019 / ‹#› Bolts Bolt Head Bolts use a wide variety of head designs, as do screws. These are designed to engage with the tool used to tighten them. Common bolt heads include : ▪ Hex Head, ▪ Slotted hex washer Head, and ▪ Socket cap Head Bolt materials Depending on required strength and circumstances, there are several material types can be used for fasteners. Steel fasteners (grade 2,5,8) - the level of strength Stainless steel fasteners Bronze and brass fasteners - water proof usage Nylon fasteners - used for the light material and water proof usage. In general, steel is the most commonly used material of all fasteners: 90% or more. Fasteners 24 June 2019 / ‹#› Bolts Markings in Bolts The particular markings found in the head of bolts and nuts are a distinct feature that characterizes their manufacturing quality. They identify the grades or standards of the bolts. It determines their capacity for strength and durability Some sizes of bolts that are small in diameter can lack the identification mark on the head. Fasteners 24 June 2019 / ‹#› Bolts Markings in Bolts British Common Grades of Steel Fasteners Steel is a common type of material used in the production of fasteners. These are the following grades of steel: Grade 2: the common and less expensive steel perfect for the high precision requirement Grade 5: processed to harden in quality and increase the strength of automotive applications Grade 8: the hardest type among all three and is used in critical and stressful applications Fasteners 24 June 2019 / ‹#› British Common Grades of Steel Fasteners Fasteners 24 June 2019 / ‹#› Bolts Markings in Bolts Metric common Grades of Steel Fasteners These are the following grades of steel: 5.6: Mild steel 8.8: High tensile steel (commonly used on hex head fasteners) 10.9: Commonly used in the automotive industry 12.9: Commonly used in the automotive industry 14.6: High-grade steel used in pressure-critical applications. Fasteners 24 June 2019 / ‹#› Bolts Markings in Bolts Fasteners 24 June 2019 / ‹#› Bolts Metric and Imperial Marking methods Comparison between two different Standards :British/USA & Metric system Fasteners 24 June 2019 / ‹#› Bolts Metric and Imperial Marking methods More Details about British /USA system: Fasteners 24 June 2019 / ‹#› Bolts Metric and Imperial Marking methods More Details about Metric System: Fasteners 24 June 2019 / ‹#› Bolts Metric and Imperial Marking methods More Details about Metric System: Fasteners 24 June 2019 / ‹#› Bolts Metric and Imperial Marking methods Stainless Steel Bolt Marking EXAMPLE: Fasteners 24 June 2019 / ‹#› Bolts Metric and Imperial Marking methods EXERCISE Extract the bolts with Metric grading Extract the bolts with British grading Extract the bolts which are Stainless Steel Fasteners 24 June 2019 / ‹#› Bolts Metric and Imperial Marking methods EXERCISE Assign the grade of the following: 1. 1A 2. 1B 3. 3D 4. 4C 5. 2C Fasteners 24 June 2019 / ‹#› Bolts Metric and Imperial Marking methods Stainless Steel Bolt Marking Fasteners 24 June 2019 / ‹#› Sizes of Bolts and their Spanners/Keys Below are some common spanner (wrench) sizes for metric screw threads. Hex head widths are for DIN 934 hex nuts and hex head bolts. Other (ISO 4162) sizes may occur to reduce weight or cost, eg. M6 small series flange bolts have 8mm hexagonal heads, as would normally be found on M5 bolts Fasteners 24 June 2019 / ‹#› Bolt Torque Tables: Use Torque wrench , by monitoring the degree of beam deflection, the applied torque can be determined. Note: The table is a sample for stainless steel bolts grade 316 Refer to the tables for other grades Fasteners 24 June 2019 / ‹#› Bolts Types : Carriage Bolts Carriage Bolts provide simple installation and versatility when assembling a variety of building materials, not only with hardened steel, but also for softer materials like wood & plastic. They are designed with a smooth, large diameter head that resists pull-through in softer materials and a square neck that prevents the bolt from turning when tightening the nut. Flange Bolts Flange bolts have a round flange beneath the head that distributes the load like a washer. Because of this feature, it’s the preferred choice for metal to metal fastening. Fasteners 24 June 2019 / ‹#› Hex head bolts Hex bolts, sometimes called machine bolts, are