Aviation Australia PDF Module 11A CASA B1-11e Aeroplane Systems - Electrical
Document Details
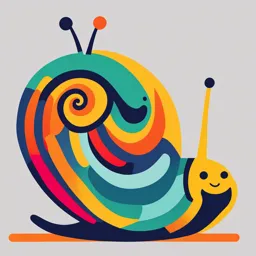
Uploaded by AccessibleConcreteArt
null
2020
CASA
Tags
Summary
This document is a training manual for aeroplane systems - electrical, and covers knowledge levels, objectives, and a table of contents. It was published by Aviation Australia in 2020.
Full Transcript
MODULE 11A Category B1 Licence CASA B1-11e Aeroplane Systems - Electrical Copyright © 2020 Aviation Australia All rights reserved. No part of this document may be reproduced, transferred, sol...
MODULE 11A Category B1 Licence CASA B1-11e Aeroplane Systems - Electrical Copyright © 2020 Aviation Australia All rights reserved. No part of this document may be reproduced, transferred, sold or otherwise disposed of, without the written permission of Aviation Australia. CONTROLLED DOCUMENT 2023-08-15 B1-11e Turbine Aeroplane Aerodynamics, Structures and Systems Page 2 of 140 CASA Part Part 66 - Training Materials Only Knowledge Levels Category A, B1, B2 and C Aircraft Maintenance Licence Basic knowledge for categories A, B1 and B2 are indicated by the allocation of knowledge levels indicators (1, 2 or 3) against each applicable subject. Category C applicants must meet either the category B1 or the category B2 basic knowledge levels. The knowledge level indicators are defined as follows: LEVEL 1 Objectives: The applicant should be familiar with the basic elements of the subject. The applicant should be able to give a simple description of the whole subject, using common words and examples. The applicant should be able to use typical terms. LEVEL 2 A general knowledge of the theoretical and practical aspects of the subject. An ability to apply that knowledge. Objectives: The applicant should be able to understand the theoretical fundamentals of the subject. The applicant should be able to give a general description of the subject using, as appropriate, typical examples. The applicant should be able to use mathematical formulae in conjunction with physical laws describing the subject. The applicant should be able to read and understand sketches, drawings and schematics describing the subject. The applicant should be able to apply his knowledge in a practical manner using detailed procedures. LEVEL 3 A detailed knowledge of the theoretical and practical aspects of the subject. A capacity to combine and apply the separate elements of knowledge in a logical and comprehensive manner. Objectives: The applicant should know the theory of the subject and interrelationships with other subjects. The applicant should be able to give a detailed description of the subject using theoretical fundamentals and specific examples. The applicant should understand and be able to use mathematical formulae related to the subject. The applicant should be able to read, understand and prepare sketches, simple drawings and schematics describing the subject. The applicant should be able to apply his knowledge in a practical manner using manufacturer's instructions. The applicant should be able to interpret results from various sources and measurements and apply corrective action where appropriate. 2023-08-15 B1-11e Turbine Aeroplane Aerodynamics, Structures and Systems Page 3 of 140 CASA Part Part 66 - Training Materials Only Table of Contents Electrical Power (11.6) 8 Learning Objectives 8 Aeroplane Electrical Power System 9 Electrical Power System Maintenance 9 Electrical Power Distribution 9 Aeroplane Batteries 10 Aircraft Battery Systems 10 Ventilation Requirements 14 Battery Connection 16 Battery Compartments 17 Battery Installation Procedures 18 Battery Servicing 18 DC Power Generation 19 DC Power 19 AC Power Generation 21 AC Power 21 Constant-Speed Drive Systems 22 Integrated Drive Generator 23 CSD/IDG Indication and Warnings 24 Emergency Power Generation 29 Introduction to Emergency Power Generation 29 Emergency AC Generation System 29 Voltage Regulation 32 Voltage Regulators 32 DC Generator Voltage Regulation 32 DC Generator Vibrating-Type Voltage Regulator 33 DC Three-Unit Regulator 34 DC Carbon Pile Voltage Regulator 36 Solid State Voltage Regulators 39 Transistorised Voltage Regulator – DC Alternator 40 AC Brushless Alternator Control 41 Power Distribution Systems 44 Electrical Bus Systems 44 Basic DC Generation Bus System 46 2023-08-15 B1-11e Turbine Aeroplane Aerodynamics, Structures and Systems Page 4 of 140 CASA Part Part 66 - Training Materials Only Basic Twin-Engine Split DC Bus System 46 Basic Twin Engine Split AC Bus System 46 Basic Twin AC Tied Bus System 47 Multi-Engine Split AC Bus System 48 Relays, Breakers and Contactors 49 Bus Tie Breaker 50 Generator Circuit Breaker 50 Auxiliary Contacts – Bus Tie Breaker and Generator Circuit Breaker 51 Inverters, Transformers and Rectifiers 53 Inverters 53 Transformers 55 Rectifiers 57 Transformer Rectifier Unit 57 Circuit Protection 60 Fuse 60 Current Limiter 60 Circuit Breakers 61 Switched Reverse Current Relay 64 Reverse Current Circuit Breakers 65 DC Overvoltage Protection 67 AC Overvoltage Protection 68 Differential/Feeder Fault 69 Merz-Price Protection System 71 External and Ground Power 72 Introduction to External and Ground Power 72 DC Power Receptacle 72 DC External Power Circuit 72 AC Power Receptacle and Plug 73 Ice and Rain Protection (11.12) 76 Learning Objectives 76 Ice and Rain Protection 77 Ice Protection 77 Rain Protection 77 Ice Formation 78 Types of Ice 78 Dangers of Ice Forming on an Aeroplane 80 Ice Detection 82 2023-08-15 B1-11e Turbine Aeroplane Aerodynamics, Structures and Systems Page 5 of 140 CASA Part Part 66 - Training Materials Only Ice Detection Methods 82 Visual Ice Detection 82 Electrical Ice Detection 82 Anti-Icing and De-Icing Systems 86 Types of Ice Control Systems 86 De-Icer Boots 86 De-icer Boot Inspection, Maintenance and Repair 87 Chemical De-icing 89 Propeller De-icing – Fluid System 90 Electrical Propeller De-Ice Control 90 Thermal Pneumatic Anti-Icing Systems 92 Engine Air Inlet Anti-Ice Systems 94 Electric Windshield Anti-Icing 97 Probe and Drain Heating 100 Pitot Static Probe Heaters 100 Pitot Static Probe Heater Circuit 101 Total Air Temperature Probe Heater Circuit 102 Galley and Lavatory Drain Heaters 103 Rain Removal and Repellent Systems 106 Windshield Wipers 106 Windshield Wiper Circuit 108 Windshield Washers 109 Pneumatic Rain Removal System 110 Rain Repellent System 111 Lights (11.14) 113 Learning Objectives 113 Aircraft Exterior Lighting 114 Exterior Lighting Systems 114 Navigation Lights 114 Anti-Collision Beacons 116 White Collision-Avoidance Strobe Lights 118 Landing Lights 120 Taxi Lights 122 Ice Detection or Wing Leading Edge Lights 123 Internal Lighting Systems 125 Cabin Lighting 125 Cabin Window Lighting 125 2023-08-15 B1-11e Turbine Aeroplane Aerodynamics, Structures and Systems Page 6 of 140 CASA Part Part 66 - Training Materials Only Passenger Advisory Signs 126 Lavatory Lighting 127 Passenger Reading Lights 128 Flight Compartment Lighting 129 Integral Instrument Panel Lighting 129 Post or Pillar Lights 130 Trans-Illuminated Panels 131 Floodlights 132 Utility or Wander Lights 133 Cargo Compartment Lights 134 Emergency Lighting 136 Emergency Lights 136 Emergency Exit Lights 136 Warning and Caution Lighting 138 Troubleshooting Lighting Systems 139 2023-08-15 B1-11e Turbine Aeroplane Aerodynamics, Structures and Systems Page 7 of 140 CASA Part Part 66 - Training Materials Only Electrical Power (11.6) Learning Objectives 11.6.1 Explain the installation and operation of aeroplane batteries (Level 3). 11.6.2 Explain the purpose and operation of aeroplane DC power generation (Level 3). 11.6.3 Explain the purpose and operation of aeroplane AC power generation (Level 3). 11.6.4 Explain the purpose and operation of aeroplane emergency power generation (Level 3). 11.6.5 Explain the purpose and operation of aeroplane voltage regulation (Level 3). 11.6.6 Explain the purpose and operation of aeroplane power distribution (Level 3). 11.6.7 Explain the purpose and operation of aeroplane inverters, transformers and rectifiers (Level 3). 11.6.8 Explain the purpose and operation of circuit protection (Level 3). 11.6.9 Explain the purpose and operation of external/ground power (Level 3). 2023-08-15 B1-11e Turbine Aeroplane Aerodynamics, Structures and Systems Page 8 of 140 CASA Part Part 66 - Training Materials Only Aeroplane Electrical Power System Electrical Power System Maintenance When performing maintenance on aircraft electrical systems, reference to electrical power can be found in the relevant aircraft system of manuals. These manuals include the Aircraft Maintenance Manual, The Wiring Diagrams Manual, the Illustrated Parts Catalogue and component vendor manuals. Transport aircraft maintenance manual systems comply with the Air Transport Association (ATA) Specification Reference under chapters ATA 20 Standard Practices and ATA 24 Electrical Power. Electrical Power Distribution Aircraft electrical power distribution block diagram A typical large aircraft electrical power system makes and supplies AC and DC power to the aircraft. A standby AC and/or DC system gives normal and emergency power. 