Oxy-Fuel & Other Materials PDF
Document Details
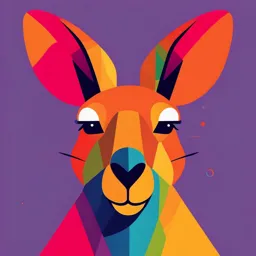
Uploaded by VirtuousSense6339
Conestoga College
Tags
Summary
This document provides information about oxy-fuel and other materials, including different joining processes like soldering, brazing, braze welding, and welding, and their similarities. The document details the materials used and processes involved. It also includes various images and diagrams.
Full Transcript
L1 - OXY-FUEL AND OTHER MATERIAL. Studied Processes: Soldering, Brazing, Braze-welding, Welding, ‘Cutting’, and Heating. SHOWN ITEM(S), INCLUDING ITS/THEIR POSITION/CONDITION/SHAPE AND/OR ANY SETTING(S) IS/ARE NOT TO BE INTERPRETED AS RECOMMENDED, AVAILABLE OR ACTUAL. SOME PPE....
L1 - OXY-FUEL AND OTHER MATERIAL. Studied Processes: Soldering, Brazing, Braze-welding, Welding, ‘Cutting’, and Heating. SHOWN ITEM(S), INCLUDING ITS/THEIR POSITION/CONDITION/SHAPE AND/OR ANY SETTING(S) IS/ARE NOT TO BE INTERPRETED AS RECOMMENDED, AVAILABLE OR ACTUAL. SOME PPE. Shade 5. Always wear your safety glasses. Gloves must be oil free. All skin should be covered. SHOWN ITEM(S), INCLUDING ITS/THEIR POSITION/CONDITION/SHAPE AND/OR ANY SETTING(S) IS/ARE NOT TO BE INTERPRETED AS RECOMMENDED, AVAILABLE OR ACTUAL. ONE MAIN DIFFERENCE BETWEEN FOUR JOINING PROCESSES. Soldering. Brazing. Braze welding. Welding. Temperature. Fit-up. Filler metal is optional. “Filler metals suitable for soldering are those that are completely molten below 840 F.”* “Filler metals suitable for brazing are those that begin to melt, or change to a liquid state, above 840 F.”** “Braze welding (BW) is a joining process … in which the filler metal is not distributed into the joint by capillary action.”*** “welding: The coalescence or joining together of metals, with or without a filler metal … ”**** *B. J. Moniz, (2015), Welding Skills, Fifth Edition Orland Park, Illinois: AMERICAN TECHNICAL PUBLISHERS, Page 286. **B. J. Moniz, (2015), Welding Skills, Fifth Edition Orland Park, Illinois: AMERICAN TECHNICAL PUBLISHERS, Page 277. ***B. J. Moniz, (2015), Welding Skills, Fifth Edition Orland Park, Illinois: AMERICAN TECHNICAL PUBLISHERS, Page 284. ****B. J. Moniz, (2015), Welding Skills, Fifth Edition Orland Park, Illinois: AMERICAN TECHNICAL PUBLISHERS, Page 769. ‘SOLDERING’ AND ‘BRAZING’ – SIMILARITIES. “Soldering involves the use of a non-ferrous metal whose melting point is below that of the base metal …”* “Brazing is a metal joining process which uses a non-ferrous filler metal with a melting point below that of the base metals … The filler metal wets the base metal when molten in a manner similar to that of a solder and its base metal …. The molten metal flows between the close-fitting metals because of capillary forces.”** *ERIK OBERG, FRANKLIN D. JONES and HOLBROOK L. HORTON, (1981), MACHINERY’S HANDBOOK, TWENTY-FIRST EDITION, Fourth Printing, New York, N.Y.: INDUSTRIAL PRESS INC., Page 2195. **ERIK OBERG, FRANKLIN D. JONES and HOLBROOK L. HORTON, (1981), MACHINERY’S HANDBOOK, TWENTY-FIRST EDITION, Fourth Printing, New York, N.Y.: INDUSTRIAL PRESS INC., Page 2198. ‘CAPILLARY ACTION’. “Capillary action is a physical process in which a liquid is drawn into the space between two tightly fitted surfaces.”