Operations Management Introduction PDF
Document Details
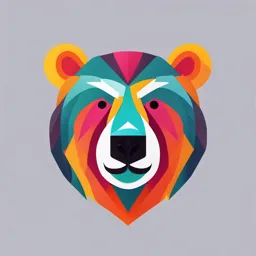
Uploaded by EquitableSlideWhistle
Tags
Summary
This document provides an introduction to the concepts of operations management. It details the differences between manufacturing and production, and explores the scope of operations management with topics like plant location, material handling, and product design.
Full Transcript
Introduction The manufacturing management is the process of converting the raw material into the finished goods whereas the production management is the process of transforming raw material into the finished goods with quality output as Unique Selling Proposition (USP). The Operations Management is...
Introduction The manufacturing management is the process of converting the raw material into the finished goods whereas the production management is the process of transforming raw material into the finished goods with quality output as Unique Selling Proposition (USP). The Operations Management is the process of creating services for the consumption purpose or it is the process of converting raw material into finished services. The major difference between the manufacturing and production are as follows Manufacturing is the process by which raw material is transformed into tangible salable goods whereas production creates the product or goods as a utility. Manufacturing convert raw materials into finished products with the help of some machinery that is used as a medium to convert raw material into finished goods on the other hand production cannot be using medium to form utility. Manufacturing is a smaller part of production whereas production is a broader concept as compared to manufacturing as it involves different operations, utility and quality output. Tangibility is seen in case of manufacturing whereas tangibility and intangibility both are seen in case of production. Manufacturing unit use any definite formula for preparing the goods whereas production has a definite formula called as output / input for preparing utility consumable products. The man power and machinery are mandatory in the case of manufacturing whereas men power and machinery may or may not be used in the case of production process. The major difference between the production and operations are as follows The production management is concerned with creation of finished goods as utility related to production function whereas operations management is concerned with regular business functions and production and delivery of services. The scope of production management is limited in nature as it is limited to production of goods and it is limited to the price of the product, quantity to be produced, and quality of goods to be produced. On the counter part, the scope of operations management is wider in nature as it is restricted to regular production function along with manpower planning in the production department and price of the product, quantity to be produced, and quality of goods to be produced and so on. The focus of production management is to deliver the right quality of product at the right price at desired time in the ordered quantity. The focus of operations management is to use all available resources of the organization to deliver routine business activities and for the delivery of services purpose. Production management is useful in every production organization where raw material is converted into finished goods. The operations management is used in service industry such as hotels, hospitals, educational institutes, banks, manufacturing firms, consultancy service providers and so on. The new challenges in Operations Management are as follows Demand for quality products or services Lowering Cost of Services Many Options and Varieties New Service Innovations Environmental impact Political and legal pressure Rapidly changing technologies Security alerts Changing needs, taste and preferences of customers Scope of operations management The scope of operations management is explained in detail as follows 1. Plant location and facilities location Selection of plant location and facility location is long term capital decision as it involves purchase of plant or factory or firm for creating and delivering the customer services or utilities. Hence while selecting plant location and facilities location, the utmost care is taken to make investment in plant location. The decision of selection of Plan location and facilities location leads to the success and failure for the service operations. 2. Plant Layout Plant layout refers to the physical arrangement of facilities. The operations management assists to understand and to arrange plant design so as to create and deliver utilities to the customers. 3. Material Handling The production and operations management assists to handle the material with proper care and to transport it and to store it at the proper location. The concept of material handling is being learnt in the production and operations management. 4. Product Design Creativity is converted into innovation in the product design. The idea generated is transformed into the services in the product design. 5.Process Design The process design is the flow diagram or layout of the process of conversion of input to the output services. The process design is the decision tree diagram or overall process path for the product development. The process flow analyses, choice of technology and workflow diagram are the parts of product design. 6. Production Planning and Control The Production planning and control is defined as the process of planning in advance the production volume, order timing, production scheduling, follow up procedure and control measures. The production planning and control is essential to deliver the services at right time at right price in right volume at right specification. 7. Quality Control The quality control is the maintenance of standards in the quality of product or in the quality of services. The quality control measure detects the defects in the product or services and eliminates the defects in the product or services. 8. Materials Management The material management is the process of purchasing material at desired process, at desired volume and controlling the material as and when needed and making the use of materials in the operations process to create and deliver the utilities or customer service. The objectives of materials management are to purchase the inventory at minimum cost, to control the material requirement and to have flow of materials in the production process or operations process. 9. Maintenance Management The maintenance management is the crucial part in the production and operations management. The maintenance of machinery needed in the production and operations department is essential without which production or operations can’t be augmented. Difference between manufacturing and service organisations 1.Operational planning Operational planning is the foundational function of operations management. Your duties within this function may include: Monitoring daily production of goods Managing and controlling your inventory Keeping tabs on team member performance and well being Production planning The role of operations management is to uphold operational efficiency. Always be on the lookout for new advancements to remove bottlenecks and improve your operations strategy. 2. Finance Finance is an essential—and universal—function of operations management because every company strives to reduce costs and increase profits. As an operations manager, you’ll ensure company leaders keep the budget in consideration when they make important decisions. Some of your tasks may include: Creating budgets to meet production goals Finding investment opportunities Allocating budgets and managing resources You may wonder how the financial duties of the operations team differ from those of the finance department. The finance department will handle everything from revenue to salaries. Meanwhile, you should limit your financial participation to things relevant to the production process. 3. Product design Product designers may be the creatives of the team, but the operations team is the eyes and ears that gathers information from the market. Once you identify customer needs and marketing trends, you'll relay what you've learned back to the designers so they can make a strong product. Specific tasks your team may handle in this function include: Consolidating market research into digestible results Communicating results to a product design team Offering design direction to help designers devise a product Without the operations team, the product design team would have trouble knowing what to create. The market is always changing, and creating a successful finished product requires extensive research. 4. Quality control Quality control goes hand in hand with product design. After the production team creates a product, the operations team will ensure it meets quality standards. You’ll need to test the product to guarantee there are no defects before releasing it to the public. Your tasks for quality control may include: Performing risk analysis to identify potential problems Inspecting products to make sure they meet quality standards Creating tests to control your product quality Documenting any defects or deficiencies of products The level and standards of quality control vary by industry—one of the first things your team should do during the quality control process is to perform market research to determine what quality standards should be in your industry. Once you’ve outlined a set of quality standards, use them as a benchmark for quality management moving forward. 5. Forecasting Forecasting isn't just a term for the weather—operations teams also use forecasting to predict the demand for a product. 6. Strategy Strategy is a broad function of operations management that can involve operational planning, monitoring, and analysis. The goal of strategic management is to make sure production decisions align with business goals. Your company’s business objectives may include: Prioritizing customer satisfaction Improving the production system Controlling costs while maintaining a competitive edge Your job as operations manager is to find ways to meet the business objectives of your company. Some strategies you could use for the examples above include: Analyzing your inventory: To prioritize customer satisfaction, start by analyzing your inventory. This can increase customer satisfaction by ensuring you’re always able to meet customer demand. Collaborating among teams: More collaboration among teams will improve the production system because communication will increase, resulting in less room for error. Prioritizing green processes: Switching to more environmentally friendly processes can save money in the long run and keep customers invested in your brand.