Electric Machines PDF
Document Details
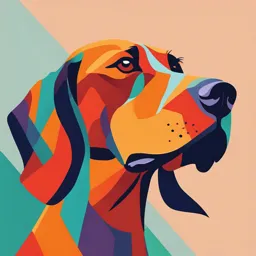
Uploaded by FineTheme
2010
D P Kothari and I J Nagrath
Tags
Related
- DC Machinery Fundamentals Chapter 7 PDF
- Elektromagnetische Energiewandlung - Universität Bremen - PDF
- Special Electric Machines Lecture Notes PDF
- CEE - Máquinas de Indução Trifásicas - 2023-2024 PDF
- Battery Electric Machine Systems Fundamentals PDF
- Battery Electric Machine (BEM) Systems Products Review PDF
Summary
This textbook, "Electric Machines", 4th edition, by D P Kothari and I J Nagrath, provides a comprehensive overview of electric machine principles and applications. It covers topics such as magnetic circuits and induction, transformers, electromechanical energy conversion, and rotating machines, along with case studies on AC and DC machines.
Full Transcript
Contents i ii Contents D P Kothari is presently Vice Chancellor of VIT University, Vellore. He obtained a BE (Electrical) in 1967, ME (Power Systems) in 1969 and PhD in 1975 from the Birla Institute of Technology and Science...
Contents i ii Contents D P Kothari is presently Vice Chancellor of VIT University, Vellore. He obtained a BE (Electrical) in 1967, ME (Power Systems) in 1969 and PhD in 1975 from the Birla Institute of Technology and Science (BITS) Pilani, Rajasthan. From 1969 to 1977, he was involved in teaching and development of several courses at BITS Pilani. Prior to his assuming charge as Vice Chancellor of VIT University, Dr Kothari served as Director In-charge and Deputy Director (Administration) as well as Head Centre for Energy Studies at Indian Institute of Technology, Delhi; and as Principal, Visvesvaraya Regional Engineering College, Nagpur. He was Visiting Professor at the Royal Melbourne Institute of Technology, Melbourne, Australia, during 1982–83 and 1989 for two years. He was NSF Fellow at Purdue University, US in 1992. Dr Kothari, who is a recipient of the Most Active Researcher Award, has published and presented 625 research papers in various national as well as international journals, conferences, guided 30 PhD scholars and 63 MTech students, and authored 21 books in Power Systems and other allied areas. He has delivered several keynote addresses and invited lectures at both national and international conferences on Electric Energy Systems. He has also delivered 42 video lectures on science and technology on YouTube with a maximum of 35,000 hits! Dr Kothari is a Fellow of the Indian National Academy of Engineering (FNAE), Fellow of Indian National Academy of Sciences [FNASc], Fellow of Institution of Engineers (FIE) and Senior Member, IEEE. His many awards include the National Khosla award for Lifetime Achievements in Engineering for 2005 from IIT Roorkee. The University Grants Commission (UGC), Govt. of India, has bestowed the UGC National Swami Pranavananda Saraswati award for 2005 on Education for his outstanding scholarly contributions. He is also a recipient of the Lifetime Achievement Award (2009) by the World Management Congress, New Delhi, for his contribution to the areas of educational planning and administration. His fields of specialization are Optimal Hydro-thermal Scheduling, Unit Commitment, Maintenance Scheduling, Energy Conservation (loss minimization and voltage control), Power Quality and Energy Systems Planning and Modelling. I J Nagrath is Adjunct Professor, BITS Pilani, from where he retired in July 1999 as Professor of Electrical Engineering and Deputy Director. He is now actively engaged in writing books related to his long teaching and research experience. He obtained his BE with Honours in Electrical Engineering from Birla Engineering College in 1951 and MS from the University of Wisconsin, USA in 1956. He has co-authored several successful books which include Electric Machines, 3/e, Modern Power System Analysis, Power System Engineering, Signals and Systems, Electrical Machines, Sigma Series and has authored Basic Electrical Engineering (all published by TMH). He has also co-authored Control System Engineering and authored Electronics: Analog and Digital. Besides he has these, published several research papers in prestigious national and international journals and continues to be active in studies and writing. Contents iii D P Kothari Vice Chancellor Vellore Institute of Technology (VIT) Vellore, Tamil Nadu I J Nagrath Adjunct Professor Birla Institute of Technology and Science (BITS) Pilani, Rajasthan Tata McGraw Hill Education Private Limited NEW DELHI New Delhi New York St Louis San Francisco Auckland Bogotá Caracas Kuala Lumpur Lisbon London Madrid Mexico City Milan Montreal San Juan Santiago Singapore Sydney Tokyo Toronto iv Contents Tata McGraw-Hill Published by the Tata McGraw Hill Education Private Limited, 7 West Patel Nagar, New Delhi 110 008. Electric Machines, 4/e Copyright © 2010, 2004, 1997, 1985, by Tata McGraw Hill Education Private Limited. MATLAB® is a registered trademark of The MathWorks, Inc., 3 Apple Hill Drive, Natick, MA 01760-2098 No part of this publication may be reproduced or distributed in any form or by any means, electronic, mechanical, photocopying, recording, or otherwise or stored in a database or retrieval system without the prior written permission of the publishers. The program listings (if any) may be entered, stored and executed in a computer system, but they may not be reproduced for publication. This edition can be exported from India only by the publishers, Tata McGraw Hill Education Private Limited. ISBN (13): 978-0-07-069967-0 ISBN (10): 0-07-069967-4 Managing Director: Ajay Shukla Head—Higher Education Publishing and Marketing: Vibha Mahajan Manager—Sponsoring: SEM & Tech. Ed.: Shalini Jha Assoc. Sponsoring Editor: Suman Sen Development Editor: Manish Choudhary Executive—Editorial Services: Sohini Mukherjee Sr. Production Manager: P L Pandita Dy. Marketing Manager—SEM & Tech. Ed.: Biju Ganesan General Manager—Production: Rajender P Ghansela Asst. General Manager—Production: B L Dogra Information contained in this work has been obtained by Tata McGraw-Hill, from sources believed to be reliable. However, neither Tata McGraw-Hill nor its authors guarantee the accuracy or completeness of any information published herein, and neither Tata McGraw-Hill nor its authors shall be responsible for any errors, omissions, or damages arising out of use of this information. This work is published with the understanding that Tata McGraw-Hill and its authors are supplying information but are not attempting to render engineering or other professional services. If such services are required, the assistance of an appropriate professional should be sought. Typeset at Tej Composers, WZ-391, Madipur, New Delhi 110063, and printed at S P Printers, 30A, Patpar Ganj Village, Delhi - 110091. Cover Printer: S P Printers DZXBCRAZDRXAQ The McGraw-Hill Companies Contents v Dedicated to Shobha — D P Kothari and Pushpa — I J Nagrath vi Contents Contents vii Preface xiii 1. Introduction 1 1.1 Introduction 1 1.2 Basic Principle, Types and Constructional Features of Electric Machines 3 1.3 Recent Trends in Research and Developments in Electric Machines 7 2. Magnetic Circuits and Induction 12 2.1 Introduction 12 2.2 Magnetic Circuits 12 2.3 Magnetic Materials and Their Properties 25 2.4 Magnetically Induced EMF and Force 27 2.5 AC Operation of Magnetic Circuits 31 2.6 Hysteresis and Eddy-Current Losses 33 2.7 Permanent Magnets 35 2.8 Application of Permanent Magnet Materials 40 Summary 42 Practice Problems 43 Review Questions 47 3. Transformers 48 3.1 Introduction 48 3.2 Transformer Construction and Practical Considerations 49 3.3 Transformer on No-Load 54 3.4 Ideal Transformer 58 3.5 Real Transformer and Equivalent Circuit 62 3.6 Transformer Losses 71 3.7 Transformer Testing 72 3.8 The Per Unit System 80 3.9 Efficiency and Voltage Regulation 82 3.10 Excitation Phenomenon in Transformers 91 3.11 Autotransformers 94 3.12 Variable Frequency Transformer 97 viii Contents 3.13 Three-Phase Transformers 101 3.14 Parallel Operation of Transformers 116 3.15 Three-Winding Transformers 120 3.16 Phase Conversion 124 3.17 Tap Changing Transformers 127 3.18 Voltage and Current Transformers 131 3.19 Audio-Frequency Transformer 135 3.20 Grounding Transformer 136 3.21 Welding Transformer 136 3.22 Transformer as a Magnetically Coupled Circuit 137 Summary 146 Practice Problems 148 Review Questions 156 Multiple-Choice Questions 157 4. Principles of Electromechanical Energy Conversion 158 4.1 Introduction 158 4.2 Energy in Magnetic System 158 4.3 Field Energy and Mechanical Force 162 4.4 Multiply-Excited Magnetic Field Systems 176 4.5 Forces/Torques in Systems with Permanent Magnets 184 4.6 Energy Conversion via Electric Field 187 4.7 Dynamical Equations of Electromechanical Systems 190 Summary 193 Practice Problems 194 Review Questions 196 5. Basic Concepts in Rotating Machines 197 5.1 Introduction 197 5.2 Elementary Machines 198 5.3 Generated EMF 205 5.4 MMF of Distributed ac Windings 216 5.5 Rotating Magnetic Field 223 5.6 Torque in Round Rotor Machine 230 5.7 Operation of Basic Machine Types 234 5.8 Linear Machines 245 5.9 Magnetic Leakage in Rotating Machines 247 5.10 Losses and Efficiency 250 5.11 Rating and Loss Dissipation 255 5.12 Matching Characteristics of Electric Machine and Load 261 Contents ix 5.13 Resume 263 Summary 263 Practice Problems 266 Review Questions 270 Multiple-Choice Questions 272 6. AC Armature Windings 273 6.1 Introduction 273 6.2 AC Windings 275 Summary 283 Practice Problems 283 Review Questions 284 7. DC Machines 285 7.1 Introduction 285 7.2 Armature Winding and Commutator 287 7.3 Certain Observations 301 7.4 EMF and Torque 301 7.5 Circuit Model 305 7.6 Armature Reaction 310 7.7 Compensating Winding 316 7.8 Commutation 318 7.9 Methods of Excitation 322 7.10 Operating Characteristics of dc Generator 326 7.11 Self-Excitation 332 7.12 Characteristics of dc Generators 335 7.13 Shunt Generator–Predetermination of External Characteristic 339 7.14 Parallel Operation of dc Generators 