On-Load Tap Changer Type H Inspection Instructions PDF
Document Details
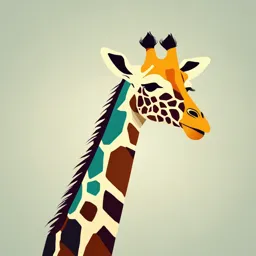
Uploaded by BestSellingBeige
null
Reinhausen
Tags
Related
- Chapter 16: Power Supply Systems for Signalling Installations PDF
- VACUTAP® VV® On-load Tap-changer Installation & Commissioning Instructions PDF
- VACUTAP® VM® On-Load Tap-Changer Installation & Commissioning Instructions PDF
- VACUTAP® VM® On-Load Tap-Changer Installation and Commissioning Instructions PDF
- Ship's Electrical System Overview PDF
- Power Supply Installation PDF
Summary
This document contains detailed inspection instructions for on-load tap changers (OLTCs). The instructions cover various procedures, including the removal and cleaning of components, as well as operational checks. It is a technical manual.
Full Transcript
MASCHINENFABRIK MIR Feisalsen ON-LOAD TAP CHANGER TYPE H Inspection instructions MASCHINENFABRI...
MASCHINENFABRIK MIR Feisalsen ON-LOAD TAP CHANGER TYPE H Inspection instructions MASCHINENFABRIK MIR FeiNratsex IA 112/89 e n - 0292/1000 Maschinenfabrik Reinhausen GmbH Printed in Germany Postfach 1 2 0 3 6 0 W-8400 Regensburg 12 Telefon (09 41) 40 90-0 Telefax (09 41) 4 42 03 Telex 6 5 881 ON-LOAD TAP CHANGER TYPE H Inspection Instructions No. 112/89 Contents Page 1. General....... iii iii ie tiir area 3 1.1 Functional principle of the OLTC 1.2 Designation of OLTC models 1.3 Principal parts of the OLTC 1.4 Inspection intervals 1.5 Summary of inspection works Preparations......... iii iirc einai 7 2.1 Tools and equipment 22 Safety precautions 2.3 Operating position w h e n removing the O L T C insert Removingthe OLTCinsert............c.cc.iiiiiiiitiinnannnnnn. 8 3.1 Removing the tap changer head cover 3.2 Removing the gear mechanism 3.3 Withdrawing the suction pipe 3.4 Switching off the change-over selector, operating key 35 Withdrawing the OLTC insert Cleaningprocedure...........ccoviiiinrrineerneescnannenonnan 11 4.1 Cleaning the oil compartment 4.2 Cleaning the OLTC insert 4.3 Cleaning the suction pipe Inspection ofthe OLTCinsert...............c0iiirtiviinnrennns 12 5.1 Measuring the transition resistors 5.2 Determination of contact wear Replacingthecontactrollers.................ccoiiiiiiinnn, 12 6.1 Removing the contact rollers 6.2 Replacing the contact rollers Reinstallingthe OLTC insert...........c.cciviitiniivrrneennnnnn 15 7.1 Reinserting the OLTC insert 7.2 Reinserting the suction pipe 7.3 Installing the gear mechanism Oilfilling..... ee 16 OthercChecKs «o.oo viii i ice iii iit icine aannas 17 9.1 Drive shaft assembly 9.2 Operational tests of motor drive unit and tap changer 9.3 Protective relay RS 2001 9.4 Voltage regulating relay 10. Appendix............ Carreras ieee 18 10.1 Coupling procedure of OLTC and motor drive unit 10.2 Inspection tools 10.3 Spare parts list 10.4 Parts of the switching element and contact cylinder 10.5 Adjustment plans 10.6 Withdrawal and installation of the OLTC insert of tap changers H lil 400 A-40/76 with change-over selector, H lll 400 A-123 and H lil 400 A-145 supplied after 5/89 1. GENERAL The OLTC operates as selector switch and fulfills the functions of a diverter 1. 1 Functional principle ofthe OLTC switch and a tap selector in one unit. (fig. 1). If necessary, the OLTC may be equip- ped with a change-over selector. The OLTC serves to connect the The change-over selector performs desired tap of a tapped transformer change-over operation prior to selector winding under load. switch operation. The selector switch transfers the cur- rent from the tap in service t o the next, thereby inserting ohmic resistors to ensure no-break current transition. Motor drive unit OLTC Switching element Time i n seconds Circuit diagram A,B — main contacts a,b — main switching contacts al, bt — transition contacts Contact movement Fig. 1 Tap-change operational sequence 1.2 Designation of OLTC models (fig. 2) On-load tap changer The type H OLTC is designed for three- H lI 400 A — 123 — 10 19 1W pole connection, a max. rated through- current of 400 A, for neutral application (up to 76 kV) or full insulation between poles and to ground, as well as for different basic connection diagrams. Type Basic connection diagram The designation incorporates all these Number of poles characteristics and permits easy Highest voltage