Eastern Samar State University Civil Engineering Written Report PDF
Document Details
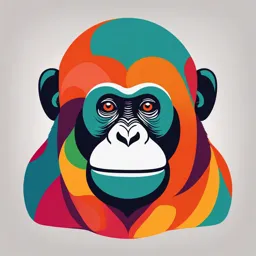
Uploaded by PerfectCarolingianArt551
Eastern Samar State University
2024
Tags
Summary
This report discusses construction equipment operations, productivity, and maintenance, with a focus on the importance of these elements in construction projects. It provides a thorough overview of different types of construction equipment and their applications, emphasizing the critical role of skilled operators and maintaining safety standards.
Full Transcript
**EASTERN SAMAR STATE UNIVERSITY -- MAIN** **College of Engineering** **Bachelor of Science in Civil Engineering** **A WRITTEN REPORT PRESENTED** **TO** **ENGR. RICHARD C. MENDOZA** *In Partial Fulfillment of the Requirements for the Subject* *CE 415 Advanced Construction Methods and Equipmen...
**EASTERN SAMAR STATE UNIVERSITY -- MAIN** **College of Engineering** **Bachelor of Science in Civil Engineering** **A WRITTEN REPORT PRESENTED** **TO** **ENGR. RICHARD C. MENDOZA** *In Partial Fulfillment of the Requirements for the Subject* *CE 415 Advanced Construction Methods and Equipment* **GROUP - 8** **Legion, Trina Mae D.** **Noroña, Adelyn** **Norte, Rose Marie** **Oriondo, Einjehl** **Paligutan, Rialyn Mae M.** **NOVEMBER 2024** **CONSTRUCTION EQUIPMENT OPERATIONS, PRODUCTIVITY,** **AND MAINTENANCE** **INTRODUCTION** In modern construction projects, heavy equipment is an integral part of efficiently completing complex tasks, ranging from earthmoving and excavation to building erection and site preparation. The term "construction equipment" encompasses a wide array of machinery designed to perform specific functions that simplify, speed up, and enhance productivity in construction operations. This machinery, which includes excavators, bulldozers, cranes, loaders, and trucks, plays a central role in ensuring that projects are completed on schedule, meet required standards, and stay within budget. To maximize the effectiveness of construction equipment, three critical elements must be understood: operations, productivity, and maintenance. Understanding the operation of each piece of equipment involves not only knowing how to control it but also mastering the skills required for its safe and efficient use. Productivity, a major goal in construction management, refers to the efficient use of resources to maximize output while minimizing costs. Regular maintenance, meanwhile, is essential to avoid unexpected breakdowns and prolong equipment life. Effective operations, heightened productivity, and timely maintenance ensure that construction projects proceed smoothly, reducing both costs and downtime. By integrating these three factors into project planning, construction managers can make strategic decisions that optimize resources, elevate project outcomes, and reduce risks. **CONSTRUCTION EQUIPMENT OPERATIONS** I. **Construction Operation** Construction operations encompass the various processes involved in creating, modifying, or dismantling buildings and infrastructure. These processes can include the construction, alteration, repair, extension, demolition, or dismantling of structures. Each of these activities requires specific skills, tools, and equipment to execute effectively and safely. For example, constructing a high-rise building requires cranes, while roadwork often involves pavers, rollers, and graders. II. **Construction Equipment** Construction equipment refers to heavy-duty vehicles specifically designed to execute tasks involved in construction operations. They are also called heavy machines, heavy trucks, heavy equipment, engineering equipment, heavy vehicles, or heavy hydraulics. Each type of construction equipment is uniquely designed to perform specific tasks in construction projects, such as excavating soil, transporting materials, lifting heavy objects, or laying pavement. The primary categories of construction equipment include: 1. **Earthmoving Equipment** -- This includes bulldozers, excavators, and backhoes used for digging, grading, and moving large amounts of soil or rock. 2. **Material Handling Equipment** -- Equipment like cranes and forklifts fall into this category. They help lift and transport heavy construction materials. 3. **Construction Vehicles** -- These include dump trucks and loaders, which transport construction materials and waste within the construction site. 4. **Construction Site Equipment** -- Asphalt pavers, compactors, and graders are examples of equipment used specifically for roadwork and pavement laying. III. **Construction Equipment Operation** Operating construction equipment requires skill, precision, and adherence to safety standards. A construction equipment operator must understand the machine's functions, controls, and operational limits. The goal is to ensure each task is executed efficiently and safely, which involves coordinating machine functions with construction objectives. Operators must consider factors such as load limits, maneuverability, and operational speed, which can influence productivity and safety on site. Proper operation also involves performing pre-operation checks and monitoring equipment throughout the project to prevent mechanical issues. IV. **Factors to Consider When Selecting Construction Equipment** Choosing the right equipment for a project is a critical decision that can affect both productivity and costs. The following are key considerations when selecting construction equipment: 1. **Standard Equipment Preference** -- Whenever possible, standard equipment should be selected, as it is typically more reliable and readily available. Standard machines often come with better support in terms of spare parts, service, and trained operators. 2. **Service at Low Cost** -- Equipment should be capable of providing high-quality service without excessive costs. It is crucial to balance the initial purchase price with the operational costs to ensure cost-effectiveness. 