Model 152 Series Service Manual PDF
Document Details
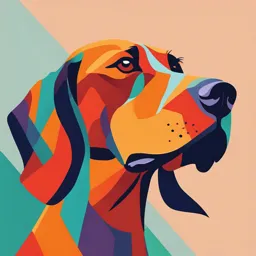
Uploaded by DaringDream
Tags
Summary
This document is a service manual for Model 152 series aircraft. It provides detailed instructions on troubleshooting, repair, and maintenance procedures for the aircraft's brake system. The instructions cover various models and include diagrams and illustrations.
Full Transcript
MODEL 152 SERIES SERVICE MANUAL 5-62. TROUBLE SHOOTING (Cont). TROUBLE BRAKES FAll. TO OPERATE. REMEDY Leak in system. If bra.ke ma.ster cylinders or wheel cylinder assemblies are leaking. repair. or in stall new pans. Air in system. La.ck of fiuid in master cylinders. Bleed system. Fill and bleed...
MODEL 152 SERIES SERVICE MANUAL 5-62. TROUBLE SHOOTING (Cont). TROUBLE BRAKES FAll. TO OPERATE. REMEDY Leak in system. If bra.ke ma.ster cylinders or wheel cylinder assemblies are leaking. repair. or in stall new pans. Air in system. La.ck of fiuid in master cylinders. Bleed system. Fill and bleed system. Defective ma.sier cylinder. Repair. or install new parts. ·5-63. BRAKE MASTER CYLINDERS. 5-64. DESCRIPI'ION. The brake master cylinders. located immediately forward of the pilot's rudder pedal.a. are actuated. by applying pressure at the top of the rudder pedals. A small reservoir ia incorporated into each master cylinder for the fluid supply. When dual brakes are installed. mec)t&nic&l linkage permits the copilot pedals to operate the ma.sier cylinders. 5-65. BRAKE MASTER CYLINDER REMOVAL. a. Remove bleeder screw at wheel brake assembly and dra.inhydraulic fluid from brake cylinders. b. Remove front seats &Dd rudder bar shield for access to the brake master cylinders. c. Disconnect parking brake Unkap and disconnect brake master cylinders from rudder pedals. d. Disconnect br_ake master cylinders at lower attach points. e. Disconnect hydraulic hoae from master cylinders and remove cylinders. f; Plug or cap hydraulic fittings. hoe and lines to prevent entry of foreign matter. 5-66. DISASSEMBLY. (Thru 1978 Models.) (See figure 5-12. sheet 1 of 3.) I a. Un.screw clevis UJ andjamnut l2). b. c. d. e. f. g. h. i. PROBABLE CAUSE Remove screw (18). spring (21). lock plate (22). washer (19) and spacer (20). Remove filler plug ( 17). Remove setscrew (5). Unscrew cover (4) and remove up over piston rod (3). Remove pision rod (3) and compensating sleeve (16). Slide sleeve (16) up over rod (3). Unscrew nut (12) from threads of piston rod (3). Remove Lock-O-Seal (15). 5-67. INSPECTION, REPAIR, AND OVERHAUL. (Thru 1978 Models.) (See figur 5-12, sheet 1 of 3). Repair and overhaul are limited to installation of new parts, cleaning, and adjusting. {Refer to reassembly paragraph for adjustment.) Use clean hydraulic fluid (MIL-H-5606) as a lubricant during reassembly of the cylinders. a. Inspect Lock-O-Seal (Parker Seal Co. pin 800-001-6) and replace if damaged. Re place all O-rings. Filler plug U7) must be vented so pressure cannot build up in the reservoir during brake operation. Remove plug and drill 1/16-inch hole, 30 ° from vertical, if plug is not vented. 5-68. REASSEMBLY. (Thru 1978 Models.) (See figure 5-12, sheet 1 of 3.) a. Install Lock-O-Seal (12) at bottom of piston rod (3). Revision I 5-35 I MODEL 152 SERIES SERVICE MANUAL i-1a 1------: I 1 19 16 ,...- -15 14 2---c ! 9 I 2., 20 - I I 22 11 17 3 7 nmu 5 1978 MODELS 3 1. Clevis 2. Jamnut Piston Rod 4. Cover 5. Setscrew 6. Cover Boss 3. 7. 5-36 Body Revision 1..... 8. Reservoir 9. 10. 11. 12. 13. 14. 15. 0-Ring Cylinder Piston Return Spring Nut Piston Spring Piston Lock-0-Seal Compensating Sleeve Filler Plug Screw Washer Spacer Spring 22. Lock Plate 16. 17. 18. 19. 20. 21. Figure 5-12. Brake Master Cylinder (Sheet 1 o f 3) MODEL 152 SERIES SERVICE MANUAL 0 1 THRU 1978 MODELS 2 3 4 5 22 17 8 9 21 Vi wA-A ---11 0.040:0.0005-INCH- DO NOT DAMAGE LOCK-O-SEAL 1. 2. 3. 4. 5. 