Safety and Health Management in SAIL
Document Details
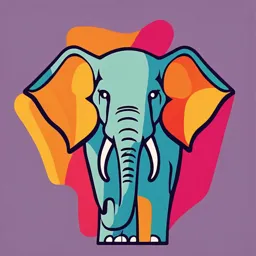
Uploaded by PraisingCerium
Tags
Related
- Industrial Health and Safety Management System PDF
- Safety Management Systems PDF
- Bab 5: Siasatan Dan Pelaporan Kemalangan PDF
- Management of Occupational Health and Safety Test Bank PDF
- Industrial Safety (The Occupational Health and Safety) PDF
- Safety Refresher Training Manual PDF (Southern Petrochemical Industries Corporation Ltd)
Summary
This document details SAIL's Safety and Health Management system, highlighting engineering controls, education initiatives, and enforcement measures. It emphasizes continuous improvement and employee involvement in achieving zero-harm goals within steel plants and units.
Full Transcript
Chapter – 12 Safety and Health Management in SAIL 12.1 Introduction: SAIL believes that excellence in Safety and Health yields excellent business results, therefore at SAIL nothing is more important than the Safety and Health of the people working in and around the steel plants & units. To ensure th...
Chapter – 12 Safety and Health Management in SAIL 12.1 Introduction: SAIL believes that excellence in Safety and Health yields excellent business results, therefore at SAIL nothing is more important than the Safety and Health of the people working in and around the steel plants & units. To ensure this, SAIL has been continually & consistently improving its safety and health management systems & practices with the ultimate aim to have safe and healthy workplace. Safety is fully adhered in all processes and operations inside Plants/ Units premises. Safety & Health issues are monitored and guided from the apex level of management i.e. our Board as well as Board Sub-committee on Health, Safety & Environment. All pertinent issues related to safety & health are discussed and deliberated as opening item at all appropriate forums in various levels of management hierarchies. SAIL envisions to become as one of the industry’s leaders in safety performance. To realize this vision, SAIL has a Corporate Safety Policy and Guiding Principles aiming at providing a safe and conducive work environment to all its employees, contractors and all stakeholders / people associated in its operations including those living in the neighborhood of its Plants, Mines and Units. All safety activities & measures are planned in consonance with the Safety Policy. With the aim of continuous improvement, the safety & health objectives are planned and set well in advance and successfully achieved through well-established OH&S management programmes. SAIL has achieved consistent improvement and steady growth in Safety and Occupational Health parameters as a result of proper systems, procedures and improved work practices. Internationally established standards like ISO 45001, ISO 9001 and ISO 14001 are adopted for Safety, Occupational Health, Quality and Environment protection based upon the P-D-C-A philosophy of continual improvement. Safety Setup Effective leadership is critical in achieving and sustaining a positive Safety culture that supports the goal of zero harm. Safety performance is regularly monitored at the highest level of management i.e. Board, Chairman and Directors' level. The efforts of 88 the Company for achieving a safe and healthy environment are guided and monitored by a Board Sub Committee on Health, Safety & Environment (BSC on HSE) on quarterly basis. Director I/cs & Executive Directors of respective Plants & Units closely monitor safety aspects on day-to-day basis. A full-fledged Safety Engineering Deptt. (SED) functions at each Plant/ Unit to ensure safety in operations & maintenance/ repair jobs. Fire Services Deptt., fully equipped with necessary resources & facilities, remains on alert for meeting various emergency requirements, relief & rescue operations as well as monitoring fire prevention related aspects. In each department/ shop, Departmental Safety Officer (DSO) & Safety Steward/ Captain ensures adherence to laid down standards & safe working procedures. DSOs play an important role by monitoring safety aspects at the forefront on daily basis and working in close coordination with SED. In Project & expansion areas, Zonal Safety Officers (ZSOs) are deployed to monitor safety during various phases of project / construction work. 1.1 Systems & Procedures The entire Safety Management System of SAIL hinges around 3 E’s of accident prevention i.e. Engineering, Education & Enforcement. a) Engineering: Safety is ensured by incorporating engineering measures & features i.e. thru’ built-in features at design stage. Safety interlocks, limit switches, alarms & detectors, CCTVs, Fire retardant paint on cables etc. are few examples of Engineering measures which protect the men & machines from abnormal situations. These measures/ devices/ facilities