*** ***JOHN R. WALKER, (2004), MODERN METALWORKING, Ninth Edition, Tinley Park, Illinois: The Goodheart-Willcox Company, Inc., Page 206. SOLDERING IMAGES - 1/2. SHOWN ITEM(S), INCLUDING ITS/THEIR POSITION/CONDITION/SHAPE AND/OR ANY SETTING(S) IS/ARE NOT TO BE INTERPRETED AS RECOMMENDED, AVAILABLE OR ACTUAL. SOLDERING IMAGES – 2/2. SHOWN ITEM(S), INCLUDING ITS/THEIR POSITION/CONDITION/SHAPE AND/OR ANY SETTING(S) IS/ARE NOT TO BE INTERPRETED AS RECOMMENDED, AVAILABLE OR ACTUAL. ‘FLUXES’. “Fluxes for Soldering. - … Fluxes clean the surfaces of the metal in the joint area by removing the oxide coating present, keep the area clean by preventing formation of oxide films, and lower the surface tension of the solder thereby increasing its wetting properties.”* “Fluxes for Brazing. - … Fluxes are used mainly to prevent the formation of oxides and to remove any oxides on the base and filler metals. They also promote free flow of the filler metal during the course of the brazing operation. They are made available in the following forms: powders, pastes or solutions, gases or vapours, and as coatings on the brazing rods. ”** REGARDING FLUX AND BRAZE WELDING. “The flux is also used for the same purpose as in soldering and silver brazing. It chemically cleans the base metal, removes any impurities from the weld, and allows the braze metal to flow more easily onto the base metal.”*** *ERIK OBERG, FRANKLIN D. JONES and HOLBROOK L. HORTON, (1981), MACHINERY’S HANDBOOK, TWENTY-FIRST EDITION, Fourth Printing, New York, N.Y.: INDUSTRIAL PRESS INC., Page 2195. **ERIK OBERG, FRANKLIN D. JONES and HOLBROOK L. HORTON, (1981), MACHINERY’S HANDBOOK, TWENTY-FIRST EDITION, Fourth Printing, New York, N.Y.: INDUSTRIAL PRESS INC., Page 2198. ***JAMES A. PENDER, (1986), WELDING, THIRD EDITION, TORONTO MONTREAL NEW YORK ET ALL: MCGRAW-HILL RYERSON LIMITED, Page 85. FILLER METALS – SOLDERING. “An ALLOY is a mixture of one metal with one or more metals and/or nonmetals.”* “There are different solders for soldering tin, copper, brass, aluminum, bronze, sheet iron, sheet steel, and even glass to glass.”** *Andrew D. Althouse, Carl H. Turnquist, William A. Bowditch and Kevin E. Bowditch, (1984), modern WELDING, South Holland, Illinois: THE GOODHEART-WILLCOX COMPANY, INC., Page 178. **Andrew D. Althouse, Carl H. Turnquist, William A. Bowditch and SHOWN ITEM(S), INCLUDING ITS/THEIR POSITION/CONDITION/SHAPE Kevin E. Bowditch, (1984), modern WELDING, South Holland, Illinois: AND/OR ANY SETTING(S) IS/ARE NOT TO BE INTERPRETED AS THE GOODHEART-WILLCOX COMPANY, INC., Page 177. RECOMMENDED, AVAILABLE OR ACTUAL. FILLER METALS – BRAZING AND BRAZE WELDING. “Brazing filler metals are available in wire, rod, strip, and powder forms. …. The AWS classification consists of the letter B, which identifies it as brazing filler metal, followed by the chemical symbols of the metallic elements included in the filler metal. ”* “Braze welding filler metals are