identification of the OLTC. Max. rated t h r o u g h_| - for equipment c u r r e n (t in amperes) U p inkV The inherent designation of the basic circuit diagram identifies: number of selector switch contacts, Neutral connection T - number of operating positions, number of mid-positions and type of change- A n y other c o n n e c t i o n A over selector. Example in fig. 2: Type H OLTC, three-pole, max. rated through-current Basic connection diagram 400 A, for delta-connected tap winding, insulation to ground and between poles 10 19 1 w for Um = 123 kV, basic connection diagram 10 191 W, that is 10 selector switch contacts, 19 operating posi- tions, one of which being a mid- Contact circle pitch Mid-position(s) Change-over selector position and a change-over selector used as reversing switch. 0 1 10 Max. number of 3 G w 1.3 Basic parts of the OLTC (fig. 3) 12 operating Coarsetap Reversing 14 positions selector switch 17 The basic parts of the OLTC are: — the tap changer head Without change- With change- over selector over selector — the oil compartment Fig. 2 - the OLTC insert Designation of OLTC 10 19... 12 23 ] Um = 123kvor 145kV and basic circuit 1 27 — the separate change-over selec- diagram 17 33 Up, = 4 0 k Vo r 76 kV tor (for H lll 400 A-145 type only) OLTC main parts subject to inspection are clearly marked in colour (see fig. 3). Fig. 3 Component parts 11 tap changer head 12 tap changer head cover upper gear unit bleeder valve inspection window for position indication mounting flange 21 oil compartment cylinder 22 grading ring change-over selector terminal 24 selector switch terminal 25 current take-off terminal 26 oil compartment bottom 27 kerosene drain screw 31 gear base plate HIll400Y, H I 400A, H lll 400A-123 32 cog-wheel with coupling Change-over selector built-in 33 Geneva wheel for selector switch drive shaft 34 drive crank for change-over selector 41 selector switch drive shaft 42 switching element 43 contact roller for movable main switching and transition contacts 44 selector switch stationary arcing contact 45 contact roller for main contact contact roller for current take-off 47 current collecting ring 48 transition resistor 49 bottom bearing movable contact carrier C8RRER grading ring movable change-over selector change-over selector drive lever Change-over selector separately attached change-over selector drive shaft change-over contact shel change-over selector stationary contact 58 electrode H Wi 400 A-145 6 1 a pipe connection R for protective relay 61b pipe connection S with bleeder screw for suction pipe 6 1 c pipe connection Q for return pipe (with oil filter unit only) 61d pipe connection for transformer oil 62 internal connection pipe 63 suction pipe centering 1.4 Inspection intervals The user should regularly test the If inspection is not carried out by MR transformer insulating oil. The dielec- personnel, please send us your in- We recommend inspection of the tap tric strength and the water content of spection report for our files. This will changing equipment at regular inter- the oil (record oil temperature during enable us to give you useful recom- vals to maintain a high level of operat- ~~ sample-taking) must comply with the mendations for future inspections. ing reliability. respective standards such as IEC Publication 422 (1973), DIN 57 370 In general, the inspection can be Teil 2/VDE 0370 Teil 2/12.78. carried out by qualified and trained e n oromarad ant r a y r rovided itis On-load tap changer Water content”) Dielectric strength™") Inquire f h A HNl400Y 40 ppm 30kV/2.5 mm nquire for spare parts when preparing yj 400 A, H 111 400 a-123, 30 p p m 40 kV/2.5 m m an inspection which shall not be car- H 111400 A-145 ried out by MR personnel (please indi- cate OLTC serial no. and number of *) measured according to the Karl Fischer method based on operations). IEC Publication 814 (1985) **) measured according to DIN 57 370 Teil 1/VDE 0370 Teil 1/12.78 The number of tap change operations determining the inspection intervals indicated in table I are figures based on experience with oil qualities nor- Rated transformer Number of tap change operations mally used. Regardless of the number ~~ On-load tap changer current without oil filter ~~ with oil filter of operations we recommend inspec- tion after 6 to 7 years of