3. **Moderate Unit Production Cost** -- The equipment should be chosen based on its ability to deliver work at a reasonable unit cost of production. This metric can be calculated by considering the output of the equipment and its operating costs. 4. **Ease of Repair and Low Downtime** -- Equipment that is easy to repair minimizes downtime. Downtime can be costly, especially in projects with tight schedules. Equipment should have readily available spare parts and support for fast repairs. 5. **Disposability** -- Construction projects are often temporary, and the equipment may need to be sold or disposed of after the project ends. Equipment that retains good resale value or can be easily disposed of can reduce the financial burden. 6. **Project-Specific Requirements** -- Equipment should be capable of handling the specific demands of the job. For instance, a project requiring extensive excavation would benefit from choosing machines with high digging capacity. 7. **Multi-functionality** -- Choosing equipment capable of performing multiple tasks can optimize the fleet and reduce the need for multiple machines. For example, an excavator with an attachment for breaking concrete can eliminate the need for a separate breaker. 8. **Moderate Size and Complexity** -- Equipment of moderate size tends to have fewer moving parts, which can reduce wear and tear. Machines that are less complex and have fewer parts are easier to maintain, often resulting in lower operational costs and higher reliability. Construction equipment is central to the productivity and success of construction projects. Selecting the appropriate equipment, understanding its operations, and maintaining it well can significantly enhance project efficiency, safety, and profitability. The construction industry in the Philippines, for example, has embraced a wide range of equipment to meet the demands of rapid infrastructure development, highlighting the relevance of effective equipment management. By focusing on strategic equipment selection, operation, and maintenance, construction companies can ensure that they are well-equipped to handle current and future projects. **TYPES OF CONSTRUCTION EQUIPMENTS** Construction equipment is categorized into several types based on their primary functions, from earthmoving and material handling to compaction and paving. Each category serves specific purposes on construction sites, contributing to improved efficiency, productivity, and safety in the completion of construction tasks. The following are the different types of construction equipment, their uses, and their importance in the construction process: I. **Earth Moving Equipment** Earthmoving equipment comprises large, powerful vehicles designed to move, relocate, and manipulate substantial quantities of earth, rock, mud, dirt, and debris on construction sites. These machines are essential in preparing foundations, leveling terrain, and facilitating excavation. The primary types of earthmoving equipment include excavators, graders, loaders, backhoes, and bulldozers. Each type is tailored for specific functions on construction and mining sites. **Excavators** An excavator is a versatile piece of heavy equipment designed primarily for digging, but it can also move large objects, demolish structures, and even handle material transport on-site. Typically composed of two main parts---a cab mounted on a rotating platform and a powerful arm with various attachments---excavators are controlled by an operator seated in the cab. The arm, often equipped with a bucket, can perform a range of tasks, including trenching, lifting, and loading materials. Some models have specialized attachments, like hydraulic breakers or grapplers, which expand their applications in rock breaking, forestry, and waste handling. The rotating capability of the cab allows for 360-degree operation, making excavators highly efficient in confined spaces. **Graders** Graders, also known as motor graders, are mostly utilized in road construction projects. Their primary function is to create a flat surface by finely leveling the earth and redistributing material. Graders are essential for the construction and maintenance of dirt and gravel roads, as well as for achieving precise grading in roadbeds. They feature a long blade that can be adjusted to different angles for fine-tuning the surface, making them invaluable for grading surfaces before laying asphalt or other materials. Additionally, graders are often employed in the construction of foundations, slopes, and drainage ditches. **Loaders** Loaders are heavy equipment machines commonly seen in the construction industry, mainly used to transport and load materials onto trucks, conveyor belts, or other machinery. They are designed to scoop up materials like soil, rocks, gravel, demolition waste, and raw minerals. The loader's front-mounted wide bucket can be adjusted to gather loose material, making it a quick and efficient tool for transferring large quantities. Loaders come in various types, including wheel loaders, track loaders, and skid steer loaders, each suited for different site conditions and load requirements. **Backhoes** Backhoes, also known as rear actors or back actors, are multi-functional machines that consist of a digging bucket mounted on the end of a two-part articulated arm. Typically attached to a tractor or front loader, backhoes are versatile and suitable for medium-scale digging tasks, trenching, and moving soil. The operator can control both the bucket and the arm's movements, allowing for precision in digging tasks. Backhoes are particularly advantageous because of their ability to perform both loading and digging functions, which makes them useful for a variety of small-to-medium excavation tasks, especially in urban or restricted areas. **Bulldozers** Bulldozers are powerful, tracked