Lecture 17: Wet-End Operations (Part 1) PDF
Document Details
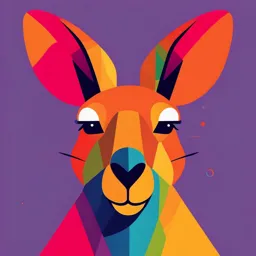
Uploaded by WellConnectedOrphism9496
University of the Philippines Los Baños
Engr. Jeanette O. Grande
Tags
Summary
This document provides a lecture on wet-end operations in paper manufacturing. It discusses the different stages and operations involved in the process, from raw material breakdown to final product. It also covers different machine types such as Fourdrinier and Cylinder machines along with various equipment and their functionality.
Full Transcript
Lecture 17: Wet-End Operations (Part 1) Slide 1 Chapter 6: Wet-End Operations (Part 1) 1 Slide 2 The course outline actually foll...
Lecture 17: Wet-End Operations (Part 1) Slide 1 Chapter 6: Wet-End Operations (Part 1) 1 Slide 2 The course outline actually follows the story of the whole papermaking process – from the initial breakdown of raw materials, to breakdown of the raw materials into fibers, and then the reassembly of the fibers to form the product – paper. The breakdown of operations forms the basis for the organization of the course. The papermaking industry can be divided into a series of sequential unit operations. The first unit operation –pulping, deals with the liberation of the fibers – product : pulp, the quality of which depends on the method used. The second unit operation – stock preparation, further prepares the fibers for their role in papermaking. Refiners modify the fibers physically. Stock preparation also includes the addition of chemicals to enhance the properties of the pulp. The next operation, actual paper/paperboard manufacturing is divided to at least three sub- operations –forming , pressing and drying. While web modification is generally found or performed on the paper machine, it is easier to treat as a separate unit operation. The most common of these operations improve the paper for printing by making the surface smoother or more resistant to water or ink. Some machines may include none of these modification operations while others may have several. The final group of operations, converting operations. For today, I’ll just give you an overview of the paper manufacturing operations, particularly that of the manufacturing machinery. Prepared by: Engr. Jeanette O. Grande Lecture 17: Wet-End Operations (Part 1) Slide 3 VII. Wet End Paper Machine Operations We will not really look at the detailed design of each part of the paper machine. At the end of our discussion, at least you’ll be able to tell the essential components, their description and influence in the papermaking process or their effects on the quality of paper. Slide 4 Fourdrinier Machine http://en.wikipedia.org/wiki/Paper_machine Organization of the outline – wet end and dry end operations, follow Smook’s outline. Other references would present the topic by considering 4 sections – the division of which is based on the 4 parts of a fourdrinier machine. One of the reasons is that fourdrinier is not the only paper machine that we have. Prepared by: Engr. Jeanette O. Grande Lecture 17: Wet-End Operations (Part 1) Slide 5 Paper Machines: 1. Fourdrinier Paper Machine http://www.glogster.com Originally, it (Fourdrinier) referred to the wet end of the earliest commercial paper machine invented by Louis Robert and first constructed in 1803 by Henry and Sealy Fourdrinier. Conventional paper machine with horizontal forming wire The machine name comes from the type of wet end used. In the Fourdrinier machine, the cleaned, screened and diluted stock enters the picture in the upper left corner behind the headbox. This machine is said to be excellent for lightweight paper Head Box - receives the liquid pulp, with all ingredients ready to make the paper Flow Spreader - controls the pulp distribution on the Table Fourdrinier Table - a perforated conveyor belt that supports the pulp solids and allows the water to drain through Press Section - rollers that squeeze water from the pulp Dryer Section - typically steam drums (cans) that progressively dry the pulp as it turns to paper; the drying section may also include electric or gas infrared heaters and convection heating hoods. Calendar Stack - metal rollers that compress the paper to form uniform thickness; may be smooth or include some sort of pattern or texture. Reel - takes up the paper as it is finished Prepared by: Engr. Jeanette O. Grande Lecture 17: Wet-End Operations (Part 1) Slide 6 2. Cylinder Machine (Cylinder Board Machine/Mold Machine) Any paper or board machine that utilizes cylinder formers However, manufacture of heavy paper or paperboard on the fourdrinier machine requires the delivery of a large amount of stock to the wire, which drains slowly and requires that the machine be run at reduced speeds. The solution to this problem is found in the use of the multicylinder machine. Slide 7 As the forming cylinder rotates through the vat of stock, the water flows through the wire on the surface of the cylinder and the fibers catch on the wire, forming the web of paper. A felt (a wool blanket woven into a continuous belt) is pressed against the wet web by the couch roll at the top of each forming cylinder. The wet web will stick to the wet felt and be removed from the forming cylinder at this point. The felt continues through the forming section, picking up sheets from all the vats in succession. The felt and web