Raw Material Handling Plant (RMHP) PDF
Document Details
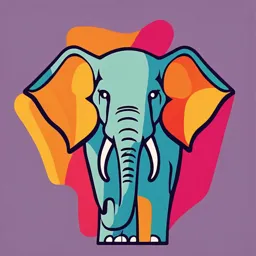
Uploaded by PraisingCerium
Tags
Summary
This document describes the raw material handling plant (RMHP) for steel production. It details different types of raw materials, their sources, and the objectives of the handling plant. It also discusses the functions and processes involved in the RMHP.
Full Transcript
Chapter – 1 RAW MATERIAL HANDLING PLANT 1.1 Introduction : Raw Material Handling Plant (RMHP) or Ore Handling Plant (OHP) or Ore Bedding and Blending Plant (OBBP) play a very important role in an Integrated Steel Plant. It is the starting point of an integrated steel plant, where all kinds of raw ma...
Chapter – 1 RAW MATERIAL HANDLING PLANT 1.1 Introduction : Raw Material Handling Plant (RMHP) or Ore Handling Plant (OHP) or Ore Bedding and Blending Plant (OBBP) play a very important role in an Integrated Steel Plant. It is the starting point of an integrated steel plant, where all kinds of raw materials ( Except coal) required for iron making/steel making are handled in a systematic manner, e.g., unloading, stacking, screening, crushing, bedding, blending, reclamation, etc. Different types of major raw materials used in an integrated steel plant are Iron Ore Lime stone Dolomite Manganese Ore Ferro and Silico manganese Quartzite Coal For Blast Furnace route Iron Making the main raw materials required are Iron ore lump Blast furnace grade lime stone Blast furnace grade dolomite Coke Sinter Scrap LD Slag Mn Ore Quartzite The main objective of raw material handling plant/ore handling plant/ore bedding and blending plant is to: homogenize materials from different sources by means of blending supply consistent quality raw materials un-interruptedly to different customers maintain buffer stock unloading of wagons/rakes within specified time norm as permitted by Railway. Raw material preparation (like crushing, screening etc.). The main functions of RMHP /OHP/OB&BP are – 1. Unloading& stacking of raw materials 2. Screening of iron ore lump & fluxes 3. Crushing & screening of coke/flux for base mix/sinter mix preparation 4. Dispatch of processed inputs to customer units 5 Different types of raw materials such as iron ore lump; iron ore fines, limestone, dolomite, manganese ore, etc. are supplied by SAIL mines (Jharkhand Group of mines, BSL, Odisha Group of Mines, RSP and Bhilai Group of Mines, BSP) or purchased from outside parties.. 1.2 Different Raw Materials and their Sources Sl. No. 1. Raw Materials Iron Ore Lumps (IOL) 2. Iron Ore Fines (IOF) 3. Blast Furnace( BF) grade Lime Stone BF grade Dolomite 4. 5. 6. 7. 8. 9. Steel Melting Shop (SMS) grade Lime Stone SMS grade Dolomite Quartzite Manganese Ore Mixed Breeze Coke 10. 11. 12. Mill Scale Flue dust LD Slag Sources Barsua,Kalta,Taldih,Kiriburu,Meghahatuburu, Bolani,Manoharpur,Gua,Dalli,Rajhara,Rowghat Manoharpur,Gua,Dalli,Rajhara Barsua,Kalta,Taldih,Kiriburu, Meghahatuburu, Bolani, Rowghat Kuteshwar, Nandini, Birmitrapur, Sonakhan , Bhawanathpur & Tulsidamar, Bhutan. Jaisalmer, Imported from Dubai & Oman. Belha, Baraduar, Hiri, Bhutan. Bobbili (AP) Barjamunda, Gua Ore Mines, MOIL(Purchased) Generated inside the plant (Blast Furnace & Coke Ovens) also interplant transport as per requirement. Generated inside the plant Generated inside the plant Generated inside the plant Recent trend in Raw Material Usage: Usage of pellet in Blast Furnace : Every attempt is being made to utilize low-grade iron ores, fines and industrial wastes. A huge amount of fine is generated during mechanized mining operation, which cannot be directly charged into blast furnace. The proportion of these fines is further increased due to narrow size distribution specification of iron ore required by blast furnace operators. For better utilization of low-grade ores, it is advised to beneficiate it after crushing and grinding. Such operations yield concentrate in finer form In addition to these fines there are good deposits of blue dust, which mostly remain unused due to its fineness These fines can be either used after agglomerations or utilized for direct reduction processes or production of powder metal products. Depending upon the size gradation of the ore fines the agglomeration can be done by sintering, pelletization, briquetting and nodulizing methods. Agglomeration generally refers to the process of forming a physically larger body from a number of smaller bodies. Thus, the major objectives of agglomeration processes are: (i) Economize mineral use by utilizing finer fraction of the minerals. 