Local Working Arrangements: Al Nairyah Depot PDF
Document Details
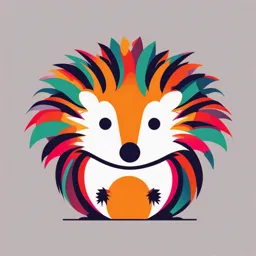
Uploaded by CureAllLlama3114
null
2022
Tags
Related
- Miami-Dade County, Florida, Firefighters CBA 2020 PDF
- Sec 2 Chap 7 British Rule After WWII PDF
- Collective Bargaining Agreement Lexington-Fayette Urban County Government & IAFF Local 526 PDF
- Curriculum Vitae Osman Reyniery Padilla Montoya PDF
- SAR Local Working Arrangements Al Nairyah Depot PDF
- 2023-2025 Collective Bargaining Agreement (City of Tacoma PDF)
Summary
This document details local working arrangements at the Al Nairyah Depot for the Saudi Railway Company. It outlines procedures for site safety and layout, responsibilities for various personnel, and communication protocols. The document also includes information on site hazards, train arrival and departure, and operational activities.
Full Transcript
Function: Freight Business Unit Dept.: Operations Management Doc. Title: Local Working Arrangements: Al Nairyah Depot...
Function: Freight Business Unit Dept.: Operations Management Doc. Title: Local Working Arrangements: Al Nairyah Depot Doc. No.: SAR-005-100-2-003 Rev. No.: 02 Effective Date: 28 March 2022 Saudi Railway Company P.O. Box: 7032 Riyadh 13422 Kingdom of Saudi Arabia [I] Internal Department: Operations Management Function: Freight Business Unit Document Title: Local Working Arrangements: Al Nairyah Depot Document information Information Document Owner Freight Business Unit Director Document Language / ☒English / ☐other Click here to enter text. Distribution list Name Dept. Andi Hucker Rolling Stock Maintenance Phil Jerstice Freight Business Unit Fahad Al Musaiteer Network Planning & Management Mohammed Bawazeer Infrastructure Maintenance & Management Document Approvals Description Job Title Name Signature Date Initiated by Train Operations Expert William Williams 16-Mar-22 Reviewed by Freight Train Operations Senior Manager Turky A. Bin Suwaidan 17-Mar-22 Accepted by CEO Advisor and SRG Chair Perry Ramsey 13-Apr-22 Approved by Freight Train Operations Director Phillip Jerstice 17-Mar-22 This document contains proprietary and confidential information. All information, data and materials submitted to the Recipient in electronic or written form shall be used solely for the purpose of which it was furnished dealings with the Saudi Railway Company (SAR). It’s the Recipient responsibility to inform its employees or agents who have access to its content of its confidential nature. Recipient's obligations with respect to the protection of Discloser's Proprietary Information shall be to use the same reasonable degree of care which Recipient uses to protect its own information of similar character. Upon discovery of any such inadvertent disclosure, Recipient shall endeavour to correct the effects thereof and to prevent any further inadvertent disclosure Saudi Railway Company (SAR) retains all title, ownership and intellectual property rights to the material and trademarks contained herein, including all supporting documentation, files, marketing material, and multimedia. BY ACCEPTANCE OF THIS DOCUMENT, THE RECIPIENT AGREES TO BE BOUND BY THE AFOREMENTIONED STATEMENT. All PRINTED COPIES OF THIS DOCUMENT ARE UNCONTROLLED UNLESS OTHERWISE INDICATED BY CCD Document No.: Rev. No.: [I] Internal Effective Date: SAR-005-100-2-003 02 28 March 2022 Department: Operations Management Function: Freight Business Unit Document Title: Local Working Arrangements: Al Nairyah Depot CONTENTS: 1 Purpose......................................................................................................................................................................... 5 2 Objective....................................................................................................................................................................... 5 3 Scope:........................................................................................................................................................................... 5 4 Definitions and abbreviations........................................................................................................................................ 5 5 Responsibilities.............................................................................................................................................................. 7 5.1 Mineral and Cargo Operations Manager....................................................................................................................... 7 5.2 Nairyah Depot Manager................................................................................................................................................ 7 5.3 On-Board Supervisor in conjunction with the Nairyah Train Masters/Nairyah Yard Supervisor.................................... 7 5.4 Off-Board Supervisor in conjunction with the Nairyah Yard Supervisor......................................................................... 7 5.5 Nairyah Yard Foreman.................................................................................................................................................. 7 5.6 SAR PIC........................................................................................................................................................................ 4 5.7 Locomotive Shop Supervisor......................................................................................................................................... 4 5.8 Wagon Shop Supervisor................................................................................................................................................ 4 5.9 Track Maintenance Building Supervisor........................................................................................................................ 4 PART A – SITE SAFETY AND LAYOUT................................................................................................................................... 9 6 Location......................................................................................................................................................................... 9 6.1 Site Access.................................................................................................................................................................... 9 6.2 SITE MAPS................................................................................................................................................................... 9 6.3 General site requirements - SAR policies.................................................................................................................... 13 6.4 Use of Company Vehicles within Nariyah Depot…................................................................................................................ 13 7 SAFETY...................................................................................................................................................................... 13 7.1 Adverse Weather Reporting........................................................................................................................................ 13 7.2 Fire.............................................................................................................................................................................. 13 7.3 Accident/Incident Management................................................................................................................................... 13 7.3.1 Procedure.................................................................................................................................................................... 13 8 Communications.......................................................................................................................................................... 13 8,1 Language requirements............................................................................................................................................... 13 8.2 Radio usage................................................................................................................................................................ 14 8.3 Mobile phones............................................................................................................................................................. 14 8.4 Language protocol....................................................................................................................................................... 14 PART B – Site Specific Details and requirements.................................................................................................................... 15 9 Additional PPE requirements for Nairyah.................................................................................................................... 15 9.1 PPE for Nairyah shunting staff and drivers.................................................................................................................. 15 10 Site Hazards................................................................................................................................................................ 16 10.1 Control of Level Crossings.......................................................................................................................................... 16 10.2 Crossing Over Wagons to gain access/egress from Fuel Shed.......................................................................................... 17 11 Train arrival and departure.......................................................................................................................................... 