Steel Plant Services & Roles
Document Details
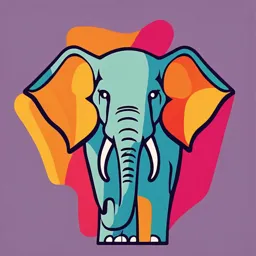
Uploaded by PraisingCerium
Tags
Summary
This document details the major services in steel plants, covering foundries, repair shops, and various fabrication methods. It discusses different metalworking processes and equipment used in steel plants, including welding methods and forging.
Full Transcript
Chapter - 10 Major Services in Steel Plants and their Role 10.1 Foundry It is an establishment where metal objects are produced by melting metal and pouring it into moulds. Like many other production processes, e.g. forging, stamping, pressing, rolling, machining, etc. casting also is a fundamental...
Chapter - 10 Major Services in Steel Plants and their Role 10.1 Foundry It is an establishment where metal objects are produced by melting metal and pouring it into moulds. Like many other production processes, e.g. forging, stamping, pressing, rolling, machining, etc. casting also is a fundamental metal forming method which is used in industries. Foundry products which are known as castings do find a wide variety of application in any integrated steel plant and that is why every integrated steel plant of our country (like Tata Steel, ISP, RSP, BSP, BSL and DSP) is having a captive foundry of its own. Some of the products of steel plant foundries: Ingots moulds, bottom plate, bottom stool (or half bottom plate), Pig mould for Pig Casting machine, Break blocks for locomotives, Trumpet, Guides for Merchant Mill, Hammers, Charging box end, full charging box, charging bar, slipper pads, bushes (of different sizes and types) for Bearing, Chilled, Aluminum shots, Axle bush draw bar link, Cover carriage, Splasher Plate etc. 10.2 Repair Shops All SAIL Plants have been provided with centralized workshop to facilitate repairs and reconditioning of components, sub-assemblies and to meet a sizable volume of their spare requirements. The repair shop of SAIL Plants broadly carries out two types of activities viz. i. Production of spares and consumable items required by the plants. ii. Repair and reconditioning of different component parts, sub-assemblies and assemblies. The efficient operation of an Integrated Steel Plant to a great extent depends upon the proper upkeep of installed equipments, which calls for elaborate maintenance systems and facilities. Carrying out scientific maintenance of equipments requires the right spares of the right quality and in the right quantity in the right time. Their nonavailability can result in the postponement of shut downs and preventive maintenance and the sections have to be fully equipped with spares, sub-assemblies and assemblies. The latest concept of the modular replacement of assemblies and subassemblies which minimize downtime and ensure better quality of repairs, places still higher demand on captive engineering shops. Repair shops of steel plant are basically engineering workshops for forging, machining, heat treatment and fitting and dismantling. Usually each repair shops consists of Forge shops, Fabrication shops, Machine shops, Tool Room, Fitting and Dismantling shops. 78 Welding / Fabrication Shop : Welding is a materials joining process used in making welds. This is a highly versatile process used for day to day and regular repair of plant equipments. The main Welding processes are : a) Oxyfuel Gas welding – Use the heat produced by a gas flame for melting the base metal and if used, the filler metal. Pressure may or may not be applied. b) Arc Welding – A fusion welding process wherein union of work piece is produced by melting the surfaces to be joined with the heat energy obtained from an A.C. or D.C source. c) Resistance Welding – A group welding process, which produces union of metals with heat obtained from resistance offered by the work to the flow of electrical current through the parts being joined. Fabrication Shop Welding, forming and fitting are the three basic processes used mainly for fabrication of metal structures / equipments. This is very important for repair /manufacture of steel plant equipments and structures. Fabrication Shop is generally equipped with Profile cutting machines, Plate Bending machines, Shears, Welding machines of different types, Hydraulic presses, facilities for heating & Material handling etc. Forge Shop Forging is a process of shaping metal by application of force and heat or by application force alone. Forging is the shaping of metal either by i) impact or ii) steady compression between a hammer or ram and an anvil.Forging hammers are to make stock / blanks for various spares. Forging is a process of plastic deformation of metal. In case of forging, the plastic deformation of metal is achieved by applying force of sufficiently high magnitude so that the stress developed within the work material is greater than the yield stress when “permanent set” takes place within the work material. However, in most of the cases, the work material is heated and with little force the plastic deformation in work material is achieved. Therefore in forge shops the following equipments are installed: forging hammer and press. Fabrication at structural shop: Fabrication means joining together. In fabrication shops the usual, work materials are plates, sheets, angles, channels, joists and other structural materials. In fabrication shops these materials are first “marked” and are then cut to size as per markings by either gas cutting or shearing or punching or by any other operation. Properly sized materials are then given shape by bending or pressing or by any other methods. After cutting, marking, and shaping, the structural are fabricated by riveting or by welding. The usual fabrication shop equipment are E.O.T crane, JIB crane, Gas cutting torches, Profile (gas) cutting machines, shearing machine, drilling machine, plastic bending 79 rolls, bending machine, hydraulic press, gas welding sets, electric arc welding machines, submerged arc