structural fasteners that have hexagonal heads and machine threads. They’re meant to be used with a nut and washer as part of a total fastener assembly. They may also be installed directly into a tapped hole. Fasteners 24 June 2019 / ‹#› Square Head Bolts Square head bolts are utilized in applications where strong fastening is needed but visibility is restricted. These bolts are simple to tighten with a wrench and have large, flat sides. Square heads work best in small, dim areas where a fabricator or machinist must blindly tighten the bolt. Even without any visible marks, it is easy to fit a tool across the square head, reducing the likelihood of tool slippage. Square screw Driver Fasteners 24 June 2019 / ‹#› Socket head cap screws/ Allen Bolt Threaded fasteners with a recessed hexagon drive and a cylindrical head. Also referred to as Allen head screws, are tightened to far greater torque standards than a crossed recessed or slotted drive fastener. In circumstances where there is not enough clearance to utilize a fastener with an exterior hexagon head, socket head cap screws are frequently used. Fasteners 24 June 2019 / ‹#› Eye Bolt Mainly used in an assembly to lift or suspend a load (usually a machine), eye bolts are characterized by a loop in one end & a threaded rod on the other. Stud bolt Stud Bolts are solid bars with a circular cross section that is fully threaded. They are used with 2 hexagonal nuts to commonly connect flanges for pipeline, drilling, petroleum / petrochemical refining and other industries requiring sealing and flange connections. Fasteners 24 June 2019 / ‹#› Dynabolt A dynabolt is a general purpose all steel medium duty sleeve anchor mainly used for masonry and concrete, and it features a split expansion sleeve over a threaded stud bolt body and integral expander, nut and washer. In order to anchor it to the base material, torque is applied at the nut or screw of the dynabolt, where an internal expander causes the expansion sleeve to expand & grip the hole tightly. U-Bolt A “U”-shaped curved bolt having threaded holes on both ends Are used to support piping. Fasteners 24 June 2019 / ‹#› Screws Lag Screw/ Bolt Lag screws, sometimes called a lag bolt, are similar to hex head bolts, with the only difference that it has wood threads instead of machine threads. Because of this, they are mainly used in heavy lumber & similar materials to bear a heavy load. Countersunk-headed screw/ bolt A countersunk screw, often referred to as a flat-head screw, is a specific kind of screw that is intended to lay flush with the item or surface into which it is placed. Because they “sink” into objects and surfaces, they are known as “countersunk screws.” They have a flat head that tapers along the shaft. Fasteners 24 June 2019 / ‹#› Screws Types of Screws: In the field of industrial lightweight construction, basically there are two types : 1. self-tapping (also called thread-cutting) 2. self-drilling screws. Diameter Screws for industrial lightweight construction usually have a diameter of 4.8 mm to 8.0 mm Fasteners 24 June 2019 / ‹#› Screws Self-tapping screws Self-tapping screws are screws assembled with sealing washers without drill points. Self-tapping screws seal the bore hole towards the outside and thus protect it from wetness. They are therefore mainly used in outdoor areas on facades or roofs. Since the screws do not have a drill point, a through hole must first be made in a previous work step. However, the thread is then formed automatically in the screwing process. Fasteners 24 June 2019 / ‹#› Screws Self-tapping screws Fasteners 24 June 2019 / ‹#› Screws Fasteners 24 June 2019 / ‹#› Screws Self-drilling screws The self-drilling screws represent a further improvement of the screws assembled with sealing washers. Here, the thread-forming screws are combined with a cutting drill point. They are called self-drilling screws, as there is no need to pre-drill the substructure. The classic self-drilling screws are suitable for parts made of different materials such as steel or aluminium Fasteners 24 June 2019 / ‹#› Screws Self-drilling screws Fasteners 24 June 2019 / ‹#› Screws Self-drilling screws Based on their drilling Capacity, two types capacities can be recognized: 1. Low drilling capacity. 