17 11.1 TRAIN ARRIVALS NORTHBOUND:............................................................................................................................ 17 11.2 TRAIN ARRIVALS SOUTHBOUND:........................................................................................................................... 17 Document No.: Rev. No.: [I] Internal Effective Date: SAR-005-100-3-003 02 28 March 2022 Department: Operations Management Function: Freight Business Unit Document Title: Local Working Arrangements: Al Nairyah Depot 11.3 TRAIN DEPARTURES NORTHBOUND:.................................................................................................................... 19 11.4 TRAIN DEPARTURES SOUTHBOUND:..................................................................................................................... 19 12 Operational activity of the site...................................................................................................................................... 19 12.1 Speeds........................................................................................................................................................................ 19 12.2 Nairyah Yard Inspection & Shunting Sheet................................................................................................................. 19 12.3 Required train documentation..................................................................................................................................... 19 12.4 Shunting of Trains....................................................................................................................................................... 19 12.4.1 General Shunting Duties............................................................................................................................................. 19 12.4.2 Job Brief....................................................................................................................................................................... 19 12.5 Operation of LFOP & Zone Control............................................................................................................................. 19 12.6 Shunting Movements................................................................................................................................................... 19 12.7 Stabling Vehicles......................................................................................................................................................... 19 Handbrakes............................................................................................................................................................................. 26 12.8 DEPOT PROTECTION............................................................................................................................................. 266 13 Train Processing Nariyah Depot...............................................................................................................................................26 13.1 Processing By-pass-Underframe Inspection Trains............................................................................................................. 26 PART C Locomotive and Wagon Maintenance..................................................................................................................... 26 14.1 Person in ChargeWagon Maintenance Shop.............................................................................................................. 26 14.2 Movements in or out of the WMS area........................................................................................................................ 26 14.3 Movements by WMS................................................................................................................................................... 26 14.3.1 Vehicles which are required for maintenance or repair............................................................................................... 26 14.3.2 Vehicles which are required collection from maintenance or repair............................................................................. 26 14.3.3 Vehicle in section prior to moving following collection from WMS............................................................................... 26 14 Locomotive Maintenance Shed (LMS)......................................................................................................................... 27 14.1 Person in Charge........................................................................................................................................................ 27 14.2 Locomotive Movement Request................................................................................................................................... 27 14.2.1 Locomotive delivery to the LMS.................................................................................................................................. 27 14.2.2 Locomotive collection/change of track from LMS........................................................................................................ 27 15 Locomotive Maintenance Shed................................................................................................................................... 28 15.1 Person in Charge........................................................................................................................................................ 28 15.2 Locomotive Movement Requests................................................................................................................................. 28 15.2.1 Locomotive Delivery to the LMS.................................................................................................................................. 20 15.2.2 Internal On-Track Machine movements...................................................................................................................... 20 16 Track Maintenance Building........................................................................................................................................ 30 17 RECORDS.................................................................................................................................................................. 30 18 REFERENCES............................................................................................................................................................ 30 19. DOCUMENT HISTORY............................................................................................................................................................ 30 APPENDIX A: Nairyah Depot Train Input Form........................................................................................................................ 30 APPENDIX B: Certificate of Closure........................................................................................................................................ 30 APPENDIX C: Dangerous Goods Transportation Invoice (if available).................................................................................... 30 APPENDIX D: Dangerous Goods Documentation and Equipment Check List Form............................................................... 30 Document No.: Rev. No.: [I] Internal Effective Date: SAR-005-100-3-003 02 28 March 2022 Department: Operations Management Function: Freight Business Unit Document Title: Local Working Arrangements: Al Nairyah Depot APPENDIX E: Defect Cards..................................................................................................................................................... 30 APPENDIX F: Track Access Protection Form.......................................................................................................................... 30 APPENDIX G: Nariyah Yard Inbound Inspection and Hand Over Form.......................................................................................... 31 APPENDIX H: Driving Authorization Form........................................................................................................................................... 32 APPENDIX J: Locomotive Fitness for Service & Handover Checklist…......................................................................................... 33 APPENDIX K: Wagon Cut In Form........................................................................................................................................................ 34 APPENDIX L: Locomotive Underframe Inspection Fitness for Service & Handover Checklist…................................................ 35 Document No.: Rev. No.: [I] Internal Effective Date: SAR-005-100-3-003 02 28 March 2022 Department: Operations Management Function: Freight Business Unit Document Title: Local Working Arrangements: Al Nairyah Depot 1 Purpose: This Local Working Arrangements (LWA) describes the operations carried out at Al Nairyah Depot for the inspection and maintenance of locomotives, vehicles and rail operations. These Arrangements also apply to the shunting and preparation of freight trains. It is the duty of all staff to ensure that they understand (and carry out) their obligations, as described in this document. 2 Objective: The objective of this document is to define the Local Working Arrangements for the inspection and maintenance of locomotives and vehicles, along with the shunting and preparation of freight trains at the Al Nairyah depot. 