Ipe Marva PDF - Radiographic Imaging Techniques
Document Details
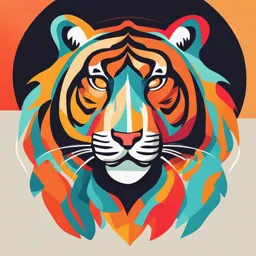
Uploaded by RenownedModernism4421
Riverside College, Inc.
Dean Abelardo L. Marva III
Tags
Related
Summary
This document provides an overview of radiographic imaging techniques, including radiography, radiology, and radiographs. It details the technical aspects of these procedures.
Full Transcript
Personal Notes from Dean Abelardo L. Marva III’s Research and Lectures Overview of Radiographic Imaging Techniques negatively charged electrode three parts – lar...
Personal Notes from Dean Abelardo L. Marva III’s Research and Lectures Overview of Radiographic Imaging Techniques negatively charged electrode three parts – large and small filament, and focusing cup Radiography filament radiography – use of ionizing radiation to produce a recorded o source of electrons image o small coils of tungsten wire about 1 to 2 cm in length radiography can be described as an art and as a science ▪ tungsten can withstand tremendous heat o the art of radiography requires specific skills in ▪ provides a good source of electrons through performance thermionic emission o as a science, radiography requires study of natural o 2 types phenomena ▪ small filament or small focus directs electrons to a smaller area on the target Radiology ▪ large filament or large focus directs radiology – the full name of the medical specialty electrons to a larger area on the target two groups of professionals o thermionic emission – occurs when the negatively o radiologists – board certified physicians who practice charged electrons break away from the hot filament to radiology form a space charge o radiologic technologists – professionals who are skilled o space charge – a cloud of electrons around the in the use of x-rays and radiation for the production of filament which becomes the source of electrons in x- high quality images of the human body ray production o space charge effect – phenomena where further Radiograph thermionic emission is halted by the space charge itself radiograph – image produced using x-radiation, it is the end focusing cup product of radiography o filament cup, encases the two filaments characteristics of a radiograph o focuses the space charge on a target area on the a. exposure factors are adequate anode b. there has been adequate penetration of the part of o the focusing cup is negatively charged, thus repelling interest electrons and focusing them c. sufficient radiographic density and contrast are present The anode (+) d. field size selection is appropriate positively charged electrode e. motion is eliminated during exposure two types – rotating (mostly) and stationary (outdated f. the anatomic part is properly positioned technology) g. proper accessories have been selected three parts – rotating target, stem and rotor rotor Technical competencies of the radiographer o shaft-like structure made of copper 1. operation of the control panel o rotation device that turns the stem and target area 2. selection of appropriate accessories stem 3. selection of correct factors to make exposures o attaches rotating target area to rotor 4. use of terminology in the evaluation of radiographs o copper – excellent conductor, dissipates heat away 5. measurement from the target area 6. evaluation of results (poor, fair and good) rotating target o circular, disk-like structure with a beveled edge The X-ray tube o receives electrons as they move from cathode to anode Tube housing o tungsten – can withstand tremendous heat heavy and lead-lined o angles on the edge of the anode – 8 to 20°/ 9 to 15° o rotations – 3000 to 10,000 rpm support for the x-ray tube and protection from electrical hazards o the rotation distributes heat to a larger area when x-rays are produced, they are emitted in all directions o focal spot – area of focal track that is struck by the housing serves as a protective device, preventing x-rays from electrons ”leaking” o focal track – runs the circumference of the anode disk has several openings for electrical cable connections and the port or window Line-focus principle design of the angled anode target area Glass envelope the angle makes the actual physical target area appear smaller the x-ray tube is located in the tube housing, enclosed in a glass resulting in a smaller effective focal spot size envelope actual focal spot – area being struck by electrons material – Pyrex glass, heat and chemical resistant to withstand effective focal spot – area directly below the target projected tremendous heat produced in x-ray production towards the window window of the glass envelope – small area in the Pyrex glass this angle also allows a greater surface area for heat dissipation which is made thinner so x-ray photons can pass easily Stationary anode X-ray tube designed similarly to rotating anode but without rotating capacity a diode tube – has two electrodes and reduced output special vacuum tube – air interferes with x-ray production long shaft of copper with tungsten target embedded in the consist of two electrodes inside a glass envelope slanted surface o positive anode usually found in dental x-ray units and some mobile radiographic o negative cathode units The cathode (–) 1 Personal Notes from Dean Abelardo L. Marva III’s Research and Lectures X-ray Production Milliampere second meter Control panel (old x-ray generator units) provide info to the RT by indicating the total current passing part of the radiographic equipment that is very familiar to the through the x-ray tube during the exposure radiographer located in the high-voltage section of the x-ray circuit the controls are the on/off switch, exposure timer, milliampere mAs – total amount of tube current selector, mA/mAs meter, kilovoltage selector, kV meter, rotor