Oxy-Fuel Torch Guide PDF
Document Details
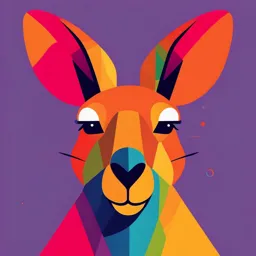
Uploaded by VirtuousSense6339
Conestoga College
2005
Howard B. Cary and Scott C. Helzer
Tags
Summary
This document provides a guide on using oxy-fuel torches, including safety procedures, parts, and different types. It covers various aspects of the torch and gas types. The document also has safety notes included and is from the 6th edition of *Modern Welding Technology*.
Full Transcript
REGULATORS – ANOTHER DISTINCTION. “There are two types of regulators, the single-stage regulator and the two-stage regulator. The single-stage regulator reduces the cylinder pressure of the gas to a working pressure in one step. Single-stage regulators must be readjusted from time to time to maintai...
REGULATORS – ANOTHER DISTINCTION. “There are two types of regulators, the single-stage regulator and the two-stage regulator. The single-stage regulator reduces the cylinder pressure of the gas to a working pressure in one step. Single-stage regulators must be readjusted from time to time to maintain the required working pressure. The gas pressure in the cylinder decreases gradually as gas is withdrawn …. The two-stage regulator makes the reduction of pressure in two steps. The first step reduces the cylinder pressure to an intermediate pressure. The second step reduces the intermediate pressure to the desired working pressure. A two-stage regulator is simply two single-stage regulators in the same case. The two-stage regulator provides more accurate regulation and eliminates the need to readjust the regulator as the pressure in the supply tank is reduced.” *Howard B. Cary and Scott C. Helzer, (2005), Modern Welding Technology, Sixth Edition, United States of America: Pearson Prentice Hall, Page 168. TWO SAFETY CONSIDERATIONS CONCERNING START-UP. The regulator is to be ‘pinky loose’ It is recommended to stand to one side before turning the cylinder’s valve ‘on’. before turning the cylinder’s valve ‘on’. SHOWN ITEM(S), INCLUDING ITS/THEIR POSITION/CONDITION/SHAPE AND/OR ANY SETTING(S) IS/ARE NOT TO BE INTERPRETED AS RECOMMENDED, AVAILABLE OR ACTUAL. HOSES. “The gas hoses may be separate or moulded together. The green (or blue) hose is for oxygen, and the red (or orange) is for acetylene. The hose fittings are different to prevent hooking them up incorrectly. Oxygen hose has fittings with right-hand threads, and acetylene hose has fittings with left-hand threads.”* *Thomas Bieber Davis & Carl A. Nelson Sr., (2004), MECHANICAL TRADES POCKET MANUAL ALL NEW 4TH EDITION, United States of America: Wiley Publishing, Inc., Page 350. SHOWN ITEM(S), INCLUDING ITS/THEIR POSITION/CONDITION/SHAPE AND/OR ANY SETTING(S) IS/ARE NOT TO BE INTERPRETED AS RECOMMENDED, AVAILABLE OR ACTUAL. (REVERSE FLOW) CHECK VALVES. ‘(Reverse flow) check valves’ have been associated with stopping the flow of gas/gases moving in a ‘reverse direction’. With some torches, the reverse flow check valve is already ‘built in’. SHOWN ITEM(S), INCLUDING ITS/THEIR POSITION/CONDITION/SHAPE AND/OR ANY SETTING(S) IS/ARE NOT TO BE INTERPRETED AS RECOMMENDED, AVAILABLE OR ACTUAL. FLASHBACK ARRESTORS. ‘Flashback arrestors’ have been associated with stopping the flow of gas/gases moving in a ‘reverse direction’, and the prevention of flame(s) movement. SHOWN ITEM(S), INCLUDING ITS/THEIR POSITION/CONDITION/SHAPE AND/OR ANY SETTING(S) IS/ARE NOT TO BE INTERPRETED AS RECOMMENDED, AVAILABLE OR ACTUAL. NOTE THE NOTCHING - 1/2. The notching is present only on the shown fuel fitting. SHOWN ITEM(S), INCLUDING ITS/THEIR POSITION/CONDITION/SHAPE AND/OR ANY SETTING(S) IS/ARE NOT TO BE INTERPRETED AS RECOMMENDED, AVAILABLE OR ACTUAL. NOTE THE NOTCHING – 2/2. Although this is a different torch, the notching is again, only on the fuel fitting. SHOWN ITEM(S), INCLUDING