service. Hlll400Y/A © u p t o 200A 100 000 150 000 over 2 0 0 A 70000 140 000 The first inspection of tap changers H I l 400 A , H l l l 4 0 0 - 1 2 3A and H l l l 400 A-123 u p t o 2 0 0A 7 0 000 140 000 H I 400 2-145 should be carried out over 200A 50 000 100 000 aftera period of 2-3 years of service. y y 40081 4 5 u p t o 200 A 70000 140 000 If the number of operations per year is over 2 0 0 A 5 0 000 100 000 30 000 or higher, we recommend the use of our oil filter plant type 51 Table!l Inspection intervals (see Operating Instructions No.18). Filtering of switching oil allows the extension of the inspection and oll change intervals. Continuous filtering also increases the mechanical life of the selector switch by immediately removing all abrasive particles. 1.5 Summary of inspection work 2. PREPARATION The inspection comprises: 2.1 Tools and equipment — Removing and reinstalling the The following equipment is needed: OLTC Insert — Empty vessels for dirty oil, the ne- — Cleaning the oil compartment, the cessary quantity of new oil for oil OLTC insert, and the oil conser- change and cleaning purposes vator tank (oil filling quantities, see table II) — Changing the switching oil oLTC H I 400 Y ‘ H I I 400A H I I 400A-123 | HII 400 A-145 — Checking the OLTC insert and oil WO kV 76 kV compartment without shange- | 200 240 260 290 32s — Determination of the contact wear with change- over selector 220 270 290 355 325 — Measuring the transition resistors Table l l Oil filing quantities in litres — Checking the protective relay, drive shafts, motor drive unit, — An oil pump for the ease of the ail and — where present — the oil filter change unit and voltage regulating relay. — Miscellaneous brushes and rags The OLTC insert should not be ex- — Special brushes for cleaning the oil posed to air for longer than necessary suction pipe, the selector switch (at max. for 10 hours) drive shaft, and the oll compart- ment cylinder (see appendix, Inspection work should not be inter- par 10.2) rupted. Care and cleanliness should be strictly — Awork table observed. — Alifting device: the OLTC insert weighs 80 kgs max., observe the withdrawal heights in table I i oLTC Hill 400 Y H I I 4 0 0A HII1400A-123 | H l 400 A-145 40 kV 76 kV without change- | 4459 1400 1550 1750 2000 withchange- 1300 1650 1750 2150 2000 Table l l l Withdrawal heights of the OLTC insert in mm — Inspection tools 2.2 Safety precautions (see appendix, par. 10.2) Switch off the transformer. Isolate and — Spare parts secure against reclosing. Check no- (see appendix, par. 10.4) voltage condition. Ground all terminals visibly. Mark out the working area. Please note: Lock tabs, self-locking screws and nuts should never b e used twice; please ensure sufficient spare parts when preparing for an inspection. 2.3 Operating position when removing the OLTC insert The OLTC Insert can be withdrawn in any operating position. Note the ope- rating position when withdrawing the unit. It is, however, recommended to with- draw the OLTC insert in the adjustment position which is marked by an arrow on the position dial of the motor drive unit (fig. 4). Please note, that all in- spection procedures described here refer to the adjustment position. The adjustment position is reached by cranking the motor drive clockwise. Caution: D o not operate the motor drive unit while the tap changer i s uncoupled. To prevent electrical operation by re- mote control, it is good safety practice to disconnect the motor drive unit by tripping the motor protective switch. 3. REMOVING THE OLTC INSERT 3.1 Draining the oil Shut the stop valve between oil con- servator tank and tap changer. Open the OLTC drain valve and the bleeder valve of the head cover (see fig. 5). Remove cap screw M30/wrench size 36, lift tappet by means of a screw- driver. If an oil filter is installed: open the return pipe sample valve and operate 6 8 the filter unit. Drain via the return pipe. Fig. 5 Tap changer head 3.2 Uncoupling the horizontal drive 1 — Drive shaft (square tube) shaft 2 — Coupling brackets with bolt Remove 6 screws M6 (w.s. 10) from 3 — Upper gear unit coupling brackets. Take care of the 4 — Tap changer head cover coupling bolt, nuts and lock tabs. 5 — Bleeder valve of head cover Normally the square shaft can be moved to one side for clearance. 