Energy Plant Control Signals Transmission PDF
Document Details
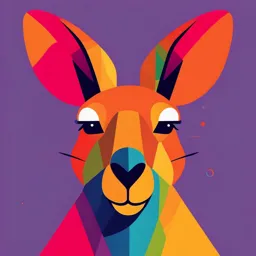
Uploaded by Reusl
Tags
Summary
This document introduces various methods for transmitting control signals in an energy plant setting, specifically focusing on pneumatic and electrical transmission methods. It also explains the role of transducers in converting physical conditions into signal representations. This would be useful for understanding industrial instrumentation and control systems.
Full Transcript
Introduction to Energy Plant Controls and Instrumentation • Chapter 1 Objective 2 Describe the various means by which control signals are transmitted, and the function of transducers. Signal Transmission Signals are information related to the measurement and control of processes. These are often t...
Introduction to Energy Plant Controls and Instrumentation • Chapter 1 Objective 2 Describe the various means by which control signals are transmitted, and the function of transducers. Signal Transmission Signals are information related to the measurement and control of processes. These are often transmitted from one location to another. Figure 6 shows some of the most common methods of signal transmission. Note that these methods convey process information in either analog or digital format. These will be discussed below. Figure 6 – Signal Transmission Methods 4th Class Edition 3 • Part A 1-13 Unit A-9 • Energy Plant Instrumentation and Controls Pneumatic Pneumatic instruments use variations in compressed air pressure to transmit information. The most common pneumatic signal range is 20 to 100 kPa. The supply pressure for a pneumatic control system is typically regulated to 140 kPa. Pneumatic control systems are analog systems. The pneumatic pressure signal is “analogous” to the process variable (meaning that the pressure represents the process condition). For example, a measured temperature range of 160°C to 220°C could be represented by a pneumatic signal ranging from 20 to 100 kPa. A value of 160°C could correspond to 20 kPa, and 220°C could correspond to 100 kPa. In this example, temperatures over 220°C would also be represented by a pneumatic signal of 100 kPa. A positive pneumatic pressure (20 kPa) is used to indicate the lowest process variable in the measurement range. Using the above as an example, if the temperature dropped below 160°C (say to 150°C), the pneumatic signal would not drop below 20 kPa. If the pneumatic signal drops below 20 kPa, a fault in the controller or the air supply is likely. The main advantages of using pneumatic signals are: a) They are simple and provide trouble-free operation. b) They may be less expensive than corresponding electronic instruments. c) They are safer to operate, especially in explosive environments. They present no risk of electric shock, fire, or explosion. Their disadvantages are: a) Their signals may be too weak to transmit over long distances. b) There is always a lag between the time a change in signal takes place at the transmitting location, and the time that the change in signal is sensed at the receiving end. This delay is caused because pressure takes time to build up at the other end of the line when the controller output increases. The longer the transmission lines, the greater the delay. c) The cost of purchasing and installing tubing for pneumatic signals is greater than for electrical wiring. d) The compressed air must be kept clean of oil or other contaminants, and must be extremely dry. Dirty or wet air freezes or otherwise plugs pneumatic control lines. Electrical Transmission systems may convey process information by using voltage or current signals. Some of the main advantages of using electrical signals over pneumatic signals are: a) Instant signal transmission (no delays) b) Precise and accurate signals c) Quiet operation Some of the disadvantages are: a) The electrical signal is more susceptible to corruption by outside influences (such as nearby power lines) b) Higher initial cost c) May be unsafe to operate in areas exposed to explosives and flammable materials 1-14 4th Class Edition 3 • Part A Introduction to Energy Plant Controls and Instrumentation • Chapter 1 Voltage Signals Voltage signals are transmitted by using electrical conductors as either discrete digital signals (on/off ) or variable voltage signals. Discrete Digital Voltage Signals Signals can convey detailed information about processes, such as precise temperature, level, or flow. However, often it is unnecessary to know the precise condition. It may be enough to know if a particular temperature has been reached, if a level is adequate, or if flow has been established. For this type of information, discrete digital signals are used. This type of information can be described with words like “true/false,” “on/off,” “start/stop,” “in/out” or “yes/no.” When used with a digital or electronic control system, these inputs are called contact closure inputs. Discrete input signals are produced by specific types of sensors that will always be in one of two possible states. These sensors are switches that detect level, pressure, temperature, or position (proximity). They change state (open or close) at specific conditions of the measured variable. They provide voltage signals, when they open or close, that correspond to their state. Controllers send discrete output voltage signals to devices such as motor starters, solenoids, and relays. The output signal either energizes or de-energizes these devices, causing them to start, stop, open, or close. When used with a digital or electronic control system, these inputs are called contact closure outputs. Consider the actions of a boiler combustion programmer. Depending on the programmer, one or more discrete voltage signals (contact closure inputs) from various sensors in the boiler safety circuit are required, before the purge begins. For boiler control, these switches are often called permissives. These permissives may be switches for level (boiler low water cut-off ), pressure (boiler high-pressure cut-off ), or temperature (boiler high temperature cut-off ). When all boiler start-up conditions are met, the combustion programmer sends a discrete voltage signal (a contact closure output) to a motor starter to start the draft fan. Next, the programmer waits for a discrete voltage signal from the airflow-proving switch and low fire start switches. When