Refinery Equipment Operation & Safety Lecture 7 PDF
Document Details
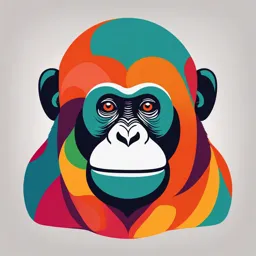
Uploaded by TrustyCornett
Professor Khaled AlKhaldi
Tags
Summary
This lecture continues the discussion of refinery equipment and operation safety, focusing on a hydrocracking flowsheet. The document lays out differences between different refinery operations, including details of high and low-temperature separation. Concepts like DEA absorption for H2S removal, and the operation of fractionator trays are covered.
Full Transcript
REFINERY EQUIPMENT OPERATION & SAFETY 1 HYDROCRACKER UNIT OPERATION: PART 5 2 Differences This flow sheet hydrocracking feed differs from Kuwait Refinery In Kuwait Refinery, the feed is made from: o Atmospheric gasoil o Vacuum light gasoil...
REFINERY EQUIPMENT OPERATION & SAFETY 1 HYDROCRACKER UNIT OPERATION: PART 5 2 Differences This flow sheet hydrocracking feed differs from Kuwait Refinery In Kuwait Refinery, the feed is made from: o Atmospheric gasoil o Vacuum light gasoil o Vacuum heavy gasoil o Coker gas oil 3 Hydrocracker Flowsheet 4 TWO STAGES OPERATION MODE 7. High Pressure Separator (stationary equipment) The recycle gas made of unreacted hydrogen plus H2S and NH3 is separated in the high-pressure separator It operates at 140°F and 2280 psig. While the mixed liquid stream (Sour water +liquid hydrocarbons) continues to the low-pressure separator. 5 TWO STAGES OPERATION MODE 7. High Pressure Separator (stationary equipment) Can you tell if hydrogen, hydrogen sulfide, and ammonia are not liquids at this high pressure? For H2, Pc =188.2 bar For H2S, Pc = 1309 psi For NH3, Pc =1647 psi No substance can be liquid at a pressure greater that the critical pressure 6 TWO STAGES OPERATION MODE 8. Low Temperature Separator (stationary equipment) The liquid is depressurized to 550 psig before it is flashed at low pressure in the low-pressure separator. The sour water (water+H2S) is then separated from the liquid hydrocarbon and sent to sour water treating facilities while the hydrocarbon stream leaving the low-pressure separator is fed to H2S stripper T-101. The low-pressure separator overhead vapors flow to high-pressure amine contractor. 7 8 TWO STAGES OPERATION MODE The amount of H2S that can react 9. Recycle Gas Absorber (stationary equipment) depends on the operating DEA (diethanolamine) absorption is used to conditions. remove H2S from the recycled gas in recycle Low temperature, high pressure, gas absorber. and high H2S concentration in the DEA: Di-Ethanol-Amine H2S absorber favor the reaction. H2S gas is absorbed by the DEA solution About 90% of the H2S formed by because of the chemical reaction of DEA with the desulfurization reactions is H2S. removed from the recycled gas in 2R 2 NH + H2 S ⇌ 2(R 2 NH2 ) + S a high-pressure absorber by scrubbing the gas with aqueous This reaction proceeds to the right at low T, to diethanolamine solution. the left at high T 9 The absorber is a vertical vessel packed with stainless steel ballast rings. Recycled gas flows through a support plate and upward through the packing. 10 A lean DEA solution from the DEA regenerator enters the top of the absorber through an inlet distributor and flows downward through the packing. Rich DEA from the bottom of the absorber is sent to the H2S recovery unit. 11 TWO STAGES OPERATION MODE 10. Recycle Gas Compressor (rotary equipment) Recycled gas is circulated by recycle gas compressor C-101, driven by a steam turbine. The largest portion of the recycled gas stream joins the oil feed stream before the feed effluent exchangers. A portion of the gas stream from the recycling compressor flows on temperature control to interbed quenching. 