3 Scope: This document is applicable to the following locations contained within the boundary of Al Nairyah: Loco Maintenance Shop Wagon Maintenance Shop Fuel Point Track Maintenance Siding Zones 1 – 9 4 Definitions and abbreviations: Term Description Air Hose The flexible pipes that are fitted to the headstocks of vehicles and are connected between vehicles by means of a coupling head. When connected, the hoses allow pressurised air to flow between (and into) each vehicle. This is to enable vehicle-mounted, air-operated equipment to function (i.e. air brakes / door operating systems). Air Pipe Cock A valve fitted at the fixed end of the air hose and operated by a rotating handle. When opened, the rotating handle will allow air to flow through the air hose. When closed, it will prevent the flow of air through the hose. Automatic A vehicle coupling device whose operation requires no manual handling. It is operated by a Coupling single (release) lever, which is controlled by the Shunter, providing he is standing in a safe position to the side of the vehicle headstock. Conductor A train driver or shunter who has knowledge of either the vehicle or the track layout and is responsible for advising the driver of the machine which the conductor is traveling in. Dead A locomotive that cannot be operated under its own power and needs to be towed by another Locomotive operable locomotive. Draw Gear A generic term used to describe mechanical coupling components. Driver Qualified locomotive operator or machine operator Dummy A fitting that is attached to an air hose coupling head when the air hose is not in use. It secures Coupling the air hose and prevents dirt and moisture from getting into the hose. Vehicles left in such a position that they may come into contact with vehicles moving on an Foul adjacent track are referred to as Standing Foul. A location where this may occur is known as a ‘Fouling Point’. Document No.: Rev. No.: [I] Internal Effective Date: SAR-005-100-3-003 02 28 March 2022 Department: Operations Management Function: Freight Business Unit Document Title: Local Working Arrangements: Al Nairyah Depot Term Description Global System for Mobile Communication-Railway. International wireless communication GSM-R standard for railway communication and application Hauling A rail movement when the locomotive (and driver) is leading. Local Field Operations Panel. A panel which will allow the operator to move switches for the LFOP desired route to be set. LMS Loco Maintenance Shop. LWA Local Working Arrangements Locomotive A self-propelled motive power unit. Facility A self-propelled motive power unit dedicated to shunting and not for main-line operations. Locomotive Mobile A radio, GSM-R handset, telephone or any other device which permits two-way Communications communications. Device Multiple Unit Two or more locomotives coupled together and configured for operation from the leading unit. For the purposes of these Arrangements, multiple unit operation will include the towing of ‘dead’ locomotives. Not to be Moved A sign which indicates that the vehicle must not move under any circumstances. Only the Board person who applied the Board can remove it OCC Operations Control Centre is the location which provides Zone Control in Nairyah Person In The person responsible for rail activities and ensuring a safe system of work is in operation. Charge (PIC) The PIC is responsible for the Yard Shunt Team’s activities Pilot Assistant to the Driver. PPE Personal Protective Equipment. Propelling A rail movement when the locomotive (and driver) is at the rear end of a set of vehicles which are being pushed by the locomotive Protection Person responsible for ensuring a suitable Safe System of Work is in place to protect Officer individuals who are required to work on or near the line Radio A (hand-held) radio handset permitting two-way communication. RAT Run-Around Track. Rolling Stock Wheeled vehicles that run on railway lines that are either self- propelled (i.e. a locomotive) or vehicles that require attaching to a self-propelled vehicle (i.e. a vehicle) to enable them to be moved. RSM Rolling Stock Maintenance. RSM Zone The area which falls under the operational supervision of the RSM supervisor or foreman. This area is protected by Stop Boards and controlled by LFOP. Shunting The movement and positioning of rolling stock within the yard, as determined by operational or maintenance requirements. Solebar The load bed of the vehicles. Stop Board Indication of limit of movement without further authority Trains Master SAR manager who is responsible for the management and compliance of train drivers and pilots Document No.: Rev. No.: [I] Internal Effective Date: SAR-005-100-3-003 02 28 March 2022 Department: Operations Management Function: Freight Business Unit Document Title: Local Working Arrangements: Al Nairyah Depot Term Description Underframe A type of Inspection carried out on the Suspension tubes of SD70 Locomotives Vehicle(s) An item (or items) of rolling stock. Vehicle A list of activities to be carried out on rolling stock or locomotives which advises of task and Maintenance timescales for the task to be carried out Instruction (VMI) Wagon Alternative name for some types of vehicle. WMS Wagon Maintenance Shop WMS Foreman The Wagon Maintenance Shop (WMS) Foreman is to control movement to/from the WMS, including all internal movements within the WMS. Yard Shunt Dedicate personnel who undertake the movement and positioning of rolling stock within the Team yard Yard Supervisor The person responsible for all rail movements and shunting staff within the Nairyah complex 5 RESPONSIBILITIES: 5.1 Freight Train Operations Senior Manager The Freight Train Operations Senior Manager is responsible for: Initiating any changes to this procedure via the Document Controller in accordance with SAR-CCD-QUL01 “Document Control & Management Policy and Procedure” 5.2 Nairyah Depot Manager The Nairyah Depot Manager is responsible for all movements, maintenance, staff welfare and operations within the Locomotive Maintenance Shop, Wagon Maintenance Shop, Fuel Point and Yard Facility Building. The Nairyah Depot Manager is further responsible for ensuring that all staff and managers both understand and comply with this procedure 5.3 Mainline Section Head The Mainline section Head, with the assistance of the Nairyah Train Masters is to ensure drivers and pilots have a thorough understanding and comply with these Local Working Arrangements. 5.4 Terminals & Yards Section Head The Terminals & Yards Section Head, with the assistance the Nairyah Yard Supervisor is to ensure that groundstaff have a thorough understanding and comply with these Local Working Arrangements. 5.5 Nairyah Yard Supervisor The Nairyah Yard Supervisor will ensure that all operations staff working within Nairyah are briefed & fully understand the Local Working Arrangements Document No.: Rev. No.: [I] Internal Effective Date: SAR-005-100-3-003 02 28 March 2022 Department: Operations Management Function: Freight Business Unit Document Title: Local Working Arrangements: Al Nairyah Depot 5.6 Nairyah Yard Foreman The Yard Foreman (YF) will: Manage ground staff resource and organise the necessary resource to shunting activities across the YT, GFT and STT Tracks. Ensure shunting and train preparations standards are maintained. Co-ordinate internal yard movements. Liaise with OCC to coordinate train arrival and departures. 5.6 SAR PIC The SAR PIC is responsible for: The safe movement of trains Confirming that all routes, switches and derailers are secured for the movement Reports any vehicle or loco defects to the Yard Foreman Movement of vehicles/locomotives to and from the LMS/WMS as required by the Yard Foreman 5.7 Locomotive Shop Supervisor The Locomotive Shop Supervisor is responsible for the safe operation of all activities within the Locomotive Maintenance Shop. This includes welfare of staff and their awareness, and compliance, to the LWA. 5.8 Wagon Shop Supervisor The Wagon Shop Supervisor is responsible for the safe operation of all activities within the Wagon Maintenance Shop. This includes welfare of staff and their awareness, and compliance, to the LWA. 5.9 Track Maintenance Building Supervisor The Track Maintenance Facility Supervisor is responsible for the safe operation of all activities within the Track Maintenance Facility. This includes welfare of staff and their awareness, and compliance, to the LWA. Document No.: Rev. No.: [I] Internal Effective Date: SAR-005-100-3-003 02 28 March 2022 Department: Operations Management Function: Freight Business Unit Document Title: Local Working Arrangements: Al Nairyah Depot PART A – SITE SAFETY AND LAYOUT 6 Location 6. 1 Nariyah Yard Location Nairiyah Yard is situated East of Nairiyah, South of Highway 85 Lattitude 27.412927 Lontitude 48.607878 Using Satelite Navigation (Google Maps) for guidance to the location use code CJ75+44 Nairyah Acess into the Freight Yard in via a security gate manned by security guards situated to the east of the yard. Once within the yard follow the (1 KM) long approach road which will take you towards the LMS WMS track Maintenance and Operations buildings. Safety NOTE if following directions below. BE AWARE OF RAIL CROSSINGS SITUATED AT VARIOUS LOCATIONS THROUGHOUT THE YARD. PROCEED WITH CAUTION, BE PREPARED TO STOP PRIOR TO THE RAIL CROSSINGS AND DO NOT STOP YOUR VEHICLE ON ANY OF THE RAIL CROSSINGS 6.2 Directions to the Operations Building From the initial approach road (once through the security gate), take the first turning right (there is a large hatched area as you enter this road). Follow this road and at the first junction on this road, proceed ahead (looking left and right with caution), go straight across the rail crossing and onto the road immediately in front of you. This road will immediately take you to the right and in a westerly direction. Follow this road, the GFT and YT lines along with RAT1 are situated to the right of this road, the STT lines are situated to the left. Continue on this road and go over another rail crossing (rails situated within the tarmac) until you see the operations building to the left and the fuel shed facility to the right. There are car parking areas on the left situated to both the east and west side of this operations buidling. 