Holy Cross College Building Systems Design Module 2 Part 2 PDF
Document Details
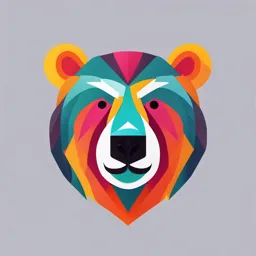
Uploaded by MultiPurposeCurl
Holy Cross College
2024
Tags
Related
- Holy Cross College Engineering Building Systems Design Module 2 Part 2 PDF
- Building Systems Design Module 2 – Part 2 PDF
- Building System Designs Preliminary Examination Reviewer PDF
- CE 35 Building Systems Design Lecture Notes PDF
- Construction Systems 1 (BENG 301) 2023-24 PDF
- Building Service System PDF
Summary
This document provides information on building systems design, including ceiling heights, room dimensions, and air space requirements. It also includes technical documentation and specifications for construction projects.
Full Transcript
HOLY CROSS COLLEGE Sta. Lucia, Sta. Ana, Pampanga SCHOOL OF ENGINEERING, COMPUTER AND LIBRARY STUDIES First Semester, A.Y. 2024 -2025...
HOLY CROSS COLLEGE Sta. Lucia, Sta. Ana, Pampanga SCHOOL OF ENGINEERING, COMPUTER AND LIBRARY STUDIES First Semester, A.Y. 2024 -2025 INSTITUTE OF CIVIL ENGINEERING BUILDING SYSTEMS DESIGN Module 2 – Part 2 Reading Assignment: 1. Section 212: Administrative Fines 2. Section 301: Building Permits 3. Section 307: Appeal Rule VIII: Light and Ventilation SECTION 805: Ceiling Heights 1. Habitable rooms provided with artificial ventilation shall have ceiling heights not less than 2.40 meters measured from the floor to the ceiling; provided that for buildings of more than one (1) storey, the minimum ceiling height of the first storey shall be 2.70 meters and that for the second story 2.40 meters and the succeeding stories shall have an unobstructed typical head-room clearance of not less than 2.10 meters above the finished floor. Above- stated rooms with natural ventilation shall have ceiling heights of not less than 2.70 meters. 2. Mezzanine floors shall have a clear ceiling height not less than 1.80 meters above and below it. SECTION 806. Sizes and Dimensions of Rooms 1. Minimum sizes of rooms and their least horizontal dimensions shall be as follows: a. Rooms for Human Habitations – 6.00 sq. meters with a least dimension of 2.00 meters; b. Kitchen – 3.00 sq. meters with a least dimension of 1.50 meters; and c. Bath and toilet – 1.20 sq. meters with a least dimension of 900 millimeters. SECTION 807. Air Space Requirements in Determining the Size of Rooms 1. Minimum air space shall be provided as follows: a. School Rooms – 3.00 cu. meters with 1.00 sq. meter of floor area per person; b. Workshop, Factories, and Offices – 12.00 cu. meters of air space per person; and c. Habitable Rooms – 14.00 cu. meters of air space per person. 1 Sizes and dimension of rooms Minimum air space Table VIII. G.1. Easement Along Water Bodies/Way by Location (PD 1067) WATER CODE Location of Water Body/Way Easement Urban Areas 3.00 meters per side of waterway (Fig.VIII.G.3.) Agricultural Areas 20.00 meters per side of waterway Forest Areas 40.00 meters per side of waterway 2 TECHNICAL DOCUMENTATION A. BID DOCUMENTS AND CONTRACT DOCUMENTS A Bid Document applies to before the contract is signed, whereas the Contract Document applies to after the contract agreement is signed by the owner and the contractor. Bid Documents consists of: Invitation to bid COST EFFECTIVE Instruction to bidder Bid forms Drawings Specifications Requirements for bonds and insurance All addenda The following information are necessary for the contractor to prepare an estimate and submit a bid. After the owner has make the decision to accept the bid, the owner and the contractor sign the contract agreement, which then forms the contract documents. Contract Documents consists of: The signed (contract) agreement Bonds and insurance Drawings Specifications Change Orders The purpose of the contract is to provide a legal document for construction and completion of the project. B. TECHNICAL SPECIFICATIONS A written requirement for a material, product, or service for a proposed project, like a ASTM-CONCRETE -STEEL PIPES building, bridge, or machine. -CARBON It describes the quantity of materials, proportion of mortar/concrete, workmanship, etc. which are not mentioned in the drawing. Specification are presented in an orderly, logical manner, they are organized into divisions and sections representing, in the opinion of the specification writer, the trades that will be involved in the construction. Factors: Nature of work Availability of materials Strength of materials 2500PSI Quality of materials TYPES OF SPECIFICATIONS DBARP 1. Descriptive Specifications Describe the components of a product and how they are assembled. Usually, architects and engineers do not have the resources, laboratory, or technical staff capable of conducting research on the specified materials or products. CONCRETE SAND 3 WATER GRAVE CEMENT 2. Reference Specifications CSI,ASTM,NSCP,RNFCP These employ standards of recognized authorities to specify quality. 3. Proprietary Specifications BRAND NAME NA POPROVIDE These specify materials, equipment, and other product by trade name, model number and manufacturer. 4. Base-Bid Specifications LINIENT, MADAMING BRAND NA RECOMMENDATION call out specific materials or products but allows the general contractor to substitute products they believe are “equal” These established acceptable materials and equipment by naming one or more manufacturers and fabricators. Base-bid specifications often provide the greatest control of quality of materials and equipment. 