6. Clevis Jamnut Piston Rod Cover Setscrew Cover Boss -- 3 7. 8. 16 Body Reservoir 9. 0-Ring 10. cylinder 11. Piston Return Spring 12. Nut 13 Piston Spring 12 l 15 14. Piston 15. Lock-0-Sea.l 16. Compensating Sleeve 17. Filler Plug 18. Screw 21. Spring 22. Lock Plate Figure 5-12. Brake Master Cylinder (Sheet 2 of 3) Revision 1 5-37 MODEL 152 SERIES SERVICE MANUAL CENTER LINE OUTLET PORT lB l B 7 5 8 ------, 14 View A-A 15 ViewB-8 BEGINNING WITH 1979 M O D E L S 15 1. 2. 3. 4. 5. 6. 7. 8. 9. 10. 11. 12. 13. 14. 15. Clevis Nut Screw Washer Spring Spacer Lock Plate Filler Plug Cap Piston Ring Packing Spring Setscrew Cylinder Body :15 10 Figure 5-12. Brake Master Cylinder (Sheet 3 of 3) 5-38 MODEL 152 SERIES SERVICE MANUAL b. Install O ring (9) in groove in piston (14); insert piston spring (13) into piston. and C. d. e. f. g. slide assembly up on bottom threaded pord.on of piston rod (3). Run nut (12) up threads to spring (13). Tighten nut (12) enough to obtain 0.040:.0.005iDch clears.nee between top of piston a.nd bottom of Lock-O-Seal. as shown in the figure. Install piston return spring (11) into cylinder (10) portion of body (7). IDsu.ll piston rod (3) end through spring (11). Slide compensating sleeve (16) over rod (3). Insta.ll cover (4). lock plate (22). spacer (20). washer (19). spring (21) and screw (18). NOTE Installation of spring (21) muat not contact rod (3). I h. Installjamnut (2) and clevis (1). i. j. Install filler plug (17). making sure vent hole is open. Install setscrew (5). 5-69. DISASSEMBLY. (BegiDDiDft with 1979 Models.) (See figure 5-12. sheet 3 of 3.) 5-70. INSPECTION AND R E PA I R. (Begimtinl' with 1979 Models.) (See figure 5-12. sheet 3 of 3.) I L Unscrew clevis (1) and nut (2). b. Remove screw (3), w&aber (4) spring (5), spacer (6) a.nd lock plate (7). c. Remove filler plug (8). d. Remove setscrew (14). e. Unscnrw cover (9) and remove up over piston (10}. f. Remove pmcm (10} a.nd spring (13). g. Remove packing (12) and back-up ring (11) from piston (10). Repair is limited to iDstallation of new pans and cleaning. Use clean hydraulic fiuid (Mll.-H-5606) as a lubric&nt during reassembly of the cylinders. Replace packing and backup ring. Filler plug (8) must be vented so pressure cannot build up during brake operation. Remove plug a.nd drill 1/16-inch hole. 30° from vertical. if plug is not vented. Refer to view AA for location of vent hole. 5-71. REASSEMBLY. (Beginning with 1979 Models.) (See figure 5-12. sheet 3 of 3.) 5-72. BRAKE MASTER CYLINDER INSTALLATION. 5-73. HYDRAULIC B R A K E LINES. &. b. c. d. e. f. g. h. Install Install Install Inst&ll Install Install Install Install spring (13) iD cylinder body (15). back-up ring (11) and packing (12) in groove of piston (10). piston (10) in cylinder body (15). cap (9) over piston (10) and screw cap into cylinder body (15). lock plate (7). spacer (6), spring (5), washer (4) and screw (3). nut (2) a.nd clevis (1). setscrew (14). filler plug (8), making sure vent hole is open. a. Connect hydraulic hose to cylinder. b. Install cylinder at lower attach point. c. Connect master cylinder to rudder pedals. d. Connect parking brake linkage e. Install rudder bar shield and install front seats. f. Fill and bleed bra.ke system in accordance with applicable paragraph in this section. Reviston 1 5.39 MODEL 152 SERIES SERVICE MANUAL DESCRIPTION. The brake lines are rigid tubing. except for flexible hose used at the brake master cylinders. A separate line is used to connect each brake master cylinder to its corresponding wheel brake cylinder. 5-75. WHEEL B R A K E ASSEMBLIES. 5-78. DESCRIPTION. (See figure 5-3.) The wheel brake assemblies use a disc which is attached to the main wheel. The assemblies also employ a floating brake assembly. 