ITS/THEIR POSITION/CONDITION/SHAPE AND/OR ANY SETTING(S) IS/ARE NOT TO BE INTERPRETED AS RECOMMENDED, AVAILABLE OR ACTUAL. SOME ‘COMMONLY USED TERMS’ FOR TORCH COMPONENTS. G2 G1 D B I H F E C A J A – Hose for fuel gas. B - Hose for oxygen. C – Valve for fuel gas. D – Valve for oxygen. E – Torch body. F – Nut. G1 – Oxygen lever. G2 – Valve for oxygen on cutting attachment. H – Tubes – here, there are 3. I and J – Cutting tip nut and cutting tip. SHOWN ITEM(S), INCLUDING ITS/THEIR POSITION/CONDITION/SHAPE AND/OR ANY SETTING(S) IS/ARE NOT TO BE INTERPRETED AS RECOMMENDED, AVAILABLE OR ACTUAL. TORCHES – TWO DIFFERENT TYPES BY DESIGN. ‘Cutting Torch’. ‘Combination Torch’ with ‘Cutting Attachment’. SHOWN ITEM(S), INCLUDING ITS/THEIR POSITION/CONDITION/SHAPE AND/OR ANY SETTING(S) IS/ARE NOT TO BE INTERPRETED AS RECOMMENDED, AVAILABLE OR ACTUAL. TORCHES – TWO DIFFERENT TYPES BY NUMBER OF TUBES. ‘Three Tube’. ‘Two Tube’. SHOWN ITEM(S), INCLUDING ITS/THEIR POSITION/CONDITION/SHAPE AND/OR ANY SETTING(S) IS/ARE NOT TO BE INTERPRETED AS RECOMMENDED, AVAILABLE OR ACTUAL. TORCH. As shown, this torch may be used for welding, brazing and braze welding. SHOWN ITEM(S), INCLUDING ITS/THEIR POSITION/CONDITION/SHAPE AND/OR ANY SETTING(S) IS/ARE NOT TO BE INTERPRETED AS RECOMMENDED, AVAILABLE OR ACTUAL. CUTTING ATTACHMENT. Note the O-ring that is visible here. Required O-rings should be inspected every time components are to be used. SHOWN ITEM(S), INCLUDING ITS/THEIR POSITION/CONDITION/SHAPE AND/OR ANY SETTING(S) IS/ARE NOT TO BE INTERPRETED AS RECOMMENDED, AVAILABLE OR ACTUAL. OXYGEN LEVER. When this lever is depressed, the ‘cutting oxygen’ should be ‘engaged’ and reach the torch tip. SHOWN ITEM(S), INCLUDING ITS/THEIR POSITION/CONDITION/SHAPE AND/OR ANY SETTING(S) IS/ARE NOT TO BE INTERPRETED AS RECOMMENDED, AVAILABLE OR ACTUAL. OXYGEN LEVER – (DIFFERENT TORCH). SHOWN ITEM(S), INCLUDING ITS/THEIR POSITION/CONDITION/SHAPE AND/OR ANY SETTING(S) IS/ARE NOT TO BE INTERPRETED AS RECOMMENDED, AVAILABLE OR ACTUAL. CUTTING TIPS – TWO VIEWS. Note the 6 ‘pre-heat’ holes positioned around the ‘cutting oxygen’ (center) hole. SHOWN ITEM(S), INCLUDING ITS/THEIR POSITION/CONDITION/SHAPE AND/OR ANY SETTING(S) IS/ARE NOT TO BE INTERPRETED AS RECOMMENDED, AVAILABLE OR ACTUAL. ‘BUGGY’. These machines are common in fab/welding shops. Often, the torch is positioned on the machine to produce a bevel. SHOWN ITEM(S), INCLUDING ITS/THEIR POSITION/CONDITION/SHAPE AND/OR ANY SETTING(S) IS/ARE NOT TO BE INTERPRETED AS RECOMMENDED, AVAILABLE OR ACTUAL. LEAK DETECTION FLUID. Verify the contents, spray, look for bubbles. Never use soap and water. Always use approved leak detection fluid. SHOWN ITEM(S), INCLUDING ITS/THEIR POSITION/CONDITION/SHAPE AND/OR ANY SETTING(S) IS/ARE NOT TO BE INTERPRETED AS RECOMMENDED, AVAILABLE OR ACTUAL. TIP CLEANER(S). Tip cleaners are sized to specific diameters. It is very important to utilize the correct diameter of tip cleaner on the tip that is being cleaned. SHOWN ITEM(S), INCLUDING ITS/THEIR POSITION/CONDITION/SHAPE AND/OR ANY SETTING(S) IS/ARE NOT TO BE INTERPRETED AS RECOMMENDED, AVAILABLE OR ACTUAL. PRESSURES – 1/2. Often, it is material thickness that determines tip ‘size’ - as dictated by the owner’s manual. Often, tip ‘size’ determines pressures – as dictated by the owner’s manual. SHOWN ITEM(S), INCLUDING ITS/THEIR POSITION/CONDITION/SHAPE AND/OR ANY SETTING(S) IS/ARE NOT Tip ‘sizes’ and pressures, while both based primarily on TO BE INTERPRETED AS RECOMMENDED, AVAILABLE OR ACTUAL. material thickness, are different between manufacturers. As there are no universal tip ‘sizes’ or pressures for material thicknesses, you must consult the owner’s manual for the actual torch in use. PRESSURES – 2/2. The pressures that are shown here are likely for cutting – with a specific tip manufacturer