Manufacturing Activities PDF
Document Details
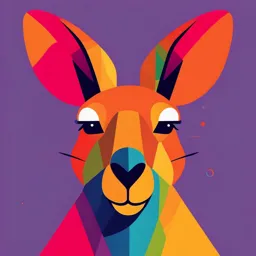
Uploaded by ProvenGalaxy
Tags
Related
- Production And Process Controls 2021 PDF
- Manufacturing Pharmacy (Lec) PDF
- Sesión 4 - Control de Calidad de Procesos, Control Inspectivo, Material de Empaque PDF
- GMP Lecture 1 & 2 PDF
- Lecture 1: Overview of Pharmaceutical and Industrial Pharmacy Regulation PDF
- C3-3 - VIÊN NANG - Manufacturing Guide PDF
Summary
This document provides an overview of manufacturing activities, including primary, secondary, tertiary, and toll manufacturing of drug products. It also discusses quality assurance, research and development, and various departments involved in pharmaceutical production. The document covers different procedures and processes related to medicine manufacturing.
Full Transcript
I. INTRODUCTION Production - Deals w/ all stages of mfg. MANUFACTURING ACTIVITIES batches of finished drug products. 1. Primary Mfg....
I. INTRODUCTION Production - Deals w/ all stages of mfg. MANUFACTURING ACTIVITIES batches of finished drug products. 1. Primary Mfg. - Accomplished the Batch - Raw materials Manuf Record (BMR) / - API + excipients Master Batch Record (MBR) 2. Secondary Mfg Batch - Dosage forms - Specific quantity of drug product having uniform 3. Tertiary Mfg. character & quality produced - Packaging, labeling, or during the same cycle of mfg. repacking of bulk finished products Lot - Portion of a batch 4. Toll Mfg. - An arrangement whereby a Batch / Lot No. competent manufactures the - Identification & traceability products for another company. Warehouse Ex: Hizon Laboratories Inc. - Stores materials and finished - Pfizer - Centrium products - Galderma - Cetaphil - Holds incoming components UNIBLAB Amherst Laboratories Inc in a quarantine area (yellow label) - Involved in purchasing & DEPARTMENTS IN A MANUF logistics COMPANY Quality Assurance Research & Development - Assures all operations meet - Formulate new products the required standards of - Improves existing products safety and efficacy (chMP) - Prepares the master formula - Conducts quality audit & - Instifies overages monitoring - Prepares SOPs Overage - Addition of an excess amount of API in an unstable preparation. Quality Control - Lactose - Test compliance of materials - Most common < and products to monohydrate specifications. anhydrous/ - Conducts sampling spray-dried - Performs in-process quality - Sucrose and Dextrose control and environmental - Microcrystalline cellulose testing. (Avicel ®) - direct compression Marketing - Starch - Studies current market trends, - Multifunctional consumer behavior, and - Dibasic Calcium Phosphate product status in the market - Only inorganic salt - Advertisement and - Mannitol and Xylitol promotion. - Chewable tablets Regulatory 2. Binder - Ensures compliance w/all - Imparts cohesiveness to pertinent regulations and powders causing them to laws about drugs and their form granules marketing - License to operate (LTO) and Inadequate Too much Certificate of Product Binder binder Registration (CPR) (Overwet) Engineering Soft granules Too hard granules - Installs, maintains and repairs equipment and premises Too much fines Difficulty in dry - Conducts validation and screening qualification. Inadequately Hampered hard tablets disintegration II. MANUFACTURING OF THE SOLID and dissolution DOSAGE FORMS ( ↓ BA) A. Formulation Components - Starch Paste - Wet granulations 1. Diluent (Filler / Bulking Agent) - Acacia & Tragacanth - Inert substances added to - Gelatin increase tablet size or fill the - Sucrose capsule body. - Cellulose Derivatives - Capillary action - Methylcellulose - Ethylcellulose - Release of gas - Carboxymethylcellulo - Effervescent tablets se - Hydroxypropylmethyl 4. Superdisintegrant cellulose - Newer class of disintegrants w/c are effective at much - PUP lower levels - Chewable tablets - Lygroscopic 3. Disintegrant Crosslinked polymers - Facilitates the breakup of a Sodium starch glycolate tablet