machines equipped with a heavy-duty metal blade at the front. This blade, or "dozer," is used to push substantial quantities of soil, sand, and debris over short distances, primarily in site preparation, grading, and demolition. The machine's rear is often fitted with a ripper, a claw-like tool that breaks up hard, compacted materials for easier movement. Bulldozers are well-suited for rough terrain due to their track system, which distributes weight evenly and provides stability on soft or uneven ground. II. **Construction Vehicles** Construction vehicles play a critical role in transporting materials and debris on-site and moving supplies to different parts of the construction area. These vehicles are built to handle heavy loads, rough terrain, and the demands of construction projects. Common construction vehicles include tippers and trailers. **Tippers** Tippers, or dump trucks, are heavy-duty vehicles equipped with an open-box bed with hydraulic rams to lift the front, allowing materials to be dumped out the back. These vehicles are designed to transport and unload bulk materials, such as sand, gravel, and demolition debris, across construction sites. Tippers are essential for removing waste from excavation sites and transporting building materials to various parts of a project. Their ability to carry large loads and unload quickly makes them ideal for fast-paced construction and mining operations. **Trailers** Trailers are unpowered vehicles that must be towed by a powered vehicle, such as a truck. In construction, they are used to transport heavy machinery, materials, and other goods that are too large or numerous to be carried in traditional vehicles. Trailers come in various types and can be customized for specific needs, such as flatbeds for equipment transport or tank trailers for liquid transport. They provide a flexible solution for moving bulky or oversized items, contributing significantly to logistical efficiency on construction sites. III. **Material Handling Equipment** Material handling equipment encompasses machinery used to lift, move, and transport materials on construction sites, warehouses, and manufacturing facilities. This category includes cranes, conveyors, hoists, and forklift trucks, each tailored to handle heavy or bulk materials. **Cranes** Cranes are lifting devices used to move heavy objects vertically and horizontally across a job site. They come in various forms, such as tower cranes, mobile cranes, and overhead cranes, each suited to specific lifting and height requirements. Cranes are integral to projects involving high-rise construction, as they can hoist building materials to significant heights. Their stability, load-bearing capacity, and range of motion make them indispensable for assembling and positioning structural components. **Conveyors** Conveyors are mechanical systems that transport materials along a moving belt or roller path, ideal for transferring heavy or bulky items over short to medium distances. They are commonly used in construction and mining to move materials such as sand, gravel, and aggregate quickly and efficiently. Conveyors reduce manual labor requirements and streamline material flow, making them beneficial in both large-scale construction sites and smaller operations. **Hoists** Hoists are devices designed to lift and lower heavy loads using a drum or lift wheel around which a chain or rope wraps. Hoists are available in various forms, such as electric, manual, and hydraulic hoists, each suited to different lifting capacities and settings. They are especially valuable in confined spaces or where precise lifting control is required, such as during equipment installation or structural assembly. **Forklift Trucks** Forklift trucks are versatile material-handling machines commonly found in warehouses and construction sites. These vehicles come with lifting forks to hoist and transport materials, typically within a load capacity range of one to five tons. Forklifts can be customized with different attachments to increase their functionality, making them useful for a wide range of material handling tasks. IV. **Construction Site Equipment** Construction site equipment includes machinery and tools specifically designed to perform tasks like mixing, compacting, paving, and more. These machines reduce the need for manual labor, enhance productivity, and ensure precision in critical construction activities. **Cement Mixers** Cement mixers, or concrete mixers, are machines that blend cement, sand, gravel, and water to create concrete. The drum rotates, combining ingredients evenly, ensuring that the mixture is ready for pouring. Cement mixers come in different sizes, from portable units for small-scale projects to large trucks for high-volume production. They are indispensable in producing consistent and high-quality concrete on-site. **Compactors** Compactors are machines used to compress soil, gravel, or other materials to create a stable foundation for roads, buildings, and other structures. By compacting loose material, these machines increase soil density, reducing the likelihood of future settlement. Compactors vary in type, including plate compactors for small areas, roller compactors for larger surfaces, and tamping rammers for confined spaces. **Road Rollers** Road rollers are a type of compactor specifically designed for road construction. They flatten surfaces by applying pressure through large cylindrical drums, which can be filled with water or sand to increase weight. Road rollers help create a smooth, compacted surface, essential for laying asphalt or other road materials. **Pavers** Pavers are machines used to lay asphalt on roadways, bridges, and other surfaces. They are typically fed by a dump truck that pours asphalt into the paver's hopper. The paver spreads the material evenly and levels it to a specified thickness, making it ready for compaction. Pavers