Moving Toward the Circular Economy: The Role of Stocks in the Chinese Steel Cycle PDF
Document Details
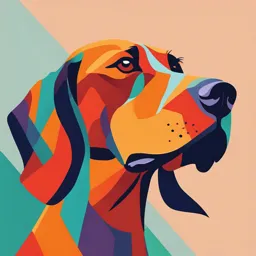
Uploaded by IdealFermat
Universidade Federal de Pernambuco, Universidade Federal do Rio de Janeiro
Stefan Pauliuk, Tao Wang, Daniel B. Müller
Tags
Related
- Structural Steel and the Circular Economy (Steel for Life PDF)
- Role of Manufacturing Towards Achieving Circular Economy: The Steel Case PDF
- Steel In The Circular Economy PDF
- Circular Steel: How Information and Actor Incentives Impact the Recyclability of Scrap PDF
- Steel in the Circular Economy PDF
- Steel Circular Economy in Civil Construction PDF
Summary
This research article investigates the role of stocks in the Chinese steel cycle and its transition to a circular economy. The study utilizes dynamic material flow analysis (MFA) in the steel sector, considering historical trends and potential future scenarios up until 2100. It forecasts a possible peak in consumption of steel between 2015 and 2020, followed by a decline.
Full Transcript
This is the original submission that lead to the journal article Moving Toward the Circular Economy: The Role of Stocks in the Chinese Steel Cycle by Stefan Pauliuk, Tao Wan...
This is the original submission that lead to the journal article Moving Toward the Circular Economy: The Role of Stocks in the Chinese Steel Cycle by Stefan Pauliuk, Tao Wang, and Daniel B. Müller published in Environmental Science and Technology. The published version of the article including its correct citation can be found under http://dx.doi.org/10.1021/es201904c 1 For initial submission to Environmental Science and Technology Moving Towards the Circular Economy: The Role of Stocks in the Chinese Steel Cycle Stefan Pauliuk1, Tao Wang,1,2,Daniel B. Müller*,1 1) Department of Hydraulic and Environmental Engineering, Norwegian University of Science and Technology, NO-7491 Trondheim 2) Research Center for Material Cycles and Waste Management, National Institute for Environmental Studies, 16-2 Onogawa, Tsukuba, Ibaraki 305-8506, Japan * To whom correspondence should be addressed: [email protected]; telephone: +47- 735-94754; RECEIVED DATE: ABSTRACT: As the world’s largest CO2 emitter and steel producer, China seems to be far from reaching the goal of a Circular Economy which comprises a reconciliation of economic development with environmental concerns and potential resource scarcities. This work examines corresponding transition pathways in the Chinese steel sector using a dynamic material flow analysis for the time until 2100 that highlights the role of stocks for moving towards a Circular Economy. If the per-capita steel stock saturates at 8-12 tons, as historic in- use stock patterns in industrialized countries suggest, consumption can be expected to peak between 2015 and 2020, whereupon it is likely to drop by up to 40% during the years until 2050. A slower stock growth could mitigate the peak and lower potential overcapacity in 2 primary production. Old scrap supply will increase substantially and it could replace up to 80% of iron ore as resource for steel making by 2050. This would however require advanced recycling technologies as manufacturers of machinery and transportation equipment would have to shift to secondary steel as well as new capacities in secondary production which could redundantize already existing integrated steel plants. KEYWORDS Material Flow Analysis; Steel; Recycling; China; Circular Economy; 1) Introduction Iron, mostly in form of steel, is a material that has been used by mankind for several millennia; the fair mechanical and chemical properties together with its relatively low economic costs allow iron and steel to be applied to a variety of uses requiring tensile and compressive strength, ductility, or ferromagnetism. In terms of mass, steel is by far the most important man-made metal with a recent yearly production of about 1.3 billion metric tons.1 On a global scale, steel production accounts for 25% of all industrial carbon emissions and 9% of process- and energy-related carbon emissions.2 As long as severe technological changes (e.g., improved reduction processes combined with CCS, electrolytic processes, etc.)3 are not in place, recycling and reuse of scrap steel are considered the only feasible route to substantially decrease the carbon footprint of the steel industry.4 Today, China is by far the biggest producer and consumer of steel.1 The Chinese government has been aware of the importance of the domestic steel industry and made its development a national priority since the 1950s.5 However, only in the recent three decades a 3 stable and strong production