picked up from the first cylinder proceed to the second cylinder, where they are pressed against the web formed there to pick it up. If each cylinder forms a web that is 0.003 in. thick, a machine with 5 cylinders can produce a web with a total of 0.015 in. Since the web is formed in thin sections, the machine can be run faster than if the total thickness were made in one layer. Prepared by: Engr. Jeanette O. Grande Lecture 17: Wet-End Operations (Part 1) Slide 8 After all the layers are picked up by the felt, the web is sandwiched between two felts and pressed to remove the water and promote bonding. The greater thickness of the web requires that it be passed through more presses and dryers than the web in the Fourdrinier machine. Slide 9 Advantages: Since the web is formed in thin sections, the machine runs faster than if the total thickness were made in one layer. Formation of each layer is better facilitated than if the total thickness were made in one former. The different plies do not need to be made from the same stock, I.e. manufacture of combination boxboard (white on the outside and gray on the inside) Combination boxboards – the white layer may contain bleached kraft pulp while the gray layer is made up of old newspapers, corrugating and carton clippings Slide 10 Prepared by: Engr. Jeanette O. Grande Lecture 17: Wet-End Operations (Part 1) Slide 11 http://www.gaspaperdryer.org Head Box - receives the liquid pulp, with all ingredients ready to make the paper Flow Spreader - controls the pulp distribution on the Table Fourdrinier Table - a perforated conveyor belt that supports the pulp solids and allows the water to drain through Press Section - rollers that squeeze water from the pulp Dryer Section - typically steam drums (cans) that progressively dry the pulp as it turns to paper; the drying section may also include electric or gas infrared heaters and convection heating hoods. Calendar Stack - metal rollers that compress the paper to form uniform thickness; may be smooth or include some sort of pattern or texture. Reel - takes up the paper as it is finished Slide 12 Headbox (Flowbox) Prepared by: Engr. Jeanette O. Grande Lecture 17: Wet-End Operations (Part 1) Slide 13 http://www.paperonweb.com/dict.htm It is very important that the headbox distribute the slurry on the Fourdrinier table in a uniform manner. Otherwise, the paper that will be produced will not have uniform strength and thickness along the cross-section of the paper. Slide 14 Slide 15 Headbox (Flowbox) That part of the paper machine which receives the stock delivered by the fan pump (approach system) and transforms the pipeline flow into a uniform rectangular flow equal in width to the paper machine and at uniform velocity in the machine direction. Prepared by: Engr. Jeanette O. Grande Lecture 17: Wet-End Operations (Part 1) Since the formation and uniformity of the final paper product are dependent on the even dispersion of fibers and fillers, the design and operation of the headbox system is absolutely critical to a successful papermaking system. Head Box or Flow Box or Breast Box The part of the paper machine whose primary function is to deliver a uniform dispersion of fibers in water at the proper speed through the slice opening to the paper machine wire. The flow spreader supplies the pulp in a single pass through the tapered manifold. Slide 16 Approach system FAN PUMP (APPROACH SYSTEM) Fan pump loop wherein the paper stock is measured, diluted, mixed with any necessary non-fibrous additives and finally screened and cleaned before being discharged onto the paper machine forming medium. It extends from the machine chest to the headbox slice lip; occasionally, certain stock chests and refiners may also be considered part of the approach system. Assuming good control in the pulp mill, the pulp furnish should be reasonably free from impurities. Still, most paper machine approach systems utilize screens and cleaners as insurance against foreign contamination. In practice, the screens function mainly to remove gross contamination and defloc the fibers, while the centricleaners are designed to remove debris. The heart of the approach system is the fan pump, which serves to mix the stock with the white water and deliver to blend to the headbox. (white water – general term for any stock filtrate or process water that contains fiber fines. On the papermachine, white machine is produced during the forming and dewatering of the web. “Rich white water” contains high concentration of fiber fines, while “lean white water” contains a low concentration. Prepared by: Engr. Jeanette O. Grande Lecture 17: Wet-End Operations (Part 1) Slide 17 Headbox: Specific Operational Objectives 1. Spread stock evenly across the width of the machine. 2. Level-out cross-currents and consistency variations. 3. Level out machine direction velocity gradients. 4. Create controlled turbulence to eliminate fiber flocculation. 