are essential for creating durable, smooth road surfaces and are widely used in highway and urban road construction. Construction equipment is diverse and specialized, each type designed to fulfill specific roles and contribute to the successful completion of construction projects. By selecting the right equipment, operators and construction managers can ensure efficiency, quality, and safety on site. From earthmoving to material handling and site-specific equipment, these machines are integral to modern construction and infrastructure development. **IMPORTANCE OF SKILLED OPERATORS** Operating heavy construction equipment requires specialized skills, in-depth training, and a comprehensive understanding of both machinery and safety protocols. Not everyone is suited to operate heavy machinery; it takes a combination of training, experience, and technical knowledge to ensure safe and efficient equipment operation. Skilled operators are essential in the construction industry and other sectors where heavy equipment is used, as their expertise contributes significantly to workplace safety, operational efficiency, productivity, and the overall quality of work. The following are various reasons why skilled operators are indispensable and the broader impact they have on projects, personnel, and the organization: I. **ENSURING WORKPLACE SAFETY** Safety is one of the most critical considerations on any construction site. Heavy equipment, such as excavators, bulldozers, cranes, and loaders, can be dangerous if not handled correctly. Inadequate training or a lack of experience in operating these machines can lead to accidents, injuries, and even fatalities. Skilled operators are trained not only in handling equipment but also in identifying potential hazards and following strict safety protocols. **Accident Prevention** Experienced operators understand how to control the equipment smoothly and are trained to recognize hazards specific to the machinery they use. Skilled operators perform pre-operation checks to ensure the equipment is in good working condition, reducing the likelihood of mechanical failures. They also have a deep understanding of the machine's limits, helping prevent incidents caused by overloading or using equipment in ways it wasn't designed for. **Adherence to Safety Protocols** Trained operators are familiar with site safety protocols and follow these guidelines rigorously. They know the correct procedures for emergency situations, how to secure equipment properly when not in use, and how to navigate around other personnel safely. With this knowledge, they contribute to a safer environment for everyone on site, not just those operating equipment. Skilled operators are also trained to communicate effectively with other team members to ensure that everyone is aware of ongoing operations, reducing the risk of collisions or accidents. **Compliance with Regulations** Many construction sites and industrial projects are subject to strict safety regulations. Skilled operators are trained to operate in compliance with these regulations, ensuring that the project meets local and national safety standards. By adhering to these regulations, companies reduce the risk of legal penalties, shutdowns, and reputation damage. II. **MAXIMIZING OPERATIONAL EFFICIENCY** Efficient operation of heavy equipment is crucial for the timely completion of construction projects. Skilled operators are not only capable of operating machinery accurately but are also trained in optimizing the machinery\'s capabilities, which improves the overall efficiency of the project. **Reduced Downtime** Skilled operators know how to avoid situations that could lead to mechanical wear, overuse, or equipment breakdown. This reduces downtime, which can be costly on a project with tight deadlines. An experienced operator will also know how to handle minor issues without causing further damage, enabling quick troubleshooting and problem-solving without the need to call for technical support. Reduced downtime directly translates to faster project completion and lower costs. **Higher Productivity** Skilled operators are adept at maximizing the machine's capabilities, allowing for quicker and more precise work. For example, a trained excavator operator can dig trenches or remove earth with greater speed and accuracy, while a skilled crane operator can position materials precisely and efficiently. By using equipment to its full potential, these operators ensure that each task is completed in the shortest time possible while maintaining quality, ultimately speeding up the project timeline. **Optimal Use of Resources** In construction, every hour of equipment uses costs money, whether it's fuel, labor, or machine wear. Skilled operators manage equipment in a way that minimizes fuel consumption and reduces wear and tear, helping to extend the lifespan of the machinery. They understand how to use just enough power for the task at hand, reducing unnecessary strain on the machine, which leads to savings in both maintenance costs and fuel expenses. III. **IMPROVING THE QUALITY OF WORK** Skilled operators significantly contribute to the quality of work on a project. Their precision and attention to detail ensure that tasks are performed to the required standards, reducing the likelihood of mistakes and rework. In construction, even small errors can lead to significant setbacks and increased costs, making precision a top priority. **Precision and Accuracy** Experienced operators can handle equipment with a high degree of control, allowing for precise adjustments during operations. This accuracy is essential for tasks like grading, trenching, and leveling, where even slight deviations can compromise the project's structural integrity or visual appeal. Skilled operators can perform these tasks with minimal corrections, ensuring that they meet design specifications the first time