Total Quality Process Chapter 13 PDF
Document Details
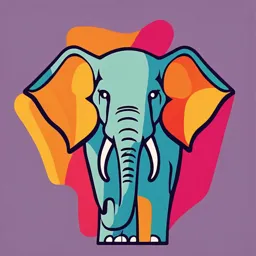
Uploaded by PraisingCerium
Tags
Related
- Quality Assurance and Total Quality Management CA2 PDF
- Deming's 14 Points On Total Quality Management PDF
- Evolución del Concepto de Calidad PDF
- Quality Improvement in the Modern Business Environment PDF
- Total Quality Management (TQM) Introduction and Evolution PDF
- Operations Management Continuous Improvement PDF
Summary
This document chapter discusses the concept of Total Quality management. It explains how Total Quality differs from conventional quality and emphasizes the importance of preventing defects rather than just detecting them. The chapter also introduces ISO 9001 standards and their importance.
Full Transcript
Chapter – 13 Total Quality Process 13.1 Introduction Quality may be defined as the degree to which a set of inherent characteristics fulfils requirements. These inherent characteristics may include the following: Physical (e.g. mechanical, electrical, chemical or biological characteristics) Sensory...
Chapter – 13 Total Quality Process 13.1 Introduction Quality may be defined as the degree to which a set of inherent characteristics fulfils requirements. These inherent characteristics may include the following: Physical (e.g. mechanical, electrical, chemical or biological characteristics) Sensory (e.g. related to smell, touch, taste, sight, hearing) Behavioral (e.g. courtesy, honesty, veracity) Temporal (e.g. punctuality, reliability, availability) Ergonomic (e.g. physiological characteristic or related to human safety) Functional (e.g. maximum speed of an aircraft) The concept of total quality represents the way a company runs its business and it needs a structure approach embracing – Quality improvement Quality control Just-in-time concept & other business improvement activities to mobilise for organised creation of beneficial change in the business with outcomes as – Continuous cost reduction Elimination of variability Reduction in plant downtime Increase in yield Just-in-time concept and Improved human relations The concept of Total Quality differs from the conventional sense of quality in a way that total quality aims at the prevention of defects and starts at the beginning of the process rather than detection of defects at the end of the product line. Relying on the cost of non-conformance, Total Quality engulfs everybody at all levels and at all stages of the process as a user, as a processor, as a supplier for Quality performance and is with the main objective of satisfying the needs & requirements of the customer both internal and external. This customer perception is the essence of Total Quality thinking which directs a project team for quality improvement to apply Total Quality techniques using all of the statistical and problem solving, skills in the right environment together with various behavioural concept just introducing Total Quality is not enough. There must be clear objectives which are known to all levels of employees. It is the teamwork, which gives real power to Total Quality. 99 13.2 Total Quality Management Four major element of total quality Systems Processes Management *Quality Audit * Process *Style * Management of people *Teamwork through Cross Functional participation voluntary The power house of in improvement Total Quality activities Capability *Process control *Quality Assurance People *Process improvement The tools and concepts used in Total Quality consist of a number of techniques collectively called “Seven Quality Management Tools” – a. Pareto Analysis/Diagram b. Cause & Defect Diagram c. Stratification d. Check Sheet e. Histogram f. Scatter Diagram g. Graph & Control Chart It is the interaction between these which makes Total Quality a real fire arm and which needs emphasis on the following points – a. Strive for thorough policy control b. Aim at priorities c. Aim at problem solving d. Coordinate with various departments – quality, cost & production e. Smooth PDCA cycles f. Data cycles and fact finding Supervisor’s Role in TQP1. Study the existing cultural pattern 2. Identify those aspects, which need change 3. Secure active participation of others involved – including customer participation as well as his active assistance 4. Start on a small scale and use results to broaden application 5. Make Quality improvement project by project and in no other way 6. Make use of available tools 100 7. Make studies with application of simple to sophisticated tools of SQC 8. Provide sufficient for mental change to take place 9. Training and self-development programmes should be carried out as planned 10. Avoid surprises 11. Build Quality into the products during manufacturing 13.3 Awareness of ISO Standards International Organization for Standardization (ISO) is a world body constituted by 91 national standard making organizations including our BIS (Bureau of Indian Standards). ISO 9001 is the model for Quality Management System. It is the outcome of a need for having world parity in standards for meeting customer requirements. The need for adapting ISO 9001 by the Indian industry gains significance with the functioning of the European market and the trust given by the Government for boosting our export. ISO 9001 defines a bare minimum of quality standards for products/services being acceptable at international levels. ISO 9001 sets out the criteria for a quality management system and is the only standard in the family that can be certified to (although this is not a requirement). It can be used by any organization, large or small, regardless of its field of activity. In fact, there are over one million companies and organizations in over 170 countries certified to ISO 9001. This standard is based on a number of quality management principles including a strong customer focus, the motivation and implication of top management, the process approach and continual improvement. These principles are explained in more detail in ISO’s quality management principles. Using ISO 9001 helps ensure that customers get consistent, good-quality products and services, which in turn brings many business benefits. The objective of ISO 9001 is to provide a set of requirements that, if effectively implemented, will give you confidence that your supplier can consistently provide products and services that: Meet your needs and expectations Comply with applicable regulations ISO 9001 adopts a risk-based (“preventive”) approach to quality that covers a wide range of topics, including your supplier’s top management commitment to quality, its customer focus, the adequacy of its resources, employee competence, process management (for production, service delivery and relevant administrative and support processes), quality planning, design of the products and services it provides, review of incoming orders, purchasing, the appropriate monitoring and measurement of its processes, products and services needed to ensure conformity, its processes to resolve customer complaints, corrective actions, and a requirement to drive improvement. 101 Quality Management Principles There are 7 Quality Management Principles. These are: a. Customer focussed organization b. Leadership c. Engagement of people d. Process approach e. Improvement f. Evidence based decision making g. Relationship Management These principles are not listed in priority order. The relative importance of each principle will vary from organization to organization and can be expected to change over time. ISO 9001Certified Areas All plants and Units ISO QMS certifications in their area. BSP has received Integrated Management System (IMS) Certificate by a single certifying agency (M/s DNV), integrating QMS, EMS, OHSAS & SAMS - becoming the first SAIL unit and among few corporate houses in India to achieve this unique distinction.. Quality Policy of SAIL: --- 102