2023-08-15 B1-11e Turbine Aeroplane Aerodynamics, Structures and Systems Page 9 of 140 CASA Part Part 66 - Training Materials Only Aeroplane Batteries Aircraft Battery Systems Aircraft, almost without exception, use a negative-ground or single-wire earth (or ground) returns system. This means that the negative terminal of the battery is connected directly to the metallic portion of the aircraft structure, which places the structure at a negative potential. This allows electrical components to be connected to the structure for a return path to the battery to complete a closed circuit. Benefits for grounding in this manner include the reduction of Radio Frequency Interference (RFI) by having fewer wires that can emit RFI energy and reduced weight. The electrical components need only a single wire from the positive voltage source and a negative connection to the aircraft structure. The exception to this design occurs when the aircraft is built using composite materials in place of metallic structures. As most composite materials are non-conductive, a two-wire electrical system must be used. Negative-ground, single wire system The image shows a typical battery circuit for a light aircraft. The positive terminal of the battery connects to the battery solenoid, which is a normally-open heavy-duty switch. Some manufacturers refer to a solenoid as a contactor, but both terms are used to describe components that essentially perform the same task to remotely control a large current source with a small conductor and switch. 2023-08-15 B1-11e Turbine Aeroplane Aerodynamics, Structures and Systems Page 10 of 140 CASA Part Part 66 - Training Materials Only Starter contactor When the master switch is closed, it completes a ground path to energise the battery solenoid coil. Once the coil is energised, the main power connection is closed (in the solenoid) to complete the circuit from the battery to the electrical distribution bus. Freewheeling Diode A freewheeling diode is installed across the coil of the solenoid to eliminate spikes when the master switch is opened and the magnetic field from the coil collapses. Without a freewheeling diode, the voltage spikes could cause damage to sensitive electronic components or arcing across the master switch. The freewheeling diode allows the induced EMF (from a collapsing coil) to feed back into itself rather than back into the distribution system. Effect of a freewheeling diode 2023-08-15 B1-11e Turbine Aeroplane Aerodynamics, Structures and Systems Page 11 of 140 CASA Part Part 66 - Training Materials Only Typical Battery System A typical battery system A battery may be used for starting an aircraft. Once the generator is online, the generator will supply power to applicable systems. It will also charge the battery. 2023-08-15 B1-11e Turbine Aeroplane Aerodynamics, Structures and Systems Page 12 of 140 CASA Part Part 66 - Training Materials Only Aircraft Ground Battery Charging Some aircraft isolate the battery when external DC power is applied to prevent the possibility of thermal runaway of a Nickel-Cadmium (Ni-cad) battery. Aircraft that do not have this feature incorporate battery charger units that automatically disconnect charging current above a pre-set battery temperature. Battery temperature monitor system 2023-08-15 B1-11e Turbine Aeroplane Aerodynamics, Structures and Systems Page 13 of 140 CASA Part Part 66 - Training Materials Only Battery Temperature Monitor System Many aircraft that use Ni-cad batteries have a battery temperature monitor system. Typically, this system provides a continuous temperature indication of the battery or batteries. They may also warn of high temperature conditions. A high-temperature indication enables action to be taken to isolate the battery and prevent possible damage arising from excessive battery temperature. A battery temperature monitor system There are two independent temperature sensors (thermistors) in each battery. Each thermistor is mounted on an intercell connector link of the battery. One sensor provides the temperature input for the temperature indication circuit, while the other is used by the overheat warning circuit. 2023-08-15 B1-11e Turbine Aeroplane Aerodynamics, Structures and Systems Page 14 of 140 CASA Part Part 66 - Training Materials Only Ventilation Requirements Lead acid batteries give off large quantities of hydrogen and oxygen (gassing) when charging. Adequate ventilation is therefore required to safely remove these fumes and dump them outside the aircraft. The aircraft’s airstream can be used to create a positive airflow ventilation system for the battery compartment or sealed case by creating a pick up and outflow pipe through the aircraft’s skin. Pressurised aircraft can also use the internal pressurised air, which is passed through a non-return valve and finally dumped overboard. Battery ventilation System A uses a sump jar with a neutralising agent in it so that the fumes pass over the felt pad, neutralising any acid or alkaline fumes before they exit the aircraft. This prevents damage occurring to aircraft skin. System B is a typical light aircraft system and does not incorporate sump jar. System C is a pressurised aircraft system which passes pressurisation system air through a non-return valve and into the battery case or compartment. It may or may not utilise a sump jar. If the battery is of the sealed-case type, the ventilation system will be connected to the case to maintain some airflow through the case. 2023-08-15 B1-11e Turbine Aeroplane Aerodynamics, Structures and Systems Page 15 of 140 CASA Part Part 66 - Training Materials Only Battery showing vent and sump jar Battery Connection Light aircraft batteries have bolt-on connections like auto batteries. Smear lugs with an approved lubricant before connection to inhibit corrosion. Light aircraft lead acid battery 2023-08-15 B1-11e Turbine Aeroplane Aerodynamics, Structures and Systems Page 16 of 140 CASA Part Part 66 - Training Materials Only Larger fully enclosed batteries, where external connections cannot protrude though the case safely, will usually have a quick disconnect socket fitted to the case. This type of connector requires some form of positive locking device so that the connector does not unscrew during flight. If there is no inbuilt locking device, the connectors should be lockwired closed with 26 AWG copper wire (safety lockwire). Quick-release type battery connections Usually, these quick release terminals are lubricated with white petroleum jelly to prevent any corrosion forming on the contacts which could affect serviceability or, worse still, make the battery very difficult to remove. Remember: Once a battery is fitted to an aircraft, it may stay there for many months before it is touched again. Battery Compartments All aircraft batteries need to be securely mounted in the aircraft. Whether it has its own isolated compartment, or shares space with other equipment, it must be firmly bolted into a mounting cradle. Battery tie down 2023-08-15 B1-11e Turbine Aeroplane Aerodynamics, Structures and Systems Page 17 of 140 CASA Part Part 66 - Training Materials Only Large metal batteries will have lugs built into the cover through which the hold down bolts can pass. Plastic-cased batteries will generally have a metal clamp over the top. Whether wing nuts, hexagonal nuts or quick release clamps are used for securing purposes, all should be lockwired for security purposes. Battery Installation Procedures Before installing any battery in an aircraft, ensure the battery is the correct type. Refer to aircraft maintenance manual. Before installing, check that its mounting tray, box or compartment and the surrounding area are clean and free of corrosion or contamination. Check that the vent and drain lines are in good condition and not blocked. Check that the neutralising jar is serviceable. Usually, aircraft batteries with bolted terminals have the negative terminal of the battery connected to the aircraft structure. When installing a battery, always connect the positive lead first. This way, if contact is inadvertently made between the battery and the aircraft with a wrench, it will not cause a spark. When removing a battery, always disconnect the negative lead first. If high or difficult lifting is involved, get help or use some mechanical lifting device. If there is a possibility of contacting and shorting the battery terminals, fit an insulator plug/cap onto the terminal connector. Remember: Safe work practices must be applied to at all times. Battery Servicing The only servicing permitted on lead acid batteries fitted to an aircraft is the check and adjustment of electrolyte levels and cleaning of terminals. If any electrolyte is spilt, always neutralise it before washing it away. Lead acid batteries require a solution of water and bicarbonate of soda. Spills on aircraft from Ni-Cad batteries require a chromic acid solution as a neutralising agent. Spills off aircraft can be neutralised with a boric acid solution or vinegar. After a battery servicing, always wash your hands before going to the toilet. Acid or alkaline burns on sensitive skin are not nice. Battery servicing caution 2023-08-15 B1-11e Turbine Aeroplane Aerodynamics, Structures and Systems Page 18 of 140 CASA Part Part 66 - Training Materials Only DC Power Generation DC Power On light aircraft, where a relatively small amount of electric power is used, an AC generator requiring a constant-speed drive is simply too heavy. Modern light aircraft use DC alternators to produce electric power. A DC alternator produces an AC voltage and uses internal rectifiers to produce a DC output. Light aircraft electrical system schematic On larger aircraft, the normal DC power supply is produced by Transformer Rectifier Units (TRUs) which change the engine-driven AC-generated 115-V AC to 28-V DC. The aircraft may also have following DC power sources: Aircraft main battery Main battery charger Auxiliary battery Auxiliary battery charger. The batteries are the backup DC source if other sources do not operate. 