Fresno FFD Apparatus 310.009 Pre-Trip Inspection PDF
Document Details
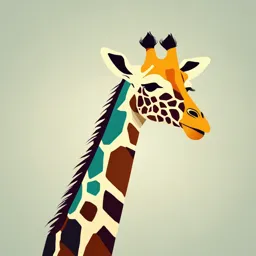
Uploaded by EfficientString
Fresno Fire Department
2007
William Veiga, Evelyn Yin-Zepeda
Tags
Related
- Spring Fire Department Personal Protective Equipment PDF
- Engine Operations Manual PDF
- HR OPS EQUIPMENT 19-40 PDF
- Hoffman Estates Fire Department Wildland Firefighting Operations PDF
- Palm Beach County Fire Rescue SOG 420-10 Rural Water Supply PDF
- Manual de Vehículos de Bomberos CEIS Guadalajara 2015 PDF
Summary
This document is a training manual for Fresno Fire Department (FFD) personnel on pre-trip inspections of fire apparatus. It covers procedures for daily inspections, emergencies, and reserve vehicles, emphasizing compliance with California Motor Vehicle Code standards.
Full Transcript
TRAINING AND EQUIPMENT MANUAL APPARATUS 310.009 PRE-TRIP INSPECTION EFFECTIVE: OCTOBER 2007 Current Revision Date: 02/08/22 Next Revision Date: 02/08/26 Author’s Name/Rank: William Veiga, Battalion Chief Evelyn Yin-Zepeda, Management Analyst II Review Level: 1 Administrative Support: ADA PURPOSE The...
TRAINING AND EQUIPMENT MANUAL APPARATUS 310.009 PRE-TRIP INSPECTION EFFECTIVE: OCTOBER 2007 Current Revision Date: 02/08/22 Next Revision Date: 02/08/26 Author’s Name/Rank: William Veiga, Battalion Chief Evelyn Yin-Zepeda, Management Analyst II Review Level: 1 Administrative Support: ADA PURPOSE The purpose of this policy is to provide instruction to Fresno Fire Department (FFD or Department) members with the procedure for performing a detailed pre-trip inspection of Department emergency response apparatus. APPLICATION All front-line firefighting vehicles are required to have a detailed pre-trip inspection (compliant with the California Motor Vehicle Code) performed at the start of each 24hour shift. OPERATIONAL POLICY The California Motor Vehicle Code requires any vehicle operated by a driver having a Class A, Class B, or Class C license, be inspected daily at the beginning of each work shift. Therefore, each in-service fire apparatus shall be inspected at the beginning of the shift using PS-Trax. PS-Trax is accessed at PSTrax.com. Department engineers shall be responsible for the following: 1. Daily Inspection: Prior to operation, the engineer shall inspect the assigned vehicle to ensure it is in safe condition and equipped as required by all provisions of law. The engineer shall also ensure all equipment is in good working order. Section 310.009 Page 1 of 14 2. Daily Report: At the start of the engineer’s tour of duty, he/she shall initiate the pre-trip inspection report indicating the condition of the vehicle and any recommended repairs deemed necessary. If, during the tour of duty, it becomes necessary to change engineers, the incoming engineer will verify the pre-trip inspection was performed during the shift and the apparatus is in compliance. 3. Emergencies: The daily inspection and corresponding report shall not prevent the company from responding to an emergency or special detail. If this occurs, the inspection and report shall be completed immediately upon return to the station. 4. Vehicle Inspection Review: Pre-Trip Inspection Reports can be viewed by querying a report from PS-Trax. Title 13 of the California Code of Regulations, Article 1234, requires a record of daily vehicle inspections. 5. Pump And Aerial Inspection: The daily inspection also includes inspection of the pump and aerial system. Engineers shall inspect those components pertinent to their assigned apparatus. While this is not a requirement of the vehicle code, daily inspection of the pump and aerial device is essential to the operations of the Department and the safety of its members. 6. Reserve Apparatus: Reserve apparatus need not be inspected daily if they are not being used. The reserve apparatus shall be inspected once they are placed in service and daily until they are placed on reserve status. If called for an emergency, the reserve apparatus need not be inspected until immediately following the emergency. While on reserve status, the reserve apparatus shall be inspected weekly on Saturdays. OPERATIONAL GUIDELINE This section intentionally left blank. Section 310.009 Page 2 of 14 PROCESS The following procedure is a useful guide taken from excerpts of the 2010 California Commercial Drivers Handbook and Department policies. Members are encouraged to follow this procedure in order to cover all areas of the apparatus. 