Incident & Accident Investigation Procedures PDF
Document Details
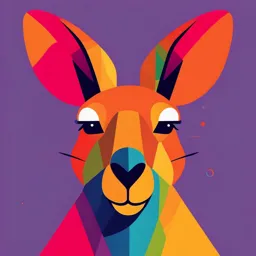
Uploaded by Reusl
Tags
Summary
This document explains the purpose, requirements, and procedures for workplace incident and accident investigation and reporting. It covers incident categories, the importance of reporting, incident investigations, and reporting forms. It also addresses the reasons why incidents are not always reported, such as fear of discipline or blame.
Full Transcript
Objective 10 Explain the purpose, requirements, and procedures for incident and accident investigation and reporting. INCIDENTS SND ACCIDENTSTEAM When an incident occurs at a work site, it is a significant event that should not be overlooked by workers or management. Many organizations define an un...
Objective 10 Explain the purpose, requirements, and procedures for incident and accident investigation and reporting. INCIDENTS SND ACCIDENTSTEAM When an incident occurs at a work site, it is a significant event that should not be overlooked by workers or management. Many organizations define an undesirable event as an incident. It can be said that all accidents are incidents, but not all incidents are accidents. If barrels of chemical were to fall from the back of a truck, but there was no loss of chemical and no one was injured, the event would be classified as an incident. However, if the chemical had spilled when the barrel fell off the truck, the event would be classified as an accident, because there was a loss (the chemical) and there may have been damage to someone or something. Incidents can be divided into two categories: near miss events and accidents. A near miss event is any event where no injury or loss occurs from an unexpected, unintentional, and undesirable occurrence. However, injury or loss could have resulted. An accident is an event involving loss, injury, or death resulting from an unexpected, unintentional, and undesirable occurrence. When an incident occurs, it is important that the event is followed up by an incident investigation and report, ensuring that the information is communicated to the appropriate personnel and authorities. All near misses and health related incidents should be investigated. Employees should understand the importance of reporting these “almost” events, since useful information can be lost if it is not reported. Incidents are not investigated and analyzed in order to assign blame or punish individuals. Incident investigations are carried out to ensure that all causes are identified, and corrective action is taken to prevent recurrence of similar events. This is key to ensuring that individuals are more comfortable in reporting all incidents, particularly near miss situations. Page 47 of 56 Requirements for Reporting and Investigation The employer responsible for a workplace has certain legal, ethical, and moral obligations whenever an incident occurs that involves a serious injury, or that has the potential of causing serious injury. These obligations are as follows: a) Report the incident to the nearest OH&S regional office. b) Carry out an investigation into the circumstances surrounding the incident. c) Prepare a report outlining the circumstances of the incident and the corrective action taken to prevent recurrence of the incident. d) Ensure that a copy of the report is readily available for inspection by an OH&S officer CAUTION Serious injuries include death, loss of sight or an eye, third degree burns, or fracture of a major bone. Examples of accidents that have the potential to cause serious injuries include the collapse of a crane or an uncontrolled explosion. OH&S Legislation includes the following features: • The penalties (including fines, prison terms, or both) that can be levied against someone who does not follow specified accident reporting and investigation procedures • The actions that can be taken at the scene of an accident to assist victims or protect property without disturbing any evidence • The procedure to be followed when an investigation committee is to be established, including details as to who should sit on the committee INCIDENTS REPORTING All incidents must be reported so that circumstances surrounding the event are communicated, and similar incidents can be prevented. Unfortunately, many potentially hazardous situations are not reported for the following reasons: a) Workers fear discipline. b) Workers are reluctant to report the actions of others. c) Workers do not want to be responsible for breaking an established safety record. d) A worker may feel that too much “red tape” is involved in treating a very minor injury. e) A worker who was recently injured may not want to report any new injuries in case they are perceived as accident-prone. f) Most workers want an employment record that is clear of any official reports. g) Some workers fear blame for a problem they did not create Page 48 of 56 The employer must address these reasons for failure to report potentially hazardous occurrences if employees are to become comfortable with reporting near miss situations. The greatest obstacle to reporting is the fear of blame or punishment. Once this fear is removed, information and communication will flow throughout the organization. Forms for Reporting Incidents Many organizations have created a simple form to assist employees in the reporting of incidents. This is often a multi-copy form, and is a simple method of reporting hazards so that action can be taken to eliminate them. In the sample form shown in Figure 13, the stigma associated with an incident form has been removed by changing the title to hazard report form. This form, although effective in documenting near miss incidents, should not take the place of other types of incident reports. Other types of incident reports might include the following: • Personal incident report • Motor vehicle incident report • Property incident report In some cases, organizations combine the incident report and investigation report into one form. Each organization will have its own form for reporting incidents that is specific to its requirements. The volume of required forms should be kept to a minimum to reduce the amount of paperwork, and the forms should be as simple as possible. The required information should be that which can be gathered