o milliampere × time (seconds) = milliampere seconds switch, accessory controls for the use of Potter-Bucky diaphragm, (mAs) and with some units, automated exposure controls Kilovoltage selection The on/off switch permits ↑ or ↓ in the voltage across the x-ray tube during the main purpose – to connect the electrical power to the x-ray exposure generator determine the specific tap on the autotransformer turned on early in the morning to warm up the generator selection of kV determines the energy of the x-rays produced main power box – turned off with on/off switch in an emergency during exposure 2 control selectors for easy specific kV setting Exposure timer o kV major – changes of ~10 kV per turn determine the length of time that x-rays will be produced o kV minor – changes of 1 to 2 kV per turn types o mechanical timers – similar to spring-set dial, shortest Kilovoltage meter setting is 1/10 s “prereading” volt meter o synchronous timers – motor driven, utilizes the 60-Hz o the meter gives reading during selection for the AC, has intervals related to 1/60 s, shortest setting is amount of voltage expected to pass across the x-ray 1/120 s tube as the exposure is made o electronic timers– most common, accurate, and the meter indicates voltage selection reliable, designed with complex circuitry, shortest position of meter indicates the amount of PD or voltage that will setting is less than 120 s move across the x-ray tube during exposure evaluation of timers – done periodically to guarantee accuracy 1. spinning top test Rotor and exposure switch ▪ used in evaluation for 1-ø, full-wave rotor switch rectified x-ray generators o initiates the rotation of the anode in preparation for ▪ consists of 2 metal parts, the exposure top part – ~3” round disk with a o maximum anode rotation is accomplished in ~1 sec small hole near the edge o activation of rotor permits full current to flow to the circular pedestal – where the cathode, causing it to become very hot and turn bright top part rests and rotates freely red ▪ steps exposure switch a. place the spinning top on top of o activated when the maximum RPM of the anode is the cassette with film reached b. the top is set by spinning with a o results in the production of x-rays flip of the fingers and exposures both switches are activated only when necessary, to permit a are made while the top is longer life for the x-ray tube spinning c. exposures – factors beginning Accessory controls with 1/60, 1/30 or 1/10 sec may include ▪ the timer is normal if there is: o Potter-Bucky diaphragm selection 1 dot per 1/120 sec exposure o vertical or horizontal devices 2 dots per 1/60 sec exposure o line voltage adjustor 4 dots per 1/30 sec exposure 12 dots per 1/10 sec exposure Automated exposure controls 2. calibrated oscilloscope AECs are designed to terminate the x-ray exposure automatically ▪ for testing a 3-ø x-ray generator o termination occurs when desired amount of exposure ▪ measures actual time of exposure which is reaches the film compared to the selected time to verify assist the RT in producing high quality and consistent radiographs accuracy requires no direct operation of the RT ▪ connected into the circuit to the primary either phototimer or ionization chamber, based on design voltage going to the step-up transformer o phototimer 3. pulse-counter device ▪ location – behind the cassette ▪ for both 1-ø and 3-ø x-ray generator ▪ faces a fluoroscopic screen that glows ▪ placed in the primary x-ray beam, where during exposure pulses are counted and evaluated ▪ terminates exposure when a proper amount of light reaches the photomultiplier Milliampere selector tube mA selector counts the amount of electrical current flowing o ionization chamber through the cathode filament ▪ location – b/w the cassette holder and ranges from 25 to 2000 mA patient (radiolucent) selection of mA determines focal spot sizes ▪ the chamber is ionized during exposure o low current for small focal spot ▪ terminates exposure once a preset charge is o high current for large focal spot accumulated and detected 2 Personal Notes from Dean Abelardo L. Marva III’s Research and Lectures back-up timer selection – a manual timer switch (ex: 1 sec) that o exposures are made using low mA (50-100 mA), large will terminate exposure if the AEC failed, thus protecting the focal spot, low to moderate kVp (65 to 70 kV), long patient and the x-ray tube from continuous exposure exposure time of 2 to 3 seconds radiographer sets optimal kVp – machine controls mAs o 3 or 4 exposures are made, several seconds between o AEC use a preselected fixed kVp while machine each exposure controls mAs o warm up again if tube is not used for several hours o varying kVp when using AEC does not alter density, before using again although contrast changes 2. switch precaution o varying kVp serves to alter penetrating ability of the o use only as needed, prolonged rotation with the beam, resulting in faster or shorter exposure time presence of a “hot” filament will shorten the life of the changing density controls on AEC allows density to be ↑ or ↓; anode and the cathode filament each step represents a change of 25% in density image quality in AEC – consistent from examination to Characteristics of x-radiation examination requirements – proper chambers selected; exact positioning over Key Points the chambers use of x-rays is vital in assisting physicians with the diagnosis of o overexposure or underexposure in AECs– caused by diseases and disorders improper chamber selection and/or patient positioning x-rays are a form of electromagnetic radiation errors radiographers must observe the rules for time, distance and shielding Selection of exposure factors image forming x-rays – those that exit the patient and interact factors selected by the RT