Production Technology Lect. 2: Joining Processes PDF
Document Details
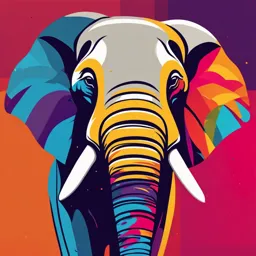
Uploaded by HealthyWillow2752
Helwan University Cairo
Mohamed A. Bhlol
Tags
Summary
This document is a lecture on Production Technology, specifically focusing on joining processes. It covers various methods, including mechanical fastening such as riveted and screwed joints, adhesive bonding, soldering, and brazing. The lecture provides details on different types of welding and their applications.
Full Transcript
Production Technology Lect. 2: Joining Processes Associate Prof. Mohamed A. Bhlol Topics Material joining methods Welding importance and applications Welding processes classification Shielded Metal Arc Welding Welding defects Welding terminology ...
Production Technology Lect. 2: Joining Processes Associate Prof. Mohamed A. Bhlol Topics Material joining methods Welding importance and applications Welding processes classification Shielded Metal Arc Welding Welding defects Welding terminology Materials joining methods Metal joining is defined as joining of two metal parts either temporarily or permanently with or without the application of heat or pressure Materials joining methods Why Joining Processes? Some products are too large to be made by individual processes. Easier, more economical to manufacture & join individual components. Products to be disassembled for maintenance Materials joining methods Mechanical fastening: Two major types of mechanical assembly: 1. Allow for disassembly. Use of the third part component. 2. Create a permanent joint with no possibility of disassembly. Types of mechanical fastening: a) Riveted joints b) Screwed joints: Materials joining methods Mechanical fastening: a) Riveted joints: A rivet is a cylindrical bar with a head integral to it. The cylindrical portion of the rivet is called shank or body and lower portion of shank is known as tail. The rivets are used to make permanent fastening between the plates such as in structural work, ship building, bridges, tanks and boiler shells. The riveted joints are widely used for joining light metals. Materials joining methods Materials joining methods Types of riveted joints: a. Single riveted joint b. Double riveted lap joint c. Single-strip butt joint d. Double-strip butt joint Materials joining methods Types of riveted joints: Double-strip butt joint Materials joining methods Mechanical fastening: Screwed joints: A screwed joint is mainly composed of two elements (i.e. bolt and nut). The screwed joints are widely used where the machine parts are required to be readily connected or disconnected without damage to the machine or the fastening. This may be for the purpose of holding or adjustment in assembly or service inspection, repair, or replacement Materials joining methods The common threaded fastener types are: Bolt is an externally threaded fastener that is inserted through holes in the parts and screwed into a nut on the opposite side. Screw is an externally threaded fastener that is generally assembled into a blind threaded hole and no nut is required. Stud is an externally threaded fastener, but without the usual head possessed by a bolt. Nut is an internally threaded fastener having standard threads. Materials joining methods Self-Tapping Screws (a) thread‑forming, and (b) thread‑cutting, also called a tapping screw. Nut Types Materials joining methods Set screws Assembly functions such as fastening collars , gears, and pulleys to shafts Materials joining methods Washer types a) plain (flat) washers b) spring washers: dampens vibration and resists loosing of bolt/screw c) Lock washer: designed to resist loosening of bolt/screw d) split lock washer: designed to resist loosening of bolt/screw (d) Materials joining methods Adhesive Bonding Joining process in which a filler material is used to hold two (or more) closely spaced parts together by surface attachment. Used in a wide range of applications for joining similar and dissimilar materials such as metals, plastics, ceramics, wood, and paper. Filler material in adhesive bonding is not metallic. Adhesive joints are not as strong as welded, brazed, or soldered joints. Materials joining methods Soldering and Brazing Soldering Soldering is a process of joining metal parts by heating and running a low-melting point alloy between the two surfaces being joined. For most purposes, the low-melting-point solder alloy is a composition of tin and lead. Solder melts at a temperature less than 300oC, which is far below the melting temperature of the metal being joined produces a low-strength joint. Materials joining methods Soldering and Brazing Brazing In brazing the joint is made by heating the base metal red hot and filling the gap with molten metal whose melting temperature is typically above 450°C. but below melting temperature of base metal. The filler metals are generally copper alloys. Cu- Zn and Cu-Ag alloys are used for brazing because they form alloy with iron and have good strength. Materials joining methods Self secured joints These joints are formed by folding and interlocking thin sheet edges together in such a manner that they are made secure without the aid of any additional joining process. Their use is confined to fabrications or components constructed with light gauge sheet metal less than 1.6 mm thick. Materials joining methods Welding Welding is a fabrication process used to join materials, usually metals or thermoplastics, together. During welding, the pieces to be joined (the workpieces) are melted at the joining interface and usually a filler material is added to form a pool of molten material (the weld pool) that solidifies to become a strong joint. Materials joining methods Welding Methods Fusion Solid state welding welding Base metal is melted by means of joining of parts takes place heat. A filler metal is added to the by application of pressure alone or a combination of heat and molten pool to facilitate the process pressure. and provide bulk and strength to the No filler metal is used. joint. Examples: diffusion welding, Examples: arc welding, friction welding, explosion resistance welding, oxyfuel welding, welding and ultrasonic welding. electron beam welding and laser welding. Welding importance and applications Welding applications: Welding is used in the manufacture of: - Automobile bodies - Aircraft frames - Railway wagons - Machine frames - Submarines - Storage tanks - Oil, gas and water pipelines - Boilers and pressure vessels - general repair work - Bridges and ship building. - Press frames Welding processes classification Welding processes can be classified as follows (based on the source of energy): Gas Arc Resistance Solid state Thermo- Radiant Welding Welding Welding Welding chemical energy Welding Welding - Oxyacetylene-Metal arc - Spot - Friction - Thermit - Electron Welding - Oxy hydrogen- Submerged arc - Seam welding beam - Ultrasonic welding - Inert-gas Weld.- Projection Welding - Laser TIG and MIG - Butt - Explosive beam - Plasma arc Welding welding Welding Welding processes classification 1) Gas welding: Gas welding includes all the process in which fuel gasses are used in combination with oxygen to obtain a gas flame. The commonly used gases are acetylene, natural gas, and hydrogen in combination with oxygen. The most commonly used gas combination is oxyacetylene process. Welding processes classification 2) Arc welding: Arc welding is a group of welding processes that use an electric arc as a source of heat to melt and join metals. Pressure or filler metal may or may not be required. Arc is struck between the workpiece and the electrode and moves relative to the workpiece, manually or mechanically along the joint. Welding processes classification 3) Resistance welding: Resistance welding involves the generation of heat by passing a high current through the resistance caused by the contact between two or more metal surfaces where that causes pools of molten metal to be formed at the weld area. Spot resistance welding Welding processes classification 4) Solid state welding: This group of welding processes uses pressure and heat (below the melting temperature) to produce coalescence between the pieces to be joined without the use of filler metal. Friction welding Welding processes classification 5) Thermo-chemical welding: Thermit welding is the process that results from a chemical reaction that is created through heating metal to a super high temperature between two reducing agents, one of which will be a metal oxide and the other aluminum or sometimes other types of reducing agents are used. Welding processes classification 6) Radiant energy welding: In this method a focused high-energy beam (Laser beam or electron beam) is used to melt the workpieces and thus join them together. Thank you