when in contact (Primojel ® / Explotab ®) w/aqueous medium Crospovidone - “Double Disintegration” Croscarmellose Na 5. AntiFrictional Agents - Added to reduce friction and improve flow - Mostly hydrophobic and added at low concentration prior to compression Running powders - Starch - Lubricant + external - Clams disintegrant - Cellulose Lubricant - Alginates - Reduces friction between the - Na Alginate, Alginic tablet and die wall to acid facilitate ejection from die - Gums cavity. - Ion-exchange Resins Antiadherent - Polacrilin Na - Reduces sticking to die walls - Moa: and picking by punches. - Swelling Glidant - Starch, alginales - Reduces friction among particles to enhance the flow - Wicking - MCL, calcium silicate Stearates (Mg, Ca, water- soluble (FD Water-insoluble (O & Na) & C) C) - Lubricant, anti-adherent Added as solution Added as a dry & glidant powder or suspension - Stearic acid Purified Talc FD&C Name - Anti-adherent Designation & lubricant Blue no. 1 Brilliant blue Colloidal Talc Blue no. 2 Indigotine - Glidant Green no. 3 Fast Green Colloidal SiO2 Red no. 3 Erythrosine (Cab-o-sil ®) - Glidant Red no. 40 Allura Red Silicates (Ca, Mg) Yellow no. 5 Tartrazine - Glidant Yellow no. 6 Sunset Yellow PEG & Sodium 7. Flavorant Lauryl Sulfate - Masks the unpleasant taste of - Hydrophilic the drug lubricants 6. Colorant Taste Flavorant - Disguises off-color drugs and Salty Cinnamon, Orange, improves apperance Cherry, Butterscotch Bitter Chocolate, Cherry, Raspberry, Mint Dyes Lakes Sour Fruity Synthetic organic Dyes adsorbed on an colorants inorganic oxide Oily Mint, Orange, Lemon - Iron oxide Unpleasantly Vanilla and Fruity - Aluminum sweet oxide FLAVORING TECHNIQUES A. Blending Nutritive Non-Nutritive - Fruit Flavors + Sour taste - Bitter taste + salty, sweet, & Sucrose Sugar Artificial sour tastes Alcohol - Salt reduces sourness and Fructose Mannitol Sucrose - increases sweetness 1000x - vanillin, Msg monosodiumy (splenda) glutanate, benzaldehyde Dextrose Xylitol Saccharin - 500x B. Overshadow MECS (high Surbitol Na Saccharin - - Addition of flavor whose fructose 300x intensity is longer and syrup) stronger than the obvious taste Erythritol Acesulfame K - 180-200x - Ex: methylsalicylate Glycyrrhiza Aspartame - Oleoresins 180-200x (Nutrasweet) C. Physical Na cyclamale - - Formation of insoluble 30x (Magic compounds Sugar) - Emulsification of oils - Effervescence UNIT PROCESS TABLETS - High viscosity of fluids - Coating of tablets D. Chemical - Adsorption of the drug on a substance - Formation of a complex of the drug - E. Physiological - Taste buds may be anesthetized by menthol or mint flavors. 8. Sweetener - Masks the unpleasant taste of the drug. - Materials is unshed in between B. UNIT PROCESS moving furface Roller Mill 1. DISPENSING - 2 metal cylindrical rolls rotating - First step in any manufacturing process E. Combined - Weighing and measuring - Utilizes both impact and attrition Objective: accuracy of weight methods - uniform dose Ball Mill - Hollow cylindrical containing balls 2. MILLING Fluid Energy Mill - Particle size reduction - Air with very high-pressure - Aka sizing, crushing, grinding, and pulverization 3. MIXING Objective: easier and more uniform mixing - Blending materials together into 1 mass Methods Objectives: A. Cutting - Uniform dose - Shearing - Even appearance - Material is cut by means of sharp Mottling blades - fibrous materials - Uneven color distribution Cutter Mill -Avoid segregation - Cuts particles using rotating knives EQUIPMENT B. Compression A. Batch Type Mixer - Material is crushed by application of - All materials are loaded together, pressure mixed for a long period and Edge Runner Mill discharged a single batch - 2 heavy wheels rotate gainst the - unit : kg/batch material B. Continuous mixer C. Impact - Motionless mixer - Material is hit by an object or it - Material continuously travel form strikes a stationary surface dragging port to the discharge nozzle Hammer Mill - Agitates and