The Winding Process PDF
Document Details
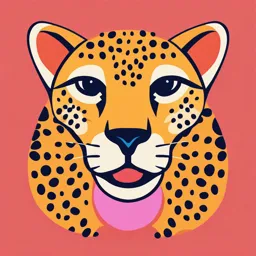
Uploaded by ImmaculateBasilisk
Textile Institute of Pakistan, Karachi
Shakeel Ahmad Paracha
Tags
Summary
This document explains the winding process in textile technology. It discusses different types of packages, winding methods, and winding machine classifications, providing valuable insights into yarn handling and storage.
Full Transcript
Textile Institute of Pakistan, Karachi. TEXT202 (Fabric Technology) The Winding Process Definition o The process of wrapping yarn on a suitable package is called winding. Package o Yarn wound on formers which facilitate convenient handling...
Textile Institute of Pakistan, Karachi. TEXT202 (Fabric Technology) The Winding Process Definition o The process of wrapping yarn on a suitable package is called winding. Package o Yarn wound on formers which facilitate convenient handling and withdrawal. o The package is a device that facilitates yarn storage in a suitable form that can be retrieved later as needed/required. Objectives of the Winding Process The main objectives of the winding process are: o To prepare a bigger package (from ring bobbins to other packages) having enough length of yarn on it. o For short or long-time storage. Sizing beams. o Doubling/Plying of yarn. o Change of cone weight as required in warping. o Change of cone to pirn/quill as required in shuttle weaving. o Change from hard wound cone to soft wound cone packages for yarn dyeing. o To remove spinning faults, e.g. thick & thin places. o Wax is also applied to the yarn to reduce the abrasion and friction during the winding process. o To produce a package of required density and shape suitable for the next stage of processing. Rule of Winding One end is fixed on a package, and other end is rotated w.r.t. fixed end around the package axis to impart coils parallel or at an angle to the diametrical plane of the package. Angles of Package Angle of Wind o The angle between a wrap of yarn on the surface of a package and the diametrical plane of the package. Angle of Crossing o The angle between two coils on the surface of the package. Angle of Reversal o Angle made by the same coil after reversal at the edge of yarn. Taper Angle o Angle made between the surface of the package to the diametrical plane package. Prepared By: Shakeel Ahmad Paracha Page 1 of 14 Textile Institute of Pakistan, Karachi. TEXT202 (Fabric Technology) Traverse It is the movement of yarn from one end of the core to the other end. Traverse Ratio No. of coils wound on per complete traverse cycle. Traverse Ratio is twice the wind. Wind No. of coils of yarn wound on per single traverse from one end of the package to the other. Ring Spinning Frame producing yarn in the form of Ring Bobbins Automatic Winding Machine Prepared By: Shakeel Ahmad Paracha Page 2 of 14 Textile Institute of Pakistan, Karachi. TEXT202 (Fabric Technology) Advantages of the Winding Process It appears that the winding process has no great significance as it is a simple process where the yarn is unwound from the ring bobbins and again wound on the new package. However, this is not true, and the winding process has great significance. Suppose if we use ring bobbins and start making warper’s beam out of them, then following problems may arise: o The ring bobbins will keep on exhausting very quickly and a lot of time will be wasted in replacing the empty bobbins with new ones. Furthermore, the winding time and cost would also be quite high. o The beam prepared from ring bobbins will be full of defects, and ultimately the woven fabric will have defects and a lot of time and resources will go wasted. o Because of the thin places, the warp threads will break more frequently and thus weaving efficiency and production will suffer. Types of Packages Prepared By: Shakeel Ahmad Paracha Page 3 of 14 Textile Institute of Pakistan, Karachi. TEXT202 (Fabric Technology) Cross Wound Parallel Wound Near Parallel Wound Cope Build Cored Core-less One Yarn Multiple Yarns Flangeless (Cheese) Flanged (Spool) Taper Side (Cone) Types of Winding Machines Based on package shape, winding machines are classified into: o Spool or Cheese Winder o Cone Winders If the winding machine produces cone as a product, then it is classified as cone winder. If the winding machine produces cheeses or spools as the product then it is classified as cheese or spool winder. Based on a package built, winding machines are classified into: o Precision Winders