growth could be achieved. After a lasting boom in capacity extension,6 China now takes first measures to limit further capacity extension in primary steel production.7-8 Decisions on future investments in production facilities should be based on robust estimates on steel demand and need to take into account future scrap flows as secondary resource. A shift from primary to secondary production is a longsome and costly undertaking due to the inertness of both production facilities and in use stocks: Assets in primary steelmaking such as blast furnaces and basic oxygen furnaces represent large capital stocks and are characterized by pay-back times of at least 30 years9 and the lifetime of buildings and infrastructure as the major steel user is often considerably longer.10-11 Anticipating long-term trends in the anthropogenic iron and steel cycle is hence of great importance for industrial investments, security of employment, mineral resource development, GHG emissions mitigation as well as geo-political strategies. At present, forecasts on future steel production are in general based on extrapolations of historic production flows and growth rates.12-13 Another common approach is to correlate the flows of steel consumption to external GDP projections e.g. in the World Energy Model14 or in a publication by Das and Kandpal.15 The steel module of the POLES model16 is a another example: It assumes that the intensity of steel use per unit GDP follows an inverse U-shape curve mimicking the economic development from agricultural to industrial and eventually a service-oriented economy.17 However, the level of future GDP is very sensitive to the assumed growth rates and thus forecasting steel consumption based on these estimates is inherently uncertain. Moreover this model makes investments decisions between primary or secondary production on a purely economic basis as the future physical availability of steel scrap is taken for granted. This approach disregards mass balance consistency and is thus not suitable to anticipate potential constraints of secondary resources that may significantly hinder the transition to a more sustainable steel cycle, especially in economies with a developing steel stock. 4 We suggest an alternative perspective by regarding the aggregated demand for steel stocks in constructions and all other metal-bearing products as a driving force of the steel cycle. A stock-driven MFA model that contains both population and lifestyle parameters has been applied previously to forecast material flows in the housing stock in the Netherlands.18 A similar study investigated the steel stocks and flows in China’s residential building stock.19 Historic patterns of stock development were also employed to forecast the future global in- use stock.20 All these approaches focus on the use phase of steel; however, a comprehensive discussion of the impact of in-use stocks on the whole metal cycle is still lacking. This is important because in-use stock patterns shape the conditions for primary and secondary production, which in turn is relevant for estimating potential carbon emission abatement and exploitation of primary resources. Historic iron flows and stocks in China from 1900 to 2009 have been analyzed by Wang et al.21 Their findings, combined with historic patterns of stock development observed in industrialized countries,22 are used as basis to perform a stock-driven quantification of the future Chinese steel cycle and to explore the development of material demand and supply in China throughout the 21st century. We extend existing models to cover the whole anthropogenic iron cycle in China, and distinguish between primary and secondary steel production in particular. In addition to future production and scrap flows, the results also provide insight into material losses to landfills and dependency on domestic and overseas ore extraction. 5 2) Methodology Throughout the text, the term ‘steel’ includes cast iron and all other iron alloys. System definition: The system of the anthropogenic iron cycle in China is presented in Figure 1. Domestic processes and industries are linked by markets for the respective goods, obsolete products, and scrap. Primary production takes place in blast furnaces (11) and basic oxygen furnaces (8). Mini-mills with electric arc furnaces are mainly fed by scrap (7). Subsequent manufacturing industries are supplied by steel mills and foundries (5). We distinguish five different use categories for steel products: ‘Construction’ (1.1), ‘Transportation’ (1.2), ‘Machinery’ (1.3), ‘Appliances’ (1.4), and ‘Other’ (1.5). For each of these five sectors, specific rates of new scrap generation