Harvesting and Threshing Terminology PDF
Document Details
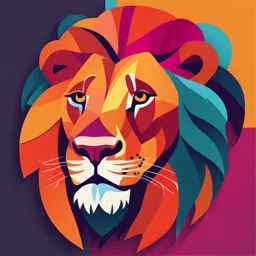
Uploaded by SolidKineticArt
Tags
Summary
This document provides a glossary of terms and an overview of harvesting and threshing techniques, and examines the types of equipment used. Information on how to determine various dimensions and measurements for harvesting and threshing machinery is also included.
Full Transcript
LESSON 1.HARVESTING AND THRESHING TERMINOLOGY Harvesting and threshing is an important operation in the farming. This can be done either manually or with the help of power operated machinery. Harvesting of field crops continues to be one of the most labour intensive operations in agricultural produ...
LESSON 1.HARVESTING AND THRESHING TERMINOLOGY Harvesting and threshing is an important operation in the farming. This can be done either manually or with the help of power operated machinery. Harvesting of field crops continues to be one of the most labour intensive operations in agricultural production system. Manual harvesting with different hand tools continues to be dominant, which takes 170-200 man-hours to harvest one hectare of paddy crop. Due to high labour demand at the time of harvesting, the operation continues for weeks together, resulting in over drying of crops in the field causes grain losses to the extent of 5 to 15 percent and even results in loss of crop due to untimely rain during harvesting. Higher shattering losses occur while harvesting crops like wheat, barley and gram in over dried conditions. Harvesting of crops like maize, sorghum and arhar is done at relatively low moisture content. The crop stacks are thick and woody and the hand sickle is adequate tool used for harvesting. For other conditions, a hand chopper is sometimes also employed. Now mechanized harvesting devices such as reapers, combine harvesters etc. are being used for harvesting these crops. Harvesting and threshing terminology 1. Combine: a machine designed for harvesting, threshing, separating, cleaning and collecting grain while moving through the standing crop. Bagging arrangement may be provided with a pick-up attachment. It may be used for handling crop that has been swathed. It may be self- propelled type or tractor operated type. 2. Self-propelled combine: a combine on which an engine of suitable power rating is mounted to serve as source of power, this may be wheeled type or track-laying type. 3. Wheeled Combine: A combine in which the pneumatic wheels are used. 4. Track-laying combine: A combine fitted with full or half tracks instead of pneumatic wheels. 5. Tractor operated combine: A combine which requires a tractor of suitable power rating to serve as a source of power for its working. It may be trailed type or side mounted type. 6. Header: The portion of the combine comprising the mechanisms for gathering the crop. 7. Gathering width: The distance between the centerlines of the outermost divider points expressed in millimeters. Where adjustable dividers are used the maximum and minimum dimensions shall be stated. 8. Grain header width: The distance between the side sheets of the header measured immediately above the forward tips of the sickle sections. Width shall be expressed in millimeters. 9. Corn Header width: The average distance between the centre lines of adjacent picking units multiplied by the number of units. Where the header width is adjustable, maximum and minimum di8mensions shall be stated. Width shall be stated in millimeters and the number of picking units shall be stated. 10. Knife or Sickle: The reciprocating component of the header fpr cutting the crop. 11. Knife or Sickle Frequency: The number of cycles which the sickle makes in a given period of time. One cycle is the full movement of the sickle in one direction and its return to the starting point. Frequency shall be expressed in whole cycles/minute. 12. Sickle Stroke: The distance that a point on the sickle travels with respect to the centre line of a guard n one half cycles. Stroke shall be expressed in millimeters. 13. Knife Registration: The alignment of centre line of knife section with the centre line of guard. 14. Pick up: A device for gathering a crop from a window. 15. Peg Drum: A cylinder having rows of spikes or pegs. 16. Rasp Drum: A cylinder having bar with serrations. 17. Cylinder Diameter: The diameter of the circle generated by the outermost point of the cylinder threshing elements, expressed in millimeters. 18. Cylinder Width: The length of the cylinder bar measured parallel to the cylinder axis, expressed in millimeters. 19. Concave Arc: A means of defining the width of a concave in degrees. This shall be measured from the front to the first bar to the rear of the last bar and in relation to the centre of the cylinder 20. Cylinder and Concave Clearance: The gap between the tip of the cylinder to the inner surface of the concave expressed in millimeters. The minimum and maximum clearance in a particular setting and adjustment range for both the front and the rear side of the concave shall be stated. 21. Concave Width: The minimum distance between the two panels of the combine in which the concave is mounted, expressed in millimeters. 22. Concave Length: The distance from the front of the first bar to rear of the last bar, measured around the contour formed by the inner surfaces of the concave bars, expressed in millimeters. 23. Concave Area: The product of the concave width and concave length expressed in square millimeters. 24. Concave grate area: That portion of the concave area which is permeable for separation. The area shall be calculated using the outside dimensions of the permeable surface and be expressed in square millimeter. 25. Concave grate extension: A permeable element approximately concentric with the cylinder and generally forming an extension of the concave contour. 26. Concave grate extension area: The product of concave ratio extension length and concave width expressed in square millimeters. 