are checked periodically for smooth & effective functioning. b) Education: Emphasis is given on competency building on continuous basis to cover at least one-third of the workforce in various training programmes including safety & health. Safety training programs are being organsied at CHRD of Plants/ Units round the year for regular employees as per fixed modules covering topics like statutory requirements, gas safety, electrical safety, crane safety, conveyor safety, material handling, Behavior Based Safety (BBS), occupational health & hygiene, first aid, stress management, preventive care for occupational diseases etc. For different work zones/ areas, 'Learning from Each Other (LEO)' workshops with participation of other Indian steel producers covering salient issues of concern as well as 'Large Group Interactions' are organised which helps in greater and effective sharing & learning. Besides, there are unit training centres at Departmental level where technical & safety 89 trainings are also organized as per need. For Contractual workers, Induction training of two days duration followed by job specific training covering areas specific hazards & associated risks as well as control measures is imparted before engaging them on the job. Practical training cum demonstration is organized for hazardous jobs like work at height, roof sheeting jobs etc. on training rig, especially fabricated for the purpose. Feedback is taken from the participants which is constructively used to bring further improvements. c) Enforcement: Safety aspects have been incorporated in SOPs, SMPs & WIs which helps in maintaining necessary technological discipline. These documents provide vital guidance to the workmen and are reviewed periodically with changing technology / process requirements, occurrence of any incident etc. and updated accordingly. The updated version of the documents is made readily available on web portals /Knowledge Management (KM) portals and can be easily accessed and referred by all employees. ‘Permit to Work’ & ‘Protocol’ Systems, having necessary safeguards, are religiously followed during execution of hazardous & critical jobs involving multiple agencies. Emergency preparedness Plan has been prepared for handling emergency situations and mock drills with the involvement of all the connected agencies like deptt. concerned, SED, Fire Services, Gas Safety, OHSC etc., are conducted to assess preparedness. Usage of conventional as well as job specific Personnel Protective Equipment (PPEs) such as safety shoes, safety helmet, Ear plug/ muffs, nose mask, Fire-retardant garments, Full body harness, arc flash suits etc. by regular employees as well as contractual workers is ensured. Road safety, gas safety, height safety, handling of hot metal/ slag, electrical safety, material handling safety norms etc. are strictly enforced inside plant premises by constant monitoring. 1.2 As a compliance to advanced safety management system (ISO 45001), Hazard identification & Risk assessment (HIRA) has been done for most of operation & maintenance activities in Plants/ Units and appropriate risk control measures are being taken (as per risk control hierarchy) to bring the risk to acceptable limits (ALARP – As low as reasonable Practicable). 1.3 Compliance to Statutory requirements like the Factories Act, Mines Act, Rules & Regulations, Electricity Act & Rules, Petroleum Act & Rules, Explosive Act & Rules etc. is ensured. 1.4 All work related incidents are investigated to find out the root cause and appropriate actions are taken to prevent its recurrence. The needed corrective & preventive actions are taken to minimize the risk as per 90 the hierarchy of controls. 1.6 Employees involvement in Safety Management Joint participation of management & workmen is important for a sustainable health and safety culture which is maintained by the Company's Health and Safety Committees. All of our employees are covered by the formal joint management-worker Health and Safety Committees at Plant/ Units and are duly involved and consulted on Health & Safety issues including in identification & mitigation of workplace hazards. Statutory Bipartite forums like Central/ Apex Safety Committees, Departmental Safety Committees, Pit safety committee etc. function with participation of Company's top management, trade union representatives & employees. Meetings of these Committees are held in a scheduled manner in which all health and safety issues are deliberated for bringing continuous improvement of the OH&S Standards. 