Chapter 1: Supply Chain Management PDF
Document Details
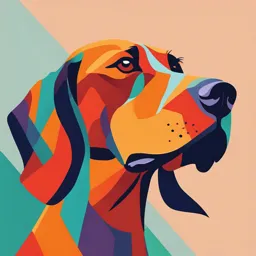
Uploaded by EverlastingTuba
Tags
Related
Summary
This document details the basic concepts and overview of supply chain management, focusing on features, benefits, functions, and factors affecting supply chains in the hospitality industry. It provides a high-level introduction to supply chain processes and their roles in different levels of business operations.
Full Transcript
CHAPTER 1: BASIC CONCEPT AND OVERVIEW OF SUPPLY CHAIN MANAGEMENT A supply chain involves a network of suppliers, manufacturers, assemblers, delivery centers, and logistics installations that perform functions like material sourcing, processing...
CHAPTER 1: BASIC CONCEPT AND OVERVIEW OF SUPPLY CHAIN MANAGEMENT A supply chain involves a network of suppliers, manufacturers, assemblers, delivery centers, and logistics installations that perform functions like material sourcing, processing, and shipment to buyers, including manufacturers, shipping providers, warehouses, dealers, and consumers. FEATURES OF SUPPLY CHAIN MANAGEMENT 1. Integrated behavior- client and provider work closely together, sharing information and making decisions as a team. 2. Mutually Sharing Information- Efficient SCM exchange of information between channel participants is needed. 3. Mutually Sharing Channel Risk and Rewards- means that supply chain partners share both the potential losses and the benefits to maintain long-term success and competitiveness. 4. Cooperation- Cooperation in a supply chain means that all participants work together, aligning their efforts and operations, to achieve better overall results than they could individually. 5. Focus on Serving Customers- means that all members of the supply chain work together with a shared goal of meeting customer needs and ensuring their satisfaction. 6. Integration Processes- involve aligning and connecting all systems and functions within the supply chain, from production to delivery, often requiring collaboration between different departments, suppliers, and third-party services to work smoothly together. 7. Partners to Build and Maintain Long-term Relationships- means that successful partnerships focus on aligning policies and reducing overlap, which helps partners work more efficiently and cost-effectively, provided they share compatible cultures and management strategies. BENEFITS OF SUPPLY CHAIN 1. Builds stronger partnership and support clients 2. Provide better distribution processes, with less delay 3. Increases efficiency and functions for companies 4. Lowers shipping and warehouse costs 5. Eliminates costs directly and implicitly 6. Supports the shipping at the right spot with the right goods 7. Enhances asset management and encourages the effective implementation of just in time inventory models 8. Assists business in responding to global dynamics 9. Assists business in the supply chain to reduce duplication and eliminate risk FUNCTIONS OF SUPPLY CHAIN MANAGEMENT 1. Strategic level- Optimize network: Improve the setup and location of warehouses, fulfillment centers, and facilities. Build relationships: Develop crucial contacts and integrate technology like cross- docking or third-party logistics. Manage inventory: Balance new and existing goods, and manage supply chain capacity. IT in operations: Oversee information technology systems in the supply chain. Align plans: Ensure the corporate strategy aligns with supply chain strategies. 2. Tactical level- Sourcing and procurement: Make decisions about acquiring materials and resources. Production decisions: Plan contracts, schedules, and operations for production. Purchasing: Choose inventory size, location, and consistency. Transportation: Plan transport strategies, including speed, routes, and contracts. Benchmarking: Compare processes and practices against competitors. Cost management: Monitor fees and set milestones. Customer focus: Address customer demand and habits. 3. Operational level- Daily output coordination: Manage the allocation of production at each plant minute by minute. Demand preparation and forecasting: Align customer needs and share predictions with suppliers. Supply preparation: Coordinate with vendors on inventory and forecast demands. Inbound activities: Handle retailer transport and receipt of shipments. Production processes: Oversee material use and the flow of finished products. Outbound operations: Manage customer efficiency, warehousing, and transport tasks. Order fulfillment: Process orders from retailers, production, and fulfillment centers, respecting supply chain constraints. Transit disruption: Address and plan for disruptions and manage consumer payments with insurance. FACTORS AFECTING SUPPLY CHAIN IN HOSPITALITY INDUSTRY a. Customer satisfaction: In the hotel industry, guests are highly valued, sometimes referred to as "GOD." Ensuring consistent customer satisfaction can be challenging. b. Management systems: Different hotel management models, such as operators, franchisees, and chain hotels, have different effects on supply chain management. c. Market trends: Modern trends show that computerized property management systems are primarily used for front office tasks and reservations. CHALLENNGES OF HOSPITALITY INDUSTRY RELATED TO SUPPLY CHAIN 1. Raw Material Costs: In the hotel industry, raw material costs are high, especially for organic consumables. Hotels often buy large quantities at low prices, but due to perishability, bulk purchases can go to waste. 2. Material Ordering Costs: Agencies often use handwritten orders and handle transactions independently. 3. Inventory Handling: Uncertain product forecasts often lead to overstocking. The purchasing department may stockpile large quantities but fail to deliver items on time, increasing expenses. 4. Emergency Purchases: Lack of preparation leads to frequent emergency purchases, made on-the-spot and later formalized with paperwork. CHAPTER 2: SUPPLY CHAIN MANAGEMENT STRATEGY Hospitality management involves strategic, tactical, and operational supply chain decisions that impact the entire business, aligning with the company's overall business plan and affecting all processes. DECISION AREAS ON STRATEGIC SUPPLY CHAIN PROCESSES 1. Product development- When sales drop or product cycles mature, management may choose to launch new versions, streamline the product portfolio, or expand the range of products and services. 2. Customers: At the strategic stage, an organization must identify and understand its clients for its goods and services. 3. Manufacturing: At the strategic level, decisions involve choosing the right manufacturing facilities and technologies. 4. Suppliers: The company’s management must settle on strategic supply chain plans for vendors. 5. Logistics: Logistics is crucial for supply chain performance. Effective order delivery and distribution network decisions are key for business leaders. DEVELOPMENT OF SUPPLY CHAIN STRATEGY 1. Customer Requirements: A supply chain that is demand-driven and customer-focused is both productive and reliable. 2. Internal Capabilities: A thorough review of internal supply chain capabilities is essential to identify gaps between current success and customer needs. 3. Supply Chain Trends: Organizations must use a coordinated supply chain approach to identify key patterns and determine solutions for each. 4. Competitive Analysis: The company must evaluate the market and competitors to make informed strategic decisions on what actions to take or avoid. 5. Supply Chain Technology: Technology enables an enterprise to integrate and sustain innovative processes and capacities within its supply chain strategy. 6. Risk Assessment: Weak risk identification, priority setting, management, and mitigation pose a significant challenge to an enterprise's supply chain and policies. RISK AFFECTING SUPPLY CHAIN MANAGEMENT Supply risk Demand risk ✓ Supplier opportunism ✓ Inbound product quality ✓ Demand variability ✓ Transit time variability ✓ Forecast errors ✓ Risks affecting suppliers ✓ Competitor moves ✓ Risks affecting customers Operational risks ✓ Inventory ownership ✓ Asset and tools ownership ✓ Product quality and safety