27. Transition grate: A permeable element to provide transition from the concave or concave grate extension to the straw walkers or rack. 28. Transition grate length: The contour length of the upper surface of the transition grate, ex[pressed in millimeters. 29. Transition grate area: The product of the transition grate length and the concave width, expressed in square millimeters. 30. Straw walker or straw rack area: The product of thee straight length and the inside width of the separator side structure immediately adjacent to the straw walkers or rack, expressed in square millimeters. Where walker extensions are used in the standard specifications of the machine. 31. Straw raddle area: The product of the raddle length and the exposed width of the raddle, expressed in square millimeters. 32. Shoe: The oscillating structure which supports the cleaning sieve of sieves and which may also support the chaffer sieve and chaffer sieve extension. 33. Sieve cleaning areas of the shoe: The chaffer sieve, intermediate sieve, cleaning sieve and extensions to them. The area of each shall be calculated using the outside dimensions of the permeable surface, and shall be expressed in square millimeters. 34. Pneumatic cleaning areas: Where chaff is removed by aerodynamic means alone. These areas shall be calculated as the product of the width and depth of the air stream at the point of contact of the air with the crop material. The depth shall be measured perpendicular to the direction of the air flow. The area shall be expressed in square millimeters. 35. Other cleaning areas: Dirt screens, re-cleaners and other auxiliary cleaning devices. These areas shall be specified. 36. Cleaning area total: The sum of the area of each chaffer, chaffer extension, cleaning sieve (s) and sieve extension (s), if any, obtained by using the outside dimensions of the sievable surface expressed in square millimeters. 37. Component areas: For purposes of combine specification, the areas defined in 28, 29, 31, 34, 35, 36, 38, 39, and 40 shall be listed individually and should not be used singly or in combination as a measure of machine performance or capacity. 38. Header loss: The loss of grains and ear heads being shed and left over on the ground as a result of operation of cutter bar and header unit. 39. Non-collectable loss: The loss of grains and ear heads being shed and left over on the ground as a result of operation of cutter bar and header unit. 40. Pre-harvest loss: The loss of grain or ear heads from the standing crop prior to the operation of harvesting machine in the field. 41. Cylinder loss: The loss of unthreshed heads and damaged grains passing out of threshing cylinder. 42. Rack loss: The threshed grains passing out in the straw. 43. Shoe loss: The threshed grains blown or carried out with the chaff. 44. Engine displacement: Engine displacement shall be expressed in cubic centimeters to the nearest whole number. 45. Turning radius: The distance from the turning center to the center of tire contact of the wheel describing the largest circle while the vehicle is executing its shortest turn without turning brakes in operation. The wheel base and guide wheel tread width shall be stated. Turning radius shall be expressed in whole centimeters. 46. Clearance radius: The distance from the turning centre to the outermost point of the combine executing its shortest turn without brakes in operation. If equipment options on attachment affect this dimension, such equipment shall be specified. The wheel base and guide wheel tread width shall be same as in turning radius. Clearance radius shall be expressed in whole centimeters. 47. Combine weight: The weight of the complete machine equipped for field operation. The weight shall be determined under the conditions specified in cutter bar height no. 16 and the fuel tanks shall be full. If other equipment options or attachments affect the weight, such equipped shall be specified. Combine weight shall be expressed in quintals. 48. Combine length: The overall dimension from the foremost point to rear-most point of the combine equipped for field operation measured parallel to the longitudinal centre line of a combine. The header installed shall be stated, and if other equipment options or attachments affect the length, such equipment shall be specified. Combine length shall be expressed in whole centimeters. 49. Combine height: The vertical distance from plane on which the combine is standing to the highest point on the combine. The height shall be measured under the conditions expressed in cutter bar height no. 16. The height with all components in position for field operation shall be specified. Combine height shall be expressed in whole centimeters. 50. Combine width: The overall width measured horizontally covering outer extremities of combine expressed in millimeters. 51. Ground clearance: The height of the lowest point of the combine from a level supporting surface when the combine is fitted with all its usual accessories, fuel, radiator, hydraulic, lubrication and grain tank full and tyres inflated to recommended pressure for field work. 52. Ground contact area (Track): Product of track chain length and width on ground multiplied by two, expressed in square millimeters. 53. Length of track-chain on ground: Length at base of track shoes disregarding the grouser, as measured between first and last track roller centers, on from front idler wheels centre line if they are so designed as to hold the track chain level with the track rollers expressed in millimeters. 54. Medium plain of wheels or tracks: It is equidistant from the two planes containing the periphery of the rim or tracks at their outer edges. 55. Specific ground pressure: The quotient of front axle mass and ground contact area, giving a rating comparable to tyre pressure in case of wheeled combine. 56. Wheel base: The horizontal distance between front and rear wheels on a wheeled combine measured at the centre of ground contact. 57. Wheel-base: The horizontal distance between front and rear wheels on a wheeled combine measured at the centre of ground contact. 