357 7.15 Characteristics of dc Motors 361 7.16 Starting of dc Motors 382 7.17 Speed Control of dc Motors 390 7.18 Braking of dc Motors 408 7.19 Efficiency and Testing 410 7.20 Testing of dc Machines 412 7.21 DC Machine Dynamics 423 7.22 Permanent Magnet dc (PMDC) Motors 426 7.23 DC Machine Applications 430 Summary 431 Practice Problems 433 Review Questions 441 Multiple-Choice Questions 442 x Contents 8. Synchronous Machines 444 8.1 Introduction 444 8.2 Basic Synchronous Machine Model 445 8.3 Circuit Model of Synchronous Machine 451 8.4 Determination of the Synchronous Reactance 454 8.5 MMF Method 462 8.6 Determination of Armature Reaction Ampere-Turns and Leakage Reactance of a Synchronous Machine—Potier Method 465 8.7 ASA (American Standards Association) Method (Latest) 473 8.8 Nature of Armature Reaction 475 8.9 Synchronizing to Infinite Bus-Bars 476 8.10 Operating Characteristics 478 8.11 Efficiency of Synchronous Machines 494 8.12 Power Flow (Transfer) Equations 497 8.13 Capability Curve of Synchronous Generator 518 8.14 Salient-Pole Synchronous Machine Two-Reaction Model 521 8.15 Staying in Synchronizm – The Synchronizing Power (Torque) 536 8.16 Determination of XD And XQ —Slip Test 543 8.17 Parallel Operation of Synchronous Generators 545 8.18 Hunting in Synchronous Machines 549 8.19 Starting of Synchronous Motors 554 8.20 Short-Circuit Transient in Synchronous Machine 555 8.21 Single-Phase Synchronous Generators 563 8.22 Brushless DC Motors 575 Summary 582 Practice Problems 585 Review Questions 590 Multiple-Choice Questions 591 9. Induction Machine 593 9.1 Introduction 593 9.2 Construction 593 9.3 Flux and MMF Waves in Induction Motor—Principle of Operation 596 9.4 Development of Circuit Model (Equivalent Circuit) 601 9.5 Power Across Air-Gap, Torque and Power Output 605 9.6 Tests to Determine Circuit-Model Parameters 614 9.7 The Circle Diagram (Approximate) 630 9.8 Starting 638 9.9 Cogging and Crawling 645 9.10 Speed Control 647 9.11 Deep-Bar/Double-Cage Rotor 663 Contents xi 9.12 Classes of Squirrel-Cage Motors 666 9.13 Induction Generator 667 9.14 Induction Machine Dynamics: Acceleration Time 670 9.15 Inverted Induction Machine 685 9.16 High Efficiency Induction Motors 687 9.17 Linear Induction Motor (LIM) 688 Summary 691 Practice Problems 694 Review Questions 699 Multiple-Choice Questions 701 10. Fractional Kilowatt Motors 702 10.1 Introduction 702 10.2 Single-Phase Induction Motors 702 10.3 Single-Phase Synchronous Motors 722 10.4 Circuit Model of Single-Phase Induction Motor 725 10.5 Balanced 2-Phase Motor Fed from Unbalanced Supply 734 10.6 Stepper Motors 740 10.7 Series Motor—Universal Motor 746 Summary 751 Practice Problems 752 Review Questions 752 11. Generalised Theory of Electrical Machines 753 11.1 Introduction 753 11.2 Convention 753 11.3 Basic Two-Pole Machine 753 11.4 Transformer with a Movable Secondary Winding 755 11.5 Kron’s Primitive Machine 757 11.6 Linear Transformations in Machine 758 11.7 Three-Phase to Two-Phase (a, b, c To a, b. 0) Transformation 761 11.8 Rotating Axis (a, b. 0) to Stationary Axis (d, q, 0) Transformation 762 11.9 Physical Concepts of Park’s Transformation 765 Review Questions 766 12. Motor Control by Static Power Converters 767 12.1 Introduction 767 12.2 Solid State Devices 769 12.3 Electrical Drives 782 12.4 Power Converters 783 12.5 Thyristor Motor Control 785 xii Contents 12.6 DC Motor Control Through Converters 786 12.7 DC Motor Control Through Choppers 800 12.8 Converter Topologies for dc Motor Drives 811 12.9 AC Motor Control 813 12.10 Inverters 819 12.11 Forced Commutation 828 12.12 Vector Control of an Induction Motor 831 Summary 837 Practice Problems 837 Review Questions 839 Multiple-Choice Questions 839 Appendix I: AC Steady-State Circuit Analysis 841 Appendix II: Three-Phase Systems 851 Appendix III: Special Topics in Transformers 863 Appendix IV: Cross-Field Machines 866 Appendix V: AC Commutator Machines 869 Appendix VI: Resistance 875 Appendix VII: Sample Examples Solved Using Matlab 877 Appendix VIII: Table of Constants and Unit Conversion 891 References 892 Answers to Problems 897 Index 907 Contents xiii The aim of this book is to give deep exposition of the theory of electromechanical devices, with specific emphasis on the theory of rotating electric machines. The basic concepts have remained more or less the same over the years since the first edition of this text appeared in 1985. Since the appearance of the third edition in 2004, most of the advances in the application and control of electric machines have taken place owing to the further breakthroughs in power electronics and microprocessor/computer-based control systems. As a result, a much broader spectrum of electric machine types are now available. Particularly, permanent-magnet and variable-reluctance machines are now used in many applications and this is bound to increase further in future. AC drives are becoming more and more attractive in many applications, such as those requiring variable speed and flexible control, while earlier dc machines were the only choice. Realising this fact, these machine types find increased coverage in the fourth edition. This book presents simple, explicit, and yet rigorous and comprehensive treatment of transformers and electric machines in a single volume. Considerable emphasis is laid on the fundamentals, physical concepts, principles and on rigorous development of circuit model equivalents of both transformers and machines. Each circuit model is closely related to the physical reality, the underlying assumptions are sharply focussed and consequent limitations on the range of operation over which the model is valid are fully explained. The clarity of the physical basis of models developed would be most satisfying to the reader and it would enable him to make intelligent use of the models in the solution of machine problems and in the design of systems using these devices. The prediction of device performance follows as an immediate sequel to its model. Furthermore, as a next step (not covered in this book), the circuit parameters could be conveniently related to the physical dimensions and properties of the materials used in the device. While the circuit theory approach to electro-mechanical devices is introduced early in Chapter 2, the machine analysis in the bulk of the book follows the field-theory approach which, as is well-known, is better understood and appreciated by undergraduates and provides a deep insight into and a clear understanding of the electric machine. This is the only book which clearly brings home to the reader the distinction in the sign convention between the synchronous machine model and the transformer-type model, also employed for the induction machine. Another distinguishing feature of the book is the clarity with which it brings out the difference between a sinusoidally spaced distributed quantity (field) represented as a vector and sinusoidally time- varying quantities represented as phasors and how a rotating vector creates a time phasor. In order that the teacher and student can both make convenient use of symbols on the blackboard or on paper, the phasors are symbolically represented by capital letters with superbars and the vectors are represented by capital letters with superarrows. The book covers all the essential ingredients of machine knowledge expected of a modern-day undergraduate in electrical engineering. With new and vital topics crowding the curriculum in electrical engineering, machine courses have rightly been squeezed into two time slots of one-semester duration each. xiv Contents Preface The book is designed to meet this need. The book is primarily designed to cater to a one-semester core course common for all engineering disciplines and a one-semester topping off course for those majoring in electrical engineering. The core course may comprise Chapters 1, 2, Secs 3.1 to 3.9 (except Sumpner’s test), 3.11, 3.12 (partly), Chapters 4,5 and Secs 7.1 to 7.4 for dc machine coverage along with a quick resume of armature reaction, commutation, methods of excitation and characteristics of generators and motors. These topics are covered in initial portions of the relevant sections of Chapter 7. The dc machine winding can be explained to the class by merely projecting the two developed winding diagrams of Chapter 6. The remaining portions of the book would then comprise the second course. The book is written in a flexible style and a high degree of selectivity is inbuilt so that the teacher may leave out advanced articles of various topics in coping with the time factor without any loss of continuity. It is even possible to select a single one-semester course out of the book where time exigencies so demand. The theory and applications of various machines as control-system actuators is treated at appropriate places in the book. The methods of control-system analysis have not been included as these form a full course in a modem curriculum. Linear approximations are employed for tackling non-linearities associated with most machines. Wherever warranted, the effect of magnetic nonlinearity is accounted for in steady-state analysis. Although the models advanced are strictly applicable for steady-state analysis of device performance, these are extended to the dynamic case at a few places by making strong assumptions. The transient analysis of the synchronous machine is treated qualitatively and a graphical picture of the phenomenon is presented. The reader is expected to have a prior grounding in electricity and magnetism, introductory circuit theory, basic mechanics and elementary differential equations. However, appendices on ac steady-state circuit analysis and three-phase systems have been included for ready reference. New to this Edition The chapters on dc machines and synchronous machines are re-written completely. The highlights of this edition are large number of solved problems and practice problems that have been added in all the chapters. The key features of this