usually brasses, with an approximate composition of 60% copper and 40% zinc … ”** Brass is Copper and Zinc. Bronze is Copper and Tin. *B. J. Moniz, (2015), Welding Skills, Fifth Edition, Orland Park, Illinois: AMERICAN TECHNICAL PUBLISHERS, Page 281. SHOWN ITEM(S), INCLUDING ITS/THEIR POSITION/CONDITION/SHAPE **B. J. Moniz, (2015), Welding Skills, Fifth Edition, Orland Park, Illinois: AND/OR ANY SETTING(S) IS/ARE NOT TO BE INTERPRETED AS AMERICAN TECHNICAL PUBLISHERS, Page 286. RECOMMENDED, AVAILABLE OR ACTUAL. A FILLER METAL USED FOR OXY-FUEL WELDING. DESIGNATION; R – 45. It is best not to ‘burn’ this important information off of the filler rod. SHOWN ITEM(S), INCLUDING ITS/THEIR POSITION/CONDITION/SHAPE AND/OR ANY SETTING(S) IS/ARE NOT TO BE INTERPRETED AS RECOMMENDED, AVAILABLE OR ACTUAL. CYLINDER STORAGE. There are many rules to follow when storing compressed gas cylinders. Compressed gas cylinders must be properly secured when stored. The valve protection cap is to be properly in place on a stored compressed gas cylinder. SHOWN ITEM(S), INCLUDING ITS/THEIR POSITION/CONDITION/SHAPE AND/OR ANY SETTING(S) IS/ARE NOT TO BE INTERPRETED AS RECOMMENDED, AVAILABLE OR ACTUAL. AN OXY-FUEL ‘PORTABLE UNIT’. Note the following: No pressure indicated in the system, Hoses wrapped up, Cylinders vertical and chained. SHOWN ITEM(S), INCLUDING ITS/THEIR POSITION/CONDITION/SHAPE AND/OR ANY SETTING(S) IS/ARE NOT TO BE INTERPRETED AS RECOMMENDED, AVAILABLE OR ACTUAL. A COMPRESSED GAS CYLINDER. Note the following: Threading for the valve protection cap, Labels on the cylinder’s shoulders, Label hatching. SHOWN ITEM(S), INCLUDING ITS/THEIR POSITION/CONDITION/SHAPE AND/OR ANY SETTING(S) IS/ARE NOT TO BE INTERPRETED AS RECOMMENDED, AVAILABLE OR ACTUAL. COMPARING CYLINDER CONSTRUCTION. ‘TYPICAL’ COMPRESSED ‘TYPICAL’ ACETYLENE GAS OXYGEN CYLINDERS: CYLINDERS: ‘Seamless’, ‘Not seamless’, Inside is honeycombed, Inside is not honeycombed, A pressure of 250 psi A pressure of 2200 psi is common, at 70 DEG F is common, Max pressure to be used is 15psi Are associated with safety Are associated with safety devices that are triggered devices that are triggered by pressure. by heat. (100⁰C or 212⁰F) SHOWN ITEM(S), INCLUDING ITS/THEIR POSITION/CONDITION/SHAPE AND/OR ANY SETTING(S) IS/ARE NOT TO BE INTERPRETED AS RECOMMENDED, AVAILABLE OR ACTUAL. OXYGEN CYLINDERS Typically, 5 ft tall When full weighs approx. 150 lbs Standard and liquid oxygen cylinders are the same height A typical liquid oxygen cylinder is twice the diameter as a standard oxygen cylinder and holds 12 times as much oxygen. SHOWN ITEM(S), INCLUDING ITS/THEIR POSITION/CONDITION/SHAPE AND/OR ANY SETTING(S) IS/ARE NOT TO BE INTERPRETED AS RECOMMENDED, AVAILABLE OR ACTUAL. WITHDRAWAL RATES FOR ‘STANDARD’ ACETYLENE CYLINDERS. “Acetone absorbs acetylene in the same manner as water absorbs carbon dioxide in a carbonated drink …. The withdrawal rate of gas from a cylinder should not exceed one-seventh of the total cylinder capacity per hour.”