2. Large drilling capacity Fasteners 24 June 2019 / ‹#› Screws Type of screw Heads A distinguishing feature between the various types of screws and bolts are their heads, which are designed to fulfil a particular function. A few are listed below: 1. Truss Head screw 2. Flat Head screw 3. Raised Head screw 4. Domed Head screw 5. Flange Head screw 6. Bugle Head screw 7. Pan Head screw Fasteners 24 June 2019 / ‹#› Screws Wood screw Sheet metal screw Type of screw Threads Metal Sheet / Wood Threads : 1. Type A 2. Type AB 3. Type B 4. Type 25 5. HI-LOW 6. Plastic Thread 7. Type PLAST 8. Type TEK 2 9. Type 17 Fasteners 24 June 2019 / ‹#› Screws Type of screw Points Bothe types self tapping and self drilling may have different types of point designs: 1. Spoon point screw 2. Tapping point screw 3. Drilling point screw 4. Type 17 point screw 5. Wing TEKs point screw Fasteners 24 June 2019 / ‹#› Screws Screw Shank Screw Shank is locating between the thread and the head of the screw, this is the blank portion of the screw. Why there is no thread geometry and there is a blank shank on this portion? Answer: First, when a screw that is fully threaded is driven into wood, this screw can connect two pieces of material together but it will not pull the two pieces against each other; once the head reaches the material, the screw will stop spinning. Having an unthreaded shank at the top allows the tip of a screw to pull the screw into the wood just as a regular screw would. Fasteners 24 June 2019 / ‹#› Screws Second, when a fully threaded screw is being screwed into metal the screw threads cause friction. This friction results in the screw heating up. This causes two flaws in the material: As the metal heats up it will begin to expand. Once it expands inside of a hole that was drilled for a specific sized screw, the screw will seize in the hole. At the same time, the materials overall strength has now also been compromised due to the heat. Overheating leads to a screw breaking and snapping. Fasteners 24 June 2019 / ‹#› Screws Fasteners 24 June 2019 / ‹#› Fasteners 24 June 2019 / ‹#› Nuts A nut is a type of fastener with a threaded hole. Nuts are almost always used in conjunction with a mating bolt to fasten multiple parts together. The two partners are kept together by a combination of their threads' friction (with slight elastic deformation), a slight stretching of the bolt, and compression of the parts to be held together. The most common shape today is hexagonal, for similar reasons as the bolt head: In applications where vibration or rotation may work a nut loose, various locking mechanisms may be employed Fasteners 24 June 2019 / ‹#› Nuts Fasteners 24 June 2019 / ‹#› Nuts Fasteners 24 June 2019 / ‹#› Nuts Coupling nuts A threaded fastener for joining two male threads, most commonly a threaded rod, but also pipes Flange nuts / Wedge Nuts Has a wide flange at one end that acts as an integrated washer. Hexagonal/ hex nuts Hex nuts have six sides. When no “locking” mechanism is needed, these nuts with internal threading are frequently used with machine-threaded bolts and screws. Wing Nut Has two large metal "wings", one on each side, so it can be easily tightened and loosened by hand without tools. Fasteners 24 June 2019 / ‹#› Nuts Cap Nut A nut with a domed end on one side is referred to as a cap nut. When paired with a threaded fastener that has an exterior male thread, the domed end encloses the external thread to either protect it or keep it away from neighbouring items. Lock nuts Lock nuts have a built-in mechanism inside the nuts to prevent itself from loosening from vibrations. Square nuts Four-sided nut. Compared to standard hex nuts, square nuts have a greater surface in contact with the part being fastened, and therefore provide greater resistance to loosening (though also greater resistance to tightening) Fasteners 24 June 2019 / ‹#› Nuts Castle nuts In contrast to slotted hex nuts, castle hex nuts have cylindrical slots that are roughly equal in length to the depth of the slot and somewhat smaller in diameter. Swage nut Used on sheet metal. It permanently anchors itself to the sheet metal by swaging the surrounding material. T - Nut Used to fasten a wood, particle or composite materials workpiece, leaving a flush surface. Fasteners 24 June 2019 / ‹#› Nuts Back Nut Back Nut is a superior plumbing fitting made