in manufacturing (3), lifetime distributions in the use phase (1), and recycling efficiencies in the waste management (17) can be assigned. The use phase (1) plays a central role by establishing a causal relation between the five consumption inflows X2_1,i and future outflows of obsolete products X1_16,i via a product lifetime distribution L. Different lifetimes for the different categories of use (1.1-1.5) apply. X= 1 _ 16, i (t ) ∑X t'≤ t 2 _ 1, i (t ') ⋅ L(t − t ',τ i , σ i ) (1) Two different ways of quantification are performed to determine the historic stocks and future flows: a) Quantification of the historic cycle (1900-2009),’forward calculation’, cf. upper part of Fig. 1: Historic statistical data are compiled in order to determine the apparent final consumption of iron by sector i (X2_1,i) as the mass balance of the market for final products.21 Equation (1) returns X1_16,i and the accumulation of in-use stock is determined by mass balance of the use 6 phase. By comparing the computed supply of old scrap with data on total scrap consumption we can justify our assumptions on historic lifetimes and efficiency of waste management. b) Stock driven mode (2010-2100),’backward calculation’, cf. lower part of Fig. 1: Future demand for the total in-use stock S(t) is derived by combining future population P(t) with assumptions on future lifestyle expressed in terms of per capita stock of iron by category of use ci(t): S (t ) = P(t ) ⋅ c(t ) = ∑ S (t ) = i i P(t ) ⋅ ∑ ci (t ) i (2) For each model year from 2010 on, we first compute the outflow X1_16,i by equation (1) and then adjust the consumption X2_1,i so that the given stock demand is met (mass balance). With given transfer coefficients and the mass balance we successively quantify upstream and downstream industries. We make scenario-specific assumptions on the future share of EAFs, the shares of scrap use in different steel-making technologies, and the annual amount of extracted domestic ore. Finally, net scrap export and net ore import are determined from balancing domestic demand and supply. The transition from historic development to future trend (2008-2009): While per-capita in-use stock is the final result of the historic quantification until 2009; from 2010 on, it becomes the driver of the cycle. The transition is assumed to be continuous. Furthermore, the model stock is chosen to be tangent to the historic stock at the transition point (2009): The recent boom in China has led to a huge increase in newly-built production capacity, which is strongly related to the stock growth rate. In 2008-2009, this rate has been larger than ever. Nonetheless, there have been regulations in place to phase out outdated steelmaking capacities and to limit overinvestment,23 we therefore assume that the trend will not become much bigger in the next years. 7 Parameter estimation and scenario analysis: To quantify the historic cycle, statistical data on production and trade of iron ore, pig iron, castings, and finished steel as well as trade data on final products and scrap have been compiled.21 Information on the share of EAFs and the rate of new scrap generation in manufacturing are included as well. We chose a log-normal lifetime distribution for all items in the use phase where the mean lifetime τ equals the standard deviation σ. This distribution has a long tail compared to the normal distribution in Hu et al.19 and demolishing within a certain cohort happens over a longer period of time. This reflects the slackness of the residential building stock better than a normal distribution. Based on previous studies,22 we chose the following mean lifetimes: Transportation: 25 years, Machinery: 30 years, Appliances: 15 years, and Others: 15 years. For the construction sector we calibrated the lifetime of historic cohorts that contribute to present scrap flows to be at least 65 years. We use this value as representative for all cohorts until 2009. The lifetime of cohorts in construction from 2010 on is scenario-dependent. We propose a set of 6 simple scenarios to depict future development. An overview on the major parameters is included in Figure 2. To quantify the level of steel use we make the central assumption that the future per capita in use stock of iron in China will follow a similar trajectory as it has occurred in industrialized countries. This approach is in line with the ambitious goals for industrialization set by the Chinese government.24 From previous work22 we indentify two different patterns of in-use-stocks of steel: a) a saturation after a certain time at a level of (10±2) ton/cap as seen in the US, the UK, and France and b) a continued linear