Aircraft Electrical Systems Chapter 11 PDF
Document Details
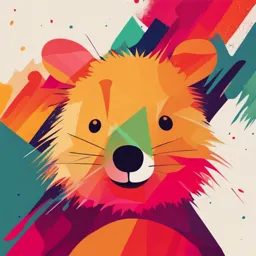
Uploaded by RefinedDysprosium8876
Tags
Summary
This document describes the inspection and care of aircraft electrical systems, including storage batteries and charging procedures. It details checks, adjustments, repairs, and cleaning of equipment. The information is relevant to professionals in aviation maintenance.
Full Transcript
9/8/98 AC 43.13-1B CHAPTER 11. AIRCRAFT ELECTRICAL SYSTEMS SECTION 1. INSPECTION AND CARE OF ELECTRICAL SYSTEMS 11-1. GENERAL. The term “electrical a. Damaged, discolored...
9/8/98 AC 43.13-1B CHAPTER 11. AIRCRAFT ELECTRICAL SYSTEMS SECTION 1. INSPECTION AND CARE OF ELECTRICAL SYSTEMS 11-1. GENERAL. The term “electrical a. Damaged, discolored, or overheated system” as used in this AC means those parts equipment, connections, wiring, and installa- of the aircraft that generate, distribute, and use tions. electrical energy, including their support and attachments. The satisfactory performance of b. Excessive heat or discoloration at high an aircraft is dependent upon the continued re- current carrying connections. liability of the electrical system. Damaged wiring or equipment in an aircraft, regardless c. Misalignment of electrically driven of how minor it may appear to be, cannot be equipment. tolerated. Reliability of the system is propor- tional to the amount of maintenance received d. Poor electrical bonding (broken, dis- and the knowledge of those who perform such connected or corroded bonding strap) and maintenance. It is, therefore, important that grounding, including evidence of corrosion. maintenance be accomplished using the best techniques and practices to minimize the pos- e. Dirty equipment and connections. sibility of failure. This chapter is not intended to supersede or replace any government speci- f. Improper, broken, inadequately sup- fication or specific manufacturer’s instruction ported wiring and conduit, loose connections regarding electrical system inspection and re- of terminals, and loose ferrules. pair. g. Poor mechanical or cold solder joints. 11-2. INSPECTION AND OPERATION CHECKS. Inspect equipment, electrical as- h. Condition of circuit breaker and semblies, and wiring installations for damage, fuses. general condition, and proper functioning to ensure the continued satisfactory operation of i. Insufficient clearance between exposed the electrical system. Adjust, repair, overhaul, current carrying parts and ground or poor in- and test electrical equipment and systems in sulation of exposed terminals. accordance with the recommendations and procedures in the aircraft and/or component j. Broken or missing safety wire, broken manufacturer’s maintenance instructions. Re- bundle lacing, cotter pins, etc. place components of the electrical system that are damaged or defective with identical parts, k. Operational check of electrically oper- with aircraft manufacturer’s approved equip- ated equipment such as motors, inverters, gen- ment, or its equivalent to the original in oper- erators, batteries, lights, protective devices, ating characteristics, mechanical strength, and etc. environmental specifications. A list of sug- gested problems to look for and checks (Refer l. Ensure that ventilation and cooling air to the glossary for a description of the check passages are clear and unobstructed. types) to be performed are: Par 11-1 Page 11-1 AC 43.13-1B 9/8/98 m. Voltage check of electrical system 11-5. BATTERY ELECTROLYTE COR- with portable precision voltmeter. ROSION. Corrosion found on or near lead- acid batteries can be removed mechanically n. Condition of electric lamps. with a stiff bristle brush and then chemically neutralized with a 10 percent sodium bicar- o. Missing safety shields on exposed bonate and water solution. For Nickel Cad- high-voltage terminals (i.e., 115/200V ac). mium (NiCad) batteries, a 3 percent solution of acetic acid can be used to neutralize the 11-3. FUNCTIONAL CHECK OF electrolyte. After neutralizing, the battery STAND-BY OR EMERGENCY EQUIP- should be washed with clean water and thor- MENT. An aircraft should have functional oughly dried. tests performed at regular intervals as pre- scribed by the manufacturer. The inspections 11-6. ADJUSTMENT AND REPAIR. Ac- or functional check periods should be clearly complish adjustments to items of equipment stated in the aircraft maintenance manual, such as regulators, alternators, generators, along with the overhaul intervals. contactors, control devices, inverters, and re- lays at a location outside the aircraft, and on a 11-4. CLEANING AND PRESERVA- test stand or test bench where all necessary in- TION. Annual cleaning of electrical equip- struments and test equipment are at hand. ment to remove dust, dirt, and grime is rec- Follow the adjustment and repair procedures ommended. Suitable solvents or fine abrasives outlined by the equipment or aircraft manu- that will not score the surface or remove the facturer. Replacement or repair must be ac- plating may be used to clean the terminals and complished as a part of routine maintenance. mating surfaces if they are corroded or dirty. Adjustment of a replacement voltage regulator Only cleaning agents that do not leave any type is likely since there will always be a difference of residue must be used. Components must be in impedance between the manufacturer’s test cleaned and preserved in accordance with the equipment and the aircraft’s electrical system. aircraft handbooks or manufacturer’s instruc- tions. Avoid using emery cloth to polish 11-7. INSULATION OF ELECTRICAL commutators or slip rings because particles EQUIPMENT. In some cases, electrical may cause shorting and burning. Be sure that equipment is connected into a heavy current protective finishes are not scored or damaged circuit, perhaps as a control device or relay. when cleaning. Ensure that metal-to-metal Such equipment is normally insulated from the electrically bonded surfaces are treated at the mounting structure since grounding the frame interface with a suitable anti-corrosive con- of the equipment may result in a serious ductive coating, and that the joint is sealed ground fault in the event of equipment internal around the edges by restoring the original failure. Stranded 18 or 20 AWG wire should primer and paint finish. Connections that must be used as a grounding strap to avoid shock withstand a highly corrosive environment may hazard to equipment and personnel. If the end be encapsulated with an approved sealant in connection is used for shock hazard, the order to prevent corrosion. ground wire must be large enough to carry the highest possible current (0.1 to 0.2 ohms CAUTION: Turn power off before max.). cleaning. Page 11-2 Par 11-2 9/8/98 AC 43.13-1B 11-8. BUS BARS. Annually check bus bars for general condition, cleanliness, and security of all attachments and terminals. Grease, cor- rosion, or dirt on any electrical junction may cause the connections to overheat and eventu- ally fail. Bus bars that exhibit corrosion, even in limited amounts, should be disassembled, cleaned and brightened, and reinstalled. 11-14. [RESERVED.] 11-9. Par 11-8 Page 11-3 (and 11-4) 9/8/98 AC 43.13-1B SECTION 2. STORAGE BATTERIES 11-15. GENERAL. Aircraft batteries may 1.4 and 1.5 volts per cell are generally used. In be used for many functions, e.g., ground all cases, follow the recommendations of the power, emergency power, improving DC bus battery manufacturer. stability, and fault-clearing. Most small pri- vate aircraft use lead-acid batteries. Most 11-17. BATTERY FREEZING. Discharged commercial and military aircraft use NiCad lead-acid batteries exposed to cold tempera- batteries. However, other types are becoming tures are subject to plate damage due to freez- available such as gel cell and sealed lead-acid ing of the electrolyte. To prevent freezing batteries. The battery best suited for a par- damage, maintain each cell’s specific gravity ticular application will depend on the relative at 1.275, or for sealed lead-acid batteries check importance of several characteristics, such as “open” circuit voltage. (See table 11-1.) Ni- weight, cost, volume, service or shelf life, dis- Cad battery electrolyte is not as susceptible to charge rate, maintenance, and charging rate. freezing because no appreciable chemical Any change of battery type may be considered change takes place between the charged and a major alteration. discharged states. However, the electrolyte will freeze at approximately minus 75 °F. a. Storage batteries are usually identified by the material used for the plates. All battery NOTE: Only a load check will deter- types possess different characteristics and, mine overall battery condition. therefore, must be maintained in accordance with the manufacturer’s recommendations.. TABLE 11-1. Lead-acid battery electrolyte freezing points. State of Charge (SOC) for sealed WARNING: It is extremely danger- Specific Freeze point lead-acid batteries at 70° ous to store or service lead-acid and Gravity C. F. SOC 12 volt 24 volt 1.300 -70 -95 100% 12.9 25.8 NiCad batteries in the same area. In- 1.275 -62 -80 75% 12.7 25.4 troduction of acid electrolytes into al- 1.250 -52 -62 50% 12.4 24.8 1.225 -37 -35 25% 12.0 24.0 kaline electrolyte will destroy the Ni- 1.200 -26 -16 Cad and vice-versa. 