from durable galvanized steel. Thanks to the galvanization process, this fitting is resistant to wear, rust, and water damage. A reliable choice for all of your plumbing needs. Conduit Locknut A conduit lock nut is a specialized fastener designed to secure threaded conduits and connectors. They're typically used in hard-to-reach areas like electrical junction boxes or enclosures that are exposed to wet conditions. Fasteners 24 June 2019 / ‹#› Washers A washer is a thin plate (typically disk-shaped, but sometimes square) with a hole (typically in the middle) that is normally used to distribute the load of a threaded fastener, such as a bolt or nut. Other uses are as a: Spacer, Spring (Belleville washer, wave washer), Preload indicating device, Locking device Reduce vibration (rubber washer). Fasteners 24 June 2019 / ‹#› Washers : Flat Type Washers defined by their outer and inner diameters also by their thickness Fasteners 24 June 2019 / ‹#› Washers : Serrated Type Serrated washers defined by their outer and inner diameters , also by their thickness Also by the number of serration is mentioned in addition to their elevation Diameter (d) d1 d2 s h Serrations M3 3.35-3.10 8 0.63-0.57 1.00-0.80 28 M4 4.40-4.10 10 0.94-0.86 1.40-1.15 32 M5 5.40-5.10 12 1.14-1.06 1.80-1.45 36 M6 6.40-6.10 14 1.34-1.26 2.10-1.75 45 M8 8.56-8.20 18 1.44-1.36 2.35-1.90 45 M10 10.56-10.20 22 1.65-1.55 2.75-2.25 45 M12 12.83-12.40 27 1.85-1.75 3.10-2.60 45 M14 14.83-14.40 30 2.46-2.34 3.70-3.20 45 M16 16.83-16.40 32 2.86-2.74 4.10-3.60 50 M20 21.02-20.50 40 3.26-3.14 4.90-4.30 50 Fasteners 24 June 2019 / ‹#› Washers Flat washers A flat annulus or ring, often of metal, used to spread the load of a screwed fastening. Additionally, a plain washer may be used when the hole is a larger diameter than the fixing nut Belleville washer, cupped spring washer or conical washer A washer with a slight conical shape, which provides an axial force when deformed. The surface may be serrated, which will have improved locking capabilities Curved disc spring Similar to a Belleville, except the washer is curved in only one direction, therefore there are only four points of contact. Unlike Belleville washers, they exert only light pressures Fasteners 24 June 2019 / ‹#› Washers Wave washers A washer with a "wave" in the axial direction, which provides spring pressure when compressed. Wave washers, of comparable size, do not produce as much force as Belleville washers. Split washer or spring lock washer A ring split at one point and bent into a helical shape. This causes the washer to exert a spring force between the fastener's head and the substrate, which maintains resistance to rotation. Spring washers are a left hand helix and allow the thread to be tightened in a right hand direction only, i.e. a clockwise direction. Fasteners 24 June 2019 / ‹#› Washers Toothed lock washer, serrated washer or star washer A washer with serrations that extend radially inward or outward to bite into the bearing surface. This type of washer is especially effective as a lock washer when used with a soft substrate, such as aluminium or plastic, and can resist rotation more than a plain washer on hard surfaces Tab washer A locking washer that works by having a side tab that can be bent into place against a nut. Metallic or non-metallic, the tab washer notch prevents rotation relative to the shaft or fastener. Fasteners 24 June 2019 / ‹#› Washers Wedge lock washer A hardened two-piece washer with radial teeth on the outside to grip both the fastener and mounting surface. The two halves of this washer form a wedge seam, which requires additional tension to be placed on the fastener in order for them to separate after tightening. While generally more expensive per piece, these washers provide the highest amount of vibrational loosening prevention Fasteners 24 June 2019 / ‹#› How to install ? Bolt , Washers ,Nut Fasteners 24 June 2019 / ‹#› Nut Splitter: As the name implies, it splits nuts. If you have a seized / Jammed nut, this tool will cut the nut in two, in position. Better types are hydraulic. Bolt Cutter OPITO OUTCOMES COVERED KNOWLEDGE CRITERIA K 1.13 Bolt cutters, component parts uses and care Bolt Cutter 24 June 2019 / ‹#› Bolt cutter Bolt cropper Is a tool used for cutting bolts, chains, padlocks, rebar and wire