1.7 Safety Monitoring Mechanism Three tier Safety Audits are being conducted at plants & units as mentioned below: a) Internally by concerned Area Safety Officer of Safety Engg. Department & DSO. b) Safety audit by SAIL Safety Organization. c) Externals safety audits by third parties as per statutory requirements. Safety inspections are conducted at different levels in Plants & Units. a) Apex Inspection by HOD, Sectional I/Cs & DSO. b) By Safety Engg. Department associating DSOs. 91 c) By Safety Engg. Department associating different departments like Civil Engg. Department, Electrical Department, Crane Engg Department, Structural Inspection Departments etc. d) Fire Safety Inspections by Fire Services Department associating DSOs & departmental personnel. e) Apex inspection by line managers & DSOs. f) 1.8 Behavioural Interventions as a part of ongoing Safety Management consultancy, with a view to identify unsafe acts & situations in the plants. Safety Review: Periodic review of safety performance is made at top management level including DICs, Head of Works, and Head of Departments & Heads of Safety of respective plants / units. Issues of concern are discussed and strategic action plans are drawn on priorities to bring continuous improvement. 12.2 SSO- FORMATION, ROLES & RESPONSIBILITIES At the Corporate level, SAIL Safety Organization (SSO) was formed in 1988, to coordinate, guide& facilitate the Safety and Fire service activities of Plants & Units. The major functions of SSO are: a) To facilitate in development of safety culture across the Plants & Units. b) Development of policies, systems and procedures for workplace safety improvement. c) Conduct periodic audits of Safety Management System of Plants & Units to ascertain its effectiveness and suggest measure to liquidate the gaps, if any. d) Competence building through training of employees. e) Performance monitoring by organizing periodic review meetings. f) Conducting on-the-spot study of fatal / serious incidents. g) Maintaining Incident/Accident Data Management & Information System. h) Carrying out secretarial functions of JCSSI (Joint Committee on Safety, Health & Environment in Steel Industry). i) Liaison with CO, MoS, Parliament cell, NSC, WSA etc. j) Spreading awareness through publications, competitions etc. 92 a) To facilitate in development of safety culture across the Plants & Units: It is increasingly being recognized that Safety being a cultural issue, by bringing attitudinal change towards safety, change in mindset & behavior of the individuals will take place which will help in improving safety culture at company level. With this objective, a safety consultant of global repute has been deployed at 5 ISPs i.e. Bhilai, Bokaro, Rourkela, IISCO Steel Plant, Durgapur Steel Plants & Alloy Steels Plant for strengthening the safety management systems apart from addressing behavioural related issues. SSO played a key role in preparation of NIT mainly w.r.t defining the eligibility & capability criteria as well as evaluation of suitable bidders. b) Development of policies, systems and procedures for workplace safety improvement: ‘Inter Plant Standards in the Steel Industry (IPSS)’ in the area of safety help in a big way in augmenting our safety standards. IPSS 1:11-Standards Committee on Personnel Safety Appliances and Procedures, which is headed by ED, SSO and represented by SAIL, Tata Steel Ltd., RINL, MECON, JSPL, HEC etc. formulates new standards as well as reviews and updates existing standards by utilizing knowledge & experience of domain experts as well as core safety professionals. IPSS standards are available for various kinds of jobs such as Working at Height, Roof sheet changing, Wagon tippling, demolition of building & structures in steel industry, loco operation, Gas Line jobs, Hydraulic safety, etc. The standards formulated by the committee serve as a useful reference document and are uploaded on IPSS portal which is available in the SAILNet as well as open domain i.e. internet and accessible for the benefit of common user. SAIL played a key role as one of the member of working group headed by ED, SSO which was constituted by MOS for preparation of comprehensive Code of Practices for enhancing the safety eco-system in the steel producers in the Iron & Steel sector. 25 nos. safety guidelines were finalized and uploaded on the MOS website for reference & use by all stakeholders. Further, process based safety guidelines are being framed in consultation with leading steel producers. c) Conducting periodic audits of Safety Management System of Plants & Units to ascertain its effectiveness and suggest measures to liquidate the gaps, if any: 93 To assess the effectiveness of prevailing OS&H systems, compliance to regulatory requirements and identify areas or improvement, Safety Audits are conducted by SSO on regular basis as per APP in accordance with Indian Standard IS 14489:2018 i.e. 