2023-08-15 B1-11e Turbine Aeroplane Aerodynamics, Structures and Systems Page 19 of 140 CASA Part Part 66 - Training Materials Only Twin commercial jet electrical schematic 2023-08-15 B1-11e Turbine Aeroplane Aerodynamics, Structures and Systems Page 20 of 140 CASA Part Part 66 - Training Materials Only AC Power Generation AC Power AC generators, often called alternators, are used as the principal source of electric power in almost all transport-category aircraft. The AC system supplies almost all the electric power required for the aircraft. Where DC is needed, rectifiers are used. For emergency situations, AC generators driven by Auxiliary Power Units (APUs) or Ram Air Turbines (RATs) are often used. AC power systems produce more power per weight of equipment than DC systems; however, most AC generators require a constant-speed drive to maintain a constant AC frequency. A Constant- Speed Drive (CSD) is a type of transmission that maintains a constant output rpm with a variable input rpm. Alternators are classified according to voltage, amperage, phase, power output (watts or kilovolt- amperes [kVA]) and power factor. Three-phase alternators are typical for most aircraft applications. The aircraft electrical power system has four main AC power sources and a standby power source: Left engine driven generator Right engine driven generator APU generator or starter-generator External power. Typical aircraft power generation and distribution 2023-08-15 B1-11e Turbine Aeroplane Aerodynamics, Structures and Systems Page 21 of 140 CASA Part Part 66 - Training Materials Only On a turbine-powered aircraft, the engine-driven generators are driven through a Constant Speed Drive (CSD). More modern aircraft use an Integrated Drive Generator (IDG), which is a constant- speed drive and generator integrated into one unit. The generators supply three-phase, 115/200-V AC at 400 Hz. The typical AC power system design prevents two sources to the same load at the same time. A static inverter supplies a single-phase, 115-V AC output to the AC standby power system. Constant-Speed Drive Systems Constant-speed drive and generator assembly In an AC power system, it is usually necessary to maintain a constant speed in the AC generator. This is because the frequency of the AC generator is determined by the speed with which it is driven. It is especially important to maintain constant generator speed in installations in which the generators operate in parallel. In this case, it is essential that generator speed be kept constant within extremely close limits. A Constant-Speed Drive (CSD provides constant-speed generator operation in an AC electrical system. CSD units are manufactured in many designs to fit a variety of applications. The principle of operation for all CSDs is essentially the same. The complete CSD system consists of an Axial Gear Differential (AGD), whose output speed relative to input speed is controlled by a flyweight-type governor that controls a variable-delivery hydraulic pump. The pump supplies hydraulic pressure to a hydraulic motor, which varies the ratio of input rpm to output rpm to maintain a constant output rpm to drive the generator and maintain an AC frequency of 400 Hz. 2023-08-15 B1-11e Turbine Aeroplane Aerodynamics, Structures and Systems Page 22 of 140 CASA Part Part 66 - Training Materials Only Most CSDs are equipped with a Quick Attach/Detach (QAD) adapter. This unit allows generator and CSD assembly removal and replacement in a matter of minutes. The QAD ring is mounted to the CSD by means of several bolts through the mounting flange. To remove the generator from the aircraft, one must only release the QAD using one fastener. This mounting technique allows for quick line repair of an aircraft that has a defective generator CSD. Integrated Drive Generator Integrated drive generator (IDG) Modern turbine-powered aircraft produce AC using an Integrated Drive Generator (IDG). The IDG contains both the generator and the CSD in one unit. This concept helps to reduce both the weight and the size of the traditional two-unit system. The generator is an integral part of the IDG and cannot be replaced separately from the IDG. The generator is mounted on the aft face of the CSD. The CSD, containing hydraulic trim units and a differential assembly, converts the variable engine rpm to an alternator input speed of 12 000 rpm. Older alternators typically rotate at 8000 to 9000 rpm. The 30 percent increase in alternator speed, along with improved cooling features, has allowed for a reduction in alternator size without a decrease in output power. The IDG used on the Boeing 747 produces 90 kVA three-phase power for aircraft electrical systems at 115 volts 400 Hz at 12 000 rpm. Three electrical subassemblies make up the generator (alternator) portion of the IDG: the Permanent Magnet Generator (PMG), the exciter generator and rectifier assembly and the main generator. The term generator is still used even though these items are brushless alternators. 2023-08-15 B1-11e Turbine Aeroplane Aerodynamics, Structures and Systems Page 23 of 140 CASA Part Part 66 - Training Materials Only CSD and IDG quick attach/detach (QAS) adapter An integrated drive generator is shown. However, CSD installations are similar. CSD/IDG Indication and Warnings A normal operating temperature for the cooling oil is approximately 93 °C (200 °F). To maintain the correct cooling capacity, the oil level should be monitored periodically. A sight glass is installed on most constant-speed drives to allow a quick check of the oil level. In the case of an in-flight oil loss or an over temperature condition, a warning indicator will illuminate on the flight deck. In this situation, the CSD is disengaged and inspected upon landing. Most constant-speed drive units are equipped with an electrically activated generator-drive disconnect mechanism. This disconnect couples the CSD input shaft to the CSD input spline. The CSD disconnect is switched manually from the aircraft’s flight deck or automatically by a generator control unit. The disconnect is activated in the event of certain generator system failures. After disconnection, The CSD can only be reconnected on the ground. Example of an generator panel 2023-08-15 B1-11e Turbine Aeroplane Aerodynamics, Structures and Systems Page 24 of 140 CASA Part Part 66 - Training Materials Only IDG/CSD Operation IDG operational diagram The IDG installation (a CSD and generator assembly is similar) consists of an alternating current generator and a hydraulic transmission with mechanical control governing the rotational speed of the alternating current generator (CSD). The power used to drive the alternating current generator is controlled and transmitted from the aircraft engine through the combined effects of the differential, the variable displacement hydraulic units and the fixed displacement hydraulic units. 2023-08-15 B1-11e Turbine Aeroplane Aerodynamics, Structures and Systems Page 25 of 140 CASA Part Part 66 - Training Materials Only Governing Section In the governing section of the CSD, the governor is a spring-biased, flyweight-operated hydraulic control valve. It functions to control porting of transmission charge oil to the control cylinder. During steady state operation, supply pressure is reduced to the required control pressure. Depending on valve stem position, charge oil is ported to the control piston or control oil is drained to the transmission case. The normal operating frequency of the system is 400 (±4) Hz; however, the governor can be adjusted on the aircraft by means of the adjustment screw to compensate for frequency variations. Clockwise rotation of the adjustment screw increases the frequency. Counter-clockwise rotation of the adjustment screw decreases the frequency. A 360-degree turn of the adjustment screw changes the frequency by approximately 3–4 Hz. Note: Unstable and erratic frequencies cannot be corrected by governor adjustment. Charge Pump The charge pump is in the hydraulic circuit between the all-attitude reservoir, the charge filter and the transmission. The charge pump supplies filtered oil to the cylinder blocks, governor, control piston, lubricating system and generator cooling circuit. Transmission Scavenge Pump The transmission scavenge pump is in the hydraulic circuit between the transmission sump and the scavenge filter. The transmission scavenge pump picks up lube oil and internal leakage and pumps it through the scavenge filter and the aircraft IDG cooler into the all-attitude reservoir. Generator Scavenge Pump The generator scavenge pump is in the hydraulic circuit between the generator and the scavenge filter. The generator scavenge pump picks up generator cooling and lube oil and pumps it through the scavenge filter and aircraft cooler into the all-attitude reservoir. Charge Relief Valve The charge relief valve is in the hydraulic circuit between the hydraulic units and the reservoir. The charge relief valve regulates the operating pressure of the charge oil system. The valve accomplishes this function by controlling/metering the discharge of oil from the charge oil system to maintain the pre-set charge pressure. 2023-08-15 B1-11e Turbine Aeroplane Aerodynamics, Structures and Systems Page 26 of 140 CASA Part Part 66 - Training Materials Only Oil Cooler The oil cooler uses fan air from the engine to cool the CSD oil. The cooler has a pressure-operated bypass valve that opens if the pressure differential across the cooler reaches a pre-determined value (such as cold oil). Hydraulic System Reservoir The reservoir de-aerates the oil, returning some to the transmission sump. The remainder supplies the charge pump. Hydraulic Filters Two filters are used to filter the oil in the hydraulic system: the charge filter, located in the charge pressure line; and the scavenge filter, which is in the scavenge line between the scavenge pump and the reservoir. Note: These filters don't have by-pass capabilities, therefore, if either becomes blocked, and the Differential Pressure Indicator is showing, the IDG must be replaced. Differential Pressure Indicator The scavenge filter housing contains a differential pressure indicator. This indicator warns of an impending blockage and should not be ignored. Note: As previously stated, if the Differential Pressure Indicator is visible, the IDG must be replaced. CSD Disconnect Mechanism The disconnect is an electrically actuated device that de-couples the input shaft from the input spline shaft in the event of a transmission malfunction. When the disconnect solenoid is activated by the flight crew, a spring-loaded pawl moves into contact with threads on the input shaft. The input shaft acts as a screw, and input rotation causes the input shaft to move away from the input spline shaft, separating the driving dogs on the two shafts. When the driving dogs have been separated, the input spline shaft, which is still being driven by the aircraft engine, spins freely in the transmission without causing transmission rotation. Reset may be accomplished, with the engine stationary, by pulling out on the reset handle until the solenoid snaps into position. 