6 (ii) (iii) Energy conservation by preparing the burden so as to increase the efficiency of reduction process and decrease the coke rate. Environment improvement by utilizing the waste in-plant fines. Pelletising: Pelletization is an agglomerating process by balling in the presence of moisture and suitable additives like bentonite, lime etc. into 8-20 mm or larger size. These green pellets are subsequently hardened for handling and transportation by firing at 1200 – 13500C. Many times cement is added and pellet can be divided into (a) Acidic Pellets & (b) Basic Pellets Low grade iron ore, iron ore fines and iron ore tailings/slimes accumulated over the years at mine heads and generated during the existing washing processes, need to be beneficiated to provide concentrates of required quality to the Indian steel plants. However, these concentrates are too fine in size to be used directly in the existing iron making processes. For utilizing this fine concentrate, pelletization is the only alternative available. Advantages of Pellets: Iron ore pellet is a kind of agglomerated fines which has better tumbling index as compared to that of parent ore and can be used as a substitute for the same. Iron ore pellets are being used for long in blast furnaces in many countries where lump iron ore is not available. In India, the necessity of pelletisation is realized because of several reasons and advantages. The excessive fines generated from the iron ore mining and crushing units for sizing the feed for blast furnace and sponge iron ore plants are mostly un-utilized. Pelletisation Technology is the only route that is going to dominate the Indian steel industry in future. Pellets have: Good Reducibility: Because of their high porosity that is (25-30%), pellets are usually reduced considerably faster than hard burden sinter or hard natural ores/lump ores. Good Bed Permeability: Their spherical shapes and containing open pores, gives them good bed permeability. Low angle of repose however is a drawback for pellet and creates uneven binder distribution. High uniform Porosity (25-30%): Because of high uniform porosity of pellets, faster reduction and high metallization takes place. Less heat consumption than sintering. Approx. 35-40% less heat required than sintering. Uniform chemical composition & very low LOI: The chemical analysis is to a degree controllable in the concentration processing within limits dictated by economics. In reality no LOI makes them cost effective. Easy handling and transportation. 7 Unlike Sinter, pellets have high strength and can be transported to long distances without fine generation. It has also good resistance to disintegration.. Pellets Green Balls Fired Pellet Good Quality Fired Pellet Bad Quality 8 Pellet - Blast Furnace Grade: Chemical Quality (Typical) Parameter Specification Fe 65% min SiO2+Al2 O3 5% max Al2 O3 0.60% max Na2O 0.05% max K20 0.05% max TiO2 0.10% max Mn 0.10% max P 0.04% max S 0.02% max V 0.05% max Basicity (CaO+MgO)/(SiO2+Al2O3 ) 0.40 Moisture (free moisture loss at 1050C) 4% max (fair season) 6% max (monsoon) Screen Analysis Specification +16mm 5%max -16mm ,+9mm 85%min -9mm,+6.35mm 7.00%max -5mm 5%max Tumbler test (ASTM) Tumble index (+6.35 mm) 94.00 % min Abrasion index (+ 0.6 mm) 5.00 % max Specification Swelling 20% max. Compression Strength 250 KG/PELLET min Porosity 25.00 % min Reducibility 60% min Right quality raw material is the basic requirement to achieve maximum output at lowest operating cost. Quality of raw materials plays a very important and vital role in entire steel plant operation. Quality of 9 raw materials (incoming) and processed material (outgoing) is monitored by checking the incremental samples collected from the whole consignment. Samples are collected at Auto Sampling Unit or Sampling Unit. The samples prepared after quarter and coning method are sent for further analysis. 1.3 Quality Requirements of Raw Materials Sl. No. 1. Material Chemical Iron Ore Lump Fe Physical SiO2 62.3-63.2 % 1.8-2.8% 2. Iron Ore Fines Fe 62-63% 3. 4. 