edition are ∑ New chapter on ‘Generalized Theory of Electric Machines’ ∑ Detailed description of Transformers, dc Machines, dc Machines Excitation, Predetermination of external characteristics of dc Generator, Parallel operation of dc Generators, Efficiency and Testing of dc Machines, Speed control of Induction Motor, Linear Induction Motor ∑ Enhanced coverage of Permanent Magnet dc Motors, Permanent Magnet Materials and their applications ∑ Discussion on Silicon Controlled Rectifier (SCR), Insulated Gate Bipolar Transistor (IGBT), MOS Turn off Thyristor (MTO) and Emitter Turn off Thyristor (ETO) to cover new trends ∑ Synchronous generator (alternator), MMF Method, ASA Method, V curves and inverted V curves, Rating of alternator, phasor diagrams, Reactive power flow from generator ∑ MATLAB examples to facilitate problem-solving skills ∑ Excellent pedagogy including Contents Preface xv Though no sophisticated knowledge of mathematics is required for the reader of this book, the mathematics involved in this subject at times can get messy and tedious. This is particularly true in the analysis of ac machines in which there is a significant amount of algebra involving complex numbers. One of the significant positive developments in the recent years is the widespread availability of software such as MATLAB which greatly facilitates the solution of such problems. MATLAB is freely used in many institutions and colleges and is also available in a student version (http://www.mathworks.com). This edition, therefore, incorporates MATLAB in some sample solved examples. It should be emphasized here that the use of MATLAB is not a prerequisite for using this book. It is just an enhancement, an important one though! Further, it may be noted that even in the cases where it is not specifically suggested, some of the problems in the book can be attempted using MATLAB or an equivalent program. Some additional programs for solving problems using MATLAB are included in this book. The introductory chapter discusses electrical–electrical and electromechanical energy conversion processes and devices from a general point of view with the explicit purpose of motivating the reader for studying transformers and electric machines. This chapter, however, is not a prerequisite for the rest of the book. Chapter 2 brushes up magnetic circuits and the principle of induction. In Chapter 3, the transformer is treated exhaustively. The circuit-model approach is emphasized and for obvious reasons the role of the phasor diagram is underplayed. This chapter lays the ground work for the understanding of electromechanical energy conversion processes in machines and the circuit model of the induction machine in particular. Then follows Chapter 4 on the underlying principles of electromechanical energy conversion in the end of which is answered the question, “Why is electric field not used as a coupling medium instead of the magnetic field?” Cases of both linear and nonlinear magnetization (saturation) are treated. Exposition of the basic concepts of rotating machines from a generalized point of view as well as engineering aspects, such as cooling, rating and load mechanics is advanced in Chapter 5. General expressions for emf and torque are derived. The torque production is explained here via interaction of two magnetic fields assumed to be sinusoidally distributed. An alternative current-sheet approach is also given for the interested reader. Elementary treatment of specific machine types—synchronous and induction—then follows and their important characteristics are visualized on a field-interaction basis. Since interacting fields are assumed to be sinusoidal, which is justified in these two classes of machines only, a most rudimentary treatment of the de machine is given here because the fields in this class of machines are essentially nonsinusoidally distributed. While Chapter 5 gives the essential treatment of ac windings, the details including important practical features are dealt with in Chapter 6 devoted entirely to ac windings. Also given is a reasonably detailed account of dc armature windings in Chapter 7. Where time is a limiting factor, ac winding details can be skipped and dc winding directly introduced via the two developed diagrams with a brief explanation of parallel paths, commutation and brush location. Chapters 7–9 cover in depth the three basic machine types—the dc machine, synchronous machine and induction machine. The approach adopted in all the three is one of rigorous modelling with due stress on explanation of the underlying assumptions. The dc machine is the first to be dealt with as its steady-state model is the simplest. The modelling in each machine results in a circuit model of the linear kind by virtue of the assumptions made, which for all practical purposes are quite valid for steady-state performance analysis as well as under certain transient situations. In Chapter 8, on the synchronous machine, a heuristic methods are advanced to account for the effect of strong magnetic nonlinearity on the machine performance. xvi Contents Preface Tests to determine circuit-model parameters are advanced at appropriate places. Assumptions involved in machine modelling are once again stressed at this stage. Once the circuit model of the machine has been arrived at, the discussion is then focussed on power flow and operating characteristics. The constructional features and important practical details are included at suitable places and the circumstances under which a particular machine would be employed as a motor are discussed. With the availability of electronic calculators, circle-diagram methods have lost their significance. However, the circle diagram for the induction machine is included as it gives the complete machine performance at a glance and is quite useful in qualitative reasoning. A simple approach to machine dynamics is given in all the three machine types. In the case of the synchronous machine, dynamics is restricted to the phenomenon of “hunting”, while transient stability receives elementary treatment. Chapter 10 deals with the important topic of fractional-kW motors. A qualitative-cum-heuristic analysis of a single-phase induction motor and its circuit model are followed by a rigorously developed circuit model for a two-winding motor. This rigorous coverage may be skipped when time does not permit it. A variety of single-phase induction, synchronous and series commutator types of motors are treated. Comprehensiveness is imparted to this chapter by the inclusion of stepper motors, ac servomotor and ac tachometer; the latter two follow simply as a corollary from the two-winding motor analysis. Chapter 11 is an entirely new chapter and deals with the generalised theory of electrical machines. Probably the most significant development in recent years in the allied area of motor control is the use of power semiconductors—diodes, power transistors and thyristors. The growth in this area has already qualified for a separate undergraduate level course. However, for the sake of completeness, a comprehensive chapter is included in this book. This in our view is a better approach than to burden the previous chapters by spreading out the relevant details. Chapter 12 on this topic has a wide coverage and includes all the three varieties of SCR (silicon controlled rectifier) circuitry, namely converters, choppers and inverters. The contents and effects of non-smooth dc and nonsinusoidal ac outputs of these control equipment on the circuit behaviour and on machine performance are beyond the scope of this book. With the phenomenal developments in SCR circuitry for power control, cross-field machines and ac commutator machines have become almost obsolete. However, to fulfil the need of such universities which still include these topics in their curriculum, fairly detailed appendices (IV and V) on these topics are added. A number of cross-sectional views of built-up machines and their parts are included and the student is exhorted to carefully study these to help him visualize the physical picture of the machine being modelled. Laboratory exercises always associated with a machines course will further aid this process. A large number and variety of illustrative examples are spread throughout the book. These would greatly help in imprinting a clear physical picture of the devices and associated physical reasoning on the student’s mind. An equally large number of unsolved problems are given as exercises at the end of each chapter. Answers to all the unsolved problems are given. Some of these problems are devised to illustrate some points beyond what is directly covered in the text. International Standard (SI) units are used throughout the book. The list of symbols is necessarily large. Apart from being illustrated at the point of occurrence, the symbols used are listed in the beginning of the book. Web Supplements The web supplements can be accessed at http://www.mhne.com/electmach4e and contain the following material: Contents Preface xvii For Instructors: Solution Manual and Power Point Lecture Slides For Students: Interactive Quiz and Web links for Study Material. Acknowledgements While revising the text, we have had the benefit of valuable advice and suggestions from many teachers, students and other readers who used the earlier editions of this book. All these individuals have influenced this edition. We express our thanks and appreciation to them. We hope this support / response would continue in future also. We are grateful to the authorities of VIT University, Vellore, for providing all the facilities necessary for writing the book. One of us (D P Kothari) wishes to place on record the thanks he owes to his colleagues—Mr K Palanisamy, Mr Dilip Debnath, Mr Umashankar, Mr N Murali and Mr N Sreedhar—for their help in preparing and typing rough drafts of certain portions of the manuscript, writing MATLAB programs and solving problems using Simulink (MATLAB) and for helping in preparing the