1. Apparatus Overview: As a member approaches the vehicle, he/she should notice its general condition. The member should look for damage or if the vehicle is leaning to one side and look under the vehicle for fresh oil, coolant, grease, or fuel leaks. Member should also check area around the vehicle for hazards to vehicle movement such as people, other vehicles, objects, low hanging wires, limbs, etc. Members are to review the previous entries of the vehicle inspection report. Drivers must complete a vehicle inspection report each day and ensure the vehicle has been released for service by the Shop mechanics, if applicable. The Shop is to repair any items listed on the report, which affect safety, and is to certify on the report if those repairs were made or were unnecessary. Remember, when the driver gets behind the wheel, he/she (not the mechanic) is responsible for the safe operation of the vehicle. 2. Engine Compartment: The parking brakes should be on, the wheels chocked, and loose objects secured. The hood may have to be raised, the cab tilted, or the engine compartment door opened to check the following: a. Engine oil level. b. Coolant level, condition of hoses, and reservoir. c. Power-steering fluid level and hose condition. d. Batteries. i. Securely mounted to vehicle, not leaking or damaged. ii. Fluid at proper level, cell caps secure, and vents free of foreign material (except maintenance-free type); if the fluid is low, contact the Shop. iii. Terminals secure and clean; cables not worn, frayed, or loose. Section 310.009 Page 3 of 14 e. Alternator, water pump, and air-compressor secure; belts tight and not worn/frayed; learn how much give the belts should have when adjusted correctly and check each one. f. Engine compartment for leaks (fuel, coolant, oil, power-steering fluid, hydraulic fluid, battery fluid). g. Electrical wiring insulation for cracks or signs of wear. h. Transmission fluid level (may need to start engine). i. Lower and secure the hood or engine compartment door. 3. Cab Compartment: a. The engine must be started. i. Ensure the parking brake is on and the transmission is in neutral or park. ii. Listen for unusual engine noises. b. Gauges must be checked. i. Oil pressure gauge should come up to normal within seconds after the engine is started. ii. Ammeter and/or voltmeter gauge(s) should be in the normal range (average voltage should read 13.8 to 14.2 volts). iii. Coolant temperature gauge should begin a gradual rise to the normal operating range. iv. Air pressure gauge should start to gradually rise. v. Warning lights and buzzers for the oil, coolant, charging circuit and air pressure should go out right away. c. Condition of the controls should be checked for looseness, sticking, damage, or improper setting. i. Check the steering wheel; with the engine running, check for excessive play by turning the steering wheel back and forth; play should not exceed 10 percent (about 2 inches on a 20-inch steering wheel) before the left-front wheel Section 310.009 Page 4 of 14 moves. Ensure no binding or knocking and that steering operates smoothly. ii. Accelerator. iii. Service brake. iv. Parking brake. v. Retarder/engine brake controls (if vehicle has them). vi. Transmission control. vii. Interaxle differential lock (if vehicle has one). viii. Horn(s) and siren. ix. Heater and defroster. x. Windshield wipers. xi. Windshield washer and washer fluid. xii. Seat belts and warning lights and alarm. d. Mirrors and windshield must be inspected for cracks, dirt, illegal stickers, or other obstructions and should be cleaned and adjusted as necessary. e. Emergency equipment. i. Warning devices for parked vehicles (three reflective triangles or safety cones). ii. Fire extinguisher should be properly charged and rated. f. Lights and dash indicators should be checked for operation and condition. i. Check code three lights. ii. Check headlights; high and low beams. iii. Check tail, back-up, and brake lights. iv. Check turn signals, hazard, and marker lights. Section 310.009 Page 5 of 14 v. Check spot lights for operation and adjustment. vi. Check flood lights and hose pick-up lights. g. Radios, spare batteries, flashlights, and keys. 4. External Inspection: Walk around the vehicle and check each identified area, in an orderly manner, paying particular attention to the following items: a. Left front. i. Driver’s door glass should be clean. ii. Door latches or locks must work properly. iii. Check lights and reflectors. iv. Check windshield-wiper arms for proper spring tension. v. Ensure wiper blades are secure, not damaged, cracked or stiff. vi. Left-front wheel. 