Operations Management Continuous Improvement PDF
Document Details
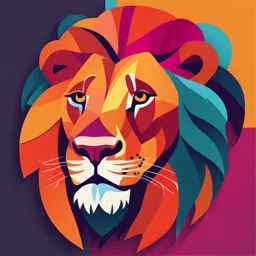
Uploaded by DelightfulHeliotrope2387
Polytechnic University of the Philippines - Taguig Branch
Tags
Summary
These notes cover the core principles of Total Quality Management (TQM) and continuous improvement, including Juran's Trilogy, Kaizen, 5S Methodology, PDCA, 7 Quality Tools, and more. They explain concepts like Pareto Analysis, Fishbone Diagrams, Control Charts, and Histograms.
Full Transcript
POLYTECHNIC UNIVERSITY OF THE PHILIPPINES - TAGUIG CAMPUS CORE TQM PRINCIPLES: CONTINUOUS IMPROVEMENT POLYTECHNIC UNIVERSITY OF THE PHILIPPINES - TAGUIG CAMPUS Students will be able to: evaluate organizational processes to identify are...
POLYTECHNIC UNIVERSITY OF THE PHILIPPINES - TAGUIG CAMPUS CORE TQM PRINCIPLES: CONTINUOUS IMPROVEMENT POLYTECHNIC UNIVERSITY OF THE PHILIPPINES - TAGUIG CAMPUS Students will be able to: evaluate organizational processes to identify areas for improvement and apply continuous improvement techniques and tools. understand continuous improvement strategies that foster incremental enhancements in quality, efficiency, and customer satisfaction within a business context. analyze the impact of continuous improvement initiatives on organizational performance Continuous Improvement refers to an ongoing, systematic effort to enhance processes, products, services, and overall organizational performance. Key components of continuous improvement Incremental Progress Continuous improvement involves making small, incremental changes to processes rather than large, disruptive ones. Key components of continuous improvement Employee Involvement Employees at all levels are encouraged to actively participate in identifying areas for improvement and proposing solutions. x Key components of continuous improvement Data-Driven Decision Making Continuous improvement relies on the analysis of data and performance metrics to identify weaknesses and opportunities for improvement. Key components of continuous improvement Feedback Loops Regular feedback loops are established to monitor the impact of changes and to gather insights from employees and customers. Key components of continuous improvement in T Adaptability Continuous improvement recognizes that the business environment is dynamic. Key components of continuous improvement Integration into Organizational Culture To be successful, continuous improvement should become a core element of the organizational culture. Juran’s Trilogy Juran’s Trilogy is a holistic approach to quality management introduced by Dr. Joseph Juran. It comprises three interconnected components essential for achieving and maintaining quality excellence. Juran’s Trilogy Quality Planning Quality Control Quality Improvement 1. Quality Planning Quality Planning is the activity of developing the products and processes required to meet customers' needs. It involves: Customer-centric approach. Setting quality objectives and standards. 2. Quality Control Quality Control is the activity of monitoring production activities to ensure that they are producing the correct product or service according to plan. It includes: Monitoring the performance of the processes Ensuring that all steps in the process are performed correctly Corrective action when necessary 3. Quality Improvement Quality Improvement is the activity of making changes to improve the process and raising quality performance to unprecedented levels (breakthrough). This may involve: Establish the quality improvement infrastructure Identify the improvement projects Provide the resource, motivation, and training needed by the team Kaizen Kaizen is a key concept in Total Quality Management (TQM) that emphasizes continuous improvement. 5S METHODOLOGY Sort (Seiri) Set in Order (Seiton) Shine (Seiso) Standardize (Seiketsu) Sustain (Shitsuke) 5S METHODOLOGY PDCA (Plan-Do-Check-Act) PDCA stands for Plan-Do-Check- Act, a systematic and iterative four-step management method used for the continuous improvement of processes and products. 7 Quality Tools ±Pareto Analysis ±Cause-and-Effect Diagrams ±Control Charts ±Histograms ±Scatter Diagrams ±Flowcharts ±Check Sheets Pareto Analysis Pareto Analysis is a technique used to prioritize tasks, problems, or issues based on the principle that a small number of factors are responsible for the majority of the results or problems. The Pareto Principle, or the 80/20 rule, is applied, suggesting that roughly 80% of the effects come from 20% of the causes. Fishbone Diagrams ±Fishbone Diagrams , also known as Cause-and-Effect Diagrams or Ishikawa Diagrams, are visual tools used to identify and analyze the potential causes of a specific problem or effect. Control Charts Control Charts are statistical tools used to monitor and control processes over time. Histograms ±Histograms are graphical representations of the distribution of data, showcasing the frequency of occurrences. Scatter Diagrams ±Scatter Diagrams are visual representations of the relationship between two variables. Flowcharts A flowchart is a visual representation of a process, showing the steps and decisions involved in completing a task or solving a problem. It uses symbols and arrows to illustrate the flow of activities from the start to the end. Check Sheets A check sheet is a simple and structured form used for collecting and organizing data in a systematic way. Seven Deadly Wastes 1.Overproduction 2.Inventory (Excess Inventory) 3.Waiting 4.Transportation 5.Motion (Unnecessary Movement) 6.Overprocessing 7.Defects Business Process Reengineering (BPR) Business Process Reengineering (BPR) is a management approach that involves the radical redesign and restructuring of an organization's business processes to achieve significant improvements in performance, efficiency, and overall effectiveness. QUESTIONS? PREPARE FOR A QUIZ LESSON END