6.3 Directions to the LMS and WMS buildings From the initial approach road (once through the security gate), take the first right turning (there is a large hatched area as you enter this road). Follow this road and at the first junction on this road, proceed ahead (with caution), straight across the rail crossing and onto the road immediately in front of you. This road will immediately take you to the right and in a westerly direction. Follow this road and take the first left for the WMS (Wagon Maintenance Shop) or second left for the LMS (Locomotive maintenance Shop) 6.4 Site Access Nairyah depot comprises a range of maintenance, administration and accommodation buildings. The principal buildings are: Fuelling Point Loco Maintenance Shop Wheel Lathe Shop Warehouse Document No.: Rev. No.: [I] Internal Effective Date: SAR-005-100-3-003 02 28 March 2022 Department: Operations Management Function: Freight Business Unit Document Title: Local Working Arrangements: Al Nairyah Depot Wagon Maintenance Shop On-Track Machine Building Paint Shop 6.5 SITE MAPS a) Buildings A buildings location map above. b) Track Layout a layout can be briefly found below with switch numbers. Document No.: Rev. No.: [I] Internal Effective Date: SAR-005-100-3-003 02 28 March 2022 SAR-005-100-3-003 Document No.: Document Title: Local Working Arrangements: Al Nairyah Depot Function: Freight Business Unit Nariyah Yard - NorthEnd (not to scale) TI( 627.532 T 627.739 TK 629.409 TK 629.661 TK 629,961 TK 630.006 TK 630.832 - 1. ·. - r 1-----. ------- :.- ·-··-··-··-··-··-"- 5P11 : : 16P70 Z 2 , : !6PO,. 16f11 : , : 16m I One 1>303 \ / 1 P1 loP/4: TK 627 627 02 Rev. No.: - RATl Ola> 16P19 :..,_,, J.liPijj.. - , , _,,._,, - ,, - , , - , ,,_,, - RAT2 -RAT3 - Other RoBd Acee : Zone1 DO [Qu] FuelTanks m 1□□ 1 lJnknow Department: Operations Management I FuelPoint I Operatl'cns Contrc I Room IllControl Room I LocomotiveMaintenance Shop Loc.omotllveWa h Facllllty I Wareho se Zone 4 28 March 2022 Effective Date: I WheelShop I Warernouse.Zone 6 ::! TSMG !rn Accommodation I Wa1on Wash Wagon Maintenarnce Facility Shop Pairnt Shop 161)111 ,{t......... eU,, l Kbarooah@sar ,rom.a t::i:I [I] Internal Version 1-01/11/2018 I iwn Zone7 · "iiiiiiiiittiiiiiiiiiiaiiiiiiiiiia - aiiiiao111111iiiiiiiiiiall-ll-tt-ff... tt-!tl- - - -ro"'- - j Page 1 of 2 [I] Internal eU,, l t::i:I.{t......... Department: Operations Management Function: Freight Business Unit Document Title: Local Working Arrangements: Al Nairyah Depot TK 634.170 Page 2 of 2 Version1-01/11/}.(118 Nariyah Yard - South End (not to scale) I '161'11!i TK 633.667 TK 632.460 [I] Internal TK 631.660 Document No.: Rev. No.: Effective Date: SAR-005-100-3-003 02 28 March 2022 Department: Operations Management Function: Freight Business Unit Document Title: Local Working Arrangements: Al Nairyah Depot 6.6 General site requirements - SAR policies Whether visitors, contractors or SAR employees, everyone working within Nairyah Depot are required to be familiar with and adhere to the following SAR policies. These policies will be available for contractor/visitor inductions and all SAR staff should ensure they are familiar with the policies, if there is any doubt you are to contact your line manager for advice a) Drugs And Alcohol Policy b) Smoking Policy c) Mobile Electronic Device Policy d) Road Vehicle Driving Policy e) Code of Business Conduct 6.7 Use of Company Vehicles within Nairyah Depot Only company vehicles are to be used for business purposes within Nairyah depot. To use a company vehicle within the depot you MUST hold the relevant valid driving licence obtain a “Driving Authorization” permit specific to the vehicle you are required to drive. You are not authorized to drive any company vehicles without a valid Driving Authorization form, which can be acquired from the support services office. APPENDIX H 7 SAFETY 7.1 Adverse Weather Reporting The OCC are to be informed immediately if operations are stopped or commenced due to adverse weather conditions. OCC will be advised that operations have been ceased by the SAR PIC. The SAR PIC will advise the OCC when conditions are suitable for operations to re-commence. 7.2 Fire Fire extinguishers, fire alarms and Fire Notice Cards are available and are clearly marked in all buildings. All visitors will receive a briefing on location of Fire Assembly Points when they receive their briefing of emergency actions Only use fire-fighting equipment if you are trained and competent. 7.3 Accident/Incident Management All staff are to report any accident/incident and near misses to the Yard Supervisor/Shop Foreman (nominated deputy), together with the OCC as soon as it is safe to do so. 7.3.1 Procedure The SAR accident and incident investigation procedure is provided for in SAR-012-100-4-016 Document No.: Rev. No.: [I] Internal Effective Date: SAR-005-100-3-003 02 28 March 2022 Department: Operations Management Function: Freight Business Unit Document Title: Local Working Arrangements: Al Nairyah Depot 8 Communications 8.1 Language requirements All safety critical communication within SAR is to be spoken and written in English using the phonetic alphabet when spelling difficult words. 8.2 Radio usage GSM-R radios are the primary means of communication for all shunting activities within Nairyah 8.3 Mobile phones Mobile phones are not permitted within Nairyah when carrying out safety critical work. When carrying out such work all mobile phones must be left in the Yard Facility Building. The PIC is permitted a mobile phone, but must ensure he is in a position of safety when making or receiving calls. 8.4 Language protocol You must make sure you properly understand the meaning of all messages whether they are communicated by telephone, radio or face-to-face. If you do not understand you must ask the other person to explain more clearly. Details of all communication requirements are contained within your SAR Rule Book SAR-006-300-2-020 Document No.: Rev. No.: [I] Internal Effective Date: SAR-005-100-3-003 02 28 March 2022 Department: Operations Management Function: Freight Business Unit Document Title: Local Working Arrangements: Al Nairyah Depot PART B – Site Specific Details and requirements 9 Additional PPE requirements for Nairyah 9.1 PPE for Nairyah shunting staff and drivers All SAR operation staff are required to have the following PPE: Safety Boots High Visibility clothing or vest Snake Gators Clear and dark glasses (for day/night use) Safety Gloves Only use PPE supplied by SAR. Ensure you are familiar with the correct use of the PPE supplied. Report any defective of missing PPE Immediately in order for replacements to be obtained. You are required to look after your PPE and store it in a secure place when not in use. In the interest of personal hygiene, avoid sharing your PPE with another person. Document No.: Rev. No.: [I] Internal Effective Date: SAR-005-100-3-003 02 28 March 2022 Department: Operations Management Function: Freight Business Unit Document Title: Local Working Arrangements: Al Nairyah Depot 10 Site Hazards There are a significant number of hazards on site which will be briefed on the safety induction/safety briefing. A non-exhaustive list of site hazards includes: un-gated crossings, ground-level manhole covers, moving trains, road vehicles and close proximity to running railway lines. All visitors will be briefed on site hazards during their site safety induction or their location specific safety induction. 10.1 Control of Level Crossings Level crossing are numerous and located all around the Nairyah Yard complex. These crossing are open crossings with signage alerting road vehicles of the crossing approaching. All users of road vehicles are to remain vigilant when approaching a crossing The shunting staff will ensure the crossing is safe to proceed over by blocking the crossing with a road vehicle. Alighting from the road vehicle, then prevent any vehicles passing over the crossing whilst the train is making the movement. The train driver will not pass the crossing until assurance is guaranteed from the shunter that the crossing is safe to proceed over with the train. 