58. Wheel track: The distance between the median planes of wheels or tracks on the same axle measured at the point of ground contact. 59. Width of track-chain on ground: Width of track shoes including rounded ends if any expressed in millimeters. 60. Discharge height of unloader: The vertical distance from the plane on which the combine is standing to the lowest point of the discharge opening with the unloader in operating position. The height shall be measured under conditions specified in cutter bar height 16; discharge height shall be expressed in whole centimeters. 61. Clearance height of unloader: The vertical distance from the plane on which the combine is standing to a point on the underside of the unloader located at a horizontal of 914 mm from the lowest point of the discharge opening. 62. Reach of unloader: The horizontal distance measured perpendicular to the longitudinal centre line of the combine from the lowest point of the unloader discharge opening to the outermost point of the header on the unloader side. The reach shall be measured under conditions specified in discharge height of unloader and expressed in whole centimeters. 63. Grain tank capacity: The number of the volumetric units of wheat that are unloaded by its own unloading system expressed in cubic meters. 64. Grain tank unloading time: It is the minimum time in seconds required to unload the grain tank capacity. 65. Reaper: A machine to cut grain crops. 66. Side delivery reaper: A machine which harvests crops and delivers them on the side having the space for the next run clear. 67. Windrower: A machine to cut crops and deliver them in a uniform manner in a row. 68. Binder: A machine for cutting standing crops and tying them into neat and uniform sheaves. 69. Cutter loader: A machine to cut crops and to deliver them to vehicle. 70. Ejection: Throwing of the tied bundles over the conveyor of a reaper binder. 71. Knotting: The operation of automatic tying of bundles in a reaper binder. LESSON 2. PRINCIPALS AND TYPE OF CUTTING MECHANISM The operation of cutting plant is carried out by four different actions: Slicing action with a sharp smooth edge. Tearing action with a rough serrated edge. High velocities single element impact with a sharp or dull edge. A two-element scissors type action or shearing type cutting. Generally manual harvesting involves slicing and tearing actions those results in plant structure failure due to compression, tension or shear. The serrated sickle combines a slicing and sawing action. It does not require repeated sharpening as in the case of smooth edge sickle. A single element impact cutting may be either moving or stationary type. An impact cutter has a single high speed cutting element and cuts mainly due to inertia. This cutting method is an economical method widely used in rotary lawn mowers, forage choppers and in some tractor mounted cutter bar. Usually a single element, sharp edged blade requires a velocity of about 10 m/s for impact cutting. A dull edged single element blade requires a velocity of about 45 m/s. In the rotary cutter the knives rotate in a horizontal plane as in the rotary mowers, whereas, in flail shredder the knives rotate in a vertical plane parallel to the direction of travel. In shearing type cutting, cutting takes place due to shear. A system of forces acts upon the material in such a manner as to cause it to fail in shear. Shear failure is invariably accompanied by some deformation in bending and compression, which increases the energy required for cutting. A common way of applying the cutting force is by means of two opposite shearing elements, which meet and pass each other with little or no clearance between them. Both or one of the elements may be moving with a linear uniform, reciprocating or rotary motion. This type of cutting mechanism is most widely used for harvesting agricultural crops. The reciprocating cutter bars that are commonly used for harvesting wheat or paddy crops use this principle. The inclined angle between the cutting edge is about 30 degrees. The serrated blades cannot easily slip between the two cutting edges. Reciprocating cutter bars do an excellent job of harvesting but are characterized by high-energy losses, short dynamic imbalance and limited operating speeds. Balancing of Reciprocating Masses The cutter bar of a reaper is one such component and is major cause for vibrations of the reaper and a limiting factor for the speed of reaper. Mostly slider crank mechanism is employed for converting rotary motion in translating motion. Such components are seldom balanced in the farm machinery and are one of the major factors in the frequent breakdown of such machinery. The inertial force ‘F’ transmitted to the frame and the rotating un-balanced mass ‘mrot’ are the main causes of vibrations. The periodic vertical reactions Fg may cause early fatigue failure of the knife back if the knife guides are loose. The rotary unbalanced mass can be balanced by providing a counter balancing mass on the flywheel but in opposite direction of crank pin so that Rb x mb = R x mrot Where, mb = the counter balancing mass The full dynamic balancing of reciprocating parts can be obtained by the addition of a second driven reciprocating mass that moves in direct opposition to first mass (cutter bar) and is as closely in line with it as feasible. So the balancing mass induces equal inertial forces but in the opposite direction that of the cutter bar. If the reciprocating counter weight is offset from the line of motion of the knife it will induce a cyclic couple. The rotating counter weight commonly provided on the flywheel on a pitman type drive does not give complete balancing because its centrifugal force is constant where as the inertia force of the reciprocating parts is a function of the crank angle q. The usual practice is to provide sufficient mass opposite the crank pin to counter balance mb and half of the reciprocating unbalanced mass mrot. The vertical vibration