6 — Pipe connection R for protective If not, remove the other coupling relay RS 2001 brackets (on the side of the bevel 7 — Pipe connection S with bleeder gear), as well (screws, nuts and lock screw for suction pipe tabs as above) and remove the 8 — Position indicator horizontal drive shaft. 8 3.3 Removing the tap changer head cover Remove the cover bolts M10 x 35 (w.s.17), take care not to lose spring washers. Take off the head cover. Take care not to damage the O-ring gasket of head cover. 3.4 Removing the gear mechanism The gear mechanism support plate is attached into the tap changer head by 5 support arms (fig. 6, 7). Note the position of red gear marks to ensure correct reinstallation. Disconnect the suction pipe and energy accumulator. Unscrew suction pipe R 3/4” (w.s. 27 & 39), d o not lose the gasket. Push the plug into the head casting. Pull out the fixing bolt for the energy accumulator. Unlock and remove 5 screws M8 x 30 (w.s.13) from the support arms (fig. 8, 9). Remove the gear mechanism. Note the position of the red triangular marks for correct reinstallation (fig. 10, 11). Store the detached gear mechanism (fig. 12, 13) and all loose parts safely until reinstallation. 13 »with built-in change-over selector« swithout change-over selector or with separately attached change-over selector« 3.5 Withdrawing the suction pipe The suction pipe centers the OLTC insert in the bottom bearing. The suction pipe must be withdrawn against the contact pressure. Lift out the suction pipe by inserting a screwdriver into the upper slot of the tube. Then seize the second slot and remove by hand (fig. 14, 15). 3.6 Switching off the change-over selector The OLTC insert is removed with the aid of an operating key no. 1 or no.2 (refer to par. 10.2) which attaches to the switching shaft coupling by 3 screws M10 x 20 (fig. 16) In the dimension drawings 896 054 and 896 957 (see par. 10.2) the operating keys no.1 and no. 2 are assigned to the corresponding OLTC types. For OLTC models with built-in change-over selector using the operating key no. 1 disengage the moving change-over selector con- tacts from their mating stationary contacts and move into withdrawal position (fig. 16). For this purpose turn the attached key in clockwise direction to get the moving change-over contacts into the middle between phases of stationary contacts (fig. 17, 18). The radial supports of the OLTC insert must be removed prior to withdrawal of the OLTC insert (each attached by 2 hex. head screws M8 x 16, wrench size 13, 1 lock tab, see fig. 18). I n case of OLTC with upper switch- ing element displaced b y 180° (fig. 19), please strictly observe the information regarding withdrawal and installation of the OLTC insert according t o section 10.6. 3.7 Withdrawing the OLTC insert Attach the lifting hook to the operating key. Lift the OLTC insert slowly and carefully (fig. 20). Make sure, that there is sufficient clearance between oil compartment and both grading rings and switching elements of the OLTC insert while lifting up. Put the OLTC insert aside, secure and let the oil drip off. 10 4. CLEANING PROCEDURE 4.1 Cleaning the oil compartment (fig. 21) Open the stop valve between tap chan- ger head and oil conservator tank of the tap changer. Drain off oil until clean oil flows. If necessary, flush the oil conservator tank with transformer oil. Flush the oil compartment with trans- former oil. Remove carbon deposits by means of rags or a special brush with extended handle (see par. 10.2). Flush again with oil. Drain the oil com- partment completely. Put the cover on the oil compartment and insert the screws as a precaution. 4.2 Cleaning the OLTC insert (for examples see fig. 22) The OLTC insert is best cleaned with a brush. Special care should be taken with the cleaning of the switching elements, transition resistors and the switching shaft. Rinse all parts with transformer oil. Fig. 21 Tap changer open, inside -view of the oil compartment For the interior of the switching shaft use a special brush with extended 1 — Bottom bearing handle (fig. 23), see par. 10.2. 2 — Kerosene drain screw 3 — Selector switch contact In addition, the interior of the switching 4 — Current collecting ring shaft is cleaned by thorough flushing 5 — Change-over selector contact with transformer oil. Finally check that the inside and outside of the switching shaft are perfectly clean. 