10.2 Crossing Over Wagons by LMS staff in order to gain access/egress the Fuel Shed At times when trains are occupying tracks through the fuel shed on either YT2,YT3,YT4, and/or RAT1 these can block pedestrian access/egress for LMS staff required to walk to/from various areas of the fuel shed. When this occurs, the following process must be followed to avoid a train being moved whilst LMS staff are crossing over the wagon in either direction. LMS staff in the first instance MUST contact the Yard Foreman and ask if the wagons to be crossed are going to move. Once the yard foreman confirms that the wagons will be remaining stationary, the LMS staff can proceed to cross immediately following this confirmation. If a period of more than 10 minutes elapses between the request being made and the crossing taking place then a new request to cross must be made by the LMS staff to the Yard Foreman. This rule applies when crossing in both directions IE from Fuel Shed to Road Side and/or from Road Side to Fuel Shed. A request to cross from Fuel Shed to Road Side must be made by the LMS member of staff to the Yard Foreman by using a mobile phone. Mobile phones should not be used in the proximity of any fueling equipment. Document No.: Rev. No.: [I] Internal Effective Date: SAR-005-100-3-003 02 28 March 2022 Department: Operations Management Function: Freight Business Unit Document Title: Local Working Arrangements: Al Nairyah Depot 11 Train arrival and departure 11.1 TRAIN ARRIVALS NORTHBOUND: Prior to a train being provided a Movement Authority to enter Nairyah Yard from the direction of Jubail Junction the Train Controller will confirm with the Nairyah Yard PIC (or nominated deputy) that the train has permission to enter the yard. The Train Controller will confirm with the Nairyah Yard PIC (or nominated deputy) the forecast arrival time of the train. Once permission has been granted for the train to enter Nairyah Yard, the Train Controller will set the route, using the route setting functionality on the HIS as far as D1003 colour light signal which will provide a movement authority to the driver. The route setting functionality will not be used beyond D1003 signal. The Nairyah Yard PIC (or nominated deputy) will ensure the route is set correctly for the train to move on to the relevant reception road, YT1, YT2, YT3, YT4 or RR. The Nairyah Yard PIC (or nominated deputy) will confirm the route is set and secured for the train arrival. Control for Zone 3 will then be handed back to the OCC. Once the route is correctly set the Train Controller will authorise the Driver to pass D1003 signal and traverse onto the reception road. The driver will then cancel the ERTMS for the train and proceed as instructed. 11.2 TRAIN ARRIVALS SOUTHBOUND: Prior to a train being provided a Movement Authority to enter Nairyah Yard from the direction of AZ1 the Train Controller will confirm with the Nairyah Yard PIC (or nominated deputy) that the train has permission to enter the yard. The Train Controller will confirm with the Nairyah Yard PIC (or nominated deputy) the forecast arrival time of the train. Once permission has been granted for the train to enter Nairyah Yard, the Train Controller will set the route, using the route setting functionality on the HIS as far as U903 colour light signal which will provide a movement authority to the driver. The route setting functionality will not be used beyond U903 signal. The Nairyah Yard PIC (or nominated deputy) will ensure that the relevant track through the fuel shed is clear and the route is set correctly for the train to move on to the relevant reception road, YT1, YT2, YT3, YT4 or RR. The Nairyah PIC will advise staff working within the Fuel Shed as well as any Facilities and/or Track Maintenance staff in the vicinity of the movement about to take place. The Nairyah Yard PIC (or nominated deputy) will confirm the route is set and secured for the train arrival and confirm which track has been set & secured. Control for Zone 1 will then be handed back to the OCC. Once the route is correctly set the Train Controller will authorize the Driver to pass U903 signal and traverse onto the relevant reception road. The driver will then cancel the ERTMS for the train and proceed as instructed. Document No.: Rev. No.: [I] Internal Effective Date: SAR-005-100-3-003 02 28 March 2022 Department: Operations Management Function: Freight Business Unit Document Title: Local Working Arrangements: Al Nairyah Depot 11.3 TRAIN DEPARTURES NORTHBOUND: Prior to a train departing from YT1, YT2, YT3, YT4 or RR the Nairyah Yard PIC (or nominated deputy) will contact the Train Controller and advise him that the train is ready to depart. The Train Controller will check there are no conflicting movements approaching, entering or passing Nairyah Yard, preventing the train from departing. The Nairyah PIC will ensure that the relevant lane through the fuel shed is clear and that staff working within the fuel shed as well as any facilities and/or track maintenance staff in the vicinity are advised of the movement about to take place. The Nairyah Yard PIC (or nominated deputy) will advise the Train Controller which signal the train is departing from. The Nairyah Yard PIC (or nominated deputy) will confirm the route is set correctly for the train to approach the departure signal. Atr this stage the Control for the zone will be handed over to OCC. When it is confirmed by the Nariyah PIC that the route is set correctly OCC will authorise the Driver to approach the departure signal. Upon arrival at the departure signal the Driver will contact the Train Controller, reporting his arrival and that he is ready to depart Nairyah. The train will be set up for departure in Level ETCS level zero and will transition after passing either D303 or D505 colour light signals. The Train Controller will set the route, using the route setting functionality on the HIS from the departure signal (D303 or D505) to BED Marker Board. 11.4 TRAIN DEPARTURES SOUTHBOUND: Prior to a train departing from YT1 or YT3 the Nairyah Yard PIC (or nominated deputy) will contact the Train Controller and advise him that the train is ready to depart. The Train Controller will check there are no conflicting movements approaching, entering or passing Nairyah Yard, preventing the train from departing. The Nairyah Yard PIC (or nominated deputy) will advise the Train Controller which signal the train is departing either U603 or U607 colour light signal. The Nairyah Yard PIC (or nominated deputy) will advise any facilities or track maintenance staff working in the vicinity of the movements about to take place and confirm to OCC that the route is set correctly for the train to approach the departure signal. When it is confirmed by the Nariyah PIC that the route is set correctly the Control for Zone 2 and 3 will then be handed over to the OCC Upon arrival at the departure signal the Driver will contact the Train Controller, reporting his arrival and that he is ready to depart Nairyah. The train will be set up for departure in Level ETCS level zero and will transition after passing either U603 or U607 signals. The Train Controller will set the route, using the route setting functionality on the HIS from the departure signals (U603 or U607) to BEU Marker Board. Document No.: Rev. No.: [I] Internal Effective Date: SAR-005-100-3-003 02 28 March 2022 Department: Operations Management Function: Freight Business Unit Document Title: Local Working Arrangements: Al Nairyah Depot 12 Operational activity of the site 12.1 Speeds The below are the maximum rail speeds within Nairyah Yard and associated locations, the SAR PIC will confirm the safe speed for the movement through a Job Brief. Maximum Terminal Speeds (Subject to any lower emergency or temporary speed restriction) Activity Speed Plain line in forward direction 30 km/h Through any switch in a forward direction 20 km/h Forward but adjacent to buildings or facilities 10 km/h Propelling 10 km/h Moving vehicles in the WMS 5 km/h Moving locomotives in LMS 5 km/h Proceeding through the Fuel Point 5 km/h Proceeding over a Level Crossing 5kph Document No.: Rev. No.: [I] Internal Effective Date: SAR-005-100-3-003 02 28 March 2022 Department: Operations Management Function: Freight Business Unit Document Title: Local Working Arrangements: Al Nairyah Depot 12.2 Nairyah Depot Train Input Form The Nairyah Depot Train Input form must be completed for every train that enters/departs Nairyah Yard (APPENDIX A). This document is completed by the Yard Foreman and is to be retained on file for a period of one year. The Nairyah Yard Inspection and Shunting Certificate will include a pre-departure check or train examination upon entry to Nairyah. The pre-departure check is the last check of the train before it goes onto the network. It is vitally important that a thorough check is completed. When conducting a departure roll-by inspection you are to ensure you: Stand in a position of safety Conduct the check with 2 x persons (1 each side of the train) Avoid Distractions and remain focused on the moving train and its condition Be prepared to STOP the movement immediately should any problem with the train be identified The Requirements of the Pre Departure and Roll-By examination are contained within the Nariyah yard Inbound Inspection & Handover form (Appendix G) 12.3 Required train documentation Trains leaving Nairyah Yard are required to have the following documentation. It is the responsibility of the train driver and train pilot to ensure the documents are on the lead loco of the train. The Train Pilot is responsible for checking the contents of the document pack and equipment bag to ensure that all the required equipment is present. The documents and equipment bag (including its contents) must be signed for by the driver/pilot and copies of this signed document must be retained at Nairiyah. The contents of the equipment bag must contain 2 x fully functional GSMR radios with chargers, Heat Gun. The same bag will be required for DG however 2 x H2S monitors will be added. Examples of the required train documentation can be found in the Appendices of this document: Certificate of Closure (Dangerous Goods trains only) – Appendix B White Copy of the Transportation Invoice and the Yellow copy of the Dangerous Goods Transportation Invoice (if applicable) – Appendix C Dangerous Goods Handover Form – Appendix D Loco Fitness for Service and Handover Checklist, 1 for each Loco in the train consist. (Appendix J). These must be handed to the Loco driver and retained on the lead locomotive. Document No.: Rev. No.: [I] Internal Effective Date: SAR-005-100-3-003 02 28 March 2022 Department: Operations Management Function: Freight Business Unit Document Title: Local Working Arrangements: Al Nairyah Depot 12.4 Shunting of Trains 12.4.1 General Shunting Duties The SAR PIC (or nominated deputy) is responsible for all movements within Nairyah Depot. Prior to any rail movement within Nairyah the SAR PIC (or nominated deputy), is to formulate a plan for the movement. A Job Brief will be conveyed to all staff involved with the proposed movement. Before the movement commences, a clear understanding must be reached between all parties involved with the proposed rail movement. Everyone involved must be fully conversant with the requirements of the movement prior to the movement starting. Should circumstances change and the plan for the rail movement requires amendment, provided it is safe to do so, the movement must cease immediately. A revised plan must be formulated, and the amended Job Brief conveyed to all parties involved with the movement. The SAR PIC is to follow the Job Brief and also ensure that there are no personnel working (or other movements taking place) on adjacent roads. Any personnel in the vicinity are to be advised that a shunt movement is taking place they are then to move to a position of safety and remain there until the SAR PIC informs them that it is clear and safe to return to their work. The locomotive horn is to be sounded prior to starting a shunt movement in any direction. The sounding of the horn is to be of a duration, volume, intensity and repetition appropriate to the circumstances and appropriate to the distance over which it is to be heard. 