Warp Knit Structures PDF
Document Details
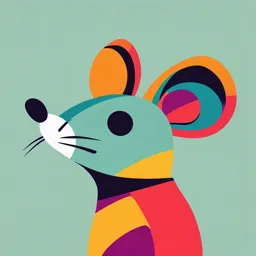
Uploaded by SimplestSaxhorn
Tags
Summary
This document provides an overview of warp knit structures, delving into concepts like overlaps, underlaps, and various types of lapping. It details the formation of different stitches, and differences between closed and open laps.
Full Transcript
Knitting Technology Warp Knitted Laps ►Loops are termed ‘laps’ in warp knitting because the warp guides lap their yarn around the needles in order to form the loop structure. ►The loops (overlaps) may be open or closed. Basic Warp Knit Structure ► A warp knitted structure is made up o...
Knitting Technology Warp Knitted Laps ►Loops are termed ‘laps’ in warp knitting because the warp guides lap their yarn around the needles in order to form the loop structure. ►The loops (overlaps) may be open or closed. Basic Warp Knit Structure ► A warp knitted structure is made up of two parts. ►The first is the stitch itself, which is formed by wrapping the yarn around the needle and drawing it through the previously knitted loop. ► This wrapping of the yarn is called an overlap. Basic Warp Knit Structure ►The second part of stitch formation is the length of yarn linking together the stitches and this is termed the underlap, which is formed by the lateral movement of the yarns across the needles. Warp Knit Structure ►The length of the underlap is defined in terms of needle spaces. ►The longer the underlap, the more it lies at right angles to the fabric length axis. Warp Knit Structure ►The longer the underlap for a given warp the greater the increase in lateral fabric stability, conversely a shorter underlap reduces the width-wise stability and strength and increases the lengthways stability of the fabric. Warp Knit Structure ►The length of the underlap also influences the fabric weight. ►When knitting with a longer underlap, more yarn has to be supplied to the knitting needles. Warp Knit Structure ►The underlap crosses and covers more wales on its way, with the result that the fabric becomes heavier, thicker and denser. ►Since the underlap is connected to the root of the stitch, it causes a lateral displacement in the root of the stitch due to the warp tension. Warp Knit Structure ►Run-in: the yarn consumption during 480 knitted courses ►Rack: a working cycle of 480 knitted courses ►The run-in, therefore, is the yarn consumption for one rack. Warp Knit Structure ► For a given machine with a given warp: A longer run-in produces bigger stitches and a generally slacker, looser fabric A shorter run-in produces smaller and tighter stitches With more than one guide bar the ratio of the amount of yarn fed from each warp is termed the run-in ratio. Open & Closed Laps ►The stitch formed has an open or closed character according to the direction of the underlap and overlap motions. ►The underlaps can be of differing magnitudes and directions: Open & Closed Laps ►If the underlap and overlap are in opposite directions then the stitch formed would have a closed character ►If the underlap and overlap are in the same direction, then the stitch formed will have an open character. Closed Lap ►A closed lap is produced when a subsequent underlap shogs in the opposite direction to the preceding overlap, thus lapping the same yarn around the back as well as around the front of the needle. Open Lap ►An open lap is produced either when a subsequent underlap is in the same direction as the preceding overlap. ►Closed laps are heavier, more compact, more opaque, and less extensible than open laps produced from the same yarn at a comparable knitting quality. Lapping Diagrams Single- Or Double-needle Overlaps ►Overlap movements are normally across only one needle space because two-needle overlaps cause both the warp thread and the needles to be subjected to the severe strain of two simultaneous adjacent knock-over actions. Single- Or Double-needle Overlaps ►In addition, different tensions on the two loops in the structure adversely affect their appearance. Single- Or Double-needle Overlaps ►The underlap between the double overlaps has the appearance of a sinker loop. Single Bar Structures ►A plain warp knitted structure is produced on a single needle bar. ►The resulting structures are known as single face fabrics. ►Rib and interlock warp knitted structures are produced on double needle bars, and these structures are known as double face fabrics. Single Bar Structures ►In single face structures (plain), stitches are visible on one side, known as the technical face, and on the other side (known as the technical back) only underlaps are visible. Single Bar Structures Single Bar Structures 5 Basic Variations ►All guide bar lapping movements are composed of 5 lapping variations. 5 Basic Variations ►An overlap followed by an underlap in the opposite direction (closed lap). 5 Basic Variations ►An overlap followed by an underlap in the same direction (open lap) 5 Basic Variations ► Only overlaps and no underlaps (open laps) 5 Basic Variations ► Only underlaps and no overlaps (laying-in) 5 Basic Variations ► Neither overlaps nor underlaps (miss-lapping) Pillar Lap ►A pillar stitch (or chain stitch) is a stitch construction where lapping of a yarn guide takes place over the same needle. ►As there are no lateral connections between the neighboring wales, the stitches are only interconnected in the direction of the wales. Pillar Lap ►Due to the absence of underlaps, a fabric is not created, only chains of disconnected wales. Underlaps Only ►Underlap alone cannot form into a fabric and is commonly used with other lapping movements. 