moves materials - 4 or more hammering ____ on a through the equipment, mixing them shaft; swinging arms are fixed in one quick pass - Unit: kg/hour D. Attrition MIXING EQUIPMENT Rotating Shell / Tumbling Mixers - Increase flowability & - Drum type blender compressibility - Cylindrical shaped drum - Types: - Rotates horizontally - Good Granules - 90% - Poor crossflow - Pass through sieve #20 What to do? Baffles - Fine Granules - 10% - Double - Lone Blender - Pass through sieve - conical shaped at both ends #40 - better crossflow - Two-Shell / U-Shell blender METHODS OF GRANULATION - alternating combines and draws the ingredients apart 1. Wet Granulation - for solid - solid blending - Most common; produces granules of the best quality Fixed Shell Mixers - Addition of liquid binder to - Ribbon blenders powders that forms larger - Consist of trough-like shell agglomerates. with moonled spiral or helical blades. Disadvantages: - Disadvantage: difficult to - Not for sensitive materials clean and increase power Ex: moisture sensitivites requirement - Multivitamins - Sigma Blade Mixers - Aspirin - Consist of double trough - Fine-consuming and labor intensive shaped shell w/ 2 sigma shaped blades killed 1. Blending of dry ingredients horizontally. - API, Diluent, internal - Planetary Mixer disintegrant - Paddles move around its own axis and around the central 2. Addition of liquid binder axis. - Moisture content: 31-35% - Vertical Impeller Mixer - Screw types impellers 3. Screening of the damp mass rotating inside a conical shell - Sieve no. 6 or 8 4. Granulation 4. Drying the granulation - Powder size enlargement to granules - Moisture content: 0.5 - 1% - Objectives: 5. Screening the drug granules - Sieve no. 12-20 - Compression of materials within the die cavity by the pressure excited by 6. Addition of running powder the punches. Fluid Bed Granulation - Easier and faster than the traditional PARTS OF TABLETING MACHINE process. - Materials are suspended in air while 1. Hopper the liquid binder is sprayed. - Holds the materials to be compressed. Slugging - Compression in large flat tablets. 2. Feed Shoe - Transfers the materials into 2. Dry Granulation the die cavity. - Double compression or pre-compression 3. Die - Powders are compacted into - Defines the size and shape of large pieces and crushed. the tablet Disadvantage: 4. Punches - Dusty - Compress the materials - For moisture sensitive and within the die. healt-labile material Processes: 5. Cam Tracks - Slugging formation of slugs - Guide the movement of (large tablets) punches - Roller compaction-formation of sheers REQUIREMENTS FOR TABLETING DRUG GRANULATION EQUIPMENT 1. Flowability Chilsonator Roller Compactor - Facilitates transfer - Used to compress powder into thin sheets Problems: - Arching/Bridging Oscillating Granulator - Arch-shaped obstruction - Used to crush slugs or sheets above the hopper outlet. into granules - Rat-holing - Discharge takes place only C. MANUFACTURING OF TABLETS above the hopper outlet. Tableting 2. Compressibility - Forms a stable, compact mass - Double impression material-related when pressure is applied. - Due to free rotation of the punches with engraving the Direct compression faces - Tablet processing without - Due to more than 1 factor granulation - Mottling process-related, - Used for some crystalline substances excipient-related, material-related - Increase flowability and - uneven color distribution compressibility (due to different color - Ex: KCl, NaCl, NaBr material) - Diluent: anhydrous/spray dried - process/excipient. lactose, Avicel ® Coating TABLETS DEFECTS - Application of coating material to a - Due to the tableting process moving bed of tablets w/ concurrent. - Capping - process-related - Use of heated air - Removal of top/bottom portion of tablet (air Methods: entrapment) Pan poring - Lamination process-related - For viscous coating solutions. - Separation of tablet into 2 or Pan spraying more layers (air entrapment) - Improves efficiency