quickly, efficiently, and accurately soon after the event occurs. Page 49 of 56 A copy of all incident reports must be available on the request of an occupational health and safety officer. The officer may also ask for design drawings of equipment, log books, maintenance records, or samples of materials. The officer is allowed, under OH&S Legislation, to make copies of documents. The officer may also seize or take samples of any substance, material, product, tool, appliance, or equipment that was present at, involved in, or related to the incident under investigation. INCIDENT INVESTIGATION If the incident investigation is perceived only as a process for blaming an individual, the process will surely fail. The investigator must have the trust of the workers. The supervisor in control of the area or process where the incident occurred will usually conduct the investigation. Workers, management, and the company health and safety committee should be involved in the investigation. If a supervisor’s actions indicate his or her main motivation is the prevention of future incidents and the creation of a more productive workplace, workers are inclined to cooperate and assist in the reporting of problems before they become incident. Timing of Investigations When an incident occurs, the first priority must be to take care of any injured workers and remove all potential hazards for the investigators. After this, the investigation of the incident should take place as quickly as possible, for the following reasons: • The shorter the time between the incident and the investigation, the more vivid the recollection of details are. • Observers will relate the facts more accurately if there was no time to have their opinions biased by discussions with others. • Changes in circumstances such as weather conditions, darkness, crew changes, and repositioning of equipment will have less time to occur. • It is less likely that evidence will be inadvertently removed or destroyed. • A quick investigation is an opportunity for the investigator to show sincere concern for the workers involved. Page 50 of 56 Conducting the Investigation In carrying out an investigation, it is helpful to use a standardized investigation form, so that the necessary information can be gathered and recorded in a standard format. Any form that asks for the following information can be used: • Names of the workers involved • Name of department and job titles • Location, date, and time of the incident • A description of what happened from witnesses and workers involved • A description of injury or illness • A description of damage to equipment, vehicles, or buildings • Causes of the incident • Suggestions for corrective action The investigator should have the following equipment readily available: a camera, notebook, pen, pencil, tape measure, investigation form, and safety equipment. Upon arrival at the scene, the investigator should carry out the following steps and procedures: 1. Get an overall view of the incident before talking to anyone. 2. Immediately take note of details like time of day, weather conditions, road conditions, and names of people at the scene. 3. Take pictures of the general area and incident scene. If the interviews are conducted in an office, the pictures taken at the scene may be used to recall or clarify points brought up in later conversation. 4. Make simple sketches for future recall. 5. Determine, from viewing the area, which person(s) would have the most accurate recollection of the incident. Ask, for example, who would have been facing the incident? Who would have had an unobstructed view? Who may have heard something? Who may have felt something? 6. Determine what events led up to the accident. This aspect could be the most important part of the investigation because it may be very easy to change a procedure to prevent a recurrence. 7. If possible, the first person to be interviewed should be the individual who has the most knowledge of the situation. In some cases, this may be a person who has been injured in the accident. Page 51 of 56 The key to a good investigation is effective interviewing of witnesses to the event. A complete report is made from notes taken during the interviews. Note: If an injury is serious, or has the potential for being serious, OH&S may also conduct an investigation at the work site. When this happens, all employees are required to cooperate in the investigation. The OH&S officer may ask to see documents such as training, maintenance, and inspection records. Incident Analysis Identifying and attempting to rectify the cause of an incident is an important step to incident investigation. In the past, most people believed that workplace accidents were inevitable and could not be prevented. Today, it is known that all accidents are preventable. As understanding of the causes of incidents has grown over the years, there have been several learning phases, or periods of time, when one particular belief was held above all others. The first widely held belief was that the design of facilities was the main cause of incidents. For example, people working closely with moving equipment could be caught up in a moving part, resulting in tragic injuries. It was believed that if buildings and equipment were designed and built properly, people would not be injured. Improving design to eliminate hazards in the equipment, and understanding more about ergonomics (how people and machines interact), does result in a drop in the number of injuries. However, people were still injured, leading to a new belief that accidents happen because employees are the problem. This belief led to the development of rules and written procedures that ensure employees would not injure themselves. This approach was successful because it emphasized the importance of establishing job procedures and rules, and it stated the consequences for any employers or workers who continued to place themselves or others at risk. It has been recently recognized that, while both of the previous factors have an impact on injury prevention, the real force for change resides with management, because this group has the most influence in the workplace. A positive influence from management can empower employees to become engaged in a safety culture that understands safe behavior, practices the safe behavior, and