to produce high quality radiographs: with the image receptor 1. kilovoltage exit beam – the x-rays that remain as the useful beam exits the 2. milliamperes patient 3. exposure time 4. table-top vs. Potter-Bucky diaphragm Characteristics of x-ray photons 1. cannot be focused by lens as in photography X-ray production 2. travel in straight lines and diverge from the point of origin before exposure 3. cannot be deflected by mirrors or other devices o patient is ready and in proper position 4. when x-ray photons strike certain substances, visible light is o equipment must be in place emitted – luminescence o appropriate factors are selected on the control panel 5. causes the changes that occurs in the sensitive emulsion of the sequence of events when making an exposure film 1. activation of the rotor switch 6. when interacting with matter, secondary and scatter radiation are 2. anode begins rotating as it reaches the proper RPM produced 3. meanwhile, the cathode filament gets very hot, resulting in thermionic emission Imaging system: X-ray film 4. electrons are “boiled off” the filament, creating a space charge Image receptor 5. with the filament hot, the space charge ready, and the radiographic film – the film records the image based on the anode rotating at peak RPM, the next step is activating pattern of transmitted x-rays and light produced by the the exposure switch intensifying screens. 6. as the exposure switch is activated, the current will a supercoat or protective coating is then used to protect the flow from the (–) cathode to the (+) anode target sensitive emulsion surface, essential at the time of use in the film 7. electrons move at a very high speed as a result of the holder PD, amounting to thousands of volts (kilovolts) applied basic parts – base & emulsion to the 2 electrodes during the exposure other parts – adhesive layer & overcoat 8. electrons strike the anode target (focal spot) with great force, resulting in many diff types of interactions thickness – 150 to 300 μm ▪ production of heat (~99%) biggest size – 35 × 43 cm. or 14 × 17 in. ▪ production of x-rays (~1%) smallest size – 20 × 25 cm. or 8 × 10 in. 9. x-rays are produced travelling in all directions, then absorbed mostly by the lead tube housing Film composition 10. useful rays are those that pass through the tube 1. Base window and housing port (primary x-ray beam) strike o the film base is the support that allows the film to the patient and produce a radiograph (remnant beam) maintain its shape, prevent bending and provide support for the emulsion Proper care of radiographic equipment o foundation and skeletal framework of the film life of the x-ray tube = action of the radiographer o x-ray film is made of flexible thin transparent base x-ray equipment is very expensive coated on both sides with a sensitive emulsion o the base does not affect basic fog level on the the RT is accountable for proper use of equipment to prevent radiographic film damage o characteristics focal track pitting – occurs from continuous bombardment of the 1. lucency – must be nearly transparent to electrons on the focal track, rhenium is added to the tungsten white light target to prevent pitting 2. dimensional stability – maintain size and 1. warm up procedures shape to prevent distortion of image o tube should be preheated before use 3. superior physical stability – flexible and o anode target area – preheated each morning before sturdy to prevent damage when handling use and processing 3 Personal Notes from Dean Abelardo L. Marva III’s Research and Lectures 4. blue tint – decrease eye strain, decrease 1. the number of silver halide crystals parallax effect, improve contrast, 2. the size of silver halide crystals contributes to 0.15 OD o film speed is given an arbitrary number o composition a. 200, 300, etc. – fast ▪ polyester – a polymer matrix b. 100 – average ethylene glycol c. >50 – slow dimethyl terephthalate o imaging system – the combination of a particular film o history – glass plate → cellulose acetate → cellulose and screen type triacetate → polyester o IR speed formula 1 2. adhesive layer ▪ in R to produce an OD of 1.0 ↑ b+f exposure o substratum layer ▪ ex: how much exposure is required to o coated on the base before adding the emulsion produce an OD of 1.0 above base plus fog o simply adheres the base to emulsion density on a 600-speed image receptor? o provides maximum contact b/w the base and emulsion 1 ▪ speed = 3. emulsion exposure 1 1 o the emulsion is the radiation sensitive and light ▪ exposure = = = 0.00167 R speed 600 sensitive layer of the film ▪ exposure = 1.67 mR o coated on both sides of the base (duplitized) o density maintenance (speed vs. mAs) o the spectral response of an emulsion is the absorption old speed new mAs ▪ = of visible light emitted by the phosphors new speed old mAs o ↑ contrast emulsion = small, uniform grain size ▪ ex: a PA chest examination requires 120 o composed of silver halide crystals suspended in gelatin kVp and 8 mAs with a 250-speed image o gelatin receptor. what radiographic technique ▪ a colloid extracted from cattle hooves and should be used with a 400-speed image hide, then rendered into a very pure, receptor? old speed new mAs uncontaminated state ▪ = new speed old mAs ▪ an ideal suspension medium for the silver old mAs (old speed) ▪ new mAs = halide crystals new speed 8 mAs (250) ▪ swells during processing so that chemicals ▪ new mAs = = 5 mAs 400 can penetrate the silver halide crystals film latitude ▪ rehardens after the invisible image o margin of errors in technical factors that the film becomes visible allows that will still produce an acceptable range of o silver halide crystals densities ▪ size – 1.0 to 1.5 μm o inherent characteristic of the film emulsion that allow ▪ active ingredient