Occupational Health and Safety Programs PDF
Document Details
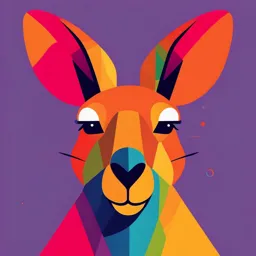
Uploaded by Reusl
Tags
Related
- Power House Hazards PDF
- Safety and Health Management in SAIL
- Management of Occupational Health and Safety Test Bank PDF
- Practice of Occupational Health and Safety Procedure PDF
- Industrial Safety (The Occupational Health and Safety) PDF
- Health, Safety and Environment (EGHS1140) Course Plan - FALL2024 PDF
Summary
This document details common occupational health and safety programs found in plants. It covers site-specific policies, joint committees, emergency response plans, and safety training requirements. The document emphasizes the importance of employee safety and preparedness for emergencies.
Full Transcript
Unit A-4 • Introduction to Plant and Fire Safety OBJECTIVE 1 Describe common occupational health and safety (OH&S) programs found in most plants. OCCUPATIONAL HEALTH AND SAFETY (OH&S) PROGRAM An occupational health and safety program in a workplace can be defined as an organized plan of action t...
Unit A-4 • Introduction to Plant and Fire Safety OBJECTIVE 1 Describe common occupational health and safety (OH&S) programs found in most plants. OCCUPATIONAL HEALTH AND SAFETY (OH&S) PROGRAM An occupational health and safety program in a workplace can be defined as an organized plan of action to • prevent work related accidents and occupational diseases, • respond to emergencies, and • proactively identify and control hazards. Many industrial plant sites have their own specific health and safety program focuses and requirements to meet their particular needs. The following are the general elements commonly found in most health and safety programs. Establishment of Site Specific Occupational Health and Safety Policy This policy expresses a company's committee to its employee's health and safety, and guides the company's actions. Clearly defined objectives include: a) Employees understanding of their right to refuse unsafe work. b) Accountability and Responsibility of Management and Employees. c) Orientation training for new and returning employees. d) Safe work and emergency procedure development and training. e) Process and procedure for accident and incidents reports, audits, and investigation. f) Process and procedure for risk assessment, hazard identification, and control. g) Regular and active promotion of workplace Health and Safety. h) Medical aid, including first aid facilities provision. i) Other health and safety requirements specific to the worksite. Establishment of Joint Occupational (Workplace) Health and Safety Committee It is recommended that a joint health and safety committee be established. The committee must consist of members from both workers and management. The Canadian Labour Code PART II - Occupational Health and Safety describes the duties and responsibilities of the Workplace Health and Safety Committees. The following is based on the Canadian Labour Code. 2-4 <(-------------------------------4t_ h _C_Ias_s_E_d_iilo_n_J • P _a _r_l_ A ( Plant Safety Programs • Chapter 2 Workplace health and safety committees must be established in any workplace under federal jurisdiction, where there are 20 or more employees. Some of the many duties of the committee are listed below. a) Consider and quickly resolve health and safety complaints. b) Participate in all of the inquiries, investigations, studies, and inspections that pertain to employee health and safety. c) Participate in implementing and monitoring a program for the provision of personal protective equipment, clothing, devices, or materials. If there is no policy committee, participate in the development of the program. d) Participate in planning and implementing changes that may affect occupational health and safety, including work processes and procedures. e) Inspect all or part of the workplace each month, so that every part of the workplace is inspected at least once a year. Employees appointed to the workplace health and safety committee must receive training and compensation for participating in meetings and carrying out their duties. The safety meetings consist of equal representation of management and workers. Emergency Response Plans Emergency procedures need to be created to deal with potential threats from fire, hazardous spills, hazardous leaks, or hazardous actions. These following points must be included in these procedures. a) A plan for an emergency evacuation of personnel. Provisions are to be included for those requiring special assistance. b) A full description of the emergency procedures that are to be followed. c) The location of emergency equipment in the plant. d) The name and address of the owner of the building. e) Designated evacuation routes and muster areas (gathering places). f) Training, responsibility, and location ofWardens. Designated employees serve as Wardens during an emergency. They may be in charge of specific areas, such as a floor of a large building or a lab area. If necessary, they will assist and direct the evacuation toward the assigned muster area. g) Emergency evacuation drills must be carried out at least once a year. Records of the drill are to be kept on file. The local fire department and emergency services should be notified prior to the drill. h) Bi-annual safety inspections. These inspections are done to make sure fire escapes, exits, stairways, and fire equipment are all in worldng order. Inspection records must be kept for two years. Site Specific Safety Training Requirements The elements of occupational, health and safety programs discussed above apply to basic general requirements at most plant sites. In addition, specialized safety training is required to address site-specific needs. Some examples of site-specific training will be discussed in the next few objectives.