mesh. It typically has long handles and short blades, with compound hinges to maximize leverage and cutting force. A typical bolt cutter yields 20 kilonewtons (4,500 lbf) of cutting force for a 250 newtons (56 lbf) force on the handles. Bolt Cutter 24 June 2019 / ‹#› Bolt cutter Bolt Cutter Components The following components are making the bolt cutter: Blades Jaws Jaw Joint Blade adjustment Bolts Handle stop Handle Handle grip Bolt Cutter 24 June 2019 / ‹#› Bolt Cutter Components Jaws: The jaws form the head of a pair of bolt cutters and are forged separately from the handles. The part of the tool where the blades are connected to the handles is called the neck. They are secured in place by a pair of bolts. Blades: The blades are the actual cutting surfaces of the jaw section. They are made to be extremely hard and they come in a variety of configurations (such as centre cut or shear cut) to make them suitable for different uses. Bolt Cutter 24 June 2019 / ‹#› Bolt Cutter Components Joints Diagram of bolt cutter hinges, showing jaw joint bolts, middle bolts and handle bolt. The multiple joints on most bolt cutters are vital to the tool’s strength, as they compound – or multiply – the force applied to the handles. There are three key joints: 1. the handle bolt (which connects the two handles), 2. the middle bolts (which attach the jaws to the handles) 3. the jaw joint bolts (which keep the blades aligned). All three joints act as pivots when the jaws are opened and shut, and this compound arrangement helps to magnify the force that the user applies to the handles Bolt Cutter 24 June 2019 / ‹#› Bolt cutter Bolt Cutter Components Adjustment bolts Most bolt cutters (except fixed-head compact types) have one or two adjustment bolts on the neck which can alter the angle of the blade they are closest to. Where tools have two bolts, both blades can be adjusted. Labelled picture of adjustable jaw joint bolts on a pair of bolt cutters In addition, the bolts on the jaw plates can be turned to adjust the gap between the blades. Bolt Cutter 24 June 2019 / ‹#› Bolt cutter Bolt Cutter Adjustment – Neck Bolt Adjustment How to adjust the jaws on bolt cutters? Step 1 - Secure Bolt Cutters Place the head of your bolt cutters, jaws closed, in a vice, or hold the tool firmly between your knees. Step 2 - Turn Bolt Using an open-ended spanner, turn the adjustment bolt clockwise, moving the adjacent blade inwards towards the other blade. Bolt Cutter 24 June 2019 / ‹#› Bolt cutter Bolt Cutter Adjustment – Neck Bolt Adjustment How to adjust the jaws on bolt cutters? Step 3 - Repeat if Necessary If your tool has a second neck adjustment bolt, then turn the cutters over in the vice halfway through and turn this bolt, in the same manner, to draw in the other blade an equal distance. Step 4 - Check Gap Width with a Piece of Paper Once you have arrived at a narrow, equal gap between the jaws, take the tool out of the vice, open the arms slightly and clamp a single piece of paper between the blades. If you can pull out the piece of paper easily, they need closing a little further. If they clamp the paper lightly, then you have the gap just right. Bolt Cutter 24 June 2019 / ‹#› How to adjust the jaws on bolt cutters? Bolt Cutter Adjustment – Neck Bolt Adjustment Step 5 - Readjust if Necessary If the paper, when you release it, has a marked groove in it then the jaws are probably a little too tight and you need to slacken them off. Turn the adjustment bolt(s) anti-clockwise slightly to adjust the gap. There is no benefit in having the blades very tightly closed, as material is crushed, not sliced, between them. Over-tight jaws could result in damage to the hardened blade edges. Bolt Cutter 24 June 2019 / ‹#› Bolt cutter Bolt Cutter Adjustment – Jaw Bolt Adjustment Jaw Adjustment Bolts The adjustment bolts mounted on the jaws of bolt cutters can be used to alter the distance between the bevelled cutting edges along the length of the jaws. Turning the bolts will move the blades closer together or push them further apart, opening or closing the gap between them in its entirety. When would you use Jaw Adjustment Bolts? 