43 Cleaning the suction pipe Clean the outside of the suction pipe with rags. Clean the inside of the suction pipe by inserting a special brush with along handle (fig. 24), see par. 10.2. Thoroughly flush with transformer oil. H lll 400A-123 H Ill 400A-145 w i t h built-in w i t h separately change-over attached change- selector over selector 24 11 5. INSPECTION OF THE OLTC INSERT 5.1 Measuring the transition resistors Measuring of transition resistors is carried out while they are still con- nected to the contact rollers, i. e. between transition and main switching contact rollers of each switching element (fig. 25). The resistance is in the order of 0.5 to 20 ohms. The mid contact roller of the three contact rollers of any switching element is the main switching contact. No. of selector Diameter of contact rollers Contact MR-item no. switch contacts inmm Measured resistance values should be new minimum identical and must comply with the name-plate. A 10 percent deviation is ab 091 385 10, 12, 14, 17 22.0 17.0 permissible. right: 091722 a1, b 1 , 12 22, 17. left: 085495 10 0 0 5.2 Determination of contact wear right: 091487 at, 4,17 16. The contact wear is determined by bi left: 086 064 ! X 200 60 measuring the actual contact roller diameter using a vernier gauge Table l V Diameters of contact rollers new and when to be replaced (fig, 26) and comparing the reading with the diameter when new (refer to - table IV). Replace the contact rollers when the minimum contact diameter has been reached or is likely to be reached be- fore the next inspection. If o h e contact rolier needs to be replaced, replace all contact rollers of the OLTC insert. 6. REPLACING THE CONTACT ROLLERS 6.1 Removing the contact rollers Place the OLTC insert i n a horizontal position (fig. 27). Detach the upper grading fing: 6 screws MS x 8 (w.s. 8), unlock and remove (fig. 28). Push the grading ring up. Disconnect the contact braids for the transition contacts: disconnect the braids on both connectors of transition resistors, 2 headless screws M4 x 10 (w.s. 2.5), fig 29. 12 Pull the crimp connector out of the connector and cut it off (fig. 30). Slip out the contact braids (fig. 31). Disassembling the switching element: 4 screws M6 x 25 (w.s.10) of upper base plate, unlock and remove (fig. 32). Take off the upper base plate (fig. 33). Withdraw 2 insulating tubes of the contact bralds (fig. 34). Take off compression springs and spring holders from transition contact rollers (fig. 35). Pull both transition contact rollers upwards to remove (fig. 36). Withdraw the arc chutes on both sides of the main switching contact. Disconnect the contact braid for main switching contact: unlock and loosen 2 screws M5 x 18, w.s. 8 (fig. 37), d o not remove them. Pull out the braid from inside the clamping plate. 13 Remove 4 guide rollers with axles (fig. 38). Take note of washers, for later reinstalling them in the same place. Take off compression spring and spring holder from the main switching contact (fig. 39). Remove the recess head bolt M6 x 60 (w.s. 4) from the stop tube of the main switching contact sledge (fig. 40). Remove stop tube and braid for main switching contact. Pull out the main switching contact roller together with its sledge (fig. 41). All contact rollers are now removed. 6.2 Replacing the contact rollers Replacement of contact rollers is done in the reverse order to disassembly. Always use new lock tabs. Please observe the following details for screw connections: Reinstall the stop tube (on the rear of main switching contact sledge: 1 recess head bolt M6 x 60 (w.s. 4), max. torque 9 Nm (fig. 42). The bolt is self-locking, therefore replace it with new one. Clamp the main switching contact braid to the switching element case: 2 screws M5 x 18 (w. s. 8), max. torque 5 Nm, locked by lock tabs. Attach the upper base plate: 4 screws M6 x 25 (w.s.10), max. torque 9 Nm, 2 lock tabs (fig. 43, 44). Connect the transition contact braids: 2 headless screws M4 x 10 (w.s.2.5) for each connector, max. torque 2 Nm, locking by loctite fluid. The contact braids are to be fitted with a cable pin, using crimping pliers (fig. 45). 