or Spindle Driven Winders o Random Winders or Grooved Drum Winders In precision winders the package is driven directly from the spindle, so they are also called as spindle driven winders. Prepared By: Shakeel Ahmad Paracha Page 4 of 14 Textile Institute of Pakistan, Karachi. TEXT202 (Fabric Technology) In random or cross-wound winders, the package is driven by frictional contact of a grooved drum, so they are also called as grooved drum winders. Conventional Winding Machine Automatic Winding Machine Prepared By: Shakeel Ahmad Paracha Page 5 of 14 Textile Institute of Pakistan, Karachi. TEXT202 (Fabric Technology) Magazine o It is used to place the small cones for winding. Usually 12 packages can be placed in it. Balloon Breaker o It is used to avoid the formation of the balloon, which is formed by the unwinding of yarn in over end withdrawal. Tension Device o The tension device maintains a proper tension on the yarn to achieve a uniform package density. It also serves as a detector for excessively weak spots in the yarn that break under the added tension induced by the tension device. The tension of the winding machine is controlled with the help of additive tensioner. Pre-cleaner (Yarn Clearer) o The purpose of yarn Clearer is to remove thin and thick places. o Yarn Clearers are usually of two types: Mechanical Electronic ▪ A mechanical clearer is as simple as two parallel blades. The distance between the plates is adjustable to allow only a predetermined yarn diameter to pass through. It only detects and cut thick places (slubs). ▪ The electronic clearers used today is of two types: ❖ Capacitive ❖ Photoelectric In capacitive clearer, the variation in the mass of yarn passing through the plates changes the capacitance of the unit. The system measures the mass of yarn, and the signal is not based on the physical dimensions of yarn. So, two yarns having the same mass may have different diameters because of low twist and high twist in the yarn. In a photoelectric clearer, the yarn passes between a light source and photocell. Any fluctuation in yarn thickness causes a fluctuation in light intensity coming to the photocell, which changes its resistance. The signal is transferred to yarn cutter, and it cuts the yarn. Waxing o It is used to reduce the hairiness or make the yarn surface smooth for further process. Stop Motion o The purpose of stop motion is to stop the winding machine when the yarn breaks or runs out. Stop motion varies from machine to machine. Electronic stop motion simply senses the existence of yarn without mechanical contact. Splicer o The joining of two broken ends with the help of air pressure is called splicing and device responsible for it is known as a splicer. o The working principle of splicer is untwisting of broken yarn ends and then twisting of both yarn ends with air pressure. o Leading parts in splicing operation/unit are: Prepared By: Shakeel Ahmad Paracha Page 6 of 14 Textile Institute of Pakistan, Karachi. TEXT202 (Fabric Technology) Retie pipe & suction mouth Untwisting & twisting nozzles Clamp plates Yarn guide lever Yarn cutters Yarn holding lever o When the yarn is broken, or bobbin is required to change the retie pipe and suction mouth start their working. The retie pipe takes the yarn from the bobbin side, and suction mouth from cone side & both suck the yarn with the help of air suction. Yarn Take-in o The upper and lower guide levers push the yarn ends into splicer, and both ends are clamped into clamping plates. Cutting of Yarn Ends o The upper and lower yarn cutter cut the ends of the upper and lower yarns. The cutting length is adjusted according to staple length. Untwisting o The cut yarn ends are sucked into the untwisting nozzle pipes and untwisted. The yarn guide lever returns a little to allow enough length of yarn to be untwisted. The untwisting length depends upon the staple length of fibres in yarn. Splicing o The yarn guide levers push the yarn ends, and these are pulled out from the untwisting nozzles according to the length required. The yarn is pressed by yarn holding lever, and it allows splicing nozzles to let out the compressed air at the same time. So, the yarn ends are tangled and twisted to complete splicing. The untwisting pressure is 6 - 6.5 bar and twisting pressure is 5 - 6 bars. The strength of splice should be 80 - 85 % of the inherent strength of yarn. Drum o It is used for indirect winding of yarn on the package. It has grooves in it, through which yarn is