component introduced by the counter-weight is then equal to the reduced maximum horizontal component. Full dynamic balancing minimizes vibration at a given crank speed. It also permits the use of higher crank speeds and, hence, greater forward speeds. Counter balancing is not imperative if the weight of the machine or component supporting the cutter bar is large in comparison with the reciprocating force, as on a self-propelled windrower or combine. But counter balancing is needed much on a field mower because its frame is relatively light. Balancing Machine Elements with Rotary & Translatory Motion The balancing of members that do not move with plane rotation is much more difficult. A typical four-bar mechanism is the most common of all mechanisms (representing rocking mechanism or mechanism for transferring rotary motion to oscillating motion, oscillating sieves or oscillating blade). Crank 2 rotates with a constant angular velocity, rocker 4 oscillates, and coupler 3 moves with a combination of rotation and translation. The system can be balanced by introducing mechanisms that produce the opposite effects. A mechanism that is the mirror image of the original but moves in the opposite sense can be introduced to balance the vertical shaking forces and moments due to angular accelerations of links 3 and 4. The motion of the combination of linkages would give unbalanced horizontal shaking forces, which can be balanced by a mechanism that is a mirror image of this combination but moves in the opposite sense. This method of balancing is usually impractical. Partial balance of the four-bar mechanism can easily be obtained. First, it is necessary to consider equivalent links. Two members are dynamically equivalent if they have the same total weight, the same center of gravity, and the same moment of inertia. The equivalent coupler replaces the original coupler. Link 2 and weight W1 can be balanced by W3 to bring the centre of gravity to centre of rotation. Similarly, link 4 and W2 can be balanced by W4. This will eliminate all vertical and horizontal shaking forces, but there will remain the unbalanced and variable torque on the frame owing to the angular acceleration of links 2.3 and 4. The sieves of thresher sieve rocking mechanism and oscillating blades of oscillating implements can be partially balanced by this technique. Shearing - type cutting mechanism The cutting mechanism depending entirely on shearing utilizes the principle of scissor action which causes cutting by bringing two edges to bear on one plane across the material to be cut. As such there is negligible bending or crushing and only resistance to be overcome is the shearing strength of the material. The well-known mechanism in this category is the pitman and reciprocating knife-bar type mechanism. The invention of this mechanism can truly be regarded as a "mechanical break- through" for harvesting. The cutter bar has triangular knife sections riveted to a bar which reciprocates in slots of the stationary guards to cut the crop against the ledger plates of the guards. This type of cutting mechanism is used in the mowers, reapers, binders, forage harvesters and combines. The greatest efficiency in this mechanism is affected when there is minimum of crushing and bending of the material and when there is no bunching of material at the rear of the knife sections. Generally, a 3" (75 mm) stroke is used. However, double knife bars with 6" (150 mm) stroke with opposite motions are also used now. The reciprocating motion is imparted with the help of a crank wheel and a pitman. Cutting Speeds required for reapers: The speed requirement of the reciprocating knife-bar at peak cutting velocity seldom exceeds 100 m/min for the reapers, binders and combines. But when such a mechanism is used in a grass mower/forage harvester, the speed ranges from 120 to 170 m/min. The speed of the knives is essentially dictated by the "feed rate" of the material to be cut and its shearing resistance. The shearing resistance of the grain crop depends upon the moisture content of the stalks. As such the stage of maturity at the time of harvesting is an important parameter in determining the power requirements for cutting. For the grasses and fodder crops, the feed rate is usually higher than the grain crops. As such the shearing resistance is also considerably higher, depending upon the succulence and fiber-content of the stems and leaves. The reciprocating speed of the knife bar should be 20 to 25 higher than the forward speed of travel for efficient shearing of grain crops but about 40 to 45 higher than the forward speed for grass mowers to overcome the problem of bunching and over-feeding. In the reapers, binders and combines, it is not essential to use knife-clips to minimize clearance at shear and ensure maximum bearing of the shearing edges. In fact, in many grain harvesting machines now a days, there are not separate ledger plates, instead the case-hardened guard edges only serve as stationary shear plates. Even in such machines, the impact has little to do with cutting, since the cutter bar speed is too low. It is unwise to attempt to gain affect of impact-shear in cutter bar-type mechanism because 800 to 1600 strokes per minute with a back and forth stroke of 75 mm is far too short of the 4000 strokes which is the minimum requirement to effect the shear by impact alone. It is not possible to use higher speeds in the pitman and reciprocating cutter-bar type mechanisms since it is difficult to balance the unbalanced forces. A part of the unbalance is caused by uneven load and a part is the function of the constantly changing crank angle. If higher cutting bar speeds are to be used in reapers, binders and combines, it would lead to rapid wear and even mechanical failure of components. LESSON 3. SHEAR TYPE CUTTING MECHANISMS, ADJUSTMENTS, REGISTRATION AND ALIGNMENT It has knife that moves against stationary fingers. Horizontal reciprocating type mower has knifes that rotate at high speed in horizontal plane (Fig. 