'Code of Practice on Occupational Safety & Health Audit' associating sister plants. Major departments of all Plants/ Units including Mines and Warehouses are covered during such audits. Emphasis is laid on identifying issues of concern and carries out in-depth system-based audit. Compliance audits are also conducted to verify implementation status of suggested measures. System of conducting Theme based audits has been introduced recently, covering specific theme such as ‘Fuel Gas Safety’ in the plants. Of late, the audit process has been enriched by introducing reality check mechanism i.e. checking the actual level of safety perception among the working personnel, vis-à-vis desired level. Also surprise audit is carried out to any other deptt. or projects site. d) Competence building through training of employees: HRD interventions in safety include organizing training programmes for safety officers and DSOs of Plants & Units at MTI / plant locations. Thrust has been laid by SSO to organize LEO workshops on identified areas of concern like Gas safety, Safety in Iron making/ steel making / Rolling, Electrical safety, Crane safety, Rail/ Road safety etc. with participation of SAIL plants as well as other private steel producers in India. For mines & collieries, customized training programmes are organized with the help of external expert agencies. In addition, a nos. of webinars are conducted through digital platforms on topics of relevance/ importance for the plant personnel with the help of experts from DGFASLI/ in-house domain experts. e) Performance monitoring by organizing periodic review meetings: Structured review meetings are conducted by SSO through scheduled Heads of Safety & Heads of Fire Services meetings of all SAIL plants /units. Periodic visits of Head of SSO to Plants are held where interactions at various levels like HOS, HODs & CGMs, DSOs etc. are held and feedback is given to Head of Works & DIC. 94 f) Conducting on-the-spot study of fatal / serious incidents: On the spot study is carried out for fatal / serious incidents and report containing various aspects along with root cause analysis & recommendations to prevent recurrence, is circulated to all Plants & units for horizontal deployment. An e-book of fatal accident case studies is published every year by SSO and circulated to Plants & units learning & implementation. Compliance status of recommendations is monitored by SSO & at various levels in Plants/ Units. g) Maintaining Incident / Accident Data base for generation of MIS reports: All incidents including near miss cases are compiled and analyzed by SSO on monthly & annual basis for determining the thrust areas. Daily, Monthly & Annual reports are published by SSO based on the information received from Plants& Units and circulated to all concerned. In accordance with MoS target of covering 100% employees in training programmes every year, training figures are compiled on weekly basis and communicated to MoS for dashboard. h) Carrying out secretarial functions of JCSSI (Joint Committee on Safety, Health & Environment in Steel Industry): Joint Committee on Safety, Health & Environment in the Steel Industry (JCSSI), a unique bipartite forum at national level with representation from major central trade unions and management of major steel producers of the country, acts as a common bridge by jointly evolving recommendations/ action plans for ensuring safe & healthy work environment in the entire steel industry. For recognizing and rewarding good safety performance of the member organizations & their employees, various competitions and an annual award function & meetings of the Committee are organized. Distinguished performance of the individuals is also suitably rewarded. Learning from each other approach is followed for sharing best practices of the participating steel producers through periodic meetings as well as various workshops / seminars, plant visits etc. Sharing of information among members is also facilitated through the JCSSI website - www.jcssi.com. Some of the activities of JCSSI are: Scrutinizing key issues related to Safety, Occupational Health & Environment. Spreading awareness among the Committee members by sharing of best practices through meetings, workshops, seminars, plant visits etc. Organizing competitions amongst employees of member organizations for supporting and encouraging participation in Safety, Health & Environment. 