growth in time as seen in Japan, Australia, and Canada with stock levels of (12±2) ton/cap in the year 2005. We define the BASIC scenario as reference cycle as it assumes saturation at an average level of about 10 t/cap, which is also the pattern that has been observed in the US. The mean 8 lifetime of future cohorts in construction is set to 50 years which reflects the more rapid turnover within the construction sector in Asian countries compared to European countries or parts of the US.11 The speed of growth is determined by the current production capacity as pointed out above. We investigate the effect of a changing use pattern by varying the two most important use phase parameters each at a time (cf. Fig. 2). The in-use stock pattern is changed by varying both the stock level (8 t/cap for Stock8 and 12 t/cap for Stock12) for saturation scenarios as well as by choosing a different pattern (sustained linear growth in construction to 10 t/cap by 2100 for LinearStock10). The lifetime of post-2009 cohorts in construction and infrastructure is changed as well (35 years in Lifetime35 and 75 years in Lifetime75). For all scenarios we consider that actors will be aware of resource constraints and realize the necessity to curb energy demand and emissions: As an increase in old scrap supply is expected, all alternatives include an increase of the share of external scrap in Basic Oxygen Furnaces to 20% by 2035 as this is a potential that can be seized easily. Although end-of-life products may hibernate in obsolete stocks and waste management may be inefficient, it is assumed that from 2010 on, 90% of all end-of-life steel will be available on the scrap market. This ambitious figure shall identify the potential impact of secondary production. Each scenario is run twice: Initially, the share of EAFs remains at its present value of 9% until 2100 and later, it is adjusted in a way that all domestic new and old scrap can be processed within the country (NSE or ‘no scrap export’ version). The latter option corresponds to the notion of a ‘circular economy’. All six scenarios assume trade flows to be zero except iron ore and scrap trade. 3) Results Between 2015 and 2020, steel consumption reaches a pronounced peak independent of the scenario while the stock curve attains its maximum growth and inflection point (Fig. 2). After 2020, consumption exhibits a moderate to sharp decline which is a direct consequence of the 9 stock patterns we apply: after passing the inflection point of the saturation curve at 4-6 ton/cap, growth starts to slow down. In 2010, the in-use stock of steel was about 4 Gt, that is roughly the size of the US in-use stock.25 By around 2045 in-use stock will more than triple and reach a maximum of 14 Gt (Basic), ranging from 12 Gt (Stock8) to 17 Gt (Stock12). Due to shrinking population it will eventually decline to a level between 14 Gt (Stock12) and 9 Gt (Stock8) by 2100. For LinearStock10 the stock will remain rather constant at 12 Gt after 2040. For the Basic scenario, consumption peaks at ca. 600 Mt/year around 2020. Thereafter, domestic demand will drop continuously: Between 2020 until about 2050 demand is dropping due to beginning stock saturation. During the second half of the century, shrinking population in combination with accomplished saturation causes further decline. At the end of the century, it will settle down at ca. 60 % of the peak value. The magnitude of the peak is not sensitive to construction lifetime because the expected scrap and reconstruction boom arrives too late to fill in the gap. It is also relatively robust towards a change in saturation level as for a ±25% variation (Stock8 and Stock12) the magnitude of the peak only changes by about ±100 Mt/year or ±15%. For all scenarios the consumption peak will occur before 2020. In LinearStock10 the peak is less distinct however, as per capita stock grows steadily and demand for input is postponed to later decades. Supply of iron in obsolete products follows the consumption boom with a delay of 20-30 years and will rise considerably: It will exceed 50% of domestic steel production in the period of 2025 to 2035, and around 2050, it will even surpass domestic consumption provided that obsolete products do not accumulate with their former users. Contrary to the peak level, the time when scrap flows will rise sharply is slightly sensitive to construction lifetime (resulting in a shift of ca. ±5 years) and only little sensitive to the stock pattern. Increasing scrap availability opens up options for more secondary production. Today, EAF steel is predominantly used for constructions. As scrap flow increases further, domestic use 10 of this