5. 6. Lime Stone (BF) grade. Dolomite (BF) grade. Al2O3 2.6-3.0 % SiO2 2.3 – 3.6% Al2O3 2.8 – 3.3% CaO MgO SiO2 43 - 50% 2.25-5% 3.5-6.5% CaO MgO SiO2 30% 18% 5% Lime CaO Stone(SMS) 52% grade(Jaisalmer), Imported(Dubai & Oman) Dolomite(SMS) CaO grade 29 % -10mm= 5% Max +40mm= 5% max +10mm= 5% Max - 1mm= 30 % max -5mm= 5% max +40mm= 5% max -5mm= 5% max +50mm= 5% max MgO SiO2 1% 1.5 % (max.) -40mm= 7% max +80mm= 3% max (30-60mm) MgO 23.5% -40mm= 5% max +70mm= 5% max SiO2 2.5 % 7. Mn Ore Mn= 30% (min.) 10-40mm size 8. Coke Breeze Fixed C>70%, SiO2-12-15% Moisture- 10-15% (max.) < 15mm 10 1.4 Process Flow Diagram of RMHP/OHP/OBBP Iron Ore (Lump +Fines), Lime Stone, Dolomite (Lump + Fines), Mn Ore From Mines Wagon Tippler/ Track Hopper Base Mix Preparation Unit Designated Beds Auto Sampler/ Sampling Unit Screening Unit Bedding & Blending Despatch to Customer 1.5 Material Handling Equipments Major equipments which are used in RMHP/OHP/OBBP areSl. No. 1. 2. 3. 4. 5. 6. 7. 8. 9. Major Equipments Wagon Tippler Car Pusher / Side Arm Charger. Track Hopper Stackers/ Stacker- cum Reclaimer (SCR) Barrel / Bucket wheel /SCR Transfer Car Screens Crushers Belt Conveyors Main Function For mechanized unloading of wagons For pushing / pulling the rakes for wagon placement inside the wagon tippler. For manual unloading of wagons For stacking material and bed formation For reclaiming materials from the beds For shifting equipments from one bed to another For screening to acquire desired size material For crushing to acquire desired size material For conveying different materials to the destination /customer. 11 Logistics: For smooth operation, the planning of Raw Material requirement for the set target is of prime importance. Raw material requirement plan is to be made ready and communicated to the concerned agencies well in advance to avoid any setback for the process. The different agencies which are involved in this process are -RMHP/OHP/OBBP -Traffic and Raw Material Department -Raw Materials Division (RMD) -Production Planning Control (PPC) -Finance - Materials Management (Purchase) -Railways, etc, Indian Railway acts as a linkage between mines and steel plant as major mode of Raw Material transport. Inside the plant, Traffic Department (of the Plant) plays the major role for foreign wagons (Railways) rakes movement and the processed/waste material movement by the plant wagons. Depending on the types of wagons, raw materials rakes supplied by the mines through railways are being placed either in wagon tippler or track hopper for unloading. The types of wagons for unloading in wagon tippler and /or track hopper is as given below – For Wagon Tippler - BOXN, BOXC, BOST, NBOY For Track Hopper - BOBS, NBOBS. The material such as Iron Ore Lumps, Iron Ore Fines, Lime Stone, Dolomite, Quartzite etc, unloaded in wagon tippler or track hopper is being conveyed through series of belt conveyors to the designated bed and stacked there with the help of stackers/ SCR. Bed formation takes place by means of to and fro movement of stacker. Number of optimum layers in a bed is controlled by stacker speed. Number of layers in a bed determines the homogeneity of the bed and is reflected in standard deviation of final bed quality. More is the number of layers more is the bed homogeneity and lower the standard deviation. Blending is the mechanized process of stacking & reclaiming to get optimum result in physical & chemical characteristics of raw material; this means that blending is a process of homogenization of single/different raw materials over a full length of pile/bed. Homogenization increases rapidly as the no of layers exceeds 400 and the effect becomes constant after 580 layers. 