1.175 -20 -4 1.150 -15 +5 1.125 -10 +13 11-16. BATTERY CHARGING. Operation 1.100 -8 +19 of storage batteries beyond their ambient tem- perature or charging voltage limits can result in 11-18. TEMPERATURE CORRECTION. excessive cell temperatures leading to electro- U.S. manufactured lead-acid batteries are con- lyte boiling, rapid deterioration of the cells, sidered fully charged when the specific gravity and battery failure. The relationship between reading is between 1.275 and 1.300. A maximum charging voltage and the number of 1/3 discharged battery reads about 1.240 and a cells in the battery is also significant. This will 2/3 discharged battery will show a specific determine (for a given ambient temperature gravity reading of about 1.200, when tested by and state of charge) the rate at which energy is a hydrometer and the electrolyte temperature is absorbed as heat within the battery. For lead- 80 §F. However, to determine precise specific acid batteries, the voltage per cell must not ex- gravity readings, a temperature correction (see ceed 2.35 volts. In the case of NiCad batteries, table 11-2) should be applied to the the charging voltage limit varies with design and construction. Values of Par 11-15 Page 11-5 AC 43.13-1B 9/8/98 hydrometer indication. As an example, a hy- wiring and connectors or accumulation of drometer reading of 1.260 and the temperature powdered salts). If the battery needs to be re- of the electrolyte at 40 °F, the corrected spe- filled often, with no evidence of external leak- cific gravity reading of the electrolyte is 1.244. age, this may indicate a poor state of the bat- tery, the battery charging system, or an over TABLE 11-2. Sulfuric acid temperature correction. charge condition. Electrolyte Temperature Points to be subtracted or added to (1) Use a hydrometer to determine the specific gravity readings specific gravity of the battery electrolyte, °C °F which is the weight of the electrolyte com- 60 140 +24 55 130 +20 pared to the weight of pure water. 49 120 +16 43 110 +12 38 100 +8 (2) Take care to ensure the electrolyte is 33 90 +4 returned to the cell from which it was ex- 27 80 0 23 70 -4 tracted. When a specific gravity difference 15 60 -8 of 0.050 or more exists between cells of a bat- 10 50 -12 5 40 -16 tery, the battery is approaching the end of its -2 30 -20 useful life and replacement should be consid- -7 20 -24 -13 10 -28 ered. Electrolyte level may be adjusted by the -18 0 -32 addition of distilled water. -23 -10 -36 -28 -20 -40 -35 -30 -44 c. State of Charge. Battery state of charge will be determined by the cumulative 11-19. BATTERY MAINTENANCE. effect of charging and discharging the battery. Battery inspection and maintenance procedures In a normal electrical charging system the bat- vary with the type of chemical technology and tery’s generator or alternator restores a battery the type of physical construction. Always fol- to full charge during a flight of one hour to low the battery manufacturer’s approved pro- ninety minutes. cedures. Battery performance at any time in a given application will depend upon the bat- d. Mechanical Integrity. Proper me- tery’s age, state of health, state of charge, and chanical integrity involves the absence of any mechanical integrity. physical damage as well as assurance that hardware is correctly installed and the battery a. Age. To determine the life and age of is properly connected. Battery and battery the battery, record the install date of the battery compartment venting system tubes, nipples on the battery. During normal battery mainte- and attachments, when required, provide a nance, battery age must be documented either means of avoiding the potential buildup of ex- in the aircraft maintenance log or in the shop plosive gases, and should be checked periodi- maintenance log. cally to ensure that they are securely connected and oriented in accordance with the mainte- b. State of Health. Lead-acid battery nance manual’s installation procedures. Al- state of health may be determined by duration ways follow procedures approved for the spe- of service interval (in the case of vented bat- cific aircraft and battery system to ensure that teries), by environmental factors (such as ex- the battery system is capable of delivering cessive heat or cold), and by observed electro- specified performance. lyte leakage (as evidenced by corrosion of Page 11-6 Par 11-18 9/8/98 AC 43.13-1B e. Battery and Charger Characteristics. weakening of a cell. After replacing the bad The following information is provided to ac- cell with a good cell, the battery’s life can be quaint the user with characteristics of the more extended for five or more years. Full dis- common aircraft battery and battery charger charge is not harmful to this type of battery. types. Products may vary from these descrip- tions due to different applications of available (6) NiCad sealed batteries are similar in technology. Consult the manufacturer for spe- most respects to NiCad vented batteries, but do cific performance data. not normally require the addition of water. Fully discharging the battery (to zero volts) NOTE: Under no circumstances con- may cause irreversible damage to one or more nect a lead-acid battery to a charger, cells, leading to eventual battery failure due to unless properly serviced. low capacity. (1) Lead-acid vented batteries have a (7) The state of charge of a NiCad bat- two volt nominal cell voltage. Batteries are tery cannot be determined by measuring the constructed so that individual cells cannot be specific gravity of the potassium hydroxide removed. Occasional addition of water is re- electrolyte. The electrolyte specific gravity quired to replace water loss due to overcharg- does not change with the state of charge. The ing in normal service. Batteries that become only accurate way to determine the state of fully discharged may not accept recharge. charge of a NiCad battery is by a measured discharge with a NiCad battery charger and (2) Lead-acid sealed batteries are simi- following the manufacturer’s instructions. lar in most respects to lead-acid vented batter- After the battery has been fully charged and ies, but do not require the addition of water. allowed to stand for at least two hours, the fluid level may be adjusted, if necessary, using (3) The lead-acid battery is economical distilled or demineralized water. Because the and has extensive application, but is heavier fluid level varies with the state of charge, wa- than an equivalent performance battery of an- ter should never be added while the battery is other type. The battery is capable of a high installed in the aircraft. Overfilling the battery rate of discharge and low temperature per- will result in electrolyte spewage during formance. However, maintaining a high rate charging. This will cause corrosive effects on of discharge for a period of time usually warps the cell links, self-discharge of the battery, di- the cell plates, shorting out the battery. Its lution of the electrolyte density, possible electrolyte has a moderate specific gravity, and blockage of the cell vents, and eventual cell state of charge can be checked with a hy- rupture. drometer. (8) Lead-acid batteries are usually (4) Do not use high amperage automo- charged by regulated DC voltage sources. This tive battery chargers to charge aircraft allows maximum accumulation of charge in batteries. the early part of recharging. (5) NiCad vented batteries have a (9) Constant-current battery chargers 1.2 volt nominal cell voltage. Occasional ad- are usually provided for NiCad batteries be- dition of distilled water is required to replace cause the NiCad cell voltage has a negative water loss due to overcharging in normal temperature coefficient. With a constant- service. Cause of failure is usually shorting or voltage charging source, a NiCad battery Par 11-19 Page 11-7 AC 43.13-1B 9/8/98 having a shorted cell might overheat due to ex- g. Aircraft Battery Inspection. cessive overcharge and undergo a thermal run- away, destroying the battery and creating a (1) Inspect battery sump jar and lines possible safety hazard to the aircraft. for condition and security. DEFINITION: Thermal runaway can (2) Inspect battery terminals and quick- result in a chemical fire and/or explo- disconnect plugs and pins for evidence of cor- sion of the NiCad battery under re- rosion, pitting, arcing, and burns. Clean as re- charge by a constant-voltage source, quired. and is due to cyclical, ever-increasing temperature and charging current. (3) Inspect battery drain and vent lines One or more shorted cells or an exist- for restriction, deterioration, and security. ing high temperature and low charge can produce the cyclical sequence of (4) Routine pre-flight and post-flight events: (1) excessive current, inspection procedures should include observa- (2) increased temperature, tion for evidence of physical damage, loose (3) decreased cell(s) resistance, connections, and electrolyte loss. (4) further increased current, and (5) further increased temperature. 