of - Cracking process-related coating process. - In concave tablets: rapid expansion of tablets COATING EQUIPMENT - Due to excipients Standard Coating Pan - Sticking excipient-related - Consists of a rotating circular - Die walls metal pan w/ducts. - Adhesion of material to the - Ex: Pellegrini Pan face of the press punch (excessive moisture) Perforated Coating Pan - Picking excipient-related - Heated air is exhausted - Punches through the perforations in - Adhesion of material to the the drum punch tip (excessive - Ex: Accela-cota pan moisture) - Chipping excipient-related Fluidized Bed Coater - Removal of small portion of - Air suspension coating or tablet edges (lack of binder) luvirster process. - Due to machine - Similar with fluid - 60-70% syrup bed-granulator. 4. Color Coating TYPES OF COATING - Critical step -> color % elegance 1. Sugarcoating Color coating agent: - Oldest method 60_70% syrup + colorant - Involves successive coating STEPS: of sucrose-based solution 4.1 Grossing - Develops color Disadvantage: 4.2 Heavy Syruping - Large increase in weight (50-100%) - Builds up color - Time-consuming 4.3 Regular Syruping - Requires expertise - Final color SUGAR COATING STEPS 5. Polishing - Produces shine/gloss 1. Sealing Polishing agents - Waterproofing Waxes (Ex: beeswax) - Separates tablet core from water 2. Film Coating Sealcoating Agents - Involves deposition of thin Shellac - pharmaceutical film of polymer around the glaze tablet core. CAP - Cellulose acetate phthalate Advantage: PVAP - polyvinyl acetate - Minimal increase in weight (2-3%) phthalate - Easier and faster Zein FILM COATING COMPONENTS 2. Subcoating Film former - Rounds off the tablets edges - Produces smooth, thin film - Most critical step Ex: - Step that adds most weight - Non-enteric: Subcoating agents - Celluloses Alternatives layers of grim or - Methacrylate gelatin and dusting powder. - PUP - Enteric: 3. Smoothing - Shellac - CAP - PVAP Mottling - PUAP - Uneven color distribution - Salol -> Phenyl sallicylate Sweating - Oily film or droplets of liquid Plasticizer - Due to humid conditions - Produces flexibility and elasticity Bridging Ex: - Markings are obscured - Castor oil - Due to coating pulling away within - Glycerin the logo - Phthalate esters - Logo-infilling - Due to accumulation of Surfactant partially spray-dried - Enhances spreadability of the materials. film Ex: Erosion - Polysorbate (Tween ®) - Removal of coating from the tablet surface due to friction among Alloying substance themselves. - Provides water solubility or permeability to the film Cratering Ex: - Craters appear exposing the tablet - PEG surface - Due to disruption of coating at the Glossant crown where the surface is more - Provides luster to the tablets porous without a separate polishing operation Blistering Ex: - Reduced adhesion and detachment of - beeswax the film - Due to the entrapment of gasses Volatile solvent underneath the film; decrease drying - Allows the spread of the temperature other components over the tablets. Blooming Ex: - Fading or dulling of the film - Alcohol + acetone - Due in high concentration and low molecular weight of plasticizer COATING DEFECTS Blushing - Whitish pecks or haziness of the film HGC Filling Steps - Due to precipitation of polymers at 1. Rectification high temperature; decrease drying 2. Separation temperature 3. Filling - known as tamping & disc dosing Twinning 4. Joining/closing - 2 tablets sticks together 5. Ejection - Due to inappropriate tablet shape or 6. Finishing - cleaning & polishing tacky coating formulation Orange Peel HGC Special Techniques - Rough, non-glossy film surface - Due to inadequate spreading of the 1. Sealing film: decrease in viscosity a. Gelatin Banding - Seals w/ a band of Film Cracking gelatin. - Type I b. Heat Welding - Due to thermal expansion of - Fuses through double tablet cores cause by over wall thickness. drying c. Thermal coupling - Type II - Uses liquid wetting - Due to core swelling caused agent. by excessive moisture uptake. 