Recording and Reporting Lecture Notes PDF
Document Details
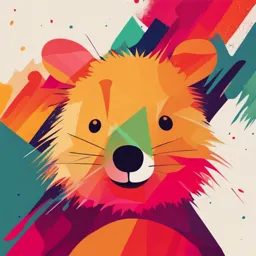
Uploaded by WellBalancedAsteroid
Tags
Related
- Bonita Springs Fire Control And Rescue District Standard Operating Procedures PDF
- SCADA Historical Configuration PDF
- Biological Functions Lec 1 Dr Faten Zahra PDF
- AUBF (Chapter 5) Chemical Examination of Urine PDF
- OOS Test Results for Pharmaceutical Production Guidance for Industry PDF 2022
- Quality System (Veterinary Medicine, BeniSuef University) PDF
Summary
This document explains rules and procedures for recording and reporting data, possibly in quality control settings. It details the importance of accurate data and appropriate documentation. Forms should be easy to use and follow guidelines for corrections, audits, and archiving.
Full Transcript
Recording and reporting 1 Introduction / Importance This chapter deals with the construction of various types of forms and reports that could be used by the QA/QC department for recording and reporting information. We have in other lectures explained the various re...
Recording and reporting 1 Introduction / Importance This chapter deals with the construction of various types of forms and reports that could be used by the QA/QC department for recording and reporting information. We have in other lectures explained the various reports. The structure of Reports and forms are not cast in stone but is adapted to suit the firms requirements, product and process. We’ll provide certain rules that apply to the completion and recording of data and information on these forms. 2 Rules for forms No blank areas on forms Analysts to initial/sign each completed entry for traceability of analyses. No Tippex to be used. Incorrect recorded results to be “deleted“ by a line drawn across the result and the correct result be entered in close proximity. The corrected result to be initialled/signed by the analyst. All entries to be recorded using a blue or black pen. Audited results to be entered using a green pen. Recording of results using any indelible ink/pencil is not allowed. Completed forms to be signed off by the supervisor. Any action relating to incorrect records to be clarified in the comments column. All forms to be appropriately dated. The time when analyses were completed and recorded to be duly entered in relation to the result. Create forms that are easy to use. Limit forms to one page if possible or group products together in terms of product/factory types. Areas where tests are not done on specific products must be blocked out. Forms must be kept for at least the shelf-life of the product and archived according to a SOP. (Explained in ISO 9000) 3 Any Questions ? THE END 4