1. After sharpening the blades on bolt cutters 2. When the neck adjustment bolts is not bringing the blades close enough together. These bolts should only be used rarely. The neck adjustment bolts are designed to be easier to operate on a regular basis and allow for more precise tuning as they can tilt the tips of the blades through a wider range of positions. Bolt Cutter 24 June 2019 / ‹#› Bolt cutter Bolt Cutter Components Handles Bolt cutter handles vary both in length and in the material they are made from, this makes a significant difference to their weight and usability. Longer lengths are helpful for cutting materials which are : - down low, up - out of reach - require a large amount of force, Short pairs are lightweight and useful for thinner materials which are easily within range. Bolt Cutter 24 June 2019 / ‹#› Bolt cutter Bolt Cutter Components Handle stops Regular long-handled bolt cutters often have a pair of metal protrusions (or “stops”) at the neck or a short way down the handles. These prevent the handles – and hence also the blades – moving too close together and overlapping at the end of a cut. Handle grips For extra comfort and tool control, most long-handled bolt cutters have grips at the end of the handles. Bolt Cutter 24 June 2019 / ‹#› Bolt cutter Blades There are different types of cutting blades for bolt cutters, including: Angle cut blade : Angle cut has the cutter head angled for easier insertion. Typical angling is 25 to 35 degrees Centre cut blade : Centre cut has the blades equidistant from the two faces of the blade. Shear cut blade : Shear cut has the blades inverted to each other (such as normal paper scissor blades) Clipper cut blade : Clipper cut has the blades flush against one face (for cutting against flat surfaces) Bolt Cutter 24 June 2019 / ‹#› Blades Centre cut blade : Clipper cut blade : Shear cut blade : Angle cut blade : The bolt cutters with clipper cut blades are designed especially for cutting flush against a (concrete) wall or roof panel. The clipper cut blades ensure that your hands stay free of the surface. Bolt Cutter 24 June 2019 / ‹#› Additional designs Additional variants designs of Bolt Cutters: End cut Ratchet bolt cutters Eelectric Power Cutter Hydraulic bolt cutters Bolt Cutter 24 June 2019 / ‹#› Bolt cutter Bolt Cutter Size The size of the bolt Cutter is measured by its length The length is measured from the tip of the jaw to the end of the handle. Bolt cutters are usually available in : 12, 14, 18, 24, 30, 36 and 42 inches 30.5, 35.6, 46, 61, 76, 91.4 and 107 cm. Bolt Cutter 24 June 2019 / ‹#› Bolt cutter Electrician Bolt Cutter Bolt cutters with fiberglass handles can be used for cutting live electrical wires and are useful during rescue operations. The fiberglass handles have another advantage of being lighter in weight than the conventional drop forged or solid pipe handles, making it easier to carry to the place of operation. Bolt Cutter 24 June 2019 / ‹#› Typical Bolt Cutter information: Weight 1,70 kg Length 450mm (18") Capacity (mm.) 500N/mm2 Ø 8 Capacity (mm.) 40HrC Ø 6 Example: Soft & Medium Cutting Max Capacity: 7/16'' (1.1 cm) Hard Material Cutting Max Capacity: 5/16'' (0.8 cm) Bolt Cutter 24 June 2019 / ‹#› What is HRC? Hardness of steel according to the rockwell scale (HRC) Hardness refers to the ability of a material to resist local deformation, especially plastic deformation, indentation or scratches. Carbon is the chemical element that has the greatest impact on the hardness of steel Bolt Cutter 24 June 2019 / ‹#› What is HRC? Hardness of steel according to the Rockwell scale (HRC) There are many methods to measure material hardness, however the most common methods is: Rockwell hardness HRC Rockwell scale starts from : 20.3 HRC (770 Mpa) to 57.8 HRC (2180 Mpa) From 58.3 to the end of the scale at 68 HRC , compared to other hardness methods. Assembly-Disassembly Procedure OPITO OUTCOMES COVERED KNOWLEDGE CRITERIA K 1.14 Simple dismantling and assembly procedures Assembly-Disassembly Procedure 24 June 2019 / ‹#› Art of Disassembly and Assembly Introduction Disassembly and assembly are essential processes when it comes to, appliances, machinery, and various other items. Mastering the art of disassembly and assembly is a valuable skill that can save time, money, and frustration in various situations. By following best practices and safety precautions, you can confidently tackle any disassembly and assembly project with ease. Importance of Disassembly and