2. Coating Delayed Dissolution - Modifies solubility - Associated with exposure of tablet - Ex: cores to coating process conditions - Salol rather than a direct effect of the - CAP applied coating. - PUAp D. MANUFACTURING OF CAPSULES SGC METHODS: 1. Plate Process Hard Gelatin Capsules (HGC) - Oldest, uses gelatin sheets - HGC shells are manufactured in a 2. Rotary Die Process separate operation 3. Reciprocating the Process - Prom filling 2-3 Definition: Soft Gelatin Capsules (SGS) - Use gelatin ribbons brought together - Formed, filled and sealed in single Between 2 rotating dies operation III. MANUFACTURING OF SEMISOLID DOSAGE FORMS 2. Semisynthetic Polymers - Cellulose derivatives A. Manufacturing of ointments - Sodium starch glycolate - Primojel/Explotab ® 1. Incorporation - The components are mixed 3. Synthetic Polymers until a uniform preparation is - Carbomers (Carbopol ®) attained. - Smells at basic pH Ex: Unguator ® Electronic Mortar - Polyvinyl alcohol Pestle Ointment Roller Mill EQUIPMENT 2. Fusion 1. Mixing Tunk - The components are - Jacketed to allow heating or combined by melting cooling of contents together and cooled with - Made of stainless steel constant stirring until - SS 304-18% Cr an 8% Ni congested. - Most common Ex: Steam-jacketed kettle - SS 316, 16% cr, 10% Ni, Ointment Roller Mill 2%HO - Most inert - Resistant to B. Manufacturing of Gels conversion Gelling Agents 2. Mixers - Substances which when added to a. Mechanical stirrer water or an aqueous mixture, - Mixer w/various increase its viscosity. impellers mounted on shafts. TYPES OF GELLING AGENTS - WTD? Baffles Slanted (45 1. Natural Polymers degrees) - Alginic acid - Gelatin b. Colloid Mill - Starch - Used for - Acacia comminution of solids - Tragacanth and dispersion of - MgAlSilicate (Veegum) suspension - Bentonite c. Homogenizer - Compresses liquids Acids with high pressure; - Benzoic acid for emulsification - Sorbic acid MOA: Disrupts pH homeostasis d. Ultrasonifier - Uses ultrasonic Esters energy to produce - Parabens (p.hydroxybenzoic emulsions acid) Disadvantage: limited output - Methyl - Molds - More - Propyl - yeast/bacteria expensive - Long chain -> endocrine disruptors Components MOA: Cell wall disruption 1. API 2. Solvent/Vehicle Quaternary Ammonium 3. Buffers - Benzalkonium chloride 4. Viscosity Enhancers - Centriole 5. Humectants - Cetylpyridinium 6. Colorants, Flavors, and Fragrances - Chloride 7. Stability Enhances MOA: Cell wall disruption - Preservatives - Antioxidants Organic Mercurial - Thimerosal STABILITY ENHANCES - Phenylmercuric nitrate MOA: Binds to SH A. Preservatives - Enzyme inactivation - Prevent microbial growth - Effective at low STABILITY ENHANCERS concentration against all possible microorganism B. Antioxidants - Prevents oxidation of the CLASSIFICATION OF PRESERVATIVES API, fats, and oils - Butylated Alcohols hydroxytoluene - Ethanol anisole - Propylene glycol - Chlorobutanol CLASSIFICATIONS: - Phenylethyl alcohol MOA: Protein denaturation True antioxidants - Alpha tocopherol, BHT, - Diluted w/20:40 parts BHA, alkyl gallates of H2O - React with free radicals - Al acetate (Burrow’s Reducing Agents solution) - Ascorbic acid, sulfites, glutathione 3. Solution by extraction - For drugs of vegetable or animal origin. - Extracted with water or other Antioxidant Synergists solvents - EDTA, citric acid, tartaric - Ex: Belladona Extract acid - Percolation (alcohol + - Chelating agents H2O) - react with heavy metals STEPS: 1. Dispensing IV. MANUFACTURING OF SOLUTIONS - Meishing and measuring of A. Methods raw materials 1. Simple Solution 2. Mixing - Prepared by dissolving the - Dissolution of solute in solute in most of the solvent, solvent mixing until dissolved, then adding sufficient solvent to Methods to fasten dissolution: bring the solution up to Vigorous agitation proper volume. Application of heat (Except Ca Salts) - Ex: Ca (OH)2 Topical Particle size reduction Solution Use of solubilizers