around. **Consistency in Work Quality** Skilled operators have a proven track record of delivering consistent, high-quality work. Their training and experience allow them to perform tasks in a reliable manner, ensuring uniform results throughout the project. This consistency contributes to the overall aesthetic and structural quality of the completed project, reducing the need for costly rework. **Attention to Detail** A trained operator is also skilled in assessing the finer details of a job. For example, they can notice if the ground is uneven while operating a grader or if soil is not compacted enough when using a roller. These small details, often overlooked by unskilled operators, can significantly affect the durability and longevity of the construction work. By paying close attention to such factors, skilled operators add an additional layer of quality assurance to the project. IV. **REDUCING LONG-TERM COSTS** While hiring skilled operators may initially seem more costly, their expertise results in long-term savings for the project. Skilled operators help reduce maintenance costs, lower fuel expenses, minimize downtime, and enhance equipment longevity, all of which contribute to significant cost savings over the course of a project. **Lower Maintenance Costs** Skilled operators understand how to handle machinery in ways that reduce wear and tear. By operating within the equipment's limitations, avoiding overuse, and conducting regular checks, they help prevent unnecessary damage. This approach leads to fewer repairs, extended machine life, and reduced maintenance costs over time. **Improved Fuel Efficiency** An experienced operator knows how to operate equipment in the most fuel-efficient manner. They can adjust their techniques to minimize fuel usage without sacrificing productivity. Over the span of a project, even a small reduction in fuel consumption can result in substantial cost savings, making skilled operators an asset to budget-conscious projects. **Increased Equipment Longevity** Proper operation reduces the strain on heavy machinery, allowing it to last longer and maintain performance over time. Skilled operators follow maintenance schedules, perform preventive care, and ensure that machinery is used as intended. This can extend the equipment\'s lifespan and delay the need for costly replacements, which is especially important on projects where the same equipment will be reused for multiple tasks or across different sites. V. **ENHANCING PROJECT REPUTATION AND CLIENT SATISFACTION** Projects completed with high-quality work, efficient use of resources, and strong safety records help build a positive reputation for the company. Skilled operators contribute to client satisfaction by ensuring that projects are completed on time, within budget, and to the highest standards. **Timely Project Completion** Skilled operators contribute to staying on schedule, allowing for timely project completion. By keeping operations smooth and efficient, they help prevent delays, which can be a crucial factor in client satisfaction. Timely delivery not only improves the company's reputation but also establishes trust and reliability in the eyes of clients. **Quality Standards and Reliability** A skilled operator's work reflects a commitment to quality, which directly influences the reputation of the construction company. When clients see that skilled operators have achieved results that meet or exceed industry standards, they are more likely to be satisfied with the outcome and to recommend the company for future projects. **Positive Workplace Culture** Skilled operators set a standard for professionalism on-site, which can positively impact the workplace culture. Their knowledge, adherence to safety, and efficiency can inspire other team members to uphold these standards. A positive workplace culture often leads to better teamwork, higher morale, and a more productive work environment, further contributing to the success of the project. The role of skilled operators cannot be overstated. Their expertise, precision, and commitment to safety directly contribute to the success of construction projects. By preventing accidents, maximizing operational efficiency, maintaining high-quality work, and reducing long-term costs, skilled operators provide value that goes far beyond their day-to-day tasks. Investing in skilled operators is an investment in the safety, efficiency, and quality of the entire project, ultimately leading to satisfied clients, enhanced company reputation, and a positive impact on the construction industry as a whole. **CONSTRUCTION EQUIPMENT PRODUCTIVITY** Construction equipment productivity is a crucial determinant of success for construction projects of all sizes, impacting everything from timelines and costs to quality and safety. It refers to the efficiency and effectiveness with which construction machinery such as excavators, loaders, cranes, and bulldozers performs its tasks on a worksite. High productivity in construction equipment means completing tasks within optimal timeframes and at minimal cost while maintaining the highest standards of quality and safety. With the continuous rise in infrastructure demands worldwide, particularly in developing nations, improving construction equipment productivity is more critical than ever. Effective use of machinery can mitigate delays, reduce overall project costs, and ensure a higher standard of work output. In countries like the Philippines, where rapid urbanization drives a demand for new roads, buildings, and public facilities, construction productivity has a direct effect on the economy's growth and development. However, achieving high productivity requires careful attention to a range of factors, including operator skill, equipment maintenance, and site conditions. I. **FACTORS AFFECTING CONSTRUCTION EQUIPMENT PRODUCTIVITY** Several interdependent factors influence the productivity