14 Attach the upper grading ring: hanging OLTC insert so the switching 6 screws M5 x 8, max. torque 5 Nm, elements are in approximate adjust- 3 lock tabs. ment position when the OLTC insert is installed. Disassemble and reassemble the other switching elements likewise. Lower the OLTC insert into the oil The O L T Ci s thenready for reinstal- compartment. Make sure, that screen- Jation. ing rings and parts of the switching elements have sufficient clearance to the parts of the oil compartment. Reattach the radial supports to the OLTC insert (each with 2 hex. head 7. REINSTALLING THE OLTC screws M8 x 16, wrench size 13, INSERT max. torque 14 Nm, 1 lock tab). 7.1 Reinserting the OLTC insert The reinstallation of the OLTC insert is performed in the reverse order to removal (please refer to par. 3.4). To pick up the lifting device, use the operating key no. 1 or 2 (see par. 10.2), which is attached onto the OLTC insert coupling by 3 screws M10 x 20. In case of OLTC with built-in change- over selector (fig. 46) place the 46 operating key onto the coupling that its dog engages into the pocket of the coupling. For OLTC without change- over selector or separately attached change-over selector set the dog between the centering supports. Remove the head cover and lift the OLTC insert over the open tap changer head. Reinstall the OLTC insert. OLTC with built-in change-over selec- tor and upper switching element dis- placed by 180° (see fig. 46): please strictly observe the information regarding withdrawal and reinstallation of the OLTC insert. OLTC with built-in change-over selec- tor and not displaced upper switching element: position the hanging OLTC insert so that switching elements can easily pass between the stationary change-over selector contacts when lowering the OLTC insert (fig. 47). OLTC without built-in change-over Fig. 47 Position of switching elements and stationary change-over selector or with separately attached selector contacts change-over selector: position the 15 7.2 Setting the adjustment position, reinserting the suction pipe Set the OLTC insert to the adjustment position (see appendix par. 10.4, adjustment plans) by using the operat- ing key (fig. 48). For OLTC with built-in change-over selector: set the unit to adjustment position by operating the change-over selector movable con- tacts counterclockwise into switched position. Detach the opera-ting key and reinsert the suction pipe (fig. 49). Center the OLTC insert in the oil compartment by pressing onto the upper end of the suction pipe (fig. 50). The OLTC insert is now ready for reinstalling the gear meachanism (fig. 51, 52). 7.3 Installing the gear mechanism (fig. 53, 54) The gear mechanism is reinstalled in reverse order to removal (see par. 3.4). Set the gear mechanism to the adjust- ment position (by means of the posi- tion indicator dial and with the aid of the red gear marks). The gear mecha- nism can only be remounted and coupled to the OLTC insert in this position. Attachment of the gear mechanism supporting plate: 5 screws M8 x 30 (w.s.13), max. torque 14 Nm, locked by lock tabs. Insert the energy accumulator fixing bolt, reconnect the suction pipe fitting R 3/4” (w.s. 27, 39), remember the gasket. 8. OIL FILLING Fill the oil compartment with new transformer oil up to the level of the gear mechanism support plate. Close the cover of the tap changer head. Make sure that the O-ring gasket is in good condition; otherwise replace it with a new gasket. : | Ha k. »with built-in change-over selector« »with change-over selector or with 16 separately attached change-over selector« Attachment of head cover: 24 bolts Thereby check coincidence of the For this purpose also withdraw the M10 x 35 (w.s. 17), max. torque position indication of tap changer diverter switch unit. 35 mm, locked by spring washers. and motor drive i n all operating posi- tions. In addition see Operating Instructions Open the stop valve between oil con- No. 59 for the protective relay servator tank and tap changer head. Check the electrical and mechanical R S 2001. Bleed the tap changer head through end position of the motor drive unit the bleeder valve of the head cover (see our Operating Instructions No. 40 Before returning t o service, make {remove screw cap M30/w.s. 36, lift for motor drive MA 7 or No. 80 for sure that the tap changer and trans- tappet by means of a screwdriver and MA 9 respectively). former