scrap would imply that eventually, secondary steel will have to penetrate other sectors. We propose to rank the five sectors in the order Construction, Machinery, Transportation, Appliances, and Other, according to the sophistication of steel applications within them. We break down the final demand for steel products on the five use categories and compare it to old scrap supply and iron ore consumption (Fig. 3). We can see that the drop in total consumption is mainly caused by a maturing steel stock in the construction sector which leads to a sharp demand decline after ca 2015. For Lifetime75, the drop in new constructions even will be about 80% due to the long lifetime of buildings and infrastructure erected during the boom. This collapse of demand will be partly compensated for by growth in the other four sectors, mainly transportation and machinery. If the present technology mix is maintained, the total amount of scrap consumed (Fig. 3, black solid line) will never exceed demand from construction. In other words under all examined conditions, the stock in buildings and infrastructure will be able to assimilate the flow of recycled steel from old scrap. However, the potential for recycling will be much higher: The black dashed line indicates the amount of old scrap that will be available if the scrap market was closed (No-Scrap-Export-variants of the scenarios). Around 2025, old scrap supply will reach 200 million tons/yr and quantity of secondary material will not be an issue anymore. However, if the extent of recycling shall be adopted to the available scrap flow, maintaining the overall quality of steel will become a challenge: Between 2025 and 2035, old scrap supply will exceed total demand from construction sector (black squares in Fig. 3) and firstly, machinery producers will need to settle for recycled steel. Further expansion of recycling requires that at latest between 2030 and 2040, recycled old scrap will have to start to replace primary steel in transportation equipment (black circles in Fig. 3) and ultimately in appliances. Figure 4 shows a comparison of major iron flows and stocks across the six scenarios both with open and closed scrap market. It allows to identify the changes proposed in the scenario definition will have the biggest effect. In-use stock (B) and final use (3) show a similar 11 pattern for all scenarios, as utilization of steel in most industrialized countries lies in the rather narrow range between 8 and 12 t/cap. Accordingly, all flows of old scrap supply (5) follow the same pattern and only quantitative changes of ±70 Mt/yr are identified. Qualitative changes only occur if the structure of the steel system is shifted from a linear supply chain to a circular, material-preserving cycle. Then mass balance allows to almost phase out primary production as consumption of pig iron (2) would be below 50 Mt/yr for all NSE variants. Consequently the import of iron ore (1) and its accumulated counterpart (A) could be reduced substantially, leading to a lower dependency on foreign resources and to a large potential for lowering greenhouse gas emissions. Plot (1) shows that there would even be some export of Chinese ore in a circular economy. This is due to the assumption that domestic mining follows a given exponential curve. 4) Conclusions In the course of industrialization, the Chinese steel system is expected to shift from a linear chain focusing on quantitative expansion to a relatively stable in-use stock with a recycling- based circular steel economy being possible in terms of quantity. Our scenarios identify three major challenges resulting from this development that are expected to emerge already within the next 20 years: Consumption peak: The present steel production capacity allows the in-use stock to grow at a very high rate of 250-300 kg/cap*yr, a speed at which the level of the saturation level of the US per capita stock would be reached around 2030. As stock growth will slow down in the saturation scenarios, steel demand will peak already between 2015 and 2020, whereupon it will start to decline heavily. In principle consumption could remain on a high level by shifting to replacement of products, buildings, and infrastructure. However, lifetime of 12 constructions (35-75 years), which account for 50 % of all steel stocks, is so long that a) the expected scrap boom from reconstructing buildings and infrastructure will arrive too late to step in and b) the production volume needed for replacement is considerably lower than the consumption peak. The peak can be mitigated most effectively by slower, but more sustained growth in the construction sector alone. Still the