believes that everyone is responsible for a safe workplace. There have been various incident analysis models used over the years. Today, the most widely accepted method of analyzing an incident is based on identifying the hazard and then controlling or mitigating it. Page 52 of 56 Once all the facts surrounding the incident are gathered, a summary of the circumstances surrounding it can be written, hazards can be identified, and corrective actions can be recommended in the investigation report. Hazard Identification In this step, unsafe workplace conditions and procedures are identified and indirect causes of the incident are examined. Some of the unsafe conditions that have the potential to cause an injury include the following: • Inadequate guards or barriers • Inadequate or improper protective equipment • Defective tools, equipment, or materials • Congested or restricted action • Inadequate warning systems • Fire or explosion hazards • Poor housekeeping and a disorderly workplace • Hazardous environmental conditions, like gases, dusts, smoke, and vapours • Exposure to noise, radiation, or high and low temperatures • Inadequate or excessive illumination • Inadequate ventilation Unsafe Acts Unsafe acts are the actions taken by the worker at the time of the incident, such as the following: • Operating equipment without authority • Failure to warn nearby workers • Failure to secure equipment • Removing safety devices, or making them inoperable • Using defective equipment • Using equipment improperly • Failing to use personal protective equipment • Using improper procedures for loading, placement, or lifting • Working in an improper position for the task • Servicing equipment while in operation • Engaging in horseplay, or working under the influence of alcohol or other prohibited drugs Page 53 of 56 Indirect Causes The indirect causes of an incident are the conditions that led to the unsafe situation or allowed the unsafe act to occur. They could include any of the following: • Inadequate leadership and supervision • Inadequate physical/physiological or mental/psychological capability • Mental or physical stress • Lack of knowledge and skill • Improper motivation • Inadequate engineering, purchasing, or maintenance • Inadequate tools and equipment • Inadequate work standards • Abuse or misuse of equipment and facilities Hazard Control Both the identified unsafe conditions and unsafe acts can usually be corrected immediately by the development of preventive measures and/or workplace changes, such as the following: • Giving verbal instructions on how to safely carry out certain actions • Identifying the hazards • Seeking out and discussing safer techniques • Improving worker training and education Controlling the identified indirect cause of workplace incidents or accidents is typically a longer term development process involving preventive measures or system changes, such as the following: • Developing written procedures • Conducting planning sessions to obtain feedback • Changing design, purchasing, or maintenance policies Once a method of hazard control is decided upon, it must be implemented, evaluated, and possibly revised before final procedures are implemented. Page 54 of 56 Publication of Investigation Findings The importance of publishing the findings of an incident investigation can be illustrated by the example of a report given by the airline industry following an incident involving an aircraft. If there is a defect in the aircraft or a defect in a procedure, an industry-wide announcement is made so that all companies can inspect their aircraft for similar problems. The investigation report is published to ensure that a similar incident does not happen. Airlines have excellent safety records, and the close cooperation of the industry as a whole in publishing incident investigations has played a role in their successful safety record. There must be a positive attitude towards the publishing of an incident investigation. It should never be used to embarrass or blame an individual. Incidents cost money, and the only return on the investment of an incident is to use the findings in an educational program to prevent similar occurrences. When an incident investigation is made public, and there is a plan for preventing a recurrence, the action plan should also be made public. A progress report concerning the action plan must be published to instill confidence in the people involved. The pertinent details of the incident can be published on a standard investigation report form. The facts should be stated, and attention should be drawn to similar situations where the same problem could result unless action is taken. Many government agencies, companies, and industry associations publish safety alert bulletins and monthly safety newsletters to ensure the information reaches as many readers as possible. Page 55 of 56 SUMMARY OF SAFETY MANAGEMANT SYSTEMS Occupational health and safety, with its two levels of legislation at the federal and jurisdictional level, serves as the basis for workplace health and safety. The OH&S Legislation includes the responsibilities of the employer, employees, and workplace health and safety committee. In this chapter, typical workplace hazards were presented along with a system of identification and control. Hazard identification, mitigation, and control measures were discussed more thoroughly as they relate to safe work permits, equipment isolation and lockout, confined space entry, and ground disturbance and excavation. Specific procedures and permits relating to equipment lockout, confined spaces, and excavation were also reviewed. The purpose and typical components of an emergency response plan were highlighted, including typical emergencies, notification processes, key personnel, and response procedures. An explanation of the Workplace Hazardous Materials Information System (WHMIS) and the Globally Harmonized System of Classification and Labelling of Chemicals (GHS) was discussed. This explanation included the use of labels, safety data sheets (SDSs), and the responsibilities of the employer and employee. The chapter finished with information relating to incident and accident investigation and reporting. Safety management systems are used in the workplace to ensure the health and safety of all workers. Page 56 of 56