are undamaged. Never recon- bleed). nect the transformer without check- ing beforehand. Bleed the suction pipe (screw cap 9.3 Protective relay RS 2001 (see M16/w.s. 22, cheesehead bleeder Operating Instructions No. 59) In case of serious trouble with tap screw M6, max. torque 2 Nm). changer or motor drive — provided The transformer must be immediately that the repair cannot easily be done If a stationary oll filter unit is installed: switched off by the circuit breakers o n site — and i n case of a response of operate and bleed the unit. when the protective relay is energized. the protective relay or the tap-change The operational test of the protective monitoring circuit please contact the Refill the oil conservator tank t o its relay should, therefore, include check- authorized MR representative, the previous level. ing the proper function of the circuit transformer manufacturer or breakers. Maschinenfabrik Reinhausen G m b H Make sure that the transformer cannot Technischer Service 9. OTHER CHECKS be energized and its ground connec- tions cannot be removed during the Falkensteinstrasse 8 test. Furthermore, make sure that the Postfach 12 03 60 9.1 Drive shaft assembly fire-extinguishing equipment, if coupled W-8400 Regensburg 12 with the tripping of the protective relay Telefon (09 41) 40 90-0 Couple the horizontal drive shaft cannot operate. Telefax (09 41) 4 42 03 to the upper gear unit and bevel gear Telex 6 5 881 (6 screws M6, w.s. 10, Proceed a s follows: Telegramme: oltc reinhausen max. torque 9 Nm, lock tabs). 1. Close the circuit breakers with Check horizontal and vertical drive isolating switches open and trans- 9.4 Voltage regulator shafts, especially the coupling points. former terminals grounded. (see corresponding If necessary, grease coupling bolts and Operating Instructions) O-rings (e.g. with SHELL 6432), adjust 2. Open the hood for access to the axial clearance to 3 mm. test push-buttons (3 screws M6, If the tap changer is controlled by a w._s. 10). Press the push-button voltage regulator: Check bellows and greasing of ball TRANSFORMER OFF. The circuit joints (special design). breakers must open. Check settings of voltage level, sen- sitivity (bandwidth) and delay time Check upper gear unit at tap changer 3. With the protective relay in according t o the operating instructions head cover and bevel gear (add lubri- TRANSFORMER OFF position, it in order to avoid unnecessary tap cating grease if necessary). must be impossible to close the change operations. circuit breakers. This is to be checked. 9.2 Operational tests of motor drive unit and tap changer 4. Reset the protective relay to the TRANSFORMER IN SERVICE Check symmetrical coupling of motor position and lock the hood (3 drive to the tap changer. screws M6, max. torque 5 Nm). The follow-up of the motor drive must Note: be approximately identical in both In case of a response of the protective directions (adjust if necessary, see relay it is absolutely necessary to section 10.1 of appendix). Perform trial check the tap changer and trans- operations across the whole tapping former. range. 17 10. APPPENDIX 10.1 Coupling of the tap changer and motor drive unit (see also 10 15 20 hao | c m s Operating Instructions No. 40 for A TE motor drive MA 7 and No. 80 for 2+ 1 ie motor drive MA 9) | operation OF DIVERTER SWITCH 20 15 10 5 it is absolutely necessary that the tap changer operation Is finished before the motor drive stops. This is ensured by setting the time of the selector switch action (= on-load tap changing) at a distinct interval before the end of the motor drive action (1.5 — 2 sections before the red OPERATION OF center mark on the tap change indication wheel). This red DIVERTER SWITCH center mark is used as reference when adjusting. i S 10 15 20 > 30 One tap change op ponds to one rotation indication wheel.In case of MA 8 motor drive the tap change indication wheel is divided into 30 sections with one section corresponding t o one rotation of the crank. of the IZEE TT TTT LL 1 a! 1 { _operaTiON OF TTT ray TIT T T E Y c The number of sections counted from the beginning of the tap DIVERTER SWITCH change operation until the red center mark of the indication wheel faces the mark on the inspection window, should be equal i n both directions. Minor asymmetry is admissible. Symmetrical coupling is achieved as follows: When adjusting ensure that the position indication readings of motor drive and tap changer are equal. UNCOUPLE I — Tap changer and motor drive have to be i n the adjustment position. — Couple tap changer and motor drive. 