Warp Knitting Machine PDF
Document Details
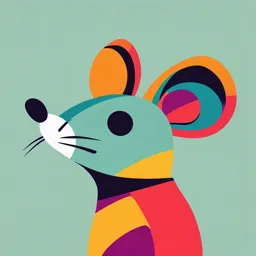
Uploaded by SimplestSaxhorn
Tags
Summary
This document provides an overview of warp knitting technology, including the construction of warp knitted fabrics, warp beams, guide bars, yarn feeding technology, and take-down technology, useful for those interested in textile engineering or manufacturing.
Full Transcript
Knitting Technology Basics of Warp Knitting ► Construction of warp knitted fabrics ► The warp beams ► The guide bar ► The guides ► Yarn feeding technology ► Take-down Technology Construction Of Warp Knitted Fabrics ►In a warp knitted structure, all ends supplied from the same w...
Knitting Technology Basics of Warp Knitting ► Construction of warp knitted fabrics ► The warp beams ► The guide bar ► The guides ► Yarn feeding technology ► Take-down Technology Construction Of Warp Knitted Fabrics ►In a warp knitted structure, all ends supplied from the same warp sheet normally have identical lapping movements because each is lapped by a guide attached to the same guide bar. The Warp Beams ►To ensure uniform conditions of warp feed and tension, the yarn ends are supplied from flanged beams attached to shafts that turn to unwind the warp sheet in parallel formation. The Warp Beams ►For convenience of handling, a number of beams may be attached to a beam shaft to achieve the full width of the warp sheet, ►For example, a warp sheet 84 inches (213 cm) wide might be supplied from a full-width beam, from two beams each 42 inches (106 cm) wide, or from four beams each 21 inches (53cm) wide. The Guide Bar ►Each guide bar is normally supplied with a warp sheet from its own beam shaft to suit its requirements of threading and rate of warp feed for its particular lapping movement. ►The minimum number of guide bars and warp sheets for commercially acceptable structures is usually two. The Guides ►Warp guides are thin metal plates drilled with a hole in their lower end through which a warp end may be threaded if required. ►They are held together at their upper end as a single unit in a metal lead and are spaced to the same gauge as the needles. Yarn Feeding Technology ►Yarn is fed to the needle typically from a warp beam that will contain yarns spaced at the same pitch as the machine gauge. ►Modern warp beams may contain 30,000 to 50,000 metres of warp. Yarn Feeding Technology ►On earlier raschel machines and even today on raschel machines with more than six guide bars and warp systems, the yarn tension developed in the warp by the pull of the needles was used to turn the warps against a warp tension controlled warp brake system or let-off. Take-down Technology ►The take-down system on warp knitting machine is relatively simple as compared with weft knitting machine. ►The fabric is drawn down through the nip of a two or three roller system driven by a gear train or by chains and gears directly from the main shaft of the machine. Take-down Technology ►In the diagram roller 1 is the main driven roller pulling the fabric from the sinker via yarn tension a1. ►Roller 2 is a pressure roller pressed against roll 1 by spring 3 to prevent the fabric slipping. ►The fabric passes through the nip between roller 1 and 2. ►The other group of three rolls show the fabric being wound-up on the fabric roller. Warp Knitting Machines Tricot Machine Compound Needle Warp Raschel Machine Knitting Machine