12.4.2 Job Brief The contents of the shunting plan will formulate the job brief, the minimal (and non-exhaustive) list of requirements for the Job Brief will be as follows: Who is controlling the movement and the means of communication What is the requirements of the proposed shunting movement The tracks, the rail movement will be using for the movement. Any personnel who are working where the movement will take place have been moved to a position of safety. Vehicles involved with the proposed shunting movement, where they will be collected and where they will be left Confirm there are no vehicles left “foul” on any tracks which are involved with the movement. There will be no vehicles left “foul” of other lines after the movement. Document No.: Rev. No.: [I] Internal Effective Date: SAR-005-100-3-003 02 28 March 2022 Department: Operations Management Function: Freight Business Unit Document Title: Local Working Arrangements: Al Nairyah Depot 12.5 Operation of LFOP & Zone Control Nairyah Yard is situated between signals D603 or D607 from the north and D303 Stop Board or D505 Stop Board from the south. Nariyah Yard is separated into 9 Operational Zones, which are indicated on the map below. The OCC control Zones 1 & 3 at all times with the remainder of the zones under the control of the SAR operational staff, please see Nairyah Yard map at the start of this document. The protecting turnouts for Nairyah Yard are 16P06 and for south departure/arrival, the switch will be set away from the mainline The protecting turnouts for Nairyah Yard are 16P05 and for north departure/arrival, the switch will be set away from the mainline All switches within Nairyah are set away from any buildings and to avoid any crossings. OCC will take control of zone 1 2 or 3 during departures or arrivals of trains to/from the yard. Control is handed back to the SAR PIC once arrival or departures of each train has been completed. In order to operate an LFOP, the SAR PIC (or nominated deputy) must request control of the respective Zone (1 or 3) from the OCC. All other Zones remain under the control of the shunting teams within Nairyah although the OCC can resume control should they wish to do so. Prior to operating any LFOP the SAR PIC (or nominated deputy) MUST ensure the clamps of the relevant switch are removed and that all staff are clear of the switch. Prior to authorizing any movement over the switch:, o The operator of the switch must ensure the lights for the relevant switch have stopped flashing and are steady o Once the integrity of the switch is confirmed a clamp is required to be fitted to the switch which will prevent any subsequent movement of the switch whilst the movement is traversing the switch o The operator of the LFOP must ensure that there are no train movements being conducted when the switch is being operated o It must be ensured that all locomotives are clear of axle counters (minimum of 10 meters away from the switch) when the switch is being operated The SAR PIC (or nominated deputy) will then authorize the movement over the switch. The driver will repeat the instruction back prior to making the movement Should the intended function of the LFOP or switch not take place due to a fault, the movement MUST NOT START. Any fault that occurs (IE lights going out/loss of detection) to the LFOP during any part of the movement, then the movement MUST STOP IMMEDIATELY and the fault reported via the Yard Foreman to OCC 12.6 Shunting Movements All communication between the OCC and the SAR PIC (or nominated deputy) must be clearly understood and repeated back. A Job Brief must be carried out prior to the shunting activity taking place. A clear understanding must be reached between all parties prior to any movement taking place. The route MUST be set and confirmed for any movement within Nairyah Yard. The SAR PIC (or nominated deputy) must ensure that all switches are set correctly (and clamped) before any movement over them. The Driver/Pilot is to Document No.: Rev. No.: [I] Internal Effective Date: SAR-005-100-3-003 02 28 March 2022 Department: Operations Management Function: Freight Business Unit Document Title: Local Working Arrangements: Al Nairyah Depot monitor every switch the locomotive traverses, should any switch be set against the movement, the Driver/Pilot is to stop the movement and inform the SAR PIC (or nominated deputy) immediately. The movement must be controlled by the SAR PIC (or nominated deputy) who will be in a position of safety and in advance of any propelling movement. The SAR PIC will monitor the speed of the train and advise the driver accordingly. Prior to attaching to any vehicle a shunting movement must stop 5 metres before coupling up to any locomotive or vehicle. Whilst the movement is taking place, the shunter or PIC will count down the distance to stationary vehicles to the driver. Be aware of any possible limited clearances whether real or perceived STOP AND CHECK, always ensure you keep a good lookout at all times. All Stop Boards at Nairyah are required to have authority of the SAR PIC in order to pass any Stop Board. Staff are not to assume that there is permission to pass any Stop Board in Nairyah unless confirmation has been provided by the SAR PIC. “Stop Boards” or “Not to be Moved Boards” applied as depot protection by RSM or Track Maintenance staff MUST BE observed. They are NOT to be removed. Only the staff that applied the Stop Board or Not to be Moved boards are authorized to remove these protection devices. 12.7 Stabling Vehicles Handbrakes All vehicles stabled in Nairyah, without a locomotive attached (with the exception of trains being shunted and assembled for departure) are required to have the handbrakes applied As a minimum requirement, handbrakes are to be applied as follows: 3 handbrakes for 1-30 Vehicles, 10% for 31 and over. 12.8 DEPOT PROTECTION Should the RSM wagon maintenance, or locomotive maintenance staff, be require to examine a train for routine examination in an operational siding or attend a locomotive in the Fuel Shed the following must be adopted: The Wagon Maintenance Team Leader (WMTL) will advise the SAR PIC of the requirement for the train inspection. The WMTL will include in the advice tracks upon which the Wagon Maintenance Team will be working, duration of the expected work activity, how many people will be working and any other relevant detail The SAR PIC will place Stop Boards at either end of the train, providing 50 meters distance between the train and the Stop Board. Upon completion of the work the WMTL will advise the SAR PIC that all work has been completed. The SAR PIC will remove the Stop Boards placed on the relevant track Document No.: Rev. No.: [I] Internal Effective Date: SAR-005-100-3-003 02 28 March 2022 Department: Operations Management Function: Freight Business Unit Document Title: Local Working Arrangements: Al Nairyah Depot 13 Train Processing Nairyah Depot 1. Train Arrives on either of the YT Lines or RAT 1 (as per the pre-arranged plan between OCC, Yard Foreman and Shunt Team Leader) 2. Once the Train has been brought to a complete stop, berthed and secured, the Main Line Driver and Pilot will disembark the lead loco and will be collected by the LV driver. 3. Lead locos are then detached by the shunters and placed into Fuel Shed for Inspection unless otherwise directed by LMS. Yard Foreman will advise LMS (via e-mail) once Locos are placed at the designated area 4. Wagons are set up for inspection by the Yard Loco driver by either using the inbound DP Loco or GPL Loco to supply Air and Train Line power to the wagons. 5. Once set-up for inspection, WMS will be advised by the Yard foreman (via e-mail) that the wagons are ready for inspection. 6. WMS Team will install the relevant depot protection (as per section 12.8) and will inspect all wagons in the train consist. 7. When the wagon inspection is near completion, the WMS team will request to the Yard Foreman (via e-mail or phone call) to remove Train Line Power in order for the WMS inspection team to carry out a continuity/resistance check to the wagons power cables and connections. 8. Once the train inspection is completed, the WMS team will apply the relevant color cards to the wagons required to be removed (see APPENDIX E). Prior to the WMS team leaving the wagon inspection location they will remove the depot protection. WMS will then inform the Yard Foreman that inspection is completed and then advise of the wagons that need to be removed on the wagon cut out form that will be handed over by the WMS team leader. 