of construction equipment. From the initial selection of machinery to operator skill and site layout, each factor plays a unique role in determining how effectively equipment performs. **Selection and Suitability of Equipment** Selecting the appropriate type and size of equipment for each specific task is a foundational element of productivity. Equipment that is either too large or too small for the job can lead to inefficiencies. For instance, using an oversized excavator for a light digging task can consume excessive fuel and cause unnecessary wear. Conversely, undersized equipment may need multiple passes, prolonging the task. Ensuring that equipment matches project requirements is essential for minimizing time and cost. **Operator Skill and Training** The productivity of construction equipment largely depends on the skill and experience of its operator. Well-trained operators know how to control machinery efficiently, optimizing speed, precision, and fuel consumption. They also know how to troubleshoot minor issues and make quick adjustments to avoid delays. For instance, a trained bulldozer operator can achieve the correct grading with fewer passes, which directly enhances productivity. **Site Conditions and Physical Layout** The conditions of the construction site significantly influence productivity. Soil type, weather, and the physical layout of the site affect how easily equipment can maneuver and perform tasks. For example, wet clay soil can slow down earthmoving activities, and narrow spaces in urban construction sites can make it challenging for larger equipment to operate efficiently. Planning the site layout to minimize movement and maximize equipment efficiency is essential to keeping productivity high. **Equipment Condition and Maintenance** Regular maintenance is vital to keep equipment in optimal working condition. Breakdowns and mechanical issues can lead to significant downtime, halting progress and increasing costs. Scheduled preventive maintenance, including regular inspections, lubrication, and timely part replacements, ensures machinery performs at its best. Proper maintenance routines reduce the risk of unexpected failures, extending the equipment\'s life and enhancing productivity. **Environmental and External Factors** Environmental conditions, such as temperature, rain, and humidity, can affect equipment performance and productivity. For instance, excessive heat may require equipment to be operated at a slower pace to prevent overheating. Rain and muddy conditions can delay excavation work and reduce the precision of tasks that require firm ground. External factors like supply chain delays for fuel and parts, along with regulatory compliance requirements, can also impact productivity. II. **STRATEGIES FOR ENHANCING CONSTRUCTION EQUIPMENT PRODUCTIVITY** Increasing equipment productivity involves a combination of training, maintenance, technology, and efficient planning. The following strategies are commonly employed to enhance productivity on construction sites. **Operator Training and Certification** Skilled operators are essential for maximizing productivity. Training programs should cover not only equipment operation but also fuel-efficient driving techniques, safety protocols, and minor troubleshooting skills. Certification ensures operators are familiar with equipment handling techniques that improve productivity and safety. **Preventive Maintenance Programs** Implementing preventive maintenance routines keeps equipment in peak condition, reducing the risk of breakdowns. Regular inspections, timely part replacements, and proactive repairs ensure machines remain operational and effective. Maintenance schedules can be adjusted based on usage intensity, environmental conditions, and manufacturer recommendations to keep machinery running smoothly. **Site Layout Optimization** A well-planned site layout reduces unnecessary movement and ensures equipment operates without interference. Strategic placement of loading zones, material storage, and parking areas reduces idle time and optimizes the movement of machinery. In congested urban sites, planning the layout to accommodate maneuvering space can prevent delays and improve safety. **Use of Telematics and GPS Technology** Telematics systems and GPS tracking provide real-time data on equipment location, fuel consumption, maintenance needs, and performance metrics. This data allows construction managers to optimize scheduling, monitor productivity, and make proactive adjustments. GPS tracking also aids in route planning, reducing travel time on large sites and ensuring that equipment is where it's needed most. **Automation and Advanced Technologies** Automated construction equipment, such as autonomous trucks and excavators, can complete tasks with high precision and consistency, which is particularly useful for repetitive tasks. Additionally, sensors and smart technology improve data collection and decision-making, allowing for productivity optimization. Although automation requires an upfront investment, it has the potential to reduce long-term costs and improve overall efficiency. **Effective Fuel Management** Fuel is a major operational cost in construction, so optimizing fuel usage can have a significant impact on productivity. Implementing fuel management strategies, such as regularly tracking consumption, using fuel-efficient equipment, and training operators on energy-efficient operation techniques, can reduce costs and improve sustainability. III. **CHALLENGES IN ACHIEVING HIGH CONSTRUCTION EQUIPMENT PRODUCTIVITY** Despite best efforts, the following are the several challenges that can limit construction equipment productivity: **High Initial Costs of Equipment and Maintenance** Modern construction equipment with advanced features is often expensive, and regular maintenance adds to operational costs. While high-quality equipment typically offers