* “A multiple cylinder manifold system allows the necessary volume of acetylene to be supplied to the work area. Acetylene can be used at a maximum rate of one-seventh the total volume of the cylinder per hour … ”** At this time, the 1/7 fraction appears to be the maximum allowable. This may change, or may have already changed. *Larry Jeffus, (2017), Welding Principles and Applications, Eighth Edition, Boston, MA: DELMAR, CENGAGE Learning, Page 768. **B. J. Moniz, (2015), Welding Skills, Fifth Edition, Orland Park, Illinois: AMERICAN TECHNICAL PUBLISHERS, Page 52. WITHDRAWAL RATES FOR ‘STANDARD’ ACETYLENE CYLINDERS - CALCULATIONS. If an acetylene cylinder has a known capacity of 130 cubic feet of acetylene, and the owner’s manual for an oxy-fuel torch specifies that a certain ‘tip model and size’ - at a certain pressure - will consume approximately 8 cubic feet per hour of acetylene, is this an acceptable withdrawal rate – all other factors not considered? If an acetylene cylinder has a known capacity of 75 cubic feet of acetylene, and the owner’s manual for an oxy-fuel torch specifies that a certain ‘tip model and size’ - at a certain pressure - will consume approximately 34 cubic feet per hour of acetylene, is this an acceptable withdrawal rate – all other factors not considered? IMAGES OF CYLINDERS - AS AT A SUPPLIER – 1/4. SHOWN ITEM(S), INCLUDING ITS/THEIR POSITION/CONDITION/SHAPE AND/OR ANY SETTING(S) IS/ARE NOT TO BE INTERPRETED AS RECOMMENDED, AVAILABLE OR ACTUAL. IMAGES OF CYLINDERS – AS AT A SUPPLIER – 2/4. SHOWN ITEM(S), INCLUDING ITS/THEIR POSITION/CONDITION/SHAPE AND/OR ANY SETTING(S) IS/ARE NOT TO BE INTERPRETED AS RECOMMENDED, AVAILABLE OR ACTUAL. IMAGES OF CYLINDERS - AS AT A SUPPLIER – 3/4. SHOWN ITEM(S), INCLUDING ITS/THEIR POSITION/CONDITION/SHAPE AND/OR ANY SETTING(S) IS/ARE NOT TO BE INTERPRETED AS RECOMMENDED, AVAILABLE OR ACTUAL. IMAGES OF CYLINDERS – AS AT A SUPPLIER – 4/4. SHOWN ITEM(S), INCLUDING ITS/THEIR POSITION/CONDITION/SHAPE AND/OR ANY SETTING(S) IS/ARE NOT TO BE INTERPRETED AS RECOMMENDED, AVAILABLE OR ACTUAL. GASES AND CYLINDERS - POINTS OF INTEREST - 1/4. According to sources: “Acetylene, hydrogen, and natural gas are shipped in a gaseous form, while propane, MAPP … and others are shipped in liquid form.”* “The pressure in a cylinder containing a liquefied gas is not an indication of the level of gas in the tank. …. High withdrawal rates of gas from liquefied gas cylinders will cause a drop in pressure, a lowering of the cylinder temperature, and the possibility of freezing the regulator.”** *JAMES A. PENDER, (1986), WELDING, THIRD EDITION, TORONTO MONTREAL NEW YORK ET ALL: MCGRAW-HILL RYERSON LIMITED, Page 24. **Larry Jeffus, (2017), Welding Principles and Applications, Eighth Edition, Boston, MA: DELMAR, CENGAGE Learning, Page 769. GASES AND CYLINDERS - POINTS OF INTEREST - 2/4. According to a source: “Although acetylene is commonly used for certain types of welding, other gases may be used. The most common of these are … MAPP gas, and hydrogen. …. Although propane itself is very stable, its low flame temperature limits its capabilities for welding.”