5-77. WHEEL B R A K E REMOVAL. (See figure 5-3.) Wheel brake aaaemblies can be remo ed by disconnecting the brake line (drain hydraulic brake fluid when disconnecting line) and removing the brake back plate. The brake disc is removed after the w h H l is removed and disassembled. To remove the torque plate. remove wheel and w e. See figure 5-3 for brake disassembly. 5-78. WHEEL B R A K E INSPECTION A N D R E PAIR. a. Clean &ll parts except brake liJli.ngs and O-rings in dry clea.niDg solvent and dry thoroughly. b. Insu.ll all new O-rings. l l O-ring reuse is necessary. wipe with a clean cloth saturated in hydraulic fluid and inspect for damage. NOTE Thorough cleaning is important. Dirt and chips are the greatest single cause of malfunctions in the hydraulic bra.kesystem. c. Check brake Uning for deterioration and mmrnum permissible wear. (Refer to applicable paragraph for rnuirn1u:n wear limit.) d. Inspect brake cylinder bore for scoring. A scored cylinder will leak or cause rapid Oring wea.r. Inst&ll a new brake cylinder if the bore is scored. e. If the anchor bolts on the brake assembly a.re nicked or gouged. they shall be sanded smooth to prevent binding with the pressure plate or "torque plate. When new anchor bolts are 'tO be installed. press out old bolts and install new bolts with a soft mallet. f. Inspect wheel brakes disc for a rniDirnum thickness of 0.190 (McCauley) or 0.190 (Cleveland). I f brake disc is below rninjmnm thickness. install a new part. 5-79. WHEEL B R A K E REASSEMBLY. (See figure 5-3.) NOTE Lubricate parts with clean hydraulic fluid during brake reassembly. a. 5-80. See figure 5-3 for assembly procedures. WHEEL B R A K E INSTALLATION. a. Place brake assembly in position with pressure plate in place. NOTE If torque plate was removed. install as the axle is installed or install on axle. If the brake disc was removed from the wheel. install as wheel is assembled. I 5-40 Revision 1 MODEL 152 SERIES SERVICE MANUAL 5-81. C H E C K I N G B R A K E L I N I N G WEAR. New bra.ke lining should be installed when the existing lining has worn to a mjnjm1un thickness of 3/32-inch. A 3/32-inch thick strip of material held adjacent to each lining can be used to determine amount of wea.r. The shank end of a drill bit of the correct size can also be used to determine wear of brake linings. 5-82. B R A K E LINING INSTALLATION. (See figure 5-3.) a. Remove bolts securing back plate. and remove back plate. b. Pull bra.ke cylinder out of torque plate and slide pressure plate off anchor bolts. c. Place back plate on a table with lining side down flat. Center a 9/64-inch (or slightly sm&ller) punch in the rolled rivet. and hit the punch sharply with a hammer. Punch out all rivets securing the linings to the back plate and pressure plate in the same manner. NOTE A rivet setting kit, Part No. 199-00100, is available from Cessna Parts Distribution (CPD 2) through Cessna Service Stations. d. Clamp the flat side of the anvil in a vise. e. Align new lining on back plate and place brake rivet in hule with rivet head in the lining. Place the head against the anvil. f. Center rivet setting punch on lips of rivet. While holding bal'.k plate duwn firmly against lining. h i t punch with hammer to set rivet. Repeat blows on punch until lining is firmly against back plate. Realign the lining on the back plate and in::.tall and set rivelii in the n:maining hulcii. InstaJ1 a new lining on pressure plate in the same manner. 