12 TWO STAGES OPERATION MODE The stripper overhead vapor is partially condensed in air cooler and a water 11. H2S Stripper (stationary equipment) cooler then flashed in reflux drum. The Hydrocarbon liquid flows to the stripper sour gas from the reflux drum is sent pre-flash drum to remove some of the to a low-pressure amine contactor. The light ends and H2S from the low-pressure condensed hydrocarbon liquid is separator oil before it is stripped in the refluxed back to the stripper. H2S stripper T-101. H2S stripper bottoms are sent to The stripper column contains packed product fractionator T-102 after heat sections below the feed plate and two exchange with diesel in E-116, sieve trays above the feed inlet. Stripping circulating reflux in E-118, and is achieved with steam, which removes fractionator bottoms in E-118. H2S and light ends. 13 TWO STAGES OPERATION MODE 12. Fractionator (stationary equipment) The fractionator feed is then brought to column temperature by heating in the feed heater H-102. After heating, the partially vaporized fractionator feed is introduced into the flash zone of the fractionator. In the flash zone, the vapor and liquid separate. 14 TWO STAGES OPERATION MODE 12. Fractionator (stationary equipment) The vapor passes up through the rectifying section, containing approximately 27 trays. Vapor leaving the top tray of the column is condensed in overhead condensers. The condensed overhead vapor is separated into hydrocarbon and water phases. Part of the hydrocarbon is recovered as overhead product, and the rest is sent back to the column as reflux to ensure good separation. Heat is removed from the fractionator column in the overhead condenser and by the falling liquid reflux. 15 TWO STAGES OPERATION MODE Pumparounds: Liquid is removed from the tower, cooled by exchanging heat, 12. Fractionator (stationary then returned to the tower at a higher equipment) plate Pumparounds (circulated side Sometimes only a portion of the streams taken from higher pumparounds is returned to the tower, temperature (below) regions and the rest is taken as a product stream returned to lower temperature regions (above)), provide extra The pumparound return stream liquid refluxes to enhance the condenses more of the vapors coming separation and provide heat for from the lower tower section and then the reboiler and feed preheat. increases reflux below that point 16 TWO STAGES OPERATION MODE 12. Fractionator (stationary equipment) Pumparounds (circulated side streams taken from higher temperature (below) regions and returned to lower temperature regions (above)), provide extra liquid refluxes to enhance the separation and provide heat for the reboiler and feed preheat. 17 TWO STAGES OPERATION MODE 12. Fractionator (stationary equipment) The portion of the column below the flash zone contains five trays. Superheated steam is injected below the bottom tray. As the steam passes up through the stripping section, it strips light components from the residual liquid from the flash zone. 18 FRACTIONATOR TRAYS Vapor bubbles 1. Sieve trays Tray weir downcomer Vapor goes up through Tray holes 19 FRACTIONATOR TRAYS Vapor bubbles 2. Valve trays Tray weir downcomer Vapor goes up through Tray holes 20 FRACTIONATOR TRAYS Vapor bubbles 3. Bubble Cap trays Tray weir downcomer Vapor goes up through Tray holes 21 OPERATION MODES Hydrocracker units can be operated in the following possible modes: 1. single-stage (once-through-mode) operation, 2. single-stage operation with partial or total recycling, and 3. two-stage operation. The choice of the process configuration is tied to the catalyst system. The main parameters to be considered are feedstock quality, the product quality required, and the investment and operating costs of the unit. 22 OPERATION MODES 1. One-Stage Hydrocracking: for light feed, conversion between 40%-80%. 2. One-Stage with recycle: Recycle of the bottoms of the distillation tower enhances the conversion 23 OPERATION MODES 3. Two-Stage Hydrocracking: the fractionator bottoms are sent to the second reactor 24 TWO-STAGE HYDROCRACKING First Stage main reactions are: HDS: Hydrodesulfurization HDN: Hydro-denitrification HDA: Aromatic Hydrogenation 25 TWO-STAGE HYDROCRACKING Second Stage main reactions are: HDA: Aromatic Hydrogenation HDI: Hydro-isomerization HDC: Hydrocracking 26