1) Check the condition of wheel and rim; ensure the wheel is not damaged or cracked; ensure there are no missing, bent, broken or loose studs, clamps, or lugs. 2) Check the condition of the tires; ensure the tires are properly inflated and the valve stem and cap are okay; check for any serious cuts or bulges; tread wear should be even and the depth at 4/32-inch minimum for front tires; ensure the type and size of the tire is the same as the right side. vii. Report rust-streaked lug nuts. viii. Check hub oil level and look for leaks. ix. Ensure all equipment is in place and secure. Section 310.009 Page 6 of 14 b. Right front. i. Perform the same checks as left front. ii. Primary and safety-cab locks engaged (if cab-over-engine design). c. Right rear. i. Compartment doors are closed, and equipment is secure. ii. Check the condition of wheel and rim; ensure the wheel is not damaged or cracked; ensure there are no missing, bent, broken or loose studs, clamps, or lugs. iii. Check the condition of the tires; ensure the tires are properly inflated and the valve stem and cap are okay; check for any serious cuts or bulges; tread wear should be even and the depth at 4/32-inch minimum for rear tires; all tires on the same axle are to be of the same type and size. iv. Wheel bearing/seals not leaking. v. Check lights and reflectors. d. Left rear same as right. 5. Underneath the Vehicle: Inspect underneath the vehicle, paying particular attention to the following items: a. Left front. i. Left-front suspension. 1) Condition of axle, spring, spring hangers, shackles, U-bolts. 2) Shock absorber is secure and not leaking. ii. Left-front brake. 1) Condition of brake chamber and slack adjuster. 2) Brake drum/rotor intact, no damage or cracks. Section 310.009 Page 7 of 14 3) Ensure the brake lining is intact, not too thin, no rivets or bolts are showing and is not contaminated with grease or oil. 4) Condition of hoses. iii. Condition of steering system. 1) No loose, worn, bent, damaged, or missing parts. 2) Grab steering mechanism to test for looseness. b. Right front perform same checks as left front. c. Middle. i. Rear of engine is not leaking. ii. Transmission is not leaking. iii. Drive shaft(s) not bent and couplings secure and free of foreign objects. iv. Exhaust system is secure, not leaking, not touching wires, fuel, or air lines. v. Frame and cross members have no bends or cracks. vi. Air reservoirs secure and not damaged or leaking. vii. Air lines and electrical wiring are secured against snagging, rubbing, and wearing. d. Right rear. i. Suspension. 1) Condition of axles, springs, spring hangers, shackles, and U-bolts. 2) Powered axle not leaking lube oil. 3) Condition of torque rod arms and bushings. 4) Shock absorbers secure and not leaking. Section 310.009 Page 8 of 14 ii. Brakes. 1) Condition of brake chambers and slack adjusters. 2) Brake drums/rotors intact; no damage or cracks. 3) Ensure the brake lining is intact, not too thin, no rivets or bolts are showing, and is not contaminated with grease or oil. 4) Hoses not damaged, cracked, bulging, or leaking. iii. Fuel tank and lines securely mounted and not damaged or leaking. e. Left rear perform same checks as right rear. 6. Brake System: Conduct an inspection of the brake system, paying particular attention to the following items: a. Park brake test: must stop apparatus while rolling below five miles per hour. b. Low air pressure: warning light or alarm turns on at 55-75 psi. c. Governor: cut-in no less than 85 psi and the governor cut-out at less than 130 psi. d. Reservoir leakage (static test): less than 2 psi drop in one minute. e. Service air leakage (applied test): less than 3 psi drop in one minute. f. Emergency/parking brake test: between 20 and 45 psi. push/pull valve operates g. Brake measurement. Note: ---- See Training and Equipment Manual, Section 310.001, Air Brake System Inspections, for detailed instructions on brake inspection. Section 310.009 Page 9 of 14 7. Pump Operation: Inspect and test the pump operation as follows: a. Ensure pump operation once placed in pump gear. b. Operate the transfer valve if using a two-stage pump. c. Operate and adjust the relief valve or governor. d. Check gauges at the pump panel for accuracy. e. Disengage the pump. f. Ensure water tank is full. 8. Aerial System: Conduct an inspection of the aerial system as follows: a. Ensure the power take-off operates once engaged. b. Check hydraulic lines for leaks. c. Check cables for signs of wear or fray/not excessively loose. d. Check electrical lines on the aerial for damage or wear. e. Ensure lift cylinders are properly attached and not leaking fluid. f. Check the ladder for damage or wear. g. Ensure the ladder pipe is in the “rescue” position. INFORMATION Discrepancies found during the inspection are to be correctly noted on the daily check. Fire apparatus shall be placed out of service and the shop and battalion chief notified should severe conditions exist