2023-08-15 B1-11e Turbine Aeroplane Aerodynamics, Structures and Systems Page 27 of 140 CASA Part Part 66 - Training Materials Only Generator Cooling Owing to their compact size, most AC generators require some means of cooling during operation. Older and/or less powerful generators are typically cooled by means of ram air forced through the units. Newer systems use oil as the cooling agent. The oil is sent from the CSD through the generator and then through an air/oil heat exchanger. The air cools the oil, which is once again cycled through the CSD and generator. The use of oil cooling allows for a higher-speed rotor within the generator section. A higher-speed rotor means a lighter, more compact generator. 2023-08-15 B1-11e Turbine Aeroplane Aerodynamics, Structures and Systems Page 28 of 140 CASA Part Part 66 - Training Materials Only Emergency Power Generation Introduction to Emergency Power Generation Emergency power generation is installed on many aircraft to supply essential power in the event of losing all normal power generation. Such a situation could arise if the engine-driven generators failed. Emergency generators are driven either directly by an airstream-driven generator or driven from a hydraulic motor being supplied pressure from an airstream-wind-driven hydraulic pump. Emergency generators are, normally without exception, permanent magnet alternators and are typically constructed with a permanent magnet rotor and do not require battery power to function. Emergency AC Generation System Hydraulic electrical generating system (HEGS) Larger transport aircraft utilise a hydraulic motor-driven emergency generator system to provide emergency or standby electrical power in the event of the loss of both normal main generator buses. The Airbus A330 system will be discussed here. The emergency AC generation system consists of a hydraulic motor-driven generator which is designed to restore the essential power network in case of the loss of the two main generator buses (AC bus 1 and AC bus 2). Hydraulic power for the hydraulic motor is supplied by a ram air turbine. 2023-08-15 B1-11e Turbine Aeroplane Aerodynamics, Structures and Systems Page 29 of 140 CASA Part Part 66 - Training Materials Only Ram air turbine A Ram Air Turbine (RAT) is installed on most large or complex twin-engine passenger aircraft to provide an emergency source of hydraulic and electric power. The RAT is an airstream-driven hydraulic pump that provides emergency hydraulic power for the flight controls if hydraulic power is lost on both engines. On some aircraft, the RAT is automatically deployed if both engine-driven generators fail, providing emergency hydraulic power to run a hydraulic motor-driven generator and emergency hydraulic power. The hydraulic electrical generating system consists of the following components: Hydraulic Constant Speed Motor and AC Generator (CSM/G) Generator Control Unit (CSM/G GCU). The hydraulic constant speed motor can be supplied by the aircraft’s main hydraulic system, which is powered either by the engine driven hydraulic pumps or by the Ram Air Turbine (RAT) pump. The RAT will supply hydraulic pressure if both engines or both engine-driven hydraulic pumps fail. With the loss of the main AC busbars, the CSM drives the AC generator, which is controlled by the Emergency Generator Control Unit CSM/G GCU. The AC power supplied is three-phase 115-V AC at 400 Hz, which is fed to the essential AC and DC buses through the Emergency Bus Supply contactor and Essential Transformer Rectifier unit (ESS TR). If power is lost to the essential AC and DC main busbars, the battery supplies the DC essential bus (DC ESS BUS) and the AC ESS BUS via the static inverter and the emergency bus supply contactor. 2023-08-15 B1-11e Turbine Aeroplane Aerodynamics, Structures and Systems Page 30 of 140 CASA Part Part 66 - Training Materials Only The AC ESS shed bus and the DC ESS shed bus are shed respectively by their essential shed bus contactors when the CSM/G is supplied by the RAT hydraulic pump. In the battery only configuration, the AC ESS bus shed network is isolated by the emergency bus supply contactor. 2023-08-15 B1-11e Turbine Aeroplane Aerodynamics, Structures and Systems Page 31 of 140 CASA Part Part 66 - Training Materials Only Voltage Regulation Voltage Regulators Voltage regulators Regardless of whether it is an AC generator, DC generator or DC alternator, typically the voltage regulator senses the output and controls (regulates) the field current under varying load conditions. As load conditions change, the voltage regulator adjusts the field current, automatically (typically) maintaining the generator output at the required output voltage. Typically, aircraft DC generators/alternators are regulated to 28-V DC (14-V DC for 12-V light aircraft) and AC generators to 115-V AC (200-V AC 3Ø). DC Generator Voltage Regulation Control of the field current using a rheostat in the field coil circuit 2023-08-15 B1-11e Turbine Aeroplane Aerodynamics, Structures and Systems Page 32 of 140 CASA Part Part 66 - Training Materials Only Efficient operation of electrical equipment in an aircraft depends on maintaining a fixed supply voltage under varying load requirements. One factor which determines the voltage output of a generator is the strength of the field current, which can be easily controlled. One way to control the field current is to install a rheostat in the field coil circuit. When the rheostat is set to increase the resistance in the field circuit, less current flows through the field coils, and the strength of the magnetic field decreases. Consequently, less voltage is induced into the armature, and generator output decreases. When the resistance in the field circuit is decreased with the rheostat, more current flows through the field coils, and the magnetic field becomes stronger. This allows more voltage to be induced into the armature, which produces a greater output voltage. One thing to keep in mind is that the weaker the magnetic field is, the easier it is to turn the armature. On the other hand, if the strength of the magnetic field is increased, more force is required to turn the armature. This means that when the load on a generator increases, additional field current must be supplied to increase the voltage output, and additional force is required to turn the armature. DC Generator Vibrating-Type Voltage Regulator Vibrating-type voltage regulator This basic rheostat principle is further developed by the addition of a solenoid which electrically connects or removes the field rheostat from the circuit as the voltage varies. This type of setup is found in a vibrating-type voltage regulator. 2023-08-15 B1-11e Turbine Aeroplane Aerodynamics, Structures and Systems Page 33 of 140 CASA Part Part 66 - Training Materials Only When the output voltage rises above a specified critical value, the downward pull of the solenoid’s coil exceeds the spring tension and contact B opens. This reinserts the field rheostat in the field circuit. The additional resistance reduces the field current and lowers output voltage. When the output voltage falls below a certain value, contact B closes, shorting the field rheostat, and the terminal voltage starts to rise. Thus, an average voltage is maintained with or without load changes. The dashpot P provides smoother operation by acting as a dampener to prevent hunting, and capacitor C across contact B helps eliminate sparking. With a vibrating-type voltage regulator, contact B opens and closes several times per second to maintain the correct generator output. Based on this, if the solenoid should malfunction or the contacts stick closed, excess current would flow to the field, and generator output would increase. DC Three-Unit Regulator A three-unit regulator Many light aircraft employ a three-unit regulator for their generator systems. This type of regulator includes a current limiter and a reverse current cut-out in addition to a voltage regulator. The action of the voltage regulator unit is like the vibrating-type regulator described earlier. The second of the three units is a current regulator to limit the output current of the generator. The third unit is a reverse current cut-out that disconnects the battery from the generator. If the battery is not disconnected, it will discharge through the generator armature when the generator voltage falls below that of the battery, thus driving the generator as a motor. This action is called “motoring” the generator and, unless prevented, will discharge the battery in a short time. The operation of a three-unit regulator shown is described in the following paragraphs. 