95 Organising annual award function for recognizing members for their outstanding efforts as per approved Ispat Suraksha Puraskar scheme. Analysis of causes of incidents/ accidents and sharing views on corrective measures. Printing and publishing information material like safety posters & calendars for distribution amongst member organizations for awareness generation. i) Liaison with CO, MoS, Parliament cell, NSC, WSA etc.: SAIL is a Member of Occupational Safety & Health Committee of World Steel Association (WSA). Sharing of accident data in Annual Safety Survey of WSA is done by SSO which is published in Annual Safety & Health survey report. SAIL, SSO is having an MOU with National Safety Council (NSC) of India in the areas of safety audit & training. SAIL is a Member of Indian Steel Association (ISA) and periodic meetings of Health & Safety Committee are attended by ED, SSO. Draft replies to safety related Parliament / MOS / CO queries are prepared & submitted on time. j) Spreading awareness through publications, competitions etc.: SSO Information Portal contains various safety related information like Annual & Monthly Reports, Safety manuals, checklists, protocols, accident briefs year wise, training PPTs, videos, animations etc. The portal is regularly reviewed and updated. E-Scan, an in-house magazine containing various articles, case studies & other informative material is published by SSO on half-yearly basis and circulated. Annual Performance Plan (APP) on Safety & Fire Services activities of SSO & Plants/ Units are compiled & published by SSO every year in booklet / e-book form and circulated to all Plants. Good safety initiatives taken by the employees from all plants & mines are identified and suitably rewarded in HazAn.Com - Hazard Analysis Competition organised by SSO which gives the employees an opportunity to showcase their work and spread the learning points at organisation level. With a view to disseminate learning points from incidents / accidents, system of sharing Safety Alert Messages (SAM) amongst all Plants & Units has been started. Good Safety Practices (G-SaP) prevailing in SAIL plants & units as well as steel industry are captured by SSO and disseminated amongst Plants & Units for awareness and implementation. 96 National Safety Day, World Steel Safety Day etc. are celebrated by organizing various competitions for the employees of SAIL units at Ranchi & their wards, school children etc. to generate awareness. NEW INITIATIVES BY SSO 1. SUKRITI: An e-Book covering Good Safety Systems & Practices of the Steel Industry & important points of safety consultants compiled by SSO, was released by Director (T, P & RM), SAIL at MTI, Ranchi on 4th October 2023. This will facilitate all the Plants & Units in implementing the good practices. 2. SAMIKSHA: An e-Book comprising of Learning from the Past incidents department / area wise was compiled by SSO with a view to ensure effective implementation of recommendations to prevent recurrence. The book was released by Director (T, P & RM), SAIL on 22nd March, 2023 at MTI, Ranchi in presence of EDs & senior officers of Ranchi based SAIL units. Subsequently, SAMIKSHA covering incidents upto December, 2023 was updated. 3. SURAKSHA MANTHAN: A new initiative titled ‘Suraksha Manthan’ was launched to align the thinking & working of SSO with the Plants & Units. As a part of this, a meeting is organized on monthly basis under the leadership of ED, SSO with participation of Heads of Safety of all Plant & Units. The pertinent issues including major accidents (if any) are discussed, good practices are shared and action plans are chalked out with a view to achieve the target of ‘Zero fatality’. 4. SAMPARK: A new safety interaction module was conceived for better communication and implementation for achieving zero fatality. As a part of this, detailed interactions are held with HODs, Line Managers & Senior Management in the plants/ units. 5. SPARSH: A short & customized safety module titled “Sparsh” introduced by SSO in the beginning of all Training Programmes at MTI, Ranchi with a view to sensitize & orient the employees to achieve the target of “Zero Fatality” in SAIL. 97 6. Safety Operating Committee (SOC) Safety Operating Committee (SOC) was formed for the first time and first meeting on the theme ‘Safety during Steel Making’ was organized during 12th-13th Oct ‘23 at DSP. The meeting was attended by 73 participants from 19 organisations like Directorate of Factories (WB), Major Technology Provider (Prime Metal, SMS Group), TATA Steel, JSW - Dolvi & Vijayanagar, AM/NS, Hospet Steel, NMDC, MECON etc. HUMAN RESOURCES At SSO, personnel are broadly categorized as non-executives and executives. There are 3 non-executives and 15 executives as on 1st January, 2024. It is ensured that employees engaged in performing various tasks are competent on the basis of appropriate education, training, skills and experience. The break-up of manpower in various grades is as follows: Grade(s) E-9 E-8 E-7 E-6 E-5 E-3 S-11 S-9 Nos. 01 01 04 02 05 02 02 01 The executives (E-7 & below) have been assigned one or more of the desk covering all Plants & units of SAIL. They coordinate and monitor with their respective desk on dayto-day basis and maintain two-way communication for retrieval / sharing of important information related with safety & fire services activities. Non-executive employees assist the executives in discharging their responsibilities and also perform any other tasks as assigned from time to time. --- 98