solutions of examples and unsolved problems of certain chapters. We also express our appreciation for all those reviewers who took out time to review the book. Their names are given below. R K Jarial National Institute of Technology, Hamirpur, Himachal Pradesh K N Vaishnav National Institute of Technology, Jaipur, Rajasthan P P Tarang JSS College of Technical Education, Noida, Uttar Pradesh Imtiaz Ashraf Aligarh Muslim University, Aligarh, Uttar Pradesh Sanjay Parida Indian Institute of Technology, Patna, Bihar S N Mahto National Institute of Technology, Durgapur, West Bengal Urmila Kar Netaji Subhash Engineering College, Kolkata K K Ghosh Dream Institute of Technology, Kolkata N Kumaresan National Institute of Technology, Trichy, Tamil Nadu Ashok S National Institute of Technology, Calicut, Kerala A Nirmal Kumar Bannari Amman Institute of Technology, Tamil Nadu B K Murthy National Institute of Technology, Warangal, Andhra Pradesh T B Reddy GPR Engineering College, Kurnool, Andhra Pradesh K S Pawar BSD College of Engineering, Dhule, Maharashtra We also thank TMH personnel and our families who supported us during this period and given all possible help so that this book could see the light of the day. Feedback We welcome any constructive criticism of the book and will be grateful for any appraisal by the readers. The suggestions can be sent on my email: [email protected] D P KOTHARI I J NAGRATH xviii Contents Preface Publisher’s Note Tata McGraw-Hill invites suggestions and comments from you, all of which can be sent to [email protected] (kindly mention the title and author name in the subject line). Piracy-related issues may also be reported. Introduction 1 1 1.1 INTRODUCTION Electricity does not occur naturally in usable form and it also cannot be stored* in usefully large quantities. Therefore, it must be generated continuously to meet the demand (of power) at all times. An efficient and convenient way to generate electric power is by conversion of mechanical power into electrical form in a rotating device** called a generator. In the process a small part of power is lost in the generator (efficiencies in large generators are above 90%). The mechanical power is itself obtained from heat power by thermodynamical means in a steam turbine (efficiency in the range of 40–50% as the present upper limit) or by conversion of potential energy of water in a hydraulic turbine with very little loss. The basic source of mechanical power—steam/hydraulic turbine is called the prime mover. Electricity can also be generated directly from hot gases in plasma form, obviating the need of converging heat power to intermediate mechanical power. This process† is still in an experimental stage. The electromechanical process of electric power generation is shown schematically in Fig. 1.1. Under steady conversion conditions, Pelectrical Shaft w Prime Electric Heat power mover generator TPM TG Pmechanical Losses Fig. 1.1 Electric generator TPM (prime mover) = TG (generator) and the turbine and generator run at steady speed. Other than lighting and heating††, the major use of electric energy is made by converting it back to the mechanical form to run the wheels of industry as well as tiny household appliances. The intermediary, the * Attempts are on to store a sizeable amount of electric energy in large superconducting coils. While these attempts are not likely to succeed in the near future, this stored energy would only be sufficient to meet sharp load peaks. ** The device always has an outer stationary member (refer to Sec. 1.2). † The process is known as magnetohydrodynamics (MHD) which uses the Hall effect to generate electric power. The process is inefficient because the outlet gases are at high temperature. By utilizing the hot gases in a conve- nient gas turbine, the composite process could be made more efficient than the conventional steam turbine. † † It is expensive to use electricity for heating except in special processes (e.g. electric arc furnaces) and where highly accurate controlled heating is required (e.g. induction heating). 2 Electric Machines electric power, permits the use of large efficient central generating stations, while it is easily transported to the myriads of use points. The electromechanical energy conversion process is a reversible one and simple adjustment of mechanical shaft and Pelectrical electrical conditions reverses the flow of power as Shaft illustrated in Fig. 1.2. In this mode of operation, TL w the electromechanical device, in general called Load Electric the electric machine, is known as the motor and (mechanical) motor the machine is said to be in the motoring mode. TM Under steady speed operation, again TM (motor) Losses = TL (load). Both in generating and motoring Pmechanical modes, losses occur in the electric machine but Fig. 1.2 Motoring mode of operation of an electric machine the overall conversion efficiencies are very high (close to or above 90%). Electric machines are employed in almost every industrial and manufacturing process. Pages can be filled in listing the applications of electric machines right from giant-size generators (500 MW and above), industrial motors ranging up to a few megawatts to fractional-kW domestic appliances and to sophisticated aerospace applications requiring stringent reliability in operation. This book deals with the important topic of electric machines, the indepth understanding of which is necessary to tackle the problems of energy, pollution and poverty that presently confront the whole of mankind. Since Thomas Alva Edison developed an electric generator, more than hundred years ago, engineers have continually strived and successfully reduced the size and revised upwards the efficiencies of electric machines by the use of improved materials and optimal design strategies. We appear to have reached close to the upper limit imposed by nature. A transformer is a static device that transforms electric energy from one ac voltage level to another. It is this device that has made the electric system almost universally ac. The electric power is generated at relatively low voltages (up to a maximum of 33 kV) which then is raised to very high voltages (e.g. 756 kV) by means of a transformer and then transmitted. High voltages are associated with low currents and reduced transmission losses. Geographically close to the use points, the electric power is transformed back to safe low utility voltages (400/231 V). A transformer consists basically of two coils (three sets of coil pairs for a 3-phase system) tightly coupled by means of magnetic (steel) core. Figure 1.3(a) gives the symbolic Electric power Electric power (a) Transformer Transmission line Load Generator (ac) Transformer Transformer (step-up) (step-down) (b) Simple electric power system Fig. 1.3 Introduction 3 representation of a transformer and Fig. 1.3(b) shows a simple electric power generation transmission and reception system. A practical electric power system is an integrated one, far more complex than the simple diagrammatic representation of Fig. 1.3(b), and is in the form of an interconnected network for reasons of economy, operational efficiency and reliability. Because the principle of rotating ac machines is akin to that of a transformer, these two are always studied together in a book. Further, since the transformer analogy can be extended to both the ac machine types, the transformer study usually precedes the machine study. 1.2 BASIC PRINCIPLE, TYPES AND CONSTRUCTIONAL FEATURES OF ELECTRIC MACHINES There are three basic rotating electric machine types, namely 1. the dc machine, 2. the polyphase synchronous machine (ac), and 3. the polyphase induction machine (ac). Three materials are mainly used in machine manufacture; steel to conduct magnetic flux, copper (or aluminium) to conduct electric current and insulation to insulate the voltage induced in conductors confining currents to them. All electric machines comprise of two parts: the cylindrical rotating member called the rotor and the annular stationary member called the stator with the intervening air-gap as illustrated in Fig. 1.4. The rotor has an axial shaft which is carried on bearings at each end located in end covers bolted to the stator. The shaft extends out of the end cover usually at one end and is coupled to either the prime mover or the load. The stator and rotor are both made of magnetic material (steel) which conducts the magnetic flux upon which depends the process of energy conversion. In both dc and synchronous machines, the main field is created by field poles excited with direct current. Air-gap The winding on the field poles is called the field winding. The relative motion of the field past Rotor a second winding located in the other member Shaft induces emf in it. The winding interchanges Stator current with the external electric system depending upon the circuit conditions. It is this winding, called the armature winding, which handles the load power of the machine, while the field winding consumes a small percentage (0.5% to 2%) of the rated load power. The load dependent armature current is known as load Fig. 1.4 An electric machine current. In a dc machine the field poles are on the stator while the rotor is the armature as shown in the cross- sectional view of Fig. 1.5. The field poles are symmetrical and are even in number, alternately north and south. As the armature rotates, alternating emf and current induced in the armature winding are rectified to dc form by a rotating mechanical switch called the commutator, which is tapped by means of stationary carbon brushes. The commutator is cylindrical in shape and comprises severel wedge-shaped copper segments 4 Electric Machines bound together while they are insulated from each other. The armature is made of laminated steel with slots cut out on the periphery to accommodate the insulated armature winding. The ends of each armature coil are connected to the commutator segments to form a closed winding. The armature when