11-20. ELECTROLYTE SPILLAGE. This will not become a self-sustaining Spillage or leakage of electrolyte may result in thermal-chemical action if the con- serious corrosion of the nearby structure or stant-voltage charging source is re- control elements as both sulfuric acid and po- moved before the battery temperature tassium hydroxide are actively corrosive. is in excess of 160 °F. Electrolyte may be spilled during ground servicing, leaked when cell case rupture oc- (10) Pulsed-current battery chargers are curs, or sprayed from cell vents due to exces- sometimes provided for NiCad batteries. sive charging rates. If the battery is not case enclosed, properly treat structural parts near CAUTION: It is important to use the the battery that may be affected by acid fumes. proper charging procedures for bat- Treat all case and drain surfaces, that have teries under test and maintenance. been affected by electrolyte, with a solution of These charging regimes for recondi- sodium bicarbonate (for acid electrolyte) or tioning and charging cycles are de- boric acid, vinegar, or a 3 percent solution of fined by the aircraft manufacturer acetic acid (for potassium hydroxide and should be closely followed. electrolyte). f. Shop-Level Maintenance Procedures. CAUTION: Serious burns will result Shop procedures must follow the manufac- if the electrolyte comes in contact with turer’s recommendations. Careful examination any part of the body. Use rubber of sealed batteries and proper reconditioning of gloves, rubber apron, and protective vented batteries will ensure the longest possi- goggles when handling electrolyte. If ble service life. sulfuric acid is splashed on the body, Page 11-8 Par 11-19 9/8/98 AC 43.13-1B neutralize with a solution of baking c. Battery Venting. Battery fumes and soda and water, and shower or flush gases may cause an explosive mixture or con- the affected area with water. For the taminated compartments and should be dis- eyes, use an eye fountain and flush persed by adequate ventilation. Venting sys- with an abundance of water. If potas- tems often use ram pressure to flush fresh air sium hydroxide contacts the skin, neu- through the battery case or enclosure to a safe tralize with 9 percent acetic acid, overboard discharge point. The venting sys- vinegar, or lemon juice and wash with tem pressure differential should always be water. For the eyes, wash with a weak positive, and remain between recommended solution of boric acid or a weak solu- minimum and maximum values. Line runs tion of vinegar and flush with water. should not permit battery overflow fluids or condensation to be trapped and prevent free 11-21. NOXIOUS FUMES. When charging airflow. rates are excessive, the electrolyte may boil to the extent that fumes containing droplets of the d. Battery Sump Jars. A battery sump electrolyte are emitted through the cell vents. jar installation may be incorporated in the These fumes from lead-acid batteries may be- venting system to dispose of battery electrolyte come noxious to the crew members and pas- overflow. The sump jar should be of adequate sengers; therefore, thoroughly check the vent- design and the proper neutralizing agent used. ing system. NiCad batteries will emit gas near The sump jar must be located only on the dis- the end of the charging process and during charge side of the battery venting system. (See overcharge. The battery vent system in the air- figure 11-1.) craft should have sufficient air flow to prevent this explosive mixture from accumulating. It is often advantageous to install a jar in the battery vent discharge system serviced with an agent to neutralize the corrosive effect of bat- tery vapors. 11-22. INSTALLATION PRACTICES. a. External Surface. Clean the external surface of the battery prior to installation in the aircraft. b. Replacing Lead-Acid Batteries. When replacing lead-acid batteries with NiCad FIGURE 11-1. Battery ventilating systems. batteries, a battery temperature or current monitoring system must be installed. Neu- e. Installing Batteries. When installing tralize the battery box or compartment and batteries in an aircraft, exercise care to prevent thoroughly flush with water and dry. A flight inadvertent shorting of the battery terminals. manual supplement must also be provided for Serious damage to the aircraft structure (frame, the NiCad battery installation. Acid residue skin and other subsystems, avionics, wire, fuel can be detrimental to the proper functioning of etc.) can be sustained by the resultant high dis- a NiCad battery, as alkaline will be to a lead- charge of electrical energy. This condition acid battery. Par 11-20 Page 11-9 AC 43.13-1B 9/8/98 may normally be avoided by insulating the g. Quick-Disconnect Type Battery. If a terminal posts during the installation process. quick-disconnect type of battery connector, that prohibits crossing the battery lead is not Remove the grounding lead first for battery employed, ensure that the aircraft wiring is removal, then the positive lead. Connect the connected to the proper battery terminal. Re- grounding lead of the battery last to minimize verse polarity in an electrical system can seri- the risk of shorting the “hot terminal” of the ously damage a battery and other electrical battery during installation. components. Ensure that the battery cable connections are tight to prevent arcing or a f. Battery Hold Down Devices. Ensure high resistance connection. that the battery hold down devices are secure, but not so tight as to exert excessive pressure 11-29. [RESERVED.] 11-23. that may cause the battery to buckle causing internal shorting of the battery. Page 11-10 Par 11-22 9/27/01 AC 43.13-1B CHG 1 SECTION 3. INSPECTION OF EQUIPMENT INSTALLATION 11-30. GENERAL. When installing equip- ode. The best protection against diode destruction ment which consumes electrical power in an by voltage surges is to make certain that the bat- aircraft, it should be determined that the total tery is never disconnected from the aircraft's electrical load can be safely controlled or man- electrical system when the alternator is in op- aged within the rated limits of the affected eration. The battery acts as a large capacitor components of the aircraft’s electrical power and tends to damp out voltage surges. The supply system. Addition of most electrical battery must never be connected with reversed utilization equipment is a major alteration and polarity as this may subject the diodes to a requires appropriate FAA approval. The elec- forward bias condition, allowing very high cur- trical load analysis must be prepared in general rent conduction that will generally destroy accordance with good engineering practices. them instantly. Additionally, an addendum to the flight man- ual is generally required. 11-34. STATIC ELECTRICAL POWER CONVERTERS. Static power converters em- 11-31. INSTALLATION CLEARANCE ploy solid-state devices to convert the aircraft’s PROVISIONS. All electrical equipment primary electrical source voltage to a different should be installed so that inspection and voltage or frequency for the operation of radio maintenance may be performed and that the in- and electronic equipment. They contain no stallation does not interfere with other systems, moving parts (with the exception of a cooling such as engine or flight controls. fan on some models) and are relatively main- tenance free. Various types are available for ac 11-32. WIRES, WIRE BUNDLES, AND to dc or dc to ac conversion. CIRCUIT PROTECTIVE DEVICES. Be- fore any aircraft electrical load is increased, the a. Location of static converters should new total electrical load (previous maximum be carefully chosen to ensure adequate venti- load plus added load) must be checked to de- lation for cooling purposes. Heat-radiating fins termine if the design levels are being ex- should be kept clean of dirt and other foreign ceeded. Where necessary, wires, wire bundles, matter that may impair their cooling proper- and circuit protective devices having the cor- ties. rect ratings should be added or replaced. b. Static power converters often emit un- 11-33. ALTERNATOR DIODES. Alter- acceptable levels of EMI that may disrupt nators employ diodes for the purpose of con- communication equipment and navigation in- verting the alternating current to direct current. struments. Properly shielded connectors, ter- These diodes are solid-state electronic devices minal blocks, and wires may be required, with and are easily damaged by rough handling, all shields well grounded to the airframe. abuse, over heating, or reversing the battery connections. A voltage surge in the line, if it CAUTION: Do not load convert- exceeds the design value, may destroy the di- ers beyond their rated capacity. Par 11-30 Page 11-11 AC 43.13-1B CHG 1 9/27/01 11-35. ACCEPTABLE MEANS OF d. In installations where the ammeter is CONTROLLING OR MONITORING THE in the generator or alternator lead and the ELECTRICAL