a moderate or acceptable range of densities to be ▪ the material sensitive to radiation and light recorded ▪ functions as energy detectors o range of exposures that produce OD within straight ▪ sensitivity specks – imperfections in the line region or diagnostic range of sensitometric curve crystal structure o inversely proportional to contrast ▪ silver bromide – ~98% ▪ ↑ latitude = ↓ contrast ▪ silver iodide – ~2% o film latitude – ability of film to record an acceptable ▪ AgNO3 (silver nitrate) + KBr (potassium range of densities bromide) = AgBr (silver bromide) + KNO3 ▪ narrow film latitude = high contrast (potassium nitrate) emulsion, “short” gray scale ▪ AgNO3 = NO3 (nitric acid) + Ag (metallic ▪ wide film latitude = low contrast emulsion, silver) “long” gray scale 4. supercoat o exposure latitude – ability of exposure factors to o topcoat or overcoat record an image with an appropriate range of densities o a durable protective layer that is intended to prevent on the film damage to the sensitive emulsion layer underneath it ▪ narrow exposure latitude – few factors can be applied to produce acceptable OD layer thickness material ▪ wide exposure latitude – many factors can base 200 μm polyester be applied to produce acceptable OD (more ethylene glycol “forgiving”) dimethyl terephthalate film contrast adhesive layer 3 – 5 μm o inherent ability to record minute differences in emulsion 150 – 300 μm gelatin densities across the film silver halide crystals o ability of the radiographic film to provide a certain silver bromide level of image contrast silver iodide o high contrast emulsions – provide good quality image supercoat 10 – 20 μm hard gelatin o low contrast emulsions – provide poor quality image Characteristics of x-ray film Brief history film speed date innovations o speed point 1895 photographic glass plates o speed is the degree to which the emulsion is sensitive 1914 cellulose nitrate film base (highly flammable) to x-rays or to light 1918 duplitized films, exposure is reduced to half o ↑ speed = ↑ sensitivity = ↓ exposure necessary to 1933 tinted film base produce a specific density 1936 direct exposure film o 2 primary factors that affect the speed point 1940 film suitable for direct and indirect exposure 4 Personal Notes from Dean Abelardo L. Marva III’s Research and Lectures 1958 fast light-sensitive film o globular grains 1960’s polyester film base and film for rapid o calcium tungstate phosphor (broad band emission) processing o insensitive to red, orange, and yellow orthochromatic film Types of x-ray film o green sensitive, sensitive to wavelength 1 year radiation reaching the film to continue in ▪ 0°C – storage temperature to store at to the AEC stop aging process ▪ has no lead foil film should be warmed up to room temperature at 35°C or Imaging system – intensifying screen 85°F before using again ▪ ↑ temperature = ↑ aging process Intensifying Screens ▪ store film in original packaging to note the used since the 1900s expiration date, which is located on the top acts as a transducer – converts x-ray energy to light which of the box or at the side exposes the radiographic film ▪ adhere to “first in, first out” or “last in, last intensifies the action of x-rays out” system intensifying screens fluoresce but not phosphoresce ▪ expired films are discarded made of polyester base with an active layer containing phosphors *can be returned to the that produce visible light when struck by x-rays manufacturer for silver recovery normally mounted inside the cassette in pairs for use with o prevent pressure double-emulsion film ▪ films are stored vertically, at edge, straight contact between the screens and the film must be perfect; poor or upright contact results in: ▪ film sheets may or may not be separated by o localized loss of recorded detail photo-inert leaves of paper that prevent o localized blurring on the image films from sticking to one another or to prevent pressure artifacts poor film-screen contact may be verified by radiographing a wire- o protect from radiation mesh test ▪ films are packed in a photo-inert allows 15 to 20 times less radiation exposure polyethylene bag or in a metal foil to advantages protect them from light/radiation and o ↓ radiation dose, ↓ technical factors, ↑ tube life moisture disadvantages ▪ store away films from radiation areas or use o ↑ quantum mottle, ↓ image quality protective barriers ▪ 12 µR limit Layers of the intensifying screen store chemicals away from the 1. base films o thickest part – 1 mm or 1000µm a box of potassium bromide o provides support to the phosphor layer with traces of radioactive 40K o made of high grade cardboard, plastic or polyester emits 7 µR because of decay, o characteristics two boxes will emit 14 µR ▪ resilient & moisture resistant o protect from chemicals ▪ does not suffer radiation damage or ▪ chemical fumes discoloration ▪ chemical fog – contamination of developer ▪ chemically inert & not interact with the solution with 0.1% of fixer phosphor layer ▪ a splash guard is placed to cover the ▪ flexible but not elastic developer tank when the fixing tank must ▪ must not contain impurities be removed 2. reflective layer ▪ development fog – restrainer prevents o thickness – 25 µm chemical fog by regulating development o serves to redirect light toward the film o use recommended safelight o intercepts light photons headed in other direction & ▪ safelight fog – most common form of film redirects them to the film fogging o ↑ film efficiency o very thin layer of white shiny substance made of Film holders magnesium oxide & titanium dioxide the cassette is the rigid, light-tight container that holds the o use of reflective layer = 2x film speed = 2x density = ↓ screens and film in close contact mAs by ½ to maintain density o screens may