Energy Plant Instrumentation and Controls PDF
Document Details
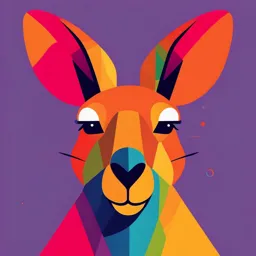
Uploaded by Reusl
Tags
Summary
This document provides an overview of instrumentation and controls in energy plants, focusing on components that are not part of the core control loop. It details indicators, switches, alarms, and logic devices, and how these components function in plant processes.
Full Transcript
Unit A-9 • Energy Plant Instrumentation and Controls Objective 3 List and describe the types of instruments that are not control loop components. Non-Control Loop Instruments A process may be equipped with numerous instruments that do not perform routine process control functions as part of contro...
Unit A-9 • Energy Plant Instrumentation and Controls Objective 3 List and describe the types of instruments that are not control loop components. Non-Control Loop Instruments A process may be equipped with numerous instruments that do not perform routine process control functions as part of control loops. These devices may be used to: a) Monitor process conditions b) Sound alarms that draw attention to improper or hazardous operating conditions c) Shut down equipment when unsafe conditions exist d) Remotely operate block valves e) Automatically start or stop process equipment. Devices in these types of services have special names, depending on their function. The following is a brief overview. Indicators Indicators are gauges, typically used to show temperature, pressure, flow, or level. In addition, instruments are manufactured to measure and indicate: • Control valve position • Fluid density • Material composition • Dew point • Weight • Vibration • Shaft position • Smoke, heat, and fire • Presence of toxic gases • Viscosity • pH • Conductivity • Turbidity • Rotational speed • Radiation levels Indicators may provide local or remote readings, or may be connected to other devices. In many cases, they serve as sensing elements in control loops. 1-20 4th Class Edition 3 • Part A Introduction to Energy Plant Controls and Instrumentation • Chapter 1 Switches Switches may act like indicators. For example, high or low-pressure switches may trigger alarms, or light up panel-mounted indicator lamps. Some switches initiate safety shutdown of equipment operating outside of normal operating parameters. A good example of this is a boiler low water cut-off. Switches are often connected to systems where information is passed from one device to another. The term “relay” is used in this context. A shutdown relay, for example, is a switch that transfers a shutdown signal, often converting the signal in the process. EP switches, for example, receive discrete voltage signals and convert them to pneumatic signals. Switches come in many different designs. They may be actual mechanical devices or computer “bits.” In either case, switches can turn pneumatic, hydraulic, electrical, electronic, or digital signals on or off. Alarms Alarms use indicators or switches, as sensing elements. They give visual, audible, or combined warning of unsafe or improper operating conditions. Alarm conditions may be displayed on specially lit panels called annunciators, or on computer terminal screens. This provides a quick indication of problem conditions. Some alarms have switches connected to dedicated hard-wired circuits. Their alarm points can only be changed by changing the switch set points. Computer based alarms compare transmitted process variables to “soft” alarm set points that can be changed (if necessary) from central control stations. These soft alarms give operators the flexibility to assign the alarms as desired, during special circumstances like startups. Alarms are sometimes confused with trips (or shutdown) switches. Although alarms and trips are often connected in shutdown systems, they are separate devices. An alarm itself does not shut down equipment. Logic Devices Switches, relays, and indicators can be incorporated into automatic decision-making systems such as Programmable Logic Controllers (PLC). In addition to controlling during routine operation, PLCs may be used to shut down or start up equipment in a very specific sequence. An example is the startup system of an automatic boiler. The burner ignition equipment (igniter and fuel valves) follows a sequence timer, if various permissives, such as air and fuel pressure switches, are satisfied. Logic systems are also used in batch processing, such as pumping operations, where storage tanks are filled in sequence. Logic systems may use dedicated hard wiring; or may be operated with computer software or PLCs. In processes such as air compression, where oil pressure, motor current and other conditions must be satisfied during the start sequence, logic systems are often used to control motor starts and stops. 4th Class Edition 3 • Part A 1-21