and a specific ‘size’. Note that the recommended acetylene pressure shown is “7-8”, while the pressure SHOWN ITEM(S), INCLUDING ITS/THEIR POSITION/CONDITION/SHAPE recommended for oxygen is AND/OR ANY SETTING(S) IS/ARE NOT TO BE INTERPRETED AS “30-35”. RECOMMENDED, AVAILABLE OR ACTUAL. In contrast, recommended pressures for welding and brazing could be termed ‘balanced’ or ‘even’. “6 and 6” or “8 and 8” are often mentioned. THREE COMMON OXY-ACETYLENE FLAME SETTINGS. Three common oxy-acetylene flame settings are known as: ‘carbonizing’, ‘neutral’ and ‘oxidizing’. Shown below is a ‘neutral flame’. Note the absence of a ‘feather’. TORCH TIP CONE ENVELOPE NTS The term ‘neutral’ has been applied to both joining and cutting work. SHOWN ITEM(S), INCLUDING ITS/THEIR POSITION/CONDITION/SHAPE AND/OR ANY SETTING(S) IS/ARE NOT TO BE INTERPRETED AS RECOMMENDED, AVAILABLE OR ACTUAL. FLAMES AND TEMPERATURES. “A neutral oxyacetylene welding flame will produce a temperature of approximately 5600 F (3093 C). A neutral oxypropane flame reaches 5300 F (2927 C). An oxidizing flame will produce a slightly higher temperature.”* *Andrew D. Althouse, Carl H. Turnquist, William A. Bowditch and Kevin E. Bowditch, (1984), modern WELDING, South Holland, Illinois: THE GOODHEART-WILLCOX COMPANY, INC., Page 117. Acetylene mixed in air can ignite when the acetylene amount is from 2.5% to 80% ACETYLENE’S CHEMICAL COMPOSITION; C 2 H2 ‘EDGE CUTS’ VERSUS ‘PIERCE CUTS’. When cutting, cuts may be categorized as ‘edge cuts’ or ‘pierce cuts’. Generally, edge cuts are considered to be ‘easier’ and ‘safer’. NTS NTS Edge cut. Pierce cut. SHOWN ITEM(S), INCLUDING ITS/THEIR POSITION/CONDITION/SHAPE AND/OR ANY SETTING(S) IS/ARE NOT TO BE INTERPRETED AS RECOMMENDED, AVAILABLE OR ACTUAL. CUTTING PIPE. When cutting pipe or tube, there are a number of concerns. Be aware that some pipes may It is common for hot material to be contain coatings, that in some ejected from the ends of the pipe – cases, have been deemed regardless of where the ‘cut’ is being harmful to health. made. SHOWN ITEM(S), INCLUDING ITS/THEIR POSITION/CONDITION/SHAPE AND/OR ANY SETTING(S) IS/ARE NOT TO BE INTERPRETED AS RECOMMENDED, AVAILABLE OR ACTUAL. CUT ‘QUALITY’. The ‘quality’ of any oxy-fuel cut is affected by a number of factors including: Tip selection and gas pressures, Torch angle, Travel speed. The shown cut(s) were likely done with an oxy-fuel process. SHOWN ITEM(S), INCLUDING ITS/THEIR POSITION/CONDITION/SHAPE AND/OR ANY SETTING(S) IS/ARE NOT TO BE INTERPRETED AS RECOMMENDED, AVAILABLE OR ACTUAL. THE ‘KERF’ OF A CUT. The ‘kerf’ shown here as a Two layout lines drawn to dimensional consideration. improve part size accuracy. The kerf of a cut, could be considered ‘lost material’. Most ‘cutting’ processes, including oxy-fuel cutting, will create a kerf. It is common, particularly on thicker material, to lay out both sides of a cut to account for the kerf. This helps to improve dimensional accuracy of both parts. SHOWN ITEM(S), INCLUDING ITS/THEIR POSITION/CONDITION/SHAPE AND/OR ANY SETTING(S) IS/ARE NOT TO BE INTERPRETED AS RECOMMENDED, AVAILABLE OR ACTUAL. WELDING AND STRESS RELIEVING. According to a source: “STRESS is a force which causes or attempts to cause a movement or change in the shape of parts being welded (strain).”* “Stresses which remain in parts after welding is completed are known as RESIDUAL STRESSES. …. These residual stresses may cause the metal to distort at any time if not removed. To reduce the residual stresses caused by welding, parts should be given a stress relieving heat treatment.”