better productivity, the upfront costs can be prohibitive, especially for small to medium-sized contractors. **Shortage of Skilled Operators** The construction industry often faces a shortage of trained and skilled equipment operators. Without skilled personnel, equipment may be operated inefficiently or incorrectly, leading to productivity losses and higher maintenance costs. **Regulatory Compliance** Regulatory requirements around safety, emissions, and environmental impact are necessary but can also limit productivity. For example, noise regulations may restrict the use of certain equipment in residential areas during specific hours, while environmental regulations may impose delays for dust and emissions control. **Environmental and Weather Constraints** Extreme weather conditions, such as heavy rainfall, high humidity, and extreme heat, can affect machinery performance and operator safety, reducing productivity. Some sites may need to halt operations during adverse conditions, causing delays. Construction equipment productivity is a critical factor in project success, affecting timelines, costs, and overall quality. By understanding and optimizing the factors that influence productivity such as equipment selection, operator skill, site layout, and maintenance practices construction companies can improve efficiency, reduce downtime, and enhance project outcomes. While challenges such as high equipment costs, skilled labor shortages, and environmental constraints remain, the adoption of advanced technologies, efficient planning, and preventive maintenance can greatly enhance productivity. Effective management of construction equipment productivity contributes to meeting the demands of today's growing infrastructure needs, enabling faster, safer, and more cost-effective project completion. The productivity of construction equipment is a foundational component of construction project management. Through strategic investments and ongoing improvements, construction companies can meet growing demands and ensure sustainable success in an increasingly competitive industry. **CONSTRUCTION EQUIPMENT MAINTENANCE** In the construction industry, the performance and reliability of equipment are critical factors that can significantly impact project timelines, budgets, and safety. Equipment downtime due to breakdowns or malfunctions not only causes delays but can also increase costs and compromise the safety of workers. As such, maintaining construction equipment is essential to ensure its optimal performance, reduce operational risks, and extend its useful life. A comprehensive maintenance strategy, involving various techniques and practices, helps minimize the risk of failure and improve the overall efficiency of construction operations. This process involves several types of maintenance approaches tailored to the specific needs of equipment, as well as daily checks that ensure immediate readiness for operation. I. **IMPORTANCE OF EQUIPMENT MAINTENANCE** **Safety** Equipment failures can lead to accidents, putting the operator and others at risk. Proper maintenance ensures that critical safety systems, such as brakes, safety belts, and alarms, are functioning as intended, reducing the chances of accidents due to mechanical failure. **Longevity** Regular and effective maintenance prolongs the lifespan of construction equipment. By addressing minor issues before they escalate into major repairs, maintenance helps protect the investment in the machinery and ensures that it continues to perform optimally throughout its service life. **Availability** Well-maintained equipment is less likely to experience unexpected downtime. This increases its availability for use, which is crucial for keeping projects on schedule and avoiding costly delays. **Expenses** Neglecting equipment maintenance can lead to costly repairs and even replacements of major components. Proactive maintenance minimizes the likelihood of such expenses and helps optimize operational costs by improving fuel efficiency and reducing the need for emergency repairs. II. **TYPES OF MAINTENANCE** **Preventive Maintenance (PM)** Preventive maintenance aims to prevent equipment failures by identifying and addressing potential issues before they occur. This is typically done through regular inspections and scheduled tasks, such as oil changes, cleaning, and part replacements. Preventive maintenance follows a calendar-based approach, where activities are carried out at regular intervals, often multiple times per year, based on the manufacturer's recommendations. Example: In the Philippines, construction companies may implement a preventive maintenance schedule for bulldozers and excavators used in road construction projects, ensuring timely oil changes and regular inspections of critical components like hydraulic pumps and engines. **Condition-Based Maintenance (CBM)** Condition-based maintenance is a more advanced approach that focuses on monitoring equipment while it is in use. Instead of performing maintenance based on a fixed schedule, operators assess equipment performance through real-time data and observations. Maintenance is only performed when indicators, such as unusual noise or temperature fluctuations, signal potential issues. This method helps avoid unnecessary maintenance and reduces downtime. Example: A construction site in the Philippines may use condition-based maintenance for cranes, where sensors monitor key parts of the crane to detect any deviations from normal operating conditions, allowing maintenance to be performed only when necessary. **Predictive Maintenance (PDM)** Predictive maintenance uses technology to monitor equipment in real time. Sensor devices are installed on machinery to gather data on various parameters, such as vibration, temperature, and pressure. This data is then analyzed to predict when a component is likely to fail, allowing maintenance teams to take