and chelating - More soluble in cold agents water 3. Storage and aging 2. Solution by Chemical Rxn - For solutions with high - Prepared by reacting 2 or amounts of volatile oils more solutes with each other - Ex: aromatic waters, spirits, in a suitable solvent mouthwashes) - Ex: Aluminum Subacetate - Enhances odor and flavor’ Topical Solution. - Al203 + acetic acid 4. Filtration - Process of separating liquids 3. Finely Divided Solids from solids with the use of a - Colloidal clay filter medium - Bentonite - Mg(OH)2 TYPES: - Al(OH)3 Parallel filtration - 1 filter media 4. HMW Alcohols Series filtration - Glyceryl monostearate - 2 or more filter media - Stearyl alcohol - Cetyl alcohol 5. Filling - Cholesterol - Methods: 5. Synthetic surfactants Gravimetric A. Anionic: - Weight; + viscosity - Soaps Volumetric - Sulfonates - volume - Increase pH - Constant-level detergent - Weight of container B. Cationic IV. MANUFACTURING OF EMULSION - Quat ammonium compounds A. Emulsifying agents - Decrease pH - preservatives CLASSIFICATION C. Amphoteric 1. Carbohydrate materials - Betaine - Tragacanth - Mild detergent - Acacia - Agar D. Nonionic - Pectin - Unaffected by pH and - Chondrus salts - Xanthan Span - Carrageenan - Sorbitan esters - (Ex: sorbitan 2. Protein Substances monooleate) - Gelatin - Lipophilic - Egg yolk Tween ® - Casein - Polysorbates - (ex: PFG-20-Sorbitan - Complete fusion of droplets nanopalmitate) - hydrophilic 6. Breaking/Cracking - Complete separation of oil EMULSIFYING AGENTS and water - irreversible ACTIVITY HLB Value Antifoaming 1-3 w/o emulsifier 3-6 Wetting agent 7-9 O/w emulsifier 8-18 Detergent 13-16 IV. MANUFACTURING OF SUSPENSIONS Solubilizer 15-20 Sodium LaurylSulfate 40 A. Formulation B. INSTABILITY OF EMULSIONS 1. Suspending Agents Viscosity 1. Creaming ○ Increasing agents - The upward movement of used to reduce dispersed globules sedimentation rate of - o/w particles in a vehicle. Ex: 2. Sedimentation ○ Tragacanth - The downward movement of ○ Acacia dispersed globules. ○ Agar - w/o ○ Cellulose ○ Veegum ® 3. Phase Inversion ○ Bentonite magma - An o/w changes to a w/o ○ Carrageenan emulsion or vice versa. ○ Gelatin ○ Kaolin 4. Flocculation/Aggregation - The dispersed globules come 2. Wetting Agents together but do not fuse - Displace air from crevices of hydrophilic solids to allow 5. Coalescence penetration of water. Ex: Surfactants C. STERILIZATION METHODS Glycerin PPG 1. Moist Heat PEG - Autoclave (121°, 15 psi, Syrup 15-20 minutes) - HLOA: protein coagulation 3. Flocculating Agents - Bacterial indication: - Prevent cracking Bacillus stearothermophilus - Reduce the electrical (zeta potential) barrier between the 2. Dry Heat particles of the suspensoid - Oven (160°-170°, 2-4 hours) and forming a bridge so as to - MOA: oxidation link them together - BI: Bacillus subtilis Ex: Electrolytes - NaCl, KCl Surfactants, polymers 3. Filtration - Membrane Fillers V. MANUFACTURING OF STERILE - QC test: Bubble Point test DOSAGE FORM - MOA: Separation - BI: Brevundimonas diminuta A. Sterile Production Area - 0.23 um Clean Rooms - Room in which the 4. Gas concentration of airborne - For finished products particles is controlled - Ethylene oxide, - Filtered air supplied formaldehyde, - (+) pressure B-propiolactone - HEPA filter - MOA: Alkylation - High efficiency - BI: Bacillus subtilis particulate air - Removes 99.97% of 5. Ionizing Radiation particles (>0.3 um) - Gamma or cathode rays from air - MOA: DNA mutation - Airlocks for entry - BI: Bacillus pumilus - Spaces with interlocked doors QC Test: DioctylPhthalate Test B. STERILE MANUFACTURING OPERATIONS CLASSIFICATION OF CLEAN ROOMS - Preservation, and filtration US ISO WHO MAX NO. Dry solids: CUSTOMARY AMP OF - Spray-drying or PARTICLE freeze-drying S PER FT3 (lyophilization) (>0.5 um) 3. Filtration Class 100 ISO Grade 100 - 5 A critical Methods areas Clarification - 2-3 um particles Class 1000 1SO Grade 1,000 Cold filtration 6 B - 0.2-0.3 um particles Class 10,000 ISO Grade 