welding machines, metal arc welding machine (MAG) etc. Welding at Fabrication Shop: Welding is a materials joining process used in making welds. This is a highly versatile process used for day to day and regular repair of plant equipments. The main Welding processes are : a) Oxyfuel Gas welding – Use the heat produced by a gas flame for melting the base metal and if used, the filler metal. Pressure may or may not be applied. b) Arc Welding – A fusion welding process wherein union of work piece is produced by melting the surfaces to be joined with the heat energy obtained from an A.C. or D.C source. c) Resistance Welding – A group welding process, which produces union of metals with heat obtained from resistance offered by the work to the flow of electrical current through the parts being joined. Machine Shop Machining operation in general means removal of extra material in the form of “chips” from the work body with the help of a machine tool. Different conventional machining operations depending upon the method of removal of material, the relative motion between the work and the cutting tool, etc. the various machining operation are given different names e.g. turning, boring, facing, knurling, milling shaping, slotting, hobbing, drilling, reaming, grinding etc. To carry out these conventional machining operations, machine shops of SAIL units are equipped with all types of conventional, general types of machine tools. Machining is an important method of shaping metal parts and especially of finishing them to close dimensions. Machine Shop consists of light and heavy Machining Sections equipped with lathes, planers, Horizontal and Vertical Boring machines, Gear cutting machines, Slotting machines and Grinders for manufacturing and repair of equipment spares like Shafts, Liners, Gears, rolls etc. Balancing machine determines the unbalance of rotating parts. Balancing mass is added/ removed to balance these parts, which is essential to maintain rotating equipments against unbalance and breakdown. Electrical Repair Shop Electrical Repair Shop (ERS) is a critical repair shop of Electric Motors. Apart from motors, Load Lifting Magnets, Welding Machines, Brake Coils, Reactors, Slip ring are also repaired/manufactured in Shop. Main activities of ERS are overhauling all (medium repair) of motors, which includes dismantling, clearing, change of broken damage, parts varnishing and testing. For burnt motors (Stator and Rotor) winding are replaced/repaired and tested after necessary repair and overhauling. 80 10.3 Gas Utilities & Water Management Gas Utilities consists of following sections: (a) Oxygen Plant Oxygen Plants (both Captive & Outsourced) produces Oxygen, Nitrogen and Argon for steel making. These products are produced in both gases form and liquid form. Purity of Liquid Oxygen & Gaseous Oxygen maintained is above 99.55%, Liquid Nitrogen & Gaseous Nitrogen below 10 ppm impurity and Liquid Argon below 2 ppm impurity. Oxygen, Nitrogen and Argon gases are separated from air using Cryogenic Distillation Process in Air Separation Units (ASUs). Dust free air is compressed in Air Compressors followed by pre-cooling of the compressed air. Moisture and other hydrocarbon are removed in absorber bed. Selective distillation of various components of dry air is done at their respective boiling temperatures in ASUs. Cooling required for separation is produced in expansion Turbine and Heat exchanger. High Pressure Oxygen, Nitrogen and Argon is produced using IC pumps and by using Nitrogen Compressor. High pressure Gaseous Oxygen, Nitrogen is directly sent to customers in gaseous pipeline grid. Liquid Oxygen, Nitrogen and Argon are stored in cryogenic storage vessel. Buffer vessels of oxygen, nitrogen and argon are provided to take care of fluctuating demands of consumers. Use of Oxygen, Nitrogen and Argon Oxygen is primary used in increasing oxygen enrichment in Blast Furnace and for production of Steel. In Blast Furnace, Oxygen enrichments helps in reducing coking coal, increasing PCI (pulverised coal injection), optimizing furnace chemistry and furnace temperature, thus oxygen helps in production of molten iron known as hot metal. Steel is produced in Basic Oxygen Furnace (BOF), High pressure Oxygen is blown in BOF which contain Hot metal, this process reduces carbon percentage in hot metal, and thus Steel is produced. Liquid Oxygen is also supplied for medical purpose across country in mobile cryogenic tankers. Nitrogen being an inert gas is required in various departments Plants. It is used for maintaining inert atmosphere during PCI grinding in Blast Furnaces, purging operation for controlling explosive mixtures in pipelines and furnaces, Pneumatic gas for valve operation. Nitrogen is also used as seal gas for various equipments and slag splashing in BOFs in SMS department. Argon being chemically inert gas is used in production of special steel. Inert atmosphere is maintained in RHOB using argon gas. It is also used for bottom purging in convertors of SMS-II (b) Acetylene Plant Acetylene gas is produced from calcium carbide and filled in the cylinders. Filled cylinders are supplied to consumers through Stores all over the Plant. The main 81 consumers of Acetylene Plant are Continuous Casting Shop where acetylene is used for cutting slab through cutting torches. (c) Protective Gas Plant (PGP) It is used for providing inert atmosphere in Annealing and Galvanizing furnaces of CRM. Protective Gas is a physical mixture of 95% of pure nitrogen and 5% hydrogen. Water Management Water Management involves total supply and disposal of water system in the plant. Different systems are as follows: 1. Procurement & storage of raw water. 2. Industrial/Technical clean water system: Used for cooling of various technological equipments/application/products. 3. Industrial/Technical contaminated water system: Used for cleaning and cooling of various technological processes like Gas Cleaning Plants, Scale flushing, dedusting units etc. 4. Drinking water system: Water is treated at water treatment plants and distributed in plant and township. 