2023-08-15 B1-11e Turbine Aeroplane Aerodynamics, Structures and Systems Page 34 of 140 CASA Part Part 66 - Training Materials Only The action of vibrating contact C1 in the voltage regulator unit causes an intermittent short circuit between points R1 and L2. When the generator is not operating, spring S1 holds C1 closed; C2 is also closed by S2. The shunt field is connected directly across the armature. When the generator is started, its terminal voltage will rise as the generator comes up to speed, and the armature will supply the field with current through closed contacts C2 and C1. As the terminal voltage rises, the current flow through L1 increases and the iron core becomes more strongly magnetized. At a certain speed and voltage, when the magnetic attraction on the movable arm becomes strong enough to overcome the tension of spring S1, contact points C1 are separated. The field current now flows through R1 and L2. Because resistance is added to the field circuit, the field is momentarily weakened and the rise in terminal voltage is checked. Also, since the L2 winding is opposed to the L1 winding, the magnetic pull of L1 against S1 is partially neutralized, and spring S1 closes contact C1. Therefore, R1 and L2 are again shorted out of the circuit, and the field current again increases; the output voltage increases, and C1 is opened because of the action of L1. The cycle is rapid and occurs many times per second. The terminal voltage of the generator varies slightly but rapidly above and below an average value determined by the tension of spring S1, which may be adjusted. The purpose of the vibrator-type current limiter is to limit the output current of the generator automatically to its maximum rated value to protect the generator. L3 is in series with the main line and load. The amount of current flowing in the line determines when C2 will open, placing R2 in series with the generator field. This action decreases the field current and the generated voltage. When the generated voltage is decreased, the generator current is reduced. The core of L3 is partly demagnetized, and the spring closes the contact points. This causes the generator voltage and current to rise until the current reaches a value sufficient to start the cycle again. A certain minimum value of load current is necessary to cause the current limiter to vibrate. By reducing the output voltage, we also reduce generator current. The voltage regulator is actuated by line voltage, whereas the current limiter is actuated by line current. 2023-08-15 B1-11e Turbine Aeroplane Aerodynamics, Structures and Systems Page 35 of 140 CASA Part Part 66 - Training Materials Only Inside a three-unit regulator The purpose of the reverse current cut-out relay is to automatically disconnect the battery from the generator when the generator voltage is less than the battery voltage. If this relay was not used in the generator circuit, the battery would discharge through the generator, driving the generator as a motor (termed “motoring the generator”). This could flatten the battery, damage the generator windings, stall the engine or break the connecting generator engine quill shaft. There are two windings, L4 and L5, on the soft iron core. The current winding, L4, consisting of a few turns of heavy wire, is in series with the line and carries the entire line current. The voltage winding, L5, consisting of many turns of fine wire, is shunted across the generator terminals. When the generator is not operating, contact C3 is held open by the spring S3. As the generator voltage builds up, L5 magnetizes the iron core. When the current (because of the generated voltage) produces sufficient magnetism in the iron core, contact C3 is closed, as shown. The battery then receives a charging current. The coil spring, S3, is so adjusted that the voltage winding will not close the contact points until the voltage of the generator is more than the normal voltage of the battery. The charging current passing through L4 aids the current in L5 to hold the contacts tightly closed. Unlike C1 and C2, contact C3 does not vibrate. When the generator slows down or, for any other cause, the generator voltage decreases to a certain value below that of the battery, the current reverses through L4 and the magnetic field of L4 opposes that of L5. This reduction in the magnetism of the core causes C3 to open, preventing the battery from motoring the generator. C3 will not close again until the generator terminal voltage exceeds that of the battery by a predetermined value. 2023-08-15 B1-11e Turbine Aeroplane Aerodynamics, Structures and Systems Page 36 of 140 CASA Part Part 66 - Training Materials Only DC Carbon Pile Voltage Regulator Aviation Australia Carbon-pile voltage regulator Since contacts tend to pit or burn when large amounts of current flow through them; vibrating-type regulators and three-unit regulators cannot be used with generators that require a high field current. Therefore, heavy-duty generator systems require a different type of regulator, such as the carbon- pile voltage regulator. Carbon-pile voltage regulators controlling compound-wound generators with reverse-current cut- out relays were used in older aircraft DC generating systems. Compound wound generators DC generators have both series and shunt field windings. The output voltage remains relatively constant for all values of load current within the design of the generator. The carbon-pile voltage regulator derives its name from the fact that the regulating element (variable resistance) consists of a stack, or pile, of carbon discs. Usually, the carbon pile has alternate hard carbon and soft carbon discs contained in a ceramic tube with a carbon or metal contact plug at each end. At one end of the pile, several radially arranged leaf springs exert pressure against the contact plug, thus keeping the discs pressed firmly together. For as long as the discs are compressed, the resistance of the pile is very low. If the pressure on the carbon pile is reduced, the resistance increases. By placing an electromagnet in a position where it will release the spring pressure on the discs as the voltage rises above a predetermined value, a stable and efficient voltage regulator is obtained. 2023-08-15 B1-11e Turbine Aeroplane Aerodynamics, Structures and Systems Page 37 of 140 CASA Part Part 66 - Training Materials Only Carbon pile voltage regulator circuit The carbon pile voltage regulator is connected with the carbon pile in series with the generator field, and the voltage coil is shunted across the generator output. A small manually operated rheostat is connected in series with the voltage coil to provide a limited amount of voltage adjustment. 2023-08-15 B1-11e Turbine Aeroplane Aerodynamics, Structures and Systems Page 38 of 140 CASA Part Part 66 - Training Materials Only Equalising Circuit When two or more generators are connected in parallel to a power system, the generators should share the load equally. If the voltage of one generator is slightly higher than that of the other generators in parallel, that generator will assume the greater part of the load. For this reason, an equalising or paralleling circuit must be provided that will cause the load to be distributed evenly among the generators. An equalising circuit includes an equalising coil wound with the voltage coil in each of the voltage regulators, an equalising bus to which all equalising circuits are connected and a low-resistance shunt in the ground lead of each generator. The equalising coil will either strengthen or weaken the effect of the voltage coil, depending on the direction of current flow through the equalizing circuit. By controlling the generator output voltages, each generator shares the load current equally. The low-resistance shunt in the ground lead of each generator causes a difference in potential between the negative terminals of the generators that is proportional to the difference in load current. The shunt is of such a value that there will be a potential difference of 0.5 V across it at maximum generator load. Equalising circuit 2023-08-15 B1-11e Turbine Aeroplane Aerodynamics, Structures and Systems Page 39 of 140 CASA Part Part 66 - Training Materials Only Solid State Voltage Regulators The grounded regulator type (L) and the grounded field type (R) Two regulator designs can be used: The grounded regulator type—the regulator controls the amount of battery ground (negative) going to the field winding in the rotor. The grounded field type—the regulator controls the amount of battery positive (B+) going to the field winding in the rotor. Transistorised Voltage Regulator – DC Alternator Transistorised voltage regulators Transistorised voltage regulators have now superseded other forms of voltage regulators in modern aircraft. The regulator discussed in this section is used on a light aircraft alternator rectifier unit. 2023-08-15 B1-11e Turbine Aeroplane Aerodynamics, Structures and Systems Page 40 of 140 CASA Part Part 66 - Training Materials Only Operation The master switch is turned on, and the charge light illuminates, gaining its earth via the alternator (L) terminal, alternator rotor and transistor T1 (which is biased on). This small current gives the field initial excitation. Once the engine is started, the alternator output builds up. The rotor voltage is half wave rectified by the field exciter diodes and supplies the alternator rotor field gaining earth via the biased-on transistor T1. When the alternator voltage approaches battery voltage, the charge indicator light has near equal potential on each side and will extinguish. Alternator output voltage is dropped across resistors R1, R2 and R3. When the set voltage value is reached, the Zener Diode (ZD) will conduct biasing transistor T2 on. The flow of current through T2 and R4 causes a voltage drop across R4 which biases T1 base emitter off. T1 switching off stops the rotor field current, and the alternator voltage drops. This drop-in voltage across R1, R2 and R3 causes the zener diode to stop conducting, and transistor T2 switches off. T2 switching off lowers the voltage drop across R4 and the base of transistor T1 increases (more positive) and switches on, allowing field current to flow. This process is repeated at a rate required to maintain alternator output voltage at the set value with varying load and speed conditions. The surge quench diode in the regulator is connected across the alternator rotor field winding. When power is applied to the field by transistor T1, the surge quench diode is reverse biased and will not conduct. When transistor T1 switches off the field current, the magnetic field around the field coil collapses, inducing a current in the field coil with opposite polarity to that of the applied voltage (inductor theory). The opposite polarity forward biases the diode, which conducts and shorts out the current induced in the field coil, preventing transistor T1 from sustaining any damage if the induced voltage exceeds the peak inverse voltage of T1. Note: Late model transistorised regulators are now mounted in the alternator rectifier unit and are sealed. They are encapsulated, and if they are unserviceable, repair can only be done by replacing them with a new item. Some light twin engine aircraft have one regulator controlling both alternators and one regulator as an alternate that can be selected by the pilot if the first regulator fails. 