carrying current produces stationary poles (same as number of field poles) which interact with the field poles to produce the electromagnetic torque. Main pole Field winding Pole shoe Yoke N Armature winding + la Va(dc) S S – lf Vf (dc) N Armature Commutator Brushes Fig. 1.5 Cross-sectional view of dc machine In a synchronous machine the field poles could be either on the stator or rotor, but in all practical machines the rotor carries the field poles as shown in the cross-sectional view of Fig. 1.6. The field poles are excited Armature winding Field winding N la 3-phase lb ac S lc S Stator lf Vf (dc) N Rotor Main pole Pole Shoe Fig. 1.6 Cross-sectional view of synchronous machine Introduction 5 by direct current. The stator forms the armature carrying a 3-phase winding wound for the same number of poles as the rotor. All the three phases have identical windings with the same angular displacement between any pair of phases. When the rotor rotates, it produces alternating emf in each phase forming a balanced set with frequency given by nP f= (1.1) 120 where f = frequency in Hz n = rotor speed in rpm P = number of field poles For a given number of poles, there is a fixed correspondence between the rotor speed and the stator frequency; the rotor speed is therefore called the synchronous speed. When balanced 3-phase currents are allowed to flow in the armature winding, these produce a synchronously rotating field, stationary with respect to the rotor field as a result of which the machine produces torque of electromagnetic origin. The synchronous motor is, however, nonselfstarting. In both dc and synchronous machines the power handling capacity is determined by the voltage and current of the armature winding, while the field is excited from low power dc. Thus these machine types are doubly excited. Quite different from these, an induction machine is singly excited from 3-phase mains on the stator side. The stator winding must therefore carry both load current and field-producing excitation current. The stator winding is 3-phase, similar to the armature winding of a synchronous machine. When excited it produces a synchronously rotating field. Two types of rotor constructions are employed which distinguish the type of induction motor. 1. Squirrel-cage rotor Here the rotor has copper (or aluminium) bars embedded in slots which are short- circuited at each end as shown in Fig. 1.7(a). It is a rugged economical construction but develops low starting torque. 2. Slip-ring (or wound-rotor) rotor The rotor has a proper 3-phase winding with three leads brought out through slip-rings and brushes as shown in Fig. 1.7(b). These leads are normally short-circuited when the motor is running. Resistances are introduced in the rotor circuit via the slip-rings at the time of starting to improve the starting torque. The rotating field created by the stator winding moves past the shorted rotor conductors inducing currents in the latter. These induced currents produce their own field which rotates at the same speed (synchronous) with respect to the stator as the stator-produced field. Torque is developed by the interaction of these two relatively stationary fields. The rotor runs at a speed close to synchronous but always slightly lower than it. At the synchronous speed no torque can be developed as zero relative speed between the stator field and the rotor implies no induced rotor currents and therefore no torque. Single-phase ac motors are employed for low-voltage, low-power applications—fractional-kW motors. They operate on the same basic principles as the 3-phase motor, but the pulsating single-phase field produces additional losses, reducing motor torque and the pulsating torque component increases the noise level of the motor. An induction machine connected to the mains when driven at supersynchronous speed behaves as a generator feeding power into the electric system. It is used in small hydroelectric stations and wind and aerospace applications. The insulation of a machine (or transformer) is its most vulnerable part because it cannot be stressed beyond a certain temperature. For a given frame size, the steady temperature rise is determined by the machine loading, 6 Electric Machines End rings Conducting bars embedded in slots and shorted at both ends by end rings (a) A squirrel-cage rotor (schematic diagram) Brushes Slip-rings Windings (details not shown) embedded in slots, leads brought out to slip-rings (b) A wound rotor (schematic diagram) Fig. 1.7 the associated power loss (this appears in the form of heat) and the cooling provided. Thus the maximum machine loading called its rating for a given frame size is limited by the permissible temperature rise which is dependent upon the class of insulation used. In the case of high-speed dc machines poor commutation (reversal of current in armature coils) may become a limiting factor even before the temperature limit is reached. The speed itself may be a limiting factor in very high-speed machines on account of the centrifugal forces developed. This limit is more stringent in dc machines with complicated armature construction than in the rugged rotor induction motor. Because of their high thermal capacity, machines are quite capable of withstanding a fair amount of overloads for short durations. Motor Control There is great diversity and variety in the components and systems used to control rotating machines. The purpose of a motor control may be as simple as start/stop or the control of one or more of the motor output parameters, i.e. shaft speed, angular position, acceleration, shaft torque and mechanical power output. With the rapid development of solid-state power devices, integrated circuits and cheap computer modules, the range, quality and accuracy of electronic motor control has become almost infinite. Machines and other electromechanical systems having the highest possible precision and reliability have been developed for nuclear power and space applications. Using solid-state power converters, schemes have been devised to start, stop or reverse dc motors in the megawatt range in a matter of seconds. Finally, as the nonconventional and Introduction 7 renewable sources of energy, such as solar, windmill, etc., would become economical, viable electromechanical energy converters will be required with matching characteristics. Economic and Other Considerations As in other devices, economics is an important consideration in the choice of electric machines and the associated control gear. The trade-off between the initial capital investment and the operating and maintenance cost must be taken into account in this choice; the decision may be in favour of a high-efficiency high-cost motor, particularly in an environment of rising energy costs. While the transformer produces magnetic noise, the rotating machines, in addition, produce mechanical noise arising from bearings, windage, etc. In present- day noise-pollution levels, the noise figure in decibels can be an important factor in motor choice. These considerations are not the subject matter of this book which emphasises electromechanical principles and the theory and application of electric machines including transformers. 1.3 RECENT TRENDS IN RESEARCH AND DEVELOPMENTS IN ELECTRIC MACHINES Design and operation of electrical machines become easier and cheaper with suitable electric drives. This electric drive converts and feeds the input energy to the machine according to the desired operation. A power electronic converter constitutes the heart of the drive system which uses the power semiconductor devices. These converters help to convert the power from one form to another. Various advancements in converter topologies, and control methods have been proposed to convert and control the energy efficiently. Other intelligent techniques such as Neural Network, Artificial Intelligence, Expert system, Fuzzy logic and Evolutionary Computing are used to make the control most accurate and fast. Research in converter topologies has also improved the power quality at the supply end. Various multipulse and multilevel power electronic converters have been developed for power-quality improvement along with cost-effective ac-dc converters for power factor improvement in electric drive system. Electrical energy offers the most flexible, economic and efficient mode of power generation, transmission, distribution and utilization compared to other forms of energy systems. Most of the power required for human activities round the globe continues to come from electrical machines from the very large generators installed in power stations to the very small motors in automotive control systems. The rapid depletion and the increased cost of conventional fuels have given a thrust in the research on isolated asynchronous generators as alternative power sources, converting from wind energy, biogas, hydro units and biomass. Asynchronous generators operated in isolated systems for supplying electricity to the remote areas, where grid supply is not accessible, are best options because of having certain advantages such as low cost, less maintenance and brushless constructions. In a wind-energy conversion system, the voltage and frequency variation at the generator terminals is due to varying consumer loads as well as change in wind speeds. Therefore, the controller should have the capability to control the voltage and frequency of isolated generators under dynamic conditions. Various types of voltage and frequency controllers are proposed for constant-speed, constant-power applications. Friction, vibration and noise can be eliminated in industrial drive by using permanent magnet direct-drive technology. Both ac and dc PM motors are more suitable for high performance and wide speed variation applications. Motors with higher torque and low speed are highly appreciated. PM brushless motors are of this category. The electric machines market is rapidly growing because of various developments and emerging areas such as wind energy, marine, traction and offshore. 