1). Due to reciprocating action of knife, grasses are cut uniformly. The mower/reaper consists of following parts: Cutter Bar: Cutter bar is designed to cut 25-50 mm above the ground level up to 100 mm or more. It must be able to cut a wide variety of crop materials from grasses to tough stocks without clogging. A number of attempts have been made to replace the reciprocating knife with continuous moving cutting units such as chain or band knives in helical roller cutters but none have performed so well that commercially feasible. It is steel flat made with high-grade steel. All other sub component included in the cutting mechanism is connected directly or indirectly to it. Cutter Bar Assembly: It is heart of the mower. The knife is metal bar on which blades are mounted that are triangular shaped sections. The cutting edges of these sections are mostly smooth edges. The knife sections move back and forth and cut plants in both directions. The section of the knife should always stop at the center of the guard on each stroke. The length of the stroke is 7.5 cm. Guards are provided with ledger plates on which the knife sections move. Knife clips hold the sections down against ledger plates but allow it to move freely. Knife clips are placed together with the wearing plates to absorb the rearward thrust of the crop to the knife. A badly worn wearing plate or a loose knife clip may allow the knife to bend. This is a common cause of the knife head, breaking at the point where it is attached to the bar. There is a grass board on the outer end of the mower, which causes the cut plants to fall towards the cut material. The angle of the board can be changed for different crops. A shoe on each end of the cutter bar is always provided to regulate the height of the cut above the ground. The inner shoe has a larger area of contact with the ground than the outer one. This results in smooth and easy sliding of the cutter bar on the ground. Guards: These are provided to hold the forage while it is being cut. These also serve to secure the cutting units and provide a place for the ledger plates. The guards are made with malleable casting or pressed steel, pointed at one end for parting and guiding the grass to the knife sections. Ledger Plate: The ledger plates are fixed over to the guards. They form one half of the cutting unit, the knife section acts as the other half. The edges of ledger plates are serrated to prevent stems of grass from slipping off the points of the shears. Knife Section: Triangular shaped knife sections are fixed over to the cutter bar. The rear part of knife section is kept square shaped for its easy fixing. These are perfectly smooth and work well in most of the grass and legume crops. Some sections are top serrated which work well in dry grass or straw. Wearing Plates: Wearing plates supports the knife from rear side. They provide vertical support to the rear of the knife sections and also absorb the forward thrust of the knife. Knife-clips: These are provided to hold the knife section down close against the holder plates. They are made of malleable iron or steel. Knife clips are generally spaced three or four guards apart. Inside Shoe: The inner end of the cutter bar during the operation is supported with a shoe like runner. A replaceable sole is placed underneath the shoe, which is adjustable to regulate the height of cut. Outside Shoe: The outside shoe supports the outer end of cutter bar. It also has an adjustable sole to regulate the height of cut. The pointed front part of the other shoe acts as a divider. It separates the cut grass from standing uncut grass. Power Transmission Unit: The knife of cutter bar is powered through a long pitman attached to the knife head. The power transmission consists of main axle, gears, crankshaft, crank wheel and pitman. The main axle receives power from one of the transport wheels. A spur gear mounted on the main axle drives the spur pinion on one end of the counter shaft in the gearbox. The bevel gear, which is provided to the other end of the counter shaft, engages with the bevel pinion on the crankshaft. The crank wheel and pitman are fixed on the outer end of crankshaft and the reciprocating motion is transmitted to the pitman, which in turn operates the knife in the cutter bar. The knife is connected to the pitman with a ball and socket joint. Crank speeds on most of the mowers are 850-1000 rpm for conventional pitman drives and 1000-1200 rpm for dynamically balanced systems. The knife makes about 1600 cutting strokes per minute. The tractor-drawn mowers are operated by PTO shaft. Most tractor-drawn mowers have a V-belt in the drive which provides overload protection and check high frequency peak torque and shock loads, sometimes dog clutch or a slip clutch is provided. Wheels: A pair of wheel made of cast iron with sufficient widths and number of lugs to develop better traction are provided in the mowers. Now, pneumatic wheels are also in use. The transport wheels transmit power to the knife. It is so arranged that when the wheel move forward the ratchet and pawl mechanism comes into play to drive the main axle. When the wheel is turned backward the pawl slips giving a clicking noise. Frame: The main frame of the mower is made with heavy casting that supports other parts and provides openings for main axle, counter shaft and crank shaft. It provides space for gearbox, clutch and bearing. A triangular shaped welded frame is common in semi-mounted mowers over which power transmission unit is installed. Pitman: The pitman is the connecting rod between the crank wheel and the knife. Pitman may be made of well-seasoned wood or of steel which supports weight and absorbs vibrations. Grass Board and Stick: The grass board is provided to clear the cut material from narrow strip next to the standing crop and hence provide a place for the inner shoe for operation on the next turn. A stick is also provided to keep the forage falling correctly. It can be set high for tall grass and low for short material. The