preventive action before a breakdown occurs. This approach reduces downtime and maximizes the efficiency of equipment. Example: On large-scale construction projects in the Philippines, predictive maintenance may be used for concrete pumps, where sensors collect data on pump performance, alerting operators to potential issues before the pump fails. **Corrective Maintenance** Corrective maintenance is typically initiated when equipment is found to be malfunctioning or breaking down while in operation. Unlike preventive or condition-based maintenance, corrective maintenance occurs in response to an unexpected issue, usually when the equipment is not functioning as expected. This approach is reactive, addressing issues as they arise, often under time pressure. Example: If a bulldozer experiences a hydraulic failure on a construction site in the Philippines, corrective maintenance will be required to repair or replace the faulty component and restore functionality. **Predetermined Maintenance** Predetermined maintenance is carried out based on guidelines and recommendations from the equipment manufacturer, typically after a thorough assessment of the equipment\'s operating conditions and performance. These guidelines often come in the form of charts or schedules, advising the maintenance team when to perform specific tasks like oil changes, filter replacements, and more. Example: A construction company in the Philippines might follow predetermined maintenance schedules for its backhoes, following the manufacturer's recommendation for regular inspections and component replacements based on usage hours. III. **DAILY MAINTENANCE CHECKS** Daily maintenance checks are essential to ensure that equipment is ready for use at the start of each workday. These checks involve a thorough visual inspection and functional testing of critical systems, helping to identify any immediate issues that could affect performance or safety. **Visual Inspection** Examine the exterior of the equipment for any signs of damage, such as cracks, dents, or loose parts. Also, check for leaks, including oil, fuel, and hydraulic fluid, as these could signal potential problems. **Fluid Levels** Check the oil levels in the engine, transmission, and hydraulic systems. Ensure that the fluid levels are within the recommended range, as low fluid levels can cause severe damage to components. **Tire Inspection** Check tire pressure and look for signs of wear or damage. Proper tire pressure is critical for safe operation and fuel efficiency, while worn or damaged tires can lead to safety hazards. **Brakes** Test the brakes to ensure they are functioning properly. This includes checking brake pads, brake fluid levels, and the overall responsiveness of the braking system. **Safety Features** Test critical safety features, such as seatbelts, horns, alarms, emergency stop buttons, and lights. These features are vital for protecting operators and other workers on the site. **Cleanliness** Ensure that the equipment is free of dirt, debris, and grease. Regular cleaning not only helps maintain the aesthetic condition of the equipment but also prevents the buildup of materials that could affect its operation. **Documentation** Keep detailed records of all inspections, maintenance activities, and any issues found. This documentation helps track the equipment's maintenance history and assists in planning future maintenance tasks. Regular and systematic maintenance of construction equipment is vital for ensuring the safety, efficiency, and longevity of machinery on construction sites. Whether through preventive, condition-based, predictive, corrective, or predetermined maintenance approaches, each method serves to address specific challenges faced by construction equipment operators. By conducting daily maintenance checks, addressing minor issues before they escalate, and following manufacturer recommendations, construction companies can avoid costly repairs, improve productivity, and ensure that their equipment remains in peak operating condition for the long term. Proper maintenance not only protects the machinery but also ensures the safety of the workforce and the timely completion of construction projects. **CONCLUSION: CONSTRUCTION EQUIPMENT OPERATIONS, PRODUCTIVITY, AND MAINTENANCE** In the construction industry, the efficient operation of equipment is fundamental to the success of any project. Properly maintained equipment not only ensures smooth operations but also enhances productivity, reduces downtime, and minimizes costs. Construction equipment operations, from heavy machinery like excavators to smaller tools, require skilled operators and careful management to maximize their potential and maintain safety standards. When equipment is well-maintained, it functions optimally, preventing breakdowns and improving the speed and efficiency with which tasks are completed. Productivity is directly linked to the condition of the equipment. Well-maintained machines operate faster, with fewer interruptions, and can handle more demanding tasks without frequent repairs. Implementing a robust maintenance strategy, which includes preventive, condition-based, predictive, and corrective maintenance, ensures that equipment is always in top shape and ready for use when needed. Regular daily checks and adherence to manufacturer guidelines further reduce the risk of costly downtime and equipment failure. Ultimately, the intersection of effective equipment operations, high productivity, and strategic maintenance is crucial for achieving construction project goals. By prioritizing maintenance, construction companies not only safeguard their assets but also enhance their operational efficiency, improve safety standards, and ensure that projects are completed on time and within budget. Proper equipment management is not just a technical necessity it is an essential part of ensuring overall project success.