5. Automated specifications MODEL-SHEAR AND MOMENT, For building projects, specification writers normally maintain a library of master documents that are used as a basis for creating project specifications with a computer. Computers are used to facilitate and speed production of specifications and other technical documents. Standard forms for technical specifications can be obtained from the Construction Specifications Institute (CSI). The following is the division format developed by CSI: Division 01 — General Requirements – includes most requirements that apply to the job as a whole or several of the technical sections. Division 02 —Existing Conditions—includes most subject dealing site preparation and development. Division 03 — Concrete — include most items traditionally associated with concrete work; exceptions are paving, piles, waterproofing and terrazzo. Division 04 – Masonry – includes most materials traditionally installed by mason, exceptions are paving, piles, waterproofing, and terrazzo. Division 05 – Metals – includes most structural metals and metals not falling under the specific provision of other divisions. Division 06 – Wood, Plastics, and Composites – includes most work traditionally performed by carpenters. Division 07 – Thermal and Moisture Protection – includes most items normally associated with insulation and preventing the passage of water vapor. Division 08 – Openings – includes hardware, doors, windows, and frames; metal and glass curtain walls; transparent and translucent glazing. Division 09 – Finishes – includes interior finishes not traditionally the work of the carpenter trade. Division 10 – Specialties – includes factory-assembled, pre-finished items. Division 11 – Equipment – includes most items of specialized equipment. Division 12 – Furnishings – includes most items placed in the finished building. Division 13 – Special Construction – includes on site construction consisting of items that normally would fall under several division but require control that can be attained only by all parts in a single section. Division 14 – Conveying Equipment – includes the system that utilize power to transport people or materials. Division 21 – Fire Suppression – includes most materials to control fire. 4 Division 22 – Plumbing – includes most items that have been traditionally associated with the plumbing trades. Division 23 – Heating, Ventilating, and Air Conditioning – includes most items in HVAC Systems. Division 26 – Electrical – includes most items that have been traditionally associated with the electrical trades. Division 27 – Communications – includes most items in communication systems. Division 28 – Electronic Safety and Security – includes most items associated with safety and security. Division 33 – Utilities – includes items such as operation and maintenance of water utilities, hydrocarbon utilities, and electrical utilities. Division 34 – Transportation – includes items for the construction of roads, railways, airports, and bridges. Division 35 – Waterways and Marine Construction – includes dam construction, waterway construction, and coastal construction. SECTION FORMAT Section Format provides a uniform approach to organizing specification text contained in a project manual. It assists in the organization of specification sections by establishing a structure consisting of three primary parts. These are: General, Product, and Execution ADVANTAGES OF USING SECTION FORMAT Provides a standard for locating information within a section. Reduces the chances for omissions or duplications in a section. Facilitates coordination of project documentation within a project manual. DEFINITIONS 1. Project Manual – The written construction documents prepared for bidding or negotiating a construction contract and for construction project. The project manual typically contains bidding requirements, contract forms, conditions of the contract, and specifications. 2. Division – A standard category of construction specifications. 3. Section – A portion of the specifications covering one or more segments of the total project. Sections are included in a project manual as needed to meet project requirements. PARTS A section is a portion of a Division. 4. Part – one of the three groups of related information that make up a section (General, Product, and Execution) 5. Article – A major subject within a PART of a section consisting of one or more related paragraphs. 6. Paragraph – One or more statements, addressing a particular subject. 7. Subparagraph – One or more statements, related to a paragraph. Group of paragraph and subparagraph relate similar information under appropriately titled article. 8. Quality Assurance – Procedures for guarding against defects and deficiencies before and during the execution of the work. PROACTIVE 9. Quality Control – Procedures for evaluation, completed activities, and elements of the work for conformance with contract requirements. DISCREPANCY REACTIVE 5 SECTION FORMAT STRUCTURE ASTM,CSI, Part 1: General Requirements - It describes administrative, procedural, and temporary requirements unique to the section. o Summary o Project/Site Condition o References ASTM,CSI,NSCP o Sequencing o Definitions o Scheduling o Systems Description o Warranty o Submittals o System Start Up Owner’s o Quality Assurance Instructions Commissioning o Delivery, Storage and o Maintenance Handling Part 2: Products - includes information about systems, materials, manufactured units, components, and accessories; include mixes, shop fabrication, and factory finishing prior to installation or incorporation into the project. - It may also include products supplied for incorporation under other sections. - In addition, it may include items such as software programs used in direct digital control systems for heating, ventilating, and air conditioning systems. o Manufacturers o Accessories o Existing Products o Mixes o Materials o Fabrication o Manufactured Units o Finishes o Equipment o Source Quality Control o Components ADD MIXTURE-FAST CURING Part 3: Execution - Describes installation or application, including preparatory actions and