Engineering Designs, Principles, Applications, and Operations of DOST-Developed Freeze Dryer PDF
Document Details
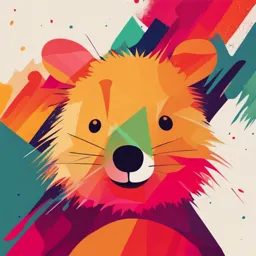
Uploaded by SimplerChrysoprase2916
null
Adrian C. Flores
Tags
Summary
This document provides a detailed description of a DOST-developed freeze dryer, including its components, specifications, and operational procedures. It covers topics like the design principles, applications, and operation of the freeze dryer, including its parts and functions.
Full Transcript
Engineering Designs, Principles, Applications and Operations of DOST Developed Freeze Dryer Adrian C. Flores, RME, LPT, RMP, MSMfgE Program Chair, Mechanical Engineering Department HITS Developed Freeze Dryer Descriptions The DOST HITS developed freeze dryer is equipped with 2 horsepower vacu...
Engineering Designs, Principles, Applications and Operations of DOST Developed Freeze Dryer Adrian C. Flores, RME, LPT, RMP, MSMfgE Program Chair, Mechanical Engineering Department HITS Developed Freeze Dryer Descriptions The DOST HITS developed freeze dryer is equipped with 2 horsepower vacuum pump that can pull down the operating pressure to less than 300 Pascals (Pa) and 1 horsepower compressor to provide a temperature of less than – 20 degree Celsius in the condensing chamber. The unit is designed with 5-layer trays with a maximum condensing capacity of 4 Liters of condensing rate of approximately 3 Liters/24 hours depending on the properties of materials being freeze dried. It is also equipped with digital Pirani gauge that can monitor the actual operating pressure inside the chamber as part of the instrumentations for process control. Water Phase Change Processes Review Main Components of Freeze Dryer Item Component Use No. Vacuum drying 1 chamber with Where the main drying occurs heating device To remove the water vapor Ice Condensing 2 from the vacuum chamber then Chamber changes the vapor to ice To measure the vacuum 3 Pirani Gauge pressure inside the chamber To evacuate the air and water 4 Vacuum Pump vapor Main Components of Freeze Dryer Item Component Use No. To provide refrigeration to the 5 Condensing Unit system Where the switches, controls and 6 Control Panel displays are located Type – K Use to measure the temperature of 7 Thermocouple the trays inside the chamber Use to let the air enter the chamber 8 Relief Valve after drying and make pressure inside back to atmospheric pressure To drain the water in the ice 9 Drain Valve condensing chamber Technical Specifications Refrigeration System Ice Condenser Approximately – 20 Temperature degree Celsius Maximum Vapour 3 Liters Condensing Capacity Shelf Temperature 10 to 60 degree Celsius Range Compressor Power 1 hp Refrigerant R 404A Condensing Rate 3 Liters/24 hours Freeze Dryer Components Arrangement and Connections Technical Specifications Vacuum Pump Vacuum Pump 2 hp Power Operating 100 – 300 Vacuum Pascals (Pa) Pressure Vacuum Pull – 15 minutes Down Time (min) Technical Specifications Electric Heater (5) 120 W Capacity Approximate Dimensions Width 0.95 m Length 1.0 m Height 1.6 m Technical Specifications Tray Dimension (5 pcs) 300 mm x 500 mm Approximate Weight 300 kgs Electrical Controls Pressure Gauge Pirani Gauge Temperature Sensor Type – K Thermocouple Standard Voltage 220 VAC Defrost Method Natural General Procedure: Heat is added by means of the electric heater attached to the trays. Sublimation will occur because of the energy added. General Procedure: Due to the continuous operation of the vacuum pump, water vapor is generated that goes to the condensing chamber that will then be turned into ice by the condensing coils. The condensing coils are connected to a separate refrigeration system. General Procedure: It is important to take note that the water vapor generated during the drying phase is not pumped off by the vacuum pump but collects in the ice condenser (condensing coils). General Procedure: The purpose of the vacuum pump is to lower the partial pressure of the non – condensable gasses so that the water vapor can be transported from the product to the ice condenser. General Procedure: However, small quantities of water vapor are also pumped off by the vacuum pump. Therefore, the vacuum pump is equipped with a gas ballast device. The collected ice on the surface of the condensing coils will be defrosted naturally. The water will then be drained by opening the drain valve. Freeze Dryer: Parts and Functions Familiarization Vacuum Drying Chamber - where the freeze drying occurs Subcomponents: Sight Glass Product Trays Tray Support Electric Heaters Type – K Thermocouple Seal/O – ring Vacuum Relief Valve Sight Glass - Attached to the front cover for viewing the inside of the main chamber - Material: Polycarbonate Glass Product Trays - Where product to be freeze dried are placed - Material: SS304 - Dimensions (LxW): 500mm x 300mm Tray Support - Attached inside the main chamber to support the trays and heaters - Material: SS304 Type – K Thermocouple - To measure the temperature of the heating trays Seal/O - ring - To ensure the sealing and prevent leakage in the vacuum chamber - Material: Viton Vacuum Relief Valve - Used to increase pressure inside the vacuum chamber Ice Condensing Chamber Assembly - Used to evacuate the water vapor from the vacuum chamber then change the vapor to ice Subcomponents: Chamber Front and Back Cover Sight Glass Seal/O – rings Insulation Drain Valves Chamber - Cylindrical shape vessel - Material: SS304 - Covered by insulation foam Front and Back Cover - Dome – shaped with flange - With holes for the attachment of sight glass Sight Glass - Attached on the front and back cover for viewing the inside of the chamber Seal/O – ring - To ensure the sealing and prevent leakage in the ice condensing chamber - Material: Viton Insulation - Used to insulate the vacuum chamber - Wrapped around the chamber and the covers - Material: Insulation Foam Drain Valve - Used to drain the water in the ice condensing chamber after using the equipment Pirani Gauge - To measure the vacuum pressure inside the chamber - Pressure range: 0.05 – 101325 Pa Vacuum Pump - Used to evacuate air and water vapor in the system - Comes with VFD to convert the 3-phase pump to a single phase - Type of Pump: Oil Sealed Rotary Vacuum Pump Pumping Speed: 10 cubic meter per hour Oil Capacity: 1.0 – 2.5 Liters Motor Power: 1.5 kW - Important Parts Oil Mist Trap Gas Ballast Valve Oil Level Gauge Oil Mist Trap - Reduces Noise - Reduce oil mist coming out from the pump Gas Ballast Valve - Admits air into the pump preventing liquefication of the water vapor that got into the pump Refrigeration System - To provide refrigeration to the ice condensing chamber - Subcomponents Condensing Unit (Compressor and Condenser) Receiver Pressure Gauge Condensing Unit - Composed of compressor and condenser Compressor - increase the pressure of refrigerant that will enter the condenser Condenser - where heat is released Receiver - Used to store liquid refrigerant after it leaves the condenser Pressure Gauge - To measure the operating pressure in the evaporator and condenser Pipe Connection (Ball Valve) - Used to disconnect the flow of vapor in the vacuum chamber to the other parts of the system Control Panel - Holds the control circuit elements switches and light indicators