8 Electric Machines The materials used for making the electrical machines play a major role in their performance. Particularly, maximum temperature rise of the material (permanent magnet and insulation materials) used will affect the rated torque of an electrical machine. The operating temperature strongly affects the performances of electrical machines. Finite Element Analysis (FEA) can be used to compute the temperature of the material and machines. A thermal network of the electrical machines is considered and input to this network is calculated from magnetic and electrical loading of the machines. An Object Oriented Program (OOP) is used to develop thermal network and it allows a convenient organization of thermal analysis process. Modern commercial electrical steels can be grouped under non-oriented, grain-oriented and rapidly quenched alloy types, of which the first two dominate the applications. Because of the limitations on the shape of the magnetic path, grain-oriented types are used predominantly in large power and distribution transformers, while non-oriented ones are used in rotating machines and small apparatus. The silicon content is critical to the performance of electrical steels because it increases resistivity but it, also reduces the anisotropy and so reduces losses and magnetostriction and permeability and makes the material brittle. In non-oriented type, this content varies between 2.9% to 3.2%. The continuing development of high permeability silicon-steel, metallic glass, ferrites, aluminum ceramics and high temperature insulating materials, permanent magnetic materials like Neomax (Nd-Fe-B) and rare-earth cobalts has been influencing the construction and design of many large and small machines and apparatus from large generators to small step motors. Not only the cost of material per kVA has come down in many cases, more reliable and highly efficient machines have been successfully designed. Areas which have revolutionized the growth of research in electrical machines could be grouped as (a) Design of power electronic converters for motor drive and with better efficiency and control (b) Increase in rating of power semiconductor solid-state devices (c) Development of cheap digital signal processing controllers for operation and control (d) The development of evolutionary computing techniques, artificial intelligent techniques for machine design, operation and control (e) Power quality and power factor improvement using improved power quality converters for various motor-drive applications (f ) Design of motor drives of electric and hybrid electric vehicles (g) Condition monitoring of electrical machines using Artificial Intelligence techniques (h) Design of electric machines using CAD/CAM techniques and validation through FE analysis Thyristor is still unbeaten in high voltage and current rating among power semiconductor devices with voltage and current rating of 12 kV and 6 kV, respectively. New devices such as IGCT, GCT, power MOSFET, power IGBT have opened up new vistas for the electronic switching and control of energy-converting devices; ac/dc, dc/ac, ac/ac and dc/dc converters are at their peak in various applications and totally changed the way of operating the machines from the conventional mode of operation. Development of self-commutated devices overcome the drawbacks of line commutated converters and it is used in both Voltage Source Converters (VSC) and Current Source Converters (CSC). High voltage dc transmission (HVDC), Flexible ac Transmission System (FACTS), variable frequency operation of machines, voltage control of dc machines, Switched Mode Power Supply (SMPS), offer a wide variety of applications for converters and for power engineers to develop new and realiable system configurations. The most common application is the variable speed drives using dc and ac machines. Power electronics appear to have shifted the emphasis of electrical engineers from the design of special types of variable speed machines to the use of special electronic circuits to make an existing machine to give the desired variable speed characteristics and performances. Introduction 9 Electric vehicles and hybrid electric vehicles are one of the most recent and potential applications of electrical machines. These vehicles use the motor drives in association with power electronic converters. Application of electrical drives in system automobile began with 6 V in the first quarter of the 20th century. Initially, it was used only for basic and necessary functions such as ignition, cranking and lighting loads. Since then, there has been a constant increase in power demand and now the whole vehicle is driven by the electrical system. Electrical system has replaced all mechanical, pneumatic and hydraulic systems, thereby increasing the efficiency and performance of the automobile system. Present voltage level being used is 12 V, and in the future it is expected to switch over to higher levels such as 42 V and 300 V. There is a immense challenge in design of power electronic converters and suitable high-efficiency machines for hybrid electric vehicles. To make the squirrel-cage induction motor run like a separately excited dc motor has remained a dream of generations of electrical engineers. Direct Torque Control (DTC) has fulfilled this dream and simplified the control circuit of induction motor to a great extent. The availability of cheap microprocessor-based system has further improved the control of electrical devices of all forms for obtaining the desired steady state, transient as well as dynamic characteristics from the existing drive machine with the help of suitable designed solid-state control circuits. Electrical machines and drive systems are subjected to many different faults. They may include stator faults, rotor electrical faults and rotor mechanical faults, failure of power electronics system and damage of mechanical parts. Most of industrial processes demand continuous operation. This is mainly influenced by the condition monitoring leading to fault diagnosis and prediction of performance of electrical machines and drives. Fast and accurate diagnosis of machine faults results in prevention of failure and avoiding processes interrupt and reduce the idle time of machines. It also helps in reducing financial loss, avoids harmful effects and devastation of the system. For many years, the manufactures and users had relied on protective relays such as over-current and over- voltage relays to trip fault machines. This scheme may lead to machine damage and other harmful effects. Various intelligence techniques such as Artificial Neural Networks (ANN), Expert System (ES), Fuzzy System (FS) are being used for machines analysis for monitoring and control to make the process continuous, fast and accurate. One of the latest developments in ac motor research has been in the direction of field-oriented control or making ac motors perform like dc motors with highly accurate torque and power control. Another recent development in ac motor drives is a system called Direct Torque Control and Direct Self-Control. There is no modulator and no need for an encoder to feedback information about motor shaft speed and position. The DTC sensorless-type control incorporates fast digital signal processing hardware, resulting in a torque response which is ten times faster than any ac or dc drive. One of the reasons why ac technology will continue to make inroads into dc dominance is reduced power consumption. Brushless dc will survive eventually but it is not dc at all but a completely different technology. It is called dc because of the concept of external commutation. Now there are increased levels of customer support. With the emphasis on just-in-time production, downtime is unacceptable. With today’s systems, if the machine goes down one can, via modem, have a technician at a remote site use system diagnosis software to troubleshoot the entire system from anywhere in the world. Large Rating Machines The innovative design features as direct water-cooled armature windings, gap-pickup rotor winding cooling, Micapal II stator insulation, Class F rotor and stator insulation, advanced Tetraloc stator endwinding 10 Electric Machines support systems, and the side ripple-spring armature bar slot support structure were developed for heavy rating machines. The Finite Element Model (FEM) is exercised to interrogate the generator assembly for all loads encountered during assembly and operation. Electromagnetic force is the most likely force to cause structural issues. This force is cyclic and acts in the radial direction at the inside diameter of the stator core with a magnitude of one million pounds. The resulting stator core vibration and the transmission to the generator structure and foundation is a significant design consideration. Forced harmonic response analyses are performed to ensure that the electromagnetic forces cannot excite the machine’s natural frequencies. The structural design of the stationary components also must be considered when calculating the dynamic behavior of the rotor, since the rotor is supported on bearings located in the end shields of the machine. In this load configuration, the structural vibratory loads caused by the rotor, and the loading caused by stator vibration that drives rotor behavior, are interrogated. Once again, a forced harmonic analysis is performed to understand and optimize the interactions. Lastly, the structural design has a major impact on the overall producibility and serviceability of the generator. The complexity of the fabrication determines the unit’s machining cycles as well as its accessibility for thoroughly cleaning the inner cavities of the machine before shipping. Generator 2 pole machine running at 3000/3600 rpm and 4 pole machine running at 1500/1800 rpm have become common for large outputs or 1000 MW of more. The main dimension of 1000 MVA machine is the output coefficient C