have a crossover effect of 30% or more cassettes are film holders used to transport film for use without o anti-crossover layer – also called crossover control exposing the film to room light layer, is designed for rare-earth screens and green- 2 to 3 inches – when loading, the top should not be fully opened sensitive films in order to prevent dust and formation of artifacts o anti-halation layer – designed for single-emulsion films cassette front such as mammographic films o metal frame with low Z and radiolucent front 3. phosphor layer o composition – magnesium, Bakelite or carbon fiber o thickness – 150 to 300 µm or 60 mg/cm2 contact felt o crystal size – 5 to 15 µm o compression layer o active and most important layer of intensifying screen o maintains proper film-screen contact 7 Personal Notes from Dean Abelardo L. Marva III’s Research and Lectures o emits light during stimulation by x-ray o for ↓ kVp techniques o luminescence – ability to give off visible light o for high resolution imaging o fluorescence – ability of phosphor to give off light only o ↑ mAs = ↓ quantum mottle while exposed to x-ray rare earth ▪ light emission during x-ray exposure or o speed – 1000 to 1200 while/promptly emitted or within 10-8 o more efficient in converting x-rays to light seconds o needs less x-ray energy to provide the same energy ▪ important to radiography conversion as calcium tungstate o phosphorescence – continue to emit light even after x- o ↑ conversion efficiency = no ↑ in crossover = ↑ image ray exposure has ceased or stopped sharpness ▪ produces afterglow or screen lag o 18 to 25% x-ray to light conversion ▪ somewhat after 10-8 seconds o only efficient in 40 to 75 kV range ▪ important to fluoroscopy o too ↑ or ↓ kV = ↑ quantum mottle o characteristics of a good phosphor o for green-sensitive film, has tabular grains ▪ detective quantum efficiency – the ability o specific emissions – only one color of the phosphor to interact with x-ray o lanthanum oxybromide – blue ▪ ↑ Z = ↑ DQE o gadolinium oxysulfide – green ▪ conversion efficiency – the ability of the o yttrium tantalite – ultraviolet, violet, blue, green phosphor to convert x-ray into light ▪ rare earth phosphors = ↑ CE Selection of radiographic imaging system ▪ spectral matching – specific color that the spectral sensitivity – refers color of light to which particular film is phosphors emit must match with the most sensitive spectral sensitivity of the film spectral emission – color of light produced by a particular ▪ minimum afterglow/lag – lag is insignificant intensifying screen in radiography but is used in fluoroscopy spectral matching – matching the sensitivity of the film to the 4. protective coating color of emission of intensifying screen o thickness – 10 to 20 µm o gives physical protection to the delicate phosphor layer Comparison of screen speed o provides a surface which can be handled and cleaned screen speed – the capacity of the screen to produce visible light without damaging the phosphor ↑ screen speed = ↑ light emission = ↑ density = ↓ quality o prevents static build up screen factors o transparent to x-ray o type of phosphor used o thickness of phosphor layer thickness material ▪ ↑thickness/size = ↑ screen speed = ↑ base 1000 µm high grade cardboard quantum mottle = ↓ recorded detail plastic or polyester ▪ ↑ light emission = ↑ density = ↓ mAs = ↓ reflective layer 25 µm magnesium oxide patient dose titanium dioxide o crystal size phosphor layer 150–300 µm calcium tungstate ▪ same as thickness lead barium sulfate o reflective layer barium fluorochloride ▪ use = 2x screen speed = ↑ quantum mottle zinc sulfide = ↓ recorded detail rare earth ▪ 2x light emission = 2x density = ↓ mAs = ↓ lanthanum oxybromide patient dose gadolinium oxysulfide o absorbing layer and dye in phosphor yttrium tantalite ▪ use = ↓ screen speed = ↓ quantum mottle protective 10–20 µm = ↑ recorded detail coating ▪ ↓ light emission = ↓ density = ↑ mAs = ↑ patient dose Phosphor materials Screen factors speed detail dose mottle calcium tungstate ↑ phosphor layer thickness ↑ ↓ ↓ ↑ o introduced by Thomas A. Edison ↑ size of crystals ↑ ↓ ↓ ↑ o responds well to x-rays reflective layer 2x ↓ ½ ↑ o manufactured in different speeds absorbing layer ↓ ↑ ↑ ↓ ▪ slow dye in phosphor ↓ ↑ ↑ ↓ ▪ medium or par ▪ high speed Screen speed measurements o 5% x-ray to light conversion screen speed – capability of the screen to produce light o used with blue-sensitive films, has globular grains tfilm speed – capability of the film to absorb light o broad band emissions – blue, indigo, violet intensification factor o scheelite – blue o intensifying action of the screen barium lead sulfate or barium fluorochloride o standard intensification factor – 30 to 50 o used to produce high-speed screens o formula o for high kVp techniques exposure w/o screens ▪ IF = o It was used to ↓ patient dose exposure w/ screens o ↓ mAs = ↑ quantum mottle ▪ intensification factor = ↑ intensifying action zinc sulfide relative speed value o used in fluoroscopic screens o most common method of designating screen speed o responds well with low intensity radiation o the ability of the screen to produce light and density 8 Personal Notes from Dean Abelardo L. Marva III’s Research and Lectures o 200 – RSV that requires 5 µR to produce speed point density Factors to Consider in the Processing Room o formula 1. location ▪ mAs1 = relative speed2 o in proximity/near to exposure room mAs2 relative speed1 mAs1 × relative speed1 o placed in the department that requires the RT to walk ▪ mAs2 = as few steps as possible relative speed2 o values 2. size ▪ 25 – ultra detail o 15 ft. × 9.5 ft. or greater for 200 radiographs/day ▪ 50 – slow/high resolution/detailed o wet and dry section ▪ 100 – standard/medium/par ▪ 4 ft. away from each