Assembly Disassembly and assembly allow for easier transportation, storage, and maintenance of items. By breaking down larger objects into smaller components, they become more manageable and less prone to damage during handling or relocation. Assembly-Disassembly Procedure 24 June 2019 / ‹#› Art of Disassembly and Assembly Disassembly Definition Disassembly, on the other hand, refers to the process of taking apart a product, system, or structure into its individual components or parts. It is often done for maintenance, repair, or replacement purposes. Disassembly can be a complex and time-consuming task, requiring specialized tools, skills, and knowledge. It involves careful planning, documentation, and organization to ensure that the parts are not damaged or lost during the process. Disassembly can also have environmental and social implications, such as the disposal of hazardous materials or the impact on local communities. Assembly-Disassembly Procedure 24 June 2019 / ‹#› Art of Disassembly and Assembly Disassembly Example. Assembly-Disassembly Procedure 24 June 2019 / ‹#› Art of Disassembly and Assembly Assembly Definition The assembly of a machine, device, or object is the process of fitting its different parts together. It is often done for maintenance, repair, or replacement purposes. Assembly can be a complex and time-consuming task, requiring specialized tools, skills, and knowledge. It involves careful planning, documentation, and organization to ensure that the parts are not damaged or lost during the process. Assembly can also have environmental and social implications, such as the disposal of hazardous materials or the impact on local communities. Assembly-Disassembly Procedure 24 June 2019 / ‹#› Art of Disassembly and Assembly Disassembly Example. Assembly-Disassembly Procedure 24 June 2019 / ‹#› Art of Disassembly and Assembly Maintenance Procedure The assembly /De-Assembly action is an action need to be performed based on written approved procedure. Most likely the vendor or the manufacturer will provide such a dedicated procedure to ensure maximum performance and safety aspects. Assembly-Disassembly Procedure 24 June 2019 / ‹#› Art of Disassembly and Assembly Maintenance Procedure The PDCA cycle makes sure that, in real time, new hires and even team members with prior knowledge and know-how can follow the docs to ensure both quality assurance and quality control. To start the PDCA workflow, the employee who knows and regularly performs a specific procedure should be the one to plan, develop, and write the first draft of that procedure. We call this person the “subject-matter expert” (SME) Assembly-Disassembly Procedure 24 June 2019 / ‹#› Art of Disassembly and Assembly Maintenance Procedure Maintenance procedures are steps or actions that are taken to keep something in good condition or working order Examples of maintenance procedures include: Cleaning, visual inspection, functional tests, lubrication, measurement of operating quantities and oil tests for machines or equipment Replacing and maintaining damaged parts, inspecting equipment status, this requiring assembly disassembly expertise Following safety precautions, using instruction manuals, specialized tooling, test equipment, spare parts, and consumables for maintenance tasks Carrying out maintenance as soon as possible, avoiding product contamination, and disposing of loose pieces after maintenance Assembly-Disassembly Procedure 24 June 2019 / ‹#› Art of Disassembly and Assembly Maintenance Procedure Essentials Detailed and carefully written procedure steps are essential to: Protecting the health and safety of your employees, including listing the personal protective equipment (PPE) necessary to carry out the standard maintenance procedure Ensuring that everyone performs the routine maintenance procedure as required Making it easier for standards and regulations to be followed Increasing asset and equipment reliability Training new employees Providing accident investigation information Making sure process safety rules are followed. Poorly written procedures are generally less effective, can be unsafe, and can cause equipment downtime. Assembly-Disassembly Procedure 24 June 2019 / ‹#› Step-by-Step Guide to Disassembly and Assembly Preparing the Workspace Disassembling the Item