1 & 1 Lap (Tricot Lap) ►The laps are executed in alternate overlap and underlap motions on two defined needles. ►This stitch creates a textile fabric as the underlaps connect both the courses and the wales. ►The simplest of this group of structures is made between two adjacent needles. 1 & 1 Lap (Tricot Lap) ►The laps are executed in alternate overlap and underlap motions on two defined needles. ►This stitch creates a textile fabric as the underlaps connect both the courses and the wales. ►The simplest of this group of structures is made between two adjacent needles. Tricot Lap 3 and 1 lap 2 and 1 lap Tricot Lap 4 and 1 lap Atlas Lap ►The atlas construction differs in that the laps are continued over two or more courses in one direction and then return in the other direction to the point where they started. Double Tricot Structure ► Lapping movement Front & back guide bars 1 and 1 lap in opposite directions ►Threading arrangement Front & back guide bars fully thread Double Tricot Structure ► Fabric characteristics Light weight fabric; splits very easily if a yarn breaks or a stitch drops Locknit Structures ► Lapping movement Front guide bars 2 and 1 lap Back guide bar 1 and 1 lap in opposite directions ►Threading arrangement Front & back guide bars fully threaded Locknit Structures ► Fabric characteristics Good elasticity Due to free-floating underlaps the fabric has a smooth back, which is very pleasant to touch. Light weight Non-splitting Locknit Structures Edge curling towards the technical back The structure contracts in the lateral direction after leaving the needles by about 67% (the structure was traditionally knitted on E28 machines but today knitting on E32 - E40 is becoming popular) Generally used to produce ladies lingerie Satin Structures ► Lapping movement Front guide bars 3(4) and 1 lap Back guide bar 1 and 1 lap in opposite directions ►Threading arrangement Front & back guide bars fully threaded Satin Structures ► Fabric characteristics The fabric shrinks after leaving the needles. This is due to the long underlaps Good elastic properties Very comfortable to wear Edge curling towards the technical back Satin Structures As the length of the underlaps increases, the structure exhibits a smooth and shiny technical back, but at the same time the structure becomes heavier Reverse Locknit Structures ► Lapping movement Front guide bars & bsp 1 and 1 lap Back guide bar 2 and 1 lap in opposite directions ►Threading arrangement Front & back guide bars fully threaded ►Fabric characteristics Not so stable as locknit 10 Shark Skin Structure ► Lapping movement Front guide bars 1 and 1 lap Back guide bar 3(4) and 1 lap in opposite directions ► Threading arrangement Front & back guide bars fully threaded 11 Shark Skin Structure ► Fabric characteristics The trapped longer underlaps restrict the fabric shrinkage Rigid and very stable structure Rough technical back; the reason for the name 12 Queen S Cord ► Lapping movement Front guide bars pillar lap Back guide bar 3(4) and 1 lap in opposite directions ► Threading arrangement Front & back guide bars fully threaded Queen S Cord ► Fabric characteristics High degree of stability Minimum lateral shrinkage after leaving the needles; i.e. final width of the fabric is closer to that of the knitted width Net Structures ►Net structures can be classified into the following groups: Net structures in which the distance between the wales is determined by the gap between the needles used to knit the structure Net structures that are formed by interconnecting pillars. Net Structures Net Structures Net Structures With Interconnected Wales ►The basic structure of such a net is produced by the guide bars that are threaded 1-in and 1-out. ►Principally each guide bar produces a pillar lap. Laying-in Structures ►A guide bar is used to insert yarn ends into the fabric structure. ►The laid-in yarn end is not knitted into the structure, but it is held in the structure between the stitches (in the technical front) and the underlaps (formed by other yarns in the technical back). Laying-in Structures Laying-in Structures ► Basic principal of laying-in Laying-in is achieved using a back guide bar. Generally, at least one fully threaded guide bar in front of the laying-in guide bar(s) produces the ground structure. Laying-in Structures A laying-in guide bar can be fully or partially threaded. Fully threaded laying-in guide bars increase the fabric stability. Partially threaded laying-in guide bars are utilised for patterning purposes. The laying-in guide bars carry out only the underlaps. Laying-in Structures ► Advantages of laying-in Laying-in technique allows one to knit yarns that are otherwise difficult to knit Any yarn which is capable of passing freely through the guide eye and between the needles can be inserted into the fabric Laying-in Structures Laid-in yarns contribute very little towards the fabric weight because of the lack of loops Saves on patterning yarn, which is usually more expensive, i.e. a commercial advantage Yarn Threading Plan ►In warp knitting a yarn guide wraps the yarn around the needle hook, thus forming a loop. Yarn Threading Plan ►However, to form a fabric, the yarn guide must wrap the yarn around a different needle during the next course. ►The yarn guides, therefore, must be displaced laterally during knitting. Yarn Threading Plan ►Different warp knitted structures are produced by varying the magnitude of their lateral displacement. ►Therefore warp knitted structures can be described by noting the guide bar displacement. Tulle fabric Designing Weft K Warp Knitted Knotless Nets Designing Weft K