other to prevent ▪ 200 – fast/high speed contamination of the dry section ▪ 300 – ultrafast/hi-plus ▪ a negathoscope can be located on the wet ▪ 1200 – rare earth section o RSVs of screens 3. protects against radiation ▪ calcium tungstate (slow–detail) – 30 to 50 o darkroom can be adjacent to exposure room only if the ▪ calcium tungstate (medium–par) – 100 wall is: ▪ calcium tungstate (high-speed) – 200 ▪ concrete – greater than 6 inches ▪ rare earth (slow–detail) – 100 ▪ hollow blocks – filled with cement ▪ rare earth (medium) – 300 to 500 ▪ wood – with 1.5 mm Pb ▪ rare earth (fast) – 800 to 1200 4. ventilation o ventilation in the darkroom is designed to eliminate Screen-Film contact heat and fumes the screen and the intensifying screen must be in complete o ventilation system must be light-tight contact across the entire surface to achieve maximum image o air changes – 8-10 room changes of air per hour, sharpness exhaust fan wire mesh test – test for screen-film contact o air movement – 15-25 ft/min, fan o 150 kV, 100 mA, 50 ms, 36 in SID o storage room temperature – 10-21°C or 50-70°F poor screen-film contact will result in a loss of image sharpness o dark room temperature: causes of poor screen-film contact ▪ 20°C or 67-83°F (old) o worn contact felt ▪ 18-24°C or 65-85°F (new) o loose, bent or broken latches (lock) o humidity for storage room and darkroom: o loose, bent or broken hinges ▪ 40-60% for storage room, not less than 45% o warped screen caused by excessive moisture ▪ too low humidity will cause static artifacts o warped cassette front ▪ darkroom – 30-60% o sprung or cracked cassette frame o air from the dryer of the automatic processor must be o foreign matter under the screen (most common cause) vented to the outside or to the ceiling o air trapping – transitory poor screen-film contact, more o psychrometer – a device used to measure humidity or obvious in the serial changing film cassette, a curved moisture back or curved front cassette will prevent air trapping o hygrometer– a device used to measure environmental moisture Care of screens 5. cleanliness o a darkroom’s efficiency pertains to its cleanliness care must be taken to avoid abrasions or scratches on the surface ▪ uncluttered countertops while loading the screen with film 6. light-tight entrance regular visual examinations must be made to reveal any dirt or o single door specks ▪ simplest type, a passbox is required to o UV light – to identify stain allow films to be transferred without cleaned on a regular basis entering the darkroom o antistatic cleaner ▪ interlocking system – prevents opening of o 70% isopropyl alcohol or 95% alcohol to shorten the the passbox when one side is open drying time ▪ the door should be weatherized o mild soap and water ▪ the door must be light, not heavy o cotton balls – for even cleaning ▪ locking mechanism when the lock is engaged, it will Processing the Radiograph prevent the door from opening when the storage bin is open The Radiographic Darkroom ▪ disadvantage – accidental film exposure a laboratory where radiography starts and ends o light-lock door or double door has controlled environment, designed to be functional and ▪ used only when there is darkroom convenient personnel exclusive in the darkroom designed for handling and storage of x-ray film ▪ if door 1 is open, door 2 is automatically the Occupational Safety and Health Agency requires the RT to locks wear face mask in the darkroom as fumes are carcinogenic ▪ fresh films are located on the left side, darkroom disease – hypersensitivity to fumes exposed films are located on the right main function of darkroom – to prevent/protect film from o labyrinth or maze exposure to white light and ionizing radiation during handling and ▪ easy access, zigzag type, doesn’t use a door processing ▪ used only when the darkroom is large as it latensification – an exposed film is 2-8 times more sensitive to requires more space subsequent exposure than unexposed film as it contains a latent o revolving door image 9 Personal Notes from Dean Abelardo L. Marva III’s Research and Lectures ▪ type with fastest access as RTs can enter o the film is evaluated using a densitometer and exit at the same time o acceptable safelight fog – 0.04 OD 7. illumination o if fog is present and increases with continues exposure o white light illumination – overhead light, 2 to 4 to safelight, the safelight is considered unsafe fluorescent lamps, covering 48 in of lamp per 8 m2 of 3. automatic processor temperature ceiling, for the purpose of maintenance, emergency o weekly use and cleaning, white light switch is located 4 m off o must be within ±0.3°C or 0.5°F the floor at eye level 4. replenishment rate o safelight illumination – also called safelight system, o weekly provides adequate illumination without detriment to o must be within ±5% film, film is most sensitive after exposure and before o oxidized developer processing ▪ old or exhausted developer o distance – 3 to 4 ft from the workbench, 4 ft from the o contaminated solution feedtray of the automatic processor ▪ entire solution is ineffective o wattage – 7.5 watts tungsten bulb at 3 ft distance, 15 ▪ can’t be replenished and should be replaced watts at 4 ft distance o function of replenishment o filters – filters out intensity and energy/color ▪ maintain or bring back the activity of ▪ amber filter – filters out red, orange and chemical on its original activity or yellow colors, used in blue-sensitive film composition appears brownish o fixer tank – should always be filled first when cleaning ▪ Kodak Wratten 6B filter – >550 nm, filters a processor only the intensity, used for monochromatic o an advisable period of changing processing solutions in film, alternatives include an amber filter & an automatic processor is