10.000 7 C 4. Filling Methods Class 100,000 ISO Grade 100,000 Gravity Filling 8 D - hand-operated Pressure Filling Depyrogenation - Semi-automatic - Oven settings Vacuum Filling ○ 180° for 4 hours - Fully automated ○ 250° for 45 minutes ○ 650° for 1 minute 5. Sealing - Ampoule sealing STEPS IN PREPARING STERILE Tip-seal (Bad-seal) DOSAGE FORMS - Made by melting the tip of the neck of an 1. Cleaning ampoule to form a - Manual cleaning and bead. sterilization of equipment Pull-seal - Sanitation of clean rooms - Made by heating the - Sterilization of components neck of a rotating for aseptic processing ampoule below the tip and pulling the 2. Product Preparation softened glass away. Critical process - Class 100 Solutions: - Dissolutions - Ionicity adjustments IV. PACKAGING AND STORAGE OF 1. According to Protection Ability DRUG PRODUCTS a. Well-closed A. Packaging - Protects content from - An economic way of extraneous solids. protecting, preparing, identifying, & containing the b. Tight drug product. - Protects contents from - Containers + closure extraneous solids, liquids, and vapors TYPES OF PACKAGING - Protects from deliquescence A. Primary efflorescence, evaporation - In direct contact with the product. c. Hermetic - Impervious to air or any other B. Secondary gas - Outer packaging (not always present) d. Light-Resistant - Protects from photochemical degradation PRIMARY PACKAGING Amber bottle Bottles Caps e. Child-Resistant Liners - Difficult for children under 5 Filler/coil years of age to open - Prevents salting of tablets Press down and turn - Ex: Cotton, rayon, polyester Squeeze and turn Desiccant protectant Alight the arrows - Prevents moisture Latch top Ex: Silicagel f. Tamper-Resistant SECONDARY PACKAGING - Use an indicator which if Carbon box preached or missing can Sticker label provide evidence that Inserts tampering has occurred. Corrugated boxes Shrink seal wrap - Considered as tertiary Breakable caps Tape seal B. Classification of containers Bottle seal Aerosol - (Only true ADVANTAGES DISADVANTAGES tamper-resistant packaging) Rigid and High cost 2. According to Quantity Held transparent a. Single unit impermeable fragile - Contains a single dose only and packages to Chemically Relatively heavy non-resealable containers resistant - No antimicrobial agent; Can be easily Prone to leaching water; WFI or SWFI; USP sterilized limit: 1000 mL - Ampoules, prefilled syringes TYPES OF GLASS ADVANTAGES DISADVANTAGES I - Highly Resistant Borosilicate (Pyrex, Borosil) Low cost permeable Boron - decrease coefficient of expansion Not breakable Low heat resistance II - Treated Soda Lime - Glass Light weight Hot as clear as glass Chemically inert Poor physical III- Soda Lime Glass; Dry powder; stability packaging b. Multiple unit IV/ HP - General Soda Lime Glass or - Contains multiple doses and General-Purpose Soda Lime Glass packaged in resealable containers B. Plastic - w/ antimicrobial agent; water; - Organic polymers of HMW BWFI; USP Limit: 30 mL - Vials TYPES OF PLASTICS 3. According to Material Used 1. Thermoplastics - Soft when heated and hard A. Glass when cooled; flexible and - Most widely used, made up squeezable of inorganic compounds 2. Thermoset (major component: SiO2) - Permanently hard; rigid TYPES OF POLYMERS Freezer -20 to -10°C Cool 8 to 15C No. Plastic Use Room temperature Temperature, 1 Polyethylene For beverages prevailing in the Terephthalate area 2 High-density Hard thermoset Controlled room 20 to 25°C Polyethylene For solid dosage temperature forms Warm 30 TO 40°C 3 Polyvinyl For blister packs Chloride Excessive Heat >40°C 4 Low-density Thermoplastic for Polyethylene soft squeeze bottles and medicine droppers 5 Polypropylene For autoclave containers C. Metal - Used in aerosols and collapsible tubes D. Foils, Films and laminates - Used in blister packs and strip packs E. Rubber - Used in vial stoppers and syringe plugs F. Paper - Used for divided powders C. STORAGE CONDITIONS Cold NMT 2 to 8°C Refrigerator 2 TO 8°C