LOAD. regulator system does not limit the maximum current that the generator or alternator can de- a. Output Rating. The generator or al- liver, the ammeter can be redlined at ternator output ratings and limits prescribed by 100 percent of the generator or alternator rat- the manufacturer must be checked against the ing. If the ammeter reading is never allowed electrical loads that can be imposed on the af- to exceed the red line, except for short inter- fected generator or alternator by installed mittent loads, the generator or alternator will equipment. When electrical load calculations not be overloaded. show that the total continuous electrical load can exceed 80 percent output load limits of the e. Where the use of placards or moni- generator or alternator, and where special plac- toring devices is not practical or desired, and ards or monitoring devices are not installed, where assurance is needed that the battery will the electrical load must be reduced or the gen- be charged in flight, the total continuous con- erating capacity of the charging system must nected electrical load should be held to ap- be increased. (This is strictly a “rule of thumb” proximately 80 percent of the total generator method and should not be confused with an output capacity. When more than one genera- electrical load analysis, which is a complete tor is used in parallel, the total rated output is and accurate analysis, which is a complete and the combined output of the installed genera- accurate of the composite aircraft power tors. sources and all electrical loads) When a stor- age battery is part of the electrical power sys- f. When two or more generators and al- tem, the battery will be continuously charged ternators are operated in parallel and the total in flight. connected system load can exceed the rated output of a single generator, a method should b. The use of placards is recommended be provided for quickly coping with a sudden to inform the pilot and/or crew members of the overload that can be caused by generator or combination(s) of loads that may be connected engine failure. A quick load reduction system to each power source. Warning lights can be or procedure should be identified whereby the installed that will be triggered if the battery total load can be reduced by the pilot to a bus voltage drops below 13 volts on a 14-volt quantity within the rated capacity of the re- system or 26 volts on a 28-volt system. maining operable generator or generators. c. For installations where the ammeter is 11-36. ELECTRICAL LOAD DETER- in the battery lead, and the regulator system MINATION. The connected load of an air- limits the maximum current that the generator craft’s electrical system may be determined by or alternator can deliver, a voltmeter can be in- any one or a combination of several acceptable stalled on the system bus. As long as the am- methods, techniques, or practices. However, meter never reads “discharge” (except for short those with a need to know the status of a par- intermittent loads such as operating the gear ticular aircraft’s electrical system should have and flaps) and the voltmeter remains at “sys- accurate and up-to-date data concerning the tem voltage,” the generator or alternator will capacity of the installed electrical power not be overloaded. source(s) and the load(s) imposed by installed electrical power-consuming devices. Such Page 11-12 Par 11-35 9/27/01 AC 43.13-1B CHG 1 data should provide a true picture of the status c. Wiring. Junction box layouts should of the electrical system. New or additional take into consideration the necessity for ade- electrical devices should not be installed in an quate wiring space and possible future addi- aircraft, nor the capacity changed of any power tions. Electrical wire bundles should be laced source, until the status of the electrical system or clamped inside the box so that cables do not in the aircraft has been determined accurately touch other components, prevent ready access, and found not to adversely affect the integrity or obscure markings or labels. Cables at en- of the electrical system. trance openings should be protected against chafing by using grommets or other suitable 11-37. JUNCTION BOX CONSTRUC- means. TION. Replacement junction boxes should be fabricated using the same material as the origi- 11-46. [RESERVED.] 11-38. nal or from a fire-resistant, nonabsorbent mate- rial, such as aluminum, or an acceptable plastic material. Where fire-proofing is necessary, a stainless steel junction box is recommended. Rigid construction will prevent “oil-canning” of the box sides that could result in internal short circuits. In all cases, drain holes should be provided in the lowest portion of the box. Cases of electrical power equipment must be insulated from metallic structure to avoid ground fault related fires. (See para- graph 11-7.) a. Internal Arrangement. The junction box arrangement should permit easy access to any installed items of equipment, terminals, and wires. Where marginal clearances are un- avoidable, an insulating material should be in- serted between current carrying parts and any grounded surface. It is not good practice to mount equipment on the covers or doors of junction boxes, since inspection for internal clearance is impossible when the door or cover is in the closed position. b. Installation. Junction boxes should be securely mounted to the aircraft structure in such a manner that the contents are readily ac- cessible for inspection. When possible, the open side should face downward or at an angle so that loose metallic objects, such as washers or nuts, will tend to fall out of the junction box rather than wedge between terminals. Par 11-38 Page 11-13 (and 11-14) 9/8/98 AC 43.13-1B SECTION 4. INSPECTION OF CIRCUIT-PROTECTION DEVICES 11-47. GENERAL. All electrical wires TABLE 11-3. DC wire and circuit protector chart. must be provided with some means of circuit Wire AN gauge copper Circuit breaker amp. Fuse amp. protection. Electrical wire should be protected 22 5 5 with circuit breakers or fuses located as close 20 7.5 5 as possible to the electrical power source bus. 18 10 10 Normally, the manufacturer of electrical 16 15 10 14 20 15 equipment will specify the fuse or breaker to 12 30 20 be used when installing the respective equip- 10 40 30 ment, or SAE publication, ARP 1199, may be 8 50 50 6 80 70 referred to for recommended practices. 4 100 70 2 125 100 11-48. DETERMINATION OF CIRCUIT 1 150 BREAKER RATINGS. Circuit protection 0 150 devices must be sized to supply open circuit Basis of chart: (1) Wire bundles in 135 °F. ambient and altitudes up to capability. A circuit breaker must be rated so 30,000 feet. that it will open before the current rating of the (2) Wire bundles of 15 or more wires, with wires carrying no more than 20 percent of the total current carrying wire attached to it is exceeded, or before the capacity of the bundle as given in Specification cumulative rating of all loads connected to it MIL-W-5088 (ASG). (3) Protectors in 75 to 85 °F. ambient. are exceeded, whichever is lowest. A circuit (4) Copper wire Specification MIL-W-5088. breaker must always open before any compo- (5) Circuit breakers to Specification MIL-C-5809 or equivalent. nent downstream can overheat and generate (6) Fuses to Specification MIL-F-15160 or equivalent. smoke or fire. Wires must be sized to carry continuous current in excess of the circuit protective device rating, including its time- 11-50. RESETTABLE CIRCUIT PRO- current characteristics, and to avoid excessive TECTION DEVICES. voltage drop. Refer to section 5 for wire rating methods. a. All resettable type circuit breakers must open the circuit irrespective of the posi- 11-49. DC CIRCUIT PROTECTOR tion of the operating control when an overload CHART. Table 11-3 may be used as a guide or circuit fault exists. Such circuit breakers are for the selection of circuit breaker and fuse referred to as “trip free.” rating to protect copper conductor wire. This chart was prepared for the conditions speci- b. Automatic reset circuit breakers, that fied. If actual conditions deviate materially automatically reset themselves periodically, are from those stated, ratings above or below the not recommended as circuit protection devices values recommended may be justified. For ex- for aircraft. ample, a wire run individually in the open air may possibly be protected by the circuit 11-51. CIRCUIT BREAKER USAGE. breaker of the next higher rating to that shown Circuit breakers are designed as circuit protec- on the chart. In general, the chart is conserva- tion for the wire (see paragraph 11-48 tive for all ordinary aircraft electri- and 11-49), not for protection of black boxes cal installations. Par 11-47 Page 11-15 AC 43.13-1B CHG 1 9/27/01 or components. Use of a circuit breaker as a b. Electromechanical Switches. switch is not recommended. Use of a circuit Switches have electrical contacts and various breaker as a switch will decrease the life of the types of switch actuators (i.e., toggle, plunger, circuit breaker. push-button, knob, rocker). 