every 6 months Kodak Morlite 5. solution pH ▪ Kodak GBX-2 filter– >600 to 620 nm, multi- o quarterly, every 3 months purpose, filters out yellow and orange, for o pH range – qualitative method of measuring the both blue/green sensitive film, appears dark alkalinity or acidity of a solution red ▪ 7 to 14 – base, alkaline chemical 8. color of walls ▪ 7 – neutral o pastel and light colors – ↑ reflectance of safelight, ▪ 0 to 7 – acid, acidic chemical ivory or light gray color o developer – pH of 9.6 to 10.6 o matte finish not glossy – ↓ reflectance of white light o fixer– pH of 4.2 to 4.9 o enamel & epoxy – easy to clean and durable, dries 6. developer specific gravity quickly o quarterly, every 3 months o neon color – prohibited o must not greater than 0.004 o bright color – chosen over dark colors o specific gravity is the amount of water versus chemical 9. electric wiring o hydrometer – a device that measures specific gravity o should be appropriately installed 7. processor control chart monitoring 10. safelight o daily, early in the morning o direct safelight – fixture type safelight, light is o done after the automatic processor reached its distributed directly, most common in the hospital maximum capacity or has been warmed up o indirect safelight – ceiling type safelight, light goes up o not greater than 0.15 OD from baseline measurements first before being reflected, uses sodium vapor bulb, o speed and contrast indication distance from the workbench must be 6 ft, the only 8. film sensitometry disadvantage is that it takes time to warm-up before o quantitative measurement of response of film to use exposure and development o measures Darkroom and automatic processor quality control ▪ film speed 1. darkroom environment ▪ film contrast o daily ▪ film latitude o maintained clean, well ventilated, organized and safe ▪ contrast using hydroquinone 2. safelight test o devices used o semi-annual ▪ sensitometer – optical step wedge o safelight fog ▪ penetrometer – aluminum step wedge, ▪ contributes to greater than 0.05 OD used in step-wedge exposure, alternative ▪ always check the distance, wattage and for sensitometer filters used ▪ sensitometric strips or step tablet – made o steps by exposing successive areas on a film and ▪ load a cassette with film with all lights off progressively making larger exposure until ▪ expose it with a small amount of radiation maximum density on the film is reached ▪ return to the darkroom and lay the film ▪ densitometer – measures the density of with all lights off on the area of the work exposed film by measuring the percentage counter of light transmittance ▪ cover ¾ of the film 0 OD – 100% ▪ turn on the safelight 1 OD – 10% ▪ expose the film for 1 minute, then uncover 2 OD – 1% another ¼ of the film 3 OD – 0.1% ▪ continue the procedure, until the entire film is exposed in 4 minutes Quality Control test Schedule Standard ▪ turn off the safelight and process the film Darkroom environment daily Maintained can, well ventilated, 10 Personal Notes from Dean Abelardo L. Marva III’s Research and Lectures organized and safe o 1965 – Eastman Kodak, 1st rapid processing at 90 s Safelight test semi- Must not contribute to 0.05 OD o 1987 – Konica, rapid processing at 45 s using special annually added as fog chemicals Automatic processor weekly Should vary more then ±0.5°F automatic processor installment types temperature (0.3°C) o totally inside Replenishment rates weekly Should fall within ±5% of ▪ all automatic processor are located inside manufacturer’s specification ▪ advantage – jammed films can be retrieved Development time daily Maintained within ±2 to 3% of without exposure to white light manufacturer’s specification ▪ disadvantages – ↑ heat, noise and humidity Developer specific quarterly Should not vary more than ±0.004 inside the darkroom gravity from manufacturer’s specifications o bulk inside Developer solution pH quarterly Maintained b/w 10 to 11.5 ▪ more advisable as all automatic processor Fixer solution pH quarterly Maintained b/w 4 to 4.5 are located inside but the drop tray is Processor cotrol chart daily Speed and contrast indicators should located outside monitoring not vary more than ±0.15 OD from ▪ advantages – easy retrieval of films, ↓ heat, baseline measurements noise and humidity o bulk outside ▪ only the feed tray is located inside Processing System ▪ used only when the darkroom is small processing the x-ray image changes the latent image to a visible ▪ advantages – almost no heat, noise and image that is made permanent for handling, viewing and storage humidity to process a film, one must develop, fix, wash, and dry it ▪ disadvantages – jammed films can’t be o latent/potential image – refers to the image that retrieved through white light exists on film after it has been exposed but before it has been processed Requirements for a processing room o visible/manifest image – black metallic silver image requirement comment developer solution in developer tank converts exposed silver 1. control of temperature helps maintain adequate density and bromide crystals (latent image) to black metallic silver (visible contrast image) 2. agitation of chemical solutions provides thorough mixing of fixer solution in fixer tank clears and removes unexposed silver chemical solutions bromide crystals, stops development, and hardens the emulsion 3. replenishment maintains volume and strength of water in the wash tank removes chemicals remaining on film; film solution is dried in dryer system 4. minimum spilling of chemicals reduces contamination of chemicals the overflow solution is carried over the top of the tanks into the as film moves from tank to tank water drain 5. transportation of film through controls length of time film is in manual processing system system remains constant