5. Soft Water and DM (De-Mineralized) water system: Water is chemically treated and distributed to consumers, such as boilers, furnace cooling etc. 6. Domestic sewage water: Collection, treatment and disposal of domestic waste water. 7. Storm water: Collection and disposal of rain water. 8. Industrial waste water: Collection, treatment and disposal of various industrial waste water. For handling of different types of water, it has numerous pump houses containing sump pit, pumps and motors, valves and pipelines, settling tanks, cooling towers and pipeline network throughout the plant and township. Disposal of storm water during heavy rains is a major responsibility of Water Management Deptt. to prevent flooding of underground tunnels and cellars. 10.4 Research and Control Laboratory (RCL) Research and control laboratory plays a vital role in maintaining and improving the quality of products. The essential function of a research and control laboratory is to impose necessary control measures on (i) the metallurgical and other processes employed and (ii) the material used to ensure economic production of quality materials. RCL has five wings: 1) Metallurgical Testing 2) Chemical Testing 3) Mechanical Testing 82 4) Inspection 5) Research & Development All these wings of research and development laboratory work in conjunction within themselves as well with production units as a team of helping observance of technological discipline and ensuring excellence of quality. Metallurgical mainly covers all the process control laboratories attached to different production shops like coke ovens, blast furnace, steel melting shops, rolling mills, foundry etc. Process control laboratories exercises control on quality of the inputs and production parameters such as yield, off- grade production, working practices, heat regimes, temperature control, mechanical properties, chemical compositions, requisite micro-structure etc. Some of the sophisticated equipments/instruments used for these controls are: Thermo-vision camera, digital pyrometers, ultrasonic flaw detectors, quanto-vac slag analysers, nucleonic guage variation detector and adjuster (to control guage variation of hot rolled coils in BSL), Optical Emission & Xray, Plastometer (for plastic properties of coal), RI-RDI (for hot properties of sinter), ONH Analyser (for analyzing content of Oxygen, Hydrogen & Nitrogen in steel samples) Test pieces from each production units are taken to the laboratory for testing and ensuring that the products confirm to the standards of different specification before dispatched to the valued customers. The R & C laboratory also investigates failed spare parts for causes of failure, so that the shops are properly guided to procure spares of desired quality. Chemical sections collect samples from incoming raw materials as well as from the intermediate products for analysis of chemical composition and size fraction. There are laboratories attached to different production units for quick sampling, analysis and control. They help in controlling quality of inputs from one stage to another in the long process of metamorphosis from iron ore to steel. It is finally the inspection wing, which sorts out the good from the bad. Tested quality, off grade, commercial grade, defectives, rejects etc. are carefully classified with an eye on the cost of different categories so that the customer gets what he wants and the company is not put to loss. Off grade and diversions are minimized by proper fitment into grades, to help earn more. Finally, proper embossing and packaging of the products is equally important so that the products reach its destination in a sound condition. This is also inspected before dispatch. Inspection group also observes scarfing operation of different intermediate products like slabs, blooms etc. to avoid defects in the final product. NABL accreditation has been obtained in the field of chemical and mechanical testing for steel products by DSP & BSP. The laboratories of other SAIL Plants such as RSP & ISP are in process. 83 10.5 Refractory Engineering Refractory Engineering Department (RED) Refractories are vital for steel industry. The performance of refractories considerably influences the production, productivity and economics of the plant. The successful performance of refractories is primarily governed by its quality. Refractories play a very vital role in the achievement of target for steel production. With changing pattern of steel making there is an ever-increasing demand for newer types and better quality of refractories. Technological improvements in steel plants and in refractory production have gone hand in hand. The steel industry is the largest consumer of the refractories. 60-70 % of the refractory produced, is being used by steel makers. The function of the Refractory Engineering Department is to look after the refractories maintenance of all the Units lined with refractory and acid resistance materials in the plant. Capital repair of these units are also planned and executed by this department. Refractory Material Plant (RMP) This department handles lime stone. Raw lime stone is crushed and fed into the kilns (Rotary/Vertical shaft) and is burnt under high temperature to produce lime which is used as a flux in Steel Melting. Lots of dust produced here for which electrostatic precipitators are installed to prevent pollution and environmental control. 10.6 Capital Repair Group The function of this group is: i) To plan and supervise capital repair of all the major shops. ii) To execute routine repair of all the major shops. The main objective of this department is to facilitate adequate availability of vessels and furnaces for optimum production and to reduce the cost of steel production by bringing down the consumption of spares & refractories. --- 84