** *Andrew D. Althouse, Carl H. Turnquist, William A. Bowditch and Kevin E. Bowditch, (1984), Modern WELDING, South Holland, Illinois: THE GOODHEART-WILLCOX COMPANY, INC., Page 692. **Andrew D. Althouse, Carl H. Turnquist, William A. Bowditch and Kevin E. Bowditch, (1984), Modern WELDING, South Holland, Illinois: THE GOODHEART-WILLCOX COMPANY, INC., Page 694. STRESS RELIEF. “Some of the more popular techniques used to control residual stresses are peening, preheating, and postheating.” * “The equipment for preheat and postheat may range from the ordinary oxy-acetylene torch to large, sophisticated heat-treating furnaces.”** (This slide is also in “L3 Band Saws, Pneumatic Tools…”). *JAMES A. PENDER, (1986), WELDING, THIRD EDITION, TORONTO MONTREAL NEW YORK ET ALL: MCGRAW-HILL RYERSON LIMITED, PAGE 273. **JAMES A. PENDER, (1986), WELDING, THIRD EDITION, TORONTO MONTREAL NEW YORK ET ALL: MCGRAW-HILL RYERSON LIMITED, PAGE 273. A common directive for pre-heat HEATING OPERATIONS. was; “Just chase the water out of it….” This was/is not always a good idea Heating has been employed in conjunction or accurate description… with a number of welding and fabrication practices and concerns including weld quality, and may be specified in a weld procedure. Heating has also been associated with: - stress relieving, - correction of distortion, - bending. Regarding heating and bending, heat has been employed to bend material by itself and/or to NTS increase the ease of bending. SHOWN ITEM(S), INCLUDING ITS/THEIR POSITION/CONDITION/SHAPE AND/OR ANY SETTING(S) IS/ARE NOT TO BE INTERPRETED AS RECOMMENDED, AVAILABLE OR ACTUAL. HEATING TIP. Also known as a ‘Rosebud’. SHOWN ITEM(S), INCLUDING ITS/THEIR POSITION/CONDITION/SHAPE AND/OR ANY SETTING(S) IS/ARE NOT TO BE INTERPRETED AS RECOMMENDED, AVAILABLE OR ACTUAL. SOME CONSIDERATIONS WHILE USING AN OXY-FUEL TORCH IN B001/B010 – 1/3. BEFORE: Inspect all clothing and PPE before use. Inspect all connections and components before use. Set up the torch for maximum comfort and efficiency. Be sure the torch valves are off before pressurizing the system. Use leak test, be sure to read the label on the bottle. If you smell acetylene, shut off the valves immediately.* Know your pressures and be aware of any changes shown on the regulator.* * BEFORE AND DURING. SHOWN ITEM(S), INCLUDING ITS/THEIR POSITION/CONDITION/SHAPE AND/OR ANY SETTING(S) IS/ARE NOT TO BE INTERPRETED AS RECOMMENDED, AVAILABLE OR ACTUAL. SOME CONSIDERATIONS WHILE USING AN OXY-FUEL TORCH IN B001/B010 – 2/3. DURING: Light only the fuel gas, and only with a school supplied striker. Keep the striker close to the tip when lighting but do NOT impede gas flow. Once lit, add flow of fuel gas beyond the smoke range, then add oxygen. Be aware of where you are pointing the torch. Be aware of the hoses when welding and cutting– do not allow steel and/or dross to touch the hoses. Clean tip as REQD (required) – do not use a dirty tip. Keep the tip and cone clear of the work – do not allow the tip to overheat. If you hear a popping or screeching sound, shut off all valves immediately and seek faculty assistance. If the torch becomes hot, stop work, shut down and seek faculty assistance. Do not stare at red hot steel. SHOWN ITEM(S), INCLUDING ITS/THEIR POSITION/CONDITION/SHAPE AND/OR ANY Use pliers to handle hot steel. Quench hot steel and/or label it hot. SETTING(S) IS/ARE NOT TO BE INTERPRETED AS RECOMMENDED, AVAILABLE OR ACTUAL. SOME CONSIDERATIONS WHILE USING AN OXY-FUEL TORCH IN B001/B010 – 3/3. AFTER: If leaving, when break is called, and at the end of class, follow the shut-down procedure. Orientate the torch so that it can be hung up properly with the cutting attachment on. Be sure the hoses are neatly coiled. Note that the oxygen valve on the cutting attachment is roughly centered with the other two torch valves. - END OF PRESENTATION SHOWN ITEM(S), INCLUDING ITS/THEIR POSITION/CONDITION/SHAPE AND/OR ANY SETTING(S) - “L1 OXY-FUEL & OTHER MATL” - IS/ARE NOT TO BE INTERPRETED AS RECOMMENDED, AVAILABLE OR ACTUAL. Rev – PT for ‘22