post-installation, cleaning, and protection. o Installer o Re-installation o Examination o Field Quality Control o Preparation o Cleaning o Erection, installation, o Demonstration application, and construction o Protection o Repair/restoration o Schedules 6 C. CONSTRUCTION DRAWINGS - Visually communicate the design and the information required to bring it into reality to everyone who is involved in the TYPES OF CONSTRUCTION DRAWINGS 1. Architectural Drawings — these are given to the contractor to show how to construct the building envisioned by the architect. a. Site Plan b. Working Plan c. Section Drawing d. Elevation Drawing 2. Structural Drawings — consist of describe the structural members of the building and their relationship to drawings each other. a. Foundation Plans and Details b. Beam and Column Details c. Wall Sections d. Schedules necessary to describe the structural components of the building 3. Electrical Drawing 4. Mechanical Drawing 5. Plumbing Drawing 6. Finishing Drawing The drawing is a legal document describing what work is to be performed or what parts are to be produced. A careful process of checking drawings and models helps prevent errors. Overlooking what may seem to be small or insignificant details may result in large amounts of wasted money or, worse yet, a person's injury or death. ARTICLE 1723-LIABILITY FOR 15 YEARS Checking Drawings The signature in the drawing identifies who is responsible for its accuracy. A drawing is carefully checked and signed by the person who made it. It is then checked by the lead designer for function, economy, practicability, fit, tolerance, and so on. Corrections, if any, are then made by the original drafter. The final checker should systematically review the drawing for any remaining errors. They should study the drawing with particular attention to: 1. Soundness of design – with reference to function, strength, material, economy, easy, etc. 2. Choice of views, section, lettering, and so on. 3. Dimension 4. Standard parts 5. Notes – with reference to clear wording and legibility 6. Title form information Drawing Revision - An accurate record of all changes made to release drawings is tracked via a revision block. - Any changes or additions made to a drawing are tracked by a revision number. 7 D. COST ESTIMATE - Estimating – is the technique of calculating or computing the various quantities and the expected expenditure to be incurred on a particular work or project. Composition of Project Price The total price of a construction project is the sum of direct costs, contingency costs, and margin. 1. Direct costs - are the labor, materials, and equipment costs of project construction. 2. Contingency costs — are those that should added to the cost initially calculated to take into account events, such as rain or snow, that are likely to occur during project and affect overall project cost. Although they cannot be accurately predicted, the total effect of all contingencies on project cost can be estimated with acceptable accuracy. 3. Margin – sometimes called markup, has three components: indirect or distributable costs; company-wide or general and administrative costs and profit. 4. Indirect costs – are project-specified costs that are not associated with a specific physical item. They include such items as the cost of project management, payroll preparation, receiving and accounts payable. 5. Company-wide costs – include the following: costs that are incurred during the course of a project but are not project-related like cost of some portion of company salaries and rentals; and cost that are incurred before or after a project like cost of proposal preparation and cost of outside auditing. 6. Profit – it is the amount of money that remains from the fund collected from the client after all costs have been paid. Estimating Direct Costs 1. Industry or Facility approach —it refers to tie specific commercial or industrial use for which a project is intended. The client is interested in the specific activities that will be carried out and the space that will be needed. 2. Discipline or Trade approach— it takes the point of view of the contractor rather than the client. The job is broken into disciplines, or trades, of the workers who will perform the construction. TYPES OF ESTIMATES 1. Feasibility Estimates — these give a rough approximation to the cost of the project and usually enable the building owner to determine whether to proceed with construction. The estimate is made before design starts and may not be based on the specific design for the project under consideration. 2. Order-of-Magnitude Estimates - these are more detailed than feasibility estimates, because more information is available. For example, a site for the building may have been selected, a schematic design, a sketch of the structure and a plot of its location on the site, may have been developed. 3. Preliminary Estimates — these reflect the basic design parameters. A site plan and a schematic design is required. Generally prepared by the designer, preliminary estimates are made about 5 to 10% of the design has been completed. 8 4. Baseline Estimates — these are final preliminary estimates. For most buildings, requirements for preparation of an estimate includes plans, elevations, and sections. It is made after about 10 to 50% of the design has been completed. 5. Definitive Estimates — be estimate is based on plans, elevations, and sections; flow diagrams, and equipment and instrument list (for process plants); design segment for each discipline; and outline specifications. It identifies all costs. It is generally prepared by the designer and represents be end of the designer's responsibility for cost estimates. It is made after about 30 to 100% of the design has been completed. 