11-52. CIRCUIT BREAKER MAINTE- (1) Contacts designed for high-level NANCE. Circuit breakers should be periodi- loads must not be subsequently used for low- cally cycled with no load to enhance contact level applications, unless testing has been per- performance by cleaning contaminants from formed to establish this capability. the contact surfaces. (2) Switches are specifically selected 11-53. SWITCHES. In all circuits where a based on the design for the aircraft service cur- switch malfunction can be hazardous, a switch rent ratings for lamp loads, inductive loads, specifically designed for aircraft service should and motor loads and must be replaced with be used. These switches are of rugged con- identical make and model switches. struction and have sufficient contact capacity to break, make, and continuously carry the c. Proximity Switches. These switches connected load current. The position of the are usually solid-state devices that detect the switch should be checked with an electrical presence of a predetermined target without meter. physical contact and are usually rated 0.5 amps or less. a. Electrical Switch Inspection. Special attention should be given to electrical circuit d. Switch Rating. The nominal current switches, especially the spring-loaded type, rating of the conventional aircraft switch is during the course of normal airworthiness in- usually stamped on the switch housing and spection. An internal failure of the spring- represents the continuous current rating with loaded type may allow the switch to remain the contacts closed. Switches should be der- closed even though the toggle or button returns ated from their nominal current rating for the to the “off” position. During inspection, at- following types of circuits: tention should also be given to the possibility that improper switch substitution may have (1) Circuits containing incandescent been made. lamps can draw an initial current that is 15 times greater than the continuous current. (1) With the power off suspect aircraft Contact burning or welding may occur when electrical switches should be checked in the the switch is closed. ON position for opens (high resistance) and in The OFF position for shorts (low resistance), (2) Inductive circuits have magnetic en- with an ohmmeter. ergy stored in solenoid or relay coils that is released when the control switch is opened and (2) Any abnormal side to side move- may appear as an arc. ment of the switch should be an alert to immi- nent failure even if the switch tested was (3) Direct-current motors will draw shown to be acceptable with an ohmmeter. several times their rated current during start- ing, and magnetic energy stored in their Page 11-16 Par 11-51 9/8/98 AC 43.13-1B armature and field coils is released when the g. Low Energy Loads. Switches rated control switch is opened. for use at 28 VDC or more, and at 1.0 amp or more, generally have silver contacts. In gen- e. Switch Selection. Switches for aircraft eral, silver contacts should not be used to con- use should be selected with extreme caution. trol devices which have either a voltage less The contact ratings should be adequate for all than 8 volts or a continuous current less than load conditions and applicable voltages, at 0.5 amps unless the switch is specifically rated both sea level and the operational altitude. for use with low-energy loads. Table 11-5 Consideration should be given to the variation provides general guidelines for selecting con- in the electrical power characteristics, using tact materials for low-energy loads, but is not MIL-STD-704 as a guide. applicable to hermetically sealed switches. f. Derating Factors. Table 11-4 provides (1) Typical logic load devices have a an approximate method for derating nominal voltage of 0.5 volts to 28 volts and a continu- ratings to obtain reasonable switch efficiency ous current of less than 0.5 amps. A suitable and service life under reactive load conditions. method of rating switches for use on logic load devices is specified in ANSI/EIA 5200000. WARNING: Do not use AC derated (General specification for special use electro- switches in DC circuits. AC switches mechanical switches of certified quality.) will not carry the same amperage as a DC switch. TABLE 11-5. Selection of contact material. TABLE 11-4. Switch derating factors. Nominal Type of Load Derating System Factor Voltage 28 VDC Lamp 8 28 VDC Inductive (relay-solenoid) 4 28 VDC Resistive (Heater) 2 28 VDC Motor 3 12 VDC Lamp 5 12 VDC Inductive (relay-solenoid) 2 12 VDC Resistive (Heater) 1 12 VDC Motor 2 NOTES: NOTES: 1. If sulfide, moisture, or any form of contamination is present, a sealed switch should be used. The degree 1. To find the nominal rating of a switch required to operate of sealing required (environmental or hermetic) is de- a given device, multiply the continuous current rating pendent upon the environment in which the switch is of the device by the derating factor corresponding intended to be operated. to the voltage and type of load. 2. If particle contamination in any form is likely to reach 2. To find the continuous rating that a switch of a the contacts, bifurcated contacts should be used. given nominal rating will handle efficiently, divide the switch nominal rating by the derating 3. Low-voltage high-current loads are difficult to predict factor corresponding to the voltage and type of load. and may result in a combined tendency of noncontact, sticking, and material transfer. 4. High-voltage high-current applications may require the use of Silver Nickel contacts. Par 11-53 Page 11-17 AC 43.13-1B CHG 1 9/27/01 (2) Typical low-level load devices have (2) The arcing of electromechanical a voltage of less than 0.5 volts and a continu- switch contacts generates short duration ous current of less than 0.5 amps. A suitable EMI/RFI when controlling highly inductive method of rating switches for use on logic load electrical loads. Twisting lead wires, metal devices is specified in ANSI/EIA 5200000. overbraids, and lead wire routing can reduce or eliminate generation problems when dealing h. Shock and Vibration. with arcing loads. Proximity sensors generally use a relatively low-energy electromagnetic (1) Electromechanical switches (toggle field to sense the target. Adequate spacing is switches) are most susceptible to shock and required to prevent interference between adja- vibration in the plane that is parallel to contact cent proximity sensors or other devices sus- motion. Under these conditions the switch ceptible to EMI/RFI. Refer to manufacturer’s contacts may momentarily separate. instructions. ANSI/EIA 5200000 specifies that contact separations greater than 10 microseconds and b. Temperature. that closing of open contacts in excess of 1 microsecond are failures. Repeated contact (1) Electromechanical switches can separations during high levels of vibration or withstand wide temperature ranges and rapid shock may cause excessive electrical degrada- gradient shifts without damage. Most aircraft tion of the contacts. These separations can switches operate between -55 °C and 85 °C also cause false signals to be registered by with designs available from -185 °C to 260 °C electronic data processors without proper buff- or more. Higher temperatures require more ering. exotic materials, which can increase costs and limit life. It should be noted that o-ring seals (2) Although proximity switches do not and elastomer boot seals tend to stiffen in ex- have moving parts, the reliability of the inter- treme cold. This can increase operating forces nal electronic parts of the switch may be re- and reduce release forces or stop the switch duced. Reliability and mean time between- from releasing. failure (MTBF) calculations should reflect the applicable environment. Note that the mount- (2) Proximity sensors are normally de- ing of both the proximity sensor and its target signed for environments from -55 °C to must be rigid enough to withstand shock or vi- 125 °C. During temperature excursions, the bration to avoid creating false responses. operating and release points may shift from 5 percent to 10 percent. Reliability of the i. Electromagnetic/Radio Frequency In- proximity sensor will typically be highest at terference (EMI/RFI). room temperature. The reliability and MTBF estimates should be reduced for use under high (1) DC operated electromechanical temperatures or high thermal gradients. switches are usually not susceptible to EMI/RFI. Proximity switches are susceptible c. Sealing. to an EMI/RFI environment and must be evaluated in the application. Twisting lead NOTE: The materials used for sealing wires, metal overbraids, lead wire routing, and (o-rings, potting materials, etc.) the design of the proximity switch can mini- should be compatible with any air- mize susceptibility. craft fluids to which the switch may be exposed. Page 11-18 Par 11-53 9/8/98 AC 43.13-1B (1) Electromechanical switches range in a. Use of Relays. Most relays are used as sealing from partially sealed to hermetically a switching device where a weight reduction sealed. Use a sealed switch when the switch can be achieved, or to