which will be 2 MVA s/m3 and D2L will be 10 m3. The higher value of output coefficient is made possible by enhanced cooling techniques. The excitation current is 7 kA at 650 V for 1500 MVA machine and 5.7 kA, 640 V for 1000 MVA machine respectively. The stator core, made from grain-oriented silicon steel for low loss and high permeability, is mounted rigidly on the inner frame. Isolation of the core vibration from the remainder of the structure is accomplished through the use of flexible pads between the feet on the inner frame and the base structure. The end windings are secured to a strong structure of insulating materials to be used. A solid cone of filament-wound resin bonded fibre glass is used to generate strength and long-term rigidity. The coils are bedded to the structure with comfortable packing material. The complete structure is bolted to the end of the core. Axial movement may be allowed to accommodate expansion of coils relative to the core. Low-loss stator core, of grain- oriented silicon steel, minimizes electrical losses within the core to increase machine efficiency. The insulation between turns is usually provided by interleaves of resin-bonded glass fabric material. The stator winding arrangements for 1000 MVA should be four parallel paths in 2-pole machines and in 4-pole machines, it can be in parallel or series parallel combination. The efficiency of 1000–1500 MVA is normally very high. Due to this megawatt loss, good cooling medium is required. Direct hydrogen cooling of rotors is developed for 1000 MVA. The cooling of the rotor can be done by 1). Each coil is wound with continuous length of copper strap bent on edge at the four corners, 2). Larger section conductors of silver bearing copper- containing grooves and holes to provide the passage of gas. Cool, deionized water, supplied by a closed-loop auxiliary system, flows through copper strands in the stator winding, and the warm water is discharged at the turbine end of the generator. The hydrogen-cooled machines can be designed with a higher electrical loading than the air-cooled machines due to the better cooling, and tend to have a larger subtransient reactance than an air-cooled machine. The generator’s performance is heightened by optimization of its bar strand configuration, including hollow-to-solid-strand ratio. Spring bar stator core support system isolates vibration of the stator core, to minimize vibration transmitted to the foundation. Stator winding support features top wedges and ripple springs to secure stator bars in the slot and eliminate bar vibration. This maximizes insulation life and reduces maintenance requirements. Core-end cooling is enhanced through proven design concepts to control core Introduction 11 P = K ¢Di 2 ¢L ¢n Core end with High TS 4Ni-Cr Unequal section Improved coil end flux shunt shaft forging mix strand water support cooled stator coil High TS 18 Mn-18Cr RR Optimized L/D rotor Maximized field conductor area Center grooved 2 piece babbitt Hydrogen elliptical Low Fn compact sealing ring cooled HVB journal bearing frame Fig. 1.8 Internal view of 1000 MW generator (Courtesy, Toshiba Corporatin) temperatures and minimize eddy current losses. Approaches include split tooth, stepped core, flux shields and non-magnetic materials. Retaining rings of 18-Mangaanese/18-Chromium, non-magnetic stainless steel resists stress-corrosion cracking. Internal view of a 1000 MW generator is shown in Fig. 1.8. Generator Parameters (600 MW) Parameters Unit Rated capacity MW 600 Rated power factor 0.85 Synchronous reactance Xd% 240.313 Transient reactance Xd¢% 28.281 Sub-transient reactance Xd≤% 21.582 Nagative-seq reactance X2% 21.295 Zero-seq reactance X0% 10.131 Direct axis time constant Open circuit time constant Tdo¢ Sec 8.724 Short circuit time constant Td¢ Sec 1.027 Open circuit sub-transinet Tdo≤ Sec 0.046 Short circuit sub-transient Td≤ Sec 0.035 Qudrature axis time constant Open circuit time constant Tdo¢ Sec 0.969 Short circuit time constant Td¢ Sec 0.169 Open circuit sub-transinet Tdo≤ Sec 0.068 Short circuit sub-transient Td≤ Sec 0.035 12 Electric Machines 2 2.1 INTRODUCTION The electromagnetic system is an essential element of all rotating electric machinery and electromechanical devices as well as static devices like the transformer. The role of the electromagnetic system is to establish and control electromagnetic fields for carrying out conversion of energy, its processing and transfer. Practically all electric motors and generators, ranging in size from fractional horsepower units found in domestic appliances to the gigantic several thousand kW motors employed in heavy industry and several hundred megawatt generators installed in modern generating stations, depend upon the magnetic field as the coupling medium allowing interchange of energy in either direction between electrical and mechanical systems. A transformer though not an electromechanical conversion device, provides a means of transferring electrical energy between two electrical ports via the medium of a magnetic field. Further, transformer analysis runs parallel to rotating machine analysis and greatly aids in understanding the latter. It is, therefore, seen that all electric machines including transformers use the medium of magnetic field for energy conversion and transfer. The study of these devices essentially involves electric and magnetic circuit analysis and their interaction. Also, several other essential devices like relays, circuit breakers, etc. need the presence of a confined magnetic field for their operation. The purpose of this chapter is to review the physical laws governing magnetic fields, induction of emf and production of mechanical force, and to develop methods of magnetic-circuit analysis. Simple magnetic circuits and magnetic materials will be briefly discussed. In the chapters to follow, how the concepts of this chapter are applied in the analysis of transformers and machines will be shown. 2.2 MAGNETIC CIRCUITS The exact description of the magnetic field is given by the Maxwell’s equations* and the constitutive relationship of the medium in which the field is established. ! ! ! ! —◊B = 0 and —◊D = r ! ! ! ! ∂D ! ! –12 —¥H = J + and D = e0 E ; e0 = 8.85 ¥ 10 ∂t ! ! wherein J = conduction current density and D = displacement current density, negligible for slowly-varying ! ! fields D = e0 E ; e0 = 8.85 ¥ 10–12 F/m). Magnetic Circuits and Induction 13 Such description apart from being highly complex is otherwise not necessary for use in electric machines wherein the fields (magnetic and electric) are slowly varying (fundamental frequency being 50 Hz) so that the displacement current can be neglected. The magnetic field can then be described by Ampere’s law and is solely governed by the conduction current. This law is in integral form and is easily derivable from the third Maxwell’s equation (by ignoring displacement current) by means of well-known results in vector algebra. The Ampere’s law is reproduced as follows: ! ! ! ! sÚJ ◊ ds = H ◊ dl "Ú (2.1) ! wherein J = conduction current density ! H = magnetic field intensity s = the surface enclosed by the closed path of length l ! d s = differential surface ! d l = differential length Consider the example of a simple electromagnetic system comprising an exciting coil and ferromagnetic core as shown in Fig. 2.1. The coil has N turns and carries a constant (dc) current of i A. The magnetic field is established in the space wherein most of the total magnetic flux set up is confined to the ferromagnetic core for reasons which will soon become obvious. Consider the flux path through the core (shown dotted) which in fact is the mean path of the core flux. The total current piercing the surface enclosed by this path is as follows: ! ! Ús J ◊ ds = Ni Hc i Core mean + length lc (Ferromagnetic) e N Leakage fiux – ca b Exciting coil d Fig. 2.1 A simple magnetic system Hence Eq. (2.1) acquires the form ! ! Ni = "Ú H ◊ dl (2.2) l Since N is the number of coil turns and i the exciting current in amperes, the product F = Ni has the units of ampere-turns (AT) and is the cause of establishment of the magnetic field. It is known as the magnetomotive force (mmf ) in analogy to the electromotive force (emf ) which establishes current in an electric circuit. 14 Electric Machines The magnetic field intensity H causes a flux density B to be set up at every point along the flux path which is given by B = mH = m0 mrH (for flux path in core) (2.3a) and B = m0H (for flux path in air) (2.3b) The units of flux density are weber (Wb )/m2 called tesla (T). The term m0 is the absolute permeability of free space and has a value of m0 = 4p ¥ 10–7 henry (H)/m The permeability m = m0 mr of a material medium is different from m0 because of a certain phenomenon occurring in the material. The term mr is referred to as relative permeability of a material and is in the range of 2000-6000 for ferromagnetic materials (see Sec. 2.3). It is, therefore, seen that for a given H, the flux density B and, therefore, the flux over a given area ! ! f= "Ú B ◊ d s s will be far larger in the magnetic core in Fig. 2.1 than in the air paths. Hence, it is safe to assume that the magnetic flux set up by mmf Ni is mainly confined to the ferromagnetic core and the flux set up in air paths is of negligible value. The flux set up in air paths is known as the leakage flux as if it leaks through the core; some of the leakage flux paths are shown chain-dotted in Fig. 2.1. There is no way to avoid magnetic leakage as there are no magnetic insulators in contrast to electric insulators which confine the electric current to the conductor for all practical purposes. The effect of the leakage flux is incorporated in machine models through the concept of the leakage inductance. The direction of field intensity is H and so the direction of flux f is determined from the Right Hand Rule (RHR). It is stated as: Imagine that you are holding a current carrying conductor in your right hand with the thumb pointing