2023-08-15 B1-11e Turbine Aeroplane Aerodynamics, Structures and Systems Page 41 of 140 CASA Part Part 66 - Training Materials Only AC Brushless Alternator Control Brushless generator control schematic There are three separate generators within one case: (1) the permanent magnet generator, (2) the exciter generator, and (3) the main generator. Each of these three units is an essential part of the modern brushless alternator. The permanent magnet, which is connected to the rotor, is used to induce an alternating current into the stationary PMG three-phase armature winding. The Generator Control Unit (GCU) rectifies the AC armature current and sends a DC voltage to the exciter field winding. The exciter field induces an alternating current into the exciter armature. The exciter armature is connected to the rotating rectifier, which changes the alternating current to direct current and sends a current to the main generator field. The main field induces an AC voltage into the main generator armature. The main generator armature is a three-phase winding that produces 115 volts across a single phase and 200 V across two phases. This armature is connected to the output terminals of the generator and hence supplies the electric power for the aircraft systems. 2023-08-15 B1-11e Turbine Aeroplane Aerodynamics, Structures and Systems Page 42 of 140 CASA Part Part 66 - Training Materials Only Brushless alternator electrical schematic The GCU monitors the main generator output and in turn regulates the exciter field current as needed. If more generator output is required, the GCU will increase the exciter field current; this will, in turn, increase the exciter armature output and the main field current. A stronger main field will increase the main armature’s output. If less generator output is needed, the GCU will weaken the exciter field current, and the generator output will decrease. 2023-08-15 B1-11e Turbine Aeroplane Aerodynamics, Structures and Systems Page 43 of 140 CASA Part Part 66 - Training Materials Only Power Distribution Systems Electrical Bus Systems Aircraft bus system The output from generating sources is connected to one or more low resistance conductors known as bus bars. Bus bars can be a copper or aluminium strip or cables to which the supply and feed connections can be made. Large aircraft contain several bus bars. Each has a specific task necessary for power distribution and load sharing between different loads. Bus systems are categorised into their order of importance or hierarchy: Hot battery bus Essential DC bus AC bus (main generator buses) AC essential bus AC non-essential bus. 2023-08-15 B1-11e Turbine Aeroplane Aerodynamics, Structures and Systems Page 44 of 140 CASA Part Part 66 - Training Materials Only Hot battery bus functional diagram Hot Battery Bus The aircraft battery is normally directly connected to the hot battery bus. The hot battery bus supplies power directly to a few critical loads, e.g., fire extinguishers and fuel and hydraulic fire shut off valves. Essential DC Bus The essential DC bus, also referred to as the battery bus, is connected to the hot battery bus via a contactor. AC Bus The AC bus is fed from its respective main generator.Essential buses are connected AC bus systems. They supply power to essential lighting, flight control systems, communication and navigation systems and other high-priority electrical systems required to ensure safe flight in an emergency.Non-essential buses supply galley power, non-essential lighting and other low-priority electrical systems which can be isolated in an in-flight emergency. Non-essential buses may also be called shed buses or isolation buses. 2023-08-15 B1-11e Turbine Aeroplane Aerodynamics, Structures and Systems Page 45 of 140 CASA Part Part 66 - Training Materials Only Load Shedding Non-essential systems are isolated (turned off) during partial generator system failure. This is to prevent overloading the active generator, which would be incapable of supplying electrical power to all aircraft systems. Basic DC Generation Bus System This is a simple representation of a small aircraft with one generator and how the power is distributed. The battery would be charged from the bus when generator was outputting at a higher voltage. The inverter provides the aircraft with AC voltage. Simple single-generator system Basic Twin-Engine Split DC Bus System A split bus configuration occurs when each generator powers its own individual bus. If one generator fails, then the failed generator is isolated from its bus, and the power on the other bus is coupled to that bus by a Bus Tie Breaker (BTB). Tied bus system 2023-08-15 B1-11e Turbine Aeroplane Aerodynamics, Structures and Systems Page 46 of 140 CASA Part Part 66 - Training Materials Only Basic Twin Engine Split AC Bus System In this example, the AC generators (alternators) supply their individual buses. The AC bus then feeds the Transformer Rectifier Unit (TRU or T/R) which provides the DC requirements of the aircraft as well as charge the battery. The emergency AC bus is fed from the AC bus directly. Should this AC supply fail for any reason, the static inverter would be commanded to start and provide emergency AC from the battery. Basic twin-engine split AC system Basic Twin AC Tied Bus System Tied bus system 2023-08-15 B1-11e Turbine Aeroplane Aerodynamics, Structures and Systems Page 47 of 140 CASA Part Part 66 - Training Materials Only A tied bus system means the AC generators outputs are connected onto the same bus. Before the AC generators can be connected or paralleled, they must be matched so their output waveforms must be the same: Their output voltages must be the same. They must have the same frequency. Their voltages are in phase. They must have the same phase rotation (3 phase). The phase rotation will be correct if the generators are all connected to the lines in the same way. If this is not correct, synchronisation will not be achievable.The split system breaker (SSB) will not close if the buses’ properties are outside the limits of voltage, phase rotation sequence or frequency. Multi-Engine Split AC Bus System When operated on the ground with external power connected and no engines running, all loads will be supplied by the external power source via the external power relay and the closed contacts of the BTB (note that both GCBs will be tripped and the changeover relay will be energised closed). Multi-engine split AC bus system 2023-08-15 B1-11e Turbine Aeroplane Aerodynamics, Structures and Systems Page 48 of 140 CASA Part Part 66 - Training Materials Only When one of the aircraft’s engines is started and its generator is operating within system limits, its GCB will energise close. This will cause the external power relay to open, removing external power from the system loads. The BTB, however, will remain closed, connecting the three-phase power from the operational generator to all the aircraft’s loads. When the second aircraft engine is started and its generator is operating within system limits, its GCB will close. As the power to the BTB’s close coil is now redirected through the auxiliary contacts of the GCB to the BTB’s trip coil, the BTB will trip, causing the operational generators to supply their individual busbars. Power from the generator busbars is then distributed to the AC non-essential loads and TRUs. The essential AC loads are supplied from the AC essential bus, which under normal operating conditions (both AC generators operating within system tolerance), is connected via a changeover relay to the no. 1 generator bus. If one of the generators should become inoperative (fail or be switched off), its GCB will trip. Power is now supplied via the auxiliary contacts of the tripped GCB to the close coil of the BTB, causing the BTB to close. When closed, the BTB connects both generator buses together, thereby enabling the output from the serviceable generator to supply power to all system loads. The normal, essential and emergency buses are separated from each other, particularly with respect to order of importance for flight safety and in relation to redundancy following power malfunctions. If, for any reason, both generators should become inoperative (failed or switched off) then both GCBs will trip. Battery power will energise the BTB closed; however, as both generators are off line, no power will be available to operate the non-essential loads. In this situation, the changeover relay between the no. 1 generator bus and the essential AC bus will automatically de-energise and connect the essential bus to the static inverter. The system’s essential AC loads will be supplied with 115-V AC from the static inverter, while the non-essential AC loads will be effectively isolated. As we saw in DC systems, if the system operates for a long period of time under these conditions, the battery will become discharged. Therefore, before this occurs, the circuit’s battery relay will be turned “off,” isolating the aircraft’s