simplify electrical con- will be exposed to a dirty environment during trols. It should be remembered that the relay is storage, assembly, or operation. Use a higher an electrically operated switch, and therefore level of sealing when the switch will not have subject to dropout under low system voltage an arcing load to self-clean the contacts. Low- conditions. energy loads tend to be more susceptible to contamination. b. Types of Connections. Relays are manufactured with various connective means (2) Proximity switches for aircraft ap- from mechanical to plug-in devices. Installa- plications typically have a metal face and pot- tion procedures vary by the type of connection ting material surrounding any electronics and and should be followed to ensure proper op- lead wire exits. The potting material should be eration of the relay. compatible with the fluids the switch will be exposed to in the environment. The plastic c. Repair. Relays are complicated elec- sensing face of some proximity switches may tromechanical assemblies and most are not re- be subject to absorption of water that may pairable. cause the operating point to shift should be protected. d. Relay Selection. d. Switch Installation. Hazardous errors (1) Contact ratings, as described on the in switch operation may be avoided by logical relay case, describe the make, carry, and break and consistent installation. “On-off” capability for resistive currents only. Consult two-position switches should be mounted so the appropriate specification to determine the that the “on” position is reached by an upward derating factor to use for other types of current or forward movement of the toggle. When the loads. (Ref. MIL-PRF-39016, MIL-PRF-5757, switch controls movable aircraft elements, MIL-PRF-6016, MIL-PRF-835836.) such as landing gear or flaps, the toggle should move in the same direction as the desired mo- (2) Operating a relay at less than nomi- tion. Inadvertent operation of switches can be nal coil voltage may compromise its perform- prevented by mounting suitable guards over ance and should never be done without written the switches. manufacturer approval. 11-48. RELAYS. A relay is an electrically e. Relay Installation and Maintenance. controlled device that opens and closes electri- For installation and maintenance, care should cal contacts to effect the operation of other de- be taken to ensure proper placement of hard- vices in the same or in another electrical cir- ware, especially at electrical connections. The cuit. The relay converts electrical energy into use of properly calibrated torque wrenches and mechanical energy through various means, and following the manufacturer’s installation pro- through mechanical linkages, actuates electri- cedures is strongly recommended. This is es- cal conductors (contacts) that control electrical pecially important with hermetically sealed circuits. Solid-state relays may also be used in relays, since the glass-to-metal seal (used for electrical switching applications. Par 11-53 Page 11-19 AC 43.13-1B CHG 1 9/27/01 insulation of the electrically “live” compo- 11-49. LOAD CONSIDERATIONS. nents) is especially vulnerable to catastrophic When switches or relays are to be used in ap- failure as a result of overtorquing. plications where current or voltage is substan- tially lower than rated conditions, additional (1) When replacing relays in alternating intermediate testing should be performed to current (ac) applications, it is essential to ensure reliable operation. Contact the manu- maintain proper phase sequencing. For any facturer on applications different from the application involving plug-in relays, proper rated conditions. engagement of their retaining mechanism is vital. 11-50. OPERATING CONDITIONS FOR SWITCHES AND RELAYS. Switches and (2) The proximity of certain magneti- relays should be compared to their specifica- cally permanent, magnet assisted, coil operated tion rating to ensure that all contacts are made relays may cause them to have an impact on properly under all conditions of operation, in- each other. Any manufacturer’s recommenda- cluding vibration equivalent to that in the area tions or precautions must be closely followed. of the aircraft in which the switch or relay is to be installed. 11-65. [RESERVED.] 11-57. Page 11-20 Par 11-54 9/27/01 AC 43.13-1B CHG 1 SECTION 5. ELECTRICAL WIRE RATING 11-66. GENERAL. Wires must be sized so TABLE 11-6. Tabulation chart (allowable voltage drop that they: have sufficient mechanical strength between bus and utilization equipment ground). to allow for service conditions; do not exceed Nominal Allowable voltage system drop continuous Intermittent allowable voltage drop levels; are protected by voltage operation operation system circuit protection devices; and meet circuit current carrying requirements. 14 0.5 1 28 1 2 a. Mechanical Strength of Wires. If it is 115 4 8 200 7 14 desirable to use wire sizes smaller than #20, particular attention should be given to the me- chanical strength and installation handling of bonding to the structure or a special electric these wires, e.g., vibration, flexing, and termi- current return path has been provided that is nation. Wire containing less than 19 strands capable of carrying the required electric cur- must not be used. Consideration should be rent with a negligible voltage drop. To deter- given to the use of high-strength alloy con- mine circuit resistance check the voltage drop ductors in small gauge wires to increase me- across the circuit. If the voltage drop does not chanical strength. As a general practice, wires exceed the limit established by the aircraft or smaller than size #20 should be provided with product manufacturer, the resistance value for additional clamps and be grouped with at least the circuit may be considered satisfactory. three other wires. They should also have ad- When checking a circuit, the input voltage ditional support at terminations, such as con- should be maintained at a constant value. Ta- nector grommets, strain relief clamps, shrink- bles 11-7 and 11-8 show formulas that may be able sleeving, or telescoping bushings. They used to determine electrical resistance in wires should not be used in applications where they and some typical examples. will be subjected to excessive vibration, re- peated bending, or frequent disconnection d. Resistance Calculation Methods. from screw termination. Figures 11-2 and 11-3 provide a convenient means of calculating maximum wire length for b. Voltage Drop in Wires. The voltage the given circuit current. drop in the main power wires from the genera- tion source or the battery to the bus should not (1) Values in tables 11-7 and 11-8 are exceed 2 percent of the regulated voltage when for tin-plated copper conductor wires. Be- the generator is carrying rated current or the cause the resistance of tin-plated wire is battery is being discharged at the 5-minute slightly higher than that of nickel or silver- rate. The tabulation shown in table 11-6 de- plated wire, maximum run lengths determined fines the maximum acceptable voltage drop in from these charts will be slightly less than the the load circuits between the bus and the utili- allowable limits for nickel or silver-plated zation equipment ground. copper wire and are therefore safe to use. Fig- ures 11-2 and 11-3 can be used to derive c. Resistance. The resistance of the cur- slightly longer maximum run lengths for silver rent return path through the aircraft structure is or nickel-plated wires by multiplying the generally considered negligible. However, this maximum run length by the ratio of resistance is based on the assumption that adequate of tin-plated wire, divided by the resistance of silver or nickel-plated wire. Par 11-66 Page 11-21 AC 43.13-1B CHG 1 9/27/01 TABLE 11-7. Examples of determining required tin- (3) Voltage drop calculations for alumi- plated copper wire size and checking voltage drop using num wires can be accomplished by multiplying figure 11-2 the resistance for a given wire size, defined in Check- calculated volt- table 11-10, by the wire run length and circuit Wire Size age drop (VD)= current. Run Circuit From (Resistance/Ft) Voltage Lengths Current Chart (Length) (Cur- drop (Feet) (Amps) rent) (4) When the estimated or measured 1 107 20 No. 6 VD= (.00044 ohms/ft) conductor temperature (T2) exceeds 20 °C, (107)(20)= such as in areas having elevated ambient tem- 0.942 0.5 VD= (.00028 peratures or in fully loaded power-feed wires, 90 20 No. 4 ohms/ft) the maximum allowable run length (L2), must (90)(20)= 0.504 be shortened from L1 (the 20 °C value) using 4 88 20 No. 12 VD= (.00202 the following formula for copper conductor ohms/ft) (88)(20)= wire: 3.60 7 100 20 No. 14 VD= (.00306 (254.5 °C )( L1) ohms/ft) L2 = (100)(20)= (234.5 °C )+ )(T 2) 6.12 TABLE 11-8. Examples of determining maximum tin- For aluminum conductor wire, the formula is: plated copper wire length and checking voltage drop using figure 11-2. (258.1 °C )( L1) L2 = Check-calculated (238.1 °C ) + (T 2) voltage drop Maximum (VD)= (Resis- Maximum Circuit Wire Run tance/Ft) (Length) These