developer and fixer o 70°F 6. time-temperature relationship maintains consistency with all processing system tanks processing systems o cascade compartment type 7. compact in size requires very little space to operate ▪ has a developer tank, fixer tank, and 2 wash 8. strategic placement reduces the time spent by tanks radiographers traveling to and from for initial and final washing darkroom area uses hyponeutralizer o master tank and insert tank type Automatic processor systems processing systems Automatic processors o transport system – moves film through the processor a device that has roller transport system, comprised of chemical and agitates the chemistry tanks and a dryer system for processing of radiographic film o replenishment system – adds fresh developer and dry to dry systems fixer solution for each film as it is fed into the processor standardize the processing of radiographs with consistency and o recirculation system – agitates and filters developer efficiency solution; stabilizes solution temperature; prevents processing cycle stratification of chemicals in the tank o dry-to-drop time o dryer system – dries film at approximately 120°F after o the time to process a single piece of film it leaves wash tank o usually 45 seconds to 3.5 minutes transport system processing capacity o advances the film through the processor o number of film that can be processed per hour o the speed the film is moved throughout the processor standard size of automatic processors – 24 inches/corner must remain constant 90 secs automatic processor o the transport system also agitates the solution and o 33.8 to 35°C or 90 to 95°F helps maintain the temperature o clear time – 15 to 20 seconds o overlapping of film could occur when film is ▪ 5 to 2 seconds before clearing agent begins prematurely fed into the processor because of the to function rollers double capacity processor o the transport system moves film from the feed tray o can process a film in 3 minutes into developer, fixer, wash tank, dryer, and finally out brief history of the processor to the receiving tray o 1942 – Pako, 1st automatic processor, moves films on o entrance roller – grabs the film, covered with hangers from tank to tank corrugated rubber, made up or either Plexiglas or o 1956 – Eastman Kodak, 1st roller transport system 11 Personal Notes from Dean Abelardo L. Marva III’s Research and Lectures acrylic plastic, polyester plastic, phenolic resin (water ▪ diaphragm-type pump absorbent), rubberized plastic or stainless steel ▪ bellows-type pump – most recommended ▪ a visual signal is emitted when the film ▪ magnetic-drive centrifugal pump – used by completely passes over the entrance roller Kodak processor o transport or planetary roller – vehicle transport, ▪ percentage time pump – Sonics or Litton moves the film through the chemical tanks and dryer, ▪ piston-type pump – the principle is like a distributed throughout the processor, 1 in in diameter syringe o turnaround, solar or master roller – bottom of the o volume replenishment roller assembly, turns the film from moving down the ▪ for processors with 25-50 pcs of 14×14 or transport assembly to moving up the assembly, some 14×17 films developed per day processors have a semi-master roller, 2 in in diameter ▪ utilizes a microswitch located at the o crossover roller – moves the film from one tank to entrance of the automatic processor which another controls the replenishment rate of ▪ squeegee roller – removes excess moisture processing chemicals from film surfaces using a specialized ▪ replenishment rate are normally rubber area to prevent carryover of established on the basis how much chemicals as film is moved from tank to chemistry is required per 14 in of film travel tank developer o guide plates – found in turnaround and crossover o 60-70 cc/film rollers, slightly curved metal plates, properly guide the o 4-5 mL/in leading edge of the moving film through the processor fixer o motor drive – an electric motor, provides power for o 100-110 cc/film the roller assembly to transport the film through the o 6-8 mL/in processor ▪ replenishment occurs only if 14×14 or ▪ on/off switch – connects the processor to 14×17 film is sensed by the microswitch the electric power ▪ 8×10 in – no replenishment occurs unless ▪ standby power – electric circuit that shuts two films are fed together, side by side the power off the roller assemblies when o flood replenishment (very rare) processor is not in use ▪ timed or standby ▪ belt and pulley, chains and sprocket, gears ▪ introduced by Donald Titus of Kodak – connects the motor to the rollers ▪ for processors with 98% of film emulsion exposure spectral matching – the color light emitted by the phosphors Variables Photographic Geometric must be correctly matched with the film emulsion sensitivity Properties Properties rare earth phosphors = ↑ conversion efficiency Density Contrast Detail Distortion calcium tungstate phosphors = ↓ conversion efficiency malakas mAs ↑ ↑ conversion efficiency & speed of screens = ↑ fluorescent light mahina mAs ↓ diffusion = ↓ recorded detail malakas kVp ↑ ↓ IS speed is influenced by mahina kVp ↓ ↑ o type and size of phosphor used malayo SID ↓ ↑ ↓ o thickness of the active/phosphor layer malapit SID ↑ ↓ ↑ o degree of reflectance, given the screen base malayo OID ↓ ↑ ↓ ↑ fast screens + ↓ mAs & ↑ kV factors = ↑ quantum mottle malapit OID ↑ ↓ ↑ ↓ makapal grid ratio ↓ ↑ lag or afterglow – phosphor fluorescence after the x-ray source manipis grid ratio ↑ ↓ has terminated mabilis film-screen ↑ ↓ phosphorescence – associated with fluoroscopic screens mabagal film-screen ↓ ↑ perfect screen-film contact– required to maintain recorded detail sinikipan collimation ↓ ↑ o screen–film contact is measured using wire mesh test binuka collimation