which prevent the safe operation of the vehicle. If after hours or on a weekend, the battalion chief shall be notified in order to contact Shop mechanics. Out-of-service criteria are as follows: Section 310.009 Page 10 of 14 1. Brakes (General): A vehicle is out of service if 20 percent or more of its brakes have one of the following defects: a. Brakes do not pass all of the pre-trip brake tests. (Refer to Training and Equipment Manual, Section 310.001, Air Brake Test; Section 310.001a, Hydraulic Brake Test; and the Apparatus Information Book.) b. Will not actuate effectively or friction material will not contact the drum or rotor. c. Evidence of current, ongoing lining/drum contamination where lining is wet and there is evidence of additional contamination. d. Lining dangerously thin, missing, broken, or fastener is exposed. e. Brakes missing from axle requiring brakes. f. Loose or leaking air chamber. g. Any part of drum or rotor broken off or in danger of falling off. h. Damaged, bulging, or leaking air lines. i. Reservoir pressure will not build from 85 to 100 psi in 45 seconds. j. Loose, cracked, or broken air compressor, mount, pulley, or belt. k. Air reservoir damaged, leaking, or not properly secured. 2. Suspension, Frame and Cross Member: a. Any part is missing, damaged, cracked, or loose. b. Broken or loose body or equipment mounts or supports. c. Air suspension not properly inflated. d. Any fuel leak from tank or lines. Section 310.009 Page 11 of 14 3. Exhaust System: a. System installed so wiring, air lines, tires, and fuel lines could be burned or ignited. b. Leakage forward or directly below opening in floor of enclosed cab, which would allow carbon monoxide poisoning. 4. Steering System: a. Steering wheel with power steering must have no more than 10 percent of free play arc, with engine running, before front wheels move (about 2 inches on a 20-inch steering wheel). b. Broken or loose column or steering wheel. c. Worn column universal joint. d. Loose or worn pitman arm. e. Loose or excessive fluid leakage in power assist cylinder or control valve. f. Hydraulic leakage in steering pump or high-pressure hose(s). g. Loose, cracked, or broken steering pump, mount, pulley, or belt. 5. Lights: a. Does not have at least one headlight operable on low beam. b. Does not have at least one steady burning red light in rear visible for at least 500 feet. c. Does not have at least one operative stoplight on the rear visible for at least 500 feet. 6. Emergency Code Lights: a. Does not have at least one steady burning red light in front visible for at least 500 feet (Code 2 responses only). 7. Tires: a. Any condition allowing the body or frame to contact the tire or rim assembly. Section 310.009 Page 12 of 14 b. Less than 4/32-inch of tread depth in every major tread groove on any steering tire; steering tires should be prepared for replacement at 5/32-inch depth. c. Less than 2/32-inch of tread depth in every major tread groove of a rear tire; with dual tires, both tires must be defective. d. Dual tires mounted or inflated so the inner sidewalls contact each other. e. Sidewall cut or damaged, exposing ply cords. f. Bulge suggesting tread or sidewall separation. g. Flat tire or audible air leakage. 8. Wheels and Rims: a. Lock ring is bent, broken, cracked, mismatched, or improperly seated. b. Cracked rim. c. Fasteners loose or missing. d. On ten-stud wheel, three missing or defective fasteners. e. On eight-stud wheel, two missing or defective fasteners. 9. Windshield Wipers: a. Inoperative or ineffective wiper on driver’s side during weather requiring wipers. 10. Defroster: a. Inoperative or ineffective defroster during weather requiring defroster. Following apparatus inspection, the engineer shall note its condition and place their initials and employee ID number at the bottom of the row representing the current date. If, in the opinion of the Shop mechanic, a defect need not be corrected for the safe operation of the vehicle, the mechanic shall state such information on the back of the Section 310.009 Page 13 of 14 Administrative Manual, Section 106.023, Pre-Trip Inspection Report, Form FD-03 (FD-03), sign, and date it. If in doubt, contact the Shop concerning specific questions about the safety of the vehicle. DEFINITIONS This section intentionally left blank. CROSS-REFERENCES Administrative Manual Section 106.023, Pre-Trip Inspection Report, Form FD-03 California Commercial Drivers Handbook California Motor Vehicle Code Training and Equipment Manual Section 310.001, Air-Brake System Inspections Section 310.001a, Hydraulic Brake System Inspections Section 310.003, Apparatus Information Book Section 310.009 Page 14 of 14