formulas use the reciprocal of each ma- Voltage Wire Current Length (Current) terial’s resistively temperature coefficient to drop Size (Amps) (Feet) VD= (.00126 take into account increased conductor resis- 1 No. 10 20 39 ohms/ft) tance resulting from operation at elevated tem- (39)(20)=.98 0.5 VD= (.00126 peratures. ---- 19.5 ohms/ft) (19.5)(20)= (5) To determine T2 for wires carrying a.366 4 ---- 156 VD= (.00126 high percentage of their current carrying capa- ohms/ft) bility at elevated temperatures, laboratory (156)(20)= 3.93 testing using a load bank and a high- 7 ---- 273 VD= (.00126 temperature chamber is recommended. Such ohms/ft) (273)(20)= tests should be run at anticipated worse case 6.88 ambient temperature and maximum current- loading combinations. (2) As an alternative method or a means of checking results from figure 11-2, continu- (6) Approximate T2 can be estimated ous flow resistance for a given wire size can be using the following formula: read from table 11-9 and multiplied by the wire run length and the circuit current. For inter- T2 = T1 + (TR − T1 )( I 2 / I max ) mittent flow, use figure 11-3. Page 11-22 Par 11-66 9/27/01 AC 43.13-1B CHG 1 Where: Note: Aluminum wire-From Table 11-9 and T1 = Ambient Temperature 11-10 note that the conductor resistance of T2 = Estimated Conductor Temperature aluminum wire and that of copper wire (two TR = Conductor Temperature Rating numbers higher) are similar. Accordingly, I2 = Circuit Current (A=Amps) the electric wire current in Table 11-9 can Imax = Maximum Allowable Current be used when it is desired to substitute alu- (A=Amps) at TR minum wire and the proper size can be se- This formula is quite conservative and will typi- lected by reducing the copper wire size by cally yield somewhat higher estimated tempera- two numbers and referring to Table 11-10. tures than are likely to be encountered under actual The use of aluminum wire size smaller than operating conditions. No. 8 is not recommended. TABLE 11-9. Current carrying capacity and resistance of copper wire. Wire Continuous duty current (amps)-Wires in bundles, Max. resistance Nominal Size groups, harnesses, or conduits. (See Note #1) ohms/1000ft@20 °C conductor Wire Conductor Temperature Rating tin plated conduc- area - tor 105 °C 150 °C 200 °C (See Note #2) circ.mils 24 2.5 4 5 28.40 475 22 3 5 6 16.20 755 20 4 7 9 9.88 1,216 18 6 9 12 6.23 1,900 16 7 11 14 4.81 2,426 14 10 14 18 3.06 3,831 12 13 19 25 2.02 5,874 10 17 26 32 1.26 9,354 8 38 57 71 0.70 16,983 6 50 76 97 0.44 26,818 4 68 103 133 0.28 42,615 2 95 141 179 0.18 66,500 1 113 166 210 0.15 81,700 0 128 192 243 0.12 104,500 00 147 222 285 0.09 133,000 000 172 262 335 0.07 166,500 0000 204 310 395 0.06 210,900 Note #1: Rating is for 70°C ambient, 33 or more wires in the bundle for sizes 24 through 10, and 9 wires for size 8 and larger, with no more than 20 percent of harness current carrying capacity being used, at an operating altitude of 60,000 feet. For rating of wires under other conditions or configurations see paragraph 11-69. Note #2: For resistance of silver or nickel-plated conductors see wire specifications. Par 11-66 Page 11-23 AC 43.13-1B CHG 1 9/27/01 TABLE 11-10. Current carrying capacity and resistance of aluminum wire. Continuous duty current (amps) Wire Size Wires in bundles, groups or harnesses Max. resistance or conduits (See table 11-9 Note #1) ohms/1000ft Wire conductor temperature rating @ 20 °C 105 °C 150 °C 8 30 45 1.093 6 40 61 0.641 4 54 82 0.427 2 76 113 0.268 1 90 133 0.214 0 102 153 0.169 00 117 178 0.133 000 138 209 0.109 0000 163 248 0.085 Note: Observe design practices described in paragraph 11-67 for aluminum conductor Page 11-24 Par 11-66 9/27/01 AC 43.13-1B CHG 1 11-67.METHODS FOR DETERMINING c. Single Wire in Free Air. Determining CURRENT CARRYING CAPACITY OF a wiring system’s current carrying capacity be- WIRES. This paragraph contains methods for gins with determining the maximum current determining the current carrying capacity of that a given-sized wire can carry without ex- electrical wire, both as a single wire in free air ceeding the allowable temperature difference and when bundled into a harness. It presents (wire rating minus ambient °C). The curves derating factors for altitude correction and ex- are based upon a single copper wire in free air. amples showing how to use the graphical and (See figures 11-4a and 11-4b.) tabular data provided for this purpose. In some instances, the wire may be capable of d. Wires in a Harness. When wires are carrying more current than is recommended for bundled into harnesses, the current derived for the contacts of the related connector. In this a single wire must be reduced as shown in fig- instance, it is the contact rating that dictates ure 11-5. The amount of current derating is a the maximum current to be carried by a wire. function of the number of wires in the bundle Wires of larger gauge may need to be used to and the percentage of the total wire bundle ca- fit within the crimp range of connector con- pacity that is being used. tacts that are adequately rated for the current being carried. Figure 11-5 gives a family of e. Harness at Altitude. Since heat loss curves whereby the bundle derating factor may from the bundle is reduced with increased al- be obtained. titude, the amount of current should be de- rated. Figure 11-6 gives a curve whereby the a. Effects of Heat Aging on Wire Insula- altitude-derating factor may be obtained. tion. Since electrical wire may be installed in areas where inspection is infrequent over ex- f. Aluminum Conductor Wire. When tended periods of time, it is necessary to give aluminum conductor wire is used, sizes should special consideration to heat-aging character- be selected on the basis of current ratings istics in the selection of wire. Resistance to shown in table 11-10. The use of sizes smaller heat is of primary importance in the selection than #8 is discouraged (Ref. AS50881A). of wire for aircraft use, as it is the basic factor Aluminum wire should not be attached to en- in wire rating. Where wire may be required to gine mounted accessories or used in areas operate at higher temperatures due either to having corrosive fumes, severe vibration, me- high ambient temperatures, high-current load- chanical stresses, or where there is a need for ing, or a combination of the two, selection frequent disconnection. Use of aluminum wire should be made on the basis of satisfactory is also discouraged for runs of less than 3 feet performance under the most severe operating (AS50991A). Termination hardware should be conditions. of the type specifically designed for use with aluminum conductor wiring. b. Maximum Operating Temperature. The current that causes a temperature steady 11-68. INSTRUCTIONS FOR USE OF state condition equal to the rated temperature ELECTRICAL WIRE CHART. of the wire should not be exceeded. Rated temperature of the wire may be based upon the a. Correct Size. To select the correct size ability of either the conductor or the insulation of electrical wire, two major requirements to withstand continuous operation without deg- must be met: radation. Par 11-67 Page 11-25 AC 43.13-1B CHG 1 9/27/01 (1) The wire size should be sufficient to (4) The circuit has continuous opera- prevent an excessive voltage drop while car- tion. rying the required current over the required distance. (See table 11-6, Tabulation Chart, for (5) Estimated conductor temperature is allowable voltage drops.) 20 °C or less. (2) The size should be sufficient to pre- The scale on the left of the chart represents vent overheating of the wire carrying the re- maximum wire length in feet to prevent an ex- quired current. (See paragraph 11-69 for al- cessive voltage drop for a specified voltage lowable current carrying calculation methods.) source system (e.g., 14V, 28V, 115V, 200V). This voltage is identified at the top of scale b. Two Requirements. To meet the two and the corresponding voltage drop limit for requirements (see paragraph 11-66b) in se- continuous operation at the bottom. The scale lecting the correct wire size using figure 11-2 (slant lines) on top of the chart represents am- or figure 11-3, the following must be known: peres. The scale at the bottom of the chart rep- resents wire gauge. (1) The wire length in feet. STEP 1: From the left scale find the wire (2) The number of amperes of current to length, 50 feet under the 28V source column. be carried. STEP 2: Follow the corresponding horizontal (3) The allowable voltage drop line to the right until it intersects the slanted permitted. line for the 20-amp load. (4) The required continuous or inter- STEP 3: At this point, drop vertically to the mittent current. bottom of the chart. The value falls between No. 8 and No. 10. Select the next larger size (5) The estimated or measured con- wire to the right, in this case No. 8. This is the ductor temperature. smallest size wire that can be used without ex- ceeding the voltage drop limit expressed at the (6) Is the wire to be installed in conduit bottom of the left scale. This example is plot- and/or bundle? ted on the wire chart, figure 11-2. Use figure 11-2 for continuous flow and figure 11-3 for (7) Is the wire to be installed as a single intermittent flow. wire in free air? d. Procedures in Example No. 1 para- c. Example No. 1. Find the wire size in graph 11-68c, can be used to find the wire size figure 11-2 using the following known infor- for any continuous or intermittent operation mation: (maximum two minutes). Voltage (e.g. 14 volts, 28 volts, 115 volts, 200 volts) as in- (1) The wire run is 50 feet long, in- dicated on the left scale of the wire chart in cluding the ground wire. figure 11-2 and 11-3. (2) Current load is 20 amps. e. Example No. 2. Using figure 11-2, find (3) The voltage source is 28 volts from the wire size required to meet the allowable bus to equipment. voltage drop in table 11-6 for a wire carrying Page 11-26 Par 11-68 9/27/01 AC 43.13-1B CHG 1 current at an elevated conductor temperature (3) Follow the 150 °C corresponding using the following information: horizontal line to intersect with #14 wire size, drop vertically and read 47 Amps at bottom of (1) The wire run is 15.5 feet long, in- chart (current amperes). cluding the ground wire. (4) Use figure 11-5, left side of chart (2) Circuit current (I2) is 20 amps, reads 0.91 for 20,000 feet, multiple continuous. 