0 375 — Tum crank in one direction until diverter switch action occurs, Count the remaining sections until the red center mark of the tap changer indication wheel is visible i n the middle of the inspection window. — Repeat this procedure i n the opposite direction. — Ifthere is a difference between the numbers of sections counted in both directions, the motor drive must be readjusted in relation to the tap changer by half of this difference of numbers. COUPLE f Example with motor drive MA 8: (see tig. 55) a) Tap changer is In operating position 10. Tum crank towards 11 until selector switch action occurs. Count number of sections until red center mark appears. ; 10 15 Result: 12 sections. LLU b) Tap changer is i n operating position 11. Turn crank 111 g towards 10 until selector switch action occurs. Count number of sections until red center mark appears. Result: 4 sections. } operation oF DIVERTER SWITCH Correction value: 20 15 5 0 1 / 2 (12 sections — 4 sections) = 4 sections, chosen 3.75 sections. ¢) Turn crank towards 11 until red center mark appears. d} Uncouple vertical drive shaft. b oeraron OF DIVERTER SWITCH e) Proceed i n the same direction (towards 12) b y 3.75 sections. Fig. 55 Symmetrization of coupling between tap changer and f) Couple again. motor drive g) Proceed i n the same direction (as with e} until selector switch action occurs. Count number of sections until red a,b - Counting sections after selector switch action i n both directions center mark appears. Result: 8.25 sections, [+] Cranking in the direction of the bigger number of sections d Uncoupling h) Check i n the opposite direction. e Cranking on b y correction value Result: 7.75 sections. f - Coupling g Completing operation, checking number of sections h Checking i n the opposite direction 18 10.2 Inspection tools Tools for bolts & nuts for installation and inspection Operating key No.1........ iii iii ieainaneanens 896 054 Operating key No.2..... iii inni iii e ii iiiaieiar aes Special brushes for cleaning the oil compartment, selector switch drive shaft and suctionpipe....................... item No Designation Fig. DIN Wrench size 1 1 Double-ended open jaw wrench A | 895 | 8x10 2 1 Ring & open-jaw wrench C [3113 10 3 1 Double-ended open-jaw wrench A | 895 13x17 4 1 Double-ended socket wrench B | 896 13x17 5 1 Double-ended open-jaw wrench A | 895 17x19 6 1 Double-ended open-jaw wrench A | 895 22x24 7 1 Hexagon socket screw key D | 911 25 8 1 Hexagon socket screw key D | 911 4 MASCHINENFABRIK MR reuse On-load tap changer type H 896 454 : OF — Tools for bolts & nuts for installation and inspection Survey Withdrawal and reinstallation of the OLTC insert, operating key oLTC Change-over Arrangement of Upper switching Use o f Withdrawal/ selector change-over selector element displaced operating key reinstallation by 180° acc. section H I I 400Y — 40/76 without - no no. 1 36/71 H I I 400Y — 40/76 with built-in no no. 1 36/71 H l 400 A— 40/76 without - no no. 1 36/71 H i 400 A— 40/76 with built-in no no. 1 36/71 H i 400A — 123 without —- no no. 1 36/71 HIll 400A — 123 with built-in no “no. 1 36/71 H Ill 4 0 0 A— 145 without - no no. 1 36/71 H I l l 400A — 145 with separately attached no no. 1 36/71 Design changed, effective from delivery date 5/89 H Ill 400A — 40/76 with built-in yes no. 2 10.6 H Ill 400A — 123 without — yes no. 2 3.6/7.1 H I I 400A — 123 with built-in yes no. 2 10.6 H I I 400A — 145 without - yes no. 2 36/71 H I 400A — 145 with separatly attached yes no. 2 36/71 T o b e used with OLTC H1I400Y without & with change- over selector r a — 3 5 —anf r a 20 H 111 400 A without change-over 45 selector and u p to delivery date 5/89 H 111400 A with change-over selector 257 H lil 400 A-123 without & with change-over selector 284 H 111 400 A-145 without & with change-over selector he 31 —om 155 182 Jal AT MRresaiss™" MASCHINENFABRIK REINHAUSEN On-load tap changertype V, H Operating key no.1 (092003) for tap changer insert 896 054 : 1E $28.0, To be used with OLTC 22 |Z delivery date from 5/89 ; : [