in the direction of current. Then the direction in which the fingers curl gives the direction of flux. In case of a coil you imagine that you are grasping the coil in right hand with the thumb in the direction of current; then the fingers curl in the direction of flux. The reader may apply RHR to the exciting coil in Fig. 2.1 to verify the direction of flux as shown in the figure. ! The magnetic field intensity H is tangential to a flux line all along its path, so that the closed vector integration in Eq. (2.2) along a flux-line reduces to closed scalar integration, i.e. Ni = "Ú H · dl (2.4) l With the assumption of negligible leakage flux, the flux piercing the core cross-section at any point remains constant. Further, from the consideration of symmetry it immediately follows that the flux density over straight parts of the core is uniform at each cross-section and remains constant along the length; such that H is constant along the straight parts of the core. Around the corners, flux lines have different path lengths between magnetic equipotential planes (typical ones being ab and cd shown in Fig. 2.1) so that H varies from a high value along inner paths to a low value along outer paths. It is reasonable to assume that H shown dotted along the mean path will have the same value as in straight parts of the core (this mean path technique renders simple the analysis of magnetic circuits of machines and transformers). Magnetic Circuits and Induction 15 It has been seen previously that the magnetic field intensity along the mean flux path in the core can be regarded constant at Hc. It then follows from Eq. (2.4) that F = Ni = Hc lc (2.5) where F = mmf in AT and lc = mean core length (m) From Eq. (2.5) Ni Hc = AT/m (2.6) lc If one now imagines that the exciting current i varies with time, Eq. (2.6) would indicate that Hc will vary in unison with it. Such fields are known as quasi-static fields in which the field pattern in space is fixed but the field intensity at every point varies as a replica of the time variation of current. This simplified field picture is a consequence of negligible displacement current in slowly-varying fields as mentioned earlier. In a quasi- static field, the field pattern and field strength at a particular value of time-varying exciting current will be the same as with a direct current of that value. In other words, a field problem can be solved with dc excitation and then any time variation can be imparted to it. Now, the core flux density is given by, Bc = mc Hc tesla (T) and core flux (assumed to be total flux) is given by, ! ! "Ú f = B ◊ d s = Bc Ac Wb s where Ac = cross-sectional area of core and flux in the limbs is oriented normal to cross-sectional area. Then from Eq. (2.6) Ni F f = mc HcAc = or f= = FP (2.7) Ê lc ˆ R ÁË m A ˜¯ c c F l where R= = c = reluctance* of the magnetic circuit (AT/Wb) (2.8) f mc Ac and P = 1/R = permeance of the magnetic circuit. It is, therefore, seen that by certain simplifying assumptions and field symmetries, it has been possible to lump the distributed magnetic system into a lumped magnetic circuit described by Eq. (2.7) which is analogous to Ohm’s law in dc circuits. The electrical circuit analog of the magnetic system (now reduced to a magnetic circuit) is shown in f (∼ i) Fig. 2.2 wherein F (mmf ) is analogous to E (emf ), R (reluctance) is analogous to R (resistance) and f (flux) is analogous to i (current). F (∼ E) R (∼ R) The analogy though useful is, however, not complete; there being two points of difference: (i) magnetic reluctance is nondissipative of energy unlike electric resistance, (ii) when F is time-varying, the magnetic Fig. 2.2 Electrical analog of the circuit still remains resistive as in Fig. 2.2, while inductive effects are simple magnetic circuit of bound to appear in an electric circuit. This is because there is no time- Fig. 2.1 lag between the exciting current and the establishment of magnetic flux (quasi-static field). * Unit of reluctance is AT/Wb and will not be specified every time in examples. 16 Electric Machines The lumped magnetic circuit and its electrical analog are useful concepts provided the permeability (m) of the core material and, therefore, the core reluctance is constant as is tacitly assumed above. This, however, is not the case with ferromagnetic materials, but when air-gaps are involved, the assumption of constant reluctance is generally valid and leads to considerable simplicity in magnetic circuit analysis. In more complicated magnetic circuits—with multiple excitations and series-parallel core arrangement— the general theorems of electric circuits apply, i.e. Kirchhoff’s voltage (mmf ) law and Kirchhoff’s current (flux) law. This is illustrated in Example 2.3. B-H Relationship (Magnetization Characteristic) In free space (also nonmagnetic materials), the permeability m0 is constant so that B-H relationship is linear. This, however, is not the case with ferromagnetic materials used in electric machines, wherein the B-H relationship is strictly nonlinear in two respects— (T ) saturation and hysteresis. Hysteresis non-linearity B Saturation zone is the double valued B-H relationship exhibited in cyclic variation of H (i.e. exciting current). This nonlinearity is usually ignored in magnetic circuit calculations and is important only when current wave shape and power loss are to be accounted Linear zone for. This is discussed in Sections 2.3 and 2.6. A (constant m) typical normal B-H relationship (magnetization characteristic) for ferromagnetic materials is shown in Fig. 2.3. It has an initial nonlinear zone, a middle lnitial nonlinear zone 0 almost linear zone and a final saturation zone in H(AT/m) which B progressively increases less rapidly with H Fig. 2.3 Typical normal magnetization curve of compared to the linear zone. In the deep saturation ferromagnetic material zone, the material behaves like free space. Due to considerations dictated by economy, electric machines and transformers are designed such that the magnetic material is slightly saturated (i.e. somewhat above the linear zone). In exact magnetic circuit calculations the nonlinear magnetization curve has to be used necessitating graphical/numerical solutions. Core with Air-gap Transformers are wound on closed cores as in Fig. 2.1. Rotating machines have a moving element and must therefore have air-gaps in the cores out of necessity. A typical magnetic circuit with an air-gap is shown in Fig. 2.4. It is assumed that the air-gap is narrow and the flux coming out of the core passes straight down the air-gap such that the flux density in the air-gap is the same as in the core. Actually as will soon be seen, that the flux in the gap fringes out so that the gap flux density is somewhat less than that of the core. Further, let the core permeability mc be regarded as constant (linear magnetization characteristic). The mmf Ni is now consumed in the core plus the air-gap. From the circuit model of Fig. 2.4(b) or directly from Fig. 2.4(a) Ni = Hc lc + Hglg (2.9a) Bc Bg or Ni = lc + lg (2.9b) mc m0 Magnetic Circuits and Induction 17 Hc Mean core length, lc i Cross-sectional + area A e Air-gap; Hg, lg N Rc f _ Ni Rg (a) (b) Fig. 2.4 A typical magnetic circuit with air-gap and its equivalent electric circuit Assuming that all the core flux passes straight down the air-gap (it means no fringing (see Fig. 2.5)) Bg = Bc \ f = Bc A = Bg A (2.10) Substituting Eq. (2.10) in Eq. (2.9b) Ê l ˆ Ê lg ˆ Ni = f Á c ˜ + f Á (2.11) Ë mc A ¯ Ë m0 A ˜¯ Recognizing various quantities in Eq. (2.11) F = f (Rc + Rg) = fReq (2.12) lc where Rc = = core reluctance mc A lg Rg = = air-gap reluctance m0 A From Eq. (2.12) F F /R g f= = (2.13) Rc + Rg 1 + Rc / Rg R c 0 lc But = ≪1 Rg clg because mc is 2000 to 6000 times m0 in ferromagnetic materials. The permeability effect predominates the usual core and air-gap dimensions even though lc ≫ lg. It then follows from Eq. (2.13), that f ª F/Rg (2.14) which means that in a magnetic circuit with air-gap(s), core reluctance may be neglected with no significant loss of accuracy. This assumption will be generally made in modelling rotating machines. The effect of core saturation (reduction of core permeability) will be introduced as a correction wherever greater accuracy is desired. 18 Electric Machines Magnetic Circuit Calculations Normally magnetic circuit calculations involve two types of problems. In the first type of problem it is required to determine the excitation (mmf ) needed to establish a desired flux or flux density at a given point in a magnetic circuit. This is the normal case in designing electromechanical devices and is a straight forward problem. In the second category, the flux (or flux density) is unknown and is required to be determined for a given geometry of the magnetic circuit and specified mmf. This kind of problem arises in magnetic amplifiers wherein this resultant flux is required to be determined owing to the given excitation on one or more control windings. A little thought will reveal that there is no direct analytical solution to this problem because of the non-linear B-H characteristic of the magnetic material. Graphical/numerical techniques have to be used in obtaining the solution of this problem. Leakage Flux In all practical magnetic circuits, most of the flux is confined to the intended path by use of magnetic cores but a small amount of flux always leaks through the surrounding air. This stray flux as already stated is called the leakage flux, Leakage is characteristic of all magnetic circuits and can never be fully eliminated. Calculations concerning the main magnetic circuit are usually carried out with the effect of leakage flux either ignored or empirically accounted for. Special studies of leakage must be made for ac machines and transformers since their performance is affected by it. Fringing At an air-gap in a magnetic core, the flux fringes out into neighbouring air paths as shown in Fig. 2.5; these being of reluctance comparable to that of the gap.