grass board is spring loaded and free to move to some extent when it meets an obstruction. Adjustments: A system of force acts upon the material to cut it in such a manner as to cause it to fail in shear. A common way to apply the cutting force is by means of two opposed shearing elements, one or both may be moving. The motion may be linear with uniform velocity, reciprocating or rotary. Impact cutting principle is applied in rotary cutters and flail shredders. A continuous reciprocating knife type of cutter bar is commonly used to cut a wide variety of crop materials. Cutting in this case utilizes both impact and shear. There are two adjustments, which are very important for proper functioning of a mower. They are registration and alignment. Registration: A knife is in proper registration when midpoint of the knife section stops in the center of guard on each stroke (Fig. 2). It is very essential for an even job of cutting and unclogging of the cutter bar. If it is not properly registered then it can be adjusted by moving the entire cutter bar in or out with respect to the pitman crankshaft. The results of failing to register are an uneven cutting and an uneven loading of the entire mower. It also results in more draft and clogging of knife. There is provision to change the pitman length, which is provided in some of the mowers. Fig. 2: Adjustment in the cutter bar unit. Alignment: The outer end of the cutter bar is fitted a little ahead of the inner end so that the outer end may align with the inner end, when the mower is pulled through crops. This is called lead and gives better cutting when the cutter bar is properly aligned i.e. the knife and the pitman run in a straight line. To allow for rear word deflection of the outer end of cutter bar during operation, it is customary to adjust the mower so that when not in operation, the outer end of cutter bar has a lead of about 2-cm per meter of cutter bar. To measure the lead of a mower, stretch a stirring parallel to the vertical plane of the pitman and determine the difference in the horizontal fore-and-aft distances from the string to the knife back at the inner and outer ends. Adjustment, if needed be done by rotating an eccentric bushing on one of the hinged pins. Fig. 3 shows a typical arrangement of a pitman drive and inertia-force relations for the reciprocating knife, pitman and crankpin. Pitman mass is assumed to be divided into two components, W1 being subjected to rotary motion and W2 having reciprocating motion. If Ws is the mass of knife and Wc is the mass of crankpin, uniform angular velocity of the crank can be assumed if R/(L2 - S2)1/2 is less than 0.25. The inertia force of the reciprocating parts can be represented by the equation Fig. 3: Forces due to inertia of reciprocating parts in a mower pitman drive. early fatigue of knife back. Cutting energy and power requirements of a 2.13 m tractor-mounted mower is given in Table 1. Height of cut of crop can be adjusted by varying the adjustable shoes at the inner and outer ends of the cutter bar. Table 1: Cutting energy and power requirements of a 2.13-m tractor-mounted mower. Average Average Average Peak Equivalent Knife PTO Power PTO Power Load (kN) (kW) (kW) Inertia & friction load 1.82 1.27 4.61 (no cutting) Mowing at 7.9 2.54 1.90 5.22 km/h Increase due to 0.72 0.63 0.61 cutting Source: K LESSON 4. IMPACT TYPE CUTTING MECHANISMS The impact/ cutting mechanisms are of a rather recent development. They depend upon the effective shear of the material to be cut by a sharp impact of blade(s) travelling at 1300 to 2700 m/min. The more rigid the stalks and therefore resistant to bending, the more easily they gives way through shear failure/ under impact. The impact cutting mechanisms are being used in the rotary mowers (also called flail type) and forge harvesters with great advantage. Greatest efficiency is derived from the use of sharp edged, long rotating blades to have higher peripheral speed and higher inertial momentum of the heavy blades to sustain their speed when cutting dense-growth. To utilize the impact-shear principle effectively, it is essential to employ a mechanical prime mower. The manually-carried Japanese power reaper with a circular blade employs the impact cutting principle. The advantages of impact-cutting mechanism are the minimum initial cost, simplicity of repair and maintenance as well as high efficiency. The impact-type mechanisms are particularly well-suited to rough land and rough pasture. The impact- type cutting mechanisms are, however, not suited to harvesting grain crops due to higher shattering of the grain as well as the spreading of the stalks upon being cut. The flail type forage harvesting is simple in design and construction. It can be used for cutting any type of forage crops and grasses including lodged crops. Overload encountered by the machine during operation is absorbed by freely hanging flails and thus machine components are protected from field damage. This makes it a unique machine to be used in stony, stumpy and uneven land. Forage crops cut by flail mower do not require any additional chopping by chaff cutter. This is done in the process of harvesting in the field itself by repeated beating action of the flails on the plants. Tractor rear mounted hydraulically controlled PTO operated flail type forage harvesting machine is versatile for numerous field operations such as fodder maize cutting, grass topping and mowing, green manure topping, cutting shrubs on river banks and drainage channels etc. A flail-type mower comprises of a horizontal rotor with two blades each of about 60 cm. The blade rotates at peripheral speeds of 2000-3000 rpm (Fig. 1). These mowers are extremely sturdy and as such can work under varying field conditions. When used for grasses, it causes excessive field loss as short pieces are hardly recovered in raking or during picking from the windrows. Losses can be reduced using lower peripheral speeds. A flail mower has a full width adjustable gauge roller located behind the