Organizing and Labeling Components Assembling the Item Preparing the Workspace Clear the area where you’ll be working and gather all necessary tools and equipment. Lay down a protective covering to prevent damage to floors or surfaces. Disassembling the Item Refer to manufacturer instructions, if available, for guidance on disassembly. Begin by removing any visible screws or fasteners and work methodically to disassemble the item one component at a time. Assembly-Disassembly Procedure 24 June 2019 / ‹#› Step-by-Step Guide to Disassembly and Assembly Organizing and Labelling Components As you disassemble the item, keep track of all components and hardware. Use containers or bags to store small parts and label them accordingly to ensure easy identification during assembly. Assembling the Item Follow the disassembly process in reverse order to reassemble the item. Refer to any notes or photographs taken during disassembly to ensure that components are correctly aligned and attached. Assembly-Disassembly Procedure 24 June 2019 / ‹#› Tips for Efficient Disassembly and Assembly Planning Ahead Before starting the process, take time to plan and organize your approach. Gather all necessary tools and materials, and allocate sufficient time to complete the task without rushing. Following Manufacturer Instructions Whenever possible, refer to the manufacturer’s instructions for disassembly and assembly procedures. These guidelines are tailored to specific items and can help ensure a successful outcome. Assembly-Disassembly Procedure 24 June 2019 / ‹#› Tips for Efficient Disassembly and Assembly Seeking Professional Assistance if Needed If you encounter difficulties or feel unsure about disassembling and assembling a particular item, don’t hesitate to seek professional assistance. Professional movers or repair technicians have the expertise and experience to handle complex tasks safely and efficiently. Assembly-Disassembly Procedure 24 June 2019 / ‹#› Common Challenges and Solutions Missing Parts or Hardware If you discover missing parts or hardware during disassembly, consult the manufacturer or consider purchasing replacement components. Alternatively, improvise using similar-sized hardware if feasible. Alignment Issues Alignment issues may arise during assembly, especially with complex or multi- part items. Take your time to adjust and align components properly, and refer to manufacturer instructions or diagrams for guidance. Damaged Components Inspect components for damage or wear during disassembly and assembly. Replace any damaged parts to ensure the integrity and functionality of the item. Assembly-Disassembly Procedure 24 June 2019 / ‹#› Safety Precautions Using Protective Gear Wear appropriate protective gear, such as gloves and safety goggles, to prevent injuries during disassembly and assembly. Use caution when handling sharp or heavy objects. Handling Heavy or Fragile Components with Care Exercise caution when handling heavy or fragile components to avoid accidents or damage. Enlist the help of others for lifting and manoeuvring bulky items safely. Assembly-Disassembly Procedure 24 June 2019 / ‹#› Benefits of Proper Disassembly and Assembly Extend the Lifespan of Items Regular disassembly and assembly can help prolong the lifespan of furniture, appliances, and equipment by facilitating maintenance and repairs as needed. Facilitate Transportation and Storage Disassembled items take up less space and are easier to transport and store, making them ideal for relocation or temporary storage. Prevent Damage During Relocation Properly disassembling and securing items before moving reduces the risk of damage during transit, ensuring that your belongings arrive at their destination intact. Assembly-Disassembly Procedure 24 June 2019 / ‹#› Introduction Disassembly and assembly are essential processes when it comes to, appliances, machinery, and various other items. knowing how to properly disassemble and reassemble items is crucial for a smooth and efficient experience. Basic Tools for Disassembly and Assembly Common tools required for disassembly and assembly include: screwdrivers, wrenches, pliers, and Allen keys. Having a well-equipped toolkit on hand ensures that you have everything you need to tackle the task efficiently. POWER TOOLS 24 June 2019 / ‹#› THANK YOU