AC and DC essential loads from power while allowing the aircraft to operate under emergency DC power. Relays, Breakers and Contactors There is much confusion surrounding the terminology of relays and solenoids because of their similarities. Relays are often called solenoids and vice versa. Many aircraft manufacturers have substituted the term contactor, relay or breaker for electrical switching solenoids. Relays are usually used for low-current switching applications. Relay (L) and contactor (R) functional diagram 2023-08-15 B1-11e Turbine Aeroplane Aerodynamics, Structures and Systems Page 49 of 140 CASA Part Part 66 - Training Materials Only The part of the relay attracted by the electromagnet to close the contact points is called the armature. The movement of the armature either closes or opens the contact points. In some cases, the electromagnet operates several sets of contact points simultaneously. Bus Tie Breaker Typical contactors used in high-current applications Bus Tie Breakers (BTBs) contain three heavy-duty contacts which connect three-phase power to the generator bus bars, where it is distributed to the aircraft AC loads. They also contain several auxiliary contacts that are used to connect various control and indication circuits within the AC distribution system. Power supplied to the close coil causes the main contacts to close and the auxiliary contacts change, so the normally open contacts close and become mechanically locked in this position. Power can now be removed from the close coil, and the breaker remains in the closed position. Power applied to the trip coil releases the mechanical lock, and spring-tension forces the main contacts to open and the auxiliary contacts to return to the normally closed position. BTBs may be interchangeable with three-phase contactors, Generator Circuit Breakers (GCB) or Bus Tie Contactors (BTC) of the same part number; however, each will perform different functions within the electrical circuit. 2023-08-15 B1-11e Turbine Aeroplane Aerodynamics, Structures and Systems Page 50 of 140 CASA Part Part 66 - Training Materials Only Generator Circuit Breaker The same contactor can be used a Generator Circuit Breaker (GCB). The main functions of the GCB in a split bus system are: To connect the AC generator’s output to its respective bus if the generator is serviceable To ensure that when the generator’s output is connected to the generator bus the bus tie breaker is tripped, therefore ensuring that the AC loads receive power from only one power source at any one time To isolate the generator’s output from the aircraft’s loads if a fault is detected by the generator control unit. 2023-08-15 B1-11e Turbine Aeroplane Aerodynamics, Structures and Systems Page 51 of 140 CASA Part Part 66 - Training Materials Only Auxiliary Contacts – Bus Tie Breaker and Generator Circuit Breaker Interlocking circuitry through auxiliary contacts of contactors and breakers is used to prevent unsynchronised power sources being connected in parallel. The auxiliary contacts have both normally closed and normally open contacts. The bottom set of contacts will trip all the other generator breakers, so ground-power cannot be connected to any generator. Switching on the oncoming source automatically switches off the present source. For example, if ground power is supplying the loads, and the APU generator is switched on the APU breaker will close. The APU breaker auxiliary contacts de-energise the ground power contactor, disconnecting ground power from the bus system. GCBs and BTBs 2023-08-15 B1-11e Turbine Aeroplane Aerodynamics, Structures and Systems Page 52 of 140 CASA Part Part 66 - Training Materials Only Inverters, Transformers and Rectifiers Inverters An inverter is used in some aircraft systems to convert a portion of DC power to AC. These inverters are usually built to supply current at a frequency of 400 Hz, but some are designed to provide more than one voltage, for example, 26-V AC in one winding and 115 V in another. There are two basic types of inverters: rotary and static. Either type can be single phase or multiphase. Rotary Inverter Rotary inverter Rotary inverters are motor-generators; a constant-speed DC motor is employed to drive an alternator (AC generator) designed to produce the power required. The rotors of the motor and the alternator are dynamically balanced and are mounted on the same shaft. Fans are also mounted on the shaft to provide for air cooling. Inverters utilize an input voltage of 26 to 29-V DC. The output is 115 V, single-phase; 115 V, three- phase; or 200 V, three-phase. The frequency is 400 Hz for all phases. 2023-08-15 B1-11e Turbine Aeroplane Aerodynamics, Structures and Systems Page 53 of 140 CASA Part Part 66 - Training Materials Only Maintenance of rotary inverters is set forth in the manufacturer’s maintenance or service manual. The control box on top of the inverter should not be disassembled in the field. If it appears to be defective, the entire inverter should be sent to a repair shop that is equipped to perform the electrical and electronic work and tests that may be required. Rotary inverters have automatic load demand (they begin operation once a load is activated and shut down when the load is removed). Disadvantages of a rotary inverter are a lack of frequency control, low surge capability (50% above maximum rating) and lower efficiency (50% to 80%). Rotary inverters generally require more scheduled maintenance than their equivalent static types due to the mechanical aspects of the DC motor, i.e., brushes and commutator. In most cases, rotary inverters have now been replaced by static inverters. Static Inverters A static or solid-state inverter serves the same functions as other inverters. However, it has no moving parts and is therefore subject to less maintenance problems than the rotary inverter. Static inverter The unit shown uses an input voltage of 18 to 30-V DC and produces an output of 115 V, single-phase alternating current with a frequency of 400 Hz. Static Inverter Basic Operation Static inverter block diagram 2023-08-15 B1-11e Turbine Aeroplane Aerodynamics, Structures and Systems Page 54 of 140 CASA Part Part 66 - Training Materials Only The internal circuitry of a static inverter contains standard electric and electronic components, such as diodes, transistors, capacitors and transformers. Refer to the block diagram: The filter provides a clean DC voltage to the 400 Hz oscillator. A 400 Hz oscillator produces signals with the correct timing (2.5 mS between pulses). The pulse shaper and power driver produce a 400 Hz square wave at the correct voltage and frequency. The harmonic filter removes everything that is not 400 Hz. The output stage/final filter conditions the signal for use (pure sine wave). A regulator circuit ensures the correct voltage and frequency are maintained. If static inverters require repair, they should be sent to an approved facility that is equipped to perform the work required. Because of miniaturisation of electronic components, static inverters have become relatively small and lightweight. This has made it possible for light single-engine aircraft to employ AC electrical systems for instrumentation. Transformers Transformer Transformers allow the values of AC voltage and current to be changed using mutual inductance. A typical transformer consists of two coils of wire wound around a common core but not connected electrically. When some alternating current flows in the primary coil, a voltage is induced into the secondary coil. The amount of voltage generated in the secondary coil is equal to the voltage in the primary times by the turns ratio between the two coils. 2023-08-15 B1-11e Turbine Aeroplane Aerodynamics, Structures and Systems Page 55 of 140 CASA Part Part 66 - Training Materials Only For example, 100 turns in a primary coil and 1000 turns in a secondary equates to a turns ratio of 1:10. Therefore, if 115 volts flows across the primary, 1150 volts are induced across the secondary. Since a transformer does not generate any power, the product of the voltage and the current in the secondary coil must be the same as that in the primary coil (less the transformer losses). Therefore, whenever volts are increased in a transformer, amperes must decrease by the same ratio. In other words, if the voltage is increased by a ratio of 1:10, the current must decrease by a ratio of 10:1. A transformer can have its primary coil connected directly across an AC power line, and if there is an open circuit in the secondary coil, the back voltage produced in the primary coil blocks the source voltage so almost no current flows through the primary winding. However, when the circuit is complete in the secondary coil, secondary current flows, producing lines of flux that oppose the back voltage and allow source current to flow in the primary coil. Multiple secondaries or tappings Some transformers may have multiple secondaries or tappings for various voltages (both higher and lower than supply voltage). A tap is nothing more than a wire connection made at some point on a winding between the very ends Multi-tap transformer 2023-08-15 B1-11e Turbine Aeroplane Aerodynamics, Structures and Systems Page 56 of 140 CASA Part Part 66 - Training Materials Only The winding turn/voltage magnitude relationship of a normal transformer holds true for all tapped segments of windings. Rectifiers Rectifier Principles Rectifier circuit It is often necessary to convert alternating current into direct current to power various circuits in the aircraft or within electronic equipment. The conversion of alternating to direct current is accomplished by a circuit referred to as a rectifier. Rectifier circuits typically employ diodes; these allow current flow in only one direction. In the illustration, the input would be stepped down from 115/200-V AC to around 30-V AC, which would then be rectified for a 28-V DC output. 