same level of service (expressed in terms of steel stock) would be reached by the end of the century. A slower growth of steel stocks can be facilitated both on the production side by immediately curbing capacity extension and on the consumption side by slowing down urban expansion and re-building. Scrap boom: In all scenarios China will experience a sharp rise of scrap flows between 2025 and 2050 as consequence of the present period of heavy consumption. This major change of the steel cycle will mostly be accomplished before 2050, and for the second half of the 21st century, we expect a largely stable situation with consumption being at about the same level as today, but significantly lower than the all-time high. First of all however, in-use stock will be built up mainly from primary steel during the first half of the 21st century, and the bulk of this flow will be supplied by the existing steel production capacity which predominantly was erected during the last decade. Even if scrap shares in the existing assets were increased to the technological limit, old scrap export would surpass 100 Mt/yr around 2025. Large-scale investment in EAFs would open a door to utilize domestic scrap within China (dashed lines in Fig.3). However given the typical lifetime of integrated steel plants of (30±6) years,9 we then foresee either idle integrated steel works or massive dumping of steel on the world market in the years before replacement of these plants will become cost-effective. Each new integrated steel plant is likely to exacerbate potential overcapacities and hence, discontinuing current expansion plans may help to make the transition to a mature steel cycle less abrupt. 13 Quality of recycled steel: In an industrialized society with a saturated steel stock and slightly shrinking population old scrap supply will be at about the same level as steel consumption and a circular economy with a closed steel cycle would be possible in terms of mass. However, quality requirements may impede displacement of secondary steel for primary steel for applications that require material of high quality and strength. In none of the calculations with closed scrap market demand from construction alone can absorb secondary steel produced from domestic old scrap. If a more or less closed steel cycle is the goal, manufacturers of machineries, transportation equipment, and appliances will have to adapt to secondary steel from ca. 2025 on. Today, secondary steel is often produced from a variety of alloys; and diluting contaminations with tramp elements and other residues is often suitable to meet quality requirements for structural steel. However, demand from constructions is likely to drop severely and hence there will be fewer options to dilute tramp elements. In a closed steel cycle waste management will play a central role in managing old scrap flows as secondary resource. In use stocks will have to be tracked to avoid formation of obsolete stocks and facilitate separation of scrap flows into different alloys to avoid spread of contaminations with tramp elements as copper or tin. Such a system would also facilitate preservation of valuable alloying elements such as nickel and chromium. Additionally, advanced refining technologies in secondary steel making may replace simple dilution of impurities. Reuse and re-rolling are concepts that avoid mixing different alloys and are therefore interesting not only for reducing the steel industry’s energy demand2 but also from a material purity aspect. A different perspective opens if the Chinese steel industry is analyzed as part of a larger system. Other countries, particularly India, which still have per capita stocks at a pre- industrial level21 are expected to catch up with economic development and are potential customers for both excess Chinese primary steel as well as secondary steel or post-consumer scrap to fulfill demand from constructions. Already today, the share of electric arc furnaces in 14 India’s steel industry is about 50%.1 Production in China could remain on a high level and the quality of secondary steel would be less critical while on the other hand, the country still would be dependent on imports of high-grade ore and would give away the opportunity to use old scrap as valuable secondary resource. 