9. The Yard Foreman will allocate a shunt team who will shunt the train in accordance with section 12.4 of this LWA. The shunt team will remove the wagons detailed on the wagon cut out form and collect replacement wagons from either the STT lines or direct from the WMS lines and add them to the train in order to form the train with the booked number of wagons. 10. The Yard Foreman will advise WMS (via e-mail) of the good order wagons added to the train and the position of the good order wagons in the consist by completing a Wagon Cut-In form (See APPENDIX K). 11. At a convenient time the removed wagons will be taken to an area of the yard as indicated by the WMS team. This is detailed on the wagon cut-out form. 12. During the shunting process (9), once the train is 2.5 x hours from completion, the Yard Foreman will call OCC to arrange for the train crew who will be required to depart the train from Nairyah Depot once the train is ready. 13. LMS will advise the Yard Foreman (via e-mail) of the Fleet Number of each locomotive assigned to the departing service. When applicable the position of where the locomotives should be situated on the train will be advised by LMS. 14. Once the wagons have been shunted (wagons cut out and replacement wagons attached), the required number of locos as advised by the Yard Foreman will be collected by the Yard Loco Driver from either the LMS area or the Fuel Shed and then attached to the train in the required formation. 15. Once Locomotives are attached, the train will be set-up by the Yard Loco Driver. 16. A Pre-departure check (PDX) will be completed on the train by the yard shunt team and the form contained within Appendix G will be completed. Document No.: Rev. No.: [I] Internal Effective Date: SAR-005-100-3-003 02 28 March 2022 Department: Operations Management Function: Freight Business Unit Document Title: Local Working Arrangements: Al Nairyah Depot 17. Once the Pre departure check will be completed and the train is free of all defects, the departure route can be set by the Yard Shunters and the train can be handed over to OCC by the Yard Foreman or Shunt Team Leader 18. Once the Loco Driver and Pilot arrive, they will be handed the relevant train paperwork and DG equipment (if required) by the Yard Foreman and they will then be taken by the LV Driver to board the lead loco. 19. A minimum of four shunters (two each side of the train) will place themselves in a position of safety in readiness to conduct a Pre Departure Roll-By examination. Ground staff will set-up the GSMR radios and test to ensure there is a good radio communication link with the driver/pilot at this stage. 20. Train will depart the depot whilst receiving a roll-by examination. The train can be stopped on departure at any time if any defects are identified on the train as it is departing. 13.1 Instruction to be followed when processing a by-pass / underframe inspection train in Nariyah The handling of by-pass trains that need to call into Nariyah will result in different departments interacting with each other which will require a greater coordination and control of multiple activities. By-pass trains may call into the yard from the north or south, depending on the situation. These generally call in as some attention is required to either Wagons and/or Locomotives. Locomotives may also be fueled when by- pass trains call into Nariyah for attention. A process for coordinating Locomotives requiring attention on a by-pass train is essential as locos will be fueled, whilst technicians attend any fault or inspection required and the train may need to be moved (more than once) to accommodate any inspection or attention the DP locomotives may require. There is a handover process in place which serves to coordinate these processes and ensures trains are only moved once the processes have been completed. The attached handover form is to be used to control the activities when dealing with these trains and the procedure in place is as follows:- 1. The Yard foreman will complete section 1 at the top of the “Locomotive Underframe Inspection Fitness for Service Handover” checklist. 2. The Yard foreman will hand this over to the LMS technician and loco fueling attendant. 3. Both the locomotive fueling attendant and LMS technician will apply the required protection – “Not to be moved” boards and “Stop Boards” then carry out the tasks required. 4. Once the technician and fueling attendant have completed the required tasks, they will complete section 2 of the form, remove the protection and hand this form to the Yard Foreman. 5. If the train requires to be moved in order to place the DP locomotives over the pit within the fuel shed, then the yard Foreman will retain this form and instruct the shunters to move the train. 6. Once the DP locomotives are placed within the fuel shed, the form will be handed back to the technician and fueling attendant (as applicable) by the Yard foreman. 7. The locomotive technician and fuel attendant will again apply protection as above with a “not to be moved board” and “Stop Boards” then carry out the required tasks. 8. Once all of the tasks are completed and the train has been made ready to depart, the technician and fueling attendant will remove the protection and complete section 3 of the form and return the form to the Yard Foreman. 9. The yard foreman will complete section 4 of the form to detail the instructions issued to the shunter for the shunter to depart the train. 10. Once the process has been completed and the train departs Nariyah, the form is to be retained within the train pack as a record. Document No.: Rev. No.: [I] Internal Effective Date: SAR-005-100-3-003 02 28 March 2022 Department: Operations Management Function: Freight Business Unit Document Title: Local Working Arrangements: Al Nairyah Depot PART C – Locomotive and Wagon Maintenance 14 Wagon Maintenance Shop 14.1 Person in Charge The Wagon Maintenance Shop (WMS) Foreman is to control local movements to/from the WMS including all internal movements within the WMS area. The WMS Foreman needs to communicate the nature of the moves about to take place to the Yard Shunt Team if the Yard Shunt team are expected in the area. The WMS Foreman may appoint a nominated deputy to assume the referenced duties 14.2 Movements in or out of the WMS area Note: In or around the WMS is defined as any activity in Zone 6 or Zone 7 of Nairyah Should a shunt be required which will arrive onto the tracks outside the WMS or depart from tracks outside the WMS the following must be carried out. A shunt request will be communicated to the Yard Foreman (via e-mail). The shunt request will contain details of movements to/from the WMS lines to/from any of the wagon storage areas within Nairiyah. A clear understanding must be reached between the SAR PIC and the Wagon Maintenance Foreman (or nominated deputy) There must be no other shunting movements being conducted in the area. All details of the proposed shunting movement must be discussed, the below is a non-exhaustive list: o The start time and duration of the intended movement o The route to be taken and the ultimate destination of the movement o Any vehicles planned to be left outside of the Stop Board A confirmation of a clear understanding must be ensured prior to the SAR PIC granting permission The SAR PIC will confirm with the Wagon Maintenance Foreman (or nominated deputy) when all movements are complete 14.3 Movements by WMS Should the WMS require to move vehicles and there is an operations shunt team working in the area, in proximity of Zone 6 or Zone 7 the WMS Foreman must first advise the Nairiyah PIC of the movement taking place to avoid any conflicting moves. 14.3.1 Vehicles which are required for maintenance or repair Vehicles for maintenance/repair at the WMS will be advised by the WMS Foreman (or nominated deputy), the advice will include the location where the vehicle is to be positioned for the WMS, the vehicle numbers, carded status of the vehicle. Document No.: Rev. No.: [I] Internal Effective Date: SAR-005-100-3-003 02 28 March 2022 Department: Operations Management Function: Freight Business Unit Document Title: Local Working Arrangements: Al Nairyah Depot 14.3.2 Vehicles which are required collection from maintenance or repair All vehicles required for collection from the WMS will be advised by the WMS Foreman (or nominated deputy), the advice will include the location where the vehicles are on WMS, specific number of vehicles including vehicle numbers. 14.3.3 Vehicle in section prior to moving following collection from WMS Whenever a vehicle is be collected or moved to WMS: Wagon Cards, handbrakes, continuity of the brake pipe, scotches, Not to be Moved Boards are not applied to any vehicle, all ICC cables will be checked by the groundstaff. For the purposes of advice to train crew APPENDIX E provides advice of Defect Cards which may be applied. Train crew are not to remove any defect cards. Prior to moving an vehicle a complete check of all vehicles must be made by the SAR PIC, the check will include scotches, Not to be Moved Boards, should any defect cards found WMS Foreman is to be advised and the defect card will be removed by WMS Foreman (or nominated deputy). Roll by when collecting vehicles to ensure wheels are rotating and there are no unidentified defects. 15 Locomotive Maintenance Shed (LMS) 15.1 Person in Charge The Locomotive Shop Foreman is responsible for the local control locomotive movement into and out of the LMS together with the safety of all staff in the LMS. The Locomotive Shop Foreman may appoint a nominated deputy to assume the referenced duties. Movement of locomotives may only be undertaken by members of staff who are trained and assessed as competent to drive locomotives to the relevant SAR standards. 