5. Discharge evenly from the slice opening and impinge on the forming fabric at the correct location and angle. Functions – to deliver a ribbon of stock to the wire at uniform dilution, thickness, and speed. The headbox is a tank of necessary size to deliver the volume of stock required and is positioned above or beside the wire so it can deliver the stock to the wire through the slice. Slide 18 Headboxes: Types (based on the required speed of stock delivery) A. Open Headboxes B. Pressurized Headboxes – air-cushioned or hydraulic designs Headboxes can be roughly divided into two types – depending on the speed of stock delivery required on the wire Prepared by: Engr. Jeanette O. Grande Lecture 17: Wet-End Operations (Part 1) Slide 19 A. Open Headboxes Open to the atmosphere The discharge head is provided solely by a gravity head of stock. Found mainly on slow-speed pulp machines As paper machine speeds increased, it became impractical to increase the height of stock by a corresponding amount, and the pressure headbox was developed. If we want to increase the flow rate from the headbox, we can increase the head (height of liquid). The headbox could be made taller to hold more liquid. Slide 20 B. Pressurized headboxes 1. Hydraulic design Pressurized, filled headbox The discharge velocity from the slice depends directly on the feeding pump pressure. 2. Air-cushioned headbox Pressurized, closed headbox with a controlled liquid level The air cushion above the liquid level serves to dampen out small pressure fluctuations in the approach flow. Hydraulic – does not utilize an integral air chamber Hydraulic pressure – fluid pressure contained in a closed or constricted pressure Prepared by: Engr. Jeanette O. Grande Lecture 17: Wet-End Operations (Part 1) Slide 21 Hydraulic design Slide 22 Slide 23 Flowspreader (Manifold Distributor) Headbox inlet assembly which receives a pipeline flow of dilute stock and distributes this fiber disperion uniformly across the width of the headbox. Most common type of flowspreader in current use – multi-tube, tapered inlet manifold with recirculation Tapered header – had become the most common solution to the flow-spreading problem. Prepared by: Engr. Jeanette O. Grande Lecture 17: Wet-End Operations (Part 1) Slide 24 The stock is introduced at the wide end of the manifold; as it is forced to flow out the side through the tubes into the headbox, the taper maintains the pressure and degree of turbulence in the flow. Slide 25 Prepared by: Engr. Jeanette O. Grande Lecture 17: Wet-End Operations (Part 1) Slide 26 Rectifier Roll (Perforated Roll, Holey Roll, Evener Roll, Distributor Roll) The roll nearest the slice Rotating, perforated roll within the headbox through which stock must pass on its way to the slice. The rectifier roll serves to even out irregularities and create microturbulence to keep fibers deflocculated. The corners of square-shaped boxes provide areas in which the flow can slow down or become stagnant, allowing the fibers to clump together and perhaps even allowing slime or other bacteria to grow. The roll is rotated in use, causing the stock to flow in through holes on one side, be mixed with other flows, and be passed out the holes on the other side. These rolls can help to even out the flow rate across the machine and also help keep the fibers from flocculating and causing lumpy paper. Slide 27 Prepared by: Engr. Jeanette O. Grande Lecture 17: Wet-End Operations (Part 1) Slide 28 Slice Rectangular full-width nozzle with completely adjustable opening through which the headbox delivers the stock jet to the forming zone Every slice has a top lip and an apron (bottom lip), both constructed of suitable alloy materials to resist corrosion. Types: knife (vertical or straight), converging, combination types Slice – narrow opening in the headbox through which the stock flows. It must be adjustable so that the thickness of the ribbon of stock can be controlled. The headbox and slice work together to control the volume or weight of fibers as well as the flow rate Slide 29 Slice Designs L = projection of the apron beyond the inner vertical surface b = slice opening between vertical knife and end of apron Prepared by: Engr. Jeanette O. Grande Lecture 17: Wet-End Operations (Part 1) Slide 30 Slice: 2 Types of Jet Delivery Two types of jet delivery are possible. Slide 31 Slice: 2 Types of Jet Delivery Velocity Formation – more commonly utilized Pressure formation – results in excessive discharge at the breast roll with low retention of fines and fillers and poor sheet formation Breast roll – large-diameter roll around which the fourdrinier forming wire passes at the end where the stock is discharged onto the wire Prepared by: Engr. Jeanette O. Grande Lecture 17: Wet-End Operations (Part 1) Slide 32 Operation of the Headbox: Main operating variables – stock consistency, temperature and jet-to-wire speed ratio Consistency is varied by raising or lowering the slice opening. The ratio of jet velocity to wire velocity is usually adjusted near unity to achieve best sheet formation. If the jet velocity lags the wire, the sheet is said to be “dragged”; if the jet velocity exceeds the wire speed, the sheet is said to be “rushed”. The flow rate from the box relative to the speed of the wire is important for controlling the properties of the paper. It is easy to understand that if the stock coming from the slice moves more slowly than the wire is coming, it is possible for the fibers to be caught by the wire and lined up in the machine direction. If the flow from the slice is too fast, the fibers will tumble over one another or may even form a permanent wave pattern in the paper. Slide 33 The Basic Sheet Forming Process Forming was conceptualized as a composite of 3 basic hydrodynamic processes. The most important effect of the