3A2E3 C14 Obj 3.pdf
Document Details
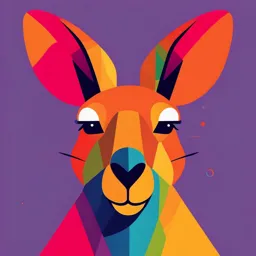
Uploaded by Reusl
CIE
Tags
Full Transcript
Objective 3 Define and give examples of typical workplace hazards, and describe a system of hazard identification and control. Hazards can be found in every workplace and can come from a wide range of sources. Every workplace has chemicals that, depending on the workplace, range from cleaning produ...
Objective 3 Define and give examples of typical workplace hazards, and describe a system of hazard identification and control. Hazards can be found in every workplace and can come from a wide range of sources. Every workplace has chemicals that, depending on the workplace, range from cleaning products to full scale chemical production. Physical hazards, such as substances or activities that threaten a persons physical safety, are another common danger. Many workplaces have health hazards that have the potential to harm workers’ short- and longterm health. Health hazards can result in diseases, disorders, and injuries. Ergonomic hazards are a lesser-known hazard category, but they influence workplace design, and considerations must be given to minimize the development of musculoskeletal disorders. Another lesser-known hazard category is the psychosocial hazards, which include stress, violence, and bullying. It is important to understand that not all hazards can be eliminated. A lot of hazards can only be mitigated. Hazard mitigation involves acting to reduce the risk of hazard exposure to the worker. In the workplace, hazard mitigation may include engineering controls, administrative controls, and the use of personal protective equipment. CLASSIFICATION of HAZARDS Inspection tours are regularly held within a workplace to identify any potential hazards to workers. In order to effectively analyze the findings of an inspection tour, it is necessary to establish criteria for the priority ranking of all hazards identified during the inspection. The best way to classify a potentially hazardous item or situation is to assess the likely outcome involving the item or situation and classify the hazard accordingly. Hazard classification systems may differ between companies, but they should all centre around rankings of critical, significant, and minor hazards. One example of a hazard classification system separates hazards into classes A, B, and C. Note: The classification system shown here is an example and is not to be construed as an official or legislated ranking system. Page 9 of 56 Class A Hazard A hazard in this class could result in a fatality or, at least, an injury resulting in a day or more of lost work time (called a lost time accident). Examples of class A hazards include the following: • Working under a suspended load • Working in an excavation that is improperly shored or cut back • Working in a confined space without proper protective equipment, or without using proper procedures • Working without fall protection when required • Entering a toxic environment without proper equipment Class B Hazard A hazard in this class is a condition or practice that is likely to cause injury or illness resulting in temporary disability, property damage, or both, and that is disruptive but not extensive. Some examples include the following: • Working without protective equipment • Working with inadequate lighting or ventilation • Slippery oil on a main aisle way • A broken tread at the bottom of office stair Class C Hazard Hazards in this class cause minor, non-disabling injury or illness, non- disruptive property damage, or both. Some examples include the following: • A carpenter handling rough lumber without gloves • A strong rancid odour from cutting oil circulating in the bed of a large lathe HAZARD IDENTIFICATION and CONTROL When conducting a safety inspection of a workplace, focus on things that can be seen or observed such as unsafe conditions or unsafe acts. An unsafe condition is a condition in the workplace that may endanger workers. An unsafe act is an act committed by a worker that may endanger that worker or fellow-workers. Using an inspection checklist that is designed specifically for the particular workplace is a good means of initiating hazard identification. Page 10 of 56 Inspection Checklist When developing a safety inspection checklist, the following items should be considered and included: • The checklist should be tailored to each specific organization and workplace. • Unsafe acts and conditions to look for in each area should be itemized so nothing important is missed. • Itemize what to look at and what to look for. • Include the checklist as part of the permanent record of the tour • Keep the checklist simple, so it is easy to follow. For example, have as many yes/no questions as possible, with minimal long answer questions. • The checklist should be detailed. For example, if the person doing the inspection must check for guards or safety devices on a piece of machinery, be sure to itemize each one. This step ensures that nothing is missed. Figure 1 shows an example of a workplace inspection report. These reports might also be called safety inspection reports or hazard inspection forms. These reports may have several parts, depending on the size of the workplace and the amount of area or equipment to be inspected. The inspection and forms are customized to the specific site and process. The process of completing a workplace inspection report may include the following: • Listing the specific items or areas to be inspected • Rating each item with one or more of the priority index numbers • Attaching relevant accompanying details of any unacceptable findings • Attaching any details of corrective actions taken at the time of inspection All reports must be followed up and action taken, with all follow-up reports posted on workplace bulletin boards. Usually timelines are set for corrective action. Page 11 of 56 Page 12 of 56