0.91 x 47 Amps = 42.77 Amps. (3) The voltage source is 28 volts. (5) Use figure 11-6, find the derate factor for 8 wires in a bundle at 60 percent. (4) The wire type used has a 200 °C First find the number of wires in the bundle (8) conductor rating and it is intended to use this at bottom of graph and intersect with the thermal rating to minimize the wire gauge. 60 percent curve meet. Read derating factor, Assume that the method described in para- (left side of graph) which is 0.6. Multiply graph 11-66d(6) was used and the minimum 0.6 x 42.77 Amps = 26 Amps. wire size to carry the required current is #14. Imax = 26 amps (this is the maximum (5) Ambient temperature is 50 °C under current the #14 gauge wire could carry at 50°C hottest operating conditions. ambient f. Procedures in example No. 2. L1=15.5 feet maximum run length for size #14 wire carrying 20 amps from figure 11-2 STEP 1: Assuming that the recommended load bank testing described in para- STEP 2: From paragraph 11-66d (5) and (6), graph 11-66d(5) is unable to be conducted, determine the T2 and the resultant maximum then the estimated calculation methods out- wire length when the increased resistance of lined in paragraph 11-66d(6) may be used to the higher temperature conductor is taken into determine the estimated maximum current account. (Imax). The #14 gauge wire mentioned above can carry the required current at 50 °C ambient (allowing for altitude and bundle derating). ( T2 = T1 + ( TR − T1 ) I 2 / I max ) (1) Use figure 11-4a to calculate the T2 = 50 ° C + (200 C − 50 C )( 20 A / 26 A Imax a #14 gauge wire can carry. = 50 °C+(150 °C)(.877) Where: T2 = 182 °C T2 = estimated conductor temperature (254.5 °C)(L1) L2 = = (234.5 °C) + (T2) T1 = 50 °C ambient temperature (254.5 °C)(15.5Ft) L2 = TR = 200 °C maximum conductor rated (234.5 °C) + (182 °C) temperature L2 = 9.5 ft (2) Find the temperature differences (TR-T1) = (200 °C-50 °C) = 150 °C. Par 11-67 Page 11-27 AC 43.13-1B CHG 1 9/27/01 The size #14 wire selected using the methods (7/35 = 20 percent) will be carrying power cur- outlined in paragraph 11-66d is too small to rents nearly at or up to capacity. meet the voltage drop limits from figure 11-2 for a 15.5 feet long wire run. STEP 1: Refer to the “single wire in free air” curves in figure 11-4a. Determine the change STEP 3: Select the next larger wire (size #12) of temperature of the wire to determine free air and repeat the calculations as follows: ratings. Since the wire will be in an ambient of 60 ºC and rated at 200° C, the change of to L1=24 feet maximum run length for temperature is 200 °C - 60 °C = 140 °C. Fol- 12 gauge wire carrying 20 amps from fig- low the 140 °C temperature difference hori- ure 11-2. zontally until it intersects with wire size line on figure 11-4a. The free air rating for Imax = 37 amps (this is the maximum current size #20 is 21.5 amps, and the free air rating the size #12 wire can carry at 50 °C ambient. for size #22 is 16.2 amps. Use calculation methods outlined in para- graph 11-69 and figure 11-4a. STEP 2: Refer to the “bundle derating curves” in figure 11-5, the 20 percent curve is selected T2 = 50 o C + (200 o C - 50 o C) ( 20 A / 37 A = since circuit analysis indicate that 20 percent 50 o C + (150 o C)(-540) = 131 o C or less of the wire in the harness would be car- rying power currents and less than 20 percent 254.5 o C(L1 ) L2 = of the bundle capacity would be used. Find 234.5 o C + (T2 ) 35 (on the abscissa) since there are 35 wires in (254.5 o C)(24ft) 6108 the bundle and determine a derating factor of L2 = o o = 0.52 (on the ordinate) from the 20 percent (234.5 C) + (131 C) 366 curve. (254.5 o C)(24ft) L2 = = 16.7 ft 366 STEP 3: Derate the size #22 free air rating by The resultant maximum wire length, after ad- multiplying 16.2 by 0.52 to get 8.4 amps in- justing downward for the added resistance as- harness rating. Derate the size #20 free air- sociated with running the wire at a higher tem- rating by multiplying 21.5 by 0.52 to get perature, is 15.4 feet, which will meet the 11.2 amps in-harness rating. original 15.5 foot wire run length requirement without exceeding the voltage drop limit ex- STEP 4: Refer to the “altitude derating curve” pressed in figure 11-2. of figure 11-6, look for 60,000 feet (on the ab- scissa) since that is the altitude at which the 11-69. COMPUTING CURRENT CARRY- vehicle will be operating. Note that the wire ING CAPACITY. must be derated by a factor of 0.79 (found on the ordinate). Derate the size a. Example 1. Assume a harness (open or #22 harness rating by multiplying braided), consisting of 10 wires, size #20, 8.4 amps by 0.79 to get 6.6 amps. Derate the 200 °C rated copper and 25 wires, size #22, size #20 harness rating by multiplying 200 °C rated copper, will be installed in an 11.2 amps by 0.79 to get 8.8 amps. area where the ambient temperature is 60 °C and the vehicle is capable of operating at a STEP 5: To find the total harness capacity, 60,000-foot altitude. Circuit analysis reveals multiply the total number of size #22 wires by that 7 of the 35 wires in the bundle the derated capacity (25 x 6.6 = 165.0 amps) and add to that the number of size #20 wires Page 11-28 Par 11-68 9/27/01 AC 43.13-1B CHG 1 multiplied by the derated capacity selected because we know all 12 wires will be (10 x 8.8 = 88 amps) and multiply the sum by carrying full load. Find 12 (on the abscissa) the 20 percent harness capacity factor. Thus, since there are 12 wires in the bundle and de- the total harness capacity is termine a derating factor of 0.43 (on the ordi- (165.0 + 88.0) x 0.20 = 50.6 amps. It has been nate) from the 100 percent curve. determined that the total harness current should not exceed 50.6 A, size #22 wire should STEP 3: Derate the size #12 free air ratings by not carry more than 6.6 amps and size multiplying 68 amps and 61 amps by 0.43 to #20 wire should not carry more than 8.8 amps. get 29.2 amps and 26.2 amps, respectively. STEP 6: Determine the actual circuit current STEP 4: Refer to the “altitude derating curve” for each wire in the bundle and for the whole of figure 11-6, look for sea level and bundle. If the values calculated in step #5 are 20,000 feet (on the abscissa) since these are exceeded, select the next larger size wire and the conditions at which the load will be car- repeat the calculations. ried. The wire must be derated by a factor of 1.0 and 0.91, respectively. b. Example 2. Assume a harness (open or braided), consisting of 12, size #12, 200 °C STEP 5: Derate the size #12 in a bundle rat- rated copper wires, will be operated in an am- ings by multiplying 29.2 amps at sea level and bient of 25 °C at sea level and 60 °C at a 26.6 amps at 20,000 feet by 1.0 and 0.91, re- 20,000-foot altitude. All 12 wires will be op- spectively, to obtained 29.2 amps and erated at or near their maximum capacity. 23.8 amps. The total bundle capacity at sea level and 25 °C ambient is STEP 1: Refer to the “single wire in free air” 29.2x12=350.4 amps. At 20,000 feet and curve in figure 11-4a, determine the tempera- 60 °C ambient the bundle capacity is ture difference of the wire to determine free air 23.8x12=285.6 amps. Each size #12 wire can ratings. Since the wire will be in ambient of carry 29.2 amps at sea level, 25 °C ambient or 25 °C and 60 °C and is rated at 200 °C, the 23.8 amps at 20,000 feet, and 60 °C ambient. temperature differences are 200 °C-25 °C = 175 °C and 200 °C-60 °C = 140 °C respec- STEP 6: Determine the actual circuit current tively. Follow the 175 °C and the 140 °C tem- for each wire in the bundle and for the bundle. perature difference lines on figure 11-4a until If the values calculated in Step #5 are ex- each intersects wire size line, the free air rat- ceeded, select the next larger size wire and re- ings of size #12 are 68 amps and 61 amps, re- peat t