these signals are received, the combustion programmer sends a discrete voltage signal to the ignition transformer and the pilot solenoid valve to begin a trial for ignition. Variable Voltage Signals Like pneumatic signals, voltage signals can also be analog. Variable voltage signals can vary widely in the voltage ranges they use. Some voltages can be millivolt signals (as in the case of a simple thermocouple output), or low voltage signals (such as 0 to 24 volt 3-wire controls). One common signal is 1 to 10 volts, with “1” representing a positive zero value. Regardless, the transmitted voltage represents the process variable. Variable voltage signals are useful for transmitting signals short distances, so that the voltage signal does not become corrupted. For example, voltage drops over a length of conductor due to conductor resistance. In instrumentation, this voltage drop is called signal attenuation. To compensate for signal attenuation, variable voltage signals transmitted over longer distances must be amplified. Also, variable voltage signals can be corrupted by voltages induced from currents flowing in adjacent conductors (referred to as noise). To prevent this form of signal corruption, signal conductors can be shielded with a special grounding sheath. 4th Class Edition 3 • Part A 1-15 Unit A-9 • Energy Plant Instrumentation and Controls Current Signals Analog direct current signal transmission is widely accepted and used in industry. By varying current instead of voltage, signal attenuation and noise are reduced. A series circuit, formed by a signal loop, will have the same current at the transmitting and receiving ends, even if transmitted over long distances. The most common signal range is 4 to 20 milliamps. The “4” represents a positive zero value, like 20 kPa in the pneumatic system. When required, DC current signals can easily be converted to voltage signals. This is done by placing a known resistance in the series circuit and measuring the voltage drop across this resistance. The voltage variation across the resistance is relative to the current flow, according to Ohm’s Law. Fibre-Optic Signals The most common form of optical signal transmission involves transmitting light along a fibre optic cable. A fibre optic cable contains very long optical glass fibres coated in plastic. These fibres transmit data using pulses of light. Signals are normally transmitted along a fiber-optic cable in digital format, although analog transmission is sometimes used. Compared to electrical signal transmission systems, transmitting data using light has a number of advantages. Fibre-optic systems are • intrinsically safe • free from induced noise • less susceptible to signal attenuation, and • capable of transmitting data much faster than standard metal conductors. However, fibre-optic cabling is more expensive than metal conductors. As well, expensive transducers are required to transform the light signals into electrical signals and vice versa. Wireless Signals Wireless transmission can be accomplished using familiar wireless protocols, such as Wi-Fi and Bluetooth, or protocols tailored for industry, such as WirelessHART. These devices all transmit digital signals. Unlike devices that use Wi-Fi and Bluetooth, WirelessHART devices communicate over a “mesh.” This means that each transmitter in a signal communication network acts as a transmitter and as a receiver. Every transmitter can send its own signal and repeat the signal from any other transmitter within range. The WirelessHART system provides many redundant signal paths. If any one transmitter fails, the signal can take many alternate paths. Using this principle, a WirelessHART network provides built-in insurance against interference. For example, a pressure transmitter may be mounted near a concrete barrier, a high-voltage transmission line, or a high-power variable frequency drive. These may block or interfere with a wireless signal transmitted directly to a receiver. With a mesh network, the wireless signal can avoid this interference by taking a more roundabout route, hopping from transmitter to transmitter. WirelessHART devices use 2.4 GHz signals, with 128-bit encryption, to communicate between field devices (transmitters for temperature, pressure, flow, etc.) and a network gateway. The gateway is an electronic device that directs the various control signals over an Ethernet connection to and from a digital controller. 1-16 4th Class Edition 3 • Part A Introduction to Energy Plant Controls and Instrumentation • Chapter 1 Analog and Digital Signals Analog Signals An analog signal can be described as any continuous signal that is infinitely variable. All observable physical conditions – such as sound, light, velocity, and temperature – are analog in nature. All can vary infinitely in intensity or condition. An analog control signal can represent any value of measured variable within a range of predetermined values. These analog signals can vary in magnitude, amplitude, and frequency. A sound wave is a good example of an analog signal. All pneumatic signals (controller inputs or outputs) are analog by their very nature. Electronic and digital control systems have provisions for both analog output and analog input signals. Analog input signals may be either variable voltage or variable current signals, and originate from any of a wide variety of transmitters. Analog output signals are sent out by the controller as variable current or variable voltage signals to the various final control elements. Digital Signals Discrete digital signals have already been discussed. They are used to transmit and receive information about process conditions that have only two states, such as “on/off,” “start/stop,” and “open/closed.” For example, a discrete digital start command may be sent to a boiler draft fan, represented by the number one (1). A small electronic contactor controlled directly by the process controller closes. This causes the draft fan motor starter to energize, starting the fan. When the fan is in operation, a windbox pressure switch closes. This switch sends a “closed” signal back to the controller, represented by the number one (1). This confirmation that the fan started may be used as a “run status” signal for the controller. In this situation, after sending a fan start command, the controller would expect an “air flow switch closed” signal to verify the fan started. Any