15 Supporting Information Available We provide the complete system definition, all model equations for 1900-2009, documentation of data sources and data treatment (1900-2009), model equations and parameters for the different scenarios through 2100, calibration of the historic cycle, and additional results. This material is freely available via http://pubs.acs.org. Acknowledgement The authors would like to thank Frank Zhong from the World Steel Association for helpful clarifications on reported statistical data. 16 REFERENCES (1) Worldsteel In Figures 2009; World Steel Association, Brussels, Belgium: 2009; (2) Allwood, J. M.; Cullen, J. M.; Milford, R. L., Options for Achieving a 50% Cut in Industrial Carbon Emissions by 2050. Environ. Sci. Technol. 2010, 44, (6), 1888-1894. (3) Meijer, K.; Denys, M.; Lasar, J.; Birat, J. P.; Still, G.; Overmaat, B., ULCOS: ultra- low CO2 steelmaking. Ironmaking & Steelmaking 2009, 36, (4), 249-251. (4) Birat, J. P.; Vizioz, J. P.; de Pressigny, Y. D.; Schneider, M.; Jeanneau, M., CO2 emissions and the steel industry's available responses to the greenhouse effect. Revue De Metallurgie-Cahiers D Informations Techniques 1999, 96, (10), 1203-1215. (5) Feng, L., China’s steel industry: its rapid expansion and influence on the international steel industry. Resour. Policy 1994, 20, (4), 219-234. (6) Wu, Y., The Chinese steel industry: recent developments and prospects. Resour. Policy 2000, 26, (3), 171-178. (7) Jie, R., Big plan to wipe out overcapacity. China Daily 2010-03-08, 2010. (8) Moody, A.; Lan, L., Overcapacity exacerbated by recession. China Daily 2010-04-12, 2010. (9) World Energy Outlook 2008; International Energy Agency, Paris, France: 2008; (10) 2008 Sustainability Report of the world steel industry; World Steel Association, Brussels, Belgium: 2008; (11) Service Lifetimes of Mineral End Uses; USGS Award nr. 06HQGR0174; Yale University: New Haven, 2007; (12) Ke Wang, C. W., Xuedu Lu, Jining Chen, Scenario analysis on CO2 emissions reduction potential in China’s iron and steel industry. Energ. Policy 2007, 35, 2320-2335. (13) Yellishetty, M.; Ranjith, P. G.; Tharumarajah, A., Iron ore and steel production trends and material flows in the world: is this really sustainable? Resour. Conserv. Recy. 2010, 54, (12), 1084-1094. (14) World Energy Model - Methodology and Assumptions; International Energy Agency, Paris, France: 2009; (15) Das, A.; Kandpal, T. C., Energy demand and associated CO2 emissions for the Indian steel industry. Energy 1998, 23, (12), 1043-1050. (16) Hidalgo, I.; Szabo, L.; Calleja, I.; Císcar, J.C; Russ, P.; Soria, A. Energy consumption and CO2 emissions from the world iron and steel industry; EUR 20686 EN, IPTS, 2003; (17) van Vuuren, D.P.; Strengers, B.J.; de Vries, H.J.M. Long-term perspectives on world metal use - a model-based approach; RIVM, Bilthoven, the Netherlands: 1999; (18) Müller, D. B., Stock dynamics for forecasting material flows - Case study for housing in The Netherlands. Ecol. Econ. 2006, 59, (1), 142-156. (19) Hu, M.; Pauliuk, S.; Wang, T.; Huppes, G.; van der Voet, E.; Müller, D. B., Iron and steel in Chinese residential buildings: A dynamic analysis. Resour. Conserv. Recy. 2010, 54, (9), 591-600. (20) Hatayama, H.; Daigo, I.; Matsuno, Y.; Adachi, Y., Outlook of the World Steel Cycle Based on the Stock and Flow Dynamics. Environ. Sci. Technol. 2010, 44, (16), 6457-6463. (21) Wang, T.; Müller, D. B.; Graedel, T. E., Iron capital formation in China and India: historic trends, outlook, and consequences. To be submitted to Environ. Sci. Technol, 2011. (22) Müller, D. B.; Wang, T.; Duval, B., Patterns of iron use in societal evolution. Environ. Sci. Technol. 2011, 45, (1), 182-188. (23) Two 10m-ton steel projects postponed to curb overcapacity: NDRC. China Daily 2009-10-20, 2009. (24) Hao, Z., China to realize full industrialization by 2021. China Daily 2007-08-10, 2007. (25) Müller, D. B.; Wang, T.; Duval, B.; Graedel, T. E., Exploring the engine of anthropogenic iron cycles. Proc. Natl. Acad. Sci. USA 2006, 103, (44), 16111-16116. 17 18 FIGURES AND CAPTIONS: Figure 0. TOC Art Figure 1. System definition. Iron cycle in the PR of China for historic quantification and stock driven mode. 19 Figure 2. Steel use by scenario. Total stock, per capita stock, total consumption (inflow), and discharge of iron in all types of products (outflow) from 1940-2009 and 2010-2100. The scenario specific parameter choices (pattern of total stock, pattern of stock in construction, lifetime of constructions) are shown as well. 20 Figure 3. Industry response for fixed share of electric arc furnaces. Steel consumption by sector of final use (red area plot), total production, iron (in ore) consumption, and supply of old scrap, 1940-2009 and 2010-2100. 21 Figure 4. Scenario comparison: Overview on major flows and stocks in a simplified steel cycle. Each scenario is run both with fixed EAF share and open scrap market as well as the EAF share following scrap supply for a closed scrap market (‘NSE’: No Scrap Export, dashed lines). 22