drainage process is the dewatering of the fiber suspension to form the mat. When the fibers are free to move independently of one another, drainage proceeds by the mechanism of filtration and the fibers are deposited in discrete layers. Prepared by: Engr. Jeanette O. Grande Lecture 17: Wet-End Operations (Part 1) Slide 34 Filtration is the dominant mechanism in most fourdrinier forming applications. When the fibers in suspension are immobilized, they floc together in coherent networks, drainage then occurs by thickening, amore felted sheet structure is formed. Slide 35 http://www.xerium.com Prepared by: Engr. Jeanette O. Grande Lecture 17: Wet-End Operations (Part 1) Slide 36 Fourdrinier (Wire Part) Horizontal forming device consisting of an endless fabric (onto which the fiber suspension impinges) travelling between the breast roll and the couch roll, and supported by various elements which dewater the fiber suspension. Coach roll (Suction Coach) – any roll used to separate the wet paper from the forming wire Breast roll – large-diameter roll around which the fourdrinier forming wire passes at the end where the stock is discharged onto the wire The fabric travels between two large rolls – the breast roll near the headbox and the couch roll at the other end. Slide 37 Dandy roll – skeletal roll with a wire cloth covering which is mounted above the fourdrinier and rides on the stock in the suction box area. The dandy roll serves to compact the sheet and improve formation in the top portion. Some dandy rolls carry a pattern in the wire facing that is transferred to the sheet to provide watermarking or other special effects. Lump breaker roll – plain covered roll riding on top of the couch roll, used to consolidate the web and aid in water removal. Prepared by: Engr. Jeanette O. Grande Lecture 17: Wet-End Operations (Part 1) Slide 38 (M) Coach roll (Suction Coach) – any roll used to separate the wet paper from the forming wire (D) Breast roll – large-diameter roll around which the fourdrinier forming wire passes at the end where the stock is discharged onto the wire The fabric travels between two large rolls – the breast roll near the headbox and the couch roll at the other end. Slide 39 (L) Dandy Roll (Marking Roll) skeletal roll with a wire cloth covering which is mounted above the fourdrinier and rides on the stock in the suction box area serves to compact the sheet and improve formation in the top portion Some dandy rolls carry a pattern in the wire facing that is transferred to the sheet to provide watermarking or other special effects. (N) Lump Breaker Roll plain covered roll riding on top of the couch roll, used to consolidate the web and aid in water removal. Watermark – design formed among the fibers of the sheet as a result of the wet paper web coming into contact with the pattern of a dandy roll or marking roll. The paper becomes thinner and more translucent where the fibers are displaced by the raised design. Prepared by: Engr. Jeanette O. Grande Lecture 17: Wet-End Operations (Part 1) Slide 40 (P) Wire Turning Roll (Forward Drive Roll) Solid roll which is generously wrapped by the forming fabric, located immediately after the couch roll on the fourdrinier Slide 41 (S) Stretch Roll (Hitch Roll) Roll incorporated into every forming wire run, press felt run or dryer fabric run which moves up and down(or backward and forward) as a unit and controls tension in the run (G) Guide Roll (Alignment Roll) roll incorporated into every forming wire run, press felt run or dryer fabric run, which has positioning adjustment at one end and serves to keep the fabric or wire running without lateral movement Slide 42 (U) Forming Fabric (Plastic Wire) Endless belt of woven synthetic monofilament cloth for the drainage of stock and forming of the fiber web (U) Forming Wire Endless belt of woven wire cloth for drainage of stock and formation of the fibrous web Almost obsolete because of the development of forming fabrics Prepared by: Engr. Jeanette O. Grande Lecture 17: Wet-End Operations (Part 1) Slide 43 Double Weave Forming Fabric http://en.jsjinni.cn Prepared by: Engr. Jeanette O. Grande Lecture 17: Wet-End Operations (Part 1) Slide 44 http://www.xerium.com The paper furnish consists of fibers, fillers, chemical systems, and water. The major task of the forming fabric is dewatering and forming an initial fiber mat to control drainage and retention properties in the successional sheet forming process. Even very thin fiber mat has a higher resistance to drainage than the wire used. The amount of dewatering is thus primarily determined by the drainage behavior of the fiber mat. However, the wire's properties influence the fiber mat's structure as well as its filtration properties. The first synthetic wires have passed through several pioneering stages as they have evolved over the past decades. Initially, the main focus was placed on the lifetime. It was not until 2.5- layer designs were introduced that an increase in fiber support became possible along with a corresponding improvement in the papermaking properties of forming fabrics. The last major step was the development of SSB fabrics, which are based on a technology that has had lasting influence on the forming fabric market. In Western Europe, this technology has captured approximately 80% of the market over the past 10 years. Prepared by: Engr. Jeanette O. Grande