* “The combination of oxygen and hydrogen generates a low-temperature flame used primarily for welding thin sections of metal, usually aluminum, on which low temperatures are required.”** *B. J. Moniz, (2015), Welding Skills, Fifth Edition, Orland Park, Illinois: AMERICAN TECHNICAL PUBLISHERS, Page 60. **B. J. Moniz, (2015), Welding Skills, Fifth Edition, Orland Park, Illinois: AMERICAN TECHNICAL PUBLISHERS, Page 61. GASES AND CYLINDERS - POINTS OF INTEREST - 3/4. According to sources: “Since MAPP gas is not sensitive to shock, it can be stored and shipped in lighter cylinders. … empty acetylene cylinders weigh about 220 lb. Empty MAPP cylinders weigh only 50 lb.”* “Refillable cylinders are made of steel or aluminum …. Most refillable cylinders have an open interior with walls of 1/4 inch steel and a reinforced neck and bottom.”** *B. J. Moniz, (2015), Welding Skills, Fifth Edition, Orland Park, Illinois: AMERICAN TECHNICAL PUBLISHERS, Page 61. **Virginia Tech. (2011). Compressed gas cylinders: cylinders. https://www.ehss.vt.edu/programs/CGC_cylinders.php p.1 GASES AND CYLINDERS - POINTS OF INTEREST - 4/4. According to a source: “… gases such as oxygen, nitrogen, argon, hydrogen and helium can be readily compressed into a cylinder.… Traditionally these cylinders have been made from high-strength steel or aluminum...”* “Many fuel gases are supplied in liquid form at room temperature … stored at lower pressures in thin-walled steel or composite aluminum cylinders.”** *Linde. (n. d.). Cylinders. https://www.lindegas.com/en/products_and_supply/supply_modes/new_cylinders/cylinders.html p.2 **Linde. (n. d.). Cylinders. https://www.lindegas.com/en/products_and_supply/supply_modes/new_cylinders/cylinders.html p.3 WRENCHES. It is not recommended to use an ‘adjustable wrench’ with oxy-fuel equipment. Specific wrenches have often been associated with oxy-fuel equipment. Be sure that the wrench is correct before using. ? SHOWN ITEM(S), INCLUDING ITS/THEIR POSITION/CONDITION/SHAPE AND/OR ANY SETTING(S) IS/ARE NOT TO BE INTERPRETED AS RECOMMENDED, AVAILABLE OR ACTUAL. SOME FUEL GAS COMPONENTS. Note the following: Notching on fittings, Cylinder pressure gage, Working pressure gage, Working pressure maximum as gleaned by the gage on the right. 15 psig has been an agreed upon maximum pressure for acetylene. SHOWN ITEM(S), INCLUDING ITS/THEIR POSITION/CONDITION/SHAPE AND/OR ANY SETTING(S) IS/ARE NOT TO BE INTERPRETED AS RECOMMENDED, AVAILABLE OR ACTUAL. SOME OXYGEN COMPONENTS. Note the following: No notching on fittings, Cylinder pressure gage, Working pressure gage. SHOWN ITEM(S), INCLUDING ITS/THEIR POSITION/CONDITION/SHAPE AND/OR ANY SETTING(S) IS/ARE NOT TO BE INTERPRETED AS RECOMMENDED, AVAILABLE OR ACTUAL. REGULATORS. The shown regulators are not interchangeable. Note that the compressed gas that each of these regulators is to be used for, is written on them. On the regulators that are shown, there should be an increase in working pressure when the adjusting screw is turned clock-wise. SHOWN ITEM(S), INCLUDING ITS/THEIR POSITION/CONDITION/SHAPE AND/OR ANY SETTING(S) IS/ARE NOT TO BE INTERPRETED AS RECOMMENDED, AVAILABLE OR ACTUAL.