6. Fixed-Price Estimates — prepared by a general contractor, a fixed-price estimate, or bid, represents a firm commitment by the contractor to build the project. It is based on the contractor’s interpretation of the design documents. A fixed-price estimate is highly accurate. It is made after 70 to 100% of the design has been completed. 7. Claims and Changes Estimates - there are prepared when a difference arises between actual construction and the project as specified in be original contract. ESTIMATING TECHNIQUES Parametric technique – it takes correlation into account; for example, for power plants, altitude and tie amount of oxygen in the air. It is usually employed for preparing feasibility or order-of- magnitude estimates. It is often used for checking high-level estimates, such as definitive, fixed price, and claims and changes that have been developed by the unit-price and development technique. It requires the most experience. Unit-Price Technique — this related directly to specific physical entities in the design — area of be office, volume of number of fixtures in restrooms. The estimator employs tie quantifies given in these documents to determine costs. It is frequently used for preparation of cost estimates. Crew Development Technique — it is used to prepare be estimate based on the costs for be specific personnel and equipment bat would be needed to complete each item during each phase of construction. Estimators tend to use be crew development technique for high-level estimates. Unlike the unit-price technique, crew development technique is based on the way the facility actually will be erected. It is the most accurate of be estimating techniques. It is the principal technique for fixed-price estimates; where accuracy is critical. ESTIMATING CONTIGENCY COSTS Contingency costs are usually expressed as a percentage of direct costs. - Contingency should be evaluated for each estimate and will vary by project type, location, and level of estimate. - Owner's contingency - covers the costs that the owner could during the course of the project - Designer's contingency — covers the costs that he designer could incur during the course of the project, such as the cost of services bat the designer renders and hat were not originally anticipated and be additional construction costs due to changes in the design. - Contractor's contingency — covers the costs that the contractor could incur during be course of the project Cost not normally covered by contingency allowances: 9 - Cost normally covered by insurance - Substitution of better materials - Increase in project size or scope - Natural disaster ESTIMATING MARGIN (MARKUP) Indirect or Distributable Cost - The technique used to calculate indirect costs resembles those used to calculate direct costs. Company-Wide Costs and Profit - Company-wide costs and profits, sometimes called gross margin, are usually lumped together for calculation purposes. - To calculate gross margin, the estimator normally consults standard handbooks that give gross margin as percentage of project cost. COMPUTER ESTIMATING 1. Utilities – these are programs that arrange information of do arithmetic. These are broad based; they can be applied to almost any estimating type, approach, and technique. 2. Databases — these contain raw information, for example, prices of plumbing fixtures that the estimator must analyze and choose from. These are designed to be used with one specific utility and one specific approach. Some are limited by a particular type of estimate and technique. 3. Expert Systems — these are programs that question the estimator, then use the answer to produce an estimate. Generally, they are even narrower in application than databases experts' systems will respond to a query as long as the estimator operates within the limits of their area of expertise. Drawbacks of Expert Systems 1. They do not take into account creative solutions or project-specific problems. 2. They do not change with changing technology. 3. They tend to be very expensive. MAKING ROUGH ESTIMATE OF THE PROJECT COST A very common practice employed by architects, engineers, builders, and estimators is to determine the probable cost of a project. Example: An architect was commissioned by one businessman to plan and supervise the construction of his commercial building with a total enclosed area of 450 square meters. For the record of construction, the total amount of expended to complete be project was Php 5,400,000.00. Find the unit cost per square meter. What would be the estimated cost of a similar establishment with 375 square meters? 10 E. VALUE ENGINEERING - Value engineering is a systematic and organized approach b provide the necessary function in a project at the lowest cost. - Value engineering promotes substitution of materials and methods with less expensive alternatives, without functionality. - It focuses solely in the function of various components and materials, rather than their physical attributes. Value engineering involves: - Identifying the main elements of a product, service or project - Analysis of the functions of those elements. - Developing alterative solutions for delivering those functions. - Assessing the alternative solutions. - Allocating costs to the alternative solutions. - Developing in more detail the alternatives be highest likelihood of success. Value engineering and sustainability - Value engineering is concerned with maximizing value, not just reducing costs, it seeks optimum solutions to remove unnecessary waste and reduce life cycle costs while improving functions, quality, and sustainability - Unnecessary waste might include: unnecessary cost, materials, resources, energy, water, time, plant, lead-in times, transportation, maintenance, replacement and disposal activities. 11