rotor to provide accurate control of cutting height and prevent scalping of high spots. Cutting widths are usually 1.8 to 3.0 meters. Pull type flail mowers are generally attached at the back of tractor and kept offset so that the tractor wheel runs on the cut hay rather than on the standing crop. Some of these units are provided with augurs to convey the cut material into trailers. It uses free-swinging chains and knives to sever the plants by beating or cutting action (Fig. 2). The flails or knives travel in the same direction the machine moves. It does not have chopping knives on the blower fan to chop the material into desired length for silage. The beating by flails more or less conditions the hay. Fig. 1: Flail action during work. Fig. 2: Details of free swing chains. Problem 1: Determine horizontal inertia force at each end of stroke and magnitude and direction of vertical reaction at each end of stroke for reciprocating cutter bar knife in a mower. Given: Crank speed = 1000 rpm; pitman length = 1.06 m; crank pin radius = 38 mm; mass of knife = 4.4 kg; mass of pitman = 3.5 kg; mass of crank pin = 0.35 kg; centre of gravity of pitman = 0.48 m from knife end and height of crank shaft centre line above pivot connection between knife and pitman = 240 mm. Solution: Refer to Fig. 3 and equation 1 in lesion 3 Weight of pitman (W1 + W2) = 3.5 kg Since centre of gravity of pitman is 0.48 m from knife end, LESSON 5. MOWERS AND WINDROWERS Forage harvesting is more complex as compared to grain crops. Forage crop is of great bulk and mass, containing 70-80% water when first harvested. For storage it must be dried, either naturally or artificially, to a safe moisture content of about 20 to 25%. Due to low product value it limits the economic feasibility of mechanization of harvesting operation of forage crops. The mowers are used to cut the crop and windrow in the field, which is manually collected for further chopping. The forage harvester consists of a combination of plant-cutting unit and a chopping unit and is called field forage harvester. The field forage harvester performs the functions of both row binder and silage cutter, as it severs the standing stalks from the ground and chops them into silage in one continuous operation in the field. It can be grouped into two according to the mechanism used to cut the crop viz. field choppers and flail harvesters. Mower The mower is a machine mainly used for harvesting grasses and forage crops. It cuts the stems of standing vegetation to make hay out of them. The mower cutter bar is capable of cutting the stems at 3- 10 cm above the ground. There are different types of mowers used for cutting grass and forage crop such as cylinder, reciprocating, horizontal rotary and flail type mowers. According to the source of power, mowers can be classified as manually operated, animal-drawn, tractor-drawn and self-propelled. According to the mode of hitching, mowers can be classified as trailed type, semi-mounted and integral mounted type. Semi-mounted and integral-mounted mowers can be further classified as rear, mid and front-mounted. According to drive used, mowers can be classified as ground-driven, engine-driven and PTO driven. The conventional animal-drawn mower has the following main parts: A cutter bar to cut the crop and separate it from uncut portion. Power transmission unit to receive and transmit motion force. Frame to support moving parts. Wheels to transport and for operating the cutting mechanism, and Auxiliary parts to lift and drop the cutter bar. Classification of Mowers The mowers on the basis of their cutting mechanism are classified as: a) Finger-type cutter bar mower Here the plant is pressed by the active knife against the fixed ledger-plate of the finger guard and sheared. b) Under-knife mower Double knife cutter bar with one knife fixed falls under this category. With this system one knife acts as ledger plate of the guard and the other performs the function of a normal reciprocating knife. These mowers are simple in construction and minimize the chances of blockage by dense crop and by small soil obstructions. However they are not suitable in stony fields. c) Double cutter-bar mower It is provided with two cutter-bars which operate in opposite directions. The plants are sheared by the two active blades instead against the ledger plate of guard. Such mowers have advantages of minimum power requirement clean cut, higher speed of operation, cutting close to the ground etc. The cutter- bar mowers are further classified on the basis of their finger spacing. (i) Normal cutter-bar: In these mowers the spacing of guard fingers and knife sections is kept equal to 76.2 mm. These mowers are most suitable for thick stemmed crops like jowar, maize, bajra etc. (ii) Medium fine cutter-bar: In this type of cutter-bar the finger spacing is reduced from 76.2 mm to 50.00 mm and the knife spacing is kept constant to 76.2 mm. This mechanism helps better cutting in dense crops. (iii) Fine cutter-bar: Here the finger spicing are kept 38.1 mm and the knife spacing remains 76.2 mm. This mechanism is especially suitable for the grasslands to harvest fine stemmed plants on broken terrain. (d) Mower-cum-crusher To perform cutting and condition operation the reciprocating mower is provided with a conditioning attachment. Such mowers are called mower-cum-crushers. (e) Disc mowers In these machines the plants are cut by the revolving blade in horizontal plane fitted on round discs. On the basis of their construction these mowers are further classified as: (i) Drum Disc Mower: These mowers are provided with drum type discs, i.e. a drum is fitted over the disc to enable the cut material to push back to place it in the swath. (ii) Rafter-disc Mower: These mowers are similar to the drum disc mowers except that (a) the power to the disc is transmitted through the system located below the disc and (b) the cut material is pushed back by the revolving discs and not by the drums as in the previous case. The discs are provided with throw- away