difference between the “fan start” command and the expected “run status” signal could be presented as an alarm, indicating the fan failed to start or it stopped running when it should be on. When the fan needs to be stopped, a stop signal sent to the draft fan would be the number zero (0). A contact then opens, causing the fan’s motor starter to open, and the fan to stop. When the airflow stops, the windbox pressure switch opens, sending a zero (0) signal to the controller to confirm the fan has stopped. Contact closure outputs are used to start and stop equipment. Contact closure inputs – simple single throw switches operated by sensing elements – are used as to provide digital run status and permissive information. Digital signals are also commonly used to transmit analog process information, but in digital form. Like the discrete signals already discussed, digital signals can be inputs or outputs. Digital input signals can provide information about process conditions, such as temperature, flow, and level. Digital output signals can be used to vary the speed of electric motors by using variable speed drives, or to change the position control valves and dampers. Digital control signals travel at high speed. They are not very susceptible to signal attenuation and noise. Modern computerized control systems can evaluate and process digital signals directly. These signals can be transmitted wirelessly, or over electrical wiring and fibre-optic cables. Digital signal transmission is now the dominant and preferred signal transmission method. For transmitters to convey analog information as digital information, small computers called analog to digital convertors are used. Typically, each local transmitter has its own analog to digital convertor. These convertors repeatedly sample analog process conditions over very short periods of time. For each sample taken, the analog to digital controller assigns a numerical value to the measured variable. After the data conversion, the information is transmitted in digital form to a controller, where it is processed directly with a computer-based controller. 4th Class Edition 3 • Part A 1-17 Unit A-9 • Energy Plant Instrumentation and Controls After the controller receives the digital signal and compares it to the set point, the controller sends a digital control output signal to the final control element. The final control element needs a digital to analog convertor. This small computer turns digital control output signals into proportional analog signals, so that the final control element can be correctly positioned. Transducers A transducer is a device that converts one form of energy into another form of energy. For example, a transducer can convert a physical condition (such as pressure, temperature, level, volume, or flow) into a corresponding signal. This type of transducer is known as a primary transducer. A good example of a primary transducer is a thermocouple that produces a variable millivolt signal, depending on the temperature it is exposed to. In the world of industrial instrumentation, primary transducers are usually called sensors. Secondary transducers convert the signal from a primary transducer to an analogous electrical or pneumatic signal. Below are some common types of secondary transducers. Current-to-Pneumatic (I/P) Transducers In many control systems, the transmitters, recorders, and controllers use variable current input and output signals (4 to 20 mA). However, control valves and other final control elements may require pneumatic signals to open or close. Current-to-pneumatic transducers change variable current signals into variable pneumatic signals to operate final control elements. Pneumatic-to-Current (P/I) Transducers P/I transducers receive pneumatic input signals (from 20 to 100 kPa) and produce variable current output signals (4 to 20 mA). In this way, pneumatic sensing devices can transmit proportional variable current signals to electronic controllers. Voltage-to-Pneumatic (E/P) Transducers Many control systems use variable voltage signals (0 to 10 V). Voltage-to-pneumatic transducers change variable voltage signals into variable pneumatic signals to operate final control elements. Pneumatic-to-Voltage (PE) Transducers PE transducers convert pneumatic signals into either discrete voltage signals or variable voltage signals. The transducers that produce discrete signals are often called PE switches. An example of a PE switch is the pressuretrol of a steam boiler. When the boiler pressure is low, the pressuretrol closes to send the boiler control a “call for heat” signal. When the boiler pressure reaches set point, the pressuretrol signals the boiler control to stop firing. PE transducers can also convert pressure signals into variable voltage signals. Consider a small packaged boiler firing rate control. Boiler pressure moves a pressure-sensitive bellows that positions a variable resistor. When the resistance changes, the voltage supplied to a voltage-sensitive modulating motor changes. The modulating motor positions the fuel valve and the combustion air damper to change the boiler-firing rate. With this setup, when the boiler pressure drops below set point, the boiler fires harder. The firing rate decreases when the pressure approaches set point. E/I Transducers E/I transducers are also called signal convertors. A transmitter may provide only variable voltage signals. However, this transmitter may be used to send signals to a controller that only accepts variable current signals. This type of transducer converts a 0–10 V signal to a proportional 4–20 mA signal. 1-18 4th Class Edition 3 • Part A Introduction to Energy Plant Controls and Instrumentation • Chapter 1 I/E Transducers I/E transducers are also signal convertors. This type of transducer converts a 4–20 mA signal to a 0–10 V proportional signal. Photoelectric Transducer Photoelectric transducers use light-sensitive sensors to detect light intensity at particular wavelengths. These transducers convert the light intensity to analog or digital signals for control purposes. Boiler flame scanners are common examples. These may detect ultraviolet, infrared, or visible light. As long as a flame scanner detects light from a fire, the burner continues to operate. If the flame goes out, the signal from the scanner ceases. This de-energizes the burner circuit and closes the fuel valves. 4th Class Edition 3 • Part A 1-19