2023-08-15 B1-11e Turbine Aeroplane Aerodynamics, Structures and Systems Page 57 of 140 CASA Part Part 66 - Training Materials Only Transformer Rectifier Unit Transformer rectifier unit Transformer Rectifier Units (TRUs) are designed to operate on a three-phase AC input and provide a continuous DC output. In the usual circumstance, it is 115-V AC (200-V AC phase to phase) 400 Hz going in and 28-V DC out. In the case of more modern aircraft (a 787, for example), the generators produce 235-V AC but are frequency wild (frequency governed by the rotational speed of the engine). They consist of a transformer and two three-phase bridge rectifier assemblies. The transformer has a star-wound primary winding and two secondary windings, one star and one delta. Each secondary is connected to an individual bridge rectifier, which is made up of six silicon diodes connected in parallel. A shunt connected in series with the output enables reading of amps at auxiliary terminals. Cooling of TRUs is typically by fan forced airflow. A thermal switch provides warning through an overheat (light) (set at 150 °C to 200 °C). 2023-08-15 B1-11e Turbine Aeroplane Aerodynamics, Structures and Systems Page 58 of 140 CASA Part Part 66 - Training Materials Only 400 Hz, three-phase AC full wave rectified The 400 Hz, three-phase AC, when full wave rectified by the six diodes, produces a DC voltage with a ripple frequency of 2400 Hz. A star-to-star transformer’s input and output are in phase. A star-to- delta transformer’s input and output are 30 degrees out of phase. The outputs of both secondary outputs are then full wave rectified. Therefore, the parallel rectified outputs of the two secondary windings have a DC ripple frequency of 4800 Hz. With such high frequency ripple, the DC voltage is almost linear, and the capacitive effect of the rectifier diodes smooths the ripple to an almost negligible amount. 2023-08-15 B1-11e Turbine Aeroplane Aerodynamics, Structures and Systems Page 59 of 140 CASA Part Part 66 - Training Materials Only Circuit Protection Fuse © Aviation Australia Typical fuses One of the cheapest and most simple forms of protection for electronic circuit is the fuse. Although the outer appearance of fuses varies widely in electronic and electrical appliances, the basic components of the physical construction are the same. These components are the body or case, mounting and fuse link. The body or case can be made of glass, ceramic, fibre or another non-conducting material. The body not only holds the fuse together, but its design and construction material have important functions. For example, a glass body allows easy identification of a blown fuse. Some ceramic fuses are designed for use in areas where a spark from a blowing fuse could be a hazard, especially in combustible environments. The mounting forms the electrical connection to the circuit. There are several types of mountings, including knife blade, cartridge or ferrule, and lead connection. The fuse link connects to the mounting and is the part of the fuse that ‘breaks’ the circuit. The fuse link is designed to disconnect circuit current once predefined limits are exceeded. The limits are determined by the size and composition of a fusing link. Once the current limit of the fusing link is exceeded, the heat generated by the current flowing through the fusing link will melt (or blow) the fusing link. There are various types of fuse link, including bead, element filament and others. In the cartridge fuse, the fuse link is enclosed in a tube of insulating material with metal ferrules at each end (for contact with the fuse holder). Some common insulating materials are glass, Bakelite or a fibre tube filled with insulating powder. In the slow-blow fuse illustration shown above, a wire wound resistor limits current flow and introduces a time factor. A fuse should only be replaced with one of the same voltage and current rating. 2023-08-15 B1-11e Turbine Aeroplane Aerodynamics, Structures and Systems Page 60 of 140 CASA Part Part 66 - Training Materials Only Current Limiter Current limiter The current limiter is another kind of fuse commonly found in aircraft power distribution systems and other high-current DC power systems. It is a device that behaves more like a fusible link than a fast- blow fuse. It is designed to protect against hard faults as opposed to continuous but small overloads. This device will carry nearly two times their rated current indefinitely and take over six times longer to open than a fast-blow fuse. Due to the long time constant and overload capability, current limiters are not subject to the nuisance tripping encountered with fuses. Current limiters are used in large aircraft to protect long power distribution leads that carry huge starter-generator currents and battery feeds. Circuit Breakers Circuit breakers overcome the one major disadvantage of a fuse when protecting a circuit. A fuse destroys itself, whilst a circuit breaker ‘trips’ and can be reset once the fault is rectified. Another advantage is that it gives a visual indication that circuit parameters have been exceeded and the circuit is no longer operating. There are magnetic and thermal circuit breakers. Magnetic Circuit Breaker Magnetic circuit breaker 2023-08-15 B1-11e Turbine Aeroplane Aerodynamics, Structures and Systems Page 61 of 140 CASA Part Part 66 - Training Materials Only Inside the sensing coil is a non-magnetic delay tube which houses a spring-biased moving magnetic core. An armature links the contacts to the coil mechanism, which functions as an electro-magnet. When the circuit breaker is set (button actuator pushed in, rocker actuator to the correct position, etc.), current flows through the sensing coil, and a magnetic field is created around the coil. As current flow increases above the circuit breakers ‘rated’ current, the following occurs: The strength of the magnetic field increases. The core moves towards the pole piece. Magnetic circuit efficiency is increased and electro-magnetic force increases. The core reaches the fully ‘in’ position. The armature is attracted to the pole piece. The trip mechanism activates (and the circuit breaker is ‘tripped’). The contacts are opened. The circuit breaker must be reset manually. Thermal Circuit Breaker Thermal circuit breaker 2023-08-15 B1-11e Turbine Aeroplane Aerodynamics, Structures and Systems Page 62 of 140 CASA Part Part 66 - Training Materials Only A thermal circuit breaker uses a bimetallic strip to operate. The basic internal construction of a thermal circuit breaker is shown above. The thermal circuit breaker consists of three major assemblies: Bimetallic thermal element Contact-type switch unit Mechanical latching mechanism. In normal operation, current flows through the main contacts and thermal element to the load. The heat produced in the thermal element is radiated away quickly. When current exceeds the circuit breakers rating (as in a short circuit), the temperature of the thermal element begins to build up.Due to the different rates of expansion of the two metals in the thermal element, the following actions occur: The thermal element distorts. The latch mechanism releases. The main switch contacts open. The push button extends. The circuit breaker has now tripped. No current is supplied to the load. Circuit breaker panels are clearly labelled to show the circuits they protect, and circuit breakers must clearly show their current rating in amps. The primary reason why circuit breakers and fuses are so close to the power supply (busbar) is to protect the wiring run from short circuits, which would cause an overload and possible fire. The secondary feature is to protect the component at the end of the wiring. Tripped circuit breaker 2023-08-15 B1-11e Turbine Aeroplane Aerodynamics, Structures and Systems Page 63 of 140 CASA Part Part 66 - Training Materials Only A small white band shows when the circuit breaker is tripped, activated or popped. This aids with the identification of tripped circuit breakers on aircraft panels. Trip-Free/Non-Trip Free Circuit Breakers Circuit breakers are classified as being trip free or non-trip free. A trip-free circuit breaker is a circuit breaker that will trip (open) even if the operating mechanism (on-off switch) is held in the on position. A non-trip-free circuit breaker can be reset and/or held on even if an overload or excessive heat condition is present. In other words, a non-trip-free circuit breaker can be bypassed by holding the operating mechanism on. Trip-free circuit breakers are used on circuits that cannot tolerate overloads and on nonemergency circuits. Examples of these are precision or current sensitive circuits, nonemergency lighting circuits and nonessential equipment circuits. Non-trip-free circuit breakers are used for circuits that are essential for operations. Examples of these circuits are emergency lighting, required control circuits and essential equipment circuits. Circuit Breaker Notes A small white band shows when tripped. They protect circuit wiring. They can be reset and there is no need to carry spares. There are magnetic or thermal (bimetallic) types. Breakers are either trip free or non-trip free. Trip free will still trip even if trying to reset. Thermal trip free must cool down before being reset. Non-trip free can be manually held closed. The most common is trip-free thermal. Circuit Breaker Precautions If a circuit breaker has tripped, do not immediately reset it. First, isolate the faulty circuit or component and repair it, then reset the circuit breaker. Resetting it immediately could result in further damage to the circuit or equipment being protected. When replacing a damaged or unserviceable circuit breaker, only use the circuit breaker stated in the applicable publication. Failure to adhere to this could damage the circuit or equipment the circuit breaker is protecting. 2023-08-15 B1-11e Tu