12 Std dev. Of Fe against No of layers Std. Dev. of Fe 1 0.5 0 200 400 600 No. of Layers 800 1000 Fig.:Change of Homogeneity of co-efficient with no. of layers after Blending Iron Ore Lump Screening: Screening of Iron Ore Lump is necessary because Iron Ore Lump coming from mines contains lot of undersize fraction (-10 mm), which adversely affects the blast furnace operation. Therefore, this undersize fraction (fines) is screened out at Iron Ore Lump screening section and then stacked in the designated Iron Ore Lump beds, from which this screened ore is supplied to blast furnace. Screened Iron Ore Lump also called sized iron ore. Screening plays a very important role as size of material is very important as far as blast furnace operation is concerned. Incoming Iron Ore Lump contains -10 mm fraction as high as 15 to 20 %. To get rid of this -10 mm fraction, vibratory screen of 10 X 10 mm mesh size is used. Base Mix Preparation: In some plants, base mix or sinter mix or ready mix for sinter is being prepared at RMHP/OHP/OBBP for better and consistent quality sinter and also for increasing sinter plant productivity. Base mix is a near homogeneous mixture of Iron Ore Fines, crushed flux (limestone and dolomite), crushed coke, LD 13 slag fines, mill scale, flue dust, return sinter etc, mixed at certain proportion. Before mixing, above said materials are stored in individual bunkers, also called proportioning bins. Prior to stacking, required ratio is to be set for Iron Ore Fines, flux, coke fines, return sinter etc., so that prepared base mix should satisfy the requirement of sintering plant. Panoramic view of RMHP/OHP/OBBP Steel Plant Panoramic view of RMHP/OHP/OBBP Iron Ore Fines: Iron Ore Fines is the base material for base mix preparation. Nearly 70-80 % Iron Ore Fines is used in base mix preparation. Fe content in Iron Ore Fines is around 62-64%. 14 Flux: Flux is a mixture of Lime Stone and Dolomite in certain proportion required in sinter making. Fraction of (-3mm.) in crushed flux is 90% and more. The main function of flux is to take care of gangue in blast furnace and also to increases the rate of reaction to form the good quality slag. Flux acts as a binder in sinter making to increase the sinter strength. Nearly 12-16% flux used in base mix preparation. Hammer crushers are used for crushing Limestone and Dolomite Lumps to required size i.e. (-3mm.) > 90%. BF Grade Dolomite 15 BF Grade Lime stone Dolo-fines Coke Breeze: Another important ingredient in base mix is crushed coke of size fraction (-3mm.) 85%.(Minimum) Coke for base mix preparation is received from Coke Ovens and Blast Furnace, called mixed breeze coke. The size fraction (+ 12.5 mm.) is screened out and sent along with sinter to blast furnace as a nut coke. The under size material is crushed in the two stage roll crusher i.e. primary and secondary roll crusher to achieve requisite size fraction of (-3mm.) 85%. Nearly 5-6% crushed coke used in base mix preparation. 16 Plant Return & Metallurgical Waste: Plant Return or BOF (LD) slag is used as a replacement of Blast Furnace grade Lime Stone. Nearly 3.5 – 4 % BOF slag is used for base mix preparation. Metallurgical Waste such as mill scale, flue dust, sludge, spillage also used in base mix preparation @ 1%. 1.6 1.7 Customers of RMHP Sl. No. 1. Customer Blast Furnace 2. Sinter Plant 3. Calcining/ Refractory Plant Product/ Material Size Ore (Screen Iron Ore Lump) & Quartzite. Base Mix/Sinter mix, crushed limestone & dolomite (Flux), crushed coke & nut coke SMS grade Limestone & Dolomite. Benefits of RMHP/OHP/OB&BP Provides consistent quality raw materials to its customer and also controlling the cost by: Centralized Raw Material facility Mechanized & faster unloading facilities Facility for sizing of materials for base mix preparation. Minimizing undersize in iron ore lump by means of screening Consistency in chemical & physical properties by means of bedding & blending. Input quality over a time period is known. Base mix preparation for Sinter Plants Supply prepared Raw Materials to Units Utilization of metallurgical waste. 1.8 Safety and Environment RMHP/OHP/OB&BP is a dust prone department due to handling of various types of Raw materials and conversion of lumpy mass into fines by crushing & screening, hence use of dust mask, safety goggles, safety helmet, safety shoes etc. is of prime important. To take care of surrounding area Dust Extraction & Dust Suppression system is installed. In some plants dry fog dust suppression (DFDS) system is also in use. Housekeeping is a major challenge for smooth operation in this department and requires special attention. Spillage materials are collected & reused by effective housekeeping. Scrap conveyor belts are regularly collected and disposed at designated place for proper disposal. This helps in maintaining personal and equipment health and safety. It makes the surrounding operation friendly. --- 17