15.2 Locomotive Movement Request 15.2.1 Locomotive delivery to the LMS The LMS Foreman (or nominated deputy) will provide the SAR PIC a request for a locomotive to be delivered to the LMS. The SAR PIC will advise the LMS Foreman (or nominated deputy) of the anticipated time for the locomotive to be delivered to the LMS. An email between SAR PIC and LMS Foreman will confirm the details. For the purposes of these Arrangements the LMS is defined as the Locomotive Maintenance Shed, or those tracks listed as LMS 2 – 10 north & south of the locomotive shed The SAR PIC and the LMS Foreman (or nominated deputy) will carry out a Job Brief to ensure there is a clear understanding of the movement to be made Document No.: Rev. No.: [I] Internal Effective Date: SAR-005-100-3-003 02 28 March 2022 Department: Operations Management Function: Freight Business Unit Document Title: Local Working Arrangements: Al Nairyah Depot The SAR PIC will set the switches for the movement and ensure all switches are clamped and secured. The SAR PIC will advise the LMS Foreman (or nominated deputy) of the movement and the locomotive will be delivered to the agreed location. Should the locomotive be delivered inside the Maintenance Shed the LMS Foreman will ensure that all staff are in a position of safety and there is no equipment left foul of the movement Once the movement has ceased the locomotive must be secured using the handbrake if operational, other vehicles if the handbrake is defective 15.2.2 Locomotive collection/change of track from LMS The LMS Foreman (or nominated deputy) will provide the SAR PIC a request for a locomotive to be collected from the LMS. The SAR PIC will advise the LMS Foreman (or nominated deputy) of the anticipated time for the locomotive to be collected from the LMS. An email between SAR PIC and LMS Foreman will confirm the details. The SAR PIC and the LMS Supervisor/ Foreman (or nominated deputy) will carry out a Job Brief to ensure there is a clear understanding of the movement to be made. Any defects on the locomotive which will be moved must be advised to the SAR PIC. The SAR PIC will advise the driver/pilot of any defects advised by the LMS Supervisor/ Foreman with the locomotive. The SAR driver will fully prepare the locomotive for service, paying particular attention to any defects identified The LMS Foreman (or nominated deputy) will ensure that all staff are in a position of safety & there is no equipment foul of the movement. The SAR PIC will advise the LMS Foreman (or nominated deputy) of the movement and will receive permission to operate within the CTP for the LMS The SAR PIC will set the switches for the movement and ensure all switches are clamped and secured The SAR Driver will prepare the locomotive for service ensuring all brakes are fully operational. Should any defects with the braking capability be identified an additional vehicle may be used to provide braking (or operational) ability to be driven safely 16 Track Maintenance Building Arrival or departure of trains to the Maintenance Track Building are required to access or egress the Track Maintenance lines. 16.1 Track or S&T work The Track Access and Maintenance Advice Handover form (APPENDIX F) must be completed by the relevant PIC & Yard Supervisor (or nominated deputy) whereby both parties agree the track which will be worked up together Document No.: Rev. No.: [I] Internal Effective Date: SAR-005-100-3-003 02 28 March 2022 Department: Operations Management Function: Freight Business Unit Document Title: Local Working Arrangements: Al Nairyah Depot with the timescales for the work to take place. If a blockage of the line is required, the form in this appendix should be used. The minimum distance for placing Stop Boards will be 50 meters either side of the work being carried out. If a turnout will be within the 50 meters of the work location Stop Boards will be placed at the turnout to prevent access to the work location. All turnouts must be set and clamped away from the work location to protect the work location from train access. 16.2 Machine arrival Machines arriving at Nairyah will arrive in the following manner: The OCC will advise the SAR PIC of the anticipated arrival of the On Track Machine Provided it is safe to do so, the SAR PIC will confirm acceptance of the On Track Machine to the OCC and set the required route for the arrival The SAR PIC will then release the relevant zone control to the OCC for the arrival of the On Track Machine Upon arrival at D1003 (from Jubail Jcn) or U903 (from AZ1) signal the On Track Machine Operator will contact the SAR PIC and confirm the route is set The SAR PIC will grant permission to enter Nairyah provided, it is safe to do so, and there are no conflicting movements The On Track Machine operator will confirm to the SAR PIC when the On Track Machine is clear of the relevant zone through which they entered Nairyah The SAR PIC will authorize the On Track Machine operator to proceed to the required destination as agreed with the SAR PIC. The SAR PIC may authorize other shunting within Nairyah provided it is safe to do so The On Track Machine operator will set the required route through Nairyah by the use of LFOPs CHECK The On Track Machine operator will confirm with the SAR PIC that the machine is at the agreed destination and all other yard activities can be carried out. Unless confirmed between the SAR PIC and the On Track Machine Operator there will be no movements made other than to the agreed destination of the On Track Machine 16.3 Machine departure On-Track Machines wishing to depart Nairyah will depart in the following manner: The On-Track Machine Operator will request approval from the SAR PIC to depart at the relevant end of Nairyah. Should the On-Track Machine be unable to depart as requested an alternative means of departure will be considered by the SAR PIC. The SAR PIC will confirm the departure of the On Track Machine with the OCC The SAR PIC will give authority for the On Track Machine to make a movement towards the agreed location All shunting activity will cease if there is any possibility of a conflicting movement with the yard The On-Track Machine will depart along the route as agreed with the SAR PIC and the On Track Machine will set the relevant turnouts for the agreed route Upon arrival at signal U603/U607 (towards Jubail Jcn) or D303 or D505 (towards AZ1) the On Track Machine operator will advise the SAR PIC of the arrival at the relevant signal The SAR PIC will give the relevant zone control to the OCC for machine departure The On-Track Machine will depart Nairyah after the signal displays a proceed aspect Document No.: Rev. No.: [I] Internal Effective Date: SAR-005-100-3-003 02 28 March 2022 Department: Operations Management Function: Freight Business Unit Document Title: Local Working Arrangements: Al Nairyah Depot 16.4 Internal On-Track Machine movements All On Track Machine operations within Nairyah must be coordinated with the Yard Supervisor (or nominated deputy). The On Track Machine operator will operate the turnouts along the route as agreed between the SAR PIC and On Track Machine Operator. A record of the agreed movement will be completed into the Track Access and Maintenance Advice Handover Form (APPENDIX F). 17 Records: In accordance with the responsibilities set out in this document, the Regional Manager is to ensure that the Local Working Arrangements are kept up to date and reflect current procedures and policies within the depot. In accordance with the responsibilities set out in this document, the department supervisors are to maintain a file containing: a) A copy of the most recent version of these Local Working Arrangements (LWA) b) A copy of all previous versions for reference. c) A record sheet to be signed by each member of staff certifying that they have received a personal copy of the latest version of the LWA.SR. No. Document No. Title 01 SAR-012-100-4-018 SAR Accident, Assault Form 01 SAR-012-100-4-020 Fire, Environment or Crime Reporting Form 01 SAR-005-100-3-060 Certificate of Closure 01 SAR-005-100-3-097 Operations Instruction Phosphate Wagon 01 SAR-005-100-3-098 Vehicle Inspection Sheet 01 SAR-005-100-3-099 Loading/Unloading Advice 01 SAR-005-100-3-004 Local Field Operations Panel Advice 18 REFERENCES: Document Reference Document Name SAR-006-300-2-020 SAR Operational Rule Book SAR-005-100-3-004 Terminal Operators’ Handbook SAR-005-100-3-002 Driver Operations Handbook SAR-012-100-4-017 A1 General Event and Near Miss Form SAR-012-100-4-018 Accident/Assault Form External Document Safe Shunting Brief 19 DOCUMENT HISTORY: Rev. No. Date Comments 00 8-Nov-18 First issue 01 1-Aug-20 Second issue - updated 02 28-Sep-20 Third issue - updated Document No.: Rev. No.: [I] Internal Effective Date: SAR-005-100-3-003 02 28 March 2022 Department: Operations Management Function: Freight Business Unit Document Title: Local Working Arrangements: Al Nairyah Depot 19. APPENDIX A: Nairyah Depot Train Input Form Nairyah Depot Train Input Form Nairyah Depot - Train Input Form Date Bypass Day Empty Train Headcode Comments Set# EOT TILT Arrival consist Locomotives Numbers(in) Locomtives Fuel(in) Total Number of commodity Wagons(in) Please write all times in this format : MM/DD/YY hh:mm Time RAK's team Inform RAK's Person Advised the NAR Yard about the Train Departure Time Departure NAR-Yard's Person Got Departure Time from RAK Informed about the Departure Time Time RSM Got Informed of RSM's Person Got Informed the Departure Time of Depart Time Please write all times in this format : MM/DD/YY hh: