Introduction To Operations Management Part 1 PDF
Document Details
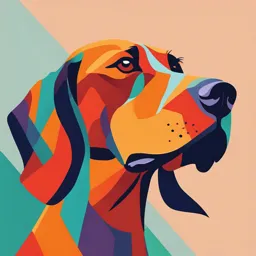
Uploaded by InvigoratingDifferential8834
Quezon City Polytechnic University
Ruel M. Tuan
Tags
Related
Summary
This document is a presentation on introduction to operations management, part 1, given by Ruel M. Tuan. It covers various aspects of operations management including the definition of operations, examples of final goods and services, and different production systems. It also describes the key concepts of efficiency, effectiveness, and value in operations management.
Full Transcript
Introduction to Operations Management Part 1 Presented by: Ruel M. Tuan, MSIEM, AAE, PIE, CIE, LSSGB-T, CSSYB INTRODUCTION 3 The Fundamentals of IE Basic industrial engineering tools, methods, and procedures and specifies their appropriate application areas f...
Introduction to Operations Management Part 1 Presented by: Ruel M. Tuan, MSIEM, AAE, PIE, CIE, LSSGB-T, CSSYB INTRODUCTION 3 The Fundamentals of IE Basic industrial engineering tools, methods, and procedures and specifies their appropriate application areas for improvements and problem solving. The theoretical basis of industrial engineering is a science of operations. To successfully use this science in most applications one must simultaneously consider at least three criteria: (1) quality, (2) timeliness, and (3) cost The goal of industrial engineering is to ensure that goods and services are being produced or provided at the right quality at the right time at the right cost. 4 WHAT OPERATIONS IS Operations refer to “any process that accepts inputs and uses resources to change those inputs in useful ways.” 2 Examples of final goods are as follows: 1. Industrial chemicals like methylene chloride, borax powder, phosphoric acid, etc., which are produced by chemical manufacturing firms. 2. Electrical products like transformers, circuit breakers, switch gears, power capacitors, etc., which are produced by electrical manufacturing firms 3. Electronic products like oscilloscope, microwave test systems, transistors, cable tester, etc., which are produced by electronics manufacturing firms 4. Mechanical devices like forklifts, trucks, loaders, etc., which are produced by manufacturing firms. 2 Examples of final services are as follows: 1. Services like those for the construction of ports, high-rise buildings, roads, bridges, etc., which are produced by constructions firms 2. Engineering consultancy services like those for construction management and supervision, project management services, etc., which are produced by engineering consultancy firms. 2 Operations Management Operations management is defined as the design, operation, and improvement of the systems that create and deliver the firm’s primary products and services. 2 Operations Management 2 Operations Management 2 Transformation Process 2 Transformations Physical--manufacturing Locational--transportation Exchange--retailing Storage--warehousing Physiological--health care Informational--telecommunications 5 13 Examples of Production Systems System Inputs Conversion Output (desired) Hospital Patients Health Care Healthy MDs, Nurses Individuals Medical Supplies Equipment Restaurant Hungry Customers Prepare Food Satisfied Food, Chef Serve Food Customers Servers Atmosphere Automobile Sheet Steel Fabrication High Quality Plant Engine Parts and Assembly Automobiles Tools, Equipment of Cars Workers University High School Grads Transferring Educated Teachers, Books of Knowledge Individuals Classroom and Skills 6 Operations Management An operation is an activity that needs to be managed by competent persons. Aldag and Stearns accurately defined operations management as “the process of planning , organizing, and controlling operations to reach objectives efficiently and effectively.” As the terms “ planning”, “organizing”, and “controlling” elaborations on the terms “efficiency” and “effectiveness” will be made. 2 Key OM Concepts ▪ Efficiency - Doing something at the lowest possible cost ▪ Effectiveness - Doing the right things to create the most value for the organization ▪ Value - Quality divided by price 8 Efficiency & Effectiveness Efficiency is related to “the cost of doing something, or the resource utilization involved.” When a person performs a job at lesser cost than when another person performs the same job, he is more efficient than the other person. Effectiveness refers to goal accomplishment. When one is able to reach his objectives, say produced 10,000 units in one month, he is said to be effective. 2 Operations Management - Overview Process Analysis Process Control Supply Chain Project and Design and Improvement Management Management Operations Quality Supply Chain Strategy Management Strategy Process Analysis Statistical Just in Time Process Control Job Design Planning for Production Consulting and Manufacturing Reengineering Capacity Management Facility Layout Aggregate Planning Services Inventory Control Waiting Line Analysis Materials Requirement Planning and Simulation Operations Strategy Strategy Process Example Customer Needs More Product Corporate Strategy Increase Org. Size Operations Strategy Increase Production Capacity Decisions on Processes Build New Factory and Infrastructure Operations Decision Making Marketplace Corporate Strategy Finance Strategy Operations Strategy Marketing Strategy Operations Management People Plants Parts Processes Materials & Products & Customers Services Planning and Control Input Output The Transformation Process (value adding) 4 Operations Management Decisions Strategic Decisions Decisions that set the direction for the entire company; they are broad in scope and long-term in nature. Tactical decisions Decisions that are specific and short-term in nature and are bound by strategic decisions. 21 Operations Management Decisions 22 2 SERVICE PRODUCTION SYSTEM The Fundamentals of Industrial Engineering 23 24 Service is… All economic activities whose output is not a physical product or a construction is generally consumed at the time it is produced, and provides added value in forms (such as convenience, amusement, comfort or health). -Zeithamal et.al (1996) 10 Front and Back Office Service Back Office does not require customer presence. Service Provider Front Office work requires customer presence. Customer 9 Source: Metters, King-Metters, Pullman, & Walton, p. 84 Core “Factory Services” Core Services are basic things that customers want from products that they purchase. Quality Flexibility Speed Price (or production cost) 10 Value-Added Services Value-added services differentiate the organization from competitors and build relationships that bind customers to the firm in a positive way. Information Problem Solving and Field Support Sales Support 11 Differences between Manufacturing and Service Organization Manufacturing organizations Organizations that primarily produce a tangible product and typically have. Service organizations Organizations that primarily produce an intangible product, such as ideas, assistance, or information, and typically have high customer contact. 10 Two Primary Distinctions: 1.) Manufacturing organizations produce physical, tangible goods that can be stored in inventory before they are needed. By contrast, service organizations produce intangible products that cannot be produced ahead of time. 10 Two Primary Distinctions: 2.) Second, in manufacturing organizations most customers have no direct contact with the operation. Customer contact occurs through distributors and retailers. 10 IMPORTANT DIFFERENCES: GOODS AND SERVICES 1. TANGIBLE? 2. CUSTOMER PARTICIPATES IN THE PRODUCTION? 3. CAN BE STORED AS INVENTORY? 4. FACILITIES SHOULD BE NEAR CUSTOMER? 33 Characteristics of manufacturing and service organizations 34 THANKS! 35