pieces which help pushing back the cut material. Rotary Mower It consists of a single high speed cutting element in horizontal plane (60-70 m/s) and relies primarily upon the inertia of the material being cut to furnish the opposing force required for shear. The ground also acts as one of the shearing elements. It works on the principle of free-cutting. When a revolving blade hits, the plant, it is sheared and carried with the blade. The normal component of the force cuts the stalk and the tangential component helps imparting kinetic energy to the plant so as to carry it along with the blade up-to certain distance. The forward velocity component also helps adding to the magnitude of both the four components. The rotary mowers are also of two types: (i) Disc-type mower and (ii) The Rotary stalk-cutter and shredder. The disc type mower has 2-3 swinging blades of approximately 75 mm x 40 mm x 3 mm size fitted to the disc. The diameter of the disc and number of the discs depends upon the swath width. Owing to the rotary speed of the disc and forward speed of the tractor, the blade travels in a cycloid- path. The tangential component of the force is much higher in magnitude than the radial component; as such the material is cut but not carried away from the cut area. The throw-away pieces are provided on the cylinder and/or on the discs to throw the cut material rearwards. The rotary cutter and shredder consist of two swinging knives rotating in a horizontal plane and housing. The rotating knives cut the material by impact and shear force. The material is carried to the discharge end by virtue of the kinetic energy imparted by the cutting blade. Flail Mower The flail mower cuts the plants, chops for them into small feed lengths and blows the cut and chopped material into the accompanying trailer. These machines are used for harvesting the crop for daily consumption or for silage making. The chopped lengths of the stalks can be varied from fine-medium to course by increasing or decreasing the clearance between the shear-bar and the flail-tip. The above machine can also be used for forge conditioning required to increase the drying rate during hay making process. Cylinder Type Mower: It is generally used for lawn mowing. It includes lawn mowers and gang mowers. It could be hand-propelled and self-propelled lawn mowers and tractor-drawn and tractor-mounted gang mowers. It has rotating helical blades arranged in horizontal plane (Figs. 1 & 2). There are three gangs in this mower having 3-4 helical blades each supported over vertical discs. The rotors of this type of mowers are supported on ball bearings at each end. With the rotation of blades, forage or grasses are cut for example lawn mower. It can cover about 1.5-2.0 ha/h at a speed of 8-10 km/h. Fig. 1: Side view of a cylinder mower. Rotating Disc-type Mowers: There are two types of disc mowers. In one type, there are discs on the periphery of which free-swinging knives (2-4 in numbers) are attached. Sometimes the rotating knives are mounted on bearings on a cutter bar similar to one used for a conventional reciprocating mower. Cutting in this type of mower takes place due to impact and as such energy requirements are comparatively low. In drum-type mowers, usually there are two large-diameter moving drums. These are driven by belt and pullet system. Three to four steel blades are attached to each disc, which revolve at a speed of about 2000-rpm. The diameter of disc ranges from 60 to 80 cm. In this one also, cutting takes place due to impact. These types of mowers make fairly good swaths and the harvested material is dried speedily. Due to absence of gear or chain drive, the action is usually quite smooth and power consumption low. Fig. 2: A view of gang mower. Adjustments of mower reaper Sr. No. Part Problem Adjustment 1. Reel i) Does not rotate i) Check tension of reel belt. Reel by hand to ensure that the drive pulley key and belt are secured. ii) Adjust height according to height of crop ii)Improper gathering of crop 2. Cutter bar Unsatisfactory cutting i) Reduce forward speed ii) Correct the registration iii) Sharpen the knife sections or replace if worn out. iv) Check drive belt tension. If loose, tighten Windrowers In some areas, farmers find that cutting and windrowing the top portion of the plants with the grain attached permit earlier harvesting and protect the grain under the following conditions. (i) When the grain is unevenly ripened. (ii) When fields are weedy. (iii) When the straw is green but the crop is ripe. (iv) When the grain is high in moisture. (v) When crop conditions are such that legume crops tend to shatter if left until ripe, and (vi) When weather conditions delay direct combining. The windrowing machine consists of a power- takeoff-driven knife, platform canvas, and reel. The heads of grain are clipped off and fall upon the travelling platform canvas, which delivers the grain over one end onto the stubble. Most windrowing machines deliver the grain over the end farthest away from the standing grain. Center-delivery machines are available. Self-Propelled Windrowers Self-propelled windrowers consist of two types of headers. The augur cross feed is the most common type on hay machines but is too aggressive for grain. The draper type is employed on windrowers intended for both grain and hay. The maximum width that should be cut with a hay windrower is limited primarily by the maximum size of windrow that will cure in an acceptable time. Windrowers with cutting widths of 3.65 m and 4.25 m are popular in irrigated areas where hay yields per cutting are usually 2.2 to 3.4 Mg of dry matter per ha. Knife speeds are about the same as on mower-conditioners but strokes are often 6 to 10 mm greater than the 76.2 mm guard spacing. Chrome-plated knife sections are used almost universally. Conditioning attachments are usually 0.9 to 1.4 m wide, but the direct-feed, full- width-conditioner system of pull-type mower-conditioners has also been applied to some 2.75 m self- propelled machines.