passed, and it causes cross winding in the package. The surface speed of the drum is given by: Cradle o It is used to keep the package on the surface of the drum at a certain pressure. Cradle pressure is controlled with the help of the piston and cylinder. Full Package Indicator Lamp (Green lamp) o This lamp lights when a full package is detected by the yarn length counter or package sizer; the package sizer stops the package when a specific diameter/specific length is achieved. Prepared By: Shakeel Ahmad Paracha Page 7 of 14 Textile Institute of Pakistan, Karachi. TEXT202 (Fabric Technology) Drum Start Button o If this button is pressed during doffing, the drum begins to rotate, and doffing is switched to automatic (the yarn length counter will be reset to zero simultaneously). Yarn Splicing Winding Machine Zones Prepared By: Shakeel Ahmad Paracha Page 8 of 14 Textile Institute of Pakistan, Karachi. TEXT202 (Fabric Technology) Types of Package Withdrawal The unwinding of the yarn from the package is called the withdrawal of the package. Two techniques are used for withdrawal of the package: o Side End Withdrawal o Over End Withdrawal Side End Package Withdrawal In this method, the package is mounted on a spindle, and the yarn is removed from its side. As long as the yarn is being removed, the package revolves. It is only suitable for slow speed machines because, at high speed, the package wobbles that can cause tension to increase. Side end withdrawal is associated with rectangular side packages. o Benefits No change in twist Less tension on yarn during unwinding o Draw Backs Slow unwinding Package needs to be rotated Over End Package Withdrawal In this method, the package is kept stationary, and the yarn is removed from the top. This method is suitable for high-speed machines. This method of withdrawal is associated with tapered packages, i.e. cones. The taper in the cone assists the efficient removal of yarn at high speed. o Benefits Package is stationary Higher unwinding speed Prepared By: Shakeel Ahmad Paracha Page 9 of 14 Textile Institute of Pakistan, Karachi. TEXT202 (Fabric Technology) o Draw Backs Not suitable for flat, polymer, rubber and metals yarns Balloon Formation Balloon breaker required Twist change If unwinding rotation is along yarn twist, the twist is increased equal to coil removed to the length removed for each traverse, else twist is decreased. Package Drive When a yarn is wound on the package, the package will have a certain rotary speed, while the yarn being wound will have a certain linear or surface speed. The surface speed of the yarn is given by: For uniform package winding and to keep the tension on the yarn constant, the surface speed of the yarn must remain constant throughout package formation. The drive given to the package on a winding machine can be of two types: o Positive or Direct Drive o Negative or Indirect Drive Prepared By: Shakeel Ahmad Paracha Page 10 of 14 Textile Institute of Pakistan, Karachi. TEXT202 (Fabric Technology) Positive or Direct Drive In this method, the package is directly driven by motors using gears, shafts, pulleys, etc. The rotary speed of the package remains constant throughout the package built. The main disadvantage is that as the diameter of the package increases, the surface speed of the yarn also increases that causes the tension on the yarn to increase. To keep the surface speed of the yarn constant, PIV gears are used. Negative or Indirect Drive In this method, the package is indirectly driven by a driving motor through frictional contact. The main advantage is that the surface speed of the yarn remains constant throughout winding. The disadvantage is that the yarn can get damaged due to frictional contact. This method of the drive cannot be used for delicate yarns. Yarn Joining Two methods of yarn joining are used: o Knotting The old method of yarn joining. Can create problems in knitting and weaving. o Splicing Introduced in the 1970 s. Splice is formed using compressed air. Splice joint is virtually invisible. Knotted V/S Spliced Yarn Prepared By: Shakeel Ahmad Paracha Page 11 of 14 Textile Institute of Pakistan, Karachi. TEXT202 (Fabric Technology) Winding Production Calculations Prepared By: Shakeel Ahmad Paracha Page 12 of 14 Textile Institute of Pakistan, Karachi. TEXT202 (Fabric Technology) Prepared By: Shakeel Ahmad Paracha Page 13 of 14 Textile Institute of Pakistan, Karachi. TEXT202 (Fabric Technology) Prepared By: Shakeel Ahmad Paracha Page 14 of 14