1. Position pressure plate on anchor boltii and place cylinder in pui tiun su that anchur bolts slide into the torque plate. Install b.ick plate with bolts and washers. J. k. Complde bra.k,e lining cunditioning. Refer to paragraph 5-83A. f 5-83. B R A K E SYSTEM BLEEDING. NOTE Bleeding with a clean hydraulic pressure source connected to the wheel bleeder is recommended. a. Remove brake master cylinder filler plug and screw flexible hose with appropriate fitting into the filler hole at top of the master cylinder. b. Immerse opposite end of flexible hose in a container with enough hydraulic fluid to cover the end of the hose. c. Connect a clean hydraulic pressure source. such a.s a hydraulic hand pump or HydroF i l l unit. to the bleeder valve in the wheel cylinder. d. A s fluid is pumped into the system. observe the immersed end of the hose at the master brake cylinder for evidence of air bubbles being forced from the brake system. When bubbling has ceased. remove bleeder source from wheel cylinder and tighten the bleeder valve. I NOTE Ensure that the free end of the hose from the master cylinder remains immersed during the entire bleeding process Revi,;ion l 5-41 I MODEL 152 SERIES SERVICE MANUAL A -- :·7 ·,,,.... ,... ,... ·:->- 3 10 Deta.i.lA 1. 2. 3. 4. 5. 6. 7. 8. 9. Return Spring L H Chain Spring Plate Parking Brake Control Link R H Chain Brake Cylinder Fuselage-to-Brake Line 10. 11. 12. 13. 14. L H Brake Lines R H Brake Lines R H & L H Brake Hose Nipple Bracket Detail 5-42 Figure 5-13. Brake Systems 8 MODEL 152 SERIES SERVICE MANUAL 5-83A. BRA.KE LINING CONDITIONING. The brake lining pads used in this assembly are either non-asbestos organic composition or iron based metallic composition. Brake pads must be properly conditioned {glazed) before use in order to provide optimum service life. This is accomplished by a brake burn-in. Burn-in also wears off brake high spots prior to operational use. lfbrake use is required before burn-in, use brakes intermittently at LOW taxi speeds. CAUTION Brake burn-in must be performed by a qualified person familiar with acceleration and stop distances of the airplane. a. Non-asbestos Organic Composition Burn-in. 1. Taxi the airplane for 1500 feet, with engine at 1700 rpm, applying brake pedal forces as needed to maintain 5 to 10 M.P.H. (5 to 9 knots). 2. Allow brakes to cool for 10 to 15 minutes. 3. Apply brakes and check to see if a high throttle static engine run-up can be held with normal pedal force. If so, conditioning burn-in is complete. 4. H static run-up cannot be held, repeat Steps 1. thru 3. as needed. b. Metallic Composition Burn-in. 1. Taxi the airplane at 34 to 40 M.P.H. (30 to 35 knots) and perform full stop braking application. 2. Without allowing brake discs to cool substantially, repeat Step 1. for second full stop braking application. 3. Apply brakes and check to see if a hiJh throttle static engine run-up can be held with normal pedal force. If so, conditioning burn-in is complete. 4. If static run-up cannot be held, repeat Steps 1. thru 3. as needed. NOTE Normal brake usage should generate enough heat to maintain the glaze throughout the life of the lining. Light brake usage can cause the glaze to wear off, resulting in reduced brake performance. In such cases, the lining may be conditioned again following the instructions set forth above. 5-84. PARKING BRAKE SYSTEM. {See figure 5-13.) 5-85. DESCRIPTION. The parking brake system consists of a control knob on the instrument panel which is connected to linkage at the brake master cylinders. At the brake master cylinders, the control operates locking plates which trap pressure in the system after the master cylinder piston rods have been depressed by toe operation of the rudder pedals. To release the parking brake, depress the pedals and push the control knob full in. 5-86. REMOVAL AND INSTALLATION. (See figure 5-13.) See the figure for relative locations of system components. The illustration may be used as a guide during removal and installation of components. 5-87. INSPECTION AND REPAIR OF SYSTEM COMPONENTS. Inspect lines for leaks, cracks, dents, chafing, proper radius, security, corrosion, deterioration, obstruction and foreign matter. Check brake master cylinders, and repair as outlined in applicable paragraph in this section. Check parking brake control for operation and release. Replace worn or damaged parts. Revision 1 5-43/( 5-44 blank l